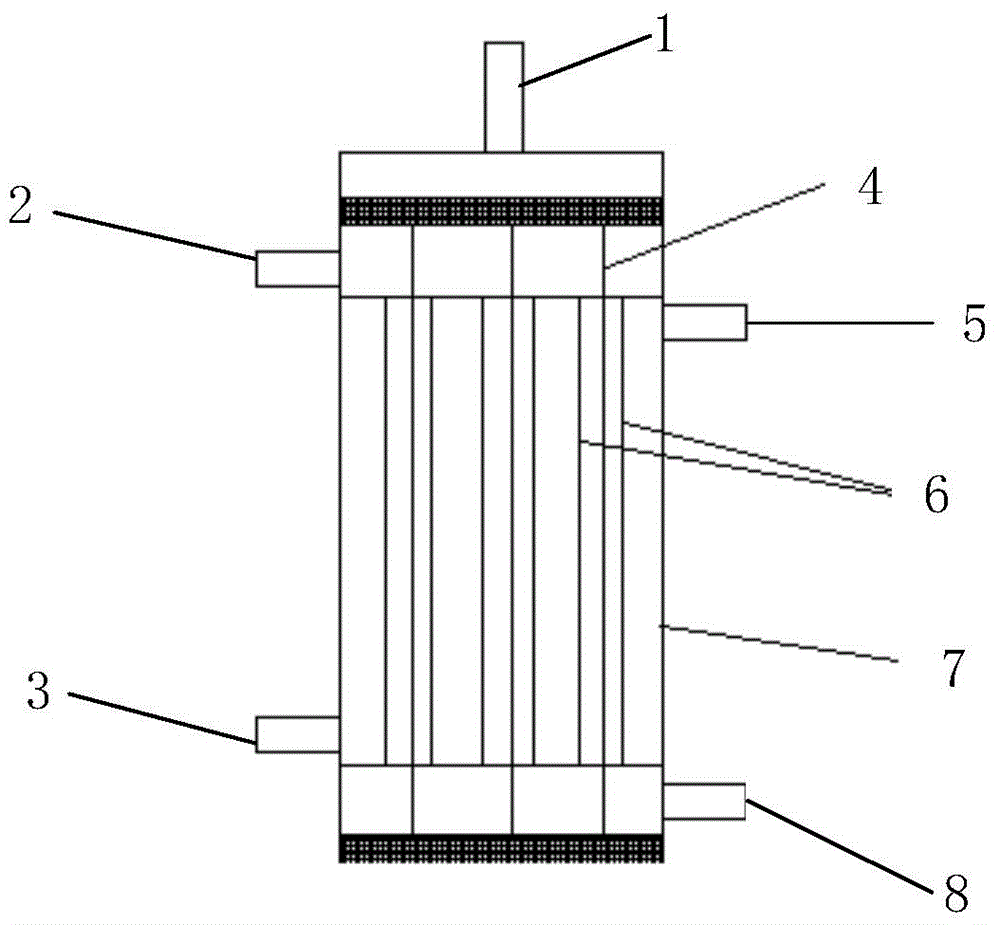
本发明涉及水处理领域的膜蒸馏方法与系统,特别是涉及一种双潜单级循环膜蒸馏方法与系统。
背景技术:
:膜分离法、蒸馏法等物理方法可以有效除盐,但是膜分离法膜成本昂贵,对预处理要求高,且存在严重的资源浪费和二次污染的问题;利用蒸馏法可以回收高盐污水中的无机盐,但设备投资巨大,运行成本较高。膜蒸馏(MembraneDistillation,MD)是一种采用疏水微孔膜以膜两侧蒸汽压力差为传质驱动力的膜分离过程,是传统蒸馏工艺与膜分离技术相结合的一种液体分离技术。在膜蒸馏过程中,疏水微孔膜并不直接参与分离作用,其作用是作为两相间的屏障,选择性完全由汽-液平衡决定。膜蒸馏的传质过程一般包含以下三个步骤:热流体侧汽-液界面处蒸发;蒸汽分子通过疏水膜微孔传递;蒸汽在低温侧冷凝(或被带走)。同其他的分离过程相比,膜蒸馏具有截留率高、操作温度比传统的蒸馏低、操作压力低、能处理高浓度废水等优点;然而膜蒸馏的能耗高依然是阻碍其发展的主要因素,目前对于多效、高效的膜蒸馏工艺方法和系统设计有很多,相同点是都对膜蒸馏产生的二次蒸汽进行回收利用,将冷凝释放的热量用来加热原料液,再利用热的原料液自身的温降进行膜蒸馏的蒸发。这个利用蒸汽冷凝加热原料液的过程可能是在膜组器内部进行,也可能在膜组器外部进行。申请号为200810053905.x一种热回收式减压膜蒸馏组件装置及方法的专利申请公开了由多组间隔排列、相互串联的框式膜蒸馏组件单元和框式热交换组件组成。热料液在膜蒸馏组件单元内蒸发出的蒸汽在热交换组件上冷凝,而达到提高效率的目的。申请号为200910170615.8热回收膜蒸馏装置和系统的专利申请公开了组件中填充可透气的膜蒸馏疏水膜和不透气的热交换膜,运行时疏水膜运行热料液,热交换膜运行冷料液,热料液膜蒸馏的蒸汽会在冷料液的实壁热交换膜上冷凝,而达到提高效率的目的。实壁热交换膜,高分子材料制备的无孔致密中空纤维丝。水和蒸汽都无法通过,可以进行热交换但传热损失大,传热速率慢,传热效果差。申请号为201210072721.4多效膜蒸馏装置与方法的专利申请公开了本发明提供一种多效膜蒸馏装置与方法。蒸馏装置包括主蒸发区、多效蒸发区;其中:主蒸发区设置循环槽以及主蒸发区膜蒸馏组件,循环槽出口连接主蒸发区膜蒸馏组件管程入口,主蒸发区膜蒸馏组件的管程出口连接循环槽入口;多效蒸发区中设置至少一级换热蒸馏装置,每一级换热蒸馏装置包括膜蒸馏组件和换热器,上述每一级膜蒸馏组件与换热器顺次管程串联,各级膜蒸馏组件之间壳程并联。本发明提出多效膜蒸馏方法,将膜蒸馏过程中的水蒸汽冷凝与原水加热过程耦合,回收膜蒸馏过程中水蒸气的相变热。框式组件无法做到蒸发与冷凝的结合,并且根据蒸发原理蒸汽的温度与真空度有关并低于蒸发液,专利申请200810053905.x中公开的的系统工艺的效率也是极其低下。柱式疏水膜和热交换膜混合装填,专利申请200910170615.8中公开的的运行方式也没有做到蒸发与冷凝的结合。如果热交换丝内通蒸汽,腔体通热料液,疏水膜内部抽蒸汽,理论上是勉强可以做到蒸发与冷凝的结合的,但是蒸汽在较长、较纤细的膜丝内的压降会更大,并且高分子的热损失会更大,这种结构热交换丝数量比例要非常大才能提供足够的热交换和均匀的热环境,而热交换丝比例过大会导致有效膜面积减少,以上情况都会导致整体效率低下。专利申请201210072721.4公开的将膜蒸馏过程中的水蒸汽冷凝与原水加热过程耦合,膜蒸馏蒸发过程的热量需求仍然是依靠热料液自身的温度降低提供,膜效率非常低。系统的能量回收在“效数”无限的情况下,即投资成本无限大的情况下,相对于蒸发的能耗仅能降低50%。综上所述,目前膜蒸馏的研究非常多,大多采用对膜蒸馏产生的二次蒸汽进行回收利用,将二次蒸汽冷凝释放的热量用来加热原料液,再利用热的原料液自身的温降进行膜蒸馏的蒸发过程,然而由于组件的放大效应,这种热量回收利用的方法在放大后的热效率极其低下,消耗能量高,限制了膜蒸馏的工业应用。技术实现要素:有鉴于上述现有技术所存在的缺陷,本发明的目的在于,提供一种双潜单级循环膜蒸馏方法与系统,使其提高能效,降低能量消耗,可适用于工业化应用。为了实现上述目的,依据本发明提出的一种双潜单级循环膜蒸馏方法,其中采用双潜膜蒸馏组件,金属管与膜壳之间运行加热蒸汽,疏水膜丝与金属管之间运行热料液,疏水膜丝内部运行膜蒸馏蒸发的二次蒸汽。本发明还可采用以下技术措施进一步实现。前述的双潜单级循环膜蒸馏方法,其中所述生成的二次蒸汽经蒸汽压缩机提高温度和压强后,作为加热蒸汽输入到膜蒸馏组件中向热料液传热。前述的双潜单级循环膜蒸馏方法,其中所述加热蒸汽冷凝成水从冷凝液出口排出后,通过换热器与将要进入料液入口的料液进行换热,从而预热料液。前述的双潜单级循环膜蒸馏方法,其中所述料液进料量为70L/min-150L/min。前述的双潜单级循环膜蒸馏方法,其中系统真空度为0.04MPa-0.08MPa。前述的双潜单级循环膜蒸馏方法,其中所述料液进料温度为50℃-90℃。前述的双潜单级循环膜蒸馏方法,其中蒸汽压缩机提高蒸汽温度5℃-15℃。为了实现上述目的,依据本发明提出的一种双潜单级循环膜蒸馏系统,其中包含双潜蒸馏膜组件、蒸汽压缩机、浓料液储罐、料液储罐、纯水罐及换热器、循环泵、真空泵;所述双潜膜蒸馏组件的二次蒸汽出口连接蒸汽压缩机的入口,加热蒸汽入口连接蒸汽压缩机的出口;料液入口连接换热器然后通过循环泵连接料液储罐或直接连接料液储罐,料液出口直接连接浓料液储罐;冷凝液出口连接换热器然后连接带有真空泵的纯水罐。本发明还可采用以下技术措施进一步实现。前述的双潜单级循环膜蒸馏系统,其中连接料液入口的换热器与连接冷凝器液出口的换热器是同一换热器,可将冷凝水的热量传递至料液。本发明与现有技术相比具有明显的优点和有益效果。借由上述技术方案,本发明的双潜单级循环膜蒸馏方法与系统,至少具有下列优点:一、本发明的双潜单级循环膜蒸馏方法与系统,采用二次蒸汽通过蒸汽压缩机提高温度和压强,作为加热蒸汽循环回到膜组件内膜壳与金属管之间,与原料液蒸发过程换热,冷凝成产品收集。膜蒸馏蒸发过程与加热蒸汽冷凝过程的有效结合,加热蒸汽的冷凝潜热刚好提供膜蒸馏的蒸发潜热需求,避免了庞大的热料液流量和大的热料液温差,可以高效的进行膜蒸馏热量的回收,可以大大提高膜蒸馏系统的效率,降低膜蒸馏运行成本。二、本发明的双潜单级循环膜蒸馏方法与系统,可以减少现有技术热回收系统的多组设备投入,降低设备占地面积。三、本发明的双潜单级循环膜蒸馏方法与系统,膜丝污染物沉积在疏水膜丝的表面,而非疏水膜丝内部,清洗方便,有效降低疏水膜丝的损耗量。四、本发明的双潜单级循环膜蒸馏方法与系统,膜组件膜面积大,密封严密,制造成本低。附图说明图1是本发明双潜单级循环膜蒸馏方法与系统较佳实施例的膜蒸馏组件示意图。图2是本发明双潜单级循环膜蒸馏方法与系统较佳实施例的膜蒸馏组件横切面示意图。图3是本发明双潜单级循环膜蒸馏方法与系统较佳实施例的膜蒸馏系统示意图。1二次蒸汽出口9蒸汽压缩机2料液出口10换热器3冷凝液出口11循环泵4疏水膜丝12真空泵5加热蒸汽入口13浓料液储罐6金属管14料液储罐7膜壳15纯水罐8料液入口具体实施方式为更进一步阐述本发明为达成预定发明目的所采取的技术手段及功效,以下结合附图及较佳实施例,对依据本发明提出的双潜单级循环膜蒸馏方法与系统其具体实施方式、步骤、结构、特征及其功效详细说明。本发明主要涉及以下技术用语:膜蒸馏:利用微孔滤膜形成气液界面,通过热推动进行液体蒸发与难挥发物质分离的过程。疏水膜丝:一种中空纤维膜丝,通过特殊的材料和工艺,使膜呈现疏水性,液态水不会通过,蒸汽可以通过,实现膜蒸馏过程。显热:液体升高或降低温度时交换的热量,如每千克水升高或降低1度时交换的显热为4.2kJ。潜热:液体蒸发或蒸汽冷凝时交换的热量,两者在同等条件下数量相同。每千克水蒸发的潜热为2300kJ左右,是显热的550倍左右,即要想蒸发一千克水需要550千克水降低一度,或55千克水降低10度,或冷凝一千克蒸汽。双潜膜蒸馏组件:一种膜组件结构,将中空纤维膜丝装填在金属管中,膜丝的数量视情况而定,将此种金属管装填在膜壳中,金属管数量视情况而定,由金属管与膜丝形成套管,金属管在膜壳内形成列阵的结构的膜蒸馏组件。经研究发现,现有膜蒸馏技术都是“显热-潜热-显热”的传热方式。如毛细管膜内流动热浓盐水,通过自身的降温,提供热量给蒸发成蒸汽通过膜,蒸汽来到毛细管膜与金属管之间接触冷的金属管被冷却成水,而金属管与膜壳之间的冷却水要通过自身的升温带走这些热量;现有技术都是将膜蒸馏过程的蒸汽冷凝过程与料液预热过程或原料液加热过程集成,其实膜蒸馏过程已经完成,没有与冷凝过程有效结合,无论是在膜组件内部还是膜组件外部,都无法有效的进行能量利用。冷凝的大量潜热用于预热,是无法高效回收的,因为需要大量的冷料液显热接收这部分蒸汽冷凝的潜热。另外,膜蒸馏的蒸发时所需的大量潜热仅仅由外部加热的热料液自身的温降显热提供,同样效率低下。这种技术方法没有将蒸发潜热与冷凝潜热有效结合,能效低,是其无法工业化应用的根本原因。下面通过理论计算来说明采用“潜热-潜热”的处理工艺比采用“显热—潜热—显热”的处理工艺具有更高的能效。“显热—潜热—显热”处理工艺理论产水量:设毛细管膜内流动着1kg/h的70℃的浓盐水;真空度为0.08MPa,温度下降到60℃通量为零,不考虑膜本身的阻力,水的比热4.2kJ/kg*℃,水的汽化热平均2300kJ/kg,则系统的理论最大产水量为:4.2kJ/kg*℃*1kg/h*(70℃-60℃)/2300kJ/kg=0.018kg/h“潜热—潜热”处理工艺理论产水量:设疏水膜丝与金属管之间流动着1kg/h的70℃的浓盐水;真空度0.08MPa,这种方法中浓盐水温度不会降低,不考虑膜本身的阻力,水的汽化热平均2300kJ/kg,则系统的理论最大产水量为:2300kJ/kg*1kg/h/2300kJ/kg=1kg/h综上所述,两种方法的极限理论效率比值为“潜热—潜热”是“显热—潜热—显热”的55.5倍,实际上随着温度的降低膜的产水量会急剧下降,所以综合效率比值会差距更大。在“显热—潜热—显热”的工艺方法中,浓盐水通过膜组件后温度降低了,就需要再加热回来,需要热量为[4.2kJ/kg*℃*1kg/h*(70℃-60℃)]=42kJ/h;冷却水通过自身的升温带走了热量也要释放,但冷却水的温度太低,所以基本上只能排到空气中。“潜热—潜热”的工艺方法中,浓盐水通过膜组件后温度没有变化,不需要额外加热;热量来源是膜蒸馏组件的新生二次蒸汽的冷凝提供,所以对冷却水的需求也很小,排到空气中浪费的热量也微乎其微。目前膜的性能研究已经能够得到产水量较大的膜,但是应用到组件、系统中的时候就效率非常低,主要原因就是“显热—潜热—显热”这种传热方法的先天限制。本发明采用“潜热-潜热”同时进行的工艺,当加热蒸汽在膜壳7与金属管6之间被冷却而形成冷凝水的同时,热量传递给金属管7与疏水膜丝4之间的料液,这些热量刚好使料液中的水蒸发成二次蒸汽透过疏水膜丝4,从疏水膜丝4内被抽出膜组件,可以使膜蒸馏过程中蒸发潜热与冷凝潜热有效结合,并通过提高二次蒸汽温度和压强作为加热蒸汽循环利用,极大的降低膜蒸馏能耗。请参阅图1所示,是本发明双潜单级循环膜蒸馏方法与系统较佳实施例的膜蒸馏组件示意图。膜蒸馏组件具有膜壳7,膜壳7上设置有二次蒸汽出口1、料液出口2、冷凝液出口3、加热蒸汽入口5、料液入口8,膜壳7内设置有金属管6,金属管6的轴线与膜壳7的轴线平行,膜壳7内距离上下端盖一定距离焊接有两个金属多孔板,金属管6两端外边缘与金属多孔板焊接密封,形成金属管内部和金属管外部两部分隔离空间;金属管6内装填不定量的疏水膜丝4,疏水膜丝4轴线与金属管6轴线平行,疏水膜丝4略长于金属管6,疏水膜丝4下端采用封胶技术浇筑密封于膜壳下端盖,上端在距离膜壳上端盖一定距离处浇筑,在疏水膜丝4内与上端盖之间形成互通的空间,膜壳7、金属管6和疏水膜丝4三者相互之前的位置关系如图2所示;加热蒸汽入口5、冷凝液出口3、膜壳7与金属管6之间形成的密闭空间组成加热蒸汽通路;料液入口8、料液出口2、金属管6与疏水膜丝4之间形成的密闭空间组成处理料液通路;二次蒸汽出口1、疏水膜丝4内部空间组成二次蒸汽通路。优选膜壳7为圆柱体型,金属管6在膜壳7内阵列分布,疏水膜丝4上下两端采用复合封胶技术密封。所述复合封胶技术是指配置硬质环氧胶固定膜丝后,再配置软质硅胶浇筑与环氧胶之上,硬质环氧胶保证组件浇筑端的强度,软质硅胶保证膜丝与封胶接触处的安全,给予膜丝足够的保护,防止断丝。疏水膜丝4的尺寸优选为直径0.1mm—10m,长度0.1mm-10m;膜壳7的厚度优选为0.1mm-1m;金属管6直径0.1mm-10m,长度0.1mm-10m;膜壳7内金属管6的数量优选为1-100000根;金属管6内疏水膜丝的数量优选为1-1000000根;疏水膜丝4的封胶厚度优选为0.1mm—1m。膜壳7材质包括但不限于PVC、ABS、不锈钢、PPR、铸铁、铝合金、钛合金、铜等金属或塑料的单一材质或多种组合。金属管6的材质包括但不限于不锈钢、铸铁、铝合金、钛合金、铜等单一材质或多种组合。疏水膜丝4的材质包括但不限于聚醚砜、聚砜、聚偏氟乙烯、聚氯乙烯、纤维素、聚酰胺、聚丙烯、聚乙烯、聚四氟乙烯等单一材质或多种组合。请参阅图3,是本发明双潜单级循环膜蒸馏方法与系统较佳实施例的膜蒸馏系统示意图。双潜单级循环膜蒸馏系统包含一个上述双潜蒸馏膜组件、蒸汽压缩机9、浓料液储罐13、料液储罐14、纯水罐15及换热器10、循环泵11、真空泵12。所述膜蒸馏组件的二次蒸汽出口1连接蒸汽压缩机9的入口,加热蒸汽入口5连接蒸汽压缩机9的出口;料液入口8连接换热器然后通过循环泵11连接料液储罐14或直接连接料液储罐14,料液出口2通过换热器10连接浓料液储罐13或直接连接浓料液储罐13;冷凝液出口3连接换热器10然后连接带有真空泵12的纯水罐15。系统稳定运行时,金属管6与膜壳7之间运行加热蒸汽,疏水膜丝4与金属管6之间运行热料液,疏水膜丝4内部运行膜蒸馏蒸发的水蒸气(二次蒸汽)。加热蒸汽与热料液通过金属管6进行热交换,加热蒸汽冷凝放出大量潜热传递给热料液,热料液经过膜蒸馏过程蒸发成蒸汽通过疏水膜丝4上端的二次蒸汽出口1排出,剩余热料液通过料液出口2进入浓料液储罐13。排出的二次蒸汽通过蒸汽压缩机9提高温度和压强,作为加热蒸汽通过加热蒸汽入口5循环回到膜组件内膜壳7与金属管6之间,与热料液蒸发过程换热,二次蒸汽冷凝成产品水通过冷凝液出口3排出膜蒸馏组件,可通过换热器利用剩余的热量加热原水之后进入纯水罐收集。如此反复,热料液中部分的溶液蒸发成二次蒸汽经过正气压缩机9变成高温蒸汽对原料液进行加热,同时这些二次蒸汽冷凝成水回收;剩余的浓溶液收集在浓料液储罐13中,形成连续不断的单级多效利用自身蒸发蒸汽的膜蒸馏过程,达到高浓料液的浓缩和纯水生产。上述过程中冷凝潜热回收与蒸发潜热供给耦合,二次蒸汽与加热蒸汽耦合,达到降低能耗、降低占地面积、提高膜效率的目的,使膜蒸馏技术的规模化应用成为可能。实施例一:双潜单级膜蒸馏系统A1,组件结构:双潜膜蒸馏组件,组件尺寸:Φ200mm*500mm。膜:中空纤维膜丝。长径比:1.5,装填密度:15%,金属管内径:10mm,膜丝内径:2mm,膜丝壁厚:0.05mm,膜壳厚度2mm、其内填充金属管的数量:100根、材质:钛合金、形状:圆形、排布形式;平均分布。测试条件:热浓盐水温度70℃,料液进料量110L/min,真空度0.06MPa,蒸汽压缩机蒸汽温升10℃。运行条件:膜壳与金属管之间运行加热蒸汽,金属管与膜丝之间运行热浓盐水,膜丝内抽真空、运行新生蒸汽。实施例二:现有常规真空膜蒸馏系统B,组件结构:常规膜蒸馏组件,组件尺寸:Φ200mm*500mm。膜:中空纤维膜丝。膜组件形式:常规,仅有膜丝和膜壳,没有中间的金属管,长径比:1.5,装填密度:15%,膜丝内径:2mm,膜丝壁厚:0.05mm,膜壳厚度2mm。测试条件:热浓盐水温度70℃,料液进料量110L/min,真空度0.06MPa。运行条件:膜壳与膜丝之间运行热浓盐水,膜丝内抽真空、运行新生蒸汽,热浓盐水在膜壳外的换热器中被加热。实施例三:现有混合装填真空膜蒸馏系统C,组件结构:柱式疏水膜和热交换膜混合装填组件,组件尺寸:Φ200mm*500mm。膜:中空纤维膜丝。膜组件形式:混合装填,仅有膜丝和膜壳,没有中间的金属管,长径比:1.5,装填密度:15%,膜丝内径:2mm,膜丝壁厚:0.05mm,膜壳厚度2mm。测试条件:热浓盐水温度70℃,料液进料量110L/min;冷凝水25℃。运行条件:疏水膜丝内运行热浓盐水,热交换膜内运行冷凝水,热浓盐水在膜壳外的换热器中被加热。本发明双潜单级循环膜蒸馏系统A1与现有技术膜蒸馏系统B、C测试结果如表1所示:表1膜蒸馏系统A1、B、C测试结果系统A系统B系统C单只产水量(L/min)553.24.3脱盐率(%)99.899.699.2单只造水比(吨蒸汽/吨水)1.043.42.8吨水能耗(Kwh/吨水)102.8342.5283.7对比表1,我们可以看出,本发明双潜单级循环膜蒸馏系统和方法产水量高,综合耗能低,可以大大降低膜蒸馏的运行成本。实施例四:双潜单级膜蒸馏系统A2,组件结构:双潜膜蒸馏组件,组件尺寸:Φ200mm*500mm。膜:中空纤维膜丝。长径比:1.5,装填密度:15%,金属管内径:10mm,膜丝内径:2mm,膜丝壁厚:0.05mm,膜壳厚度2mm、其内填充金属管的数量:100根、材质:钛合金、形状:圆形、排布形式;平均分布。测试条件:热浓盐水温度90℃,料液进料量110L/min,真空度0.06MPa,蒸汽压缩机蒸汽温升10℃。运行条件:膜壳与金属管之间运行加热蒸汽,金属管与膜丝之间运行热浓盐水,膜丝内抽真空、运行新生蒸汽。实施例五:双潜单级膜蒸馏系统A3,组件结构:双潜膜蒸馏组件,组件尺寸:Φ200mm*500mm。膜:中空纤维膜丝。长径比:1.5,装填密度:15%,金属管内径:10mm,膜丝内径:2mm,膜丝壁厚:0.05mm,膜壳厚度2mm、其内填充金属管的数量:100根、材质:钛合金、形状:圆形、排布形式;平均分布。测试条件:热浓盐水温度50℃,料液进料量110L/min,真空度0.06MPa,蒸汽压缩机蒸汽温升10℃。运行条件:膜壳与金属管之间运行加热蒸汽,金属管与膜丝之间运行热浓盐水,膜丝内抽真空、运行新生蒸汽。实施例六:双潜单级膜蒸馏系统A4,组件结构:双潜膜蒸馏组件,组件尺寸:Φ200mm*500mm。膜:中空纤维膜丝。长径比:1.5,装填密度:15%,金属管内径:10mm,膜丝内径:2mm,膜丝壁厚:0.05mm,膜壳厚度2mm、其内填充金属管的数量:100根、材质:钛合金、形状:圆形、排布形式;平均分布。测试条件:热浓盐水温度70℃,料液进料量150L/min,真空度0.06MPa,蒸汽压缩机蒸汽温升10℃。运行条件:膜壳与金属管之间运行加热蒸汽,金属管与膜丝之间运行热浓盐水,膜丝内抽真空、运行新生蒸汽。实施例七:双潜单级膜蒸馏系统A5,组件结构:双潜膜蒸馏组件,组件尺寸:Φ200mm*500mm。膜:中空纤维膜丝。长径比:1.5,装填密度:15%,金属管内径:10mm,膜丝内径:2mm,膜丝壁厚:0.05mm,膜壳厚度2mm、其内填充金属管的数量:100根、材质:钛合金、形状:圆形、排布形式;平均分布。测试条件:热浓盐水温度70℃,料液进料量70L/min,真空度0.06MPa,蒸汽压缩机蒸汽温升10℃。运行条件:膜壳与金属管之间运行加热蒸汽,金属管与膜丝之间运行热浓盐水,膜丝内抽真空、运行新生蒸汽。实施例八:双潜单级膜蒸馏系统A6,组件结构:双潜膜蒸馏组件,组件尺寸:Φ200mm*500mm。膜:中空纤维膜丝。长径比:1.5,装填密度:15%,金属管内径:10mm,膜丝内径:2mm,膜丝壁厚:0.05mm,膜壳厚度2mm、其内填充金属管的数量:100根、材质:钛合金、形状:圆形、排布形式;平均分布。测试条件:热浓盐水温度70℃,料液进料量110L/min,真空度0.08MPa,蒸汽压缩机蒸汽温升10℃。运行条件:膜壳与金属管之间运行加热蒸汽,金属管与膜丝之间运行热浓盐水,膜丝内抽真空、运行新生蒸汽。实施例九:双潜单级膜蒸馏系统A7,组件结构:双潜膜蒸馏组件,组件尺寸:Φ200mm*500mm。膜:中空纤维膜丝。长径比:1.5,装填密度:15%,金属管内径:10mm,膜丝内径:2mm,膜丝壁厚:0.05mm,膜壳厚度2mm、其内填充金属管的数量:100根、材质:钛合金、形状:圆形、排布形式;平均分布。测试条件:热浓盐水温度70℃,料液进料量110L/min,真空度0.04MPa,蒸汽压缩机蒸汽温升10℃。运行条件:膜壳与金属管之间运行加热蒸汽,金属管与膜丝之间运行热浓盐水,膜丝内抽真空、运行新生蒸汽。实施例十:双潜单级膜蒸馏系统A8,组件结构:双潜膜蒸馏组件,组件尺寸:Φ200mm*500mm。膜:中空纤维膜丝。长径比:1.5,装填密度:15%,金属管内径:10mm,膜丝内径:2mm,膜丝壁厚:0.05mm,膜壳厚度2mm、其内填充金属管的数量:100根、材质:钛合金、形状:圆形、排布形式;平均分布。测试条件:热浓盐水温度70℃,料液进料量110L/min,真空度0.06MPa,蒸汽压缩机蒸汽温升15℃。运行条件:膜壳与金属管之间运行加热蒸汽,金属管与膜丝之间运行热浓盐水,膜丝内抽真空、运行新生蒸汽。实施例十一:双潜单级膜蒸馏系统A9,组件结构:双潜膜蒸馏组件,组件尺寸:Φ200mm*500mm。膜:中空纤维膜丝。长径比:1.5,装填密度:15%,金属管内径:10mm,膜丝内径:2mm,膜丝壁厚:0.05mm,膜壳厚度2mm、其内填充金属管的数量:100根、材质:钛合金、形状:圆形、排布形式;平均分布。测试条件:热浓盐水温度70℃,料液进料量110L/min,真空度0.06MPa,蒸汽压缩机蒸汽温升5℃。运行条件:膜壳与金属管之间运行加热蒸汽,金属管与膜丝之间运行热浓盐水,膜丝内抽真空、运行新生蒸汽。本发明双潜单级循环膜蒸馏系统A1-A9测试结果如表2所示:表2膜蒸馏系统A1-A9测试结果:对比表2,系统参数对单只产水量和吨水能耗有较大的影响,对截留率和造水比影响相对较小。其中单只产水量随着进料温度升高而增大,随着进料量的增大而增大,随着真空度的增大而增大,随着压缩机升温幅度的增大而增大,吨水能耗有相反的趋势。虽然本发明已以较佳实施例揭露如上,然并非用以限定本发明实施的范围,依据本发明的权利要求书及说明内容所作的简单的等效变化与修饰,仍属于本发明技术方案的范围内。当前第1页1 2 3