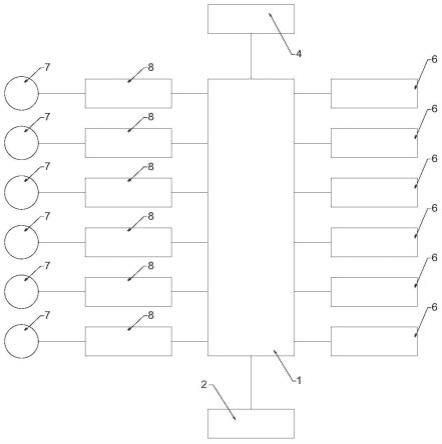
1.本发明属于纺织设备技术领域,具体涉及一种互联式高精度浆纱机多经轴退绕长度智能控制方法及装置。
背景技术:2.浆纱机是用于对织造所需经纱进行上浆的纺织生产装备。在浆纱过程中,经纱首先从若干个配置在经轴架上的经轴退绕,接着输送至浆槽吸收浆液,进入烘房烘燥,最终在车头卷绕至一个经轴上。其中,经轴架上的每一个经轴均由整经机生产,每一个经轴上都平行卷绕数百至上千根经纱。每一个经轴在生产过程中,其经纱的卷绕长度和卷绕张力都由整经机精确控制。
3.目前,所配置的每一个经轴,是由轴承固定在经轴架上的,其退绕的主动力由车头提供,每一个经轴配备一个制动装置,用于控制各经轴上经纱退绕时的张力。理论上,当各经轴的张力配置到一致水平,各经轴的退绕长度是一致的。但在实际生产中,因机械状态与人为操作误差,各制动装置的张力配置难以保持一致,这就导致各经轴的退绕长度总是存在差异。这种现象一方面造成经纱张力不匀引起制造效率降低,另一方面造成生产批次结束时大量经纱残留在经轴上,导致资源浪费。
4.为解决上述问题,“浆纱机经纱恒张力电子退绕气动控制装置(申请号为200510040762.5)”、“一种浆纱机发送装置的张力控制装置及张力控制方法(202110762964.x)”等专利,均提出采用张力检测装置检测各经轴对应输出的经纱张力,并运用闭环控制系统,动态调整制动装置的制动力。拟通过退绕经纱的张力控制来实现各经轴退绕的一致性。然而这种方式存在以下若干缺点:1)张力检测装置的设置对经纱性能造成一定影响;2)张力检测装置的设置造成浆纱机上机操作复杂度增加;3)系统对张力检测与张力控制的精度要求较高,系统维护困难;4)张力检测装置检测的对象可能仅是各织轴上经纱中的一小部分,因而可能存在采样误差。
5.根据实际的生产经验来看,通过控制各经轴退绕经纱的张力,实现各经轴退绕一致性的效果并不理想,经纱退绕结束时,经常会出现各个经轴上存在不等量的余纱,而且,个别经轴上的余纱量还很大,部分经轴上的经纱余量超过100米是很常见的现象。
技术实现要素:6.本发明首先要解决的技术问题是:提供一种互联式高精度浆纱机多经轴退绕长度智能控制方法,以解决目前经纱退绕过程中的张力控制不准确、各经轴退绕不同步、部分经轴退绕时的累计误差得不到消除、生产批次结束时存在大量残余经纱导致资源浪费的技术问题。
7.为解决上述技术问题,本发明采用的技术方案是:浆纱机多经轴退绕长度一致性智能控制方法,包括如下具体步骤:
8.1)将多根经轴依次进行编号为1、2、3、
……
、n,获取编号为i的经轴上经纱的初始
圈数mi和总长l、以及所有经轴的半径r0;
9.2)设编号为i的经轴上每层经纱厚度为δri,则δri=(l-2πr0mi)/πm
i2
;
10.3)设定经轴退绕圈数检测周期γ
t
,统计每个检测周期末经轴退绕总圈数并进行记录存储;记系统时刻为t,将经轴开始退绕的时刻记为t=0,每过γ
t
时间t的取值增加1,系统记录一次检测到的经轴退绕圈数,记为
11.4)设定制动力控制参量δs,制动力控制参量表示每次调节浆纱机经轴架制动力控制模块的制动力最小步长;
12.5)设定制动力控制周期δt,制动力控制周期表示系统对浆纱机经轴架制动力控制模块输出调节命令的周期,δt是γ
t
的整数倍且倍数大于3;从经轴开始退绕的时刻t=0时开始,每经过一个制动力控制周期δt的时间,执行一次步骤6)-10);
13.6)记当前时刻为td,对于编号为i=1,2,3,
…
,n的所有经轴,计算它们在到当前时刻td为止的所有时刻t=0,1,2,3,
…
,td时退绕至第圈时经轴i的剩余长度
[0014][0015]
其中,表示t时刻经轴上剩余经纱的圈数,wi(t)在浆纱生产中随时刻t增加而减小;
[0016]
7)对于编号为i=1,2,3,
…
,n的所有经轴,计算它们在到当前时刻td为止的所有时刻t=0,1,2,3,
…
,td时的剩余经纱长度偏差率σi(wi(t)):
[0017][0018]
其中:
[0019]
8)以经轴上剩余经纱的圈数wi(t)为自变量,根据各经轴各时刻的剩余经纱长度偏差率σi(wi(t)),计算它们在当前时刻td的剩余经纱长度偏差率梯度
[0020][0021][0022][0023]
其中δw
t,i
(td)为第i个经轴在当前时刻td的剩余长度偏差率的梯度的圈数计算窗口,其取值方法如下:
[0024]
δw
t,i
(td)=2π(r0+wi(td)δri)/δl
t
[0025]
δl
t
为梯度计算的长度窗口,依据经验取值,取值区间为[0.01,50]m;
[0026]
9)以经轴上剩余经纱的圈数wi(t)为自变量,根据各经轴各时刻的剩余经纱长度偏差率σi(wi(t)),计算它们在当前时刻td的剩余经纱长度偏差累积∑σi(wi(td)):
[0027][0028][0029]
其中δw
l,i
(td)为第i个经轴在当前时刻td的剩余长度偏差率的累积的圈数计算窗口,其取值方法如下:
[0030]
δw
l,i
(td)=2π(r0+wi(td)δri)/δl
l
[0031]
δl
l
为累积计算的长度窗口,依据经验取值,取值区间为[0.01,50]m;
[0032]
10)对于编号为i=1,2,3,
…
,n的所有经轴,在当前时刻td,设定控制量如下:
[0033][0034]
将si(td)的值圆整到δs的整数倍,向编号为i的经轴端部制动器发送控制信号,使制动器的制动力调整si(td)/δs个步长,其中k,t
l
,t
t
为系统控制参量。
[0035]
作为一种优选方案,上述多经轴退绕长度一致性控制方法还包括如下步骤:
[0036]
作为一种优选方案,上述控制方法还包括步骤11):设定控制量上限s
max
和下限-s
min
,当控制量大于s
max
时将控制量调整为s
max
;当控制量小于-s
max
时,将控制量调整为-s
min
。
[0037]
作为一种优选方案,所述梯度计算窗口δw
t
(t)与累积计算窗口δw
l
(t),均随着wi(t)的变化而变化,变化关系为始终满足窗口所对应经纱长度不变,即始终满足反比于2π(r0+wi(t)δri)。
[0038]
作为一种优选方案,在步骤1)中,经轴i上经纱的初始圈数mi通过对经轴i在整经机上卷绕经纱时,采用转数检测模块检测经轴i转动周数获得;步骤4)中,经轴i退绕所转过的圈数是采用转数检测模块对经轴架上的经轴i进行检测获得;转数检测模块为霍尔传感器、磁电传感器、磁阻传感器、编码器中的任意一种。
[0039]
本发明进一步要解决的技术问题是:提供一种互联式高精度浆纱机多经轴退绕长度智能控制装置,以解决目前经纱退绕过程中的张力控制不准确、各经轴退绕不同步、部分经轴退绕时的累计误差得不到消除、生产批次结束时存在大量残余经纱导致资源浪费的技术问题。
[0040]
为解决上述技术问题,本发明采用的技术方案是:浆纱机多经轴退绕长度一致性智能控制装置,包括一个控制模块、一个存储模块、一个用于检测经轴在整经机上转动周数的第一转数检测模块、多个与经轴架上的经轴一一对应的第二转数检测模块、多个与经轴架上的经轴一一对应的制动器以及与制动器一一对应的制动力调节模块,所述控制模块和存储模块通讯连接,第一转数检测模块和第二转数检测模块分别与控制模块电性连接,制动器一一对应地连接在经轴端部并与经轴所在的经轴架固定连接,制动力调节模块与制动器连接,调节制动器的制动力大小,制动力调节模块还与控制模块连接,受控于制动力调节模块。
[0041]
作为一种优选方案,第一转数检测模块为编码器,第一转数检测模块通过支架固定连接在整经机机头一端,第一转数检测模块与位于整经机上的经轴传动连接,检测经轴
在整经机上转动的周数并发送给控制模块。
[0042]
作为一种优选方案,第二转数检测模块也为编码器,任一第二转数检测模块通过支架固定连接在经轴架一端且与对应的经轴传动连接,检测经轴在经轴架上退绕的周数并发送给控制模块。
[0043]
作为一种优选方案,所述制动器为液压式制动器,制动力调节模块为连接在液压油路上的比例泵。
[0044]
本发明的有益效果是:本发明通过对退绕过程中各经轴上的经纱余量进行实时的监控,及时根据各经轴上的经纱余量偏差对经轴的制动力进行调整,使各经轴上的经纱余量偏差率在一个很小的范围内波动,这样就能够控制各经轴上经纱的退绕量保持基本一致,实现同步退绕的目标,也解决了退绕过程中各经纱张力控制不准确的问题。由于在退绕过程中不断地对经轴的制动力进行调节,因此,在生产过程中,任一经轴在一个调节周期内产生的累计误差,会在下一个或下几个周期内得到修正,也就避免了累计误差的不断扩大,避免了生产批次结束时存在大量残余经纱导致资源浪费这一问题的发生。
附图说明
[0045]
下面结合附图对本发明的具体实施方式作进一步详细说明,其中:
[0046]
图1是本发明的控制原理图;
[0047]
图2是第一转数检测模块的工作状态示意图;
[0048]
图3是第二转数检测模块的工作状态示意图;
[0049]
图1~图3中:1、控制模块,2、存储模块,3.经轴,4.第一转数检测模块,5、经轴架,6、第二转数检测模块,7、制动器,8、制动力调节模块,9、整经机机头,10、制动轮。
具体实施方式
[0050]
下面结合附图,详细描述本发明的具体实施方案。
[0051]
实施例1:
[0052]
参考图1~图3,本实施例以配置有6个经轴的浆纱系统为例,具体描述互联式高精度浆纱机多经轴退绕长度智能控制方法,该方法包括如下具体步骤:
[0053]
1)将六个经轴3进行编号,编号以“i”表示,i分别为[1,2,3,4,5,6]。通过整经机记录下的数据可知,每个经轴3上的绕纱总长l均为8000m,整经时经轴转过的圈数mi分别为[5160,5092,5000,5202,4986,5070]。整经时经轴3转过的圈数mi可通过对整经机机头9用于驱动经轴3转动的驱动电机的转动周数以及驱动电机与经轴3的传动比计算获得,也可以采用图1和图2中所示的第一转数检测模块4获得。第一转数检测模块4可采用霍尔传感器、磁电传感器、磁阻传感器、编码器中的任意一种。霍尔传感器、磁电传感器、磁阻传感器、编码器均为常用的计数传感器。
[0054]
2)已知经轴3半径r0为0.15m,则每层经纱厚度通过如下公式计算:
[0055]
δri=(l-2πr0mi)/πm
i2
[0056]
得δri的取值分别为[3.75,3.93,4.19,3.64,4.23,3.99]
×
10-5
m。通常同一批次经轴3的半径均一致,因此,本步骤中的半径r0即表示所有经轴3的半径。
[0057]
3)设定经轴3退绕圈数检测周期γ
t
,本实施例中γ
t
取值为1s。统计每个检测周期
末经轴3退绕总圈数并进行记录存储;记系统时刻为t,将经轴3开始退绕的时刻记为t=0,每过γ
t
时间t的取值增加1,系统记录一次检测到的经轴退绕圈数,记为
[0058]
4)设定制动力控制参量δs,本实施例中为制动力气压阀或比例阀的气压,取值为0.1kpa。制动力控制参量表示每次调节浆纱机经轴架制动力控制模块的制动力最小步长。
[0059]
5)设定制动力控制周期δt,δt是γ
t
的整数倍且倍数大于3,本实施例中δt取值为10s。记在经轴3上机完毕开始浆纱生产的时刻为t=0,此后每δt时间执行一次以下步骤6)-10)的运算与控制操作。制动力控制周期表示系统对浆纱机经轴架制动力控制模块输出调节命令的周期。
[0060]
6)记当前时刻为td,对于编号为i=1,2,3,
…
,6的所有经轴,计算它们在到当前时刻td为止的所有时刻t=0,1,2,3,
…
,td时退绕至第圈时的剩余长度
[0061][0062]
其中,表示t时刻经轴剩余圈数,在浆纱生产中随时刻t增加而减小。
[0063]
以td=600时的数据为例(本实施例中退绕圈数检测周期γ
t
为1s,因此td=600即为从经轴开始退绕后的第600s时),此时各经轴3的退绕圈数分别为[470.64,459.06,467.32,483.68,450.22,484.49],则各经轴3上的经纱剩余圈数wi(600)分别为[4689.36,4632.94,4532.68,4718.32,4535.78,4585.51],他们退绕至第圈时的剩余长度经计算可得为[7010.31,7016.22,6973.74,6994.96,7006.49,6957.07]。
[0064]
采用相同的方法,可以求得各经轴在t=599,598,597,...,591时的取值。由于δt取值为10s,γt取值为1s,故在t=600,590,580,570,
…
,10时对经轴的制动器控制力进行调整,经轴3退绕过程中每一个退绕圈数检测周期γ
t
都会检测经轴3的退绕圈数并根据上述公式计算出对应的wi(t)、因此t=600,599,598,
…
,10时的取值均得到计算并记录。
[0065]
7)对于编号为i=1,2,3,
…
,6的所有经轴,计算它们在到当前时刻td为止的所有时刻t=0,1,2,3,
…
,td时的剩余长度偏差率σi(wi(td)):
[0066][0067][0068]
8)以经轴上剩余经纱的圈数wi(t)为自变量,计算在当前时刻td各经轴3上的剩余经纱长度偏差率的梯度
[0069]
[0070][0071][0072]
其中δw
t,i
(td)为第i个经轴的剩余长度偏差率的梯度在当前时刻td的圈数计算窗口,其取值方法如下:
[0073]
δw
t,i
(td)=2π(r0+wi(td)δri)/δl
t
[0074]
δl
t
为梯度计算的长度窗口,依据经验取值,取值区间为[0.01,50]m。
[0075]
9)以经轴上剩余经纱的圈数wi(t)为自变量,计算在当前时刻td各经轴3上的剩余长度偏差率的累积∑σi(wi(td)),
[0076][0077][0078]
其中δw
l,i
(td)为第i个经轴在当前时刻td的剩余长度偏差率的累积的圈数计算窗口,其取值方法如下:
[0079]
δw
l,i
(td)=2π(r0+wi(td)δri)/δl
l
[0080]
δl
l
为累积计算的长度窗口,依据经验取值,取值区间为[0.01,50]m。
[0081]
以td=600时的数据为例,此时各经轴3平均剩余长度可计算得到为6993.13m,由此可计算得到各经轴的剩余长度偏差率σi(wi(600))为[0.246%,0.330%,-0.277%,0.026%,0.191%,-0.516%]。
[0082]
以i=4的经轴为例,在t=580,581,582,
…
,600时,w4(t)、σ4(w4(t))的取值如表1所示。
[0083]
本实施例中将梯度计算的长度窗口δl
t
设定为0.5m,依据此时的δri为[3.75,3.93,4.19,3.64,4.23,3.99]
×
10-5
m,r0为0.15m,则可求出δw
t,i
(600)为[4.09,4.17,4.27,4.05,4.29,4.18]。代入式4.27,4.05,4.29,4.18]。代入式则绝对值内值计算结果如表1,可得k1取值为592,k2取值为596。由此代入的计算公式,得到此时的取值为3.6585
×
10-5
。
[0084]
将累积计算的长度窗口δl
l
设定为0.5m,依据此时的δri为[3.75,3.93,4.19,3.64,4.23,3.99]
×
10-5
m,r0为0.15m,则可求出δw
l,i
(600)为[4.09,4.17,4.27,4.05,4.29,4.18]。带入式则绝对值内计算结果如表1,可得k取值为592。由此代入∑σi(wi(td))的计算公式,得到此时∑σ4(w4(600))的取值为0.0102。
[0085]
在本实施例中对表1的数据进行了省略,由于t的取值为从第0到第600的数据量太大,因此根据实际的k、k1和k2的取值,保留了总共21条数据信息,省略的数据信息不会影响本发明技术方案的清楚表达。
[0086]
表1:
[0087][0088]
[0089]
类似地,可以计算出td时刻其余经轴的∑σi(wi(td))。
[0090]
10)对于编号为i=1,2,3,
…
,n的所有经轴,在当前时刻td,为保证所有经轴的剩余长度一致性最高,设定控制量如下:
[0091][0092]
并圆整到δs的整数倍,其中k,t
l
,t
t
为系统控制参量,取值范围均为[0,105];在本实施例中,k取值为100,t
l
取值为10,t
t
取值为100,为保证不出现突变性张力变化,设定控制量上限s
max
和控制量下限-s
max
,当控制量大于s
max
时将控制量调整为s
max
,当控制量小于-s
max
时将控制量调整为-s
max
。本实施例中控制量上限s
max
为15kpa,控制量下限-s
max
为-15kpa。
[0093]
以td=600时的数据为例,以i=4的经轴为例,s4(600)的值为10.8119,则制动器7的制动力需要调整的步长为s4(600)/δs=108.119,采用四舍五入圆整到δs的整数倍为108,在控制量上限与下限的范围内,则在编号i为4的经轴3退绕至第600s时,控制模块1向制动力调节模块8发送信号,通过制动力调节模块8提高制动器7的制动力108个最小步长,即提高制动器7的制动力10.8kpa。
[0094]
采用相同方法,能够得到所有织轴的控制量si(td),并依照上述方式对各经轴的制动力进行调节。最终,本实施例采用本方法,有效地将各经轴3的余纱量控制在30m以下,有效降低了纱线损耗,同时保障了经纱退绕过程中各纱线之间的张力均衡性。
[0095]
实施例2:
[0096]
如图1~图3所示是用于实施上述实施例1所述方法的互联式高精度浆纱机多经轴退绕长度智能控制装置,包括一个控制模块1、一个存储模块2、一个用于检测经轴3在整经机上转动周数的第一转数检测模块4、六个与经轴架5上的经轴3一一对应的第二转数检测模块6、六个与经轴架5上的经轴3一一对应的制动器7以及与制动器7一一对应的制动力调节模块8,所述控制模块1和存储模块2通讯连接,第一转数检测模块4和第二转数检测模块6分别与控制模块1电性连接,制动器7一一对应地连接在经轴3端部并与经轴3所在的经轴架5固定连接,制动力调节模块8与制动器7连接,调节制动器7的制动力大小,制动力调节模块8还与控制模块1连接,受控于控制模块1。图1中只体现了各模块之间的相互关系,各模块的数量根据实际情况增减。本实施例中的控制模块1是单片机或工控机,优选工控机。
[0097]
如图2所示,本实施例中,第一转数检测模块4为磁电传感器,第一转数检测模块4固定连接在整经机机头9一端,检测经轴3在整经机上转动的周数并发送给控制模块1,经控制模块1处理后保存在存储模块2中。实际生产中,第一转数检测模块4也可使用霍尔传感器或磁阻传感器。
[0098]
如图3所示,本实施例中,第二转数检测模块6也为磁电传感器,任一第二转数检测模块6固定连接在经轴架5一端,检测经轴3在经轴架5上退绕的周数并发送给控制模块1,经控制模块1处理后保存在存储模块2中。实际生产中,第一转数检测模块4也可使用霍尔传感器或磁阻传感器。图3仅展示了一个经轴3的工作状态示意图,其他经轴3的工作状态与图3所示的一致。
[0099]
磁电传感器属于常规的感应计数器,其使用方法是本领域的公知常识,通常是将一个感应装置固定安装,将磁铁安装在活动部件上,在本实施例中,可以将磁铁安装在经轴3的盘片外侧,将感应装置安装在经轴架5上,在经轴3转动的时候,磁铁与感应装置交会时,
感应装置就能产生信号并发送给控制模块1,为了提高检测精度,可在经轴3的盘片外侧周向均布多个磁铁,或者在经轴架5上设置多个感应装置。
[0100]
磁电传感器在整经机机头9上的安装方式与磁电传感器在经轴架5上的安装方式类似。
[0101]
本实施例中的制动器7为液压式制动器,制动力调节模块8为连接在液压油路上的气压阀或比例阀,经轴3的轴头上固定套接有一个制动轮10,制动器7套接在制动轮外围,制动力调节模块8可调节制动器7施加在制动轮上的摩擦力,即摩擦力。
[0102]
本实施例中,经轴3与制动器7的连接方式属于本领域常规技术,可参考专利号为“202022650403.4”的实用新型专利中公开的经轴制动结构。
[0103]
本发明的工作过程如实施例1所述,此处不再赘述。
[0104]
上述实施例仅例示性说明本发明创造的原理及其功效,以及部分运用的实施例,而非用于限制本发明;应当指出,对于本领域的普通技术人员来说,在不脱离本发明创造构思的前提下,还可以做出若干变形和改进,这些都属于本发明的保护范围。