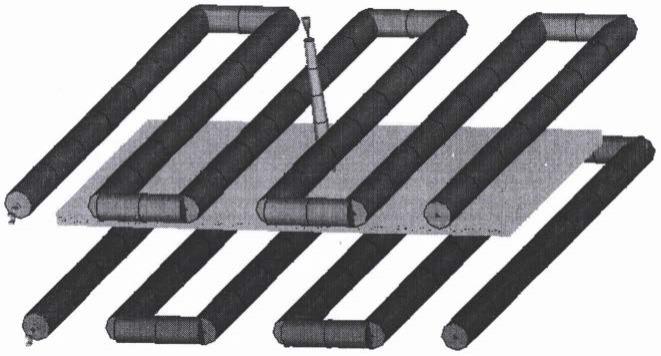
1.本发明涉及注塑件性能的研究,具体为一种纤维增强树脂注塑件的模量优化方法。
背景技术:2.塑料是树脂和各种添加剂或填充物的混合物,纤维是一种应用普遍的充填物;聚丙烯是一种密度低、加工性能优异的树脂,但是其低温脆性、刚性差等缺点限制了应用范围,经过纤维填充改性处理,可以提高其弯曲强度、拉伸强度、刚性和韧性,代替铝合金和钛合金广泛的应用于制造航空、交通、机械、电器等领域的零件。
3.纤维增强树脂的注射成型过程受填充物的影响更为复杂,在分析注塑件性能时须充分考虑熔体动力学、熔体对纤维的作用,以及纤维之间的相互作用对纤维取向的影响;纤维的取向决定聚合物的力学性能和各向异性性能,而且取向会随着流动方向、厚度和塑件的几何形状等因素的变化而变化,运用模拟分析软件将纤维增强树脂在注射成型模腔中的流动过程可视化,获取纤维增强树脂在模腔中的流动过程和取向趋势,指导注塑工艺参数的设计减少模具研发成本和试模次数,提高生产效率和产品的质量。
技术实现要素:4.本发明所要解决的技术问题是:针对现有技术的不足,提供一种纤维增强树脂注塑件的模量优化方法,以解决当前无法在塑料注塑成型过程中进行预测注塑件的力学性能的技术问题,具有节约分析成本、效率高、可靠性好等特点,提高了塑件的成型质量和生产效率。
5.本发明为实现上述目的,通过以下技术方案实现:
6.一种纤维增强树脂注塑件的模量优化方法,其特征在于所述纤维增强树脂包括长径比为25~1000的a组分纤维和树脂基材,将获取的塑件3d模型导入moldflow平台创建分析实体项目,对实体模型进行有限元网格划分,加载材料和边界条件后进行模流分析,通过调节每种工艺参数在不同水平下的设置来调节研究对象的注射成型工艺参数组合,进而获得边界条件变化对注塑件取向的影响以及模量变化的规律,据此设定与产品性能匹配的合理工艺参数。
7.优选的,塑件形状对称且厚度均匀,采用注射成型工艺生产,注塑模为1模2腔,采用矩形侧浇口的浇注系统和随形冷却的冷却系统,冷却介质温度为20℃,模具材料为tool steel p-20。
8.优选的,a组分纤维为填充物重量在20%~40%的玻璃纤维,树脂基材为聚丙烯树脂。
9.优选的,塑件3d模型通过creo创建并保存为stl格式文件。
10.优选的,边界条件包括熔体温度、模具温度、注射压力、保压压力和保压时间。
11.优选的模量优化方法,包括以下步骤:
(1)提取基本指标:综合分析纤维增强树脂注塑件成型工艺的各类参数,包括温度、压力、时间,经过整合评估,按塑件的性能要求提取实验目标为取向,目标的显性参数为模量,具体为剪切模量(纤维)、第一主方向上的拉伸模量(纤维)和第二主方向上的拉伸模量(纤维);(2)从上述相关指标中找出反映取向和力学性能的典型关联实验因子,包括熔体温度、模具温度、注射时间、保压压力和保压时间,结合材料推荐值和生产环境,制定各因子设计范围以及实验水平间隔,进行正交实验设计;(3)在moldflow平台实体分析项目中导入塑件模型进行有限元网格划分,加载边界条件进行成型窗口分析,计算求解完成后进行图形处理获得推荐注射时间,并校核最大压力降、最低流动前沿温度、最大剪切速率、最大剪切应力和最长冷却时间等参数;(4)按照实验设计的边界条件对实体模型进行模流分析,获得实验因子对塑件模量的影响均值与极差,对每个实验目标结果进行分析,得到目标因子的推荐组合,判断各参数依次影响的程度,综合进行比较和分析,确定匹配塑件力学性能的注射成型工艺设计方案。
12.进一步优选的模量优化方法,还包括:以上述实验设计得出的注射成型工艺参数设计方案为基础,通过调整冷却介质温度来改变冷却系统设置,检测塑件的模量变化,获得模量随冷却温度变化的规律和合理的冷却介质温度。
13.本发明所述模流实验是通过纤维取向保压分析生成剪切模量和拉伸模量(含第一主方向和第二主方向),剪切模量结果显示与纤维取向方向重合的xy方向上的施加的剪切应变,第一和第二主方向上的拉伸模量结果是取每个单元的所有层的平均值,模拟过程中忽略各工艺参数间交互作用所产生的影响。
14.本发明的一种纤维增强树脂注塑件的模量优化方法,通过调节研究对象的注射成型工艺参数设置进行的纤维填充模流分析获得结果包括剪切模量(纤维)、第一主方向上的拉伸模量(纤维)和第二主方向上的拉伸模量(纤维),经过研究和实验,基于正交试验设计和极差分析,发现对剪切模量(纤维)和第一主方向上的拉伸模量(纤维)影响最大的因子均为注射时间,对第二主方向上的拉伸模量(纤维)影响最大的因子为保压时间和保压压力,具体为:(1)依据塑件的剪切模量(纤维)最大时对应的工艺参数组合为a1-b1-c2-d2-e4,即熔体温度为220℃、模具温度为40℃、注射时间为1.5s、保压压力为80%、保压时间为22s时,注射成型产品得到最大的剪切模量(纤维),进一步实验测得剪切模量(纤维)为1393.5mpa;(2)当成型工艺参数组合为a2-b4-c1-d4-e4时,即熔体温度为240℃、模具温度为70℃、注射时间为1.0s、保压压力为120%、保压时间为22s时,注射成型产品得到最大的第一主方向上的拉伸模量(纤维),进一步实验测得第一主方向上的拉伸模量(纤维)为7177.5mpa;(3)当成型工艺参数组合为a2-b3-c1-d2-e4时,即熔体温度为240℃、模具温度为60℃、注射时间为1.0、保压压力为80%、保压时间为22s时,注射成型产品得到相应的第二主方向上的拉伸模量(纤维),进一步实验测得第二主方向上的拉伸模量(纤维)为3726.5mpa;此结果不是实验组中第二主方向上的拉伸模量(纤维)最大值,因为充填速度对
纤维取向的影响很大,同时取向对塑件的力学性能影响与温度和压力的影响是相互作用的,在实际过程中需要一起分析;(4)在同一注射工艺参数组合不变的边界条件下,冷却系统温度的变化能够改变塑件的剪切模量(纤维)、第一主方向上的拉伸模量(纤维)和第二主方向上的拉伸模量(纤维)等相关力学性能,这对模具设计时分型面选择有直接的指导意义。
15.本发明比现有技术具有以下优点:(1)本发明优化方法设计合理,有效将纤维增强树脂注塑件的注射成型过程模拟与模流结果的分析文件联合进行力学性能的模拟分析,为实际生产提供参考和借鉴,提高企业新产品的开发速度,节约多次试验的资金;(2)本发明流程易于操作,各项性指标具有先进性、精准且综合性,大幅提升企业的注塑生产能力和塑件质量,在纤维增强树脂注塑件生产领域具有广阔的应用前景和实际意义;(3)本发明将纤维增强树脂在注塑成型模腔中的流动过程可视化并采用正交实验优化等过程预测工艺参数对注塑件模量分析结果,能更加准确的获得所需产品力学性能和尺寸精度,实现了为模具设计和塑件模量优化提供方向。
附图说明
16.图1是本发明流程图。
17.图2是注塑件成型模具浇注系统和冷却系统示意图。
18.图3是本发明中实验组17模流分析的第一主方向上的拉伸模量(纤维)结果示意图。
19.图4是本发明中实验组18模流分析的剪切模量(纤维)结果示意图。
20.图5是本发明中实验组19模流分析的第二主方向上的拉伸模量(纤维)结果示意图。
具体实施方式
21.下面将结合本发明实施例中的附图,对本发明实施例中的技术方案(如图1)进行清楚、完整地描述,但并不因此将本发明限制在所述的实施例范围之中。
22.一种纤维增强树脂注塑件的模量优化方法,包括:步骤(1):在三维建模软件creo中分别构建塑件、浇注系统和冷却系统的模型,参见图2;步骤(2)将模型导入到moldflow中进行网格划分得到有限元模型,并执行set injection location命令和设置冷却液入口,选择材料(select material)为rtp 0105cc fr;步骤(3)在moldflow平台的set analysis sequence中调用molding window模块,加载边界条件进行成型窗口分析,计算求解完成后进行图形处理获得推荐injection time,并校核最大压力降、最低流动前沿温度、最大剪切速率、最大剪切应力和最长冷却时间等参数;步骤(4)在moldflow平台的set analysis sequence中调用cool+flow+warp,并设
置分析模块所需的相关工艺参数,具体而言,即熔体温度、模具表面温度、注射时间、保压压力、保压时间(以上各参数需要根据具体的塑件尺寸、模具尺寸、材料特性进行相应设置);保存设置,进行计算,导出结果进行分析。
23.基于上述步骤中的工艺参数创建l
16
(45)正交实验表,根据模拟结果和实际生产环境以及经验值设计正交表中16种不同a、b、c、d、e取值。
24.具体的本实施例采用得5个影响因子为熔体温度a(220℃、240℃、260℃、280℃)、模具表面温度b(40℃、50℃、60℃、70℃)、注射时间c(1.0s、1.5s、2.0s、2.5s)、保压压力d(60%、80%、100%、120%、)、保压时间e(6s、10s、14s、18s),依据步骤(4)进行成型试验,逐次完成正交试验表中确定的各项方案分析。
25.最终获取各实验组注塑件的剪切模量(纤维)、第一主方向上的拉伸模量(纤维)和第二主方向上的拉伸模量(纤维)的数值(如表1)。
26.表1
27.对同一工艺参数在相同水平下的剪切模量(纤维)数值应用极差分析法对实验结果进行分析,得到极差分析表(如表2)可以明晰各类工艺参数对剪切模量(纤维)的影响情况,并确立最优方案。
28.具体的,极差分析中可以看出,注射时间和熔体温度两种工艺参数下剪切模量(纤维)平均值变动最大,由此表明影响剪切模量(纤维)的主要成型工艺参数为注射时间和熔体温度,各因素对剪切模量(纤维)结果的影响程度排序:c>a>e>d>b,即注射时间>熔
体温度>保压时间>保压压力>模具温度,由此可知,当熔体温度为280℃、模具温度为50℃、注射时间为2.0、保压压力为100%、保压时间为14s时,即为a4-b2-c3-d3-e2成型工艺参数组合时,注射成型产品得到最小的剪切模量(纤维);当成型工艺参数组合为a1-b1-c2-d2-e4时,即熔体温度为220℃、模具温度为40℃、注射时间为1.5、保压压力为80%、保压时间为22s时,注射成型产品的剪切模量(纤维)可到最大。
29.表2剪切模量(纤维)极差分析表
30.对同一工艺参数在相同水平下的第一主方向上的拉伸模量(纤维)数值应用极差分析法,得到极差分析表(如表3)可以明晰各类工艺参数对第一主方向上的拉伸模量(纤维)的影响情况,并确立最优方案。
31.表3第一主方向上的拉伸模量(纤维)平均值分析表
32.具体的,极差分析中可以看出,注射时间变化对应第一主方向上的拉伸模量(纤维)平均值变动最大,随着注射时间的增大第一主方向上的拉伸模量(纤维)降低,由此表明影响第一主方向上的拉伸模量(纤维)的主要成型工艺参数为注射时间,各因素对第一主方向上的拉伸模量(纤维)结果的影响程度排序:c>a>d>e>b,即注射时间>熔体温度>保压压力>保压时间>模具温度,由此可知,当熔体温度为280℃、模具温度为60℃、注射时间为2.5、保压压力为60%、保压时间为18s时,即为a4-b3-c4-d1-e3成型工艺参数组合时,注射成型产品得到最小的第一主方向上的拉伸模量(纤维);当成型工艺参数组合为a2-b4-c1-d4-e4时,即熔体温度为240℃、模具温度为70℃、注射时间为1.0、保压压力为120%、保压时间为22s时,注射成型得到塑件的第一主方向上拉伸模量(纤维)最大。
33.对同一工艺参数在相同水平下的第二主方向上的拉伸模量(纤维)数值应用极差
分析法,得到极差分析表(如表4)可以明晰各类工艺参数对第二主方向上的拉伸模量(纤维)的影响情况,并确立最优方案。
34.具体的,极差分析中可以看出,保压时间和保压压力对第二主方向上的拉伸模量(纤维)平均值变动影响大,第二主方向上的拉伸模量(纤维)随着保压时间的增大而增大,并且随着保压压力的增加显著减小,各因素对第二主方向上的拉伸模量(纤维)结果的影响程度排序:e=d>c>b>a,即保压时间=保压压力>注射时间>模具温度>熔体温度;并分析可知,当熔体温度为240℃、模具温度为60℃、注射时间为1.0、保压压力为80%、保压时间为22s时,即为a2-b3-c1-d2-e4成型工艺参数组合时,注射成型产品得到最大的第二主方向上的拉伸模量(纤维);当成型工艺参数组合为a1-b4-c4-d4-e2时,即熔体温度为220℃、模具温度为70℃、注射时间为2.5、保压压力为120%、保压时间为14s时,注射成型产品得到最小的第二主方向上的拉伸模量(纤维)。
35.表4第二主方向上的拉伸模量(纤维)平均值分析表
36.如图3-5所示,依据上述正交试验得出的成型工艺参数组合进行模流分析,结果显示见表5。
37.在上述实验结果中,考虑冷却系统的影响,调整冷却系统温度能够一定程度上改善产品的内在性能和质量;将冷却介质温度从20℃调整为25℃,进行模流分析,结果显示如表5。
38.实施例在注射成型工艺设置不变时,注塑件的剪切模量(纤维)没有随着冷却介质温度的升高发生变化,说明纤维增强树脂在充填流动时受冷却温度的影响较小。
39.实施例在注射成型工艺设置不变时,当冷却介质温度从20℃调整为25℃时,注塑件的第一主方向上的拉伸模量(纤维)由7177.5mpa增加为7179.1mpa,注塑件的第二主方向上的拉伸模量(纤维)由3726.5mpa上升为3729.6mpa,说明纤维增强树脂在充填流动时受冷却温度的影响较大,同时方向性很明显,这对模具设计时的分型面选择时须重点考虑。
40.表5
41.以上显示和描述了本发明的基本原理、主要特点,所述的实施例是本发明的优选实施方式,应当指出的是,对于本技术领域的普通技术人员来说,在不脱离本发明原理的前提下,在没有作出创造性劳动前提下所获得的所有其他实施例,都属于本发明保护的范围。