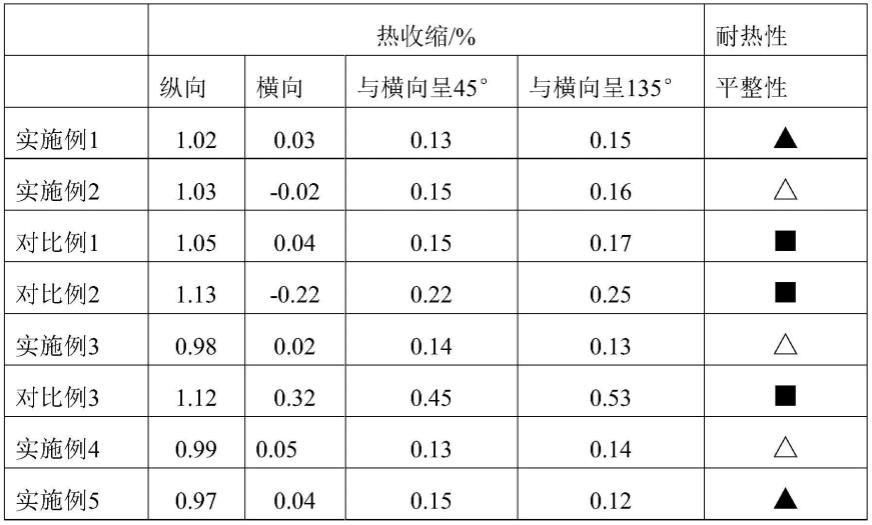
1.本发明涉及薄膜及制造技术领域,具体涉及一种高平整度耐热聚酯薄膜的制备方法及聚酯薄膜。
背景技术:2.随着全球智能终端的多元化发展,对高端显示屏的品质和性能要求越来越高。氧化铟锡(ito)发展至今技术成熟,在透明导电膜市场占主导地位,但无法满足电子产品向可弯曲、可折叠和可卷等柔性发展的趋势。柔性显示作为新一代显示技术的代表,其可塑性的优势广泛应用于多种场景的显示器,柔性显示包括透明导电膜和柔性基膜。在导电膜的制造过程经过许多加热步骤和化学处理步骤,作为导电膜的基膜热稳定性欠佳时,基膜出现热褶皱,导致基膜平面不平整,基膜上的镀层或涂层也不均,影响导电膜的光学性能和品质。而聚酯薄膜常作为导电膜的基膜,因此,所需聚酯薄膜具有耐热性。
3.在膜的制备方法中,连续的双轴拉伸包括在制备过程中沿膜运行方向的拉伸为纵向(md)拉伸,沿膜宽幅方向的拉伸为横向(td)拉伸。通常md拉伸过程膜在td方向收缩发生颈缩现象。产生颈缩后,进行td方向上的拉伸产生实际伸长量比所需伸长量大,实际伸长量与所需伸长量的差值不仅引起膜断裂,降低膜的生产效率,且导致膜厚度的均匀性欠佳,也增加了拉伸设备的机械负荷。聚酯薄膜双向拉伸后的厚度均匀性是影响耐热性的因素之一,进而保证基膜的平整度。
技术实现要素:4.本发明的目的之一在于克服现有技术中存在的缺陷,提供一种高平整度耐热聚酯薄膜的制备方法,铸片的横截面沿横向包括主体部、侧边部及连接主体部和侧边部的过渡部,通过渡部的厚度沿横向由两侧向中部逐渐减小的设置,有效解决由于膜拉伸产生颈缩后导致膜厚度均匀性欠佳的问题。
5.为了实现上述工艺效果,本发明的技术方案为:一种高平整度耐热聚酯薄膜的制备方法,包括以下步骤:
6.s1:聚酯薄膜的原料熔融,铸片成型;
7.s2:成型铸片预热,纵向拉伸,冷却;
8.s3:s2所得铸片依次经预热、加热同时横向拉伸、热定型和冷却,制得所述聚酯薄膜;
9.所述铸片的横截面沿横向包括主体部、侧边部及连接所述主体部和侧边部的过渡部,所述铸片的顶面和底面以沿厚度方向中点的集合面为对称面,所述过渡部的厚度沿横向由两侧向中部逐渐减小;所述铸片的最大厚度与最小厚度差为12~40μm;所述铸片基材的特性粘度为0.62~0.75dl/g。
10.为了优化铸片横截面的厚度变化趋势,优选的技术方案为,所述主体部的厚度为300~2000μm,所述主体部的厚度为d1,所述过渡部的最小厚度为d2,所述侧边部的厚度为
d3,d1:d2:d3=(1.005~1.2):1:(1.002~1.12)。
11.为了优化铸片最小厚度的设定位置,铸片拉伸后厚度达到最佳的均匀性,优选的技术方案为,所述铸片的幅宽为1600~1800mm,两个所述过渡部最小厚度处之间的距离为l1,所述过渡部的最小厚度处至铸片侧边的最小距离为l2,l2:l1=1:4~6。过渡部的最小厚度处至铸片一侧边的距离为较大距离,至铸片另一侧边的距离为最小距离。进一步的,l2:l1=1:4.4~5.6。更进一步的,l2:l1=1:4.6~5.5。
12.铸片幅宽两侧因纵向拉伸产生颈缩,因此铸片幅宽两侧的厚度增加,为了提高铸片幅宽两侧厚度增量的对称性,进而提高铸片拉伸后厚度达到最佳的均匀性,优选的技术方案为,所述s2中纵向拉伸倍率为2.2~3.8,所述纵向拉伸的温度为85~115℃。
13.为了进一步提高铸片幅宽两侧厚度增量的对称性,优选的技术方案为,所述纵向拉伸施加于所述横截面的单位面积张应力为3.5n/mm2~12n/mm2。进一步的,纵向拉伸施加于横截面的单位面积张应力为5n/mm2~10n/mm2。
14.为了进一步提高铸片纵向拉伸后厚度的均匀性,优选的技术方案为,所述纵向拉伸的拉伸辊包括第一拉伸辊和第二拉伸辊,所述铸片包覆于所述第一拉伸辊的包角为∠1,88
°
≤∠1≤95
°
;所述铸片包覆于所述第二拉伸辊的包角为∠2,60
°
≤∠2≤65
°
。进一步的,90
°
≤∠1≤95
°
,61
°
≤∠2≤64
°
。
15.为了保证铸片中聚合物分子结构热定型后的稳定性,且提高铸片厚度的均匀性,优选的技术方案为,所述s3中冷却包括依次的第一冷却段和第二冷却段,所述第一冷却段的温度为180~120℃,所述第二冷却段的温度为100~80℃。
16.为了防止铸片高温定型后因分子链豫驰而影响厚度均匀性和薄膜机械性能,优选的技术方案为,所述第一冷却段前铸片的横向宽度为l0,所述第二冷却段后铸片的横向宽度为l1,所述l0与l1的宽度差占l0的百分比为横向收缩率;所述冷却的总时间为t,所述横向收缩率与t比值为横向收缩速率;所述s3中冷却后铸片的横向收缩速率为0.1%~8%/s。进一步的,s3中冷却后铸片的横向收缩速率为0.1%~5%/s。更进一步的,s3中冷却后铸片的横向收缩速率为0.1%~3%/s。
17.为了提高铸片横向拉伸后厚度的均匀性,优选的技术方案为,所述s3中横向拉伸倍率为3.2~4.2,所述横向拉伸的温度为105~120℃。进一步的,横向拉伸倍率为3.3~4.1,横向拉伸的温度为115~120℃。
18.为了经拉伸后薄膜在应力作用下发生缓慢弹性变形或释放应力,改善铸片厚度的均匀性,优选的技术方案为,所述热定型的温度为240~255℃。进一步的,热定型的温度为245~255℃。
19.本发明的目的之二在于克服现有技术中存在的缺陷,提供一种高平整度耐热聚酯薄膜,所述聚酯薄膜由上述的高平整度耐热聚酯薄膜的制备方法制得。
20.本发明的优点和有益效果在于:
21.该发明的铸片横截面沿横向包括主体部、侧边部及连接主体部和侧边部的过渡部,通过过渡部的厚度沿横向由两侧向中部逐渐减小的设置,有效解决由于聚酯薄膜拉伸产生颈缩后导致膜厚度均匀性欠佳的问题,进而提高拉伸后聚酯薄膜的耐热性,保证聚酯薄膜作为导电膜的基膜具备良好的平整性。
附图说明
22.图1是本发明实施例1铸片横截面的结构示意图。
23.图中,1、横截面;10、主体部;11、侧边部;12、过渡部。
具体实施方式
24.下面结合实施例,对本发明的具体实施方式作进一步描述。以下实施例仅用于更加清楚地说明本发明的技术方案,而不能以此来限制本发明的保护范围。
25.聚酯薄膜的原料
26.基材1的特性粘度为0.675dl/g;
27.基材2的特性粘度为0.74dl/g;
28.基材3的特性粘度为0.8dl/g;
29.基材4的特性粘度为0.61dl/g。
30.铸片横截面的结构
31.进一步的,铸片主体部的厚度一致或趋于一致。
32.特性粘度
33.特性粘度是考量聚酯物性的重要指标,铸片基材的特性粘度是保证耐热性的主要因素,聚酯的分子量大,特性粘度大,成正比关系。进一步的,铸片基材的特性粘度为0.650~0.720dl/g。更进一步的,铸片基材的特性粘度0.65~0.70dl/g。
34.铸片的最大厚度与最小厚度差设置
35.铸片的最大厚度与最小厚度差根据主体部的厚度设置,且根据实际产品的膜厚设置;
36.铸片的主体部厚度为300~1000μm,对于产品的膜厚为20~75μm,铸片的主体部厚度为1001~2000μm,对于产品的膜厚为75~125μm;
37.进一步的,主体部厚度为300~1000μm,铸片的最大厚度与最小厚度差为22~36μm;主体部厚度为1001~2000μm,铸片的最大厚度与最小厚度差为12~20μm。
38.进一步的,主体部厚度为300~1000μm,d1:d2:d3=(1.01~1.16):1:(1.006~1.05);主体部厚度为1001~2000μm,d1:d2:d3=(1.005~1.038):1:(1.002~1.025)。
39.单位面积张应力
40.第一拉伸辊和第二拉伸辊之间的拉伸间隙l、铸片任一横截面的相互作用力和横截面的面积共同决定单位面积张应力的大小;150mm≤l≤380mm。
41.横向拉伸的夹持部
42.夹持部设置于宽幅两侧,进一步的,夹持部设置于宽幅侧边缘向主体部延伸至10~12mm处。
43.实施例1
44.高平整度耐热聚酯薄膜的制备方法包括以下步骤:
45.s1:聚酯薄膜的原料熔融,铸片成型;
46.s2:成型铸片预热,纵向拉伸,冷却;
47.s3:s2所得铸片依次经预热、加热同时横向拉伸、热定型和冷却,制得聚酯薄膜;
48.铸片的横截面1沿横向包括主体部10、侧边部11及连接主体部10和侧边部11的过
渡部12,铸片的顶面和底面以沿厚度方向中点的集合面为对称面,过渡部12的厚度沿横向由两侧向中部逐渐减小。
49.铸片基材的型号为fg600;铸片基材的特性粘度为0.675dl/g。
50.主体部厚度为500μm,过度部的最小距离为472μm,侧边部厚度为480μm。铸片的最大厚度与最小厚度差为28μm。
51.铸片的幅宽为1620μm,两个过渡部最小厚度处之间的距离为1157μm,过渡部的最小厚度处至铸片侧边的最小距离为231.5μm。
52.s2中纵向拉伸倍率为3.2,纵向拉伸的温度为85℃。纵向拉伸施加于横截面的单位面积张应力为6.8n/mm2。纵向拉伸的拉伸辊包括第一拉伸辊和第二拉伸辊,铸片包覆于第一拉伸辊的包角为92
°
;铸片包覆于所述第二拉伸辊的包角为62
°
。
53.s3中横向拉伸倍率为3.6,横向拉伸的预热温度为95℃,横向拉伸的温度为115℃,热定型温度为245℃,第一冷却段的温度为150℃,第二冷却段的温度为80℃。冷却后铸片的横向收缩速率为3.2%/s。
54.高平整度耐热聚酯薄膜由上述的高平整度耐热聚酯薄膜的制备方法制得,所得聚酯薄膜的膜厚为45μm。
55.实施例2
56.实施例2基于实施例1,区别在于,铸片基材的型号为fg720a;铸片基材的特性粘度为0.74dl/g。
57.对比例1
58.对比例1基于实施例1,区别在于,铸片基材的型号为bg80a;铸片基材的特性粘度为0.8dl/g。
59.对比例2
60.对比例2基于实施例1,区别在于,铸片基材的型号为fo2;铸片基材的特性粘度为0.61dl/g。
61.实施例3
62.实施例3基于实施例1,区别在于,主体部厚度为300μm,过度部的最小距离为268μm,侧边部厚度为280μm。铸片的最大厚度与最小厚度差为32μm。
63.对比例3
64.对比例3基于实施例1,区别在于,主体部厚度为500μm,过度部的最小距离为455μm,侧边部厚度为477.75μm。铸片的最大厚度与最小厚度差为45μm。
65.实施例4
66.实施例4基于实施例1,区别在于,主体部厚度为1750μm,过度部的最小距离为1738μm,侧边部厚度为1753.6μm。铸片的最大厚度与最小厚度差为12μm。s2中纵向拉伸倍率为3.35,s3中横向拉伸倍率为3.8。高平整度耐热聚酯薄膜由上述的高平整度耐热聚酯薄膜的制备方法制得,所得聚酯薄膜的膜厚为125μm。其他不变,工艺条件和参数同实施例1。
67.实施例5
68.实施例5基于实施例4,区别在于,主体部厚度为1100μm,过度部的最小距离为1080μm,侧边部厚度为1091.88μm。铸片的最大厚度与最小厚度差为20μm。其他不变,工艺条件和参数同实施例4。
69.实施例6
70.实施例6基于实施例4,区别在于,主体部厚度为1750μm,过度部的最小距离为1710μm,侧边部厚度为1728μm。铸片的最大厚度与最小厚度差为40μm。其他不变,工艺条件和参数同实施例4。
71.对比例4
72.对比例4基于实施例4,区别在于,主体部厚度为1750μm,过度部的最小距离为1740μm,侧边部厚度为1741μm。铸片的最大厚度与最小厚度差为10μm。其他不变,工艺条件和参数同实施例4。
73.实施例7
74.实施例7基于实施例1,区别在于,铸片的幅宽为1620μm,两个过渡部最小厚度处之间的距离为1193.6μm,过渡部的最小厚度处至铸片侧边的最小距离为213.2μm。
75.实施例8
76.实施例8基于实施例1,区别在于,铸片的幅宽为1620μm,两个过渡部最小厚度处之间的距离为1041.4μm,过渡部的最小厚度处至铸片侧边的最小距离为289.3μm。
77.实施例9
78.实施例9基于实施例1,区别在于,纵向拉伸施加于横截面的单位面积张应力为3n/mm2。
79.实施例10
80.实施例10基于实施例1,区别在于,纵向拉伸施加于横截面的单位面积张应力为14n/mm2。
81.实施例11
82.实施例11基于实施例1,区别在于,s3中仅仅包括第一冷却段,第一冷却段的温度为120℃。
83.对比例5
84.对比例5基于实施例1,铸片的横截面沿横向未设置过渡部,主体部和侧边部的厚度趋于一致,铸片的顶面和底面以沿厚度方向中点的集合面为对称面;铸片的型号、厚度、宽幅、制备方法和工艺参数均与实施例1一致。
85.实施例和对比例的性能测试
86.(1)热收缩
87.在所得产品聚酯薄膜上采取5个样品,样品型号大小为a3,样品裁剪方向与聚酯薄膜的横向和纵向一致。将样品沿横向、纵向、与横向成45
°
和135
°
的方向均测量长度l
0i
并做上标识线,分别对应的数据为l
01
、l
02
、l
03
和l
04
,再将样品放置150℃烘箱内热处理30min,加热后取出冷却至常温,在对应标识线处测量长度l
1i
,分别对应的数据为l
11
、l
12
、l
13
和l
14
。其热收缩值=(l
1i-l
0i
)/l
0i
*100%。
88.(2)耐热性、平整度测试
89.在所得产品聚酯薄膜上采取5个样品,样品型号大小为1000mm
×
1000mm,将样品平铺在平整的黑色大理石板上,使用塞尺测量样张的角和边长与大理石板的间隙大小,并按照以下方法进行评级:在150℃经过30min热处理后,突起高度≥1mm且凸起深度l≥100mm突起数量的个数,及突起高度≥0.5mm且凸起深度l≥10mm突起数量的个数;
90.△
:突起高度≥1mm且凸起深度l≥100mm的突起数量≤2个,同时突起高度≥0.5mm且凸起深度l≥10mm的突起数量≤5个;
91.▲
:突起高度≥1mm且凸起深度l≥100mm的突起数量≤2个,同时突起高度≥0.5mm且凸起深度l≥10mm的突起数量≤6个;
92.■
:突起高度≥1mm且凸起深度l≥100mm的突起数量>2个或突起高度≥0.5mm且凸起深度l≥10mm的突起数量>6个;
93.其中
△
和
▲
合格,
■
为不合格。
94.实施例和对比例的测定结果如下表:
[0095][0096][0097]
产品满足的条件:热收缩性同时满足,纵向为0.8~1.2;横向为-0.1~0.1;与横向呈45
°
为-0.1~0.2;与横向呈135
°
为-0.2~0.3;
[0098]
对比实施例1、实施例2和对比例1,随着基材的特性粘度增大,其耐热性越好,但不利于纵向和横向拉伸,导致膜厚度均匀性变差,从而影响平整度。
[0099]
对比例1相较于实施例1,基材的特性粘度减小,其耐热性不佳,导致膜的平整度
差。
[0100]
对比实施例1、实施例3、实施例4和实施例5,主体部厚度为300~1000μm,d1:d2:d3=(1.01~1.16):1:(1.006~1.05);主体部厚度为1001~2000μm,d1:d2:d3=(1.005~1.038):1:(1.002~1.025),所得产品热收缩性、耐热性和平整性均良好。
[0101]
实施例6相较于实施例4,铸片的最大厚度与最小厚度差偏大,纵向拉伸后会导致侧边部的厚度偏大,导致横向拉伸时膜厚度不均,热收缩性、耐热性和平整性均有消极影响。
[0102]
对比例4相较于实施例4,铸片的最大厚度与最小厚度差偏小,纵向拉伸后会导致侧边部的厚度偏小,导致横向拉伸时膜厚度不均,热收缩性、耐热性和平整性均有消极影响。
[0103]
实施例7相较于实施例1,铸片的最小厚度靠近侧边部,经拉伸后耐热性和平整性有消极影响,但仍为合格产品。
[0104]
实施例8相较于实施例1,铸片的最小厚度靠近主体部,热收缩性、耐热性和平整性均有消极影响,产品不合格。
[0105]
实施例9相较于实施例1,单位面积张应力过小,导致纵向拉伸后膜厚度的均匀性不佳,热收缩性、耐热性和平整性均有消极影响。
[0106]
实施例10相较于实施例1,单位面积张应力过大,导致膜纵向收缩增大,膜热处理后尺寸稳定性差,耐热性和平整度均不佳。
[0107]
实施例11相较于实施例1,仅进行一段冷却,热收缩性、耐热性和平整性均有消极影响。
[0108]
对比例5较于对比例1,平整性不合格。
[0109]
以上所述仅是本发明的优选实施方式,应当指出,对于本技术领域的普通技术人员来说,在不脱离本发明技术原理的前提下,还可以做出若干改进和润饰,这些改进和润饰也应视为本发明的保护范围。