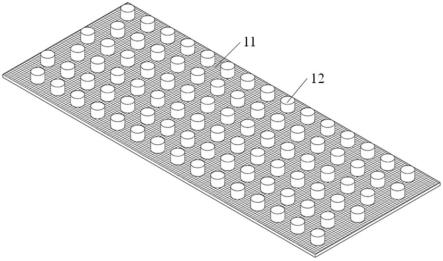
1.本实用新型涉及相变传热技术领域,特别是涉及一种采用气液一体式吸液芯的柔性平板热管。
背景技术:2.柔性电子设备的快速发展推动了相变传热器件向柔性化方向的转变,制作具有高传热性能和高弯曲疲劳寿命的轻薄化相变传热器件对解决柔性电子设备的散热难题具有重要意义。
3.现有技术的柔性平板热管主要包括两种形式。一种形式是采用多层金属丝网做吸液芯,吸液芯上面采用大孔隙的聚合物丝网做蒸汽通道,吸液芯与蒸汽通道互相分离,其存在聚合物丝网横向丝阻碍蒸汽流动,导致流动阻力大的技术问题。另一种形式是在一个相对较厚的铜壳体上用化学蚀刻的方法加工出蒸汽通道,并采用丝网作为吸液芯,吸液芯与蒸汽通道分离。由于铜壳体的铜层较厚,导致热管柔性变差。
4.如果为了保证热管的柔性而采用柔性薄膜作为壳体,则较薄的壳体厚度使得难以在其表面制作有效的蒸汽通道。同时,柔性平板热管在弯折使用的过程中其壳体两侧分别承受拉力和压力,较薄的壳体面临疲劳开裂和塑性变形产生褶皱的风险。
技术实现要素:5.针对现有技术中存在的技术问题,本实用新型的目的是:提供一种采用气液一体式吸液芯的柔性平板热管,同时兼具较好的强度和较佳的柔性,能够避免反复弯折时疲劳开裂和塑性变形产生褶皱。
6.为了达到上述目的,本实用新型采用如下技术方案:
7.一种采用气液一体式吸液芯的柔性平板热管,包括由柔性薄膜围闭成具有内腔的热管本体,由柔性薄膜围闭而成的热管本体具有较好的柔性。热管本体内腔抽真空且填充有工质,热管本体内腔中设有气液一体式吸液芯,气液一体式吸液芯包括毛细结构和多个支撑结构,毛细结构抵接于热管本体底部,由热管本体一端延伸至热管本体另一端形成液体通道;多个支撑结构间隔设置,每个支撑结构一端固接于毛细结构,另一端抵接于热管本体顶部,多个支撑结构提高了热管的抗拉和抗压能力,使得柔性平板热管在弯折使用过程中,由柔性薄膜制成的热管本体能够避免疲劳开裂和塑性变形产生褶皱的风险。多个支撑结构之间的间隙互相连通形成蒸汽通道,克服了现有技术中化学刻蚀、机械加工难以在柔性平板热管壳体表面制作有效蒸汽通道的缺陷。
8.进一步,多个支撑结构的高度相同或呈周期分布的高-矮梯度组合。
9.进一步,支撑结构的高度为0.15-5mm。
10.进一步,支撑结构的直径和相邻支撑结构的间距均为单一尺寸,或者分别呈梯度尺寸组合分布。
11.进一步,支撑结构的直径为0.1-1mm,相邻支撑结构的间距为0.4-2mm。
12.进一步,多个支撑结构为阵列排布的支撑柱。
13.进一步,支撑结构为多孔结构或实体结构,毛细结构为纤维毡、多层丝网、编织带或多层丝网与编织带结合的复合结构;丝网和编织带的材质为铜、不锈钢、尼龙、聚四氟乙烯或聚丙烯;纤维毡的材质为碳纤维、玻璃纤维或聚丙烯纤维。
14.一种采用气液一体式吸液芯的柔性平板热管的制备方法,包括以下步骤,将柔性薄膜围闭成具有内腔的热管本体;
15.将多个支撑结构间隔固设于毛细结构上,制备得到气液一体式吸液芯;
16.将气液一体式吸液芯置入于热管本体内腔中,使毛细结构由热管本体一端延伸至热管本体另一端形成液体通道,且多个支撑结构之间的间隙互相连通形成蒸汽通道;
17.往热管本体内腔灌注工质,抽真空后封口处理,制备得到柔性平板热管。
18.进一步,调整多个支撑结构的高度分布以及相邻支撑结构的间距以调节柔性平板热管的柔性。
19.进一步,毛细结构和支撑结构采用高温烧结、胶水粘接或者焊接方式连接,或采用3d打印、电沉积工艺直接在毛细结构表面制作支撑结构。
20.总的说来,本实用新型具有如下优点:
21.多个支撑结构提高了热管的抗拉和抗压能力,使得柔性平板热管在弯折使用过程中,热管本体能够避免疲劳开裂和塑性变形产生褶皱的风险。多个支撑结构之间的间隙互相连通形成蒸汽通道,克服了现有技术中难以在柔性平板热管壳体表面制作有效蒸汽通道的缺陷。
附图说明
22.图1为本实用新型具有三角形排布支撑柱的气液一体式吸液芯结构示意图。
23.图2为本实用新型具有三角形排布支撑柱、丝网编织带毛细结构的气液一体式吸液芯结构示意图。
24.图3为本实用新型正方形排布的具有梯度高度支撑柱的气液一体式吸液芯结构示意图。
25.图4为本实用新型的柔性平板热管的平面结构示意图。
26.图5为本实用新型采用气液一体式吸液芯的柔性平板热管封装工艺图。
27.附图标记说明:
28.1-气液一体式吸液芯、11-毛细结构、111-丝网、112-编织带;12-支撑结构;2-铝塑膜壳体;3-注液管。
具体实施方式
29.针对现有技术中,化学刻蚀、机械加工难以在柔性平板热管壳体表面制作有效蒸汽通道的限制,本实施例提出一种气液一体式吸液芯1,在毛细结构11表面制作多个支撑结构12,从而在支撑结构12间隙中形成蒸汽通道;进一步的,本实施例可以通过调控支撑结构12的高度和间距方便地制作出波纹结构,从而提升平板热管的柔性,降低热管壳体疲劳开裂和产生褶皱的风险。
30.下面来对本实用新型做进一步详细的说明。
31.实施例一:
32.如图1、图4所示,为本实施例具有三角形排布支撑柱的气液一体式吸液芯1,包括毛细结11和支撑结构12,毛细结构11形成液体通道,支撑结构12之间的间隙连通形成蒸汽通道。毛细结构11和支撑结构12通过烧结工艺连接。毛细结构11由3层250目、厚度0.06mm的铜丝网111组成,支撑结构12是铜粉烧结形成的多孔支撑柱。支撑柱的高度为0.6mm,支撑柱的直径为0.6mm,相邻两个支撑柱的中心距为1.6mm。本实施例的具有三角形排布支撑柱的气液一体式吸液芯1的具体制作方法如下:
33.(1)采用石墨板制作模具,石墨板尺寸为200*100*10mm,采用铣削工艺在石墨板表面加工深度0.8mm,直径0.8mm的阵列孔,相邻两个孔的中心距为1.6mm。
34.(2)采用200-300目的铜粉均匀填充石墨模具表面的孔,并采用刮刀清理模具表面多余的铜粉。
35.(3)裁剪3张尺寸200*100mm的250目的铜丝网111,叠放整齐后盖在填充了铜粉的石墨模具表面,并采用石墨板压紧。
36.(4)将多个叠放整齐的石墨模具放入高温烧烧结炉中,在混合气体(95%n2+5%h2)的保护下高温(960℃)烧结30分钟。在保护气氛下冷却后去除石墨模具,即可得到气液一体式吸液芯1。
37.由于铜粉在烧结过程中会出现收缩现象,因此设计石墨模具表面的孔的尺寸略大于最终得到的支撑柱结构尺寸。
38.实施例二:
39.如图2所示,本实施例与实施例一的区别在于,在石墨模具表面加工了微沟槽结构以放置编织带112,最终可以得到具有多层丝网111-编织带112复合毛细结构11的气液一体式吸液芯1。具体如下:
40.(1)采用石墨板制作模具,石墨板尺寸为200*100*10mm,采用铣削工艺在石墨板表面加工深度0.8mm,直径0.8mm的阵列孔,相邻两个孔的中心距为1.6mm。同时,在石墨板表面加工深度0.3mm,宽度2mm的微沟槽。微沟槽的位置根据柔性平板热管的尺寸设计,最终保证2条编织带112分别位于柔性平板热管宽度的三等分点即可。
41.(2)在微沟槽中放置编织带112,并在模具表面覆盖2层330目的铜丝网111,然后采用石墨板压紧;将多个叠放整齐的石墨模具放入高温烧烧结炉中,在混合气体(95%n2+5%h2)的保护下预(650℃)烧结30分钟。在保护气氛下冷却后去除石墨模具,得到丝网111与编织带112的复合毛细结构11。
42.(3)采用300-500目的铜粉均匀填充石墨模具表面的孔,并采用刮刀清理模具表面及微沟槽中多余的铜粉。然后将预烧结的丝网111-编织带112复合毛细芯覆盖在模具表面,确保编织带112位于模具表面的微沟槽中,并采用石墨板压紧。
43.(4)将多个叠放整齐的石墨模具放入高温烧烧结炉中,在混合气体(95%n2+5%h2)的保护下高温(960℃)烧结30分钟。在保护气氛下冷却后去除石墨模具,即可得到气液一体式吸液芯1。
44.实施例三:
45.如图3所示,本实施例与上述实施例的区别在于:本实施例中的支撑柱高度具有均匀的梯度分布,同时支撑柱的排列方式为正方形排列。具体如下:
46.(1)裁剪2张尺寸200*100mm的250目的铜丝网111和1张尺寸200*100mm的330目的铜丝网111,将3张丝网111叠放整齐后用石墨板压紧,并在混合气体(95%n2+5%h2)的保护下高温(960℃)烧结30分钟得到多孔吸液芯。
47.(2)将烧结后的多层丝网111平整放在粉床中,然后采用选择激光融化(slm)技术在丝网111表面沉积加工高度分别为0.4mm和0.6mm的粉柱,柱子直径均为0.6mm,相邻两个间距为1.6mm。
48.(3)沉积完成后取出丝网111,并去除多余的粉末,即可得到具有梯度高度支撑结构12的气液一体式吸液芯1。
49.实施例四:
50.一种采用气液一体式吸液芯的柔性平板热管的制备方法,采用气液一体式吸液芯1、铝塑膜作为壳体,封装制作了柔性平板热管。首先根据柔性平板热管的尺寸需求将气液一体式吸液芯1和铝塑膜裁剪为合适的大小。在本实施例中,气液一体式吸液芯1的毛细结构11为3层250目、厚度0.06mm的铜丝网111,支撑结构12高度为0.6mm,支撑柱的直径为0.6mm,相邻两个支撑柱的中心距为1.6mm。吸液芯的尺寸为20*100mm。铝塑膜尺寸为55*120mm,厚度为0.08mm。
51.如图5所示,采用气液一体式吸液芯1的柔性平板热管封装步骤如下:
52.将铝塑膜沿着长度方向对折,并将气液一体式吸液芯1放入铝塑膜内部。采用热压工艺封装铝塑膜壳体2的三条边,热压温度为150℃,压力为0.5mpa;并且在其中一条封边保留2-3mm宽度的缺口,以便插入注液管3。将注液铜管插入缺口并采用胶水粘接密封。通过注液管3灌注工质,本实施例采用纯水作为工质,灌注量为500ul;将待抽真空的热管放入冰水中冷冻5min,抽真空至5pa以下并对注液管3进行封口处理。在热管壳体多余部分进行二次热压并去除多余部分,得到总厚度约为0.9mm的柔性平板热管。
53.上述实施例为本实用新型较佳的实施方式,但本实用新型的实施方式并不受上述实施例的限制,其他的任何未背离本实用新型的精神实质与原理下所作的改变、修饰、替代、组合、简化,均应为等效的置换方式,都包含在本实用新型的保护范围之内。