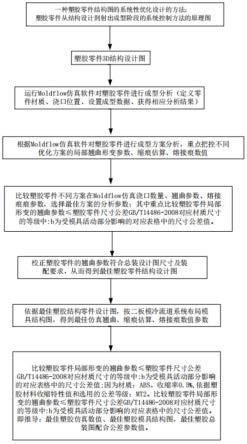
1.本发明属于工业自动化领域,尤其涉及一种塑胶零件结构图的系统性优化设计的方法。
背景技术:2.人机界面(human machine interaction,简称hmi)。人机界面(又称用户界面或使用者界面)是系统和用户之间进行交互和信息交换的媒介,它实现信息的内部形式与人类可以接受形式之间的转换。凡参与人机信息交流的领域都存在着人机界面。随着工业自动化的发展,嵌入式、立式、吊臂式的通讯设备不断推出新产品应用于自动化领域。其整机品质是由关键的塑胶零件主控模块塑胶后盖及其它关键零件的品质决定。
3.塑胶零件主控模块塑胶后盖在零件结构设计阶段即可实现到整机装配环节对其各个阶段不利因素进行分析预判,我们针对塑胶零件结构设计图进行系统性优化设计,以满足塑胶零件尺寸公差及塑胶零件总装图的技术要求。塑胶零件的品质异常包含:缩水、料花、流纹、零件局部翘曲形变、熔接痕等缺陷,造成塑胶零件品质异常因素:塑胶零件结构设计是否合理、塑胶零件结构设计图是否经过专业塑胶模流分析软moldflow进行分析并针对塑胶零件结构设计图细节问题进行改进,以满足塑胶零件尺寸公差及塑胶零件总装图的零件的装配技术要求。同时我们有必要对后端的塑胶模具结构进行设计,如果后端塑胶模具结构设计不理想,从整个系统环节来讲是不利的,会导致前端新产品品质缺陷,开发周期过长,研发投入风险加大,如果塑胶模具结构设计不理想,后端反复休模、试模、严重情况甚至导致塑胶模具报废等不确定因素产生。因此一种塑胶零件结构图的系统性优化设计的方法是我们结构设计工程师把握前端塑胶零件结构设计及掌控后端塑胶模具设计成功的“法宝”。
4.专利号cn108549764a公开的一种基于moldflow分析的汽车仪表结构优化方法,但其存在以下缺陷:
5.1、技术核心moldflow没有提出塑胶零件最佳进浇点,没有提出最佳进浇点数量,没有提出涉及模具结构细节,仅把期待寄托给后端的模具工程师和模具调机工程师,不能确保塑胶零件尤其是复杂塑胶零件的品质;
6.2、其对模具结构及产品研发中的塑胶零件品质整体把控认识存在局限,甚至没有提及后端塑胶模具流道系统结构、塑胶模具结构设计方案、塑胶模具最佳进浇点、塑胶模具最佳进浇点数量;
7.3、塑胶模具最佳进浇点及最佳浇口数量这一moldflow仿真分析软件的核心技术部分没有提及,这不仅涉及模具结构、涉及模具结构简易程度、更涉及模具费用、涉及moldflow塑胶零件仿真分析最佳准确率报告的质量,甚至该发明的moldflow塑胶零件仿真分析报告衔接后端模具工程师时候会误导模具结构设计师,导致模具结构设计存在缺陷隐患。
8.cn108549764a发明专利存在本质的技术缺陷、无法解决实质性的问题:即如何避
免和降低塑胶零件缺陷。如果后端模具工程师参考其塑胶零件moldflow分析报告资料,甚至会给模具结构设计带来隐患,甚至可以推断该发明专利中的塑胶零件结构图不是最佳结构设计方案。
技术实现要素:9.本发明目的在于提供一种塑胶零件结构图的系统性优化设计的方法,以解决传统的上游研发创新型企业产品结构设计工程师&下游制造企业模具设计工程师&模具维护工程师&模具试模工程师,多凭经验来设计、制作及生产塑胶零件,没有系统性的整合控制方法,导致上游研发创新型企业、下游制造企业设计、制作、生产塑胶零件的成本高、生产效率低、塑胶零件质量异常的技术问题。
10.为解决上述技术问题,本发明的具体技术方案如下:
11.一种基于塑胶零件结构图的系统性优化设计方法,其特征在于,包括以下步骤:
12.步骤1、建立塑胶零件的三维结构设计图方案一,运行moldflow完成对该塑胶零件的分析报告,关注塑胶零件翘曲变形数值;
13.步骤2、评估塑胶零件翘曲变形参数,对比塑胶零件总装图分析出是否需要对塑胶零件进行局部结构优化,即是否需要对塑胶零件的结构设计图进行局部优化改进;如需改进,将改进后的塑胶零件的三维结构设计图方案二进行如步骤1的方法进行分析,关注塑胶零件翘曲变形数值;
14.步骤3、若塑胶零件局部翘曲参数大,则在三维软件中针对塑胶零件局部翘曲部分进行方案三的设计优化,将改进后的塑胶零件的三维结构设计图方案三进行如步骤1的方法进行分析,关注塑胶零件翘曲变形数值;
15.步骤4、依据塑胶零件尺寸公差gb/t14486-2008核对塑胶零件的最大形变翘曲值,结合塑胶零件选用的材质,自定义塑料塑模件公差等级的选用级别,即选择出高精度或一般精度;根据塑胶零件总装图配合公差精度要求及塑胶零件尺寸公差表中公差等级,即判断出改进后的三维模型是否为最佳结构图优化方案,同时判断出改进后的三维模型在moldflow分析报告中的塑胶零件最大翘曲参数是否达到塑胶零件尺寸公差gb/t14486-2008选用的公差级别;
16.步骤5、将塑胶零件三维模型的优化方案、塑胶模型方案在moldflow分析报告中最大翘曲值、gb/t14486-2008中塑胶零件尺寸公差选用级别对比,得到塑胶零件最佳的塑胶零件最佳结构设计图方案、塑胶零件最佳尺寸公差等级选用方案,同时依据gb/t14486-2008定义塑胶模具公差等级;
17.步骤6、依据塑胶零件最佳结构设计图方案、塑胶零件最佳结构设计图方案的moldflow的最佳浇口进行塑胶模具结构设计,得出最佳塑胶零件的模具结构设计图。
18.进一步的,所述步骤1具体包括以下步骤:
19.步骤1.1、通过三维软件建立塑胶零件的三维结构设计图方案一;
20.步骤1.2、将建立的塑胶零件的三维结构设计图方案一导入moldflow软件进行诊断;
21.步骤1.3、根据步骤1.2得到的诊断结果对塑胶零件的三维结构设计图方案一进行修复,当主菜单错误信息显示为0时导出moldflow study文件;
22.步骤1.4、将步骤1.3导出的moldflow study文件导入新建的moldflow软件,moldflow软件自动建立塑胶零件仿真系统;
23.步骤1.5:在步骤1.4中塑胶零件仿真系统中创建网格,得到生成的网格窗口;
24.步骤1.6:在得到生成的网格窗口中设置全局边长参数,自定义网格匹配和计算双层面网格的厚度,立即划分网格;
25.步骤1.7:网格划分完成后,进行双层面网格统计,并根据网格划分的结果进行网格修复;
26.步骤1.8:在系统工程任务中点击重复,点击新生成的任务系统,点击填充,设置分析序列,选择浇口位置;系统自动生成浇口位置;
27.步骤1.9:进行工艺设置,双击工艺设置进入浇口位置设置,选择浇口区域定位器,点击高级选项完成工艺设置;
28.步骤1.10:点击开始分析,生成最佳浇口位置结果;
29.步骤1.11:基于生成最佳浇口位置项目,点击重复,生成新的系统项目;选择新生成的项目,选择浇口位置,设置分析序号:填充+保压+翘曲;
30.步骤1.12:设置塑胶材料,完成塑胶零件的材质设置;
31.步骤1.13:进行工艺设置,双击工艺设置进入浇口位置设置,选择浇口区域定位器,点击高级选项,完成工艺设置;
32.步骤1.14:系统自动判断以上设置是否正确;若设置异常,调整设置参数;若设置正常,开始分析;
33.步骤1.15:完成分析后,塑胶零件品质异常结果中关注锁模力参数;
34.步骤1.16:根据塑胶零件最大长度尺寸439mm,选择gb/t14486-2008高精度mt2a=1.1,b=1.2,a为不受模具活动部分影响的尺寸公差值;b为受模具活动部分影响的尺寸公差值;判断该塑胶零件moldflow分析报告中的翘曲参数是否与自定义公差级别精度吻合。
35.进一步的,所述步骤1.6中全局边长数组的数值设置为塑胶零件平均厚度的60%。
36.进一步的,步骤2对比塑胶零件仿真结果中翘曲变形与gb/t14486-2008高精度,得到塑胶零件尺寸公差参数范围,即求得塑胶零件翘曲值参数范围;若翘曲形变稍大,用solidworks软件对塑胶零件进行模型优化,即得到塑胶零件的三维结构设计图方案二。
37.进一步的,步骤6用ug软件布局塑胶零件的模具结构图,包含塑胶模具排气系统,塑胶模具水路系统,塑胶模具浇口流道系统,得到最佳的二板模冷流道塑胶模具结构图。
38.本发明的一种塑胶零件结构图的系统性优化设计的方法,具有以下优点:
39.1、本发明提供了适用于统筹上游创新型企业、下游模具行业针对塑胶零件品质缺陷的快速、高效、系统性的解决方案。先后推导得出最佳塑胶零件结构图、最佳塑胶零件的moldflow模流分析报告、塑胶零件的最佳流道系统和最佳塑胶模具结构图,本发明塑胶零件结构设计图方案(1个侧浇口)翘曲数值:2.354mm,优化改善后塑胶零件结构设计图方案(1个侧浇口)翘曲数值:0.9986mm;翘曲率约降低了135%;最佳二板模冷流道的模具结构较热流道模具费用约降低50%的模具费用;一并降低了塑胶零件成型出模后的塑胶零件的整型治具的费用若干。同时避免了从上游结构设计阶段到塑胶零件模具制作、加工、生产零件环节塑胶零件品质风险、规避模具结构设计风险、规避塑胶零件结构设计风险、规避塑胶模具维保风险、规避塑胶模具调机试模工程师反复试模风险。
40.2、本发明提出的快速、高效、系统性解决塑胶零件品质异常问题的方法,力荐由上游创新型企业结构工程师主导,改变目前上游创新型企业及下游模具设计、制造、生成型企业的运用、合作模式;为上游研发创新型企业产品结构工程师、下游制造企业模具设计工程师、下游制造企业模具维保工程师、下游制造企业模具试模工程师架起一座技术沟通的桥梁。为上、下游创新、创造型企业建立新的有益、高效、良性循环的沟通及合作体制破除技术壁垒。
41.3、本发明降低了上游创新型企业塑胶结构工程师、下游制造企业模具设计工程师、下游制造企业模具维保工程师、下游制造企业模具试模工程师分析、解决塑胶零件品质问题的技术门槛,因为本发明的特点:快速、高效、系统性助力不仅解决了塑胶品质缺陷问题、降低塑胶零件设计成本、沟通成本、管理成本。
42.4、本发明实现塑胶零件满足gb/t14468-2008对应的高精度级别,从而满足塑胶零件外观、翘曲尺寸公差、塑胶零件整机装配、塑胶零件基于整机功能要求。避免塑胶零件设计风险、塑胶模具结构设计风险、塑胶模具维保风险、塑胶零件品质异常风险。为解决制造业“卡脖子”技术问题提供助力,为推进国家“智能制造2025”创造无限可能,同时提升产品质量、企业竞争力。
附图说明
43.图1为本发明的立式、吊臂式、嵌入式人机界面总装结构的示意图;
44.图2为本发明的立式、吊臂式、嵌入式人机界面总装的通用主控模块及人机界面主控模块软胶套、人机界面吊臂的结构示意图;
45.图3为本发明的塑胶零件结构设计方案一在塑胶模具中的一个最佳浇口位置的moldflow仿真分析报告示意图;
46.图4为本发明的塑胶零件结构设计方案一在塑胶模具中的一个最佳浇口位置的moldflow仿真分析示报告中的塑胶翘曲变形示意图;
47.图5为本发明的塑胶零件结构设计方案一在塑胶模具中的一个最佳浇口位置的moldflow仿真分析示报告中的塑胶熔接线示意图;
48.图6为本发明的塑胶零件结构设计方案一在塑胶模具中的一个最佳浇口位置的moldflow仿真分析示报告中的塑胶缩痕估算示意图;
49.图7为本发明的塑胶零件结构设计方案二在塑胶模具中的二个最佳浇口位置的moldflow仿真分析示报告中的翘曲变形示意图;
50.图8为本发明的塑胶零件结构设计方案二在塑胶模具中的一个最佳浇口位置moldflow仿真分析报告示意图;
51.图9为本发明的塑胶零件结构设计方案二在塑胶模具中的一个最佳浇口位置的moldflow仿真分析示报告中的翘曲变形示意图;
52.图10为本发明的塑胶零件结构设计方案三在塑胶模具中的一个最佳浇口位置moldflow仿真分析报告示意图;
53.图11为本发明的塑胶零件结构设计方案三在塑胶模具中的一个最佳浇口位置moldflow仿真分析报告翘曲变形示意图;
54.图12为本发明的塑胶零件结构设计方案三在塑胶模具中的一个最佳浇口位置
moldflow仿真分析报告缩痕估算示意图;
55.图13为本发明的塑胶零件结构设计方案三在塑胶模具中的一个最佳浇口位置moldflow仿真分析报告熔接线示意图;
56.图14为本发明的塑胶零件结构设计图方案一优化前尺寸示意图;
57.图15为本发明的塑胶零件结构设计图方案一优化前总装示意图;
58.图16为本发明的塑胶零件结构设计图方案四优化后尺寸示意图;
59.图17为本发明的塑胶零件结构设计图方案四优化后总装示意图;
60.图18为本发明的一种塑胶零件从结构设计到射出成型阶段的系统控制方法的示意图;
61.图19为本发明的一种塑胶零件从结构设计到射出成型阶段的系统控制方法的原理示意图;
62.图20为本发明的塑胶零件结构设计图方案四进行模具设计的二板模冷流道系统及浇口示意图;
63.图21为本发明的塑胶零件结构设计图方案四进行模具设计的二板模冷流道系统定模(前模);
64.图22为本发明的塑胶零件结构设计图方案四进行模具设计的二板模冷流道系统动模(后模);
65.图23为本发明的塑胶零件结构设计图方案四进行模具设计的二板模冷流道系统的定模(前模)和动模(后模)在moldflow仿真报告中的锁模力示意图;
66.图中标记说明:1、吊臂式人机界面系统设备;2、人机界面主控模块铝合金面板;3、人机界面主控模块内支撑板;4、人机界面主控模块塑胶后盖;5、人机界面主控模块软胶套;6、人机界面吊臂。
具体实施方式
67.为了更好地了解本发明的目的、结构及功能,下面结合附图,对本发明一种塑胶零件结构图的系统性优化设计的方法做进一步详细的描述。
68.如图1所示,立式、吊臂式、嵌入式人机界面操作界面系统由通用组件人机界面主控模块及其它部件组成,人机界面主控模块与人机界面吊臂6组合为吊臂式人机界面系统1,其中人机界面主控模块为通用部件。
69.如图2所示人机界面主控模块由人机界面主控模块铝合金面板2、人机界面主控模块内支撑板3、人机界面主控模块塑胶后盖4、人机界面主控模块软胶套5组成。
70.如图18和图19所示,本发明包括以下步骤:
71.步骤1、建立塑胶零件的三维结构设计图方案一,运行moldflow完成对该塑胶零件分析报告,关注塑胶零件翘曲变形数值。
72.具体包括以下步骤:
73.步骤1.1、通过三维软件建立塑胶零件的三维结构设计图方案一,如图3所示,人机界面主控模块塑胶后盖4的塑胶零件的三维结构设计图方案一在moldflow软件中,设置浇口数量1个,分析塑胶零件模具结构中1个最佳浇口位置。
74.步骤1.2、将建立的塑胶零件的三维结构设计图方案一导入moldflow软件进行诊
断;
75.步骤1.3、根据步骤1.2得到的诊断结果对塑胶零件的三维结构设计图方案一进行修复,当主菜单错误信息显示为0时导出moldflow study文件;
76.步骤1.4、将步骤1.3导出的moldflow study文件导入新建的moldflow软件,moldflow软件自动建立塑胶零件仿真系统;
77.步骤1.5:在步骤1.4中塑胶零件仿真系统中创建网格,得到生成的网格窗口;
78.步骤1.6:在得到生成的网格窗口中设置全局边长参数,自定义网格匹配和计算双层面网格的厚度,立即划分网格;
79.步骤1.7:网格划分完成后,进行双层面网格统计,并根据网格划分的结果判断是否需要进行网格修复;
80.步骤1.8:在系统工程任务中点击重复,点击新生成的任务系统,点击填充,设置分析序列,选择浇口位置;系统自动生成浇口位置;
81.步骤1.9:进行工艺设置,双击工艺设置进入浇口位置设置,选择浇口区域定位器,点击高级选项完成工艺设置;
82.步骤1.10:点击开始分析,生成最佳浇口位置结果;
83.步骤1.11:基于生成最佳浇口位置项目,点击重复,生成新的系统项目;选择新生成的项目,选择浇口位置,设置分析序号:填充+保压+翘曲;
84.步骤1.12:设置塑胶零件的材质,完成材料设置;
85.步骤1.13:进行工艺设置,双击工艺设置进入浇口位置设置,选择浇口区域定位器,点击高级选项,自定义相关选项进行参数设置完成工艺设置;
86.步骤1.14:系统自动判断以上设置是否正确;若设置异常,调整设置参数;若设置正常,开始分析;
87.步骤1.15:完成分析后,塑胶零件品质异常结果中关注锁模力参数,如图23所示,该参数适用衔接选择处下游塑胶零件射出成型的机台吨位;
88.步骤1.16:根据塑胶零件最大长度尺寸439mm,选择gb/t14486-2008高精度mt2a=1.1,b=1.2,a为不受模具活动部分影响的尺寸公差值;b为受模具活动部分影响的尺寸公差值;判断该塑胶零件moldflow分析报告中的翘曲参数是否与自定义级别精度吻合。
89.步骤2、评估塑胶零件翘曲变形参数,对比塑胶零件总装图分析出是否需要对塑胶零件进行局部结构优化,即是否需要对塑胶零件的结构设计图进行局部优化改进;如需改进,将改进后的塑胶零件的三维结构设计图方案二进行如步骤1的方法进行分析,关注塑胶零件翘曲变形数值;如图8所示,用solidworks软件基于moldflow分析的塑胶零件的三维结构设计图方案一的翘曲变形部分优化塑胶零件,即塑胶零件的三维结构设计图方案二用moldflow计算1个最佳浇口位置,完成分析后查询该塑胶零件设置1个浇口位置,显示最佳浇口位置区域:即流动阻力指示器。
90.步骤3、若塑胶零件局部翘曲参数大,在三维软件中针对塑胶零件局部翘曲部分进行方案三的设计优化,将改进后的塑胶零件的三维结构设计图方案三进行如步骤1的方法进行分析,关注塑胶零件翘曲变形数值。
91.步骤4、依据塑胶零件尺寸公差gb/t14486-2008核对塑胶零件的最大形变翘曲值,结合塑胶零件选用的材质,得出塑料塑模件公差等级的选用级别,即选择出高精度或一般
精度;根据塑胶零件总装图配合公差精度要求及塑胶零件尺寸公差表中公差等级,即判断出改进后的三维模型是否为最佳结构图优化方案,同时判断出改进后的三维模型在moldflow分析报告中的塑胶零件最大翘曲参数是否达到塑胶零件尺寸公差gb/t14486-2008选用的公差级别;
92.步骤5、将塑胶零件三维模型的优化方案、塑胶模型方案在moldflow分析报告中最大翘曲值、gb/t14486-2008中塑胶零件尺寸公差选用级别对比,得到塑胶零件最佳的塑胶零件最佳结构设计图方案、塑胶零件最佳尺寸公差等级选用方案,同时依据gb/t14486-2008定义塑胶模具公差等级;
93.步骤6、依据塑胶零件最佳结构设计图方案、塑胶零件最佳结构设计图方案的moldflow的最佳浇口进行塑胶模具结构设计,得出最佳塑胶零件的模具结构设计图。
94.如图3所示,hmi主控模块塑胶后盖4的塑胶零件结构图方案一模型在moldflow软件中,设置浇口数量1个,分析塑胶零件模具结构中1个最佳浇口位置,分析出hmi主控模块塑胶后盖4的熔接线,发现熔接线会影响塑胶零件外观,如图5。如图3所示,hmi主控模块塑胶后盖4的塑胶零件结构图方案一模型在moldflow软件中,设置浇口数量1个,分析塑胶零件模具结构中1个最佳浇口位置,分析出hmi主控模块塑胶后盖4的缩痕估算最大值的参数:0.0524mm,如图6所示;
95.如图4所示,人机界面主控模块塑胶后盖4的三维结构设计图方案一在moldflow软件中,通过建立最佳浇口位置、设置塑胶材料:abs,制造商:chi mei corporation,牌号:polylac pa-746h,点击确定完成材料设置;完成设置注射位置、工艺设置并完成塑胶零件的三维结构设计图方案一的仿真分析结果,重点关切塑胶零件翘曲变形参数:局部最大形变尺寸2.354mm。查询零件材质abs,收缩率0.5%,根据gb/t 14486-2008塑胶材料收缩特性及常用材料模塑件尺寸公差等级选用高精度mt2;那么塑胶零件最大尺寸438.4mm对应到到模塑件尺寸公差表,寻找塑胶零件尺寸公差表查得高精度mt2对应的数值a和数值b;a为不受模具活动部分影响的尺寸公差值,b为受模具活动部分影响的尺寸公差值。推导出那么塑胶零件最大尺寸438.4mm的高精度公差尺寸范围:1.1mm至1.2mm,显然塑胶零件的三维结构设计图方案一的仿真最大翘曲变形值为2.354mm,如图4,因此判定塑胶零件的三维结构设计图方案一结构设计图不合格,需要对其进行优化,优化后的塑胶零件的三维结构设计图方案二,因为如图6。
96.如图7所示,用solidworks软件基于moldflow的翘曲变形部分,优化塑胶零件,即塑胶零件结构图方案二用moldflow计算2个最佳浇口位置,设置moldflow工艺参数,完成分析后查询塑胶零件最大翘曲变形参数:2.055mm,图15和图16中查询零件材质abs,收缩率0.5%,根据gb/t 14486-2008塑胶材料收缩特性及常用材料模塑件尺寸公差等级选用高精度mt2;那么塑胶零件最大尺寸438.4mm对应到图14,寻找塑胶零件尺寸公差表查得高精度mt2对应的数值a和数值b;a为不受模具活动部分影响的尺寸公差值,b为受模具活动部分影响的尺寸公差值。推导出那么塑胶零件最大尺寸438.4mm的高精度公差尺寸范围:1.1mm至1.2mm,显然塑胶零件结构图方案一的仿真翘曲值为2.354mm,如上图4,塑胶零件结构图方案二的仿真翘曲值为1.398mm,因此判定塑胶零件结构图方案一、二结构设计图不合格,需要对其进行优化,优化后的塑胶零件结构图方案三,因为如下图10。比较以图3至图7中设置1个浇口和2个浇口两种不同的塑胶模具结构,基于moldflow分析结果对塑胶零件结构设计
和塑胶零件模具结构趋势进行评估,其对塑胶零件结构工程师改进塑胶零件结构图方案三如图10有帮助。
97.如图9所示,用solidworks软件基于moldflow分析的塑胶零件的三维结构设计图方案一的翘曲变形部分优化塑胶零件,即塑胶零件的三维结构设计图方案二用moldflow计算1个最佳浇口位置,按图4所示,人机界面主控模块塑胶后盖4的塑胶零件的三维结构设计图方案一在moldflow软件中,通过建立最佳浇口位置、设置塑胶材料:abs,制造商:chi mei corporation,牌号:polylac pa-746h,点击确定完成材料设置;完成设置注射位置、工艺设置并完成塑胶零件的三维结构设计图方案二的仿真分析结果内容进行设置,完成分析后查询该塑胶零件最大翘曲变形参数值:1.398mm。根据gb/t 14486-2008查询零件材质abs,收缩率0.5%,根据gb/t 14486-2008塑胶材料收缩特性及常用材料模塑件尺寸公差等级选用高精度mt2;那么塑胶零件最大尺寸438.4mm对应到到模塑件尺寸公差表,寻找塑胶零件尺寸公差表查得高精度mt2对应的数值a和数值b;a为不受模具活动部分影响的尺寸公差值,b为受模具活动部分影响的尺寸公差值。推导出那么塑胶零件最大尺寸438.4mm的高精度公差尺寸范围:1.1mm至1.2mm,显然塑胶零件的三维结构设计图方案一的仿真翘曲值为1.398mm,如图4,因此判定塑胶零件的三维结构设计图方案二结构设计图不合格,需要对其进行优化,优化后的塑胶零件的三维结构设计图方案三。
98.如图10所示,用solidworks软件优化出的塑胶零件的三维结构设计图方案三,用moldflow计算出1个浇口状态的最佳浇口位置区域。
99.如图11所示,用solidworks软件优化出的塑胶零件结构图方案三,用moldflow计算出1个浇口状态的hmi主控模块塑胶后盖4的结构设计图方案三的最大翘曲变形量为0.9986mm。gb/t 14486-2008中查询零件材质abs,收缩率0.5%,根据gb/t 14486-2008塑胶材料收缩特性及常用材料模塑件尺寸公差等级选用高精度mt2;那么塑胶零件最大尺寸438.4mm对应到图14,寻找塑胶零件尺寸公差表查得高精度mt2对应的数值a和数值b;a为不受模具活动部分影响的尺寸公差值,b为受模具活动部分影响的尺寸公差值。推导出那么塑胶零件最大尺寸438.4mm的高精度公差尺寸范围:1.1mm至1.2mm,显然塑胶零件结构图方案三的仿真翘曲值为0.9986mm,如上图10,因此判定塑胶零件结构图方案三的结构设计图合格,为塑胶零件结构优化设计及塑胶零件模具结构设计提供了趋势判定方向。
100.如图12所示,塑胶零件结构图方案三如图10的在moldflow软件中设置1个最佳浇口位置,得到缩痕估算的最大参数:0.0388mm,涉及塑胶零件结构图方案三如图10的塑胶模具成型零件外观。
101.如图13所示,塑胶零件结构图方案三如上图10的在moldflow软件中设置1个最佳浇口位置,得到熔接线:涉及塑胶零件结构图方案三如上图10的塑胶模具成型零件件外观。
102.基于塑胶零件尺寸公差表gb/t 14486-2008,基于moldflow涉及最佳塑胶结构零件hmi主控模块后盖4塑胶零件结构图方案一如图三。
103.如图15所示,hmi主控模块后盖4的塑胶零件结构图方案一如图三总装。
104.如图16所示,hmi主控模块后盖4的塑胶零件结构图方案四如图19,依据塑胶模型结构图三在moldflow的翘曲变形量为0.9986mm,同时主控模块软胶套5的材质为软胶零件,定义hmi主控模块后盖4与主控模块软胶套5两个零件装配过盈量约0.2mm即可,那么我们可以定义hmi主控模块后盖4与主控模块软胶套5两个零件之间装配间隙为0.8mm,即塑胶零件
结构图方案四为最佳塑胶零件结构图。
105.如图17所示,得到hmi主控模块后盖4最佳结构模型图方案四如图16,即hmi主控模块后盖4翘曲变形影响总装尺寸3.8mm改进为3mm,满足塑胶零件整机的总装配图尺寸公差要求。
106.如图20所示,由最佳hmi主控模块后盖4塑胶零件结构图方案四和moldflow分析数据推导出该塑胶零件的模具射出成型图。
107.如图21所示,由最佳hmi主控模块后盖4塑胶零件结构图方案四和1个最佳侧进胶浇口位置快速设计最佳hmi主控模块后盖4塑胶零件结构图方案四的模具结构图二板模冷流道定模部分。
108.如图22所示,由最佳hmi主控模块后盖4塑胶零件结构图方案四和1个最佳侧进胶浇口位置快速设计最佳hmi主控模块后盖4塑胶零件结构图方案四的模具结构图二板模冷流道动模部分。
109.即:通过一种塑胶零件结构图的系统性优化设计的方法,可以得到最佳塑胶零件结构图、最佳塑胶模流分析图、最佳塑胶模具结构图,最佳塑胶零件总装图。
110.可以理解,本发明是通过一些实施例进行描述的,本领域技术人员知悉的,在不脱离本发明的精神和范围的情况下,可以对这些特征和实施例进行各种改变或等效替换。另外,在本发明的教导下,可以对这些特征和实施例进行修改以适应具体的情况及材料而不会脱离本发明的精神和范围。因此,本发明不受此处所公开的具体实施例的限制,所有落入本技术的权利要求范围内的实施例都属于本发明所保护的范围内。