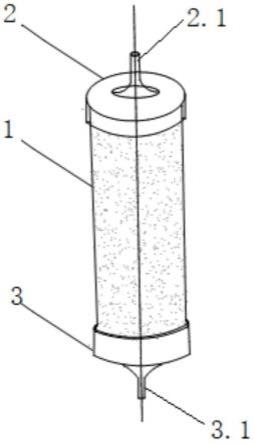
1.本实用新型涉及复合绝缘子技术领域,具体地指一种复合绝缘芯体棒纵置缠绕设备。
背景技术:2.目前国内外的复合支柱绝缘子、复合绝缘横担用大尺寸绝缘芯体棒采用空心填充方案,空心填充方案采用的内部填充绝缘气或绝缘油膏的空心管能有效降低绝缘芯体的质量,但存在内部填料泄漏和凝露的隐患,增加运行维护成本,针对这个问题,目前正在开发一种实心的复合绝缘芯体棒,然而目前的空心填充方案的缠绕设备需要使用专用的金属模具,并有一个脱模过程,而且没法缠绕实心棒,因此急需设计一种实心复合绝缘芯体棒的缠绕设备。
技术实现要素:3.本实用新型的目的就是要提供一种复合绝缘芯体棒纵置缠绕设备,本实用新型抛弃传统固定模具缠绕方式,采取复合绝缘芯一体化临时模具,仅需加工两端的金属套筒固定装置,避免了传统固定模具加工周期长、费用高及后期模具维护费用高等难题,且没有脱模过程,生产效率更高。
4.为实现此目的,本实用新型所设计的复合绝缘芯体棒纵置缠绕设备,它包括绝缘聚合物芯体、芯体上端套筒和芯体下端套筒,所述芯体上端套筒套接并固定在绝缘聚合物芯体上端的外侧壁上,芯体下端套筒套接并固定在绝缘聚合物芯体下端的外侧壁上,所述芯体上端套筒顶部固定有上端缠绕机固定轴,芯体下端套筒的底部固定有下端缠绕机固定轴。
5.本实用新型的有益效果:
6.使用本实用新型进行复合绝缘芯体棒缠绕,采取复合绝缘芯一体化临时模具,仅需加工两端的金属套筒固定装置,避免了传统固定模具加工周期长、费用高及后期模具维护费用高等难题,且没有脱模过程,生产效率更高。另外,芯体棒缠绕进行固化后,样品无需脱模,轻质高绝缘复合芯体与表面的浸胶纤维树脂一体固化成为一个整体,只需将端部两个金属固定套筒装置切割去除即可得到轻质高绝缘复合芯体棒。切割下来的轻质高绝缘芯体端部固定用的上下端套筒装置可以清除内部轻质高绝缘芯材料和表面的树脂纤维材料,实现回收重复使用。
附图说明
7.图1为复合绝缘芯体棒纵置缠绕设备的结构示意图;
8.图2为利用复合绝缘芯体棒纵置缠绕设备的缠绕工艺的结构示意图。
9.其中,1—绝缘聚合物芯体、2—芯体上端套筒、2.1—上端缠绕机固定轴、3—芯体下端套筒、3.1—下端缠绕机固定轴、4—浸胶纤维、5—固化站。
具体实施方式
10.以下结合附图和具体实施例对本实用新型作进一步的详细说明:
11.本实用新型所设计的一种复合绝缘芯体棒纵置缠绕设备,如图1和2所示,它包括绝缘聚合物芯体1、芯体上端套筒2和芯体下端套筒3,所述芯体上端套筒2套接并固定在绝缘聚合物芯体1上端的外侧壁上,芯体下端套筒3套接并固定在绝缘聚合物芯体1下端的外侧壁上,所述芯体上端套筒2顶部固定有上端缠绕机固定轴2.1,芯体下端套筒3的底部固定有下端缠绕机固定轴3.1。芯体套筒均选用不锈钢套筒,避免了树脂中酸性或碱性物质腐蚀金属套筒。
12.所述芯体上端套筒2、上端缠绕机固定轴2.1、绝缘聚合物芯体1、芯体下端套筒3和下端缠绕机固定轴3.1为同轴设置,同轴设计可以保证芯体在纵置旋转的过程出现偏转现象,维持缠绕工艺过程其平稳运行。
13.所述芯体上端套筒2和芯体下端套筒3的筒深相等,均为绝缘聚合物芯体1直径的0.5~2倍,聚合物芯体掺入套筒中合适的深度,能保证芯体与套筒更好结合。
14.所述绝缘聚合物芯体1与芯体上端套筒2为过盈配合,绝缘聚合物芯体1与芯体下端套筒3为过盈配合。其套筒的内径尺寸与绝缘聚合物芯体1直径相当,也可以稍微小于1的直径,其公差应控制在1mm范围内,保证绝缘聚合物芯体1能够和芯体上端套筒2、芯体下端套筒3完好装配;
15.所述绝缘聚合物芯体1的上、下端套筒装置上下套接后,芯体上端套筒2和芯体下端套筒3之间施加不大于100n的压力固定绝缘聚合物芯体1,或所述绝缘聚合物芯体1与芯体上端套筒2之间通过绝缘胶水固定,绝缘聚合物芯体1与芯体下端套筒3之间通过绝缘胶水固定,施加一定荷载的压力或用绝缘胶水固定,都是为了保证聚合物芯体能与套筒更好连接,保证其能和套筒能同步旋转。
16.利用复合绝缘芯体棒纵置缠绕设备生产的复合绝缘芯体棒,包括绝缘聚合物芯体和缠绕在绝缘聚合物芯体上的浸胶纤维,所述绝缘聚合物芯体为轻质高绝缘聚合物芯体;
17.所述绝缘聚合物芯体为环氧树脂与微纳米级空心有机微珠或玻璃微珠的聚合物复合芯体,或者为聚氨酯树脂与空心有机微珠或玻璃微珠的聚合物复合芯体,上述绝缘聚合物芯体为常规材料,具体见中国专利202010264017.3和中国专利201910641904.5;
18.所述浸胶纤维缠绕在绝缘聚合物芯体上的缠绕角度为10~90
°
,即浸胶纤维4与绝缘聚合物芯体1的轴向夹角为10~90
°
,可根据复合芯棒的结构强度进行缠绕角度选择。通过对纤维与绝缘聚合物芯体缠绕角度的控制,实现纤维在芯体上的铺层设计,缠绕角度越小,纤维在轴向的铺放量越大,对应制品的轴向力学强度就越强,环向的强度就相对弱些;反之,缠绕角度越大,环向纤维铺放量越多,制品的环向强度就越大,对应的轴向强度就弱些;通过合理缠绕角度控制,便可以设计出轴向及环向综合力学性能均衡的制品。
19.所述绝缘聚合物芯体1为圆柱体绝缘聚合物芯体,采用圆柱体,可以保证浸胶纤维可以更好和圆柱体表面贴合,避免纤维与芯体表现出现孔洞或缺陷,并且圆柱体垂直旋转过程,产生的偏心力最小,制备的制品表面也更均匀和光滑。
20.所述缘聚合物芯体1的密度为0.3~0.6g/cm3,复合芯体表面平整,长度不超过5米,所述缘聚合物芯体1的表面粗糙度ra值10~100微米。保持聚合物芯体表面微粗糙,可以保证浸胶纤维能更好与聚合物芯体表面结合,提升其结合界面强度,同时也避免了芯体表
面过于粗糙,导致浸胶纤维与芯体界面产生缺陷,影响制品的致密性。
21.一种利用复合绝缘芯体棒纵置缠绕设备进行复合绝缘芯体棒缠绕的工艺,如图2所示,它包括如下步骤:
22.步骤1:将芯体上端套筒2套接并固定在绝缘聚合物芯体1上端的外侧壁上,将芯体下端套筒3套接并固定在绝缘聚合物芯体1下端的外侧壁上,形成复合绝缘芯体缠绕临时模具;
23.步骤2:将复合绝缘芯体缠绕临时模具保持纵置状态,芯体上端套筒2的上端缠绕机固定轴2.1和芯体下端套筒3的下端缠绕机固定轴3.1固定到缠绕装置上;
24.步骤3:缠绕装置以预设转速带动复合绝缘芯体缠绕临时模具旋转,将浸胶纤维4以一定角度或可变的角度缠绕到绝缘聚合物芯体1表面,缠绕获得设计层厚的纤维层后,再将缠绕了浸胶纤维4的复合绝缘芯体缠绕临时模具保持垂直的状态,送入固化站5中热固化,热固化过程中浸胶纤维的复合绝缘芯体缠绕临时模具始终保持垂直、均匀旋转状态,固化过程始终保持纵置状态,且维持低速旋转,以保证制品能均匀受热,同时防止了固化过程树脂在制品表面产生流挂现象;
25.步骤4:固化后将复合绝缘芯体缠绕临时模具的芯体上端套筒2和芯体下端套筒3切除,得到绝缘复合芯体棒制品。
26.所述纤维层的设计层厚范围为8~30mm,固化温度范围为100~140℃,固化时间范围为2~4小时,根据树脂固化特性,选择合适的固化温度和时间,一般树脂活性高,其热固化温度就低且时间段,反之固化温度就高或时间长。
27.实施案例1
28.将直径为204mm、长度3500mm的轻质高绝缘复合芯体与上下端金属套筒装置(带端部固定轴)套节形成临时一体化芯体,一体化芯体垂直放置于缠绕机上,充当纵置缠绕工艺的固定模具,并在其表面缠绕浸润环氧树脂胶的玻璃纤维,纤维与一体化芯体的夹角控制为60
°
,缠绕纤维层至其厚度达到10mm,再将纵置缠绕制备的复合芯体棒预制品保持纵置的状态,送入热固化站中保持匀速旋转状态进行固化,固化温度为120℃固化2小时,期间复合芯体与外层的浸润环氧胶纤维层一体固化,得到轻质高绝缘复合芯体棒成品,切割去掉端部金属套筒固定装置,获得外径为224mm、长度3000mm的轻质高绝缘复合绝缘芯体棒,该复合绝缘芯体可以用于绝缘子支柱的芯体。
29.实施案例2
30.将直径为130mm、长度3300mm的轻质高绝缘复合芯体与上下端金属套筒装置(带端部固定轴)套节形成临时一体化芯体,一体化芯体垂直放置于缠绕机上,充当纵置缠绕工艺的固定模具,并在其表面缠绕浸润环氧树脂胶的玻璃纤维,纤维与一体化芯体的夹角控制为30
°
,缠绕纤维层至其厚度达到10mm,再将纵置缠绕制备的复合芯体棒预制品保持纵置的状态,送入热固化站中保持匀速旋转状态进行固化,固化温度为120℃固化2小时,期间复合芯体与外层的浸润环氧胶纤维层一体固化,得到轻质高绝缘复合芯体棒成品,切割去掉端部金属套筒固定装置,获得外径为150mm、长度约3000mm的轻质高绝缘复合绝缘芯体棒,该复合绝缘芯体可以用于220kv复合绝缘横担的结构芯体。
31.利用本实用新型芯体缠绕,采取了纵置缠绕工艺,避免复合绝缘芯一体化临时模具横置时,其自身的重量导致复合芯弯曲或断裂,而纵置放置结构则合理的将自重落在下
端的套筒固定装置,消除复合芯体自重对材料本体的破坏,同时纵置也减小了临时模具尺寸较长的时候,出现旋转的过程发生偏转的概率,提高了制品的加工稳定性。
32.另外,样品的外观直径尺寸可以根据需要,加工成不同尺寸,调准轻质高绝缘聚合物/填料芯体和轻质高绝缘聚合物/填料芯体上、下端套筒装置(带端部固定轴)尺寸,加工成本低,时间短。
33.并且,固化过程,保持轻质高绝缘复合芯体棒预制品垂直匀速旋转,可保证产品外圆均匀,避免横置旋转的时候树脂胶在制品表面流挂,固化后表面凹凸不平,提高了产品尺寸稳定性。
34.本说明书未作详细描述的内容属于本领域专业技术人员公知的现有技术。