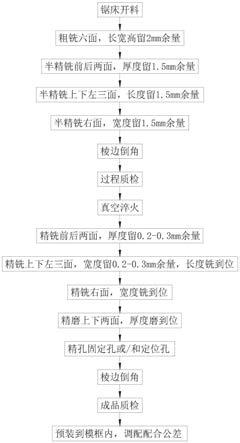
1.本技术涉及模具技术领域,尤其涉及模具方导柱。
背景技术:2.我们日常生产、生活中所使用到的各种工具和产品,大到机床的底座、机身外壳,小到一个胚头螺丝、纽扣以及各种家用电器的外壳,无不与模具有着密切的关系。模具的形状决定着这些产品的外形,模具的加工质量与精度也就决定着这些产品的质量。因为各种产品的材质、外观、规格及用途的不同,模具分为了铸造模、锻造模、压铸模、冲压模等非塑胶模具,以及塑胶模具。模板、模架是模具的重要组成部分,是模具的基础。模架具有导向柱和导向套组成的导向装置,其中注塑模具的动模板与定模板在开合模的时候一般采用方导柱来导向,才能保证合模准确顺畅。现有技术中方导柱的加工精度和加工周期很难兼顾,而且方导柱普遍存在装配和拆卸困难的问题。
3.因此,如何对现有的模具方导柱进行改进,使其克服上述问题,是本领域技术人员亟待解决的问题。
技术实现要素:4.本技术的一个目的在于提供一种在保证装配精度和装配效率的前提下,加工难度低,加工周期短,制造成本低的模具方导柱的加工方法。
5.本技术的另一个目的在于提供一种利用上述加工方法成型的模具方导柱。
6.为达到以上目的,本技术采用的技术方案为:一种模具方导柱的加工方法,包括以下步骤:
7.s1:开料成型长方体初胚,上述初胚具有上端面、下端面、左端面、右端面、前端面和后端面六个端面,设定上下方向为长度方向,左右方向为宽度方向,前后方向为厚度方向;
8.s2:粗加工六个端面,并在长度方向、宽度方向和厚度方向上均留余量a,1mm≤a≤3mm;
9.s3:半精加工前端面和后端面,在厚度方向上留余量b1,b1=(0.6~0.8)
×
a;
10.s4:半精加工上端面、下端面、左端面和右端面中任意三个端面,在长度方向或宽度方向上留余量b2,b2=(0.6~0.8)
×
a;
11.s5:半精加工剩下一端面,在宽度方向或长度方向上留余量b3,b3=(0.6~0.8)
×
a;
12.s6:精加工前端面和后端面,在厚度方向上留余量c1,c1=(0.08~0.25)
×
a;
13.s7:精加工上端面和下端面,以及左端面或右端面,在宽度方向上留余量c2,c2=(0.08~0.25)
×
a,在长度方向上加工到位;
14.s8:精加工剩下的右端面或左端面,在宽度方向上加工到位;
15.s9:精加工前端面和后端面,在厚度方向上加工到位;
16.s10:精加工至少两个固定孔,固定孔适于穿过螺栓并将方导柱固定于模框上;
17.s11:将方导柱预装配到模框内,并根据固定孔的位置调配配合公差。
18.进一步的,上述s4中,半精加工上端面和下端面,以及左端面或右端面,在长度方向上留余量b2;上述s5中,半精加工右端面或左端面,在宽度方向上留余量b3。
19.进一步的,设定方导柱与模框的配合公差、方导柱与导套的配合公差均为h7/g6或h7/f6;上述s8中,按照h7/g6或h7/f6的精度精加工右端面或左端面。
20.进一步的,上述s10中,还包括以下步骤:精加工至少两个定位孔,定位孔适于穿过销钉并对方导柱在模框上的位置进行定位。
21.进一步的,上述s5之后,上述s6之前还包括淬火步骤。
22.进一步的,上述s5之后,淬火步骤之前还包括以下步骤:对上端面、下端面与左端面、右端面的棱边进行倒角;上述s9之后,上述s11之前还包括以下步骤:对前端面、后端面的棱边进行倒角。
23.进一步的,在前一棱边倒角步骤之后,淬火步骤之前还包括过程质检步骤;在后一棱边倒角步骤和上述s10之后还包括成品质检步骤。
24.进一步的,上述s1中采用锯切开料;上述s2中采用粗铣加工;上述s3、s4、s5中采用半精铣加工;上述s6、s7、s8采用精铣加工;上述s9中采用精磨加工;上述s10中采用精孔加工。
25.一种模具方导柱,利用所述的加工方法成型,所述方导柱包括固定部和滑动部,所述固定部适于固定设置于模框内,所述滑动部适于滑动连接于导套内,所述固定部和所述滑动部平滑连接,且所述固定部与所述模框之间,以及所述滑动部和所述导套之间采用相同的配合公差;所述固定部上开设有至少两个固定孔,所述固定孔适于穿过螺栓并将所述方导柱固定于所述模框上。
26.进一步的,所述固定部上还开设有至少两个定位孔,所述定位孔适于穿过销钉并对所述方导柱在所述模框上的位置进行定位。
27.与现有技术相比,本技术具有以下有益效果:(1)本方案的方导柱由传统的台阶型结构设计为直身型结构,大大降低了工件的加工难度和生产周期,且充分考虑工件装配和拆卸的难易度,为后续工作创造了更多的便利;(2)本方案采用分步式加工方式(将粗加工、半精加工、精加工独立开来),大大降低了工件内应力的产生,一定程度上控制了工件的变形量,从而降低了工件生产不良率,延迟了工件的使用寿命;(3)在半精加工和精加工的前三步中采用先加工三端面再加工剩下一端面,而非一次性加工四个端面,可以提高加工出来的工件宽度方向上两侧面的平行度,进一步确保了工件形状位置公差。
附图说明
28.图1是根据本技术涉及的现有方导柱的结构示意图;
29.图2和图3是根据本技术的一个优选实施例两种不同结构类型的结构示意图;
30.图4是根据本技术的一个优选实施例的方向示意图;
31.图5是根据本技术的一个优选实施例采用侧面铣床加工时的立体结构示意图;
32.图6是根据本技术的一个优选实施例采用侧面铣床加工上端面时的结构示意图;
33.图7是根据本技术的一个优选实施例采用侧面铣床加工左端面时的结构示意图;
34.图8是根据本技术的一个优选实施例采用侧面铣床加工下端面时的结构示意图;
35.图9是根据本技术的一个优选实施例采用平面铣床加工右端面时的结构示意图
36.图10是根据本技术的一个优选实施例的尺寸示意图;
37.图11是根据本技术的一个优选实施例的加工方法的工序流程图。
38.图中:100、模框;200、导套;300、侧面铣床;301、加工台;302、定位块;303、侧面铣刀;304、固定气缸;400、平面铣床;401、水平台;402、夹持气缸;403、平面铣刀;1、方导柱;11、固定部;12、滑动部;13、固定孔;14、定位孔。
具体实施方式
39.下面,结合具体实施方式,对本技术做进一步描述,需要说明的是,在不相冲突的前提下,以下描述的各实施例之间或各技术特征之间可以任意组合形成新的实施例。
40.在本技术的描述中,需要说明的是,对于方位词,如有术语“中心”、“横向”、“纵向”、“长度”、“宽度”、“厚度”、“上”、“下”、“前”、“后”、“左”、“右”、“竖直”、“水平”、“顶”、“底”、“内”、“外”、“顺时针”、“逆时针”等指示方位和位置关系为基于附图所示的方位或位置关系,仅是为了便于叙述本技术和简化描述,而不是指示或暗示所指的装置或元件必须具有特定的方位、以特定方位构造和操作,不能理解为限制本技术的具体保护范围。
41.需要说明的是,本技术的说明书和权利要求书中的术语“第一”、“第二”等是用于区别类似的对象,而不必用于描述特定的顺序或先后次序。
42.本技术的说明书和权利要求书中的术语“包括”和“具有”以及他们的任何变形,意图在于覆盖不排他的包含,例如,包含了一系列步骤或单元的过程、方法、系统、产品或设备不必限于清楚地列出的那些步骤或单元,而是可包括没有清楚地列出的或对于这些过程、方法、产品或设备固有的其它步骤或单元。
43.如图1所示,在本技术人的以往设计中,方导柱与模框100的配合公差为:h7/k6或h7/m6,而方导柱与导套200的配合公差为:h7/g6或h7/f6。按这样的公差标准,方导柱的外形结构必然为阶梯结构(如图1中a处所示)。
44.方导柱的以往设计主要存在两个弊端:(1)在h7/k6或h7/m6的配合公差下(两者之间为过渡配合),因方导柱为方形结构(非圆形结构),又因方导柱与模框100配合段较长且配合较紧,导致方导柱的装配和拆卸都非常的困难;(2)因方导柱外形为阶梯结构,会导致两条侧边的加工非常困难,且需要很长的加工时间,导致方导柱加工成本和加工周期增加。
45.基于上述问题,本实施例中方导柱由传统的台阶型结构设计创新为直身型结构,大大降低了零件的加工难度和生产周期,且充分考虑零件装配和拆卸的难易度,为后续工作创造了更多的便利。具体结构如下:
46.如图2所示,方导柱1包括固定部11和滑动部12,固定部11适于固定设置于模框100内,滑动部12适于滑动连接于导套200内,固定部11和滑动部12平滑连接,且固定部11与模框100之间,以及滑动部12和导套200之间采用相同的配合公差;固定部11上开设有至少两个固定孔13,固定孔13适于穿过螺栓并将方导柱1固定于模框100上。
47.上述结构的方导柱1采用统一的配合公差,消除了阶梯结构,方便加工。又因为滑动部12和导套200之间必然需要间隙配合,因此固定部11与模框100也统一成间隙配合,方便将方导柱1固定安装到模框100上。同时,需要提高固定孔13的加工精度,保证方导柱1的
装配精度。
48.进一步具体的,根据模具产品对模架定位精度高低的需求,本实施例设计了两种方导柱1的结构类型,分别是:
49.如图2所示的标准型,适用于大众化常规模具,方导柱1与模框100的配合公差为:h7/g6,方导柱1通过四个螺栓穿过四个固定孔13固定在模板对应的模框100内。
50.如图3所示的精密型,适用于高精度模具,方导柱1与模框100的配合公差为:h7/g6,方导柱1通过两个螺栓穿过两个固定孔13固定在模板对应的模框100内;同时,在方导柱1上开设两个定位孔14,并增设两个销钉穿过定位孔14对方导柱1进行在模框100上的位置进行定位。
51.如图4至11所示,上述方导柱1的加工方法,包括以下步骤:
52.步骤一:锯床开料,成型长方体初胚;如图4所示,上述初胚具有上端面、下端面、左端面、右端面、前端面和后端面六个端面,设定上下方向为长度方向h,左右方向为宽度方向w,前后方向为厚度方向d。
53.步骤二:粗铣六个端面,并在长度方向、宽度方向和厚度方向上均留余量a,1mm≤a≤3mm;本实施例中a=2mm。
54.步骤三:半精铣前端面和后端面,在厚度方向上留余量b1,b1=(0.6~0.8)
×
a;本实施例中b1=1.5mm。
55.步骤四:如图6至图8所示,半精铣上端面、下端面和左端面三个端面,在长度方向上留余量b2,b2=(0.6~0.8)
×
a;本实施例中b2=1.5mm。
56.步骤五:如图9所示,半精铣右端面,在宽度方向上留余量b3,b3=(0.6~0.8)
×
a;本实施例中b3=1.5mm。
57.步骤六:对上端面、下端面与左端面、右端面的棱边进行倒角,以符合外形设计要求;即如图10所示的直角t和圆角r。
58.步骤七:过程质检;由于还未淬火,过程质检不合格的可以返工,当然不具备返工条件的作报废处理。
59.步骤八:真空淬火;主要用以消除上述铣削加工产生的内应力。
60.步骤九:精铣前端面和后端面,在厚度方向上留余量c1,c1=(0.08~0.25)
×
a;本实施例中c1=0.2~0.3mm。
61.步骤十:精铣上端面、下端面和左端面,在宽度方向上留余量c2,c2=(0.08~0.25)
×
a,在长度方向上加工到位;本实施例中c2=0.2~0.3mm。
62.步骤十一:精铣右端面,在宽度方向上加工到位。
63.步骤十二:精磨前端面和后端面,在厚度方向上加工到位。
64.步骤十三:精孔四个固定孔或者两个固定加两个定位孔,固定孔适于穿过螺栓并将方导柱固定于模框上,定位孔适于穿过销钉并对方导柱在模框上的位置进行定位。
65.步骤十四:对前端面、后端面的棱边进行倒角;即如图10所示的圆角e。
66.步骤十五:成品质检;过程质检不合格直接报废。
67.步骤十六:将方导柱预装配到模框内,并根据固定孔的位置调配配合公差。
68.上述加工方法的工序流程如图11所示。
69.涉及到具体加工精度,如图10所示,本实施例选择方导柱1与模框100的配合公差、
方导柱1与导套200的配合公差均为h7/g6,即模框100和导套200的间距分别等效为h7的基准孔精度,方导柱1的宽度等效为g6的轴精度,即在上述步骤十一中,以g6的精度将方导柱1的宽度加工到位。在具体实施例中,方导柱1的宽度w=120mm,根据g6对应的公差表可以查询到,w的上公差为-0.02mm,下公差为-0.05mm,可见方导柱1的宽度精度要求较高。从图10中还可以看到,在具体实施例中方导柱1的长度h=360mm,h的上公差为-0.5mm,下公差为-1mm,方导柱1的厚度d=60mm,d的上公差为0,下公差为-0.2mm,可见方导柱1在长度方向和厚度方向精度要求不高。
70.因此,本实施例加工方法的重点就是将宽度w加工到位。又根据方导柱1的工况可知,左端面和右端面的平行度,以及左右端面与前后端面的垂直度尤为关键,上述平行度和垂直度的公差过大,会直接导致方导柱1与模框100的配合公差、方导柱1与导套200的配合公差不能达到设计要求。
71.基于上述加工精度要求,从上述步骤四至步骤五,以及步骤十至步骤十一看到,本实施例对于工件侧面(即上端面、下端面、左端面、右端面)的铣削加工均采用先铣三面再铣剩下一面的顺序进行。落实到实际加工中,本实施例先采用侧面铣床铣三个侧面(即上端面、下端面、左端面),再用平面铣床铣第四侧面(即右端面),而非侧面铣床直接铣四个侧面,这是因为全面考虑了铣床的加工精度和传动原理,具体的说:
72.如图5所示,在步骤四和步骤十中,采用侧面铣床300加工工件,侧面铣床300包括加工台301、定位块302、侧面铣刀303和固定气缸304,固定气缸304固定工件。如图6所示,以左右端面为基准面紧贴定位块302,侧面铣刀303沿左右方向进给并铣削加工上端面;如图7所示,工件顺时针转动九十度,以加工好的上端面为基准面紧贴定位块302,侧面铣刀303铣削加工左端面;如图8所示,工件再顺时针转动九十度,以加工好的左端面为基准面紧贴定位块302,侧面铣刀303铣削加工下端面。在步骤五和步骤十一中,采用平面铣床400加工工件,平面铣床400包括水平台401、夹持气缸402和平面铣刀403。如图9所示,两个夹持气缸402夹持固定于前端面和后端面上,以左端面为基准面紧贴水平台401,平面铣刀403铣削加工右端面。
73.如图6至图8所示,侧面铣刀303除了沿进给方向(即图中的左右方向)对工件具有作用力,还会对工件产生沿垂直于进给方向(即图中的上下方向)的作用力,而固定气缸304对工件的固定力是有限的,因此上下方向的作用力,可能会使工件发生微小的偏转,导致加工误差的产生。图6和图8中,由于是作为基座面的右端面和左端面为长边,与定位块302的接触面积较大,因此产生的加工误差还相对较小。而图7中,以上端面作为基础面,其与定位块302的接触面积较小,产生的加工误差也相对较大。若仍以侧面铣床300加工剩下的右端面,则需要以下端面为基准面紧贴定位块302,此时产生的加工误差以及四次加工的积累误差,很可能会导致左端面和右端面的平行度出现较大偏差,进而导致工件报废或返工。因此,本实施例采用平面铣床400加工剩下的右端面,此时是以左端面为基准面紧贴水平台401,同时在垂直于平面铣刀403进给方向上的作用力不会使工件发生偏转,保证了左端面和右端面的平行度,进而能获得设计的加工精度,降低报废率和返工率。
74.更进一步的,步骤九中前端面和后端面的精铣加工,步骤十二中前端面和后端面的精磨加工,均以左端面或右端面为基准面进行加工,保证前后端面和左右端面之间的垂直度,进一步确保了工件形状位置公差。
75.通过上述对方导柱结构及其加工工艺的改进,取得了以下效果:
76.(1)设计结构的优化和创新,使方导柱装配和拆卸时间缩短50%左右。
77.(2)方导柱宽度两侧边(即左端面和右端面)平行度公差<0.015mm,平面与侧面(即前后端面与左右端面)的垂直度<0.015mm;从而确保了宽度尺寸公差控制在0.02mm以内,达到了设计上的要求。
78.(3)同比传统设计加工,采用新型工艺加工,分多次铣磨加工,逐级降低加工余量,实现精加工少切削、小切削,从而大大降低了工件内应力,使工件使用寿命延长约15%。
79.(4)同比传统加工,生产周期缩短约36小时,生产成本降低约38%。
80.(5)设计上的优化和创新,一次加工合格率达到99.95%。(传统加工的合格率约为88.6%)。
81.以上描述了本技术的基本原理、主要特征和本技术的优点。本行业的技术人员应该了解,本技术不受上述实施例的限制,上述实施例和说明书中描述的只是本技术的原理,在不脱离本技术精神和范围的前提下本技术还会有各种变化和改进,这些变化和改进都落入要求保护的本技术的范围内。本技术要求的保护范围由所附的权利要求书及其等同物界定。