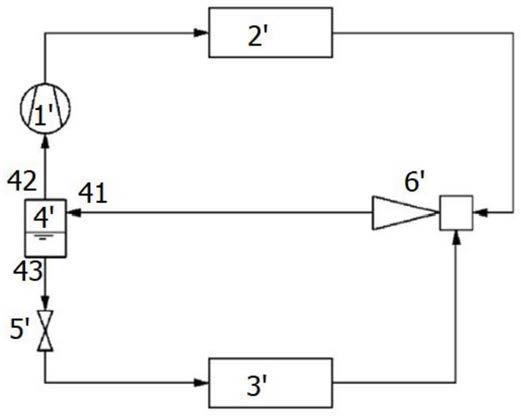
1.本发明属于涂布机和印刷长等相关行业含有机溶剂的废气处理技术领域,具体涉及一种二级制冷液化器及有机溶剂回收方法和系统。
背景技术:2.目前,工业生产排放大量的含有机溶剂的废气,例如印刷和涂布机行业,含有机溶剂的废气排放污染不可小视。涂布印刷过程中会挥发大量有机物,如烃类、醇类、酯类、醚类、腈类等,这些有机溶剂通过空气夹带以废气形式排出。因为环保要求,需要处理达标后排放。从处理工艺上来看,国内处理此类有机废气的方法主要有吸附法、气体膜分离法和冷凝法等,单元组合不同,顺序不同对最终的效果会有完全的不同。气体膜分离技术商业化并不成熟,存在分离后气体浓度低、气体分离膜易堵塞等弊端;吸附法成本较低,而且比较简单,但无法完全吸附;冷凝法要么采用常温水冷却,效率低,要么采用制冷系统,但单机温度单一,多个制冷系统成本高,能耗大。因此当前主流有机溶剂废气处理以吸附法为主处理单元,采用吸附单元处理后,或直接排放,或结合焚烧处理,或结合冷凝法,或结合气体膜分离,但吸附仅是有限吸附,与其它方法结合也是以达到排放标准为目的,一旦标准提高,则该方法很难满足要求。
3.综上,现有印刷和涂布机行业有机溶剂处理方法无法实现有机溶剂全回收,更无法实现有机溶剂再利用。在碳中和背景下,基于环保政策的改变,有机溶剂排放标准提高,指标逐步收紧,需要有机溶剂气体零排放,现有基于吸附单元为主的处理方法不能满足环保政策和要求。
技术实现要素:4.为了解决基于吸附单元为主的处理方法无法实现有机溶剂全回收,更无法实现有机溶剂再利用,无法满足收紧的环保政策和要求的技术问题,本发明提供一种二级制冷液化器。本发明进一步提供采用该二级制冷液化器的有机溶剂回收方法,本发明还提供了采用该二级制冷液化器的有机溶剂回收系统。
5.本发明的技术方案:
6.一种二级制冷液化器,包括压缩机、冷凝器、蒸发器、气液分离器、节流阀和喷射器,所述蒸发器包括一级蒸发器和二级蒸发器,所述一级蒸发器与所述二级蒸发器为并联关系,均位于所述气液分离器与所述喷射器之间,所述气液分离器、压缩机、冷凝器、喷射器和一级蒸发器依次连接成循环回路一,且所述气液分离器、节流阀、二级蒸发器、喷射器和一级蒸发器依次连接成循环回路二;
7.所述喷射器为拉瓦尔喷管,包括喷嘴、混合室和扩散器,所述喷嘴具有制冷剂冷凝液入口和制冷剂蒸发气入口,所述扩散器具有制冷剂出口,所述喷射器的制冷剂冷凝液入口与所述冷凝器出口连通,所述制冷剂蒸发气入口与所述二级蒸发器出口连通,所述制冷剂出口与所述一级蒸发器入口连通,所述一级蒸发器出口与所述气液分离器连通;所述气
液分离器包括制冷剂入口、汽态制冷剂出口和液态制冷剂出口,所述制冷剂入口与所述一级蒸发器出口连通,所述液态制冷剂出口与所述节流阀连接,所述节流阀与所述二级蒸发器入口连通,所述汽态制冷剂出口与所述压缩机入口连通,所述压缩机出口与所述冷凝器入口连通;
8.所述一级蒸发器的制冷温度为-15~-25℃,所述二级蒸发器的制冷温度为-50~-60℃。
9.所述节流阀为电磁膨胀阀。
10.所述制冷剂为可以应对-60℃以下低温的低温制冷剂或者低温可达-60℃以下的环保混合制冷剂。
11.所述压缩机采用低温活塞压缩机,容量为5p/10p或其组合。
12.所述一级蒸发器和二级蒸发器采用翅片管式或缠绕管式蒸发器。
13.所述一级蒸发器布置在下部,所述二级蒸发器布置在上部,所述一级蒸发器与所述二级蒸发器之间具有用于集液与气流分配的弧形筛孔板。
14.一种有机溶剂回收方法,采用所述的一种二级制冷液化器对含有机溶剂废气进行冷凝液化,依次与所述一级蒸发器和二级蒸发器换热分别进行一级制冷和二级制冷,得到冷凝液体,以回收有机溶剂;所述一级蒸发器的制冷温度为-15~-25℃,所述二级蒸发器的制冷温度为-50~-60℃。
15.还包括前处理和后处理,所述前处理包括增压、水冷却、干燥和预冷,所述后处理包括所述冷凝液体除水、很少量未冷凝气体吸附、达标后排空、解吸气体返回至所述增压步骤,重新进行冷凝循环。
16.预冷时,干燥后废气与所述二级制冷液化器的排气换热进行预冷,预冷后的废气的温度为0~5℃。
17.经历所述增压步骤后废气的压力为0.13-0.17mpa。
18.所述水冷却为常温水冷却,冷却后废气的温度降为30~40℃。
19.经所述干燥后废气含水量为0.02~0.03g/m3。
20.一种有机溶剂回收系统,用于实现所述一种有机溶剂回收方法,包括依次连接的增压风机、常温水冷却换热器、干燥器、回热器、二级制冷液化器,还包括液体膜分离器和气体吸附塔;所述回热器包括干燥废气入口和干燥废气出口、未冷凝气体入口和未冷凝气体出口,所述干燥废气入口与所述干燥器的出口连通,所述干燥废气出口与所述二级制冷液化器的一级蒸发器连通,所述二级制冷液化器的二级蒸发器的气体出口连通所述回热器的未冷凝气体入口,所述回热器的未冷凝气体出口连通所述气体吸附塔,吸附塔的解吸气体出口与所述增压风机的入口连通,所述增压风机位于含有机溶剂废气收集管道上;所述二级制冷液化器的冷凝液体出口与所述液体膜分离器连通。
21.所述干燥器为双层干燥剂干燥器,下层干燥剂为耐高温干燥剂,上层干燥剂为高吸水干燥剂,在所述上层干燥剂与所述下层干燥剂之间具有缓冲层。
22.所述回热器采用两股流板式换热器。
23.本发明的有益技术效果:
24.本发明的一种二级制冷液化器,在带喷射器的蒸汽压缩制冷系统的基础上,通过在气液分离器与喷射器之间增设一级蒸发器,原有蒸发器作为二级蒸发器,实现一个制冷
系统二级制冷温度,从而将二级制冷温度集成在一个液化器里面,即用单机实现二级制冷温度。所述一级蒸发器的制冷温度为-15~-25℃,所述二级蒸发器的制冷温度为-50~-60℃。一级制冷通过喷射器喷嘴的节流与二级蒸发器制冷剂蒸汽混合后实现一级制冷温度,而二级制冷温度则是气液分离器中液体进一步通过节流阀节流降温,从而实现二级制冷温度。二级低温制冷剂蒸汽通过与喷射器喷射的制冷剂蒸汽混合调节压缩机吸气压力和温度,实现压缩机的合适压比和压差。
25.优选的,压缩机采用低温活塞压缩机,容量为5p/10p或其组合,可以应对-60℃以下低温,承受较大压比和压差。所述制冷剂为可以应对-60℃以下低温的低温制冷剂或者低温可达-60℃以下的环保混合制冷剂。节流阀采用电磁膨胀阀,根据需要的温度和流量进行自动开度控制,以实现制冷量和制冷温度的匹配与协调。一级蒸发器和二级蒸发器制冷剂相同,因为节流压差不一样,所以可以形成两级不同的温度。
26.在此基础上,本发明通过采用带喷射器的蒸汽压缩制冷液化器实现二级制冷温度,针对有机溶剂气体组分进行匹配,构建二级冷却,从而实现冷凝液化方式对大部分有机溶剂进行冷凝液化回收。通常涂布机或印刷厂使用的有机溶剂都是c4以上有机物,且由多种组分构成,包括c4~c7的轻碳和c8以上称为重碳。由于重碳与轻碳的液化温度相差巨大,重碳组分-20℃左右就液化了,而轻碳需要-50℃左右才能液化。若采用单一制冷温度,则无法实现全部液化。因此通过采用二级制冷将其冷凝下来,一级蒸发器(制冷温度为-15~-25℃)液化回收重碳组分,二级蒸发器(制冷温度为-50~-60℃)液化回收轻碳组分,理论液化比率为百分百,但由于杂质缘故,实际液化比率98%左右;而且二级逐渐降温,不仅实现了温度和冷源的节省,即是节能,而且通过一级蒸发冷凝后降低了二级蒸发器的冷负荷,有利于降低系统容量,节省投资,降低能耗。比两台压缩机两级压缩既少一台压缩机成本,也会降低两级压缩运行成本,更具有商业可行性。
27.本发明的有机溶剂回收方法中,主处理方法是带喷射器的二级制冷液化器实现二级制冷温度。在冷凝前进行前处理,以提高冷凝温度和降低冷负荷。首先,有机溶剂废气首先增压,因为提高气体压力有利于降低其中一些组分的冷凝温度;通过增压后的气体进入常温水冷却换热器,可通过水冷降温到30~40℃之间,同时可除去一部分水分;进一步通过干燥器除去废气中的水分,降低制冷负荷;干燥后的气体通入回热器通过与液化器排气(-50~-60℃)换热进行预冷,温度降到0~5℃后,再送入二级制冷液化器的一级蒸发器,来降低一级蒸发器的制冷量。经一级蒸发器和二级蒸发器的冷凝降温,绝大部分有机溶剂液化。对少量没液化的含有机溶剂的废气进入吸附单元处理,排放的是吸附后的干净空气,解吸气体返回至增压风机,继续/重新参与液化,积累到一定浓度后仍然会液化,实现有机溶剂零排放,避免有机溶剂排放与焚烧排放致癌物;冷凝后液体还含有少量水分,再去液体膜分离器进行水分离,实现有机溶剂液体纯回收。综上,本技术的有机溶剂处理方法是真正意义全回收,零排放,回收后有机溶剂直接再利用,无溶剂气体任何排放。
28.相对于现有技术本发明的优势还在于:
29.1、采用带喷射器的蒸汽压缩制冷循环,循环效率高,同时得到二级制冷温度,对于气体冷却来说,逐渐逐级冷却有利于提高循环效率,延长冷却时间,促进气体液化。
30.2、采用独立设计的双层干燥剂干燥器。以应对偶发的高温(相对常温而言)。
31.3、在液化液体基础上再通过液体分离膜分离,除去水分和co2等,获得纯有机溶
剂,真正实现有机溶剂的回收利用。
32.4、少量没有冷凝下来的有机气体通过吸附塔进行收集,可以实现有机溶剂99%以上的收集捕获的同时,没有有机溶剂的气体排放。解吸出来的气体与废气管气体混合通过增压风机进行二次循环。
附图说明
33.图1为常规带喷射器的蒸汽压缩制冷系统的结构示意图;
[0034]1’‑
压缩机,2
’‑
冷凝器,3
’‑
蒸发器,4
’‑
气液分离器,41
’‑
制冷剂入口,42
’‑
气态制冷剂出口,43
’‑
液态制冷剂出口,5
’‑
节流阀,6
’‑
喷射器;
[0035]
图2为喷射器的实施例的结构示意图;
[0036]
61
’‑
喷嘴,62
’‑
混合室,63
’‑
扩散器,64
’‑
制冷剂冷凝液入口,65
’‑
制冷剂蒸发气入口,66
’‑
制冷剂出口;
[0037]
图3为本发明的一种二级制冷液化器的实施例的结构示意图;
[0038]
1-压缩机,2-冷凝器,31-第一蒸发器,32-第二蒸发器,4-气液分离器,5-节流阀,6-喷射器;
[0039]
图4为本发明的一种有机溶剂回收方法的实施例的流程示意图;
[0040]
图5为本发明的一种有机溶剂回收系统的实施例的示意图;
[0041]
1-压缩机,2-冷凝器,31-第一蒸发器,32-第二蒸发器,4-气液分离器,5-节流阀,6-喷射器,7-增压风机,8-常温水冷却换热器,9-干燥器,10-回热器,11-有机溶剂储罐,12-液体膜分离器,131-1#吸附塔,132-2#吸附塔;
[0042]
图6为双层干燥器的实施例的结构示意图;
[0043]
91-上层干燥剂,92-下层干燥剂,93-缓冲层。
具体实施方式
[0044]
为了便于理解本技术的技术方案,下面将通过具体实施例结合附图1-6详细说明。
[0045]
如图1所示,常规带喷射器的蒸汽压缩制冷系统,包括压缩机1’、冷凝器2’、蒸发器3’、气液分离器4’、节流阀5’和喷射器6’。所述气液分离器4’、压缩机1’、冷凝器2’、喷射器6’和所述气液分离器4’依次连接形成循环回路一,所述气液分离器4’、节流阀5’、蒸发器3’、喷射器6’和所述气液分离器4’依次连接形成循环回路二。如图2所示,所述喷射器6’为由收缩管7’和扩张管8’构成的拉瓦尔喷管,从所述收缩管7’至所述扩张管8’方向依次形成喷嘴61’、混合室62’和扩散器63’,喷嘴61’位于收缩管7’段,混合室62’位于扩张管8’前段,扩散器63’位于扩张管8’后段。所述喷嘴61’的嘴口为制冷剂冷凝液入口64’,所述喷嘴61’的侧方设置制冷剂蒸发气入口65’,所述扩散器63’的末端为制冷剂出口66’。冷凝器2’入口与压缩机1’连通,冷凝器2’出口与喷射器6’的制冷剂冷凝液入口64’连通;蒸发器3’出口与喷射器6’的制冷剂蒸发气入口65’连通,喷射器6’的制冷剂出口66’与气液分离器4’连通;气液分离器4’包括制冷剂入口41’、气态制冷剂出口42’和液态制冷剂出口43’,制冷剂入口41’与喷射器6’的制冷剂出口66’连通,液态制冷剂出口43’与蒸发器3’入口连通,气态制冷剂出口42’与所述压缩机1’入口连通,压缩机1’出口与冷凝器2’入口连通。在气液分离器4’与蒸发器3’之间的管路上设置有节流阀5’。
[0046]
常规带喷射器的蒸汽压缩制冷系统的制冷循环原理为:
[0047]
压缩机1’压缩制冷剂;冷凝器2’对压缩机1’排出的高压制冷剂进行冷却;蒸发器3’蒸发制冷剂;喷射器6’使自冷凝器2’供给的高压制冷剂压力降低和膨胀以抽取在蒸发器3’中已蒸发的汽态制冷剂,这样喷射器6’就将制冷剂的膨胀能量转换为压力能量而提高了压缩机1’的进气压力。具体的,喷射器6’的喷嘴61’将冷凝器2’排出的高压制冷剂的压力能量转变为速度能量,以这种方式,即喷嘴61’对制冷剂进行了等熵降压并使其膨胀。在混合室62’中,从喷嘴61’排出的高速制冷剂流将已在蒸发器3’中蒸发的气态制冷剂抽取入混合室62’,并与气态制冷剂混合。在扩散器63’中,从喷嘴61’排出的制冷剂和从蒸发器3’抽取的制冷剂得到进一步混合,以这种方式,即制冷剂的速度能量转变为压力能量而增加了制冷剂的压力。从扩散器63’排出的制冷剂经气液分离器4’分离后,气态制冷剂输送至压缩机1’,液态制冷剂输送至蒸发器3’,实现一个循环。
[0048]
常规带喷射器的蒸汽压缩制冷系统只能实现单一制冷温度,无法满足含重碳和轻碳组分的有机溶剂废气需要的不同冷凝温度,对有机溶剂的冷凝效率低。
[0049]
如图3所示,本发明的一种二级制冷液化器,在常规带喷射器的蒸汽压缩制冷系统的基础上,在喷射器6和气液分离器4之间增设一级蒸发器31,原蒸发器作为二级蒸发器32,构建两个蒸发温度。其中压缩机1采用低温活塞压缩机,可以应对-60℃以下低温,承受较大压比和压差。所述制冷剂为可以应对-60℃以下低温的低温制冷剂,例如r508b,或者低温可达-60℃以下的环保混合制冷剂,例如基于丙烷的混合物制冷剂。节流阀5采用电磁膨胀阀,根据需要的温度和流量进行自动开度控制,以实现制冷量和制冷温度的匹配与协调。一级蒸发器31和二级蒸发器32中制冷剂相同,因为节流压差不一样,所以可以形成两级不同的温度。本实施例中一级蒸发器31的制冷温度为-15~-25℃以回收重碳组分,二级蒸发器32的制冷温度为-50~-60℃以回收轻碳组分。
[0050]
本发明的一种二级制冷液化器的实施例的结构,包括压缩机1、冷凝器2、蒸发器、气液分离器4、节流阀5和喷射器6,所述蒸发器包括一级蒸发器31和二级蒸发器32,所述一级蒸发器31与所述二级蒸发器32为并联关系,均位于所述气液分离器4与所述喷射器6之间,所述气液分离器4、压缩机1、冷凝器2、喷射器6和一级蒸发器31依次连接成循环回路一,且所述气液分离器4、节流阀5、二级蒸发器32、喷射器6和一级蒸发器31依次连接成循环回路二。如图2所示,所述喷射器6为由收缩管和扩张管构成的拉瓦尔喷管,从所述收缩管至所述扩张管方向依次为喷嘴、混合室和扩散器,所述喷嘴具有制冷剂冷凝液入口和制冷剂蒸发气入口,所述扩散器具有制冷剂出口,所述喷射器6的制冷剂冷凝液入口与所述冷凝器2出口连通,所述制冷剂蒸发气入口与所述二级蒸发器32出口连通,所述制冷剂出口与所述一级蒸发器31入口连通,所述一级蒸发器31出口与所述气液分离器4连通;所述气液分离器4包括制冷剂入口、汽态制冷剂出口和液态制冷剂出口,所述制冷剂入口与所述一级蒸发器31出口连通,所述液态制冷剂出口与所述节流阀5连接,所述节流阀5与所述所述二级蒸发器32入口连通,所述汽态制冷剂出口与所述压缩机1入口连通,所述压缩机1出口与所述冷凝器2入口连通。
[0051]
液化器采用带喷射器的二级蒸汽压缩制冷循环,将一级蒸发器31布置在下部,而二级蒸发器32布置在上部。一级蒸发器31和二级蒸发器32均采用翅片管蒸发器,翅片管换热器在气体流动方向要有一定的高度,以使得气体有足够的停留冷凝时间,有利于气体液
化。一级蒸发器31和二级蒸发器32也可采用缠绕管式蒸发器。
[0052]
一级蒸发器31、二级蒸发器32之间有用于集液和气流分配的弧形筛孔板,通过弧形筛孔板,既实现了通过一级蒸发器31后未冷凝气体的再次均布,也对二级蒸发器32冷凝下来的液体进行了收集,收集后的液体通过液体管流到下部液体槽中与一级蒸发器31冷凝下来的液体混合。
[0053]
上述一种二级制冷液化器的制冷循环原理如下:压缩机1排气通过冷凝器2冷凝后得到常温高压制冷剂液体,通过喷射器6喷射后与吸入的二级蒸发器32制冷剂蒸汽混合后,进入一级蒸发器31制冷,获得一级蒸发温度。蒸发后制冷剂气体进入气液分离器4,而气液分离器4中的制冷剂液体则进一步通过节流阀5后,进入二级蒸发器32,获得二级制冷温度。二级蒸发器32中的制冷剂气体则通过喷射器6的真空带入喷射器6中与冷凝器2出来的常温高压制冷剂喷射后进行混合,混合的制冷剂进入一级蒸发器31。气液分离器4中的制冷剂气体回到压缩机1,完成一个制冷循环。
[0054]
采用上述二级制冷液化器的一种有机溶剂回收方法的实施例,如图4所示,优选的工艺过程如下:
[0055]
s1、有机溶剂废气通过增压风机增压。
[0056]
增压后废气压力为0.13-0.17mpa。提高气体压力有利于降低其中一些组分的冷凝温度,提高液化效果,增压越大,液化效果越好。
[0057]
s2、增压后的废气进入常温水冷却换热器进行水冷却。
[0058]
通过常温水冷却,可除去废气中一部分水分,提高有机溶剂气体份额。例如,涂布机或印刷厂一般排出的气体温度范围是60~80℃,气体中有机溶剂气体体积份额占比不到10%,通过水冷降温到30~40℃之间。
[0059]
s3、通过干燥器除去废气中的水分。
[0060]
经干燥后所述废气的含水量为0.02~0.03g/m3。干燥的目的是为了降低制冷负荷。
[0061]
优选的,干燥器器采用双层干燥剂干燥器,如图6所示,为了应对有机溶剂夹带水蒸气的复杂性,设计双层干燥器,下层干燥剂93采用耐高温干燥剂,如氧化铝等,而上层干燥剂91采用高吸水干燥剂,如硅胶等。上层干燥剂91与下层干燥剂93之间留出缓冲层92,有利于气体重整和均布。
[0062]
同时为了方便干燥剂替换,设计成易拆卸结构,方便罐体内干燥剂的替换。
[0063]
s4、通入回热器与二级制冷液化器的排气换热进行预冷。
[0064]
预冷后温度降到0~5℃。回热器采用两股流板式换热器,实现较高的传热系数和系统紧凑性。
[0065]
s5、预冷后废气送入二级制冷液化器,分别进行一级制冷和二级制冷,得到冷凝液体。
[0066]
液化器中放置有两级制冷蒸发器,其中一级蒸发器制冷温度-15~-25℃之间,可以将c8以上有机溶剂冷凝下来,二级蒸发器制冷温度-50~-60℃,可以将c4~c7有机溶剂冷凝下来。
[0067]
s6、冷凝液体进行液体膜分离,除去水和co2,获得纯有机溶剂。
[0068]
优选的,冷凝液体先进入有机溶剂储罐后再进行液体膜分离。经液体膜分离后的
纯有机溶剂实现再利用。
[0069]
s7、很少量未冷凝气体通入回热器后通过吸附塔吸附达标后排空。
[0070]
通过二级制冷液化器后没有冷凝的少量气体温度还比较低,因而二级制冷液化器的排气与进入液化器的气体通过回热器换热后,再送入吸附塔进行吸附,此时温度0~5℃左右,在吸附器中有利于等温吸附,提高有效吸附量,吸附达标后排空。
[0071]
同时,吸附塔可以根据废气处理量采用一台或者两台甚至更多台。例如,对于连续工作的涂布机或印刷厂常规采用2台吸附塔。
[0072]
s8、解吸气体返回至增压步骤,重新进行冷凝循环。
[0073]
吸附饱和后,吸附器再生,将步骤s3干燥后的废气通入吸附塔吹出吸附的有机气体,将其引入增压步骤,重新进行冷凝循环。
[0074]
采用上述二级制冷液化器的一种有机溶剂回收系统,如图5所示,包括依次连接的增压风机7、常温水冷却换热器8、干燥器9、回热器10、二级制冷液化器,还包括液体膜分离器12和气体吸附塔。所述回热器10包括干燥废气入口和干燥废气出口、未冷凝气体入口和未冷凝气体出口,所述干燥废气入口与所述干燥器9的出口连通,所述干燥废气出口与所述二级制冷液化器的一级蒸发器31连通,所述二级制冷液化器的二级蒸发器32的气体出口连通所述回热器10的未冷凝气体入口,所述回热器10的未冷凝气体出口连通所述气体吸附塔的1#吸附塔131和2#吸附塔132,吸附达标后排空,吸附饱和后,吸附器再生,解吸气体与所述增压风机7的入口连通,所述增压风机7位于含有机溶剂废气收集管道上;所述二级制冷液化器的二级蒸发器32的液体出口与所述液体膜分离器12连通。
[0075]
还可设置有机溶剂储罐11,设置于二级制冷液化器与液体膜分离器12之间,用于暂存冷凝液体。有机溶剂储罐入口连通二级制冷液化器的冷凝液体出口,有机溶剂储罐11出口连通液体膜分离器12的入口。
[0076]
干燥器9采用双层干燥剂干燥器,如图6所示,为了应对有机溶剂夹带水蒸气的复杂性,设计双层干燥器,下层干燥剂93采用耐高温干燥剂,如氧化铝等,而上层干燥剂91采用高吸水干燥剂,如硅胶等。上层干燥剂91与下层干燥剂93之间留出缓冲层92,有利于气体重整和均布。
[0077]
同时为了方便干燥剂替换,设计成易拆卸结构,方便罐体内干燥剂的替换。
[0078]
回热器10采用两股流板式换热器,实现较高的传热系数和系统紧凑性。
[0079]
实施例1
[0080]
采用上述一种有机溶剂回收方法,用于涂布机或印刷厂的含有机溶剂的废气的处理,包括以下步骤:
[0081]
步骤s1、在涂布机或印刷厂废气收集管道上安装轴流增压风机,将废气增压至0.15mpa;
[0082]
步骤s2、增压后的废气进入常温水冷却换热器,将温度由60~80℃降温到30~40℃之间;
[0083]
步骤s3、进一步通过双层干燥器除去废气中的水分至含水量为0.02~0.03g/m3;
[0084]
步骤s4、干燥后废气通入回热器与二级制冷液化器排气换热进行预冷,温度降到0~5℃;
[0085]
步骤s5、预冷后废气送入二级制冷液化器,分别进行一级制冷和二级制冷,得到冷
凝液体;其中一级蒸发器制冷温度-15~-25℃之间,可以将c8以上有机溶剂冷凝下来,二级蒸发器制冷温度-50~-60℃,可以将c4~c7有机溶剂冷凝下来;
[0086]
步骤s6、通过二级制冷液化器后获得的液体进入有机溶剂储罐后再进入液体膜分离器进行液体膜分离,将水和co2除去,获得纯有机溶剂,进行回收再利用;
[0087]
步骤s7、通过二级制冷液化器后很少量未冷凝的气体温度还比较低,与进入液化器的气体通过回热器换热后再送入吸附塔进行吸附,此时温度0~5℃左右,在吸附器中有利于等温吸附,提高有效吸附量,吸附达标后排空。
[0088]
步骤s8、吸附饱和后,吸附器再生,将干燥后的废气通入吸附塔吹出吸附的有机气体,将其引入增压风机之前,重新进行循环。
[0089]
采用以上方法可以实现有机溶剂99%以上的收集捕获,真正意义全回收,零排放,回收后有机溶剂直接再利用。
[0090]
除了用于处理涂布机或印刷厂的含有机溶剂的废气,该方法还可以用于去除任何含c4以上有机溶剂的废气。
[0091]
以上详细描述了本发明的有代表性的实施例和测试例,但是,本发明并不限于上述实施方式中的具体细节,在本发明的技术构思范围内,可以对本发明的技术方案进行多种简单变型,对于本领域技术人员而言显而易见的改变和组合,均属于本发明的保护范围。