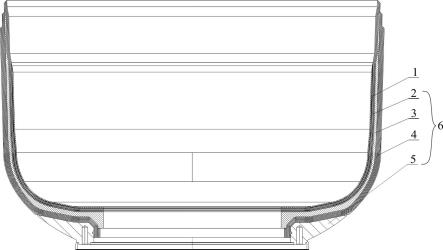
1.本发明涉及复合材料技术领域,特别涉及一种火箭发动机壳体。
背景技术:2.随着复合材料行业的发展,固体火箭发动机壳体燃烧室材料不断更新,由原来的金属材料逐渐替代为大比例复合材料,由于复合材料具有高的比强度、比刚度及其优越的抗内压能力。发动机绝热后封头的主要作用有:防止高温燃气烧坏壳体结构缠绕层、缓冲推进剂燃烧时的应力传递、对整个发动机壳体起到密封作用;并且绝热后封头属于整个发动机受内压力最大的地方,对其结构强度、耐烧蚀、抗冲刷能力有较大要求。
3.目前主流发动机壳体绝热封头主要采用三元乙丙为主要原材料,在封头金属接头背面区域增加抗冲刷层(抗冲刷层硬度高,且抗冲刷层为预制体,整体安装定位较为困难),如现有技术中的一种火箭发动机壳体复合材料绝热封头制作方法,其公开号为:cn112297461a,公开日为:2021-02-02,难以做成整体后封头抗冲刷层提高抗冲刷能力保护壳体后封头区域,如何成型后封头将抗冲刷层成型至筒身段是大家都要解决的问题,为何需要延伸抗冲刷层:固体火箭发动机壳体燃烧室工作时推进剂燃烧过程中会对发动机尾部产生较大冲刷力,三元乙丙橡胶具有一定的耐烧蚀能力及隔热能力,但抗冲刷能力较差,抗冲刷层具备较强的耐烧蚀能力及抗冲刷能力,但隔热能力一般,因此需要在壳体尾部绝热层间加一层抗冲刷层为发动机尾部提高发动机燃烧室工作时结构层抗高温冲刷能力;一些特殊型号发动机壳体推进剂燃烧时冲刷力较高,因此对发动机尾部的耐冲刷能力要求也较高,国内封头绝热成型常用工艺为模压工艺,抗冲刷层只能铺贴至弧度区域,无法再直筒段成型(若将抗冲刷层铺贴至直筒段,模压时容易变形),热压罐工艺成型成型面压力相对均匀,可以保证抗冲刷层内外三元乙丙厚度(模压工艺无法保证)。抗冲刷层延伸至筒段可以提高发动机尾部的耐烧蚀、耐压、抗冲刷能力,提火箭/导弹发动机壳体的安全系数。
技术实现要素:4.针对现有技术中存在的不足,本发明提供了一种耐冲刷发动机壳体绝热封头成型方法,解决了现有技术抗冲刷层短,无法延伸至筒体部分,还解决了火箭发动机壳体在注药冷却收缩后内层收拉力影响的问题,降低发动机运行时高温下发动机末端的应变集中水平。
5.本发明的目的是这样实现的:一种耐冲刷发动机壳体绝热封头成型方法,绝热封头包括由内而外的绝热橡胶层、抗冲刷层以及金属接头,其中抗冲刷层夹在绝热橡胶层内,绝热橡胶层分为前封头绝热层和后封头绝热层,其特征在于,所述绝缘橡胶层内还设有盖层,所述绝热橡胶层、抗冲刷层、盖层均由金属接头延伸至筒段,所述成型方法包括以下步骤:步骤1)前封头绝热层铺贴成型,将金属接头置于下模具中,铺贴橡胶层,在金属接头与前封头绝热层两者对应的粘接区域刷粘接剂,铺贴时从金属接头延伸至筒段,铺完完
成后使用热压罐工艺预固化;步骤2)抗冲刷层成型,将抗冲刷层与前封头绝热层的表面刷粘接剂,抗冲刷层也由金属接头延伸至筒段,放置好抗冲刷层后制作真空袋抽真空,然后在表面铺贴一层橡胶层,使用热压罐工艺预固化;步骤3)后封头绝热层铺贴成型,对抗冲刷层表面的橡胶层表面进行打磨、清洗,涂刷粘接剂,然后铺贴橡胶层,铺贴完成后进行模压固化,得到封头底层;步骤4)封头盖层铺贴成型,在盖层模具表面r角区域、待铺贴的橡胶表面涂刷粘接剂,每铺完一处位置再进行下一处刷胶,铺贴压实,完成后模压固化;步骤5)封头盖层与封头底层成型,将封头盖层和封头底层模压件修剪,清理;先将封头底层与封头盖层接触的面进行清理,接着在封头底层的脱粘层区域贴脱模布,脱粘层区域为封头盖层与封头底层接触区域,然后打磨未贴脱模布区域,打磨完用进行清理,晾干,最后在表面刷一层粘接剂;再将封头盖层与封头底层接触的面进行清理,在与底层接触区域进行打磨,打磨完进行清理,晾干,最后在表面刷一层粘接剂;最后将封头底层放入底层模具的阴模中,在封头底层和封头盖层的粘接面铺贴一层epdm生片,然后将盖层合并到底层中,最后打袋固化,脱模得到耐冲刷发动机壳体绝热封头。
6.作为本发明的进一步限定,步骤1)具体包括:在金属接头与前封头绝热层粘接区域刷一层底涂胶,晾干后再刷一层粘接剂,接着在清理干净的橡胶表面刷一层粘接剂,等金属接头和橡胶表面胶粘剂晾干后进行铺贴,铺贴要求对第1层铺贴完成后制袋预抽。
7.作为本发明的进一步限定,步骤2)放置好抗冲刷层后,在制作真空袋抽真空前,在表面刷少量的粘接剂。
8.作为本发明的进一步限定,步骤3)完成后还需进行检测,具体包括:检测绝热层表面平整、清洁无污,无多余物,不允许有明显鼓包、凹坑、裂纹、缺料、疏松、压伤、气孔、划伤、皱褶,用x射线对绝热层进行无损检测,检测是否有脱粘。
9.作为本发明的进一步限定,步骤4)具体为:将密封打包的橡胶取出,用医用脱脂纱布蘸取化学试剂乙酸乙酯进行清洗,至少2遍以上,清洗至表面洁净无尘,并晾干15min以上,在盖层下模模具表面r角区域刷涂粘接剂,只刷r角和料片中间,晾干3-5min,铺贴在表面,压至有点凹陷即可,每铺完一处位置再进行下一处刷胶,模具铺贴压实,橡胶之间搭接10-15mm,用卡尺进行测量,铺完后需要进行模压固化。
10.与现有技术相比,本发明的有益效果在于:(1)本发明制造的绝热封头能够承受3000℃的烧蚀3min左右,能够满足固体发动机壳体燃烧室使用;(2)本发明制造的绝热封头质量比传统方案,抗冲刷层延伸至筒身段区域,强度更高,抗冲刷能力更强,耐烧蚀能力更强,从而提高发动机运行安全系数,提高发动机工作稳定性;(3)本发明制造的绝热封头采用多次预压成型方案,可保证各个材料区域的厚度,比一体封头成型方案更容易满足各种型号产品的相关设计厚度要求;(4)本发明制造的绝热封头盖层与底层粘接质量相比传统封头模压形式粘接强度更高;(5)本发明制造的绝热封头,金属、绝热、抗冲刷层层间扯离强度、剪切强度均达到
3.0mpa以上,高于传统一体模压成型工艺;(6)本发明可适用于所有固体火箭发动机壳体封头制作,适用范围更广。
附图说明
11.为了更清楚地说明本发明实施例或现有技术中的技术方案,下面将对实施例或现有技术描述中所需要使用的附图作简单地介绍,显而易见地,下面描述中的附图仅仅是本发明的实施例,对于本领域普通技术人员来讲,在不付出创造性劳动的前提下,还可以根据提供的附图获得其他的附图。
12.图1为本发明制得的绝热封头外形图。
13.图2为本发明制得的绝热封头截面图。
14.图3为本发明中封头底层制作用模具。
15.图4为本发明中封头盖层制作用模具。
16.图5为本发明中封头盖层铺贴刷胶示意图。
17.其中,1封头盖层,2后封头绝热层,3抗冲刷层,4前封头绝热层,5金属接头,6封头底层。
具体实施方式
18.下面将结合本发明实施例中的附图,对本发明实施例中的技术方案进行清楚、完整地描述,显然,所描述的实施例仅仅是本发明一部分实施例,而不是全部的实施例。基于本发明中的实施例,本领域普通技术人员在没有做出创造性劳动前提下所获得的所有其他实施例,都属于本发明保护的范围。
19.如图1-2所示,为本发明制得的封头,包括由内而外的封头盖层1、后封头绝热层2、抗冲刷层3、前封头绝热层4以及金属接头5,其中抗冲刷层3主要为发动机提供抗推进剂燃烧冲刷能力与抗烧蚀能力,封头盖层1主要降低发动机运行时高温下发动机末端的应变集中水平。
20.绝热封头的工作环境要求,主要为发动机壳体燃烧室绝热结构层,主要作用是防止高温燃气烧坏燃烧室壳体,防止因温度过高导致壳体强度下降,并尽可能地减轻封头重量从而减轻发动机壳体重量。
21.选材方案如下:表1 三元乙丙橡胶性能 密度(g/cm3)氧乙炔线烧蚀率(mm/s)拉伸强度(mpa)扯断伸长率(%)指标要求≤1.1≤0.12≥3.5≥200
三元乙丙橡胶综合性能好,是良好的绝热层基体材料,三元乙丙橡胶密度低、延伸率高,具有良好的抗烧蚀性能和隔热性能,可长期存储,与推进剂有很好的化学相容性。
22.表2 抗烧蚀编织体性能 密度(g/cm3)氧乙炔线烧蚀率(mm/s)拉伸强度(mpa)扯断伸长率(%)指标要求≤1.40≤0.04≥15≥15
抗烧蚀编织体(抗冲刷层)氧乙炔线烧蚀率低,抗拉强度高,可有效提高整个发动机后端的抗推进剂冲刷能力,从而提高发动机运行安全系数,提高发动机工作稳定性;但抗
烧蚀编织体硬度较高,难以定位。
23.成型工艺具体如下:步骤1)前封头绝热层4铺贴成型工艺:在金属接头5粘接区域刷一层金属与橡胶粘接底涂胶开姆洛克205(晾干15min),等晾干后再刷一层ae-2(金属与橡胶粘接剂),接着在清理干净的1mm橡胶表面刷一层ae-2,等金属接头5和橡胶表面胶粘剂晾干后进行铺贴,铺贴要求对接第1层铺贴完成后制袋预抽,预抽时间≥15min,空袋内的真空度达到≤-0.085mpa以下开始计算,铺贴每层一抽,时间≥15min;前封头绝热层4橡胶铺贴结束后制作真空袋,对抗冲刷层3前的绝热层进行预成型,真空袋固化的方式可减少模压模具的投入,降低产品制作成本,并且能保证抗冲刷层3前绝热橡胶型面与理论型面相近,与后面的抗冲刷层3安装贴合较好,预成型后可使用型面样板进行匹配检测,修磨凸起位置,以保证型面与后面的抗冲刷层3完全贴合。
24.步骤2)抗冲刷层3铺贴成型工艺:在抗冲刷层3表面刷少量的ae-3(碳材料与橡胶粘接剂),然后抗冲刷层3表面刷少量的ae-3晒干3-5min;将抗冲刷层3安装到前封头绝热层4中,然后在抗冲刷层3表面再铺一层橡胶绝热层,结束后制作真空袋进行预成型。
25.步骤3)后封头绝热层2成型工艺:在抗冲刷层3表面的橡胶绝热层表面进行打磨、乙酸乙酯清洗,涂刷ae-4(绝热半熟片与熟片粘接剂),然后铺贴后封头绝热层2绝热橡胶,铺贴完成后进行模压固化,得到封头底层6。
26.步骤4)封头盖层1成型工艺:在盖层专用下模具表面r角区域刷涂少量ae-1胶(提高界面抽粘力的胶),同时在橡胶表面刷涂ae-1胶,每铺完一处位置再进行下一处刷胶,模具铺贴压实,铺贴完成后模具合模固化。
27.步骤5)封头盖层1与后封头绝热层2绝热粘接成型工艺:将封头盖层1和封头底层6模压件修剪,清理,将底层与阳模接触的面进行清理,接着在脱粘层区域贴脱模布,然后打磨未贴脱模布区域(用锉刀皮进行打磨),打磨完用乙酸乙酯进行清理,晾干,最后在表面刷一层ae-4;将盖层与阴模接触的面进行清理,在与底层接触区域进行打磨(用锉刀皮进行打磨),打磨完用乙酸乙酯进行清理,晾干,最后在表面刷一层ae-4。将底层放入底层模具的阴模中,在底层和盖层的粘接面铺贴一层0.5mm厚的epdm生片,然后将盖层合并到底层中,最后打袋固化,生片与熟片粘接性能更好,因此,分别预成型的底层、盖层间夹一层生片涂刷生片与半熟片粘接剂;且热压罐成型工艺可保证压力均匀分布在产品内表面,相比较模压成型工艺,半熟片模压可能会导致橡胶出现压不实、疏松现象。
28.绝热层橡胶铺贴主要工艺过程如下:工艺过程主要分为以下五个部分,一、裁剪、倒角,二、清洗,三、刷胶,四、铺贴,五、赶泡,为了保证壳体橡胶硫化后的粘接质量;具体过程如下。
29.1)对封头同层之间的料片进行8等分进行铺层设计下料图,按照下料图纸进行cad排版下料。
30.2)顺气流方向搭接,各层周向搭接缝不得重叠,位置错开2mm以上,搭接缝保持在10~15mm,搭接部位需进行斜边倒角,确保产品厚度一致,以满足绝热层结构制作要求。橡胶层之间刷指定j-1本体胶粘贴,要求贴片后的橡胶没有橡胶鼓泡出现。
31.3)在绝热层结构制作时,料片之间不能存在绝热材料碎屑和其他多余物,多余物按qj2850标准进行处理;绝热制作环境要求在场温度(24
±
10.℃,相对湿度≤75%,按要求
记录每天的温度与湿度。
32.4)记录每片绝热层涂胶时间、晾置时间、绝热层粘贴时间等参数,每片绝热层需进行厚度检测、涂胶量、绝热层粘贴完成后记录绝热层总重量及胶液重量。
33.其中为了保证前后封头绝热橡胶性能不受脱膜剂的影响,禁止使用脱膜剂,模具表面进行了聚四氟乙烯烧结,不使用脱膜剂可以达到较好的脱模效果。
34.下面结合具体实例对本发明做进一步说明。
35.一种耐冲刷发动机壳体绝热封头成型方法,包括以下步骤。
36.1)准备接头,对金属接头5表面进行40目石英砂喷制,喷砂后可提高金属接头5与绝热层粘接强度。
37.2)在封头底层6的阴模模具表面刷涂少量胶黏剂,同时刷涂第一层橡胶料片,晾干5min左右,铺贴在模具表面,压实,每铺完一处位置再进行下一处刷胶,铺贴压实,刷胶前与刷胶后需进行称重,属于橡胶与橡胶界面刷胶操作。
38.3)在金属接头5粘接区域(即金属接头5与橡胶接触的区域)刷一层开姆洛克205底涂胶(晾干15min),等晾干后再刷一层ae-2晾干15min。
39.4)将密封打包的橡胶取出,用医用脱脂纱布蘸取化学试剂乙酸乙酯进行清洗(至少2遍以上),清洗至表面洁净无尘,并晾干15min以上。
40.5)在清理干净的橡胶表面刷一层ae-2,晾干15min放入接头,然后将晾干的橡胶铺贴接头表面压实(压至表面有点凹陷即可),其余料片按编号顺序进行铺贴,在下模模具表面r角区域刷涂少量ae-1胶,同时刷涂其中一片,晾干3-5min,铺贴在表面,压至有点凹陷即可,每铺完一处位置再进行下一处刷胶,模具铺贴压实(橡胶之间搭接10-15mm,用卡尺进行测量),属于橡胶与橡胶界面刷胶操作。
41.6)对上述铺贴过程中,每结束铺贴一层,对橡胶表面状态进行检测,使用赶板对所有区域进行压实,若发现未压实,对残留气泡铺贴时使用钢针扎破,压实,若无法压实使用针筒注入适量的胶,晾干5min左右,再进行压实。
42.7)前封头绝热层4绝热预固化:连接到真空系统,施加-0.085mpa以下的真空压力,并施加0.5mpa的空气压力,保持至少15min不泄漏,固化参数:i)室温下加压,以0.02mpa/min速率加压至0.5mpa,室温下升温,升温速率为1℃/min;ii)介质温度设定为85℃,当最慢升温热电偶升温到80℃后,保温1小时;iii)介质温度设定为95℃,当最慢升温热电偶升温到90℃后,保温2小时;iv)介质温度设定为135℃,当最慢升温热电偶升温到130℃后,保温2小时;v)以不大于1℃/min的速度冷却,当降温最慢的热电偶温度降低至60
°
c以下后,卸压,卸压完成后可开罐。
43.8)抗冲刷层3铺贴:放置抗冲刷层3底层绝热,在表面刷少量的ae-3(晒干3-5min),然后抗冲刷层3表面刷少量的ae-3(晒干3-5min),放置后制作真空袋抽真空2h,然后在表面铺贴1层1mm三元乙丙,布置真空装置,准备预压。
44.9)抗冲刷层3预固化,固化参数:i)室温下加压,以0.02mpa/min速率加压至0.5mpa,室温下升温,升温速率为1℃/min;
ii)介质温度设定为85℃,当最慢升温热电偶升温到80℃后,保温1小时;iii)介质温度设定为95℃,当最慢升温热电偶升温到90℃后,保温2小时;iv)介质温度设定为135℃,当最慢升温热电偶升温到130℃后,保温2小时;v)以不大于1℃/min的速度冷却,当降温最慢的热电偶温度降低至60
°
c以下后,卸压;卸压完成后可开罐。
45.10)抗冲刷层3面层绝热铺贴:抗冲刷层3表面绝热用80目砂纸+打磨片打磨粗糙(提高粘接强度)后用乙酸乙酯清理(晒干3-5min),铺贴橡胶,铺完后模压固化;合模前检查模具表面是否有不允许存在的杂物,模压固化参数:(1)升温速率20℃/h,室温-80℃,80℃排气1次,保温1h后开始加压1mpa;(2)升温速率20℃/h,80℃-100℃,100℃排气3次,保温1h后开始加压3mpa;(3)升温速率20℃/h,100℃-120℃,120℃排气3次,保温1h后开始加压6mpa;(4)升温速率20℃/h,120℃-135℃,保温2h;(5)降温速率20℃/h,135℃-50℃,卸压,出炉,得到封头底层6。
46.11)封头底层6检测,绝热结构表面要求平整、清洁无污,无多余物,不允许有明显鼓包(夹气)、凹坑、裂纹、缺料、疏松、压伤、气孔、划伤、皱褶;用x射线对绝热层进行无损检测。检测是否有脱粘。
47.12)封头盖层1铺层:将密封打包的橡胶取出,用医用脱脂纱布蘸取化学试剂乙酸乙酯进行清洗(至少2遍以上),清洗至表面 洁净无尘,并晾干15min以上,在封头盖层1下模模具表面r角区域刷涂少量ae-1胶,同时刷涂r角15mm和扇面顶端2个点、底端2个点,具体如图5所示,由于三元乙丙橡胶生片自粘能力差,铺贴绝热时放止料片移位需要在料片表面涂刷抽粘力较高的胶粘剂来进行料片铺贴,但是胶粘剂会对橡胶自身融合有一定负面作用,因比料片铺贴时在贴实的基础上尽可能少刷胶粘剂,因此在绝热铺贴过程中采用五点涂刷法,晾干3-5min,铺贴在表面,压至有点凹陷即可,每铺完一处位置再进行下一处刷胶,模具铺贴压实(橡胶之间搭接10-15mm,用卡尺进行测量),属于橡胶与橡胶界面刷胶操作,铺完后需要进行模压固化。
48.13)封头盖层1模压固化,固化参数:升温速率20℃/h,室温-80℃,80℃排气1次,保温1h后开始加压1mpa;升温速率20℃/h,80℃-100℃,100℃排气3次,保温1h后开始加压3mpa;升温速率20℃/h,100℃-120℃,120℃排气3次,保温1h后开始加压6mpa;升温速率20℃/h,120℃-135℃,保温2h;降温速率20℃/h,135℃-50℃,卸压,出炉,得到封头盖层1。
49.14)封头盖层1、封头底层6合模铺贴将封头底层6与封头底层6阳模接触的面进行清理,接着在脱粘层区域贴脱模布,然后打磨未贴脱模布区域(用锉刀皮进行打磨),打磨完用乙酸乙酯进行清理,晾干,最后在表面刷一层ae-4,将封头盖层1与封头盖层1阴模接触的面进行清理,在与封头底层6接触区域进行打磨(用锉刀皮进行打磨),打磨完用乙酸乙酯进行清理,晾干,最后在表面刷一层ae-4;将封头底层6和封头盖层1合并(粘接区域再贴一层橡胶提高粘接强度)之后放入底层模具的阴模中,最后进行最终固化。
50.15)封头整体固化,采用热压罐工艺固化,固化参数如下:室温下加压,以0.02mpa/min速率加压至0.5mpa,室温下升温,升温速率为1℃/min;介质温度设定为95℃,当最慢升温热电偶升温到90℃后,保温1小时;介质温度设定为140℃,当最慢升温热电偶升温到135℃后,保温3小时;以不大于1℃/min的速度冷却,当降温最慢的热电偶温度降低至60
°
c以下后,卸压;卸压完成后可开罐。
51.16)脱模,得到最终壳体绝热封头。
52.经检测,本发明制造的绝热封头能够承受3000℃的烧蚀3min左右,能够满足固体发动机壳体燃烧室使用;本发明制造的绝热封头质量比传统方案,抗冲刷层3延伸至筒身段区域,强度更高,抗冲刷能力更强,耐烧蚀能力更强,从而提高发动机运行安全系数,提高发动机工作稳定性;本发明制造的绝热封头采用多次预压成型方案,可保证各个材料区域的厚度,比一体封头成型方案更容易满足各种型号产品的相关设计厚度要求;本发明制造的绝热封头盖层1与底层粘接质量相比传统封头模压形式粘接强度更高;本发明制造的绝热封头,金属、绝热、抗冲刷层3层间扯离强度、剪切强度均达到3.0mpa以上,高于传统一体模压成型工艺;本发明可适用于所有固体火箭发动机壳体封头制作,适用范围更广。
53.以上实施例的说明只是用于帮助理解本发明的方法及其核心思想。应当指出,对于本技术领域的普通技术人员来说,在不脱离本发明原理的前提下,还可以对本发明进行若干改进和修饰,这些改进和修饰也落入本发明权利要求的保护范围内。