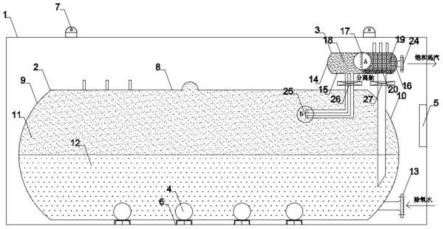
1.本发明属于储能设备领域,具体涉及一种用于储能供汽的模块。
背景技术:2.移动储能供热技术能将间断、分散、不稳定的热能有效储存并应用,有效解决能源双重浪费问题。利用移动储能供热技术可以缓解能量供求双方在时间、强度、地点上的不协调,有效对余热进行回收、储存、转移和利用,从而达到节能减排、提高能源综合利用效率的目标。
3.移动储能供热技术可脱离供热管网的局限,将热量直接输送至各用户端,实现灵活的“分布式”供热方式。移动供热项目是利用夜间低谷电或工业余热蒸汽通过快速接口进入储能装置,加热储能体,储能体一般是固体材料,内部储能材料由固态变为液态,此过程实现热能转化和储存,通过控制系统对温度、流量进行调整,使之达到供热标准。当用户侧需要供热时,利用拖车移动储能车,送至用户端,将间断的、分散的、不稳定的大量工业余热或低谷电有效地、高密度地储存并使用,替代(燃料、燃气、电)锅炉等能源设备,替代一次性不可再生能源。
4.但现有的设备存在一些明显的技术缺陷或难题,具体表现在以下几个方面。包括:
5.1、现有移动储能设备或装置的换热结构缺陷导致充、放热过程中存在二次、三次甚至多次换热,换热效率低下,如何提升换热效率是移动储能技术难题之一。
6.2、现有移动储能设备或装置内部附属装置占地空间较大,如板式换热器、电加热器、循环泵等附属设备,致使储热材料的体积占比有限,使其单位体积储热密度较低,单台设备难以规模化应用。
7.3、如何进一步提高移动储能设备换热效率及单位储能密度,单台设备如何能突破性实现加热、储热、换热(放热)功能,并可安全稳定输出蒸汽。
8.鉴于此,本发明提出一种用于储能供汽的模块。
技术实现要素:9.为解决现有技术中的难题,本发明拟解决的技术问题是,提供一种用于储能供汽的模块,使之具有单位体积储热密度高、效率高、结构简单、空间利用率高、安全可靠、可稳定输出饱和蒸汽、便于维护及运行管理方便的特征,解决了现有可移动储能供热模块存在的难题。
10.本发明解决所述技术问题的技术方案是,一种用于储能供汽的模块,其特征在于,该模块包括集装箱、加热蒸发舱、分离舱、电加热装置;所述加热蒸发舱2、分离舱3、电加热装置4全部内置于集装箱1内部,加热蒸发舱内根据储能材料的状态将封闭空腔划为加热舱和蒸发舱,加热舱中储能材料的状态为液态,蒸发舱中储能材料的状态为气态;
11.分离舱内根据蒸汽流动区域不同,通过设置在分离舱筒体内部中分面的二级汽水分离装置17,将分离舱的封闭空腔划为进汽段18、排汽段19和疏水段20;
12.所述分离舱的进汽段和蒸发舱之间连接有上汽管,分离舱的疏水段和加热舱之间连接有降液管;
13.加热舱一侧设置通过给水管连接除氧水,分离舱的排汽段连接供汽管;
14.在所述加热舱的底部设置若干数量的电加热装置。
15.所述模块还包括有控制系统,所述控制系统包括自动控制器、信号线、第一参数监测模块、第二参数监测模块,所述第一参数监测模块设置在所述分离舱上,所述第二参数监测模块设置所述加热蒸发舱上,所述第一参数监测模块和第二参数监测模块至少包括温度传感器和压力传感器,所述自动控制器与所述第一参数监测模块、第二参数监测模块和电加热装置通过电气信号线连接;所述自动控制器内挂于集装箱沿长度方向的尾部内壁面上,距地面高度不超过1.5m。
16.所述控制系统根据参数监测控制流体的温度、压力参数、加热蒸发舱内的温度及压力和电加热器功率,确保储能供汽模块安全、稳定、高效运行。
17.在集装箱内,所述加热蒸发舱沿长度方向的外圆周侧面和集装箱内壁之间留有不小于 750mm的检修空间,加热蒸发舱的顶部外空间高度距离满足分离舱安装维修使用的最低高度要求;加热蒸发舱的底部和集装箱底部内壁之间通过纵向支撑件固定连接在一起,所述电加热装置通过横向支撑件固定在加热舱内;所述加热舱11底部区域设有多组电加热装置4,多组电加热装置均匀排布,高度一致,所述电加热装置的电加热管沿所述加热舱径向方向伸入加热舱内部,电加热管末端未触及第一圆柱形壳体内壁面,留有安全距离;
18.所述集装箱顶部对称设置若干数量用于吊装的吊耳,吊耳采用高强度低合金钢材料,材料标准抗拉屈服强度下限值不低于540mpa,通过焊接方式与集装箱顶部固定连接;
19.所述电加热装置的电加热管内空腔设有电加热丝,采用铬镍合金材料,优选选用 ni80cr20;电加热管内空腔内部填充有导热绝缘材料,导热绝缘材料选用耐高温氧化镁粉;耐高温氧化镁粉的重量百分组成:93.5%的mgo、2%的cao、0.5%的fe2o3、2%的a12o3、 2%的sio2,按重量百分数取上述各组分,均匀混合,即得上述耐高温氧化镁粉,填充密度为 1.05~1.1kg/m3。
20.所述加热蒸发舱包括第一圆柱形壳体、第一左封头、第一右封头,所述第一圆柱形壳体一端与第一左封头通过焊接方式固定连接,属于不可拆卸连接;所述第一圆柱形壳体另一端与第一右封头通过螺栓、螺母和垫片固定连接,属于可拆卸连接;第一左封头将第一圆柱形壳体的一端密封,第一右封头将第一圆柱形壳体的另一端密封;第一左封头、第一右封头和第一圆柱壳体围成一封闭空腔;根据储能材料的状态将封闭空腔划为加热舱和蒸发舱,加热舱为高压饱和水加热提供加热空间,蒸发舱为高压饱和水蒸发提供蒸发空间;
21.所述分离舱,布置于所述加热蒸发舱正上方和所述集装箱正下方间,所述分离舱包括第二圆柱形壳体、第二左封头、第二右封头。所述第二圆柱形壳体一端与第二左封头通过焊接方式固定连接,属于不可拆卸连接;所述第二圆柱形壳体另一端与第二右封头通过螺栓、螺母和垫片固定连接,属于可拆卸连接;第二左封头将第二圆柱形壳体的一端密封,第二右封头将第二圆柱形壳体的另一端密封;第二左封头、第二右封头和第二圆柱壳体围成一封闭空腔;所述第二圆柱形壳体上部依次设置压力表管座、安全阀管座、温度计管座;
22.所述加热蒸发舱与所述分离舱通过上汽管和降液管互连互通,所述上汽管入口端部先沿着所述加热蒸发舱径向方向垂直伸入所述蒸发舱,在未触及所述加热舱前,水平向
第一左封头所在方向延神,水平方向延伸长度不超过所述第一圆柱形壳体长度1/8;所述上汽管出口端部垂直伸入至所述分离舱进汽段,与分离舱第二圆柱形壳体底部圆弧面通过法兰连接,属于可拆卸式连接结构;所述降液管入口端部垂直伸入至所述分离舱疏水段,与分离舱第二圆柱形壳体底部圆弧面通过法兰连接,属于可拆卸式连接结构;所述降液管出口端部沿着所述加热蒸发舱径向方向经所述蒸发舱后垂直依次伸入蒸发舱和加热舱;
23.所述上汽管入口端与上汽管出口端之间的管路上设有第一控制阀26,所述降液管入口端与降液管出口端之间的管路上设有第二控制阀27。
24.所述上汽管垂直向下进入加热蒸发舱的第一圆柱形壳体部分,降液管垂直向下插入加热蒸发舱的第二右封头部分。
25.所述二级汽水分离装置包括隔板21、格栅22和扁钢30,所述隔板整体为圆形板,圆形板的边缘与分离舱的内壁无缝焊接在一起,隔板沿第一圆柱形壳体的高度方向垂直布置,且布置于分离舱的中分面位置;所述隔板21的底部设有导流间隙28,导流间隙沿分离舱的宽度方向设置,优选地,导流间隙高度不超过隔板垂直高度的10%,不小于隔板垂直高度的5%;在导流间隙上表面的隔板位置焊接有水平向右的扁钢,扁钢另一端以焊接方式与右侧的分离舱内壁固定连接;隔板左侧为进汽段,隔板右侧为供汽段和疏水段,其中,扁钢上方的空间为供汽段,扁钢下方的空间为疏水段;
26.位于导流间隙上部的隔板上开设有多组导汽间隙29,导汽间隙处均设有格栅22,格栅覆盖住导汽间隙,使得蒸汽先经过格栅再由导汽间隙进入供汽段;所述格栅上侧与隔板均通过焊接固定连接,格栅上设置有若干数量的导汽孔。
27.所述格栅在隔板上正投影的总面积大于所覆盖的导汽间隙的面积,格栅与隔板之间的夹角为20
°
~30
°
,所述格栅上均匀布置有直径为8mm的导汽孔23,格栅的数量不低于6片,每片格栅的宽度不超过隔板高度的1/8,每片格栅上的导汽孔数量不低于16个。
28.所述上汽管位于蒸发舱内的入口端设置有用于除掉气相中携带微量雾滴的一级汽水分离装置;所述一级汽水分离装置包括环形圆盘和若干数量的倾斜安装在环形圆盘上的过滤挡片,所述过滤挡片一方面与环形盘面的内径固定,另一方面与环形盘面的外径固定,且每个过滤挡片与环形圆盘的盘面之间的夹角相同,环形圆盘的内外径之间为镂空空间,环形圆盘的内圆区域封闭,所述过滤挡片上开设有若干数量的筛孔;所述上汽管为内外套管形式,外套管与环形圆盘的外径固定在一起,内套管与环形圆盘的内径固定在一起,且外套管与分离舱和蒸发舱相连通,内套管的两端均封闭,蒸发舱内的蒸汽经过滤挡片后由环形圆盘的内外径之间进入外套管和内套管之间的空间内,最后再进入分离舱的进汽段。
29.所述过滤挡片上设置有微小的筛孔,筛孔直径φ为2.5~5mm,筛孔数量为100~200个,其中,过滤挡片为等腰直角三角形,过滤挡片与环形圆盘的夹角为10
°
~60
°
。
30.上述模块工作原理为:夜间低谷电时段,除氧水经所述给水管13进入所述加热舱12,充水高度达到设定液位值时,启动电加热装置4开始加热,由于蒸发舱和加热舱两者是相通的,加热舱12内的水被加热蒸发,产生的湿蒸汽进入蒸发舱储存,当湿蒸汽温度、压力达到储热设定值时,停止电加热装置的加热工作,储热过程完毕;
31.待非低谷电时段,开启第一控制阀26和第二控制阀27,所述蒸发舱11内的湿蒸汽经所述一级汽水分离装置25分离后通过上汽管进入进汽段,携带一部分水雾的蒸汽进入分离舱的进汽段继续分离,分离后的细水雾形成水滴经疏水段由降液管进入加热舱,分离后
的饱和蒸汽经供汽段由供汽管24对外输出;当湿蒸汽温度、压力经所述控制系统监测达到放热设定值时,关闭第一控制阀和第二控制阀,放热过程完毕。
32.与现有技术相比,本发明的有益效果是:
33.1)本发明结构简单,创新性将加热、储能与汽水分离功能耦合一体并形成模块,可实现高效汽水分离,使蒸汽纯度大大提高,同时将将汽水分离和蒸汽分配功能集成一个整体,减少了蒸汽带水量,提高蒸汽品质,模块也便于运输。一般地,传统储热车内部附属装置占地空间较大,如板式换热器、电加热器、循环泵等,致使储热材料的体积占比有限,使其单位体积储热密度较低,本发明与传统移动储能供热车相比,由于电加热装置、加热蒸发舱和二级汽水分离装置耦合集成于一体,从而节省空间(耦合指:无需通过管道的形式将三者连接形成一整体,通过各个设备本体结构以焊接方式连接,加热蒸发舱筒体尺寸较大(包括长度和直径)可满足电加热装置加热管伸入加热舱内部长度的要求,此外,电加热装置内置于加热舱可减少动力输送装置泵,降低能耗),提高储材料使用率,各项性能指标优于现有移动储能供热车,同等储能量情况下,本发明可空间节省约30%~45%。
34.2)常规移动储能设备采用非水介质作为储能材料及导热油作为中间传热介质,加热时,热量移动方向为:电加热器制热
→
导热油
→
储能材料,放热时,储能材料
→
导热油
→
水/蒸汽。因此,导致设备存在多次换热的过程。本发明一方面优化设备结构形式,改变了传统的多次换热形式,省去传统设备中的板式换热器及循环泵附属设备,从而提高了储能材料利用空间。本技术仅需一次换热,储热时,即所述电加热装置与储能材料接触的直接换热,产生的蒸汽以气态形式储存于所述加热蒸发舱中的蒸发舱。放热时,蒸发舱中的蒸汽只需经过汽水分离后即可外供用户,提高换热效率。另一方面,本技术采用的储能材料为水,储能密度为水的相变潜热,同等储能温度下,本技术储能材料的单位质量储能密度为传统储能材料的8倍。
35.3)在分离舱内通过隔板分成三段,一段为进汽段,一段为供汽段,另一段为疏水段。蒸汽从上汽管入口端进入,通过格栅上开设的导汽孔和隔板上开设的导流间隙进入供汽段,通过供汽管向外送汽。下部导流间隙较小,满足下部两侧的疏水能自由流动,有效的通过降液管排出,由于导流间隙靠近底部且有水,当蒸汽从该处流过时,对蒸汽中的小水滴有聚合作用,有利于汽水分离,同时导流间隙设计较小,不会形成蒸汽短路,保证了蒸汽经过导汽孔沿格栅高速向下流动,然后向上急剧转向进入供汽段,利用离心力对小液滴形成分离,同时蒸汽与格栅的碰撞也有利于液滴附着于格栅上进行分离。
36.4)在加热蒸发舱内填充水作为储能材料,利用储能材料的物相变化,将加热蒸发舱分成加热舱和蒸发舱,液态水储存于所述加热蒸发舱中的加热舱中,气态蒸汽储存于所述加热蒸发舱中的蒸发舱中,提高换热效率。
附图说明
37.图1是本发明一种实施例的主视结构示意图;
38.图2是本发明一种实施例的俯视结构示意图;
39.图3是本发明一种实施例的一级汽水分离装置结构局部放大图;
40.图4是本发明一种实施例的二级汽水分离装置结构局部放大图;
41.图中,1、集装箱;2、加热蒸发舱;3、分离舱;4、电加热装置;5、控制系统;6、横向支
撑件;7、吊耳;8、第一圆柱形壳体;9、第一左封头;10、第一右封头;11、加热舱; 12、蒸发舱;13、给水管;14、第二圆柱形壳体;15、第二左封头。16、第二右封头;17、二级汽水分离装置;18、进汽段;19、排汽段;20疏水段;21、隔板;22、格栅;23、导汽孔;24、供汽管;25、一级汽水分离装置;26、第一控制阀;27、第二控制阀;28导流间隙; 29导汽间隙;30扁钢。
具体实施方式
42.下面结合实施例及附图对本发明作进一步说明。具体实施例仅用于进一步详细说明本发明,不限制本技术的保护范围。
43.本发明一种用于储能供汽的模块,该模块包括集装箱1、加热蒸发舱2、分离舱3、电加热装置4、控制系统5。所述加热蒸发舱2、分离舱3、电加热装置4、控制系统5全部内置于集装箱1内部,所述加热蒸发舱、分离舱、电加热装置及仪表耦合为一整体,通过控制系统监测控制运行参数,形成具备智能化移动供汽的储能模块。
44.在集装箱内,加热蒸发舱的尺寸略小于集装箱的内部空间,所述加热蒸发舱沿长度方向的外圆周侧面和集装箱内壁之间留有不小于750mm的检修空间,加热蒸发舱的顶部外空间高度距离满足分离舱安装维修使用的最低高度要求,所述控制系统内挂于集装箱沿长度方向的尾部内壁面上,考虑检修及操作的方便性,设置控制系统的自动控制器距地面高度不超过 1.5m。
45.所述集装箱底部设有两列沿长度方向延伸的纵向支撑件(图中为绘出),两列纵向支撑件设置在集装箱宽度方向的底部两侧,纵向支撑件用于支撑加热蒸发舱2,在同时沿加热蒸发舱长度方向设置有多个电加热装置4,每个电加热装置4由至少一个横向支撑件6支撑固定,横向支撑件的设置数量不低于电加热装置4的组数。
46.进一步地,纵向支撑件采用25#标准工字钢,工字钢底部和顶部通过焊接方式分别与集装箱底部内壁和所述加热蒸发舱2的底部固定连接。所述集装箱顶部对称设置四个用于吊装的吊耳7,横向上的两个吊耳之间的间距为集装箱宽度的3/4,纵向上两个吊耳之间的间距不小于集装箱长度的3/4。
47.进一步地,吊耳采用高强度低合金钢材料,材料标准抗拉屈服强度下限值不低于540mpa,通过焊接方式与集装箱顶部固定连接。
48.所述加热蒸发舱,包括第一圆柱形壳体8、第一左封头9、第一右封头10。所述第一圆柱形壳体一端与第一左封头通过焊接方式固定连接,属于不可拆卸连接;所述第一圆柱形壳体另一端与第一右封头通过螺栓、螺母和垫片固定连接,属于可拆卸连接;第一左封头将第一圆柱形壳体的一端密封,第一右封头将第一圆柱形壳体的另一端密封;第一左封头、第一右封头和第一圆柱壳体围成一封闭空腔。根据储能材料的状态人为将封闭空腔划为加热舱11 和蒸发舱12,加热舱中储能材料的状态为液态,蒸发舱中储能材料的状态为气态;加热舱为高压饱和水加热提供加热空间,蒸发舱为高压饱和水蒸发提供蒸发空间。所述加热舱11底部区域设有多组电加热装置4,多组电加热装置均匀排布,高度一致,所述电加热装置的电加热管沿所述加热舱径向方向伸入加热舱内部,电加热管末端未触及第一圆柱形壳体内壁面,留有一定安全距离。
49.进一步地,所述电加热装置的电加热管内空腔设有电加热丝,采用铬镍合金材料,优先选用ni80cr20。为增强换热效果,电加热管内空腔内部填充有导热绝缘材料,导热绝缘
材料选用耐高温氧化镁粉。耐高温氧化镁粉成份组成:93.5%的mgo、2%的cao、0.5%的fe2o3、 2%的a12o3、2%的sio2(%为重量百分数),按重量百分数取上述各组分,均匀混合,即得上述耐高温氧化镁粉,填充密度为1.1kg/m3。填充密度是指散粒材料或粉状材料,在受外力约束状态下单位体积的质量。填充体积(含材料间空隙)颗粒材料正好装满容器时,测量该容器的容积v,根据下式计算出填充密度ρ:
[0050][0051]
式中,ρ——颗粒材料的填充密度,kg/m3;
[0052]
m——颗粒材料的重量;
[0053]vp
——颗粒材料内部孔隙的体积,m3;
[0054]vv
——颗粒材料间空隙的体积,m3;
[0055]v0
——颗粒材料的体积,不包含颗粒材料内部空孔隙,m3。
[0056]
上述的v
p
、vv、v0为材料自有物性数据,通过查物性手册找到对应材料的孔隙率,当填充密度为1.1kg/m3时,测得本实施例的电加热装置导热系数为0.5w/(m2*k),绝缘电阻值不低于1000kω/kv,满足设计标准要求。
[0057]
更进一步,所述第一右封头处设有给水管13,给水管与所述加热舱12连通,模块储能需要的除氧水由此口输入。
[0058]
所述分离舱,布置于加热蒸发舱上部的集装箱内部空间,所述分离舱3包括第二圆柱形壳体14、第二左封头15、第二右封头16。所述第二圆柱形壳体一端与第二左封头通过焊接方式固定连接,属于不可拆卸连接;所述第二圆柱形壳体另一端与第二右封头通过螺栓、螺母和垫片固定连接,属于可拆卸连接;第二左封头将第二圆柱形壳体的一端密封,第二右封头将第二圆柱形壳体的另一端密封;第二左封头、第二右封头和第二圆柱壳体围成一封闭空腔。根据蒸汽流动区域不同,通过设置在分离舱筒体内部中分面的二级汽水分离装置17,将所述分离舱封闭空腔划为进汽段18、排汽段19和疏水段20。
[0059]
进一步地,所述二级汽水分离装置包括隔板21、格栅22和扁钢30,所述隔板整体为圆形板,圆形板的边缘与分离舱的内壁无缝焊接在一起,隔板沿第一圆柱形壳体的高度方向垂直布置,且布置于分离舱的中分面位置;所述隔板21的底部设有导流间隙28,导流间隙沿分离舱的宽度方向设置,导流间隙高度太低,会使得液态水不能进入疏水段,太高达不到较好的过滤效果,优选地,导流间隙高度不超过隔板垂直高度的10%,不小于隔板垂直高度的 5%;在导流间隙上表面的隔板位置焊接有水平向右的扁钢,扁钢另一端以焊接方式与第二右封头固定连接;隔板与第二圆柱形壳体形成的左半空腔为进汽段,隔板与第二圆柱形壳体形成的右半空腔为供汽段和疏水段,其中,扁钢、垂直隔板、第二右封头和第二圆柱形壳体四面围成的上部空腔形成供汽段,分离腔剩余空间为疏水段。
[0060]
位于导流间隙上部的隔板上开设有多组导汽间隙29,导汽间隙处均设有格栅22,格栅覆盖住导汽间隙,使得蒸汽先经过格栅再由导汽间隙进入供汽段;所述格栅上侧与隔板均通过焊接固定连接。
[0061]
更进一步,所述格栅在隔板上正投影的总面积大于所覆盖的导汽间隙的面积,可提高汽水分离效果,避免未经汽水分离的蒸汽流过导汽间隙,起到一定的遮挡作用,格栅与隔板之间的夹角(格栅表面倾斜向下的方向与隔板垂直表面两者的夹角)为30
°
,所述格栅
上均匀布置有直径为8mm的导汽孔23,格栅的数量不低于6片,每片格栅的宽度不超过隔板高度的1/8,每片格栅上的导汽孔数量不低于16个。
[0062]
更进一步,所述第二圆柱形壳体上部依次设置压力表管座、安全阀管座、温度计管座,用于安装相关仪表。
[0063]
更进一步,所述第二右封头设有供汽管24,模块产生的饱和蒸汽由此口输出。
[0064]
所述加热蒸发舱与所述分离舱通过上汽管和降液管互连互通,所述上汽管入口端部先沿着所述加热蒸发舱径向方向垂直伸入所述蒸发舱,在未触及所述加热舱前,水平向第一左封头所在方向延神,水平方向延伸长度不超过所述第一圆柱形壳体长度1/8;所述上汽管出口端部垂直伸入至所述分离舱进汽段,与分离舱第二圆柱形壳体底部圆弧面通过法兰连接,属于可拆卸式连接结构。所述降液管入口端部垂直伸入至所述分离舱疏水段,与分离舱第二圆柱形壳体底部圆弧面通过法兰连接,属于可拆卸式连接结构;所述降液管出口端部沿着所述加热蒸发舱径向方向经所述蒸发舱后垂直依次伸入蒸发舱和加热舱。所述上汽管入口端部设有用于除掉气相中携带微量雾滴的一级汽水分离装置25。
[0065]
所述一级汽水分离装置包括环形圆盘和若干数量的倾斜安装在环形圆盘上的过滤挡片,所述过滤挡片一方面与环形盘面的内径固定,另一方面与环形盘面的外径固定,且每个过滤挡片与环形圆盘的盘面之间的夹角相同,环形圆盘的内外径之间为镂空空间,环形圆盘的内圆区域封闭,所述过滤挡片上开设有若干数量的筛孔;所述上汽管为内外套管形式,外套管与环形圆盘的外径固定在一起,内套管与环形圆盘的内径固定在一起,且外套管与分离舱和蒸发舱相连通,内套管的两端均封闭,蒸发舱内的蒸汽经过滤挡片后由环形圆盘的内外径之间进入外套管和内套管之间的空间内,最后再进入分离舱的进汽段18。
[0066]
所述过滤挡片可以采用合金金属过滤片或非金属过滤片,如分子筛片,若干数量的分子筛片围绕环形圆盘360度圆周倾斜布置,每个分子筛片设置有微小的筛孔,筛孔直径φ为 5mm,筛孔数量为120个,其中,分子筛片为等腰直角三角形,分子筛片与环形圆盘的夹角为30
°
。
[0067]
进一步地,所述上汽管入口端与上汽管出口端之间的管路上设有第一控制阀26,所述降液管入口端与降液管出口端之间的管路上设有第二控制阀27。
[0068]
优选地,所述分离舱位于所述加热蒸发舱的斜上方,分离舱的进汽段和蒸发舱之间连接有上汽管,分离舱的疏水段和加热舱之间连接有降液管;所述上汽管垂直向下进入加热蒸发舱的第一圆柱形壳体部分,降液管垂直向下插入加热蒸发舱的第二右封头部分,能最大程度减少降液过程的扰动,而不影响加热蒸发舱的强度。
[0069]
所述控制系统包括自动控制器、信号线、第一参数监测模块、第二参数监测模块,所述第一参数监测模块设置在所述分离舱上,所述第二参数监测模块设置所述加热蒸发舱上,所述第一参数监测模块和第二参数监测模块至少包括温度传感器和压力传感器,所述自动控制器与所述第一参数监测模块、第二参数监测模块和电加热装置通过电气信号线连接。所述控制系统根据参数监测控制流体的温度、压力参数、加热蒸发舱内的温度及压力和电加热器功率,确保储能供汽模块安全、稳定、高效运行。
[0070]
用于储能供汽的模块的工作原理为:夜间低谷电时段,除氧水经所述给水管13进入所述加热舱12,充水高度达到设定液位值时,启动所述电加热装置4开始加热,由于蒸发舱和加热舱两者是相通的,加热舱12内的水被加热蒸发,产生的湿蒸汽进入蒸发舱储存,当
湿蒸汽温度、压力经控制系统监测达到储热设定值时,停止所述电加热装置的加热工作,储热过程完毕。
[0071]
待非低谷电时段,开启第一控制阀26和第二控制阀27,所述蒸发舱11内的湿蒸汽经所述一级汽水分离装置25分离后通过上汽管进入进汽段,携带一部分水雾的蒸汽进入所述分离舱的进汽段继续分离,分离后的细水雾形成水滴经疏水段由降液管进入所述加热舱,分离后的饱和蒸汽经供汽段由供汽管24对外输出,当湿蒸汽温度、压力经所述控制系统监测达到放热设定值时,关闭第一控制阀和第二控制阀,放热过程完毕。储热过程完成的指标是:温度压力达到用户使用蒸汽的参数要求,比如用户需要的蒸汽温度压力为:165℃、0.7mpa(g);放热过程完毕的指标是;温度、压力指标降低至不能满足用户使用蒸汽的参数要求。
[0072]
本技术采用的储能材料为水,储能密度为水的相变潜热,以储能120℃的蒸汽为例,120 度水的饱合蒸汽压约是0.2mpa,水的焓值是:502kj/kg,汽的焓值是2709kj/kg,相变潜热为 2207kj/kg。传统储能材料采用硝酸镁,以储能温度为120℃为例,储能显热为272kj/kg。相比较来说,本技术储能材料的单位质量储能密度为传统储能材料的8倍,储能密度的大幅提升增强了产品经济性,可促使产品规模化应用。
[0073]
本发明未述及之处适用于现有技术。