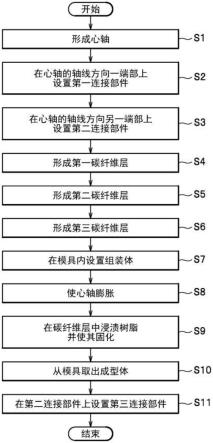
1.本发明涉及一种用作例如车辆的传动轴的纤维增强树脂制管体(fiber reinforced resin pipe body)的制造方法。
背景技术:2.安装在车辆上的传动轴(propeller shaft)具有沿车辆的前后方向延伸的管体,通过该管体将由原动机产生并由变速器减速的动力传递至最终减速装置。作为用于这种传动轴的管体,有一种利用心轴(mandrel)制成的纤维增强塑料制的管体(参照专利文献1)。
3.相对于此,在专利文献2中记载了一种在心轴上缠绕材料的方法,通过长丝缠绕法(filament winding method)在心轴上缠绕浸渍有树脂的纤维体,并通过蒸压处理(autoclaving)使浸渍有树脂的纤维体固化。另外,在专利文献3中记载了在将未浸渍树脂的纤维体缠绕于心轴之后,在模具(mould)内使树脂浸渍于纤维体。[现有技术文献][专利文献]
[0004]
专利文献1:日本发明专利公开公报特开平3-265738号专利文献2:日本发明专利公开公报特开2003-127257号专利文献3:日本发明专利公开公报特开平8-323870号
技术实现要素:[发明所要解决的技术问题]
[0005]
在专利文献3所记载的技术中,纤维体有可能会嵌入模具当中。相对于此,若为了防止纤维体嵌入模具而想要确保模具内的间隙(clearance),则被供给到纤维体的树脂的量会增加一个所述间隙的量,从而作为成品的管体的重量有可能会增加。
[0006]
本发明是为了解决这样的问题而做出的,其技术问题在于,提供一种能够确保模具内的间隙并且抑制管体的重量的纤维增强树脂制管体的制造方法。[用于解决技术问题的技术方案]
[0007]
为了解决所述技术问题,本发明的纤维增强树脂制管体的制造方法的特征在于,包括配置步骤、膨胀步骤和成型步骤,其中,在所述配置步骤中,通过长丝缠绕法将纤维体配置于树脂制的心轴的外周面;在所述配置步骤之后,在所述膨胀步骤中,将配置有所述纤维体的所述心轴设置于模具内,并对配置有所述纤维体的所述心轴的内部进行加压,据此使所述心轴膨胀;在所述膨胀步骤之后,在所述成型步骤中,向所述模具内供给树脂且使所述树脂浸渍于所述纤维体并使浸渍的所述树脂固化,据此成型管体。[发明效果]
[0008]
根据本发明,能够在将配置有纤维体的心轴配置于模具内时确保间隙,从而防止纤维体嵌入模具当中。另外,能够根据模具内的形状适当地设置心轴的膨胀形状,并且能够防止纤维增强树脂制管体的成品的树脂的量增加,从而抑制管体的重量。
附图说明
[0009]
图1是示意地表示本发明的第一实施方式所涉及的纤维增强树脂制管体的剖视图。图2是用于说明本发明的第一实施方式所涉及的纤维增强树脂制管体的制造方法的流程图。图3是用于说明本发明的第一实施方式所涉及的纤维增强树脂制管体的制造方法的心轴形成步骤、第一连接步骤和第二连接步骤的示意剖视图。图4是用于说明本发明的第一实施方式所涉及的纤维增强树脂制管体的制造方法的配置步骤的示意图。图5是用于说明本发明的第一实施方式所涉及的纤维增强树脂制管体的制造方法的配置步骤的示意图。图6是用于说明本发明的第一实施方式所涉及的纤维增强树脂制管体的制造方法的配置步骤的示意图。图7是用于说明本发明的第一实施方式所涉及的纤维增强树脂制管体的制造方法的模具内设置步骤的示意剖视图。图8是用于说明本发明的第一实施方式所涉及的纤维增强树脂制管体的制造方法的膨胀步骤和树脂浸渍步骤的示意剖视图。图9是示意地表示本发明的第二实施方式所涉及的纤维增强树脂制管体的剖视图。图10是用于说明本发明的第二实施方式所涉及的纤维增强树脂制管体的制造方法的流程图。图11是示意地表示本发明的第一变形例所涉及的心轴和纤维体的图。图12是用于说明本发明的第一变形例所涉及的纤维增强树脂制管体的制造方法的心轴形成步骤中所使用的模具的示意剖视图。图13是示意地表示本发明的第二变形例所涉及的纤维增强树脂制管体的剖视图。图14是用于说明本发明的第二变形例所涉及的纤维增强树脂制管体的制造方法所使用的模具的示意剖视图。
具体实施方式
[0010]
以用碳纤维增强塑料来制造作为纤维增强树脂制管体的车辆的传动轴(propeller shaft)的情况为例,参考附图来详细地说明本发明的实施方式。在以下的说明中,针对相同的要素标注相同的附图标记并省略重复的说明。另外,参照的附图为了易于理解而夸张地进行了图示,并未对各部件的形状、尺寸等进行准确地表示。
[0011]
<第一实施方式><管体>如图1所示,本发明的第一实施方式所涉及的纤维增强树脂制管体(以下,简称为“管体”)1a具有心轴10、第一连接部件20、第二连接部件30、第三连接部件40、含树脂纤维层50和树脂层60a。换言之,管体1a由含树脂纤维层50和树脂层60a构成,在该管体1a上连接有第一连接部件20、第二连接部件30和第三连接部件40。另外,心轴10为该管体1a的芯材。
[0012]
<心轴>心轴10为呈筒形状的树脂制部件。在本实施方式中,心轴10作为管体1a的芯材发挥功能。心轴10的材料只要是能够承受含树脂纤维层50的树脂固化时的加热的材料即可。作为心轴10的材料的例子,可列举出pp(聚丙烯树脂)、pet(聚对苯二甲酸乙二醇酯树脂)、smp(形状记忆聚合物)等。心轴10一体地具有轴向中间部的大径部11、形成于轴向一端部的锥形部12及中径部13、形成于轴向另一端部的台阶部14及小径部15。在制造管体1a前的阶段,心轴10的大径部11呈在整个轴向的范围内相同直径的圆筒形状(参照图3)。在制造管体1a后,心轴10的大径部11呈在轴向中间部向径向膨胀的桶形状。即,心轴10的外径随着从轴向中间部朝向轴向两端部而缩小。
[0013]
<第一连接部件>第一连接部件20是以插入心轴10的轴向一端部的方式连接的柱状部件。在本实施方式中,第一连接部件20为金属制的短轴。第一连接部件20从心轴10侧起依次一体地具有大径部21、小径部22和中径部23。大径部21为局部地插入心轴10的中径部13内的部位。小径部22及中径部23为从心轴10露出的部位。形成于大径部21的外周面的外齿轮与形成于心轴10的中径部13的内周面的内齿轮啮合。据此,第一连接部件20相对于心轴10的周向上的移动(旋转)被限制。
[0014]
<第二连接部件>第二连接部件30是以外嵌于心轴10的台阶部14的方式连接的筒状部件。形成于第二连接部件30的内周面的内齿轮与形成于心轴10的台阶部14的外周面的外齿轮啮合。据此,第二连接部件30相对于心轴10的周向上的移动(旋转)被限制。在本实施方式中,第二连接部件30为金属制的套环,通过花键接合被固定于心轴10。第二连接部件30的外径与膨胀前的心轴10的大径部11的外径大致相等。
[0015]
<第三连接部件>第三连接部件40是外嵌于心轴10的小径部并且与第二连接部件30连接的部件。第三连接部件40的轴向一端部与心轴10的台阶部14及小径部15的边界部和第二连接部件30的轴向另一端部抵接。在本实施方式中,第三连接部件40为金属制的短节叉,通过激光焊接与第二连接部件30接合。
[0016]
<含树脂纤维层>含树脂纤维层50设置于心轴10的大径部11、锥形部12及中径部13、第一连接部件20的大径部21以及第二连接部件30的外周面上。含树脂纤维层50从径向内侧(心轴10侧)起依次具有第一碳纤维层51(参照图4)、第二碳纤维层52(参照图5)和第三碳纤维层53(参照图6)作为碳纤维层。此外,在图4~图6中,仅图示出了各碳纤维层51、52、53的一部分。另外,第一连接部件20的大径部21的轴向一端部(第一连接部件20的轴向上的位于心轴10的相反侧的端部)的外周面及第二连接部件30的轴向另一端部(第二连接部件30的轴向上的位于心轴10的相反侧的端部)的外周面未被含树脂纤维层50覆盖而从该含树脂纤维层50露出。
[0017]
《第一碳纤维层》如图4所示,第一碳纤维层51由以覆盖心轴10的方式设置于该心轴10等的外周面的多条碳纤维构成。第一碳纤维层51中的碳纤维与心轴10的轴线方向平行地延伸设置。即,关于第一碳纤维层51,碳纤维相对于心轴10的轴线x的定向角度为0
°
。
[0018]
《第二碳纤维层》如图5所示,第二碳纤维层52被设置于第一碳纤维层51的径向外侧,由以覆盖第一碳纤维层51的方式设置的多条碳纤维构成。第二碳纤维层52中的碳纤维以相对于心轴10的轴线方向倾斜45
°
的方式卷绕1周以上,且相对于心轴10的轴线方向呈螺旋状延伸设置。即,关于第二碳纤维层52,碳纤维相对于心轴10的轴线x的定向角度在心轴10膨胀前为45
°
。
[0019]
《第三碳纤维层》如图6所示,第三碳纤维层53被设置于第二碳纤维层52的径向外侧,由以覆盖第二碳纤维层52的方式设置的多条碳纤维构成。第三碳纤维层53中的碳纤维以相对于心轴10的轴线方向倾斜-45
°
的方式卷绕1周以上,且相对于心轴10的轴线方向呈螺旋状延伸设置。即,关于第三碳纤维层53,碳纤维相对于心轴10的轴线x的定向角度在心轴10膨胀前为-45
°
。
[0020]
<树脂层>如图1所示,树脂层60a为设置于第一连接部件20的大径部21的外周面上的环状的层。树脂层60的厚度与含树脂纤维层50的厚度大致相等。树脂层60a覆盖第一连接部件20的大径部21中的从含树脂纤维层50露出的部位而对其进行保护。
[0021]
<管体制造方法>接着,使用图2的流程图来说明第一实施方式所涉及的管体1a的制造方法。
[0022]
首先,如图3所示,通过未图示的成型装置(模具)形成树脂制的心轴10(步骤s1、心轴形成步骤)。接着,在心轴10的轴线方向一端部上设置第一连接部件(短轴)20(步骤s2、第一连接步骤)。接着,在心轴10的轴线方向另一端部上设置第二连接部件(套环)30(步骤s3、第二连接步骤)。在此,步骤s2、s3的顺序能够适当变更,可以先进行步骤s3,也可以同时进行。
[0023]
接着,如图4所示,通过未图示的装置,在心轴10、第一连接部件20的大径部21及第二连接部件30的外周面上形成第一碳纤维层51(步骤s4、第一碳纤维层形成步骤、配置步骤)。接着,如图5所示,通过未图示的装置,在心轴10、第一连接部件20及第二连接部件30上的第一碳纤维层51的外周面上形成第二碳纤维层52(步骤s5、第二碳纤维层形成步骤、配置步骤)。接着,如图6所示,通过未图示的装置,在心轴10、第一连接部件20及第二连接部件30上的第二碳纤维层52的外周面上形成第三碳纤维层53(步骤s6、第三碳纤维层形成步骤、配置步骤)。在步骤s4~s6中,以在第一连接部件20的大径部21及第二连接部件30各自的轴向上的位于心轴10的相反侧的端部上未配置各个纤维的方式形成碳纤维层51~53。
[0024]
在步骤s4~s6中,各碳纤维层51~53为所谓的生丝,而不是浸渍有树脂的纤维。另外,各碳纤维层51~53分别通过多供丝长丝缠绕法而配置于心轴10及第一连接部件20的大径部21的外周面上。通过多供丝长丝缠绕法供丝的各碳纤维层51~53呈现出不相互编织在一起而作为层独立的所谓非卷曲(non-crimp)结构。
[0025]
在此,也可以构成为,在配置步骤s4~s6之前,设置通过流体等对树脂制的心轴10的内部进行加压的工序,在心轴10的内部被加压的状态下执行配置步骤s4~s6。在该情况下,即使在假设树脂制的心轴10的强度低的情况下,也能够防止心轴10由于各碳纤维层51~53设置于该心轴10的外周面时的扭矩而破损。
[0026]
接着,如图7所示,将心轴10、第一连接部件20、第二连接部件30和各碳纤维层51~
53的组装体设置于成型装置(模具)2内(步骤s7)。在此,成型装置(模具)2的内表面呈现出内径在与心轴10的大径部11的轴向中间部对应的部位为最大的形状。即,在闭模状态下,成型装置2具有其内周面的直径比层叠有碳纤维层51~53的层的外径大的部分,成型装置2的内周面具有与设置于该成型装置2内的层叠有碳纤维层51~53的层的外周面分离的部分。据此,能够防止碳纤维层51~53嵌入被分割成多个的模具的抵接面。
[0027]
接着,如图8所示,通过使加热后的流体在被设置于成型装置(模具)2内的组装体的心轴10内流通来对心轴10内进行加压,而使心轴10的大径部11膨胀(步骤s8、膨胀步骤)。心轴10的大径部11被在该心轴10内流通的流体加热而膨胀。另外,第三碳纤维层53与成型装置(模具)2的内周面紧贴。据此,所述组装体以呈现出与成型装置(模具)2的内部形状一致的桶形形状的方式变形。此外,在步骤s7中,能够省略通过流体对心轴10进行的加热。流体向心轴10内的供给和流体从心轴10内的排出通过形成于心轴10的小径部15侧的流体用浇口2a和形成于小径部15的孔部等来进行。
[0028]
此外,在配置步骤s4~s6之前执行对树脂制的心轴10的内部进行加压的工序的情况下,可以在配置步骤s4~s6结束后对心轴10的内部进行减压,并在减压后执行步骤s7、s8(再次加压)。另外,也可以在配置步骤s4~s6结束后执行步骤s7、s8(再次加压)而不对心轴10的内部进行减压。
[0029]
接着,如图8所示,向该成型装置2内供给树脂54而使配置于心轴10的外周面的第一碳纤维层51、第二碳纤维层52和第三碳纤维层53中浸渍树脂54,并通过对成型装置2进行加热而使树脂54固化,形成含树脂纤维层50和树脂层60a(步骤s9、成型步骤)。树脂54例如为热固性树脂。在本实施方式中,成型装置2的模具被分割成多个,在成型步骤中,对所述组装体施加热量,并且在闭合成型装置2的模具的闭模操作后,进一步进行对闭合的模具施加压力的合模操作,据此使模具内的压力上升,从而促进树脂54的固化。此外,在本实施方式中,按照模具被分割成多个的结构进行了说明,因此进行了闭模操作和合模操作,但合模操作未必是必需的。另外,在模具未被分割成多个的情况下,所述闭模操作和合模操作未必是必需的。在成型装置2内,在导入熔融状态的树脂54的浇口2b的出口侧形成有空间(树脂积存部2c)。导入成型装置2内的树脂54储存在位于纤维层51~53的轴向一端部的侧方的该树脂积存部2c。储存在树脂积存部2c的树脂54通过从吸出口2d进行的真空吸出而沿心轴10的轴线方向移动,并浸渍于各碳纤维层51~53,其中,吸出口2d在纤维层51~53的排列方向上形成于浇口2b的相反侧(纤维层51~53的轴向另一端部的外周面侧)。在树脂54浸渍于各碳纤维层51~53的状态下,对成型装置2施加热量并且对成型装置2内施加压力,据此形成含树脂纤维层50,并且在与树脂积存部2c对应的部位上形成树脂层60a。
[0030]
接着,从成型装置2取出成型后的组装体即成型体(步骤s10)。接着,如图1所示,在成型体的位于第二连接部件30的轴向上的与心轴10相反侧的位置且未被含树脂纤维层50覆盖的端部上,通过激光焊接来安装第三连接部件(短节叉)40(步骤s11、第三连接步骤)。
[0031]
本发明的第一实施方式所涉及的管体1a的制造方法包括配置步骤s4~s6、膨胀步骤s8和成型步骤s9,其中,在配置步骤s4~s6中,通过长丝缠绕法将树脂制的纤维体(各碳纤维层51~53)配置于心轴10的外周面;在所述配置步骤s4~s6之后,在所述膨胀步骤s8中,将配置有所述纤维体的所述心轴10设置于模具(成型装置2)内,并对配置有所述纤维体的所述心轴10的内部进行加压,据此使所述心轴10膨胀;在所述膨胀步骤s8之后,在所述成
型步骤s9中,向所述模具内供给树脂54,使所述树脂浸渍于所述纤维体,并使浸渍的所述树脂54固化,据此成型管体1a。根据所述结构,能够在将配置有纤维体的心轴10配置于模具内时确保间隙,从而防止纤维体嵌入模具当中。另外,能够根据模具内的形状适当地调整心轴10的膨胀形状,并且能够防止管体1a的成品的树脂54的量增加,从而抑制管体1a的重量。
[0032]
另外,按照管体1a的制造方法,在所述成型步骤s9之后,所述心轴10作为所述管体1a的芯材而保留。根据所述结构,不需要去除心轴10的作业,并且能够利用心轴10适当地确保管体1a的强度和刚性。
[0033]
另外,管体1a的制造方法在所述配置步骤之前还包括第一连接步骤s1,在所述第一连接步骤s1中,将第一连接部件20连接于所述心轴10的一端部,在所述配置步骤s4~s6中,还将所述纤维体配置于所述第一连接部件20的外周面。根据所述结构,通过执行成型,能够将第一连接部件20与管体1a一体成型,不需要设置在管体1a成型之后将第一连接部件20压入的工序,能够削减制造工时。另外,能够利用浸渍有树脂54的纤维层(含树脂纤维层50)增强第一连接部件20的连接。
[0034]
另外,在管体1a的制造方法中,所述模具(成型装置2)在所述心轴10和所述第一连接部件20的连接部位具有储存注入到该模具内的所述树脂54的空间(树脂积存部2c),在所述成型步骤s9中,通过吸出储存于所述空间的所述树脂54来使其浸渍于所述纤维体。根据所述结构,能够使树脂54适当地浸渍于纤维体之间,并且能够利用储存有树脂54的空间而适当地形成树脂层60a。
[0035]
另外,在管体1a的制造方法中,在所述配置步骤s4~s6中,通过多供丝长丝缠绕法来配置所述纤维体。在纤维体呈现出卷曲结构的情况下,纤维体相互编织在一起的部位上的厚度增加。相对于此,根据所述结构,由于能够使多个纤维层51~53为所谓的非卷曲结构(non-crimp structure),因此能够使所配置的纤维体不阻碍心轴10的膨胀而适当地跟随心轴10。另外,通过设为非卷曲结构,能够抑制含树脂纤维层50的厚度并且降低形状的不均匀性,减少局部应力。另外,通过设为非卷曲结构,能够使纤维体之间的隙间均匀化,从而使树脂54适当地浸渍于纤维体之间。
[0036]
另外,管体1a的制造方法在所述配置步骤s4~s6之前还包括第二连接步骤s3,在所述第二连接步骤s3中,将第二连接部件30连接于所述心轴10的另一端部,在所述配置步骤s4~s6中,还将所述纤维体配置于所述第二连接部件30的外周面。根据所述结构,通过执行成型,能够将第二连接部件30与管体1a一体成型,不需要设置在管体1a成型之后将第二连接部件30压入的工序,能够削减制造工时。另外,能够利用浸渍有树脂54的纤维层(含树脂纤维层50)增强第二连接部件30的连接。
[0037]
另外,在管体1a的制造方法中,在所述膨胀步骤s8中,通过使流体在所述心轴10的内部流通来对该心轴10的内部进行加压,并通过所述流体的热量来加热所述心轴10和所述纤维体。根据所述结构,在成型步骤中能够适当地促进树脂54的加热。
[0038]
<第二实施方式>接着,以与第一实施方式所涉及的管体1a和管体1a的制造方法的不同点为中心来
说明第二实施方式所涉及的管体和管体的制造方法。
[0039]
如图9所示,本发明的第二实施方式所涉及的管体1b具有树脂环70和树脂层60b来代替树脂层60a。换言之,管体1b由含树脂纤维层50、树脂层60b和树脂环70构成,在该管体1b上连接有第一连接部件20、第二连接部件30和第三连接部件40。另外,心轴10为该管体1b的芯材。
[0040]
<树脂环和树脂层>树脂环70为外嵌于第一连接部件20的大径部21的外周面上的环状部件。树脂环70为在与树脂54相同的材料内含有增强用纤维(例如,不连续的碳纤维等)的纤维增强树脂制环。树脂环70的轴向端部与含树脂纤维层50的轴向一端部抵接。树脂环70的内径与第一连接部件20的大径部21的外径大致相等,树脂环70的外径比含树脂纤维层50的外径小。
[0041]
树脂层60b被设置于树脂环70的外周面上。树脂层60b为环状的层。树脂层60b的外径与含树脂纤维层50抵接于树脂环70及树脂层60b的端部的外径大致相等。
[0042]
树脂环70和树脂层60b覆盖第一连接部件20的大径部21中的从含树脂纤维层50露出的部位而对其进行保护。
[0043]
<管体制造方法>接着,使用图10的流程图来说明第二实施方式所涉及的管体1b的制造方法。
[0044]
在步骤s6和步骤s7之间,将树脂环70外嵌于第一连接部件20的大径部21中的从各碳纤维层51~53露出的部位(步骤s6b、外嵌步骤)。在步骤s9中,树脂层60b以覆盖树脂环70的外周面的方式形成。
[0045]
本发明的第二实施方式所涉及的管体1b具有树脂制的心轴10、第一连接部件20、纤维体、树脂环70和树脂60b,其中,所述第一连接部件20被连接于所述心轴10的一端部;所述纤维体被配置于所述心轴10和所述第一连接部件20的外周面;所述树脂环70被设置于从所述纤维体露出的所述第一连接部件20的外周面,且含有所述纤维体;所述树脂60b浸渍于在所述心轴10和所述第一连接部件20的外周面上配置的所述纤维体,并且在所述树脂环70的外周面上形成层。根据所述结构,能够通过树脂环70缓和含树脂纤维层50和树脂层60b的成型收缩率之差,防止含树脂纤维层50与树脂层60b之间产生裂纹。
[0046]
<第三实施方式>接着,以与第一实施方式和第二实施方式的不同点为中心来说明本发明的第三实施方式所涉及的管体制造方法。
[0047]
在第三实施方式中,至少在执行步骤s3~s10的期间,心轴10维持其轴线方向为上下方向的状态(所谓立式状态)。根据所述结构,即使在纤维体(尤其是配置于最外侧的第三碳纤维层53)的定向角度小的情况下也能够适当地抑制纤维体的偏移。
[0048]
<第一变形例>如图11所示,对于本发明的第一变形例所涉及的管体1x而言,在步骤s1中,在心轴10x的大径部11的外周面上形成多个凸部11a。具有所述凸部11a的心轴10x是使用制造树脂制的该心轴10x时的成型装置(模具)3内的形状形成的。即,在步骤s1中所使用的成型装置3的内周面上形成有与凸部11a对应的多个凹部3a(参照图12)。凸部11a的高度优选为,在3层碳纤维层51~53的合计高度以下且在至3层碳纤维层51~53中的最外侧的碳纤维层53的径
向中心为止的合计高度以上。所述心轴10x的凸部11a能够防止各碳纤维层51~53的位置偏移。即,具有凸部11a的心轴10x在步骤s4~s6中能够以准确的定向角度配置各碳纤维层51~53,即使在该心轴10x膨胀之后,也能够将各碳纤维层51~53的定向角度维持在适当的角度。
[0049]
本发明的第一变形例所涉及的管体的制造方法在所述配置步骤s4~s6之前还包括心轴形成步骤,在所述心轴形成步骤中,通过使用在内表面设置有凹部3a的模具(成型装置3)形成在外周面具有与所述凹部3a对应的凸部11a的所述心轴10x。根据所述结构,在心轴10x膨胀之后,能够将纤维体的定向角度维持在适当的角度。
[0050]
<第二变形例>如图13所示,在本发明的第二变形例所涉及的管体1y中,心轴10的大径部11和设置于该大径部11的外周面上的含树脂纤维层50呈圆筒形状而不是桶形状。如图14所示,用于制造管体1y的成型装置(模具)2y的内表面呈比碳纤维层51~53的外径大的圆筒形状。
[0051]
以上,说明了本发明的实施方式,但本发明并不限定于所述实施方式,在不脱离本发明的主旨的范围内能够适当变形。例如,也可以为在步骤s9、s10的期间将心轴10从成型后的含树脂纤维层50抽出的结构。另外,也可以为心轴10被步骤s8中的流体的热量和/或步骤s9中的树脂54、成型装置(模具)2的热量熔融而去除的结构。也能够通过其他的热量、电气、振动等的能量将心轴10熔融去除。另外,可以在步骤s8中使非加热状态的流体在心轴10内流通,在执行步骤s9的过程中使加热状态的流体在心轴10内流通。另外,各碳纤维层51~53也可以呈现出彼此编织在一起的所谓卷曲结构。另外,纤维体不限定于碳纤维,只要是能够增强树脂层的纤维部件(例如,玻璃纤维、纤维素纤维等)即可。[附图标记说明]
[0052]
1a、1b、1y:管体(纤维增强树脂制管体);2、3:成型装置(模具、mould);2c:树脂积存部(空间);3a:凹部;10、10x:心轴;20:第一连接部件;30:第二连接部件;50:含树脂纤维层;51:第一碳纤维层;52:第二碳纤维层;53:第三碳纤维层;54:树脂;60a、60b:树脂层;70:树脂环。