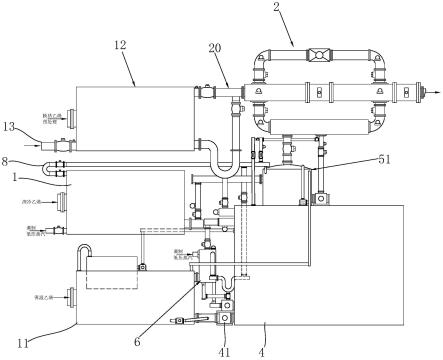
1.本技术涉及化工设备技术领域,尤其是涉及一种储运系统中的蒸汽冷凝水热量再利用系统。
背景技术:2.化工生产设计中储运系统的结构设计是否合理,是决定整体生产系统耗能的重要影响因素,也是所制备的产品市场竞争力强弱的体现之一。通常地,储运系统会与使用的加热设备相连接,而现阶段的化工企业加热设备一般是连通于工业园区内的中压蒸汽管道,中压蒸汽在这些加热设备中冷凝放热,释放的热能传递至反应釜中,对反应釜中的物料进行预热处理或者提升液料温度至理想反应温度,中压蒸汽换后会产生80-140℃的冷凝水和200℃左右的回气。
3.现有技术中,针对于产生的200℃左右的回气,通常是用于升温要求相对较低的加热设备的蒸汽源。针对于产生80-140℃的冷凝水,通常有两类利用方式,其中一种方式是:用于加热设备的夹套中循环加热源,换热后的水体经过疏水器输入园区生活用水管道,作为园区生活用水使用;另一种方式是:作为园区发电设备的水源使用。
4.针对上述相关技术,申请人发现以下缺陷:虽然相关技术中对冷凝水的热能进行回收再利用,但是受限于传输过程中热能散失损耗和加热设备的控温方式单一的影响,导致整体蒸汽冷凝水热量回收率偏低。
技术实现要素:5.为了解决现有技术存在整体蒸汽冷凝水热量回收率偏低的问题,本技术提供了一种储运系统中的蒸汽冷凝水热量再利用系统。
6.本技术提供的一种储运系统中的蒸汽冷凝水热量再利用系统,是通过以下技术方案得以实现的:一种储运系统中的蒸汽冷凝水热量再利用系统,包括用于加热深冷乙烯的换热器a、用于调整经过换热器a换热后的液体乙烯温度的换热器b、用于加热经过换热器b保温的液体乙烯至预热温度的换热器c和中压蒸汽进管,所述中压蒸汽进管连通于换热器c的加热介质进口;所述换热器c的换热介质出口连通有回汽出管;所述回汽出管连通有低压蒸汽调制机构;所述换热器c底部连通有u型冷凝水回收管件;所述u型冷凝水回收管件一端连通于换热器c底部且另一端连通于回汽出管周侧;所述u型冷凝水回收管件的底部连通有中压冷凝水汇集箱体;所述中压冷凝水汇集箱体的顶部连通于低压蒸汽调制机构;所述低压蒸汽调制机构输出的调制低压蒸汽连通于换热器a的热介质进口;所述换热器a的底部连通有低压蒸汽冷凝水管;所述低压蒸汽冷凝水管连通有低压冷凝水汇集箱体;所述低压冷凝水汇集箱体顶部连通于低压蒸汽调制机构;所述换热器a的换热介质出口连通于低压冷凝水汇集箱体的夹套层;所述低压冷凝水汇集箱体的底部连通于低压蒸汽调制机构;所述换热器b的液态换热介质进口连通于第二离心泵;所述第二离心泵连通于中压冷凝水汇集箱体底
部;所述换热器b的液态换热介质出口连通有水温调至机构;所述水温调至机构与低压蒸汽调制机构的低压蒸汽出口相连通。
7.本技术是基于乙烯合成环氧乙烷工艺中所用到的深冷乙烯进行热处理。首先本技术中发现中压蒸汽直接预热深冷乙烯的方式存在以下缺陷:一是换热温度过高,易导致部分深冷乙烯发生热聚合,为了降低热聚合的影响,阻聚剂的添加量偏大,成本上升;二是中压蒸汽流通速度基于实际加热需求下是相对偏快的,回汽余量较高,中压蒸汽的热能利用率偏低。基于上述问题,本技术的中压蒸汽对液体乙烯(保温罐中的液态乙烯)进行加热升温处理达到合成工艺理想温度,中压蒸汽换热后的回汽经过低压蒸汽调制机构的调制得到可利用的低压蒸汽对深冷乙烯进行加热处理。经过可利用的低压蒸汽处理的深冷乙烯采用中压蒸汽产生的80-120℃冷凝水进行保温调控处理得液体乙烯(保温罐中的液态乙烯)。中压蒸汽产生的冷凝水经过对液体乙烯(保温罐中的液态乙烯)换热后用于低压蒸汽调制机构中的调节水源,吸收中压蒸汽换热后的回汽中多余热能后升温至80-120℃,再收集作为液体乙烯(保温罐中的液态乙烯)的换热介质使用。
8.综上所述,本技术具有蒸汽冷凝水热量回收率较高,充分结合于生产实际,有效利用中压蒸汽产生的冷凝水热能,降低整体能耗,节约生产成本,顺应当今绿色工厂的发展趋势。
9.优选的,所述水温调至机构包括外壳体、内壳体,所述外壳体、内壳体之间形成有夹套;所述低压蒸汽调制机构的低压蒸汽出口与夹套相连通;所述外壳体底部连通有低压冷凝水回收管;所述低压冷凝水回收管连通于内壳体;所述所述换热器b的换热介质出口连通于内壳体;所述内壳体顶部连通于中压冷凝水汇集箱体;所述外壳体的上部连通有低压回汽回收管;所述低压回汽回收管为u型回收管,一端连通于外壳体和内壳体之间的夹套,另一端连通于低压冷凝水汇集箱体的夹套层;所述低压回汽回收管的底部连通有用于回收冷凝水的冷凝水收集管;所述冷凝水收集管连通于内壳体的顶部;所述冷凝水收集管连通有第三离心泵;所述低压冷凝水回收管连通于冷凝水收集管。
10.通过低压蒸汽换热后产生的回汽和产生的冷凝水进行再利用,可有效提升整体的热能利用效果,降低整体能耗,节约生产成本。
11.优选的,所述水温调至机构还包括散热件;所述散热件一端与低压蒸汽调制机构的低压蒸汽出口相连通,且另一端与低压回汽回收管相连通;所述散热件转动连接于内壳体,且所述散热件连通于夹套。
12.通过散热件可更加充分利用调制后的低压蒸汽的热能,可有效提升整体的热能利用效果,降低整体能耗,节约生产成本。
13.优选的,所述散热件包括主蒸汽流通管和多个散热浆器,单个所述散热浆器连通于主蒸汽流通管的蒸汽流通道;相邻所述散热浆器的间距相等;单个所述散热浆器包括多个支蒸汽流通管,相邻所述支蒸汽流通管的间距相等;单个所述支蒸汽流通管一体形成有支蒸汽流通道;所述支蒸汽流通道一端连通于主蒸汽流通管的蒸汽流通道,且另一端呈封闭;单个所述支蒸汽流通管的外壁固定连接有散热翅片;所述散热翅片沿支蒸汽流通管的轴向相互间隔排列;相邻所述散热翅片的间距控制在2.0-4.0mm。
14.本技术调制后的低压蒸汽的热能用于补充换热后冷凝水的热量,可使得回收冷凝水温度与输入换热器b换热介质入口端冷凝水水温相接,回收冷凝水温度可直接输入中压
冷凝水汇集箱体,可有效提升整体的热能利用效果,降低整体能耗,节约生产成本。
15.优选的,所述低压蒸汽调制机构包括主低压蒸汽输送管、调节u型管件;所述主低压蒸汽输送管沿轴向先后依次设置有第四温度压力检测仪、第一控制阀、第五温度压力检测仪、第二控制阀;所述调节u型管件一端固定连通于主低压蒸汽输送管一端周向,且调节u型管件另一端固定连通于主低压蒸汽输送管另一端周向;所述调节u型管件与主低压蒸汽输送管的连接处分别位于第一控制阀的两侧;所述调节u型管件内连接有降温组件;所述降温组件连通于低压冷凝水汇集箱体;所述低压冷凝水汇集箱体的顶部连通于调节u型管件。
16.本技术中低压蒸汽调制机中的降温组件采用的降温水源和汽源都来源于中压蒸汽多级利用得到的,将换热后产生的中压蒸汽回汽用来源于中压蒸汽多级利用得到的降温水源和汽源进行温度和压力的调制,得可利用的低压蒸汽源,充分利用了中压蒸汽的热能,有效提升整体的热能利用效果,降低整体能耗,节约生产成本。
17.优选的,所述调节u型管件包括第一连接直管、第一半弯管、低压蒸汽调制主管、第二半弯管和第二连接直管;所述第一连接直管一端固定连通于主低压蒸汽输送管一端周向,且另一端连通于第一半弯管;所述低压蒸汽调制主管一端连通于第一半弯管背向第一连接直管的管段,且低压蒸汽调制主管另一端连通于第二半弯管;所述第二连接直管一端连通于主低压蒸汽输送管另一端周向,且另一端连通于第二半弯管背向低压蒸汽调制主管的管端;所述第二连接直管与主低压蒸汽输送管的连通处位于第一控制阀、第二控制阀之间;所述第一连接直管连通有第一电磁阀;所述第一半弯管连通有第一温度压力检测仪;所述第二连接直管连通有第二电磁阀;所述第二半弯管连通有第二温度压力检测仪。
18.本技术调节u型管件元器件可对换热后产生的中压蒸汽回汽用来源于中压蒸汽多级利用得到的降温水源和汽源进行较为精确及时的温度和压力调制,得质量稳定且可利用性较好的低压蒸汽源,不仅充分利用了中压蒸汽的热能,而且使用安全可靠性性更加好,有利于化工合成厂区的安全生产。
19.优选的,所述低压蒸汽调制机构还包括预备调节u型管件;所述预备调节u型管件的结构与调节u型管件的结构区别在于:低压蒸汽调制主管连接有第一增压泵;所述预备调节u型管件一端固定连通于主低压蒸汽输送管一端周向,且另一端固定连通于主低压蒸汽输送管另一端周向。
20.本技术中的预备调节u型管件可进一步保证调制后低压蒸汽源的质量稳定、较好的可利用性,进而保证化工合成厂区的安全生产,降低生产安全隐患风险。
21.优选的,所述降温组件包括输水主管、喷淋组合管,所述输水主管沿水流输送方向依次连通有第一离心泵、第三电磁阀、第三温度压力检测仪;所述输水主管一端连通于低压冷凝水汇集箱体的周侧底部,且另一端连通于喷淋组合管;所述喷淋组合管固定连接于低压蒸汽调制主管内部;所述第三温度压力检测仪连接于输水主管靠近低压蒸汽调制主管的一端周侧。
22.通过采用上述技术方案,降温组件可对换热后产生的中压蒸汽回汽进行温度和压力的调制,获得质量稳定、较好的可利用性的低压蒸汽源。
23.优选的,所述喷淋组合管包括多根固定连接于低压蒸汽调制主管内壁的喷淋直管,相邻所述喷淋直管之间相互连通;相邻所述喷淋直管之间的间隔相等;单根所述喷淋直管沿自身长度方向连接有多个相互间隔的喷淋头;所述喷淋头垂直朝向低压蒸汽调制主管
的中轴线。
24.通过采用上述喷淋组合管的结构设计,提升对换热后产生的中压蒸汽回汽的温度和压力的调制效率,有利于提升整体的生产效率,降低整体的生产成本。
25.优选的,所述换热器a的换热介质出口连接有回汽导出管;所述回汽导出管连通于低压冷凝水汇集箱体的夹套层;所述回汽导出管周向固定连通有调节汽支管;所述调节汽支管沿气流流动方向依次设置有第二增压泵、第四温度压力检测仪、第三电磁阀;所述调节汽支管背向回汽导出管的一端连通于输水主管靠近低压蒸汽调制主管的管端周向;所述第三电磁阀靠近于调节汽支管与输水主管的连接处;所述中压冷凝水汇集箱体的顶部连通于调节汽支管。
26.本技术中采用换热器a的换热介质出口产生的回汽对低压蒸汽调制主管中的待调制汽体进行降温降压处理,充分利用了中压蒸汽的热能,有效提升整体的热能利用效果,降低整体能耗,节约生产成本。
27.综上所述,本技术具有以下优点:1、本技术具有蒸汽冷凝水热量回收率较高,充分结合于生产实际,有效利用中压蒸汽产生的冷凝水热能,降低整体能耗,节约生产成本,顺应当今绿色工厂的发展趋势。
28.2、本技术可得到质量稳定且可利用性较好的低压蒸汽源,利用调制的低压蒸汽源进行合成生产不仅充分利用了中压蒸汽的热能,而且使用安全可靠性性更加好,有利于化工合成厂区的安全生产。
附图说明
29.图1是本技术实施例的整体结构示意图。
30.图2是本技术实施例的局部结构示意图,主要展示换热器c、u型冷凝水回收管件、回汽出管和低压蒸汽调制机构的连接结构。
31.图3是本技术实施例的低压蒸汽调制机构的结构示意图。
32.图4是本技术实施例的局部结构示意图,主要展示低压蒸汽调制机构、降温组件、低压冷凝水汇集箱体的连接结构。
33.图5是本技术实施例中水温调至机构的剖视图。
34.图6是本技术实施例中水温调至机构的整体结构示意图。
35.图7是本技术实施例中散热件的整体结构示意图。
36.图中,1、换热器a;11、换热器b;12、换热器c;13、中压蒸汽进管;131、温度压力检测仪a;132、温度压力检测仪b;2、低压蒸汽调制机构;20、回汽出管;21、主低压蒸汽输送管;211、第四温度压力检测仪;212、第一控制阀;213、第五温度压力检测仪;214、第二控制阀;22、调节u型管件;221、第一连接直管;222、第一半弯管;223、低压蒸汽调制主管;224、第二半弯管;225、第二连接直管;226、第一电磁阀;227、第一温度压力检测仪;228、第二电磁阀;229、第二温度压力检测仪;23、预备调节u型管件;231、第一增压泵;3、u型冷凝水回收管件;4、中压冷凝水汇集箱体;41、第二离心泵;42、蒸汽传输管道;43、第三增压泵;5、低压蒸汽冷凝水管;51、低压冷凝水汇集箱体;52、第一离心泵;6、水温调至机构;61、外壳体;62、内壳体;63、夹套;64、低压冷凝水回收管;65、低压回汽回收管;651、冷凝水收集管;652、第三离心泵;66、散热件;661、主蒸汽流通管;662、散热浆器;6621、支蒸汽流通管;6622、支蒸汽流
通道;6623、散热翅片;7、降温组件;71、输水主管;711、第一离心泵;712、第三电磁阀;713、第三温度压力检测仪;72、喷淋组合管;721、喷淋直管;722、喷淋头;8、回汽导出管;81、调节汽支管;82、第二增压泵;83、第四温度压力检测仪;84、第三电磁阀。
具体实施方式
37.以下结合附图和实施例对本技术作进一步详细说明。
38.参照图1,为本技术公开的一种储运系统中的蒸汽冷凝水热量再利用系统,包括用于加热深冷乙烯的换热器a1、用于调整经过换热器a1换热后的液体乙烯温度的换热器b11、用于加热经过换热器b11保温的液体乙烯至预热温度的换热器c12。换热器c12的加热介质进口连通有用于连通工业园区内的中压蒸汽管道的中压蒸汽进管13。
39.参照图2,结合图1,中压蒸汽进管13靠近换热器c12的加热介质进口的管端周向连接有温度压力检测仪a131,温度压力检测仪a131会与中控室的显示端相连接,用于及时掌握输入中压蒸汽的温度和压强。换热器c12的加热介质进口通过法兰固定连接有回汽出管20。回汽出管20靠近换热器c12的加热介质出口的管端周向连接有温度压力检测仪b132,温度压力检测仪b132会与中控室的显示端相连接,用于及时掌握换热后中压蒸汽的温度和压强。
40.参照如3,结合图1,回汽出管20背向换热器c12的加热介质出口的管端通过法兰固定连通有用于调制中压蒸汽换热后产生回汽的低压蒸汽调制机构2。低压蒸汽调制机构2包括主低压蒸汽输送管21、调节u型管件22、预备调节u型管件23。主低压蒸汽输送管21一端通过法兰固定连接于回汽出管20,且另一端通过法兰固定连通于低压蒸汽输出管网。低压蒸汽输出管网是用于输出调制完成后的低压蒸汽,低压蒸汽输出管网连通于换热器a1的换热介质进口。低压蒸汽输出管网连通于水温调至机构6的换热介质进口。
41.参照图3,结合图1,主低压蒸汽输送管21沿轴向先后依次设置有第四温度压力检测仪211、第一控制阀212、第五温度压力检测仪213、第二控制阀214。其中,第一控制阀212和第二控制阀214选择的是电磁阀,电磁阀与中控室的操作端相连接。
42.参照图3,结合图4,调节u型管件22包括第一连接直管221、第一半弯管222、低压蒸汽调制主管223、第二半弯管224和第二连接直管225。第一连接直管221一端通过法兰固定连通于主低压蒸汽输送管21一端周向,且另一端通过法兰连通于第一半弯管222。低压蒸汽调制主管223一端通过法兰连通于第一半弯管222背向第一连接直管221的管段,且低压蒸汽调制主管223另一端通过法兰连通于第二半弯管224。第二连接直管225一端通过法兰连通于主低压蒸汽输送管21另一端周向,且第二连接直管225另一端通过法兰连通于第二半弯管224背向低压蒸汽调制主管223的管端。第二连接直管225与主低压蒸汽输送管21的连通处位于第一控制阀212、第二控制阀214之间。第一连接直管221与主低压蒸汽输送管21的连接处、第二连接直管225与主低压蒸汽输送管21的连接处分别位于第一控制阀212的两侧。低压蒸汽调制主管223内设置有降温组件7。
43.参照图3,结合图1,第一连接直管221通过法兰固定连通有第一电磁阀226。第二连接直管225通过法兰固定连通有第二电磁阀228。第一电磁阀226和第二电磁阀228与中控室的操作端相连接。第一半弯管222通过法兰固定连通有第一温度压力检测仪227。第二半弯管224通过法兰固定连通有第二温度压力检测仪229。第一温度压力检测仪227和第二温度
压力检测仪229会与中控室的显示端相连接,用于及时掌握调制前后中压蒸汽换热后回汽的温度和压强。
44.参照图3,结合图1,预备调节u型管件23的结构与调节u型管件22的连接结构相同,皆包含有第一连接直管221、第一半弯管222、低压蒸汽调制主管223、第二半弯管224和第二连接直管225。预备调节u型管件23一端通过法兰固定连通于主低压蒸汽输送管21一端周向,且另一端通过法兰固定连通于主低压蒸汽输送管21另一端周向。预备调节u型管件23的结构与调节u型管件22的连接结构唯一的区别在于:低压蒸汽调制主管223沟通过法兰固定连接有第一增压泵231。第一增压泵231的作用是:将经过调节u型管件22调制后的低压蒸汽但又未到达输出标准的汽体重新输入至主低压蒸汽输送管21靠近回汽出管20一端周向。
45.参照图2,结合图4,换热器c12底部周向的冷凝水出水端口通过法兰固定连通有u型冷凝水回收管件3。u型冷凝水回收管件3一端通过法兰固定连通于换热器c12底部周向的冷凝水出水端口,且换热器c12的另一端通过法兰固定连通于回汽出管20周侧。u型冷凝水回收管件3的底部通过管道固定连通有中压冷凝水汇集箱体4。中压冷凝水汇集箱体4用于储存中压蒸汽换热后产生的冷凝水。中压冷凝水汇集箱体4的顶部通过蒸汽传输管道42固定连通于降温组件7,作为降温组件7的降温蒸汽使用。
46.参照图4,结合图1,低压蒸汽调制机构2连接的低压蒸汽输出管网中输出的调制低压蒸汽连通于换热器a1的热介质进口。换热器a1的底部周侧的冷凝水出口通过法兰固定连通有低压蒸汽冷凝水管5。低压蒸汽冷凝水管5固定连通有低压冷凝水汇集箱体51,用于储存调制低压蒸汽换热后产生的冷凝水。低压冷凝水汇集箱体51的顶部通过管道固定连通于低压蒸汽调制机构2的低压蒸汽调制主管223周侧,用于收集低压蒸汽调制主管223中的冷凝水。低压冷凝水汇集箱体51的底部周侧通过法兰固定连通于调温组件7。
47.参照图4,结合图1,降温组件7包括输水主管71、喷淋组合管72,其中输水主管71沿水流输送方向依次固定连通有第一离心泵711、第三电磁阀712、第三温度压力检测仪713。第三温度压力检测仪713连接于输水主管71靠近低压蒸汽调制主管223的一端周侧。第三电磁阀712、第三温度压力检测仪713与中控室相连接。输水主管71一端通过法兰固定连通于低压冷凝水汇集箱体51的周侧底部,且输水主管71的另一端连通于喷淋组合管72。喷淋组合管72固定连接于低压蒸汽调制主管223内部。
48.参照图4,结合图1,喷淋组合管72包括六根固定连接于低压蒸汽调制主管223内壁的喷淋直管721,相邻喷淋直管721之间相互连通且相邻喷淋直管721之间的间隔相等。单根喷淋直管721沿自身长度方向连接有多个相互间隔的喷淋头722,喷淋头722垂直朝向低压蒸汽调制主管223的中轴线,相邻喷淋头722的间距为3.2cm。
49.参照图4,结合图1,换热器a1的换热介质出口固定连接有回汽导出管8。其中,回汽导出管8背向换热器a1的换热介质出口的一端固定连通于低压冷凝水汇集箱体51的夹套层,用于对低压冷凝水汇集箱体51进行控温。低压冷凝水汇集箱体51的夹套层中输出的回汽通过管道连通于换热器b11的气态热介质进口。换热器b11的气态热介质出口通过管道连通于常温水箱。常温水箱通过管道连通于中压冷凝水汇集箱体4。低压冷凝水汇集箱体51的夹套层中冷凝水通过离心泵输入至低压冷凝水汇集箱体51的顶部。换热器b11的夹套层中的冷凝水通过增压泵输入与第二离心泵41连通的管道周向,使得夹套层中的冷凝水输入换热器b11的液体换热介质进口。换热器b11的液态换热介质出口固定连通有水温调至机构6,
水温调至机构6与低压蒸汽调制机构2的低压蒸汽出口相连通。
50.参照图4,结合图1,回汽导出管8周向固定连通有调节汽支管81。调节汽支管81沿气流流动方向依次设置有第二增压泵82、第四温度压力检测仪83、第三电磁阀84。调节汽支管81背向回汽导出管8的一端连通于输水主管71靠近低压蒸汽调制主管223的管端周向。第三电磁阀84靠近于调节汽支管81与输水主管71的连接处,且第三电磁阀84位于调节汽支管81与输水主管71的连接处的下游。中压冷凝水汇集箱体4顶部连接的蒸汽传输管道42上固定连通有第三增压泵43,蒸汽传输管道42连通于调节汽支管81。中压冷凝水汇集箱体4产生的蒸汽用于降温机构7的降温汽体使用。
51.参照图5,结合图1,水温调至机构6包括外壳体61、内壳体62和散热件66。其中,外壳体61、内壳体62之间形成有夹套63,夹套63中通入经过低压蒸汽输出管网传输过来的调制完成的低压蒸汽,即低压蒸汽调制机构2的低压蒸汽出口与夹套63相连通。
52.参照图5,结合图1,外壳体61底部连通有低压冷凝水回收管64,低压冷凝水回收管64与夹套63相连通,且低压冷凝水回收管64的另一端连通于内壳体62的顶部,使得低压冷凝水回收管64中收集的冷凝水通过离心泵输入至内壳体62的内部。换热器b11的液体换热介质出口固定连通于内壳体62的底部周侧,即换热后的中压冷凝水汇集箱体4中输出的冷凝水输入内壳体62中进行温度补偿。内壳体62顶部通过管道固定连通于中压冷凝水汇集箱体4的上部周侧,将内壳体62中完成热补充的水体输入中压冷凝水汇集箱体4中备用。
53.参照图5,参照图6,外壳体61的上部连通有低压回汽回收管65,低压回汽回收管65为u型回收管。低压回汽回收管65的一端固定连通于外壳体61和内壳体62之间的夹套63,低压回汽回收管65的另一端通过管道固定连通于回汽导出管8,实现了换热后的调制低压蒸汽输向低压冷凝水汇集箱体51的夹套层,进行低压冷凝水汇集箱体51的温控处理。
54.参照图5,参照图6,低压回汽回收管65的底部固定连通有用于回收冷凝水的冷凝水收集管651,冷凝水收集管651背向低压回汽回收管65的底部的一端固定连通于内壳体62的顶部。冷凝水收集管651固定连通有第三离心泵652。低压冷凝水回收管64固定连通于冷凝水收集管651周向,且低压冷凝水回收管64与冷凝水收集管651周向的连接处位于第三离心泵652的上游。
55.参照图5,结合图1,散热件66连通于夹套63,实现了散热件66与低压蒸汽调制机构2的低压蒸汽输出管网相连通。散热件66一端连通于低压蒸汽调制机构2的低压蒸汽输出管网,另一端与低压回汽回收管65相连通。
56.参照图5,结合图7,散热件66转动且密封连接于内壳体62,散热件66的数量为两个。散热件66包括主蒸汽流通管661和多个散热浆器662,其中一个散热件66的散热浆器662的数量为三个,另一个散热件66的散热浆器662的数量为两个。具有三个散热浆器662的散热件66位于另一个散热件66的下方。
57.参照图5,结合图7,单个散热浆器662连通于主蒸汽流通管661的蒸汽流通道。相邻散热浆器662的间距相等。具有两个散热浆器662的散热件66中散热浆器662的竖直投影位于另一个散热件66的相邻散热浆器662的竖直投影之间。
58.参照图5,结合图7,单个散热浆器662包括四个支蒸汽流通管6621和散热翅片6623。其中相邻支蒸汽流通管6621的间距相等。单个支蒸汽流通管6621一体形成有支蒸汽流通道6622,支蒸汽流通道6622一端连通于主蒸汽流通管661的蒸汽流通道,且另一端呈封
闭。散热翅片6623固定连接于单个支蒸汽流通管6621的外壁,且散热翅片6623沿支蒸汽流通管6621的轴向相互间隔排列。为了保证热能传递效率,散热翅片6623为表面镀铜的不锈钢件,相邻散热翅片6623的间距控制在2.0-4.0mm。本实施例中相邻散热翅片6623的间距控制在2.8mm。
59.所述储运系统中的蒸汽冷凝器水热量再利用系统中的连接管道外壁及其中压冷凝水汇集箱体4、低压冷凝水汇集箱体51、水温调至机构6中外壳体61的外壁均涂覆有隔热保温涂料。
60.隔热保温涂料是由ab料混合制备,a料:b料的质量比为1:0.3。其中,a料是由以下重量份的原料制备而成:100份的复合调制乳胶液、25份的隔热填料、40份的沥青乳液。b料是由29.8份去离子水、0.2份的偶氮异丁氰基甲酰胺混合制备。其中,沥青乳液为40份中70#沥青乳液30份和90#沥青乳液10份,根据化工企业当地的气候进行针对性的选择,本技术实际所处地理位置在北纬30
°
15
′‑
31
°
02
′
,东经120
°
20
′‑
121
°
31
′
。100份的复合调制乳胶液是由40份丁苯胶乳、20份丁基乳胶、20份聚四氟乙烯乳液组成。25份的隔热填料是由16份的5-7微米的中空玻璃微球、5份的钛白粉、3份的碳酸钙、1份的羟乙基纤维素组成。
61.70#沥青乳液的制备方法,按配比称量1.0kg的op-10乳化剂、500g的消泡剂、3.85kg的8%氢氧化钠溶液、500g的水玻璃、1.4kg的聚乙烯醇和45.0kg的去离子水,投入反应釜a中升温至38-40℃,在600rpm转速下,搅拌混合20分钟,再升温至60-65℃,搅拌5min,得乳化液料;50kg的70#沥青加热至70℃,在300rpm转速下,维持搅拌15min,加入乳化液料、100g氢氧化镁、80g氢氧化铝,温度维持至60℃,以200 rpm转速下,维持搅拌15min,得70#沥青乳液。
62.90#沥青乳液的制备方法,按配比称量1.0kg的op-10乳化剂、500g的消泡剂、3.85kg的8%氢氧化钠溶液、500g的水玻璃、1.4kg的聚乙烯醇和45.0kg的去离子水,投入反应釜a中升温至38-40℃,在600rpm转速下,搅拌混合20分钟,再升温至75℃,搅拌5min,得乳化液料;50kg的90#沥青加热至70℃,在300rpm转速下,维持搅拌15min,加入乳化液料、100g氢氧化镁、80g氢氧化铝,温度维持至65℃,以200 rpm转速下,维持搅拌15min,得90#沥青乳液。
63.隔热保温涂料的制备方法,先按配比称量40kg丁苯胶乳、20kg丁基乳胶、20kg聚四氟乙烯乳液投入反应釜中,在58-60℃下以120rpm搅拌100s然后以300rpm搅拌15min,抽真空至50pa,持续抽15min,得复合调制乳胶液;再按配比称量30kg的70#沥青乳液、10kg的90#沥青乳液投入至反应釜中,温度控制为78-80℃,以400 rpm搅拌15min,依次加入16kg的5-7微米的中空玻璃微球、5kg的钛白粉、3kg的碳酸钙、1kg的羟乙基纤维素,以320rpm搅拌15min得沥青乳液;最后配制的复合调制乳胶液加入至沥青乳液的反应釜中,反应釜温度控制为80-85℃,复合调制乳胶液以3kg/min的速度加入反应釜中,滴加完成后,以320rpm转速混合搅拌30min,抽真空至50pa,持续抽10min,得a料。将39.8kg的去离子水和0.2kg的偶氮异丁氰基甲酰胺以300rpm混合5min得b料。将a料和b料以300rpm混合10min得可利用的隔热保温涂料。
64.本具体实施例仅仅是对本技术的解释,其并不是对本技术的限制,本领域技术人员在阅读完本说明书后可以根据需要对本实施例做出没有创造性贡献的修改,但只要在本技术的权利要求范围内都受到专利法的保护。