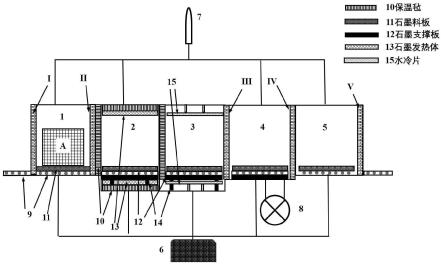
1.本发明总体地属于陶瓷基复合材料制造技术领域,尤其涉及一种适用于纤维增强陶瓷基复合材料制备的高温裂解装置。
背景技术:2.连续纤维增强/增韧陶瓷基复合材料能够解决单相陶瓷的脆性,具备较高的任性和抗冲击能力,同时兼具了陶瓷耐高温、耐磨和抗氧化等优势。
3.先驱体浸渍-裂解工艺(polymer infiltration andpyrolysis,简称pip工艺)是目前制备纤维增强陶瓷基复合材料的主要工艺之一。该工艺过程为:1)将纤维预制体放置于密封容器,抽真空;2)注入溶液或液态先驱体;3)浸渍一段时间,先驱体通过毛细管力渗入预制体;4)打开密封容器,取出已浸渍预制体晾干、交联固化;5)将预制体转移至惰性气体保护的高温炉升温至制定温度裂解;6)裂解结束后随炉冷却,取出产品;6)重复浸渍-交联-裂解工序指导获得致密的复合材料。
4.目前高温裂解设备承担了升温裂解和冷却降温两个功能,需要缓慢升温至1000℃以上(如产品多热沉大升温速率更慢),完成高温裂解后自然冷却降温,由于有保温毡的保温作用降温过程非常缓慢,一般需要2-3天,如果设备尺寸大或者装载产品多则降温时间更长。在这个升降温过程中存在如下不足:1)升降温过程导致能量损耗大,特别是降温后再次装载产品还需要重新升温,导致能源浪费;2)产品在裂解炉中原位冷却降温速率极慢导致设备占用时间长、利用率低,导致产品的生产效率低、周期长,从而制造成本上升;3)设备利用率低,导致要生产相同的产品则需要建设更多台套的设备,导致生产用设备固定投资增加,变相提高了产品的制造成本。
5.虽然有部分裂解设备集成了低温段(约500℃)随炉风冷设备,但仍然需要随炉降温且高于500℃的高温段随炉自然降温效率仍然很低。如果能裂解炉分解成不同的空间,将高温裂解功能和冷却降温功能分区实现,在冷却降温区采用辅助措施提高冷却效率,将可以达到降低能耗、提高生产效率、缩短制造周期、降低制造成本的目的。
技术实现要素:6.本发明的目的在于提供一种适用于纤维增强陶瓷基复合材料制备的高温裂解装置。
7.本发明的技术方案是,一种适用于纤维增强陶瓷基复合材料制备的高温裂解装置,所述高温裂解装置为不锈钢或普通碳钢材质围成的炉体,炉体空间内包括各自独立密封且依次相连接的进料区、高温裂解区、辐射冷却区、风冷区和出料区;还包括进气系统和传动系统;所述进气系统分别与进料区、高温裂解区、风冷区和出料区相连通,用于向上述区间内输送气体;所述传动系统设置在进料区、高温裂解区、辐射冷却区、风冷区和出料区的底部共同水平面上,传动系统通过辊轴转动使物料依次进出进料区、高温裂解区、辐射冷却区、风冷区和出料区。
8.本发明的适用于纤维增强陶瓷基复合材料制备的高温裂解装置还包括真空系统和风冷系统;所述真空系统分别与进料区、辐射冷却区、风冷区和出料区相连,用于使各区处于真空状态;所述风冷系统与风冷区相连,用于风冷区的降温。
9.进一步的,上述进料区、高温裂解区、辐射冷却区、风冷区和出料区的底部,传动系统辊轴的上表面均设置有石墨料板;所述传动系统在高温裂解区底部为无动力驱动,在高温裂解区底部以外的区间为有动力驱动;所述动力驱动结构为电动铰链驱动结构;进料区底部的电动铰链驱动结构驱动辊轴的上表面的石墨料板将高温裂解区底部的石墨料板顶出驱动至辐射冷却区,实现传动系统在高温裂解区底部的无动力驱动。
10.进一步的,上述进料区包括设置在远离高温裂解区一侧的第一密封门、靠近高温裂解区一侧的第二密封门;物料在第一密封门打开时进入进料区,在第二密封门打开时离开进料区。
11.进一步的,上述高温裂解区中垂直物料运动方向的两侧设置有保温毡,保温毡打开时物料进出高温裂解区;所述高温裂解区中平行于物料运动方向的两侧和顶部从外向内依次设置有保温毡和石墨发热体;所述石墨发热体为镂空结构,石墨发热体包括发热节点和石墨电极,所述石墨发热节点与石墨电极相连并由石墨电极支撑;所述高温裂解区底部的传动系统辊轴下侧从内向外依次设置有石墨支撑板、石墨发热体和保温毡;所述石墨支撑板、石墨发热体和保温毡之间通过贯穿石墨发热体间隙的石墨支撑柱与炉体最外侧的内层连接固定;传动系统的辊轴在高温裂解区底部为石墨材质。
12.进一步的,上述高温裂解区、辐射冷却区、风冷区外侧的炉体为双层水冷结构;所述辐射冷却区的顶部、底部和平行于物料运动方向的两侧均设置有水冷片;所述水冷片材质为铜;所述辐射冷却区的顶部和平行于物料运动方向的两侧的水冷片带有伸缩装置,用于根据物料的尺寸调节水冷片与物料的距离;所述辐射冷却区底部的水冷片位于传动系统辊轴下侧,水冷片与传动系统辊轴下侧之间还设置有石墨支撑板,石墨支撑板通过石墨支撑柱与炉体最外侧的内层相连并固定;所述水冷片直接与炉体的双层水冷结构中的冷却水连通,起到给物料冷却降温的作用;传动系统的辊轴在辐射冷却区底部为石墨材质。
13.进一步的,上述风冷区底部的传动系统辊轴下侧设置有石墨支撑板;所述风冷区通过管道连接有风机;风冷区及其连接的管道和大功率风机构成密封循环体系;所述管道为双层水冷结构,且管道中配置水冷翅片、盘管增效冷却装置。
14.进一步的,上述辐射冷却区与风冷区之间、风冷区与出料区之间、出料区远离风冷区一侧分别设置有第三密封门、第四密封门和第五密封门。
15.进一步的,上述第二密封门、第三密封门为双层水冷结构,材质为不锈钢或普通碳钢;所述第一密封门、第四密封门和第五密封门为单层结构,材质为不锈钢或普通碳钢。
16.所述高温裂解区和辐射冷却区底部的传动系统辊轴为石墨材质,其余区域的传动系统辊轴为金属材质。
17.进一步的,上述风冷区的个数≥2个,多个风冷区依次连接在辐射冷却区与出料区之间。
18.现有技术相比,本发明的优点在于:
19.1、本发明装置用于纤维增强陶瓷基复合材料的高温裂解,其将传统技术中的裂解炉分解成不同的空间,将高温裂解功能和冷却降温功能分区实现,在冷却降温区采用辅助
措施提高冷却效率,功能分区和一体化集成,降低了单位能耗,提高了生产效率和设备利用率。
20.2、本发明装置能够使整个高温裂解和冷却过程全程处于保护性气体保护状态,特别适用于生产增强纤维和陶瓷基体高温易被氧化的复合材料体系,解决纤维增强碳化硅陶瓷基复合材料生产过程中裂解升降温能耗浪费、降温冷却时间长和高温裂解设备利用率低的不足等问题。
21.3、本发明装置,与现有装置相比提高设备利用效率可提高3倍,生产用固定资产投资减少1/2-2/3,还能达到降低能耗、提高生产效率、缩短制造周期、降低制造成本的目的。
附图说明
22.从下面结合附图对本发明实施例的详细描述中,本发明的这些和/或其它方面和优点将变得更加清楚并更容易理解,其中:
23.图1为本发明实施例中一种适用于纤维增强陶瓷基复合材料制备的高温裂解装置的结构示意图。
具体实施方式
24.为了使本领域技术人员更好地理解本发明,下面结合附图和具体实施方式对本发明作进一步详细说明。
25.实施例1
26.一种适用于纤维增强陶瓷基复合材料制备的高温裂解装置,其结构如图1所示,它为不锈钢或普通碳钢材质围成的炉体,炉体空间内包括各自独立密封且依次相连接的进料区1、高温裂解区2、辐射冷却区3、风冷区4和出料区5;还包括进气系统7和传动系统9,各部分连接关系和功能如下:
27.进气系统7分别与进料区1、高温裂解区2、风冷区4和出料区5相连通,用于向上述区间内输送气体;
28.传动系统9设置在进料区1、高温裂解区2、辐射冷却区3、风冷区4和出料区5的底部共同水平面上,传动系统9通过辊轴转动使物料依次进出进料区1、高温裂解区2、辐射冷却区3、风冷区4和出料区5。
29.优选还包括真空系统6和风冷系统8;真空系统6分别与进料区、辐射冷却区3、风冷区4和出料区5相连,用于使辐射冷却区3处于真空状态,以根据物料制备的需要提供真空环境;风冷系统8与风冷区4相连,用于风冷区4的进一步快速降温。
30.各区间的具体结构和优选设计如下:
31.进料区1、高温裂解区2、辐射冷却区3、风冷区4和出料区5的底部,传动系统9辊轴的上表面均设置有石墨料板11;传动系统9在高温裂解区2底部为无动力驱动,在高温裂解区2底部以外的区间为有动力驱动;动力驱动结构为电动铰链驱动结构;进料区1底部的电动铰链驱动结构驱动辊轴的上表面的石墨料板将高温裂解区2底部的石墨料板顶出驱动至辐射冷却区3,实现传动系统9在高温裂解区2底部的无动力驱动。
32.进料区1包括设置在远离高温裂解区2一侧的第一密封门i、靠近高温裂解区2一侧的第二密封门ii;物料在第一密封门i打开时进入进料区1,在第二密封门ii打开时离开进
料区1。
33.高温裂解区2中垂直物料运动方向的两侧设置有保温毡10,保温毡10打开时物料进出高温裂解区2;高温裂解区2中平行于物料运动方向的两侧和顶部从外向内依次设置有保温毡10和石墨发热体13;石墨发热体13为镂空结构,石墨发热体包括发热节点和石墨电极,石墨发热节点与石墨电极相连并由石墨电极支撑;高温裂解区2底部的传动系统9辊轴下侧从内向外依次设置有石墨支撑板12、石墨发热体13和保温毡10;石墨支撑板12、石墨发热体13和保温毡10之间通过贯穿石墨发热体13间隙的石墨支撑柱14与炉体最外侧的内层连接固定;传动系统9的辊轴在高温裂解区2底部为石墨材质。
34.高温裂解区2、辐射冷却区3、风冷区4外侧的炉体为双层水冷结构;辐射冷却区3的顶部、底部和平行于物料运动方向的两侧均设置有水冷片15;水冷片15材质为铜;辐射冷却区3的顶部和平行于物料运动方向的两侧的水冷片15带有伸缩装置,用于根据物料的尺寸调节水冷片与物料的距离;辐射冷却区3底部的水冷片15位于传动系统9辊轴下侧,水冷片15与传动系统9辊轴下侧之间还设置有石墨支撑板12,石墨支撑板12通过石墨支撑柱14与炉体最外侧的内层相连并固定;水冷片15直接与炉体的双层水冷结构中的冷却水连通,起到给物料冷却降温的作用;
35.传动系统9的辊轴在辐射冷却区3底部为石墨材质。
36.风冷区4底部的传动系统9辊轴下侧设置有石墨支撑板12;风冷区4通过管道连接有风机;风冷区4及其连接的管道和大功率风机构成密封循环体系;管道为双层水冷结构,且管道中配置水冷翅片、盘管增效冷却装置。
37.辐射冷却区3与风冷区4之间、风冷区4与出料区5之间、出料区5远离风冷区4一侧分别设置有第三密封门iii、第四密封门iv和第五密封门v。
38.第二密封门ii、第三密封门iii为双层水冷结构,材质为不锈钢或普通碳钢;第一密封门i、第四密封门iv和第五密封门v为单层结构,材质为不锈钢或普通碳钢。
39.高温裂解区2和辐射冷却区3底部的传动系统9辊轴为石墨材质,其余区域的传动系统9辊轴为金属材质。
40.风冷区4的个数≥2个,多个风冷区4依次连接在辐射冷却区3与出料区5之间。
41.利用本实施例的高温裂解装置对纤维增强陶瓷基复合材料进行快速裂解的工艺包括以下步骤:
42.s1、进料:初始状态为所有分区的门处于关闭状态,所有炉腔均为保护气氛保护状态;打开第一密封门i,将第一批坯料或带工装的工件a通过传动系统9装入进料区1,然后关闭第一密封门i,对进料区1抽真空后注入保护性气氛;
43.s2、高温裂解:打开第二密封门ii和与第二密封门ii相连接的保温毡10,通过传动系统9将第一批坯料或带工装的工件a送入高温裂解区2,后关闭第二密封门ii和与第二密封门ii相连接的保温毡10,升温至设定温度,保温一段时间;在关闭第二密封门ii和与第二密封门ii相连接的保温毡10关闭之后,进行步骤s1中打开第一密封门i之后的操作,以将第二批坯料或带工装的工件装入进料区1;
44.s3、辐射冷却:打开高温裂解区2和辐射冷却区3之间的保温毡10,通过传动系统9将第一批坯料或带工装的工件a送入辐射冷却区3,关闭打开的保温毡10;通过水冷片15的伸缩装置将辐射冷却区3顶部和两侧的水冷片15靠近第一批坯料或带工装的工件a,通过水
冷铜片吸收第一批坯料或带工装的工件a的辐射传热,同时增加炉体夹层冷却水的流量,利用与水冷片15连接的炉体夹层冷却水循环冷却一定时间,将第一批坯料或带工装的工件a冷却到指定温度;在关闭打开的保温毡10之后,同步将第二批坯料或带工装的工件送入高温裂解区2高温裂解,然后将第三批坯料或带工装的工件送入进料区1处理;
45.s4、风冷:打开第三密封门iii,通过传动系统9将第一批坯料或带工装的工件送入风冷区4,然后关闭第三密封门iii,通过风机产生气流进行热传导冷却,使气流温度降低至设定温度;此时,第二批坯料或带工装的工件在进行步骤s3的处理;第三批坯料或带工装的工件在进行步骤s2的处理,第四批坯料或带工装的工件送入进料区1处理;
46.s5、出炉:打开第四封门iv,通过传动系统9将坯料或带工装的工件a送入出料区5,后关闭第四封门iv;打开第五密封门v,通过过传动装置9将坯料或带工装的工件a出料,关闭第五密封门v,出料区5抽真空后注入保护性气氛;此时,第二批坯料或带工装的工件、三批坯料或带工装的工件、第四批坯料或带工装的工件和第五批坯料或带工装的工件依次在步骤s4、s3、s2、s1的处理步骤中。
47.优选步骤s2中的设定温度为800-1400℃,保温时间0.5-2h,高温裂解区2升温和处理物料过程保持流动保护气氛;步骤s3中的冷却时间1-6h,炉体夹层中冷却水流量大于100t/h;坯料或带工装的工件被冷却到的指定温度温度为500-600℃;步骤s4中,风冷冷却时间6-15h,风冷至使气流温度降低至80℃。
48.本发明的上述高温裂解装置,可以使待裂解的纤维增强陶瓷基复合材料分批、依次在不同的区间分别进行进料、高温裂解、辐射降温处理、风冷处理,提高了处理效率、节省了处理能耗。
49.以上已经描述了本发明的各实施例,上述说明是示例性的,并非穷尽性的,并且也不限于所披露的各实施例。在不偏离所说明的各实施例的范围和精神的情况下,对于本技术领域的普通技术人员来说许多修改和变更都是显而易见的。因此,本发明的保护范围应该以权利要求的保护范围为准。