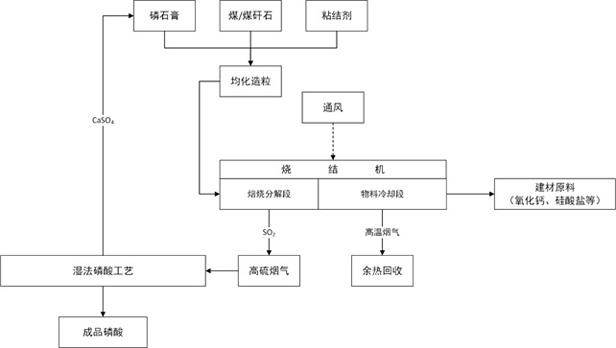
1.本发明属于磷化工综合利用技术领域,具体涉及一种利用烧结机分解处置磷石膏及资源化利用的方法。
背景技术:2.我国是一个以煤炭为主要能源的国家,我国的煤炭资源赋存具有总量大,但人均可采储量少的特点,且其中高硫煤占有比例大。由于高硫煤中硫分大于3%,燃烧会排放大量以so2为主要的污染物,对环境造成严重污染,因而被限制开采及销售。另外在煤炭开采和清选过程中会产生一种被称为煤矸石的固体废弃物,约占煤炭产量的15%,由于未找到大宗利用途径,目前大都露天堆放。煤矸石的大量堆放不仅占用大量土地,而且污染土壤及地下水。此外,煤矸石中由于存在硫铁矿和含碳物质发生自燃,产生有毒有害气体,严重污染环境。基于我国煤炭资源的赋存特点及煤矸石的处理处置状态,实现经济、社会、环境的可持续性发展,必须开发高硫煤、煤矸石的清洁利用有效途径。
3.磷石膏是湿法制取磷酸时产生的一般工业固体废弃物,预计到2021年我国磷石膏的产生量将达到8000万t/a,而其综合利用率不足30%,磷石膏的处理与处置问题尤为迫切。我国磷石膏的堆存不仅占用大量土地,而且还造成了严重的环境污染和硫资源浪费。磷石膏资源化利用,成为磷化工行业可持续发展的迫切需要。
4.目前磷石膏的资源化利用研究中,以磷石膏分解制so2和cao以回收ca、s资源是当前的主要关注点之一,但研究及生产实例中多以中空式回转窑、循环流化床锅炉作为高温分解炉来处理分解磷石膏,存在磷石膏分解率低、硫回收困难等问题,同时回转窑、流化床锅炉焙烧过程易结圈易烧损、设备磨损大、能耗高等难题,致使磷石膏分解制硫酸及联产水泥工艺在经济和环保指标下,无法满足工业化生产的需要,限制其大规模推广使用。
5.中国专利cn112250051a公开了一种磷矿浆吸收磷石膏焙烧烟气联产磷酸和水泥熟料的方法,该方法是将均化后的物料投入到中空长窑进行高温分解,其焙烧过程为全混焙烧,导致粉尘浓度高,除尘负荷大,同时由于物料及粉尘与设备在高温下磨蚀,存在设备损耗大、运行连续性差等问题。
6.中国专利cn101602518a公开了一种利用磷石膏分解制备氧化钙和二氧化硫的生产工艺,该工艺是将磷石膏与碳混合造粒的颗粒物料投入到流化床分解炉,然后通入煤气或天然气产生高温炉气直接与颗粒物料接触进行反应,存在煤气、天然气价格昂贵、技术经济性欠佳等问题。
7.为此,研发一种能解决上述问题的利用烧结机分解处置磷石膏及资源化利用的方法是非常必要的。
技术实现要素:8.本发明的目的在于提供一种利用烧结机分解处置磷石膏及资源化利用的方法。
9.本发明的目的是这样实现的,包括以下步骤:
s1、将磷石膏、煤或煤矸石以及粘结剂混合后,经造粒、干燥后得到粒料;s2、将粒料按不同粒径分层投入到烧结机内,形成粒径从下到上依次变小的颗粒层状布料结构;焙烧过程中通过引风将粒料纵向逐层热分解,产生的含硫烟气送至湿法磷酸工艺,湿法磷酸工艺固液分离产生的滤渣为磷石膏,磷石膏返回s1步骤,滤液为稀磷酸,焙烧残渣用于建筑原料。
10.与现有技术相比,本发明具有以下技术效果:1、本发明以造粒焙烧为核心,利用烧结机的颗粒层状布料结构与纵向焙烧,不但能够强化蓄热保温作用,降低通风供氧的压降损失,实现对磷石膏的高效分解的优点,而且可有效降低粉尘浓度,降低除尘设备的工作负荷、避免流化动力消耗与设备磨损;2、可利用高硫煤、低热值煤矸石等作为磷石膏热分解还原剂及能量来源,实现劣质煤、煤矸石中热值及硫的资源化利用,并实现以废治废;3、通过控制纵向风量及烧结停留时间,实现高硫烟气与高温烟气的分离,所获得的高浓度含硫烟气,有利于回用湿法磷酸生产过程;所获得的高温烟气可有效进行余热回收。
附图说明
11.图1为本发明方法流程示意图。
具体实施方式
12.下面结合附图对本发明作进一步的说明,但不以任何方式对本发明加以限制,基于本发明教导所作的任何变换或替换,均属于本发明的保护范围。
13.如附图1所示本发明包括以下步骤:s1、将磷石膏、煤或煤矸石以及粘结剂混合后,经造粒、干燥后得到粒料;s2、将粒料按不同粒径分层投入到烧结机内,形成粒径从下到上依次变小的颗粒层状布料结构;焙烧过程中通过引风将粒料纵向逐层热分解,产生的含硫烟气送至湿法磷酸工艺,湿法磷酸工艺固液分离产生的滤渣为磷石膏,磷石膏返回s1步骤,用于补充s1步骤磷石膏的消耗,滤液为稀磷酸,焙烧残渣用于建筑原料。
14.磷石膏、煤或煤矸石以及粘结剂的质量百分比为65%~90%、5%~30%、0.5%~5%。
15.所述煤为烟煤、无烟煤、褐煤中的一种或多种。
16.所述煤为高硫煤,高硫煤是指含硫量大于3%的煤。
17.所述粘结剂为膨润土、黏土、淤泥中的一种或多种。
18.所述粒料的粒径为1~20mm。
19.s2步骤烧结机料层温度控制在800~1250℃,停留时间为15~600s, 空燃比为9~11:1。
20.下面结合实施例1~实施例8对本发明作进一步说明。
21.实施例1s1、将磷石膏、烟煤以及膨润土按质量百分比65%、30%、5%混合后,经造粒、干燥后得到粒径在1~10mm粒料,将粒料分成2个不同粒径区间;s2、将粒料按不同粒径区间分层投入到烧结机内,形成下层为较小粒径区间粒料,
上层为较大粒径区间粒料的颗粒层状布料结构;焙烧过程中通过引风将粒料纵向逐层热分解,烧结机料层温度控制在800~1000℃,停留时间15~100s,空燃比9:1,产生的含硫烟气送至湿法磷酸工艺,湿法磷酸工艺固液分离产生的滤渣为磷石膏,磷石膏返回s1步骤,滤液为稀磷酸,焙烧残渣用于建筑原料;经检测,磷石膏分解率达到90%。
22.实施例2s1、将磷石膏、无烟煤以及膨润土按质量百分比76%、20%、4%混合后,经造粒、干燥后得到粒径在8~15mm粒料,将粒料分成3个不同粒径区间;s2、将粒料按不同粒径区间分层投入到烧结机内,形成最下层为最小粒径区间粒料,从下到上粒径区间依次变小的粒料的颗粒层状布料结构;焙烧过程中通过引风将粒料纵向逐层热分解,烧结机料层温度控制在900~1100℃,停留时间100~300s,空燃比10:1,产生的含硫烟气送至湿法磷酸工艺,湿法磷酸工艺固液分离产生的滤渣为磷石膏,磷石膏返回s1步骤,滤液为稀磷酸,焙烧残渣用于建筑原料;经检测,磷石膏分解率达到95%。
23.实施例3s1、将磷石膏、褐煤以及膨润土按质量百分比85%、13%、2%混合后,经造粒、干燥后得到粒径在8~15mm粒料,将粒料分成4个不同粒径区间;s2、将粒料按不同粒径区间分层投入到烧结机内,形成最下层为最小粒径区间粒料,从下到上粒径区间依次变小的粒料的颗粒层状布料结构;焙烧过程中通过引风将粒料纵向逐层热分解,烧结机料层温度控制在1100~1250℃,停留时间300~500s,空燃比11:1,产生的含硫烟气送至湿法磷酸工艺,湿法磷酸工艺固液分离产生的滤渣为磷石膏,磷石膏返回s1步骤,滤液为稀磷酸,焙烧残渣用于建筑原料;经检测,磷石膏分解率达到93%。
24.实施例4s1、将磷石膏、高硫煤以及膨润土按质量百分比90%、5%、5%混合后,经造粒、干燥后得到粒径在13~20mm粒料,将粒料分成2个不同粒径区间;s2、将粒料按不同粒径区间分层投入到烧结机内,形成下层为较小粒径区间粒料,上层为较大粒径区间粒料的颗粒层状布料结构;焙烧过程中通过引风将粒料纵向逐层热分解,烧结机料层温度控制在800~1000℃,停留时间500~600s,空燃比11:1,产生的含硫烟气送至湿法磷酸工艺,湿法磷酸工艺固液分离产生的滤渣为磷石膏,磷石膏返回s1步骤,滤液为稀磷酸,焙烧残渣用于建筑原料;经检测,磷石膏分解率达到85%。
25.实施例5s1、将磷石膏、高硫煤以及粘土按质量百分比90%、9.5%、0.5%混合后,经造粒、干燥后得到粒径在13~20mm粒料,将粒料分成2个不同粒径区间;s2、将粒料按不同粒径区间分层投入到烧结机内,形成下层为较小粒径区间粒料,上层为较大粒径区间粒料的颗粒层状布料结构;焙烧过程中通过引风将粒料纵向逐层热分解,烧结机料层温度控制在1100~1250℃,停留时间500~600s,空燃比11:1,产生的含硫烟气送至湿法磷酸工艺,湿法磷酸工艺固液分离产生的滤渣为磷石膏,磷石膏返回s1步骤,滤液为稀磷酸,焙烧残渣用于建筑原料;经检测,磷石膏分解率达到88%。
26.实施例6s1、将磷石膏、烟煤以及淤泥按质量百分比77.5%、20%、2.5%混合后,经造粒、干燥后得到粒径在1~5mm粒料,将粒料分成2个不同粒径区间;
s2、将粒料按不同粒径区间分层投入到烧结机内,形成下层为较小粒径区间粒料,上层为较大粒径区间粒料的颗粒层状布料结构;焙烧过程中通过引风将粒料纵向逐层热分解,烧结机料层温度控制在800~850℃,停留时间15~45s,空燃比9:1,产生的含硫烟气送至湿法磷酸工艺,湿法磷酸工艺固液分离产生的滤渣为磷石膏,磷石膏返回s1步骤,滤液为稀磷酸,焙烧残渣用于建筑原料;经检测,磷石膏分解率达到92%。
27.实施例7s1、将磷石膏、煤矸石以及膨润土按质量百分比78%、17.5%、4.5%混合后,经造粒、干燥后得到粒径在15~20mm粒料,将粒料分成2个不同粒径区间;s2、将粒料按不同粒径区间分层投入到烧结机内,形成下层为较小粒径区间粒料,上层为较大粒径区间粒料的颗粒层状布料结构;焙烧过程中通过引风将粒料纵向逐层热分解,烧结机料层温度控制在1200~1250℃,停留时间570~600s,空燃比11:1,产生的含硫烟气送至湿法磷酸工艺,湿法磷酸工艺固液分离产生的滤渣为磷石膏,磷石膏返回s1步骤,滤液为稀磷酸,焙烧残渣用于建筑原料;经检测,磷石膏分解率达到91%。
28.实施例8s1、将磷石膏、高硫煤以及黏土按质量百分比85%、12.2%、2.8%混合后,经造粒、干燥后得到粒径在8~13mm粒料,将粒料分成2个不同粒径区间;s2、将粒料按不同粒径区间分层投入到烧结机内,形成下层为较小粒径区间粒料,上层为较大粒径区间粒料的颗粒层状布料结构;焙烧过程中通过引风将粒料纵向逐层热分解,烧结机料层温度控制在975~1075℃,停留时间278~338s,空燃比10:1,产生的含硫烟气送至湿法磷酸工艺,湿法磷酸工艺固液分离产生的滤渣为磷石膏,磷石膏返回s1步骤,滤液为稀磷酸,焙烧残渣用于建筑原料;经检测,磷石膏分解率达到92%。