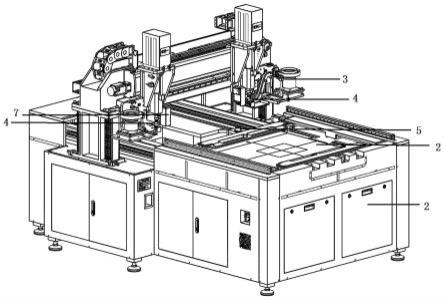
一种适用于pcb板的自动铆钉机
技术领域
1.本发明涉及机械加工技术领域,具体涉及一种适用于pcb板的自动铆钉机。
背景技术:2.在现有技术中的自动化加工设备中的自动铆钉机技术,例如,专利申请: cn202022171099.5自动铆钉机铆触点新型结构;公开的铆钉机技术领域,具体为自动铆钉机铆触点新型结构,包括自动铆钉机主体和气液增压气缸,所述自动铆钉机主体的表面固定连接有弓形支撑侧板,且弓形支撑侧板的顶端固定连接有连接座,所述连接座的顶端固定连接有气液增压气缸,所述弓形支撑侧板的内侧装设有连接块,且连接块的底端固定连接有下压方形滑块。
3.现有技术中采用了铆接结构虽然能初步实现工件的铆接,但是依然存在以下缺陷:第一、不具对待铆接的工件实现对位,特别是对多块pcb板材结构的工件进行纵向预先对位校正。
4.第二、无法对工件的上侧和下侧同时进行对位和铆接。
5.第三、不利于实现工件和铆接件的便捷上料。特别是对于工件的限位和取放操作不够便捷。
技术实现要素:6.本发明克服了现有技术的不足,提供一种适用于pcb板的自动铆钉机,便于实现对若干层工件进行定位、对位、铆接;能够适应不同型号工件的加工。
7.为达到上述目的,本发明采用的技术方案为:一种适用于pcb板的自动铆钉机,包括机架,机架上设置有组装区,以及与组装区对应的上料区一和上料区二,上料区一和上料区二分别设置有工件上料机构和连接件上料机构;组装区的下部和上部分别设置有上部铆接对位机构和下部推顶对位机构;工件上料机构包括在上料区一和组装区之间位移的位移治具组,位移治具组上设置有若干个用于定位工件的治具座。
8.本发明一个较佳实施例中,上部铆接对位机构包括设置在机架上位于组装区内的龙门架,且龙门架上设置有位移机构一,位移机构一上驱动设置有若干个安装架一,安装架一上设置有升降机构一,升降机构一的下部驱动设置有铆接机构。
9.本发明一个较佳实施例中,铆接机构包括驱动设置在升降机构一上的预压装置,预压装置上设置有铆钉吸取装置,且预压装置内穿设有能相对预压装置伸缩的铆接头。
10.本发明一个较佳实施例中,铆接机构内还包括设置在预压装置上的集尘装置,集尘装置的一侧设置有与预压装置对应的吸口,吸口的另一端还连接有真空吸管一;或/和,铆钉吸取装置包括吸料口,以及与吸料口连接的真空吸管二;或/和,所述连接件上料机构设置有衔接所述上料区二和组装区的震动上料机构,且所述震动上料机构设置在所述上部铆接对位机构的一侧。
11.本发明一个较佳实施例中,下部推顶对位机构包括设置在机架上位于组装区下方的位移机构二,位移机构二上驱动设置有若干个安装架二,安装架二上设置有升降机构二,升降机构二的上部驱动设置有推顶机构,推顶机构包括驱动设置在升降机构二上的推顶头。
12.本发明一个较佳实施例中,移治具组包括设置在上料区一和组装区之间的载具位移机构,且载具位移机构上驱动设置有载具座,载具座的上部设置有治具收纳区,治具收纳区的外围设置有能相对治具收纳区位移动作的自动压板。
13.本发明一个较佳实施例中,载具座上设置有能相对载具座纵向升降的定位件,定位件上能对接有用于承接工件的治具板;且工件至少部分位于治具板的承接面上的避空槽处。
14.本发明一个较佳实施例中,自动压板包括设置在载具座上的横向位移机构,横向位移机构上驱动设置有纵向位移机构,纵向位移机构上驱动设置有能相对治具收纳区纵向升降的压板。
15.本发明一个较佳实施例中,铆接头和推顶头能相对组装区纵向位移对位。
16.本发明一个较佳实施例中,适用于pcb板的自动铆钉机的加工方法,包括以下步骤:步骤一,预上料;通过工件上料机构和连接件上料机构分别将工件和连接件进行上料;步骤二,预取料;通过上部铆接对位机构获取连接件上料机构上的工件,工件上料机构将工件夹持定位后位移至待铆接位置处;步骤三,获取铆接位置;通过工件上料机构在龙门架上设置有位移机构一进行横向位移,利用上部铆接对位机构上设置的对位相机拍摄采集到待铆接位置处的工件位置信息;步骤四,校准加工位置;调整上部铆接对位机构以及下部推顶对位机构位移至铆接区域;步骤五,协同作业进行铆接操作;通过下部推顶对位机构位移至待铆接的工件的铆接位置处的下方,并向上推顶实现对工件上带铆接区域的向上推顶限位操作,通过上部铆接对位机构带着取出的连接件向下位移至带铆接位置,到达铆接位置时,释放连接件同时开始铆接操作,铆接操作的同时除尘装置进行抽吸,同步实现除尘操作。
17.步骤六,完成铆接并复位;完成铆接操作后,工件上料机构和连接件上料机构分别进行复位操作,取出铆接完成的工件,依次循环进行下一操作。
18.本发明解决了背景技术中存在的缺陷,本发明的有益效果:本发明提供一种适用于pcb板的自动铆钉机,便于实现对若干层工件进行定位、对位、铆接;能够适应不同型号工件的加工。
19.1、通过设置有工件上料机构和连接件上料机构实现工件的定位上料和连接件的上料;利用上部铆接对位机构和下部推顶对位机构同步实现工件和连接件的铆接操作。提升了铆接的便捷性、稳定性、有效性。
20.2、工件上料机构采用了位移治具组,用于对装载的工件进行传送上料。利用载具座上设置的自动压板能将装载的工件限定在载具座上承接的治具板上。
21.3、治具板驱动设置在载具座上,治具板能相对治具座纵向升降,便于实现工件上料时的承接,以及下料是的拿取。
附图说明
22.下面结合附图和实施例对本发明进一步说明。
23.图1是本发明优选实施例外部的轴视结构示意图;图2是本发明优选实施例工件上料机构的轴视结构示意图一;图3是本发明优选实施例工件上料机构的俯视结构示意图;图4是本发明优选实施例工件上料机构的轴视结构示意图二;图5是本发明优选实施例工件上料机构的侧视结构示意图;图6是本发明优选实施例工件上料机构的正视结构示意图一;图7是本发明优选实施例下部推顶对位机构的正视结构示意图;图8是本发明优选实施例下部推顶对位机构的轴视结构示意图;图9是本发明优选实施例上部铆接对位机构以及连接件上料机构的轴视结构示意图;图10是本发明优选实施例上部铆接对位机构以及连接件上料机构的局部放大正视结构示意图;图11是本发明优选实施例上部铆接对位机构以及连接件上料机构的局部放大的轴视结构示意图;图12是本发明优选实施例工件上料机构的正视结构示意图二;图13是本发明优选实施例内部的轴视结构示意图;其中,1-机架,11-上料区一,12-传送区一,13-组装区,14-上料区二,15-传送区二;2-工件上料机构,21-位移治具组,22-载具位移机构,23-载具座,24-自动压板,241-横向位移机构,242-纵向位移机构,25-退料机构, 252-退料气缸,253-推顶杆,254-治具板,26-刻度标尺;3-连接件上料机构,31-震动盘,32-物料传送滑槽,33-位置调节机构,34-夹料机构;4-上部铆接对位机构,41-安装架一,42-位移机构一,43-升降机构一,44-预压装置一,45-铆钉吸取装置,46-集尘装置,47-铆接机构,48-铆接头。
24.5-下部推顶对位机构,51-安装架二,52-位移机构二,53-升降机构二,54-推顶机构,541-推顶头;7-视觉检测系统,71-对位相机。
具体实施方式
25.现在结合附图和实施例对本发明作进一步详细的说明,这些附图均为简化的示意图,仅以示意方式说明本发明的基本结构,因此其仅显示与本发明有关的构成。
26.实施例一如图1-图13所示,一种适用于pcb板的自动铆钉机,包括机架1,机架1上设置有组
装区13,以及与组装区13对应的上料区一11和上料区二14,上料区一11和上料区二14的下分别设置有工件上料机构2和连接件上料机构3;上料区一11和组装区13之间预留有传送区一12,上料区二14和组装区13之间预留有传送区二15。工件上料机构2将工件从上料区一11转移经过传送区一12后转移至组装区13;连接件上料机构3将将工件从上料区二14转移经过传送区二15后转移至组装区13。组装区13的下部和上部分别设置有上部铆接对位机构4和下部推顶对位机构5。
27.具体的,工件上料机构2包括在上料区一11和组装区13之间位移的位移治具组21,位移治具组21包括设置在上料区一11和组装区13之间(即传送区一12)的载具位移机构22,载具位移机构22采用的是一对并列间隔设置的传送轨道、驱动气缸、以及由驱动气缸驱动在传送轨道上往复位移的位移滑座,位移滑座上设置有用于定位工件的载具座23。载具座23的上部设置有治具收纳区,治具收纳区的外围设置有能相对治具收纳区位移动作的自动压板24。自动压板24包括设置在载具座23上的横向位移机构241,横向位移机构241上驱动设置有纵向位移机构242,纵向位移机构242上驱动设置有能相对治具收纳区纵向升降的压板。
28.连接件上料机构3设置有衔接上料区二14和组装区13的震动上料机构。震动上料机构包括震动盘31,与震动盘31出料口连接的物料传送滑槽32,物料传送滑槽32呈从上下下倾斜的结构,物料传送滑槽32的下端的出料口与夹料机构34对应,且夹料机构34的一侧还设置有位置调节机构33,夹料机构34处还设置有物料感应机构用于检测物料有误。连接件上料机构3的具体结构可以借鉴现有技术中cn209426187u的一种用于线路板铆接的铆钉机铆压装置。本技术中的震动盘31出料口设置有吹气口,用于对震动盘31出料的连接件进行出气,将连接件一个一个分别吹落至物料传送滑槽32的下端的出料口处,通过夹料机构34夹取连接件后向前推进实现送料操作。
29.上部铆接对位机构4包括设置在机架1上位于组装区13内的龙门架,且龙门架上设置有位移机构一42,位移机构一42上驱动设置有若干个安装架一41,安装架一41上设置有升降机构一43,升降机构一43的下部驱动设置有铆接机构47。 铆接机构47包括驱动设置在升降机构一43上的预压装置44,预压装置44上设置有铆钉吸取装置45,且预压装置44内穿设有能相对预压装置44伸缩的铆接头48。铆接机构47内还包括设置在预压装置44上的集尘装置46,集尘装置46的一侧设置有与预压装置44对应的吸口,吸口的另一端还连接有真空吸管一。铆钉吸取装置45包括吸料口,以及与吸料口连接的真空吸管二。且吸料口的结构采用的是环套在铆接机构47中铆接头外围的吸料头,通过吸料头的端部设置有若干个吸料孔对铆钉实现吸附操作。
30.集尘装置46采用的是集尘罩,且集成罩与预压装置44之间预留有集尘间隙,通过集尘间隙对铆接时产生的废料进行吸附除尘操作。
31.上部铆接对位机构4还包括视觉检测系统7,即设置在安装架一41上的与组装区13对应的对位相机71。上部铆接对位机构4的具体结构可以借鉴现有技术中cn209426187u的一种用于线路板铆接的铆钉机铆压装置。
32.下部推顶对位机构5包括设置在机架1上位于组装区13下方的位移机构二52,位移机构二52上驱动设置有若干个安装架二51,安装架二51上设置有升降机构二53,升降机构二53的上部驱动设置有推顶机构54,推顶机构54包括驱动设置在升降机构二53上的推顶头
541。铆接头48和推顶头541能相对组装区13纵向位移对位。
33.实施例二如图1-图13所示,在实施例一的基础上载具座23上设置有能相对载具座23纵向升降的退料机构25,退料机构25包括用于承接工件的治具板254;且工件至少部分位于所述具板254的承接面上的避空槽上。具体的,治具座上设置有通槽,治具座的下部设置有退料气缸252,退料气缸252上驱动的推顶杆253穿设过通槽后与位于治具座上方的支撑筋衔接,治具板254通过支撑筋以及驱动支撑筋的退料气缸252、推顶杆253驱动纵向位移。定位件25采用的定位柱结构。定位件25能与治具板254的定位孔对接限位组合。
34.实施例三适用于pcb板的自动铆钉机的加工方法 ,包括以下步骤:步骤一,预上料,通过工件上料机构2和连接件上料机构3分别将工件和连接件进行上料操作。具体的,工件上料机构2采用了位移治具组21,用于对装载的工件进行传送上料。利用载具座23上设置的自动压板24能将装载的工件限定在载具座23上承接的治具板254上。治具板254驱动设置在载具座23上,治具板254能相对治具座纵向升降,便于实现工件上料时的承接,以及下料是的拿取。
35.步骤二,预取料,通过上部铆接对位机构4获取连接件上料机构上的工件,工件上料机构将工件夹持定位后位移至待铆接位置处。
36.步骤三,获取铆接位置,通过工件上料机构在龙门架上设置有位移机构一进行横向位移,利用对位相机71拍摄采集到待铆接位置处的工件信息。
37.步骤四,校准加工位置,调整上部铆接对位机构4以及下部推顶对位机构5的位移至铆接区域。
38.步骤五,协同作业进行铆接操作,通过下部推顶对位机构5位移至待铆接的工件的铆接位置处的下方,并向上推顶实现对工件上带铆接区域的向上推顶限位操作,通过上部铆接对位机构4带着取出的连接件向下位移至带铆接位置,到达铆接位置的时,释放连接件同时开始铆接操作,铆接操作的同时除尘装置进行抽吸,同步实现除尘操作。
39.步骤六,完成铆接复位,完成铆接操作后,工件上料机构和连接件上料机构分别进行复位操作,取出铆接完成的工件,依次循环进行下一操作。
40.工作原理:如图1-图13所示,通过设置有工件上料机构2和连接件上料机构3实现工件的定位上料和连接件的上料;利用上部铆接对位机构4和下部推顶对位机构5同步实现工件和连接件的铆接操作。提升了铆接的便捷性、稳定性、有效性。工件上料机构2采用了位移治具组21,用于对装载的工件进行传送上料。利用载具座23上设置的自动压板24能将装载的工件限定在载具座23上承接的治具板254上。治具板254驱动设置在载具座23上,治具板254能相对治具座纵向升降,便于实现工件上料时的承接,以及下料是的拿取。
41.以上依据本发明的理想实施例为启示,通过上述的说明内容,相关人员完全可以在不偏离本项发明技术思想的范围内,进行多样的变更以及修改。本项发明的技术性范围并不局限于说明书上的内容。