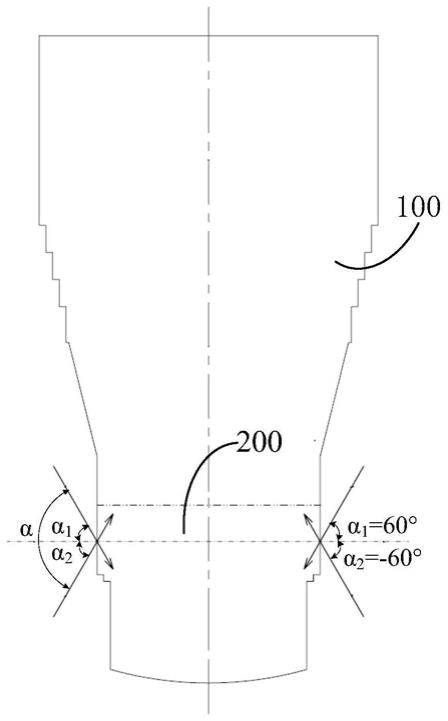
[0001]
本发明属于冶金领域,具体而言,涉及利用侧吹熔炼炉进行熔炼的方法。
背景技术:[0002]
目前,国内使用侧吹熔炼炉工艺的冶炼厂均采用炉顶加原料的方式,其主要步骤为:电子废料或精矿粉根据生产需要配料,后经炉顶加料口加入侧吹熔炼炉进行冶炼反应。但是炉顶加原料方式存在以下不足:一、部分原料块度较大,在熔体中流动性较差,与熔体接触面积较小,难以快速、完全地反应;二、当加入的原料为含塑料的电子废料时,大部分塑料会在下落的过程中燃烧,无法进入熔池内,产生的热量被烟气带走,不能为熔池补充热量,无法减少煤的配入量,增加了生产成本。因此,熔炼方法仍有待进一步改进。
技术实现要素:[0003]
本发明旨在至少在一定程度上解决相关技术中的技术问题之一。为此,本发明的一个目的在于提出一种利用侧吹熔炼炉进行熔炼的方法。该方法可以增加原料与熔体的接触面积,加快化学反应速率,避免电子废料在烟气区燃烧和/或小粒径原料被烟气带出而导致原料生产成本增高和熔炼效率偏低的问题。
[0004]
根据本发明的第一个方面,本发明提出一种利用侧吹熔炼炉进行熔炼的方法。根据本发明的实施例,该方法中,所述熔炼炉包括自上而下的烟气区和熔体区,采用喷枪将原料从所述熔体区侧壁喷吹至熔体内进行熔炼,所述原料包括电子废料和/或精矿粉。
[0005]
相比于传统侧吹熔炼炉炉顶加原料的熔炼方法,本发明上述实施例的利用侧吹熔炼炉进行熔炼的方法至少具有以下优势:一方面可以增加原料与熔体的接触面积,同时还能使熔体产生适宜的搅动,从而加快原料的扩散和化学反应速率;另一方面,当原料包括含塑料的电子废料时,若采用传统的炉顶加料方式,塑料会在下落过程中在烟气区燃烧,热量被烟气带走,不能给熔体补充热量;并且,若精矿粉和/或电子废料的粒度过小,也容易随烟气排出导致原料损失,而采用侧吹的方式将原料直接送入熔体不仅可以有效避免原料损失,而且绝大部分塑料可直接在熔体中燃烧并为熔体补充热量,从而显著减少煤等燃料的配入量,能够极大地节约生产成本,提高熔炼速率和经济效益。
[0006]
另外,根据本发明上述实施例的利用侧吹熔炼炉进行熔炼的方法还可以具有如下附加的技术特征:
[0007]
在本发明的一些实施例中,采用多个所述喷枪将原料从所述熔体区侧壁喷吹至熔体内。
[0008]
在本发明的一些实施例中,所述多个喷枪斜向上和/或斜向下和/或水平间隔分布在所述熔体区外壁的周向上。
[0009]
在本发明的一些实施例中,所述熔体区外壁的周向上,所述斜向下喷射的喷枪和所述水平喷射的喷枪交替分布。
[0010]
在本发明的一些实施例中,在水平投影方向上,所述喷枪与所述熔炼炉的交点到
所述熔炼炉中心线的连线与所述原料喷吹方向的夹角为0~45度,优选0~15度。
[0011]
在本发明的一些实施例中,所述原料喷吹方向与水平方向的角度为-60~60度,优选-30~30度,更优选为-15~15度。
[0012]
在本发明的一些实施例中,所述原料的粒度不大于20mm。
[0013]
在本发明的一些实施例中,所述喷枪中以压缩气体为载体将所述原料喷吹至所述熔体内,所述压缩气体与所述原料的气固比为(5~30):1。
[0014]
在本发明的一些实施例中,所述压缩气体的压力范围为0.1~0.3mpa。
[0015]
在本发明的一些实施例中,所述压缩气体为选自压缩空气、惰性气体、富氧空气和还原气体中的至少一种。
[0016]
本发明的附加方面和优点将在下面的描述中部分给出,部分将从下面的描述中变得明显,或通过本发明的实践了解到。
附图说明
[0017]
本发明的上述和/或附加的方面和优点从结合下面附图对实施例的描述中将变得明显和容易理解,其中:
[0018]
图1是根据本发明一个实施例的利用侧吹熔炼炉进行熔炼的方法示意图。
[0019]
图2是根据本发明一个实施例的喷枪与熔炼炉的交点到熔炼炉中心线的连线与原料喷吹方向在水平投影的夹角示意图。
具体实施方式
[0020]
下面详细描述本发明的实施例,所述实施例的示例在附图中示出,其中自始至终相同或类似的标号表示相同或类似的元件或具有相同或类似功能的元件。下面通过参考附图描述的实施例是示例性的,旨在用于解释本发明,而不能理解为对本发明的限制。
[0021]
根据本发明的第一个方面,本发明提出一种利用侧吹熔炼炉进行熔炼的方法。根据本发明的实施例,如图1所示,该方法中,熔炼炉包括自上而下的烟气区100和熔体区200,采用喷枪将原料从熔体区侧壁喷吹至熔体内进行熔炼,原料包括电子废料和/或精矿粉。相比于传统侧吹熔炼炉炉顶加原料的熔炼方法,本发明上述实施例的利用侧吹熔炼炉进行熔炼的方法至少具有以下优势:一方面可以增加原料与熔体的接触面积,同时还能使熔体产生适宜的搅动,从而加快原料的扩散和化学反应速率;另一方面,当原料包括含塑料的电子废料时,若采用传统的炉顶加料方式,塑料会在下落过程中在烟气区燃烧,热量被烟气带走,不能给熔体补充热量;并且,若精矿粉和/或电子废料的粒度过小,也容易随烟气排出导致原料损失,而采用侧吹的方式将原料直接送入熔体不仅可以有效避免原料损失,而且绝大部分塑料可直接在熔体中燃烧并为熔体补充热量,从而显著减少煤等燃料的配入量,能够极大地节约生产成本,提高熔炼速率和经济效益。
[0022]
下面参考图1-2对本发明上述实施例的利用侧吹熔炼炉进行熔炼的方法进行详细描述。
[0023]
根据本发明的一个具体实施例,可以采用多个喷枪将原料从熔体区侧壁喷吹至熔体内,由此不仅可以提高喷吹效率,还有利于原料在熔体中分散,从而加快化学反应速率。优选地,多个喷枪可以在熔体区外壁的周向上均匀分布,由此可以进一步提高原料与熔体
混合的均匀度。其中,喷枪的喷吹口可以位于侧吹熔炼炉熔体液面层以下熔体区范围内的任意炉体侧壁上,从而使原料经喷吹口送入熔体中得以完全反应。
[0024]
根据本发明的再一个具体实施例,多个喷枪可以斜向上和/或斜向下和/或水平间隔分布在熔体区外壁的周向上,由此可以使喷枪的喷吹方向可以为选自斜向上、斜向下或水平方向中的至少一种。优选地,多个喷枪可以斜向下和/或水平分布在熔体区外壁的周向上,使喷枪的喷吹方向为斜向下和/或水平方向,由此可以进一步确保原料可以被完全喷吹至熔体中。进一步地,在熔体区外壁的周向上,斜向下喷射的喷枪和水平喷射的喷枪可以交替分布,由此可以进一步提高喷吹气体对熔体搅动的均匀性和原料在熔体中的分散效果。
[0025]
根据本发明的又一个具体实施例,如图2所示,在水平投影方向上,喷枪与熔炼炉的交点到熔炼炉中心线的连线l与原料喷吹方向的夹角β可以为0~45度,例如可以为0度、5度、10度、15度、20度、25度、30度、35度、40度或45度等,发明人发现,若喷吹后原料距炉体的距离较小,则化学反应更倾向于在靠近炉体侧壁的边缘位置进行,反应放热容易导致炉体结构过热,进而导致炉体结构被破坏,本发明中通过控制喷枪与熔炼炉的交点到熔炼炉中心线的连线与原料喷吹方向在水平投影方向上的夹角0~45度,可以有效避免原料在熔炼炉边缘位置聚集,从而避免或显著改善化学反应放热对炉体结构造成的破坏。优选地,在水平投影方向上,喷枪与熔炼炉的交点到熔炼炉中心线的连线与原料喷吹方向的夹角可以为0~15度,发明人发现,当喷枪与熔炼炉的交点到熔炼炉中心线的连线与原料喷吹方向在水平投影方向上的夹角较小时,喷吹原料时对熔体产生的搅拌效果更好,由此可以更有利于原料在熔体中快速分散,由此,本发明中通过采用上述优选角度,不仅可以进一步提高原料在熔体中的分散效果,提高反应速率,还可以避免原料在熔炼炉边缘位置反应而对炉体结构产生负面影响。
[0026]
根据本发明的又一个具体实施例,如图1所示,原料喷吹方向与水平方向的角度α可以为-60~60度,例如可以为-45~60度、-30~40度、-30~30度、-15~30度、-15~15度、-60度、-50度、-40度、-30度、-20度、-10度、-5度、0度、5度、10度、20度、30度、40度、50度或60度等,需要说明的是,角度α指的是水平方向到喷吹方向的角度,以顺时针为正,逆时针为负;α1指的是原料喷吹方向为斜向下时原料喷吹方向与水平方向的夹角,为正;α2指的是原料喷吹方向为斜向上时原料喷吹方向与水平方向的夹角,为负。发明人发现,若原料喷吹方向与水平方向的夹角过大,则喷吹后原料距炉体的距离较小,容易在靠近炉体侧壁的边缘位置进行反应而导致炉体结构过热,进而影响炉体结构的稳定性,本发明中通过控制原料喷吹方向与水平方向的角度-60~60度,可以避免或显著改善原料在熔炼炉边缘发生化学反应而对炉体结构造成的破坏。优选地,水平方向到原料喷吹方向的角度α可以为-30~30度,更优选地,水平方向到原料喷吹方向的角度α可以为-15~15度,由此可以进一步避免原料在熔炼炉边缘发生化学反应而对炉体结构造成的破坏。
[0027]
根据本发明的又一个具体实施例,本发明中原料的粒度并不受特别限制,本领域技术人员可以根据实际需要进行选择,例如,原料的粒度可以不大于20mm,例如可以为不大于10mm、不大于5mm、不大于3mm或1~8mm等,由此不仅有利于将原料顺利喷吹至熔体内,还可以进一步增加原料与熔体的接触面积,提高化学反应速率。
[0028]
根据本发明的又一个具体实施例,喷枪中可以以压缩气体为载体将原料喷吹至熔体内,压缩气体与原料的气固比可以为(5~30):1,压缩气体的压力范围可以为0.1~
0.3mpa。发明人发现,若压缩气体与原料的气固比或压缩气体的压力范围过小,均不足以将原料充分喷吹至熔体内,且原料在熔体中的分散不好;而若压缩气体与原料的气固比或压缩气体的压力范围过大,又均会导致熔体过度扰动,甚至产生熔体喷溅现象,本发明中通过控制上述气固比和压缩气体的压力范围,不仅可以使原料在熔体中快速扩散,还可以避免出现熔体喷溅等现象,确保化学反应快速稳定进行。
[0029]
根据本发明的又一个具体实施例,本发明中压缩气体的种类并不受特别限制,本领域技术人员可以根据实际熔炼需要进行选择,例如压缩气体可以为选自压缩空气、惰性气体、富氧空气和还原气体中的至少一种。
[0030]
下面将结合实施例对本发明的方案进行解释。本领域技术人员将会理解,下面的实施例仅用于说明本发明,而不应视为限定本发明的范围。实施例中未注明具体技术或条件的,按照本领域内的文献所描述的技术或条件或者按照产品说明书进行。所用试剂或仪器未注明生产厂商者,均为可以通过市购获得的常规产品。
[0031]
一般方法:选用一台处理电子废料量为10t/h(干基)的侧吹熔炼炉,工作制度为297天/年,24h/天,电子废料中塑料含量为25%,电子废料经破碎系统处理后喷吹入炉反应。将电子废料送至破碎系统,破碎系统选用四轴剪切式破碎机。电子废料经破碎机处理后粒度≤2mm的部分进入喷吹系统的喷吹罐中储存,不满足喷吹粒度的部分返回破碎腔中继续破碎直至满足要求。
[0032]
实施例1
[0033]
炉体喷吹口位于侧吹熔炼炉熔体区范围内的任意炉墙位置,喷枪的喷吹方向相对于水平方向的角度为0度。喷吹系统采用压缩空气将粒度≤2mm的电子废料输送至喷吹口后直接送入熔体内进行快速、完全的冶炼反应。输送用压缩空气的压力为0.2mpa,压缩空气与电子废料的气固比为15:1。其中,电子废料中绝大部分塑料在熔体中燃烧,
[0034]
对比例1
[0035]
与实施例1区别在于:采用传统炉顶加料方式。其中,电子废料在下落过程中,80%的塑料在烟气区燃烧,产生的热量被烟气带走。
[0036]
计算对比例1中的热量损失:塑料的燃烧热值按q1=47372kj/kg算,对比例1中电子废料部分损失的热量q2=10
×
25%
×
80%
×
47372=94744mj/h。生产过程中,考虑损失的热量q2全部通过配入块煤燃烧进行补充,块煤的燃烧热值按q3=24519kj/kg算,得配入的块煤量m1=94744/24519=3.86t/h。而实施例1中,电子废料中绝大部分塑料在熔体中燃烧,上述热量q2不会被烟气带走,生产过程中可节约的配煤量m2=3.86
×
24
×
297=27500t/年,极大地降低了生产成本,提高了经济效益。
[0037]
在本说明书的描述中,参考术语“一个实施例”、“一些实施例”、“示例”、“具体示例”、或“一些示例”等的描述意指结合该实施例或示例描述的具体特征、结构、材料或者特点包含于本发明的至少一个实施例或示例中。在本说明书中,对上述术语的示意性表述不必针对的是相同的实施例或示例。而且,描述的具体特征、结构、材料或者特点可以在任一个或多个实施例或示例中以合适的方式结合。此外,在不相互矛盾的情况下,本领域的技术人员可以将本说明书中描述的不同实施例或示例以及不同实施例或示例的特征进行结合和组合。
[0038]
尽管上面已经示出和描述了本发明的实施例,可以理解的是,上述实施例是示例
性的,不能理解为对本发明的限制,本领域的普通技术人员在本发明的范围内可以对上述实施例进行变化、修改、替换和变型。