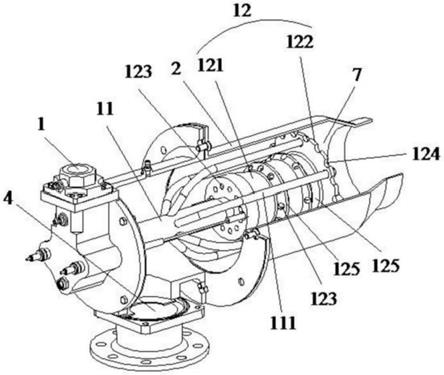
一种低氮燃烧器
1.本技术是母案名称为“一种低氮燃烧器”的发明专利的分案申请; 母案申请的申请号为:cn201810377648.9;母案申请的申请日为: 2018.04.25。
技术领域
2.本发明涉及工业锅炉和工业炉窑燃气燃烧器技术领域,具体涉及一种低氮 燃烧器。
背景技术:3.空气中的氮氧化物如no,no2,n2o3,n2o5等等统称为no
x
,一般都来 自燃料的燃烧。而工业燃烧装置所产生的no
x
,主要由二部分构成:助燃空气 中的n2氧化反应生成的高温no
x
和从燃料中的氮氧化物生成的燃料no
x
;
[0004][0005]
燃料no
x
的生成:在工业燃料中(油,煤,天然气等)中的hcn,nh3等 氮化物中所含的n称为燃料氮,燃料氮在燃烧时生成的no
x
称之为燃料no
x
, 燃料no
x
的生成与燃料的品质有关。
[0006]
高温no
x
是在燃烧过程中由助燃空气中的n2在高温下氧化反应的生成 物,它与炉膛温度和火焰温度有关。由于炉膛温度由热加工工艺决定不可改变, 所以燃烧器结构设计和燃烧技术是减少高温no
x
的关键因素。
[0007]
现有的常用的燃烧器如图1所示,包括壳体2,壳体2的一端设置有燃气 进口1和空气进口4,另一端设置有燃烧室9,所述壳体内安装有燃气管11, 燃气管11一端与燃气进口连通,另一端与燃烧室连通。使用时,通过燃气进 口通入燃气,通过空气进口通入空气,燃气经燃气管在燃气管的出口处与进入 的空气混合,经燃烧室排出,在此过程中使用点火器等工具引燃混合气体即可 使用。
[0008]
这种结构的燃烧器氮氧化物排放量较大,不能满足人们的要求,因此,燃 烧器的结构和燃烧技术改进已迫在眉睫。
技术实现要素:[0009]
本发明的目的在于提供一种低氮燃烧器,以解决上述现有技术存在的问 题,能够减少氮氧化物的排放。
[0010]
为实现上述目的,本发明提供了如下方案:
[0011]
本发明提供一种低氮燃烧器,包括:壳体、一级燃气管、二级燃气管和空 气分级导流器,所述壳体的一端设置有燃气进口和空气进口,另一端设有燃烧 室;所述一级燃气管和所述二级燃气管均安装于所述壳体内,所述一级燃气管 的一端与所述燃气进口连通,所述二级燃气管的一端与所述一级燃气管靠近所 述燃气进口的一端连通,所述二级燃气管的另一端朝向所述燃烧室;所述空气 分级导流器安装于所述壳体内,所述空气分级导流器的外壁与所述壳体内壁之 间形成为空气通道,所述空气分级导流器的一端口与所述一级
燃气管远离所述 燃气进口的一端连通,所述空气分级导流器的另一端口朝向所述燃烧室设置。
[0012]
优选地,所述空气分级导流器包括中空的筒体和旋流片,所述筒体与所述 旋流片连接,所述一级燃气管与所述筒体连接并与所述筒体内部连通,所述旋 流片的出口的一端与所述筒体内部连通,另一端与所述燃烧室连通;所述筒体 上设置有与所述筒体内部连通的第一通孔,所述旋流片的外边缘周向设置有与 所述燃烧室连通的第二通孔;所述空气进口通过所述第一通孔与所述筒体内部 连通,并且通过所述第二通孔与所述燃烧室连通。
[0013]
优选地,所述筒体在圆周方向设置有凸起,所述第一通孔为多个,其中, 一部分所述第一通孔位于所述凸起正对所述燃气进口的一侧,并且与所述筒体 的轴线有夹角,另一部分所述第一通孔位于所述筒体与所述一级燃气管连接的 连接面上,所述筒体与所述一级燃气管同轴线设置。
[0014]
优选地,所述一级燃气管延伸至所述筒体内,且所述一级燃气管延伸至所 述筒体内的侧壁上设置有燃气孔。
[0015]
优选地,所述空气分级导流器包括一级导流管、二级导流管、三级导流管 和旋流片,所述一级导流管、二级导流管、三级导流管和旋流片依次连接为一 体,并且内部连通,所述一级导流管远离所述二级导流管的一端设置有燃气通 孔及一级空气通孔,并连接所述一级燃气管,所述一级空气通孔的轴线与所述 空气分级导流器的轴线有夹角,所述燃气通孔与所述一级燃气管连通,所述旋 流片的出口的一端与所述三级导流管内部连通,另一端与所述燃烧室连通;所 述一级导流管设置有向内侧倾斜的第一斜面,所述二级导流管外表面设置有向 外侧倾斜的第二斜面,所述第一斜面和所述第二斜面连接,所述第二斜面的顶 部设置有二级空气通孔,所述二级空气通孔的轴线与所述导流器的轴线有夹 角,所述二级导流管的内侧设置有向内侧倾斜的第三斜面,所述三级导流管的 外表面设置有第四斜面,所述二级导流管与所述第四斜面连接,所述第四斜面 的底部设置有三级空气通孔,所述三级空气通孔的轴线与所述导流器的轴线有 夹角,所述三级导流管的内侧设置有向内侧倾斜的第五倾斜面,所述旋流片的 出口与所述第五倾斜面连接;所述旋流片的外边缘设置有与所述燃烧室连通的 第二通孔。
[0016]
优选地,所述燃烧室由筒形壳体和空心的圆台形壳体围成,所述筒形壳体、 圆台形壳体一体设置,所述圆台形壳体面积大的底面与所述筒形壳体连接,所 述圆台形壳体面积小的底面与所述燃烧室连接。
[0017]
优选地,所述壳体上安装有点火器;所述点火器的点火端位于所述筒体内。
[0018]
优选地,所述点火器的点火端位于所述筒体靠近所述一级燃气管的一侧。
[0019]
优选地,所述二级燃气管远离所述一级燃气管的一端穿过所述旋流片与所 述燃烧室连通。
[0020]
优选地,所述筒体内部空间占所述壳体内部空间的1/5-2/5,所述第一通 孔均匀设置于所述筒体上,并占所述筒体表面积的1/8-1/5。
[0021]
本发明提供的低氮燃烧器,通过燃气进口通入燃气,通过空气进口通入空 气,燃气通过一级燃气管进入空气分级导流器内部,空气进入壳体内部后,一 部分进入空气分级导流器的内部与燃气混合,另一部分经过空气分级导流器的 外部到达空气分级导流器的出口位置,在此过程中引燃混合气体,此时,燃烧 分两个过程:过程1:空气分级导流器内部
的混合气体在缺氧、富燃料燃烧条 件下燃烧,降低了燃烧速度和温度,因此,不但延迟了燃烧过程,而且在还原 性气氛中降低了生成no
x
的反应率,抑制了no
x
在这一燃烧中的生成量;过 程2:过程1中燃烧产生的烟气到达空气分级导流器的出口位置后,与上述的 另一部分空气混合,从而在氧气充足的环境下再次充分燃烧,在燃烧室处形成 火焰。本技术中,将进入壳体的空气分为两部分分别与燃气混合,在过程1 中,通过缺氧燃烧降低了燃烧温度,从而降低了氮氧化物的生成;在整个过程 中,n2在高温区停留时间主要在过程2中,从而减少了n2在整个过程的高温 区停留时间,进一步降低了氮氧化物的生成,从而降低了氮氧化物的排放。
附图说明
[0022]
为了更清楚地说明本发明实施例或现有技术中的技术方案,下面将对实施 例中所需要使用的附图作简单地介绍,显而易见地,下面描述中的附图仅仅是 本发明的一些实施例,对于本领域普通技术人员来讲,在不付出创造性劳动的 前提下,还可以根据这些附图获得其他的附图。
[0023]
图1为现有的一种低氮燃烧器的结构示意图;
[0024]
图2为本发明提供的一种低氮燃烧器的结构示意图;
[0025]
图3为本发明提供的一种低氮燃烧器的内部结构示意图;
[0026]
图4为图3在a处的放大图;
[0027]
图5为一种点火器的安装位置示意图;
[0028]
图6为本发明提供的一种低氮燃烧器中空气分级导流器的机构示意图;
[0029]
图7为本发明的一种支撑结构的轴向安装结构示意图;
[0030]
图8为本发明的一种支撑结构的侧面安装结构示意图;
[0031]
图中标号:1-燃气进口;11-一级燃气管;111-二级燃气管;12-空气分级 导流器;121-筒体;122-旋流片;123-第一通孔;124-第二通孔;125-凸起; 126-旋流片的出口;127-燃气孔;13-第一支杆;14-第二支杆;15-第一连接杆; 16-第二连接杆;17-第三连接杆;18-第四连接杆;19-连接板;2-壳体;210
‑ꢀ
一级导流管;211-二级导流管;212-三级导流管;213-燃气通孔;214-一级空 气通孔;215-第一斜面;216-第二斜面;217-二级空气通孔;218-第三斜面; 219-第四斜面;230-三级空气通孔;231-第五倾斜面;4-空气进口;7-燃烧室; 71-筒形壳体;72-圆台形壳体;8-点火器。
具体实施方式
[0032]
下面详细描述本发明的实施例,所述实施例的示例在附图中示出,其中自 始至终相同或类似的标号表示相同或类似的元件或具有相同或类似功能的元 件。下面通过参考附图描述的实施例是示例性的,仅用于解释本发明,而不能 理解为对本发明的限制。
[0033]
为使本发明的上述目的、特征和优点能够更加明显易懂,下面结合附图和 具体实施方式对本发明作进一步详细的说明。
[0034]
实施例1
[0035]
本实施例提供了一种低氮燃烧器,参见图2-图4,包括壳体2,壳体2的 一端设置有燃气进口1和空气进口4,另一端设置有燃烧室7,壳体2内安装 有一级燃气管11,一级燃气
管11一端与燃气进口1连通,一级燃气管11另 一端连接有空气分级导流器12,空气分级导流器12内部和外部分别与燃烧室 7连通;空气进口4分别与空气分级导流器12的内部和外部连通。
[0036]
本实施例提供的低氮燃烧器,通过燃气进口1通入燃气,通过空气进口4 通入空气,燃气通过一级燃气管11进入空气分级导流器12内部,空气进入壳 体2内部后,一部分进入空气分级导流器12的内部与燃气混合,另一部分经 过空气分级导流器12的外部到达空气分级导流器12的出口位置,在此过程中 引燃混合气体,此时,燃烧分两个过程:过程1:空气分级导流器12内部的 混合气体在缺氧的富燃料燃烧条件下燃烧,降低了燃烧速度和温度,因此,不 但延迟了燃烧过程,而且在还原性气氛中降低了生成no
x
的反应率,抑制了 no
x
在这一燃烧中的生成量;过程2:过程1中燃烧产生的烟气到达空气分级 导流12的出口位置后,与上述的另一部分空气混合,从而在氧气充足的环境 下再次充分燃烧,在燃烧室7处形成火焰。本技术中,将进入壳体2的空气分 为两部分分别与燃气混合,在过程1中,通过缺氧燃烧降低了燃烧温度,从而 降低了氮氧化物的生成;在整个过程中,n2在高温区停留时间主要在过程2 中,从而减少了n2在整个过程的高温区停留时间,进一步降低了氮氧化物的 生成,此外,在过程1中,根据热胀冷缩原理,空气分级导流器12内部的混 合气体在缺氧的富燃料燃烧条件下燃烧产生的热量相对较小,气体膨胀较小, 因此空气中的n2压力较小,从而进一步降低了氮氧化物的生成。
[0037]
在一级燃气管11上固定有二级燃气管111,二级燃气管111一端与一级燃 气管11连通,另一端与燃烧室7连通。这种结构,一是可以将燃气分级与空 气分级混合燃烧,进一步减小no
x
的生成,更重要的是,在过程2中,二级 燃气管111出来的燃气与过程1中出来的烟气能够再次反应,即,过程1中燃 烧中已生成的no遇到烃根chi和未完全燃烧产物co、h2、c和c
nhm
时, 会发生no的还原反应,反应式为:
[0038]
4no+ch4=2n2+co2+2h2o
[0039]
2no+2c
nhm
+(2n+m/2-1)o2=n2+2nco2+mh2o
[0040]
2no+2co=n2+2co2[0041]
2no+2c=n2+2co
[0042]
2no+2h2=n2+2h2o
[0043]
根据这一原理,可以进一步减少no
x
的排放量。
[0044]
以下为本技术的核心原理:燃烧温度越高,燃烧区域内氧的浓度越高,在 高温区域内燃烧气化滞留时间越长,产生的no
x
越多。低no
x
排放燃烧技术 及燃烧器通过分级燃烧技术实现了燃烧区的贫氧燃烧和降低燃烧温度,并减少 滞留时间,进而抑制no
x
的产生;同时,借助于外部控制技术和烟气循环技 术,进一步达到降低no
x
排放的目标。
[0045]
1、空气分级燃烧技术
[0046]
在第一阶段,将从主燃烧器供入炉膛一(即中空的筒体内)的空气量减少, 一般减少到总燃烧空气量的70-75%(相当于理论空气量的80%),使燃料先 在缺氧的富燃料燃烧条件下燃烧。此时第一级燃烧区内过量空气系数α<1, 因而降低了燃烧区内的燃烧速度和温度。因此,不但延迟了燃烧过程,而且在 还原性气氛中降低了生成no
x
的反应率,抑制了no
x
在这一燃烧中的生成量。
[0047]
为了完成全部燃烧过程,完全燃烧所需的其余空气则通过布置在主燃烧器 外部
的空气导流板送入炉膛二(即燃烧室内),与第一级燃烧区在“贫氧燃烧
”ꢀ
条件下所产生的烟气混合,在α>1的条件下完成全部燃烧过程。另外,这一 方法弥补了简单的低过量空气燃烧的缺点。在第一级燃烧区内的过量空气系数 越小,抑制no
x
的生成效果越好。
[0048]
2、燃料分级燃烧技术
[0049]
在燃烧中已生成的no遇到烃根chi和未完全燃烧产物co、h2、c和c
nhm
时,会发生no的还原反应,反应式为:
[0050]
4no+ch4=2n2+co2+2h2o
[0051]
2no+2c
nhm
+(2n+m/2-1)o2=n2+2nco2+mh2o
[0052]
2no+2co=n2+2co2[0053]
2no+2c=n2+2co
[0054]
2no+2h2=n2+2h2o
[0055]
利用这一原理,将燃料(一般选择80-85%)送入第一级燃烧区(中空的筒体 内),在α》1条件下,燃烧并生成no
x
。送入一级燃烧区的燃料称为一次燃料, 其余的燃料(15-20%)则在主燃烧器的上部送入二级燃烧区,在α《1的条件下 形成很强的还原性气氛,使得在一级燃烧区中生成的no
x
在二级燃烧区内被 还原成氮分子,二级燃烧区又称再燃区,送入二级燃烧区的燃料又称为二次燃 料,或称再燃燃料。在再燃区中不仅使得已生成的no
x
得到还原,还抑制了 新的no
x
的生成,可使no
x
的排放浓度进一步降低。一般来说,采用燃料分 级可使no
x
的排放浓度降低50%以上。在再燃区的上面还需布置“火上风
”ꢀ
喷口,形成第三级燃烧区(燃尽区),以保证再燃区中生成的未完全燃烧产物的 燃尽。这种再燃烧法又称为燃料分级燃烧。
[0056]
3、低过量空气燃烧
[0057]
低过量空气燃烧是燃烧过程尽可能在接近理论空气量的条件下进行,随着 烟气中过量氧的减少,可以抑制no
x
的生成。这是一种最简单的降低no
x
排 放的方法。一般可降低no
x
排放15-20%。
[0058]
4、烟气再次燃烧技术
[0059]
经验表明,烟气再次燃烧率为15-20%时,no
x
排放浓度可降低25%左右。 no
x
的降低率随着烟气再次燃烧率的增加而增加。而且与燃料种类和燃烧温度 有关。燃烧温度越高,烟气再次燃烧率对no
x
降低率的影响越大。
[0060]
5、低no
x
燃烧器
[0061]
燃气燃烧器是工业炉窑和工业锅炉燃烧系统中的关键设备。不但燃气是通 过燃烧器送入炉膛,而且燃气燃烧所需的空气也是通过燃烧器进入炉膛的。从 燃烧的角度看,燃烧器的性能对燃气燃烧系统的可靠性和经济性起着主要作 用。从no
x
的生成机理看,占no
x
绝大部分的高温no
x
是在燃气着火阶段生 成的,因此,通过特殊设计的燃烧器结构以及通过改变燃烧器的空燃比例,可 以将前述的空气分级、燃料分级和烟气再次燃烧降低no
x
浓度的大批量用于 燃烧器,以尽可能地降低着火区氧的浓度,并适当降低着火区的温度达到最大 限度地抑制no
x
生成的目的,这就是低no
x
燃烧器。
[0062]
空气分级导流器12可以使用现有的空气分级导流器,本技术中,申请人 对空气分级导流器12还做了进一步设计,参见图2-图4,空气分级导流器12 包括中空的筒体121和旋流片122,中空的筒体121与旋流片122连接,一级 燃气管11与中空的筒体121连接并与中空
侧设置有向内侧倾斜的第三斜面218,三级导流管212的外表面设置有第四斜 面219,第四斜面219的垂线与空气分级导流器12的轴线有夹角β,β一般 大于α,二级导流管211与第四斜面219连接,第四斜面219的底部设置有三 级空气通孔230,三级空气通孔230的轴线与空气分级导流器12的轴线有夹 角,该夹角最好大于α,三级导流管212的内侧设置有向内侧倾斜的第五倾斜 面231,旋流片的出口126与第五倾斜面231连接;旋流片122的外边缘设置 有与燃烧室7连通的第二通孔124。这种结构,在空气分级导流器12内形成 三级混合,在过程1中,一部分空气经一级空气通孔214进入一级导流管210 内与进入的燃气混合燃烧,产生烟气并继续前行,烟气进入二级导流管211后, 二级空气通孔217进入一部分空气与其进一步混合燃烧,产生二次烟气,二次 烟气继续前行进入三级导流管212后,三级空气通孔230进入一部分空气与其 进一步混合燃烧,燃烧后气体经旋流片的出口126进入燃烧室7与第二通孔 124过来的空气混合燃烧后经燃烧室排出,这种方式,可以使空气分级导流器 12内部燃烧分为三级,前一级比后一级过量空气系数α更小,更有利于降低 生成no
x
的反应率,抑制no
x
在这一燃烧中的生成量。此外,二级空气通孔 217和三级空气通孔230位置的设置为上部和下部交替的方式,结合一级空气 通孔214倾斜进入,与燃气混合,从而在不同角度和方向冲击燃气或烟雾,使 混合效率更快。第一斜面215和第三斜面218对气流有导向聚拢作用,使经过 连接处后进入下一级时气体扩散时与进入的空气混合,更有利于气体的混合。
[0065]
为了方便点火,参见图5,壳体2上还可以安装有点火器8;点火器8的 点火端位于中空的筒体121内,作为一种优选的方式,点火器8的点火端位于 筒体121的靠近一级燃气管11的一侧,这样更有利于燃气分级燃烧。此处所 述的点火端,即为点火器的点火位置,比如气体点火器的出口位置。点火器的 安装是本领域技术人员熟知的,此处不再赘述。
[0066]
为了方便过程2中的烟气燃烧充分,燃烧室7与旋流片122之间设置有燃 烧室,即燃烧室7与旋流片122之间预留燃烧空间以便于烟气与空气均匀混合 后充分燃烧。具体的,燃烧室由筒形壳体71和空心的圆台形壳体72围成,筒 形壳体71、空心的圆台形壳体72和燃烧室为一体的,筒形壳体71的内径大 于燃烧室的内径;空心的圆台形壳体72面积较大的底面与筒形壳体71连接, 空心的圆台形壳体72面积较小的底面与燃烧室连接,这种结构,空气经过第 二通孔124后,一边向内侧扩散,一边前行,经过圆台形壳体72的内侧面时, 经圆台体内侧面形状限制,沿圆台体内侧面向前向内侧扩散,旋流片122出口 出来的烟气一边前行,一边向外侧扩散,尤其到圆台形壳体面积较小的底面处, 内外交织,混合的更均匀。
[0067]
实施例2
[0068]
本实施例中,旋流片122上未设置有第二通孔124,安装时,旋流片122 的外边缘与壳体2之间有间距,以便于空气流过,即:壳体2为中空的,空气 分级导流器12包括中空的筒体121和旋流片122,中空的筒体121与旋流片 122连接,一级燃气管11与中空的筒体121连接并与中空的筒体121内部连 通,旋流片的出口的一端与中空的筒体121内部连通,另一端与燃烧室7连通; 中空的筒体121上设置有与中空的筒体内部连通的第一通孔123,旋流片122 的外边缘与壳体2之间有间距;空气进口4通过第一通孔123与筒体121内部 连通;并且通过旋流片122与壳体2之间的间距与燃烧室7连通。该结构空气 直接能通过旋流片122的外边缘,流过的气体更均匀,更有利于与过程1中的 烟气混合,这种结构,为了抵御气流以及缺氧燃烧对空气分级导流器产生的冲 击,中空的筒体121上安装有支撑结构,参见图7和
图8,支撑结构一般设置 为多个,图6中示意性示出了4个,支撑结构包括多个支撑体,图7中示意性 示出了2个,多个支撑体轴向平行设置,支撑体包括周向固定于中空的筒体与 筒形壳体之间的第一支杆13和第二支杆14,第一支杆13和第二支杆14之间 设置有第一连接杆15、第二连接杆16、第三连接杆17和第四连接杆18,第 一连接杆15和第三连接杆17固定于第一支杆13上,第二连接杆16和第四连 接杆18固定于第二支杆14上;第一连接杆15、第二连接杆16、第三连接杆 17和第四连接杆18之间固定连接有连接板19,第一连接杆15的延长线与第 三连接杆17的延长线相交,第二连接杆16的延长线和第四连接杆18的延长 线相交;相邻的支撑体之间的第一支杆13之间设置有第一连接杆15、第二连 接杆16、第三连接杆17和第四连接杆18,第一连接杆15和第三连接杆17 固定于其中一个第一支杆13上,第二连接杆16和第四连接杆18固定于另一 个第一支杆13上;第一连接杆15、第二连接杆16、第三连接杆17和第四连 接杆18之间固定连接有连接板19,第一连接杆15的延长线与第三连接杆17 的延长线相交,第二连接杆16的延长线和第四连接杆18的延长线相交;相邻 的支撑体之间的第二支杆14之间设置有第一连接杆15、第二连接杆16、第三 连接杆17和第四连接杆18,第一连接杆15和第三连接杆17固定于其中一个 第二支杆14上,第二连接杆16和第四连接杆18固定于另一个第二支杆14 上;第一连接杆15、第二连接杆16、第三连接杆17和第四连接杆18之间固 定连接有连接板19,第一连接杆15的延长线与第三连接杆17的延长线相交, 第二连接杆16的延长线和第四连接杆18的延长线相交。需要说明的是,为了 配合壳体形状,第一连接杆15、第二连接杆16、第三连接杆17和第四连接杆 18可以设置成弧形或直的。这种结构,支撑体的第一连杆13和第二连杆14, 配合中空的筒体与筒形壳体的形状,在第一连杆13和第二连杆14的两端形成 两个拱形支撑,抵御气流以及缺氧燃烧在垂直于轴向对空气分级导流器12产 生的冲击,第一连接杆15、第二连接杆16、第三连接杆17和第四连接杆18 配合连接板在周向相互制约,在气流以及缺氧燃烧在周向产生力时,能够产生 拉力或推力,从而抵御气流以及缺氧燃烧在周向产生的冲击。同理,相邻的支 撑体之间的第一支杆13之间设置有第一连接杆15、第二连接杆16、第三连接 杆17和第四连接杆18配合连接板能够抵御气流以及缺氧燃烧在轴向上产生的 冲击。当然,支撑结构之间也可以设置第一连接杆15、第二连接杆16、第三 连接杆17和第四连接杆18配合连接板19的结构,从而形成抵御气流以及缺 氧燃烧产生的冲击的相互配合结构,效果更好。
[0069]
在旋流片122上设置第二通孔124,安装时,旋流片122的外边缘与壳体 2之间有间距。
[0070]
本发明中应用了具体个例对本发明的原理及实施方式进行了阐述,以上实 施例的说明只是用于帮助理解本发明的方法及其核心思想;同时,对于本领域 的一般技术人员,依据本发明的思想,在具体实施方式及应用范围上均会有改 变之处。综上所述,本说明书内容不应理解为对本发明的限制。