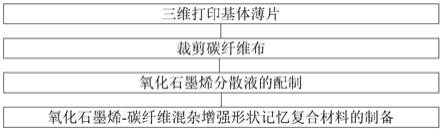
氧化石墨烯
‑
碳纤维混杂增强形状记忆复合材料制备方法
技术领域
1.本发明涉及形状记忆复合材料制备领域,具体是一种氧化石墨烯
‑
碳纤维混杂增强 形状记忆复合材料的制备方法。
背景技术:2.形状记忆聚合物是一种可以在外部激励作用下由变形状态恢复到原始状态的新型 智能高分子材料。形状记忆聚合物以其密度低、可回复形变量大等显著优势被广泛应 用于航空航天、武器装备等先进制造领域,但是由于此类聚合物材料力学性能较差, 使得形状记忆聚合物的广泛应用受到极大限制。目前,一些科研工作者将形状记忆聚 合物与力学特性优异的增强体结合制备出既具形状记忆功能又兼具高强度高刚度等良 好力学性能的形状记忆复合材料,这种新型多功能复合材料具有广泛的研究前景。
3.目前,连续纤维增强热塑性复合材料成型工艺方法主要有热压成型、拉挤成型、 缠绕成型以及树脂传递模塑成型(rtm)等。然而,采用以上工艺制备氧化石墨烯
‑ꢀ
碳纤维混杂增强形状记忆复合材料可能会存在纳米结构的氧化石墨烯易团聚且难以在 复合材料中均匀分散、制件形状较为单一、工艺过程繁琐等制备局限性。
4.三维打印技术即增材制造技术,是一种将打印模型按照层厚分解为无数层薄片, 并将这些薄片进行逐层堆积制备三维实体的先进成型工艺。该成型工艺用于成型具有 复杂几何形状的制品,操作过程简单、产品稳定性好且成型过程通常在计算机的辅助 作用下完成,可用于形状记忆聚合物叠层片的打印和成型。三维打印技术的应用,能 够显著提升工业制造、医疗设备等制造领域的工艺水平。
5.氧化石墨烯
‑
碳纤维混杂增强的形状记忆复合材料中碳纤维体积分数高,纤维与纤 维之间的间隙小且不均匀,复合材料中还可能混杂着杂质气体,要实现氧化石墨烯在 复合材料中的充分均匀浸渗较为困难,在真空的环境下浸渗能够有效排出其中的杂质 气体,获得较为充分均匀的浸渗效果。三维打印出的形状记忆聚合物叠层片在常温下 属于硬质固态物质,很难跟涂覆过氧化石墨烯的碳纤维布粘合在一起,这就需要在加 热的情况下,让三维打印出的形状记忆聚合物叠层片处于粘流态,并施加挤压力使三 维打印形状记忆聚合物叠层片和涂覆过氧化石墨烯的碳纤维布粘合在一起,形成氧化 石墨烯
‑
碳纤维混杂增强的形状记忆复合材料。
6.在公开号为cn109629076a的发明创造中针对普通增强体不具备形状记忆功能或 形状记忆聚合物力学性能较低的问题,提出了一种将形状记忆聚合物纤维与连续纤维 进行编织,并以该混编织物作为复合材料的增强体的制备方法,该方法有效保证了增 强体的形状记忆与力学特性。但该方法不能制备氧化石墨烯
‑
碳纤维混杂增强的形状记 忆复合材料,且增强体编织过程复杂,要求操作人员具有较高的技术水平,生产效率 低、复合材料质量稳定性不易保证。
7.在公开号cn109897375b的发明专利中提出了一种高强度柔性环氧树脂改性氰酸 酯树脂/碳纤维形状记忆复合材料及其制备方法,该制备方法采用增韧氰酸酯树脂作为 基
体可以解决形状记忆聚合物在实际应用中力学性能较低、形变回复率较慢等问题, 具有操作简单、成本较低等明显优势。但该发明未提及纳米尺度的氧化石墨烯和微米 尺度的碳纤维混杂增强的形状记忆复合材料的制备问题,且未提到采用三维打印技术 用于支撑结构形状较为复杂的形状记忆复合材料的制备方法,能够成型的复合材料结 构和形状较少。
技术实现要素:8.为克服现有技术中存在的氧化石墨烯不易分散、复合材料由于浸渗不充分或夹杂 杂质气体而产生气孔、分层等缺陷以及复合材料的尺寸与形状单一等问题,本发明提 出了一种氧化石墨烯
‑
碳纤维混杂增强形状记忆复合材料制备方法。
9.本发明具体过程如下。
10.第一步,三维打印基体薄片:
11.步骤1,在creo软件中建立三维打印基体外形。所述外形为60mm
×
30mm
×
0.5mm 的长方体。
12.步骤2,设置cura软件打印参数。
13.采用分层填充打印的方法打印所述基体薄片;该基体薄片通过分层打印得到,每 层的厚度均为0.125mm。
14.设定打印喷头的移动速度为50mm/s,打印温度为210℃,热床温度为50℃,喷嘴 孔径为0.4mm。
15.步骤3,在cura软件中打开stl格式文件,确定所建立的基体外形的摆放方式并 存入sd卡。所述摆放方式为该基体薄片的矩形截面abcd与cura软件的三维坐标中 的x1o1y1面重合且o1x1//ab,o1y1//ad,ab与x1轴之间的距离为40mm,ad与y1轴之间的距离为40mm。
16.步骤4,将线径为1.75mm的打印丝插入挤出机挤出孔中。
17.步骤5,打印
18.通过三维打印机打印所述基体薄片。具体过程是:
[0019]ⅰ设定打印路径。以所述基体薄片的一个直角处为原点o2,建立该基体薄片的 坐标系,并使该基体薄片的长边为x2轴,以该基体薄片的短边为y2轴。设置该坐标 系中(0.2,29.8)处为三维打印机喷头的中心的起点e。
[0020]ⅱ打印基体薄片底层。
[0021]
所述基体薄片底层的打印包括打印该基体薄片底层边框和在该底层边框内填充打 印丝。
[0022]
所述边框的层厚为0.125mm,壁厚为1.2mm;边框内打印丝的填充率为100%。
[0023]
打印该基体薄片底层边框:移动该三维打印机喷头,使其中点至所述起点e处, 按设定的打印参数打印该基体薄片的边框;所述边框分三次打印完成。具体是,使该 打印喷头中点沿该坐标系的﹣y2方向垂直移动,打印至(0.2,0.2)处;变更打印方向, 使该打印喷头中点沿该坐标系的x2方向水平移动至(59.8,0.2)处;变更打印方向, 使该打印喷头沿该坐标系的y2方向垂直移动至(59.8,29.8)处;变更打印方向,使该 打印喷头沿该坐标系的﹣x2方向水平移动至(0.6,29.8)处。完成对所述边框的第一次 打印。
[0024]
在该边框的第二次打印时,使该打印喷头以(0.6,29.8)处为起点,沿该坐标系的 ﹣y2方向垂直移动,打印至(0.6,0.6)处;变更打印方向,使该打印喷头沿该坐标系 的x2方向
水平移动至(59.4,0.6)处;变更打印方向,使该打印喷头沿该坐标系的y2方向垂直移动至(59.4,29.4)处;变更打印方向,使该打印喷头沿该坐标系的﹣x2方 向水平移动至(1,29.4)处。完成对所述边框的第二次打印。
[0025]
在该边框的第三次打印时,使该打印喷头以(1,29.4)处为起点,沿该坐标系的﹣ y2方向垂直移动,打印至(1,1)处;变更打印方向,使该打印喷头沿该坐标系的x2方向水平移动至(59,1)处;变更打印方向,使该打印喷头沿该坐标系的y2方向垂直 移动至(59,29)处;变更打印方向,使该打印喷头沿该坐标系的﹣x2方向水平移动至 (1.8,29)处。完成对所述边框的第三次打印。
[0026]
完成对该基体薄片底层边框的打印。
[0027]
在该底层边框内填充打印丝:以所述(1.8,29)处为填充打印丝的起点f。移动所 述打印喷头至该起点f,按设定的打印参数实施打印。所述打印喷头向(﹣x2,﹣y2) 方向斜线移动至距离完成的边框的左侧内表面0.2mm处折返,以斜线向(x2,y2)方 向移动至距离完成的边框的上侧内表面0.2mm处再次折返;继续以斜线向(﹣x2,﹣ y2)方向斜线移动至距离完成的边框的左侧内表面0.2mm处折返;继续以斜线向(x2, y2)方向移动至距离完成的边框的上侧内表面0.2mm处再次折返。重复所述斜线移动
ꢀ‑‑
折返
‑‑
再次斜线移动
‑‑
再次折返的过程,直至该打印喷头移动至(58.6,1.4)处;在该 打印喷头移动的过程中完成对所述基体薄片底层边框内的打印丝填充。
[0028]
所述斜线的斜率为1。该基体薄片底层的厚度为0.125mm。
[0029]
至此,完成所述基体薄片底层的打印。
[0030]ⅲ打印所述基体薄片各层:
[0031]
重复第二步打印所述基体薄片底层的过程,逐层完成对各层的打印。各层的层厚 均为0.125mm。直至达到该基体薄片设计厚度,完成基体薄片的打印。
[0032]ⅳ打印全部基体薄片:
[0033]
重复两遍所述第二步的过程和第三步的过程,完成其余各基体薄片的打印。
[0034]
本步骤共得到三片基体薄片。
[0035]
第二步,裁剪碳纤维布:
[0036]
将碳纤维布按设计要求剪裁为60mm
×
30mm的碳纤维布片;该碳纤维布片的数量 为4片,备用。
[0037]
第三步,氧化石墨烯分散液的配制:
[0038]
具体过程是:
[0039]
步骤1,粉末状的氧化石墨烯与无水乙醇按1:5或1:4的质量比混合,得到深 灰黑色氧化石墨烯溶液。
[0040]
步骤2,将得到的氧化石墨烯溶液转移至电磁搅拌器中,以300rpm的转速搅拌 20min,或以400rpm的转速搅拌15min,或以500rpm的转速搅拌10min,完成氧化石 墨烯在乙醇溶液中的初步分散。
[0041]
步骤3,将经过初步分散的氧化石墨烯溶液放置在频率为40khz、功率为200w的 超声分散器中,分散30min,实现氧化石墨烯的最终分散,得到氧化石墨烯分散液的 预制品。
[0042]
步骤4,将得到的氧化石墨烯分散液的预制品置于真空干燥箱中抽真空6h~8h,以 除去该分散液内乙醇挥发产生的气体。得到氧化石墨烯分散液。
[0043]
第四步,氧化石墨烯
‑
碳纤维混杂增强形状记忆复合材料的制备:
[0044]
具体过程是:
[0045]
步骤1,在得到的每片碳纤维布片的正反两面均匀涂覆氧化石墨烯分散液;在得 到的每片基体薄片的正反两面均匀涂覆氧化石墨烯分散液。
[0046]
将涂覆有氧化石墨烯分散液的碳纤维布片与涂覆有氧化石墨烯分散液的基体薄片 间隔的逐层叠放,并使最底层为碳纤维布片;在该碳纤维布片的上表面放置一片基体 薄片,在该基体薄片上表面放置一片碳纤维布片。如此循环,形成了最底层与最顶层 均为碳纤维布的碳纤维布片
‑
基体薄片
‑
碳纤维布片
‑
基体薄片的层叠物。
[0047]
步骤2,将得到的层叠物放置于提前预热的平板硫化机中,并通过液压机施加挤 压力。所述挤压的温度为150℃
‑
190℃,挤压的压力为0.5mpa
‑
0.9mpa,保压时间为 16min
‑
24min。
[0048]
步骤3,将经过挤压的层叠物转移至真空干燥箱中进行最终真空浸渗处理。所述 真空浸渗处理包括真空浸渗与真空固化两个过程。在真空浸渗过程中,真空度为
ꢀ‑
0.07mpa或
‑
0.09mpa,温度为150℃
‑
190℃,真空浸渗时间为55min
‑
75min。真空浸渗 过程结束后进行真空固化过程。在真空固化过程中,真空度为
‑
0.07mpa或
‑
0.09mpa, 温度为50℃
‑
90℃,时间为6min
‑
10min。
[0049]
所述最终真空浸渗处理后,得到氧化石墨烯
‑
碳纤维混杂增强形状记忆复合材料。
[0050]
氧化石墨烯
‑
碳纤维混杂增强形状记忆复合材料的制备工艺过程如图3所示。
[0051]
本发明中的氧化石墨烯
‑
碳纤维混杂增强形状记忆复合材料,是在碳纤维增强形状 记忆复合材料中加入纳米尺度的氧化石墨烯的一种微纳跨尺度混杂增强形状记忆复合 材料。由于氧化石墨烯导热系数可达3000w/m﹒k、拉伸模量可达1.01tpa且其极限 强度可达116gpa,使得加入氧化石墨烯的复合材料的热响应速率与力学承载能力都有 所提升。
[0052]
本发明将三维打印技术与真空浸渗和热压成型工艺相结合,在保证复合材料浸渗 微观组织理想、缺陷得到有效控制、形状记忆性能优良的基础上,可根据制件结构形 状的要求,设计制造不同结构形状的三维打印与真空浸渗热压成型复合材料件,进而 实现复合材料制件结构形状的多样化,并减少复合材料制件的制造周期。所制备的复 合材料形状固定率可达97.12%,形状回复率可达97.15%,形状记忆性能优良。其中, 采用三维打印技术制备形状记忆基体,解决了传统工艺生产形状记忆聚合物在形状与 尺寸上的单一性问题,能够成型复杂几何形状的制品,且由于计算机的辅助作用,使 得操作过程简单,设计制造周期大大缩短。采用真空浸渗、热压成型的制备工艺可以 有效改善复合材料制备效果。由于氧化石墨烯易团聚分散性较差,为防止其在复合材 料中发生聚集沉淀的现象,本发明将氧化石墨烯分散于无水乙醇中,在电磁搅拌与超 声分散的作用下将氧化石墨烯剥离为单层氧化石墨烯薄片,实现氧化石墨烯的均匀分 散。本发明采用的热压成型方法,保障了基体在增强体纤维中浸渗的第一阶段是在高 于基体熔融温度的挤压温度下进行,此时基体具有良好的流动性,同时在挤压力的作 用下,使基体可以克服浸渗阻力以充分浸渗复合材料内部,除此之外,复合材料中的 杂质气体可以在纤维层间排出。真空浸渗过程采用真空干燥箱,为复合材料浸渗与固 化的第二阶段提供了真空与高温环境,促使基体具有较低的粘度与良好的流动性且能 够排出由于乙醇挥发在复合材料内部产生的气泡,通过观察所制备的复合材料的微观 组织图(图6)可知,基体熔融后可以充分浸渗于纤维丝间隙之中且
通过图5可以观 察到复合材料宏观形貌良好,其气孔、气泡以及分层缺陷得到有效控制。该工艺系统 可以成型形状记忆性能优良的氧化石墨烯
‑
碳纤维混杂增强形状记忆复合材料。
[0053]
图1是确定基体外形的摆放方式示意图。
[0054]
图2是三维打印基体薄片打印过程示意图。
[0055]
图3是制备氧化石墨烯
‑
碳纤维混杂增强形状记忆复合材料的工艺流程图。
[0056]
图4是涂覆过氧化石墨烯的碳纤维布片和涂覆过氧化石墨烯的基体薄片交替放 置和叠放示意图;
[0057]
图5为实施例1中的氧化石墨烯
‑
碳纤维混杂增强形状记忆复合材料。
[0058]
图6是实施例1中提到的氧化石墨烯
‑
碳纤维混杂增强形状记忆复合材料的微观 组织。图7是本发明实施过程图。
[0059]
图中:1为表面涂敷氧化石墨烯的碳纤维布片示意图;2为表面涂敷氧化石墨烯的 基体薄片示意图;3为叠层放置;4为碳纤维布片与基体薄片的层叠物示意图;5为氧 化石墨烯
‑
碳纤维混杂增强形状记忆复合材料;6为复合材料的厚度方向;7为实施例 1中氧化石墨烯
‑
碳纤维混杂增强形状记忆复合材料厚度方向的形貌。
具体实施方式
[0060]
本发明采用实施例与对照实施例对发明内容进行详细说明。
[0061]
本发明是一种氧化石墨烯
‑
碳纤维混杂增强形状记忆复合材料的制备方法,将通过 5个实施例具体说明其实施过程。
[0062]
本发明的具体过程是:
[0063]
第一步,三维打印基体薄片:
[0064]
步骤1,在creo软件中建立三维打印基体外形。所述外形为60mm
×
30mm
×
0.5mm 的长方体。
[0065]
步骤2,设置cura软件打印参数。
[0066]
采用分层填充打印的方法打印所述基体薄片;该基体薄片通过分层打印得到,每 层的厚度均为0.125mm。
[0067]
设定打印喷头的移动速度为50mm/s,打印温度为210℃,热床温度为50℃,喷嘴 孔径为0.4mm。
[0068]
步骤3,在cura软件中打开stl格式文件,确定所建立的基体外形的摆放方式并 存入sd卡。所述摆放方式为该基体薄片的矩形截面abcd与cura软件的三维坐标中 的x1o1y1面重合且o1x1//ab,o1y1//ad,ab与x1轴之间的距离为40mm,ad与 y1轴之间的距离为40mm。
[0069]
步骤4,将线径为1.75mm的打印丝插入挤出机挤出孔中。
[0070]
步骤5,打印
[0071]
通过三维打印机打印所述基体薄片。具体过程是:
[0072]ⅰ设定打印路径。以所述基体薄片的一个直角处为原点o2,建立该基体薄片的 坐标系,并使该基体薄片的长边为x2轴,以该基体薄片的短边为y2轴。设置该坐标 系中(0.2,29.8)处为三维打印机喷头的中心的起点e。
[0073]ⅱ打印基体薄片底层。
[0074]
所述基体薄片底层的打印包括打印该基体薄片底层边框和在该底层边框内填充打 印丝。
[0075]
所述边框的层厚为0.125mm,壁厚为1.2mm;边框内打印丝的填充率为100%。
[0076]
打印该基体薄片底层边框:移动该三维打印机喷头,使其中点至所述起点e处, 按设定的打印参数打印该基体薄片的边框;所述边框分三次打印完成。具体是,使该 打印喷头中点沿该坐标系的﹣y2方向垂直移动,打印至(0.2,0.2)处;变更打印方向, 使该打印喷头中点沿该坐标系的x2方向水平移动至(59.8,0.2)处;变更打印方向, 使该打印喷头沿该坐标系的y2方向垂直移动至(59.8,29.8)处;变更打印方向,使该 打印喷头沿该坐标系的﹣x2方向水平移动至(0.6,29.8)处。完成对所述边框的第一次 打印。
[0077]
在该边框的第二次打印时,使该打印喷头以(0.6,29.8)处为起点,沿该坐标系的 ﹣y2方向垂直移动,打印至(0.6,0.6)处;变更打印方向,使该打印喷头沿该坐标系 的x2方向水平移动至(59.4,0.6)处;变更打印方向,使该打印喷头沿该坐标系的y2方向垂直移动至(59.4,29.4)处;变更打印方向,使该打印喷头沿该坐标系的﹣x2方 向水平移动至(1,29.4)处。完成对所述边框的第二次打印。
[0078]
在该边框的第三次打印时,使该打印喷头以(1,29.4)处为起点,沿该坐标系的﹣ y2方向垂直移动,打印至(1,1)处;变更打印方向,使该打印喷头沿该坐标系的x2方向水平移动至(59,1)处;变更打印方向,使该打印喷头沿该坐标系的y2方向垂直 移动至(59,29)处;变更打印方向,使该打印喷头沿该坐标系的﹣x2方向水平移动至 (1.8,29)处。完成对所述边框的第三次打印。
[0079]
完成对该基体薄片底层边框的打印。
[0080]
在该底层边框内填充打印丝:以所述(1.8,29)处为填充打印丝的起点f。移动所 述打印喷头至该起点f,按设定的打印参数实施打印。所述打印喷头向(﹣x2,﹣y2) 方向斜线移动至距离完成的边框的左侧内表面0.2mm处折返,以斜线向(x2,y2)方 向移动至距离完成的边框的上侧内表面0.2mm处再次折返;继续以斜线向(﹣x2,﹣ y2)方向斜线移动至距离完成的边框的左侧内表面0.2mm处折返;继续以斜线向(x2, y2)方向移动至距离完成的边框的上侧内表面0.2mm处再次折返。重复所述斜线移动
ꢀ‑‑
折返
‑‑
再次斜线移动
‑‑
再次折返的过程,直至该打印喷头移动至(58.6,1.4)处;在该 打印喷头移动的过程中完成对所述基体薄片底层边框内的打印丝填充。
[0081]
所述斜线的斜率为1。该基体薄片底层的厚度为0.125mm。
[0082]
至此,完成所述基体薄片底层的打印。
[0083]ⅲ打印所述基体薄片各层:
[0084]
重复第二步打印所述基体薄片底层的过程,逐层完成对各层的打印。各层的层厚 均为0.125mm。直至达到该基体薄片设计厚度,完成基体薄片的打印。
[0085]ⅳ打印全部基体薄片:
[0086]
重复两遍所述第二步的过程和第三步的过程,完成其余各基体薄片的打印。
[0087]
本步骤共得到三片基体薄片。
[0088]
第二步,裁剪碳纤维布:
[0089]
将碳纤维布按设计要求剪裁为60mm
×
30mm的碳纤维布片;该碳纤维布片的数量 为4片,备用。
[0090]
第三步,氧化石墨烯分散液的配制:
[0091]
具体过程是:
[0092]
步骤1,粉末状的氧化石墨烯与无水乙醇按1:5或1:4的质量比混合,得到深 灰黑色氧化石墨烯溶液。
[0093]
步骤2,将得到的氧化石墨烯溶液转移至电磁搅拌器中,以300rpm的转速搅拌 20min,或以400rpm的转速搅拌15min,或以500rpm的转速搅拌10min,完成氧化石 墨烯在乙醇溶液中的初步分散。
[0094]
步骤3,将经过初步分散的氧化石墨烯溶液放置在频率为40khz、功率为200w的 超声分散器中,分散30min,实现氧化石墨烯的最终分散,得到氧化石墨烯分散液的 预制品。
[0095]
步骤4,将得到的氧化石墨烯分散液的预制品置于真空干燥箱中抽真空6h
‑
8h,以 除去该分散液内乙醇挥发产生的气体。得到氧化石墨烯分散液。
[0096]
第四步,氧化石墨烯
‑
碳纤维混杂增强形状记忆复合材料的制备:
[0097]
具体过程是:
[0098]
步骤1,在得到的每片碳纤维布片的正反两面均匀涂覆氧化石墨烯分散液;在得 到的每片基体薄片的正反两面均匀涂覆氧化石墨烯分散液。
[0099]
将涂覆有氧化石墨烯分散液的碳纤维布片与涂覆有氧化石墨烯分散液的基体薄片 间隔的逐层叠放,并使最底层为碳纤维布片;在该碳纤维布片的上表面放置一片基体 薄片,在该基体薄片上表面放置一片碳纤维布片。如此循环,形成了最底层与最顶层 均为碳纤维布的碳纤维布片
‑
基体薄片
‑
碳纤维布片
‑
基体薄片的层叠物。
[0100]
步骤2,将得到的层叠物放置于提前预热的平板硫化机中,并通过液压机施加挤 压力。所述挤压的温度为150℃
‑
190℃,挤压的压力为0.5mpa
‑
0.9mpa,保压时间为 16min
‑
24min。
[0101]
步骤3,将层叠物转移至真空干燥箱中进行最终真空浸渗处理。所述真空浸渗处 理包括真空浸渗与真空固化两个过程。在真空浸渗过程中,真空度为
‑
0.07mpa或
ꢀ‑
0.09mpa,温度为150℃
‑
190℃,真空浸渗时间为55min
‑
75min。真空浸渗过程结束后 进行真空固化过程。在真空固化过程中,真空度为
‑
0.07mpa或
‑
0.09mpa,温度为 50℃
‑
90℃,时间为6min
‑
10min。
[0102]
所述最终真空浸渗处理后,得到氧化石墨烯
‑
碳纤维混杂增强形状记忆复合材料。
[0103]
本发明中各实施例的工艺参数如表1所示。
[0104]
表1
[0105][0106]
为验证本发明的效果,对所述各实施例制备的氧化石墨烯
‑
碳纤维混杂增强形状记 忆复合材料进行测定,其结果如表2所示。
[0107]
表2
[0108][0109]
对照实施例1
[0110]
本对照例是现有技术中采用三维打印与真空浸渗和热压固化方法制备氧化石墨烯
ꢀ‑
碳纤维混杂增强形状记忆复合材料的具体过程:
[0111]
第一步,三维打印基体薄片:
[0112]
步骤1,在creo软件中建立三维打印基体外形。所述外形为60mm
×
30mm
×
0.5mm 的
长方体。
[0113]
步骤2,设置cura软件打印参数。
[0114]
采用分层填充打印的方法打印所述基体薄片;该基体薄片通过分层打印得到,每 层的厚度均为0.125mm。
[0115]
设定打印喷头的移动速度为50mm/s,打印温度为210℃,热床温度为50℃,喷嘴 孔径为0.4mm。
[0116]
步骤3,在cura软件中打开stl格式文件,确定所建立的基体外形的摆放方式并 存入sd卡。所述摆放方式为该基体薄片的矩形截面abcd与cura软件的三维坐标中 的x1o1y1面重合且o1x1//ab,o1y1//ad,ab与x1轴之间的距离为40mm,ad与 y1轴之间的距离为40mm。
[0117]
步骤4,将线径为1.75mm的打印丝插入挤出机挤出孔中。
[0118]
步骤5,打印
[0119]
通过三维打印机打印所述基体薄片。具体过程是:
[0120]ⅰ设定打印路径。以所述基体薄片的一个直角处为原点o2,建立该基体薄片的 坐标系,并使该基体薄片的长边为x2轴,以该基体薄片的短边为y2轴。设置该坐标 系中(0.2,29.8)处为三维打印机喷头的中心的起点e。
[0121]ⅱ打印基体薄片底层。
[0122]
所述基体薄片底层的打印包括打印该基体薄片底层边框和在该底层边框内填充打 印丝。
[0123]
所述边框的层厚为0.125mm,壁厚为1.2mm;边框内打印丝的填充率为100%。
[0124]
打印该基体薄片底层边框:移动该三维打印机喷头,使其中点至所述起点e处, 按设定的打印参数打印该基体薄片的边框;所述边框分三次打印完成。具体是,使该 打印喷头中点沿该坐标系的﹣y2方向垂直移动,打印至(0.2,0.2)处;变更打印方向, 使该打印喷头中点沿该坐标系的x2方向水平移动至(59.8,0.2)处;变更打印方向, 使该打印喷头沿该坐标系的y2方向垂直移动至(59.8,29.8)处;变更打印方向,使该 打印喷头沿该坐标系的﹣x2方向水平移动至(0.6,29.8)处。完成对所述边框的第一次 打印。
[0125]
在该边框的第二次打印时,使该打印喷头以(0.6,29.8)处为起点,沿该坐标系的 ﹣y2方向垂直移动,打印至(0.6,0.6)处;变更打印方向,使该打印喷头沿该坐标系 的x2方向水平移动至(59.4,0.6)处;变更打印方向,使该打印喷头沿该坐标系的y2方向垂直移动至(59.4,29.4)处;变更打印方向,使该打印喷头沿该坐标系的﹣x2方 向水平移动至(1,29.4)处。完成对所述边框的第二次打印。
[0126]
在该边框的第三次打印时,使该打印喷头以(1,29.4)处为起点,沿该坐标系的﹣ y2方向垂直移动,打印至(1,1)处;变更打印方向,使该打印喷头沿该坐标系的x2方向水平移动至(59,1)处;变更打印方向,使该打印喷头沿该坐标系的y2方向垂直 移动至(59,29)处;变更打印方向,使该打印喷头沿该坐标系的﹣x2方向水平移动至 (1.8,29)处。完成对所述边框的第三次打印。
[0127]
完成对该基体薄片底层边框的打印。
[0128]
在该底层边框内填充打印丝:以所述(1.8,29)处为填充打印丝的起点f。移动所 述打印喷头至该起点f,按设定的打印参数实施打印。所述打印喷头向(﹣x2,﹣y2) 方向斜线移动至距离完成的边框的左侧内表面0.2mm处折返,以斜线向(x2,y2)方 向移动至距离完成
的边框的上侧内表面0.2mm处再次折返;继续以斜线向(﹣x2,﹣ y2)方向斜线移动至距离完成的边框的左侧内表面0.2mm处折返;继续以斜线向(x2, y2)方向移动至距离完成的边框的上侧内表面0.2mm处再次折返。重复所述斜线移动
‑‑
折返
‑‑
再次斜线移动
‑‑
再次折返的过程,直至该打印喷头移动至(58.6,1.4)处;在该 打印喷头移动的过程中完成对所述基体薄片底层边框内的打印丝填充。
[0129]
所述斜线的斜率为1。该基体薄片底层的厚度为0.125mm。
[0130]
至此,完成所述基体薄片底层的打印。
[0131]ⅲ打印所述基体薄片各层:
[0132]
重复第二步打印所述基体薄片底层的过程,逐层完成对各层的打印。各层的层厚 均为0.125mm。直至达到该基体薄片设计厚度,完成基体薄片的打印。
[0133]ⅳ打印全部基体薄片:
[0134]
重复两遍所述第二步的过程和第三步的过程,完成其余各基体薄片的打印。
[0135]
本步骤共得到三片基体薄片。
[0136]
第二步,裁剪碳纤维布:
[0137]
将t300双向碳纤维布按设计要求剪裁为60mm
×
30mm的碳纤维布片;该碳纤维 布片的数量为4片,备用。
[0138]
第三步,氧化石墨烯分散液的配制:
[0139]
具体过程是:
[0140]
步骤1,粉末状的氧化石墨烯与无水乙醇按1:5的质量比混合,得到深灰黑色氧 化石墨烯溶液。
[0141]
步骤2,将得到的氧化石墨烯溶液转移至电磁搅拌器中,以300rpm的转速搅拌 20min,完成氧化石墨烯在乙醇溶液中的初步分散。
[0142]
步骤3,将经过初步分散的氧化石墨烯溶液放置在频率为40khz、功率为200w的 超声分散器中,分散30min,实现氧化石墨烯的最终分散,得到氧化石墨烯分散液。
[0143]
第四步,氧化石墨烯
‑
t300碳纤维混杂增强形状记忆复合材料的制备:
[0144]
具体过程是:
[0145]
步骤1,在得到的每片碳纤维布片的正反两面均匀涂覆氧化石墨烯分散液;在得 到的每片基体薄片的正反两面均匀涂覆氧化石墨烯分散液。
[0146]
将涂覆有氧化石墨烯分散液的碳纤维布片与涂覆有氧化石墨烯分散液的基体薄片 间隔的逐层叠放,并使最底层为碳纤维布片;在该碳纤维布片的上表面放置一片基体 薄片,在该基体薄片上表面放置一片碳纤维布片。如此循环,形成了最底层与最顶层 均为碳纤维布的碳纤维布片
‑
基体薄片
‑
碳纤维布片
‑
基体薄片的层叠物。
[0147]
步骤2,将得到的层叠物放置于提前预热到170℃的平板硫化机中,并通过液压机 施加挤压力。所述挤压的温度为170℃,挤压的压力为0.7mpa,保压时间为20min。
[0148]
步骤3,将层叠物转移至真空干燥箱中进行最终真空浸渗处理。所述真空浸渗处 理包括真空浸渗与真空固化两个过程。在真空浸渗过程中,真空度为
‑
0.09mpa,温度 为180℃,真空浸渗时间为60min。真空浸渗过程结束后进行真空固化过程。在真空固 化过程中,真空度为
‑
0.09mpa,温度为50℃,时间为10min。
[0149]
所述最终真空浸渗处理后,得到氧化石墨烯
‑
碳纤维混杂增强形状记忆复合材料。
[0150]
本对照实施例制备的碳纤维增强形状记忆复合材料的形状固定率为94.13%,形状 回复率为93.27%。
[0151]
对照实施例2
[0152]
本对照例是现有技术中采用三维打印与真空浸渗和热压固化方法制备碳纤维增强 形状记忆复合材料的具体过程:
[0153]
第一步,三维打印基体薄片:
[0154]
步骤1,在creo软件中建立三维打印基体外形。所述外形为60mm
×
30mm
×
0.5mm 的长方体。
[0155]
步骤2,设置cura软件打印参数。
[0156]
采用分层填充打印的方法打印所述基体薄片;该基体薄片通过分层打印得到,每 层的厚度均为0.125mm。
[0157]
设定打印喷头的移动速度为50mm/s,打印温度为210℃,热床温度为50℃,喷嘴 孔径为0.4mm。
[0158]
步骤3,在cura软件中打开stl格式文件,确定所建立的基体外形的摆放方式并 存入sd卡。所述摆放方式为该基体薄片的矩形截面abcd与cura软件的三维坐标中 的x1o1y1面重合且o1x1//ab,o1y1//ad,ab与x1轴之间的距离为40mm,ad与 y1轴之间的距离为40mm。
[0159]
步骤4,将线径为1.75mm的打印丝插入挤出机挤出孔中。
[0160]
步骤5,打印
[0161]
通过三维打印机打印所述基体薄片。具体过程是:
[0162]ⅰ设定打印路径。以所述基体薄片的一个直角处为原点o2,建立该基体薄片的 坐标系,并使该基体薄片的长边为x2轴,以该基体薄片的短边为y2轴。设置该坐标 系中(0.2,29.8)处为三维打印机喷头的中心的起点e。
[0163]ⅱ打印基体薄片底层。
[0164]
所述基体薄片底层的打印包括打印该基体薄片底层边框和在该底层边框内填充打 印丝。
[0165]
所述边框的层厚为0.125mm,壁厚为1.2mm;边框内打印丝的填充率为100%。
[0166]
打印该基体薄片底层边框:移动该三维打印机喷头,使其中点至所述起点e处, 按设定的打印参数打印该基体薄片的边框;所述边框分三次打印完成。具体是,使该 打印喷头中点沿该坐标系的﹣y2方向垂直移动,打印至(0.2,0.2)处;变更打印方向, 使该打印喷头中点沿该坐标系的x2方向水平移动至(59.8,0.2)处;变更打印方向, 使该打印喷头沿该坐标系的y2方向垂直移动至(59.8,29.8)处;变更打印方向,使该 打印喷头沿该坐标系的﹣x2方向水平移动至(0.6,29.8)处。完成对所述边框的第一次 打印。
[0167]
在该边框的第二次打印时,使该打印喷头以(0.6,29.8)处为起点,沿该坐标系的 ﹣y2方向垂直移动,打印至(0.6,0.6)处;变更打印方向,使该打印喷头沿该坐标系 的x2方向水平移动至(59.4,0.6)处;变更打印方向,使该打印喷头沿该坐标系的y2方向垂直移动至(59.4,29.4)处;变更打印方向,使该打印喷头沿该坐标系的﹣x2方 向水平移动至(1,29.4)处。完成对所述边框的第二次打印。
[0168]
在该边框的第三次打印时,使该打印喷头以(1,29.4)处为起点,沿该坐标系的﹣ y2方向垂直移动,打印至(1,1)处;变更打印方向,使该打印喷头沿该坐标系的x2方向水平移
薄片,在该基体薄片上表面放置一片碳纤维布片。如此循环,形成了最底层与最顶层 均为碳纤维布的碳纤维布片
‑
基体薄片
‑
碳纤维布片
‑
基体薄片的层叠物。
[0190]
步骤2,将得到的层叠物放置于提前预热到170℃的平板硫化机中,并通过液压机 施加挤压力。所述挤压的温度为170℃,挤压的压力为0.7mpa,保压时间为20min。
[0191]
步骤3,将层叠物转移至真空干燥箱中进行真空固化过程。在真空固化过程中, 真空度为
‑
0.09mpa,温度为50℃,时间为10min。
[0192]
所述最终真空浸渗处理后,得到氧化石墨烯
‑
碳纤维混杂增强形状记忆复合材料。
[0193]
本对照实施例制备的碳纤维增强形状记忆复合材料的形状固定率为93.89%,形状 回复率为93.74%。
[0194]
通过本发明实施例1中制备的氧化石墨烯
‑
碳纤维混杂增强形状记忆复合材料的 形状固定率为97.12%、形状回复率为97.15%;实施例2中制备的氧化石墨烯
‑
碳纤维 混杂增强形状记忆复合材料的形状固定率为96.53%、形状回复率为96.71%;实施例3 中制备的氧化石墨烯
‑
碳纤维混杂增强形状记忆复合材料的形状固定率为96.32%、形 状回复率为96.67%;实施例4中制备的氧化石墨烯
‑
碳纤维混杂增强形状记忆复合材 料的形状固定率为95.34%、形状回复率为96.79%;实施例5中制备的氧化石墨烯
‑
碳 纤维混杂增强形状记忆复合材料的形状固定率为95.14%、形状回复率为96.27%;而 对照实施例1中氧化石墨烯分散液未经抽真空处理的氧化石墨烯
‑
碳纤维混杂增强形 状记忆复合材料的形状固定率为94.13%、形状回复率为93.27%;对照实施例2中复 合材料未经真空浸渗过程的氧化石墨烯
‑
碳纤维混杂增强形状记忆复合材料的形状固 定率为93.89%、形状回复率为93.74%。
[0195]
当氧化石墨烯分散液未经抽真空处理时,会导致分散液中的乙醇溶液残留较多, 在对复合材料进行热压成型、真空浸渗的过程中乙醇溶液挥发产生气泡,这些气泡在 复合材料内部形成初始缺陷,当复合材料进行形状记忆测试时,这些缺陷会逐步扩展 为裂纹或分层,从而引发复合材料的失效,严重阻碍复合材料的形状记忆性能。
[0196]
当复合材料没有进行真空浸渗过程时,会使复合材料内部基体浸渗不充分,造成 部分区域基体聚集,部分区域缺乏基体产生少基体区,在这些少基体区,没有基体附 着的纤维在形状记忆性能测试过程中会产生破坏失效,从而降低复合材料的形状记忆 能力。
[0197]
表3
[0198]