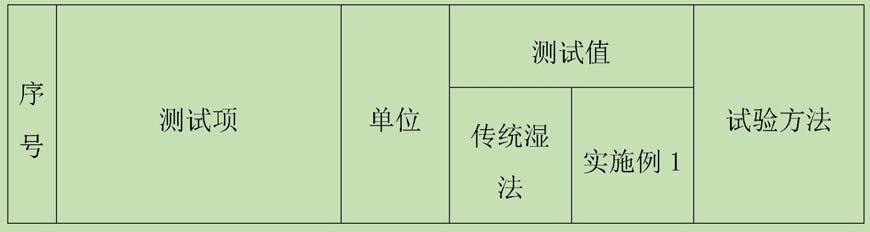
1.本发明涉及预浸料制造技术领域,具体而言,涉及一种干法制备纤维增强热固性复合材料预浸料的工艺。
背景技术:2.纤维增强复合材料由于具有质量轻、强度高、抗疲劳性能好、耐腐蚀性好、加工成型简便等优点,并具有材料可设计性强及特殊功能性如屏蔽电磁波、消音等特点,现已成为国民经济、国防建设和科技发展中无法替代的重要材料,是目前应用最广的复合材料之一。
3.纤维增强热固性复合材料产品,如环氧树脂玻璃纤维层压板、管、棒,碳纤维板、管、棒等制备半成品(即预浸料)过程中,传统工艺大都采用纤维浸渍溶剂胶后再烘干的工艺或者热熔胶涂布工艺。
4.纤维浸渍溶剂胶法由于设备简单,通用性大等特点,被广泛使用,导致每年消耗、排放大量的有机溶剂,如甲苯、丙酮和酒精等,这些易燃易爆的溶剂不仅污染了环境,对人体健康造成危害,还提高了运输企业和使用单位的管理成本,给生产企业和社会造成了极大的安全隐患。此外,由于该法制备的预浸料中往往会残留少量高沸点挥发物,就使得最终制品的某些性能如玻璃化转变温度等热态指标满足不了更高更严苛的使用要求。
5.因此,热熔法预浸料工艺煮布引起挥发分含量低、环保和无污染问题成为了当前预浸料的发展方想。但目前的传统热熔胶涂布工艺通常先将基体树脂在胶膜机上成膜,然后将胶膜与基体纤维编织布在热熔预浸机上进行复合预浸,通过胶膜厚度的调整来控制预浸料树脂的含量,但其具有成本高、生产工艺复杂和预浸料中树脂含量控制不精确的问题。
6.综上,研究出一种环保、简单、树脂含量易于控制且制品性能好的纤维增强复合材料预浸料的工艺是本领域技术人员长期以来的工作方向。
技术实现要素:7.本发明的目的在于提供一种干法制备纤维增强热固性复合材料预浸料的工艺,此工艺具有工艺简单、成本低、稳定性高和制品性能优异等优点。
8.本发明解决其技术问题是采用以下技术方案来实现的。
9.一种干法制备纤维增强热固性复合材料预浸料的工艺,具体包括以下步骤:
10.混合:将微米级的热固性树脂粉与微米级的固化剂和促进剂混合均匀,得热固性树脂混合粉料。
11.撒粉:将热固性树脂混合粉料均匀撒在基材表面。
12.加热:基材通过传送带进入加热烘道,混合树脂粉料在高于其熔融温度的加热段被熔化并渗透到基材中。
13.冷却:降低温度使混合树脂料冷却至软化温度以下,然后进行裁切或收卷,制得预浸料。
14.预浸料使用:预浸料铺层压制或卷制,制备成纤维增强热固性复合材料层压板、管
和棒。
15.在本发明的一些实施例中,上述混合步骤中的热固性树脂粉为环氧树脂、酚醛树脂、氰酸酯、苯并噁嗪和聚酰亚胺中的一种或多种固体树脂,树脂粉的粒度≤0.1mm。
16.在本发明的一些实施例中,上述混合步骤中的固化剂为酚醛树脂、二氨基二苯砜、双氰胺、咪唑和三氟化硼
‑
胺络合物中的一种或多种,固化剂粒度≤0.1mm。
17.在本发明的一些实施例中,上述混合步骤中的促进剂为咪唑、聚脲、三氟化硼
‑
胺络合物和六次甲基四胺中的一种或多种,促进剂粒度≤0.1mm。
18.在本发明的一些实施例中,上述撒粉步骤中的基材为玻璃纤维布、芳纶纤维布、棉布、碳纤维布和云母纸中的一种或多种。
19.在本发明的一些实施例中,上述混合步骤中的混合采用混粉机混合,撒粉采用撒粉机撒粉。
20.在本发明的一些实施例中,上述加热步骤中的加热温度为高于树脂熔融温度20℃~50℃,加热时间为3~20min。
21.在本发明的一些实施例中,上述冷却步骤中的冷却温度为低于树脂软化点温度30℃~45℃,冷却时间为5~30s。
22.在本发明的一些实施例中,上述混合粉料与基材的比例范围为1:(1~3)。
23.在本发明的一些实施例中,上述热固性树脂粉与固化剂、促进剂的加入质量比为100:(10~35):(0.5~1)。
24.相对于现有技术,本发明的实施例至少具有如下优点或有益效果:
25.1)本发明采用可控制含量的微粉级混合粉末制备热固性预浸料,从根本上解决了传统湿法预浸料制备过程中挥发物含量难以控制的难题;整个工艺过程不加入其他有机溶剂,从根本上解决了湿法预浸料当中的残留的挥发物对复合材料板、管和棒制品强度的影响,尤其是对热态强度的影响;并且解决了传统湿法预浸料制备过程中溶剂的挥发对空气造成的污染;从根本上规避了危险化学溶剂在运输、储存和使用带来的管理成本和管理风险。
26.2)本发明研究发现,干法制备的热固性预浸料,由于其不含高沸点溶剂残留,使得常温下的储存期明显长于传统溶剂法制备的预浸料。不仅如此,干法预浸料制备的板材、管材和棒,其热稳定性和湿热稳定性等明显优于溶剂法预浸料制备的板材、管和棒。
27.3)本发明相比传统工艺,因撒粉、加热、冷却等过程中均由传送带输送前行,整个预浸料制备过程中基材受到的张力较小,故对基材的抗拉强度要求不高,所以基材的选择范围更广泛。
附图说明
28.为了更清楚地说明本发明实施例的技术方案,下面将对实施例中所需要使用的附图作简单地介绍,应当理解,以下附图仅示出了本发明的某些实施例,因此不应被看作是对范围的限定,对于本领域普通技术人员来讲,在不付出创造性劳动的前提下,还可以根据这些附图获得其他相关的附图。
29.图1为本发明实施例中混合步骤采用的混粉机;
30.图2为本发明实施例中撒粉步骤;
31.图3为本发明实施例中的加热步骤;
32.图4为本发明实施例中的冷却步骤;
33.图5为产品实例1中制备的环氧玻璃布板;
34.图6为产品实例2中制备的环氧玻璃布管。
具体实施方式
35.为使本发明实施例的目的、技术方案和优点更加清楚,下面将对本发明实施例中的技术方案进行清楚、完整地描述。实施例中未注明具体条件者,按照常规条件或制造商建议的条件进行。所用试剂或仪器未注明生产厂商者,均为可以通过市售购买获得的常规产品。
36.需要说明的是,在不冲突的情况下,本申请中的实施例及实施例中的特征可以相互组合。下面将参考具体实施例来详细说明本发明。
37.一种干法制备纤维增强热固性复合材料预浸料的工艺,具体包括以下步骤:
38.混合:将微米级的热固性树脂粉与微米级的固化剂和促进剂在混粉机中混合均匀,得到热固性树脂混合粉料。
39.所述热固性树脂粉为环氧树脂、酚醛树脂、氰酸酯、苯并噁嗪和聚酰亚胺中的一种或多种固体树脂,树脂粉的粒度≤0.1mm,树脂粉的粒度越小的话,一方面对质量越可控,另一方面越容易融入基材纤维缝隙。
40.固化剂为酚醛树脂、二氨基二苯砜、双氰胺、咪唑和三氟化硼
‑
胺络合物中的一种或多种,固化剂粒度≤0.1mm。
41.所述促进剂为咪唑、聚脲、三氟化硼
‑
胺络合物和六次甲基四胺中的一种或多种,促进剂粒度≤0.1mm。
42.所述热固性树脂粉与固化剂、促进剂的加入质量比为100:(10~35):(0.5~1)。
43.撒粉:将热固性树脂混合粉料采用撒粉机均匀撒在基材表面,所述基材为玻璃纤维布、芳纶纤维布、棉布、碳纤维布或云母纸。
44.加热:基材通过传送带进入加热烘道,混合树脂粉料在高于其熔融温度20℃~50℃的加热段被熔化并渗透到基材中,加热时间为3~20min;微米级的热固性树脂混合粉料更容易融入进基材的纤维缝隙,使之融合更均匀。
45.冷却:降低温度至树脂软化点以下30℃~45℃,使混合树脂料冷却,冷却时间为5~30s,然后进行裁切、收卷,制得预浸料,本发明中混合粉料与基材的比例范围为1:(1~3)。
46.预浸料使用:预浸料铺层压制或卷制,制备成纤维增强热固性复合材料层压板、管和棒。
47.以下结合实施例对本发明的特征和性能作进一步的详细描述。
48.实施例1
49.一种干法制备纤维增强热固性复合材料预浸料的工艺,包括以下步骤:
50.混合:将双酚a型固体环氧树脂(牌号:e20)与酚醛树脂(牌号:2123)进行粉碎造粉处理,粉末粒径d98≤0.1mm。将上述两种树脂粉末按重量比e20:2123=3:2称量并混合,得混合树脂,加入促进剂和固化剂,本实施例中的促进剂为六次甲基四胺,促进剂的比例为混
合树脂的1%,本实施例中的固化剂为咪唑,固化剂的比例为混合树脂的25%,将上述原料在混合机中混合均匀,得热固性树脂混合粉料,混粉机如图1所示。
51.撒粉:将热固性树脂混合粉料采用撒粉机机械撒粉均匀地撒在ew
‑
140型无碱玻璃纤维布基材表面,热固性树脂混合粉料与基材的质量比为1:3,撒粉量为80g/
㎡
,其撒粉过程如图2所示。
52.加热:将撒了热固性树脂混合粉料的玻璃纤维布通过145℃~155℃(树脂熔融温度为110℃~115℃,本实施例加热温度高于熔融温度35℃~45℃)的加热烘道,热固性树脂混合粉料熔化并渗透到纤维缝隙,加热时间为10min,其加热熔融过程过程如图3所示。
53.冷却:玻璃纤维布再经过冷却段冷却到50℃(树脂软化温度为80℃,本实施例冷却温度低于软化温度30℃)以下20s,然后进行裁切,裁切过程如图4所示。
54.预浸料使用:将裁切成一定尺寸的干法预浸料按照需求进行铺层,并热压固化制得层压板,本实施例制备的压板如图1所示。
55.将实施例1制备的预浸料及制品与现有传统湿法制备所得的预浸料及制品进行测试对比,其性能对比数据如表1所示。
56.表1.传统湿法和干法制品的性能对比表
[0057][0058][0059]
从表1中可以看出,采用本发明实施例制备所得的热固性预浸料储存期最高可达
传统湿法制备的预浸料储存期的10倍,其玻璃化转变温度更高,垂直层向的弯曲强度、垂直层向击穿电压和浸水后提及电阻率均高于湿法制备的预浸料,性能更好。
[0060]
实施例2
[0061]
一种干法制备纤维增强热固性复合材料预浸料的工艺,包括以下步骤:
[0062]
混合:将固体酚醛环氧树脂(牌号:npcn704(国产))进行粉碎造粉处理,粉末粒径d98≤0.1mm,加入二氨基二苯砜固化剂和三氟化硼
‑
胺络合物促进剂,其中环氧树脂:固化剂:促进剂的重量比为100:30:0.5,在混粉机中进行均匀混合,得热固性树脂混合粉料。
[0063]
撒粉:将热固性树脂混合粉料运用撒粉机机械撒粉均匀地撒在ew
‑
140型无碱玻璃纤维布表面,热固性树脂混合粉料与基材的质量比为1:3,撒粉量为70g/
㎡
。
[0064]
加热:将撒了热固性树脂混合粉料的玻璃纤维布通过155℃~160℃(树脂熔融温度110℃,本实施例加热温度高于熔融温度45℃~50℃)的加热烘道加热5min,热固性树脂混合粉料熔化并渗透到纤维缝隙。
[0065]
冷却:玻璃纤维布再经过冷却段冷却到50℃(树脂软化温度90℃~100℃,低于软化温度40℃以下)以下15s,然后进行收卷。
[0066]
预浸料使用:将得到的预浸布卷进行卷绕,最终固化成管,本实施例制备的环氧玻璃布管如图6所示。
[0067]
实施例3
[0068]
一种干法制备纤维增强热固性复合材料预浸料的工艺,包括以下步骤:
[0069]
混合:将固体环氧树脂、聚酰亚胺树脂进行粉碎造粉处理,得到树脂粉,粉末粒径d98≤0.1mm,本实施例树脂粉中环氧树脂与聚酰亚胺树脂的质量比例为2:0.5,并加入二氨基二苯砜作为固化剂,咪唑作为促进剂,其中树脂粉、固化剂和促进剂的重量比为100:25:1,在混粉机中进行均匀混合,得热固性树脂混合粉料。
[0070]
撒粉:将热固性树脂混合粉料运用撒粉机机械撒粉均匀地撒在芳纶纤维布基材表面,固性树脂混合粉料与芳纶纤维布的质量比为1:2,撒粉量为85g/
㎡
。
[0071]
加热:将撒了热固性树脂混合粉料的芳纶纤维布通过150℃~160℃(树脂熔融温度110℃,本实施例加热温度高于熔融温度40℃~50℃)的加热烘道加热20min,热固性树脂混合粉料熔化并渗透到纤维缝隙。
[0072]
冷却:玻璃纤维布再经过冷却段冷却到65℃(树脂软化温度110℃,本实施例冷却温度低于软化温度45℃)以下20s,然后按照要求进行裁切。
[0073]
预浸料使用:将裁切成一定尺寸的干法预浸料按照需求进行铺层,并热压固化制得层压板。
[0074]
实施例4
[0075]
一种干法制备纤维增强热固性复合材料预浸料的工艺,包括以下步骤:
[0076]
混合:将固体苯并噁嗪、环氧树脂进行混合和粉碎造粉处理,得树脂粉,粉末粒径d98≤0.1mm,本实施例中苯并噁嗪与环氧树脂的质量比为0.2:1,加入同样粒度的双氰胺固化剂,以及聚脲做促进剂,其中树脂粉:固化剂:促进剂的重量比为100:10:0.8,在混粉机中进行均匀混合,得热固性树脂混合粉料。
[0077]
撒粉:将热固性树脂混合粉料运用撒粉机机械撒粉均匀地撒在云母纸基材的表面,固性树脂混合粉料与云母纸的质量比为1:2,撒粉量为60g/
㎡
。
[0078]
加热:将撒了热固性树脂混合粉料的云母纸通过145℃~150℃(树脂熔融温度105℃~110℃,本实施例加热温度高于熔融温度40℃)的加热烘道加热10min,热固性树脂混合粉料熔化并渗透到云母纸上。
[0079]
冷却:玻璃纤维布再经过冷却段冷却到50℃(树脂软化温度95℃,本实施例冷却温度低于软化温度45℃)以下20s,然后进行裁切。
[0080]
预浸料使用:将裁切成一定尺寸的干法预浸料按照需求进行铺层,并热压固化制得云母层压板。
[0081]
实施例5
[0082]
一种干法制备纤维增强热固性复合材料预浸料的工艺,包括以下步骤:
[0083]
混合:将固体氰酸酯树脂、环氧树脂进行混合和粉碎造粉处理,得树脂粉,粉末粒径d98≤0.1mm,本实施例中氰酸酯树脂与环氧树脂的质量比为0.15:1,然后加入同样粒度的二氨基二苯砜固化剂和三氟化硼
‑
胺络合物促进剂,其中树脂粉与固化剂和促进剂的重量比为100:30:0.6,将上述粉末在混粉机中进行均匀混合,得热固性树脂混合粉料。
[0084]
撒粉:将热固性树脂混合粉料运用撒粉机机械撒粉均匀地撒在棉布表面,固性树脂混合粉料与棉布的质量比为1:1,撒粉量为75g/
㎡
。
[0085]
加热:将撒了热固性树脂混合粉料的棉布通过150℃~155℃(树脂熔融温度105℃,本实施例加热温度高于熔融温度45℃~50℃)的加热烘道加热8min,热固性树脂混合粉料熔化并渗透到纤维缝隙。
[0086]
冷却:玻璃纤维布再经过冷却段冷却到50℃(树脂软化温度95℃,本实施例冷却温度低于软化温度45℃)以下20s,然后进行裁切。
[0087]
预浸料使用:将裁切成一定尺寸的干法预浸料按照需求进行铺层,并热压固化制得层压板。
[0088]
实施例6
[0089]
一种干法制备纤维增强热固性复合材料预浸料的工艺,包括以下步骤:
[0090]
混合:将固体氰酸酯树脂、环氧树脂进行粉碎造粉处理,得混合粉,粉末粒径d98≤0.1mm,本实施例中氰酸酯树脂与环氧树脂的质量比为0.25:1,然后加入同样粒度的酚醛树脂做固化剂,咪唑做促进剂,其中树脂粉与固化剂和促进剂的重量比为100:35:0.8,将上述粉末在混粉机中进行均匀混合,得热固性树脂混合粉料。
[0091]
撒粉:将热固性树脂混合粉料运用撒粉机机械撒粉均匀地撒在棉布表面,固性树脂混合粉料与棉布的质量比为1:2。
[0092]
加热:将撒了热固性树脂混合粉料的棉布通过150℃~155℃(树脂熔融温度105℃,本实施例加热温度高于熔融温度45℃~50℃)的加热烘道加热8min,热固性树脂混合粉料熔化并渗透到纤维缝隙。
[0093]
冷却:玻璃纤维布再经过冷却段冷却到55℃(树脂软化温度95℃,本实施例冷却温度低于软化温度40℃)以下10s,然后进行裁切。
[0094]
预浸料使用:将裁切成一定尺寸的干法预浸料按照需求进行铺层,并热压固化制得层压板。
[0095]
综上所述,本发明实施例的干法制备纤维增强热固性复合材料预浸料的工艺,其采用可控制含量的微粉级混合粉末制备热固性预浸料,从根本上解决了传统湿法预浸料制
备过程中挥发物含量难以控制的难题;整个工艺过程不加入其他有机溶剂,从根本上解决了湿法预浸料当中的残留的挥发物对复合材料板、管和棒制品强度的影响,尤其是对热态强度的影响;并且解决了传统湿法预浸料制备过程中溶剂的挥发对空气造成的污染;从根本上规避了危险化学溶剂在运输、储存和使用带来的管理成本和管理风险。
[0096]
并且,干法制备的热固性预浸料,由于其不含高沸点溶剂残留,使得常温下的储存期明显长于传统溶剂法制备的预浸料。不仅如此,干法预浸料制备的板材、管材和棒,其热稳定性和湿热稳定性等明显优于溶剂法预浸料制备的板材、管和棒。
[0097]
本发明相比传统工艺,因撒粉、加热、冷却等过程中均由传送带输送前行,整个预浸料制备过程中基材受到的张力较小,故对基材的抗拉强度要求不高,所以基材的选择范围更广泛。
[0098]
本发明同样可替代部分热熔法制备预浸料(包含热固性预浸料和热塑性预浸料)工艺从而大大降低了生产成本。
[0099]
以上所描述的实施例是本发明一部分实施例,而不是全部的实施例。本发明的实施例的详细描述并非旨在限制要求保护的本发明的范围,而是仅仅表示本发明的选定实施例。基于本发明中的实施例,本领域普通技术人员在没有作出创造性劳动前提下所获得的所有其他实施例,都属于本发明保护的范围。