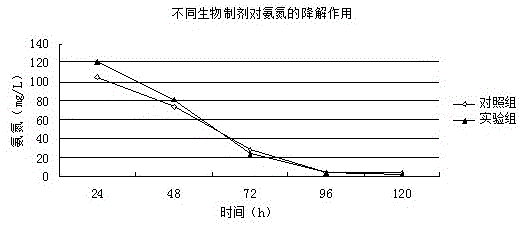
本发明属于生物
技术领域:
,具体涉及用于处理黄原胶发酵工艺废水的生物制剂。
背景技术:
:水是地球上最宝贵的财富,是人类和一切生物生存和发展不能缺少的物质。目前,地球上的水资源可供人们利用的淡水资源为存在于深度800m以下的地下蓄水层中大部分地表水,仅占2.6%,实际上真正可以作为人类生活和生产的水资源只是全球总水量中的极少部分。世界水危机已经严重威胁人类生存,全世界超过五分之一的人将要面临中高度到高度缺水的境况,这种压力正向全球发出缺水警报。我国水资源的总量位居世界第四,但是人均水量仅为世界水量的四分之一,属于缺水的国家之一,再加上水资源在不同季节不同地区的分布不均,以及主要河流、湖泊的水体污染,更加剧了我国的可用水资源危机。南海、黄海、渤海和东海四大海区中的主要污染因子中都包括氨氮、硫化物和活性磷酸盐。近年来,中国海域赤潮发生次数不断增加,赤潮高发区集中在东海海域,其赤潮发生次数和累积发生面积分别占全海域的69%和77%。在渤海湾、浙江中南部、长江口外等海域都有大面积赤潮出现。黄原胶发酵废水来源于黄原胶发酵和提取过程的几道工序,含有大量的cod、氨氮、硫化物、有机物等。废水脱氮方法有多种,如吹脱法、折点氯化法、离子交换法和生物脱氮法。就当前的技术水平和实践情况看来,生物脱氮法是最经济有效可行的。而且,随着生物技术的不断发展,生物脱氮法也逐渐完善,尤其是对当前污染面最大、水质最为复杂的城市污水,生物脱氮法是首选的处理方法。生物脱氮指的是在硝化菌和反硝化菌参与下将氨氮和有机氮最终转化为氮气,从而达到脱氮的目的。脱氮过程包括硝化和反硝化两个反应过程。硝化过程是氨态和有机氮氮在亚硝酸菌和硝酸菌的作用下,被氧化成硝酸盐(no3-n)。反硝化过程是硝酸盐在反硝化细菌的反硝化作用下,被还原为氮气,即脱氮过程结束。申请人之前对黄原胶发酵废水处理进行了长期的研究,中国专利技术“cn104313004a,一种处理黄原胶生产污水的制剂”公开了一种处理黄原胶生产污水的制剂,其为载体和复合微生物菌剂按照2:1的重量比混合制备,所述载体为壳聚糖,该制剂中包含的菌株较多,培养操作工艺比较困难,而且不能重复利用。中国专利技术“cn106882909a,治理黄原胶发酵废水的环保工艺”也使用了生物制剂,该生物制剂由四种菌和载体混合制得,所述载体由沸石、高岭石、淀粉、壳聚糖等原料烧结而成,附着力好,可以悬浮水中,降低了污泥产量,并且可以通过煅烧重复利用,但是该生物制剂无法彻底降解氨氮,水体中含有大量的硝基氮和亚硝基氮。固定化生物技术是20世纪60年代迅速发展起来的一项新技术,它是借助化学或物理的手段将游离细胞或酶定位于限定的空间区域内,使其保持活性并且可以反复利用。20世纪80年代初,国内外逐步开始应用固定化生物技术来处理工业废水和分解难以生物降解的有机污染物,并取得了阶段性进展。近年来,固定化生物技术一直是水处理领域的研究热点。由于固定化生物技术能将微生物或酶的理论停留时间提高到趋于无穷大,即使很高的稀释率也不会引起微生物的冲出现象,即可以通过进水量任意调节和控制容积负荷,这样可以使生产效率大大提高。其优点是:与普通活性污泥法相比处理能力高1~3倍,且出水水质好,抗有机负荷、水力的冲击能力较强,可降低运行费用;在降解有毒污染物方面,抗毒性作用更强。更有前途的是对高效率的混合微生物系混合包埋作为菌剂,能大大提高现存生物处理系统的处理效率。技术实现要素:本发明的目的是解决现有技术的不足,提供了用于处理黄原胶发酵工艺废水的生物制剂,该生物制剂能够彻底处理氨氮等污染物,并且可以重复使用。本发明是通过如下技术方案来实现的:用于处理黄原胶发酵工艺废水的生物制剂,其包括脱氮副球菌、产气荚膜梭菌和伸长盐单胞菌中的任意两种以上的组合。进一步地,所述生物制剂包括脱氮副球菌、产气荚膜梭菌和伸长盐单胞菌。进一步地,所述生物制剂按照如下步骤制备而得:步骤1)将高岭土和膨润土按照2:1的质量比混合,再加入到与装有球磨介质(5mm碳化硅球,料球质量比l:5)的球磨机中球磨30min,80℃烘干15min,然后过100目筛,收集筛下物;步骤2)将聚乙烯醇、凹凸棒土、尿素、水以及筛下物按照3:5:7:70:100的质量比混合均匀,然后投入到造粒机中进行造粒,得到直径为1-mm的湿颗粒,再置于80℃烘干30min,然后置于电阻炉中1000℃煅烧30min,自然冷却后,即得陶粒;步骤3)将菌剂a和陶粒按照1l:2kg的比例进行混合,置于30℃的条件下培养6h,然后依次添加菌剂b、海藻酸钠水溶液,搅拌均匀,再滴加氯化钙水溶液,边滴加边震荡,滴加完毕后,静置12h,制得生物制剂;所述菌剂a、菌剂b、海藻酸钠水溶液以及氯化钙水溶液的体积比为3-4:3-4:1-2:5-7。优选地,所述海藻酸钠水溶液的浓度为40-50g/l。优选地,所述氯化钙水溶液的浓度为20-30g/l。优选地,所述菌剂a为伸长盐单胞菌。优选地,所述伸长盐单胞菌的浓度为(1-5)×108cfu/ml。优选地,所述菌剂b由脱氮副球菌和产气荚膜梭菌按照2-3:1-2的体积比混合得到。优选地,所述脱氮副球菌和产气荚膜梭菌的浓度均为(1-5)×108cfu/ml。优选地,所述脱氮副球菌选用atcc13543;所述产气荚膜梭菌选用atcc10543;所述伸长盐单胞菌选用atcc33173。本发明可通过常规的培养方法得到所需浓度的菌液,此并非本发明的创新点,并不详述。本发明取得的有益效果主要包括但是并不限于几个方面:本发明在载体制备过程中,选用的高岭土和膨润土化学性质较为稳定,本身具有众多壳体孔洞,具有多孔质结构,孔隙率较高,吸附性能强;凹凸棒土可以作为粘合剂,聚乙烯醇作为分散剂,尿素作为造孔剂;将上述物质进行造粒,得到的陶粒强度大,气孔率高,密度和水接近,处于悬浮状态,分散性能好。本发明首先将具备厌氧反硝化功能的伸长盐单胞菌包埋到陶粒孔径的内部,是理想的厌氧环境,适合厌氧反硝化作用;然后将具备好氧硝化功能的脱氮副球菌和产气荚膜梭菌包埋到孔径的外部和表面,是好氧环境,适合好氧硝化作用;避免了好氧条件下反硝化菌与硝化菌争夺溶解氧,也避免了反硝化菌在有机碳源存在下的过度增殖;反硝化菌直接还原硝化反应产生的亚硝酸盐,降低了对氧及有机物的需求;上述方式形成短程良性循环,即氨氮-(硝基态氮+亚硝基态氮)-氮气,从而对氨氮污染物进行了彻底降解。本发明生物制剂处理废水,可以使得装置内维持较高浓度的生物量,从而提高了处理负荷,减少了处理装置体积;生物制剂密度和废水相当,处于悬浮状态;实现同时硝化和反硝化,具有脱氮速度快,效率高,工艺简单,操作控制方便等优点。附图说明图1:不同生物制剂对氨氮的降解作用;图2:不同生物制剂对硝基氮+亚硝基氮的降解作用。具体实施方式本领域技术人员可以借鉴本文内容,适当改进工艺参数实现。特别需要指出的是,所有类似的替换和改动对本领域技术人员来说是显而易见的,它们都被视为包括在本发明。本发明的产品及方法已经通过较佳实施例进行了描述,相关人员明显能在不脱离本
发明内容、精神和范围内对本文所述的产品及方法进行改动或适当变更与组合,来实现和应用本发明技术。为了进一步理解本发明,下面结合实施例对本发明进行详细说明。实施例1用于处理黄原胶发酵工艺废水的生物制剂,其按照如下工艺制备而得:将高岭土和膨润土按照2:1的质量比混合,再加入到与装有球磨介质(5mm碳化硅球,料球质量比l:5)的球磨机中球磨30min,80℃烘干15min,然后过100目筛,收集筛下物;将聚乙烯醇、凹凸棒土、尿素、水以及筛下物按照3:5:7:70:100的质量比混合均匀,然后投入到造粒机中进行造粒,得到直径为1mm的湿颗粒,再置于80℃烘干30min,然后置于电阻炉中1000℃煅烧30min,自然冷却后,即得陶粒;将菌剂a和陶粒按照1l:2kg的比例进行混合,置于30℃的条件下培养6h,然后依次添加菌剂b、40g/l的海藻酸钠水溶液,搅拌均匀,再滴加浓度为20g/l的氯化钙水溶液,边滴加边震荡,滴加完毕后,静置12h,制得生物制剂;所述菌剂a、菌剂b、海藻酸钠水溶液以及氯化钙水溶液的体积比为3:3:1:5。所述菌剂a为伸长盐单胞菌,浓度为1×108cfu/ml;所述菌剂b由脱氮副球菌和产气荚膜梭菌按照2:1的体积比混合得到,所述脱氮副球菌和产气荚膜梭菌的浓度均为1×108cfu/ml。所述脱氮副球菌选用atcc13543;所述产气荚膜梭菌选用atcc10543;所述伸长盐单胞菌选用atcc33173。实施例2用于处理黄原胶发酵工艺废水的生物制剂,其按照如下工艺制备而得:将高岭土和膨润土按照2:1的质量比混合,再加入到与装有球磨介质(5mm碳化硅球,料球质量比l:5)的球磨机中球磨30min,80℃烘干15min,然后过100目筛,收集筛下物;将聚乙烯醇、凹凸棒土、尿素、水以及筛下物按照3:5:7:70:100的质量比混合均匀,然后投入到造粒机中进行造粒,得到直径为2mm的湿颗粒,再置于80℃烘干30min,然后置于电阻炉中1000℃煅烧40min,自然冷却后,即得陶粒;将菌剂a和陶粒按照1l:2kg的比例进行混合,置于30℃的条件下培养6h,然后依次添加菌剂b、50g/l的海藻酸钠水溶液,搅拌均匀,再滴加浓度为30g/l的氯化钙水溶液,边滴加边震荡,滴加完毕后,静置12h,制得生物制剂;所述菌剂a、菌剂b、海藻酸钠水溶液以及氯化钙水溶液的体积比为4:4:2:7。所述菌剂a为伸长盐单胞菌,浓度为3×108cfu/ml;所述菌剂b由脱氮副球菌和产气荚膜梭菌按照3:2的体积比混合得到,所述脱氮副球菌和产气荚膜梭菌的浓度均为2×108cfu/ml。所述脱氮副球菌选用atcc13543;所述产气荚膜梭菌选用atcc10543;所述伸长盐单胞菌选用atcc33173。实施例3本发明陶粒的指标检测。气孔率:利用gb/t1966-1996的煮沸法测定样品的气孔率;机械强度:利用gbtl965/1996多孔陶瓷弯曲强度试验方法进行测定。具体各项指标见表1:表1组别气孔率%机械强度mpa密度g/ml实施例172.814.61.04实施例270.615.31.08可见,本发明陶粒载体的气孔率达到70%以上,孔径为0.1-10微米之间,容易加工,强度大,气孔率高,密度和水接近,处于悬浮状态,在废水中的分散性好,有利于快速吸附处理污染物。实施例4对照组:专利cn106882909a制备的生物修复制剂(采用该专利的实施例1);实验组为本发明实施例1。处理工艺相同:将废水经过过滤网(孔径为5mm)去除大颗粒的固形物,然后进入一次沉淀池进行沉淀处理,然后进入酸碱调节池,调节ph为6.5(各污染物指标为cod1553mg/l,氨氮149mg/l,ss92mg/l);再进入生物反应池,按照每立方米液体添加20g的量添加生物制剂,处理96h,经过出水口排出到消毒池,经过消毒后,排出;所述生物反应池的出水口设置阻止生物制剂流出的筛网;所述筛网的截留粒径为0.5mm。废水批次相同,分别在不同的时间点(24,48,72,96,120h)进行检测硝基氮+亚硝基氮的含量、氨氮的含量,如图1-2所示,随着处理时间的增加,对照组和实验组氨氮的含量迅速降低,而对照组硝基氮+亚硝基氮的含量降幅明显不如实验组,当处理到96h时,对照组和实验组的氨氮含量均降低到10mg/l以下,但是对照组硝基氮+亚硝基氮的含量接近50mg/l,实验组的硝基氮+亚硝基氮的含量仅为2.3mg/l,继续增加处理时间,对处理效果影响不大。可见,实验组的生物制剂更加高效,对氨氮的处理更为彻底,主要原因是陶粒内部的厌氧反硝化菌起到了作用。实施例5本发明生物制剂处理废水效果实例。处理工艺参照实施例4。取样测定cod、氨氮、ss以及硝基氮+亚硝基氮的数据;并且设置对照组,检测微生物制剂中各菌株以及载体的配伍效果:对照组1:脱氮副球菌+产气荚膜梭菌;对照组2:产气荚膜梭菌+伸长盐单胞菌;对照组3:脱氮副球菌+伸长盐单胞菌;实验组:脱氮副球菌+产气荚膜梭菌+伸长盐单胞菌;各组别处理后的cod、氨氮ss以及硝基氮+亚硝基氮的检测结果见表2:表2组别对照组1对照组2对照组3实验组cod(mg/l)97.363.247.512.9nh3-n(mg/l)21.113.210.43.1ss(mg/l)13.415.69.13.8硝基氮+亚硝基氮(mg/l)43.715.611.82.3结论,本发明生物制剂中选用的微生物种类为三种,菌株较少,各菌株之间配伍合理,协同性能好,并且采用特殊的包埋方式,避免了好氧条件下反硝化菌与硝化菌争夺溶解氧,也避免了反硝化菌在有机碳源存在下的过度增殖;反硝化菌直接还原硝化反应产生的硝酸氮和亚硝酸氮,降低了对氧及有机物的需求;上述方式形成短程良性循环,快速高效地对氨氮污染物进行了彻底降解。最后应说明的是:以上实施例仅用以说明本发明的技术方案,而非对其限制;尽管参照前述实施例对本发明进行了详细的说明,本领域的普通技术人员应当理解:其依然可以对前述实施例所记载的技术方案进行修改,或者对其中部分技术特征进行等同替换;而这些修改或者替换,并不使相应技术方案的本质脱离本发明实施例技术方案的精神和范围。当前第1页12