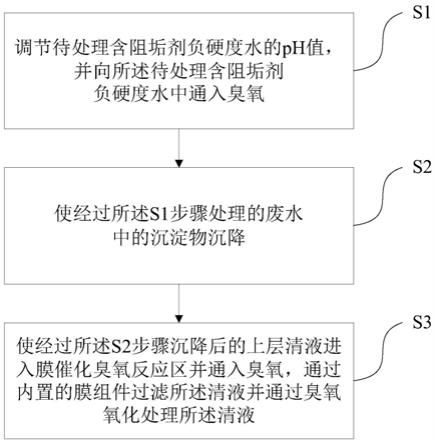
1.本发明属于煤化工废水处理技术领域,涉及一种含阻垢剂负硬度水除硬除浊除有机物的预处理方法及装置。
背景技术:2.2015年国家发布的《现代煤化工建设项目环境准入条件》要求强化节水措施,减少新鲜水用量,目标就是实现“近零排放”或“零排放”。然而煤化工生产过程和辅助工艺过程会产生焦化废水、气化废水、液化废水、循环水排污水、ro浓水、化学水中和废水等。污染物成分复杂,含有难降解的酚类物质,硬度碱度高,含有阻垢剂等,处理难度大。
3.目前,采用污污分治、深度处理、分质回用的废水处理方案,废水处理系统基本包括“一级物化预处理——二级生化处理——三级深度处理及污水回用系统”。为了实现污水回用和“近零排放”,双膜工艺使用较多,其产生的高盐废水,硬度较高,且难降解物质会得到富集;循环水、锅炉水系统中为防止结垢会添加各种阻垢剂(含磷聚合物、聚羧酸类化合物、磺酸类聚合物和绿色阻垢剂等),其对应的外排处理水中仍含有阻垢剂等;使得煤化工废水中产生含阻垢剂的负硬度水,目前常采用高密池加药剂进行除硬处理,但是存在药剂加量大等问题;也有采用电化学除硬的处理方法,存在投资高、运行维护繁琐、阳极损耗等问题。
4.如cn102285722b公开了一种煤气化灰水回用的处理方法,是通过向沉淀池中投加石灰和碳酸钠对灰水进行软化处理。该方法的操作方便,软化效果好,但为考虑絮凝反应过程,从而使反应及沉淀时间长,药剂加量大,软化效率低,产泥量大,沉淀池占地面积大。
5.如cn106830455a公开了一种处理煤气化灰水或黑水的电化学除硬除浊一体化装置及其处理方法和用途,是通过电化学方法在阳极形成铁铝的絮凝核网,起到协同软化的作用,去除大部分硬度和悬浮物,但也存在投资高、运行维护繁琐等缺点。
技术实现要素:6.为克服上述缺陷,本发明提供一种含阻垢剂负硬度水的预处理方法及装置。
7.提供一种含阻垢剂负硬度水的预处理方法,包括:s1,调节待处理含阻垢剂负硬度水的ph值,并向所述待处理含阻垢剂负硬度水中通入臭氧(o3);s2,使经过所述s1步骤处理的水中的沉淀物沉降;s3,使经过所述s2步骤沉降后的上层清液进入膜催化臭氧反应区并通入臭氧,通过内置的膜组件过滤所述清液并通过臭氧氧化处理所述清液。
8.根据本发明一实施方式,在所述s1步骤中,通过采用硫酸、氢氧化钠、氢氧化钾调节所述待处理含阻垢剂负硬度水的ph值为9~11。
9.根据本发明另一实施方式,在所述s1步骤中通入的臭氧相对于所述待处理含阻垢剂负硬度水中阻垢剂,质量比为0.1~0.5。
10.根据本发明另一实施方式,在所述s1步骤中通入的臭氧来自于所述s3步骤中收集的尾气。
11.根据本发明另一实施方式,所述s1步骤中所述待处理含阻垢剂负硬度水的硬度(碳酸钙计)为80~480mg/l,碱度(碳酸钙计)为390~1200mg/l,浊度为2~40ntu,cod为20~150mg/l,调节所述待处理含阻垢剂负硬度水的ph值为9~11,通入的臭氧浓度为0.1~5mg/l,气液比5,处理1小时。
12.根据本发明另一实施方式,在所述s3步骤中,通入的臭氧浓度为5~10mg/l,气液比为5,所述臭氧投加量25~50mg/l,处理1小时。
13.根据本发明另一实施方式,在所述s2步骤中,采用斜板或斜管沉淀方式沉降沉淀物,液面负荷为3~10m3/m2·
h。
14.根据本发明另一实施方式,在所述s3步骤中,所述膜组件为平板陶瓷膜,所述平板陶瓷膜负载有mn氧化物和ce氧化物催化剂。
15.根据本发明另一实施方式,所述平板陶瓷膜孔径为50~200nm,平均孔径为100nm,膜通量为20~120l/m2·
h,优选40~80l/m2·
h;以所述平板陶瓷膜质量为基准,所述催化剂负载量为1%~10%,优选4%~8%,所述催化剂中mn和ce的摩尔比为1:1。
16.根据本发明另一实施方式,还包括:s4,清水反洗和/或化学清洗所述膜组件。
17.还提供一种含阻垢剂负硬度水的预处理装置,包括:预反应单元;沉淀单元,与所述预反应单元相连;及膜催化臭氧反应单元,与所述沉淀单元相连,且内置膜组件。
18.根据本发明一实施方式,所述装置还包括酸碱加药装置及ph监测系统、和臭氧尾气管线及曝气装置,所述酸碱加药装置及ph监测系统、所述臭氧尾气管线及曝气装置分别与所述预反应单元相连,所述臭氧尾气管线另一端与所述膜催化臭氧反应单元相连;优选地,还包括控制模块,所述酸碱加药装置及ph监测系统通过所述控制模块在线监测所述预反应单元,实现酸碱药剂加量控制和ph调节控制;优选地,所述臭氧尾气管线及曝气装置采用聚四氟乙烯材质管线和钛曝气盘或钛曝气棒。
19.根据本发明另一实施方式,所述沉淀单元包括斜管式沉淀装置或斜板式沉淀装置、和溢流管线,所述溢流管线连接所述预反应单元和所述沉淀单元;优选地,所述斜管式沉淀装置或斜板式沉淀装置的材质选自聚乙烯、乙丙共聚、聚氯乙烯或玻璃钢中一种或多种。
20.根据本发明另一实施方式,所述装置还包括臭氧输入管线及曝气装置,所述臭氧输入管线及曝气装置与所述膜催化臭氧反应单元相连;优选地,所述臭氧输入管线及曝气装置采用聚四氟乙烯材质管线和钛曝气盘或钛曝气棒。
21.根据本发明另一实施方式,所述装置还包括膜过滤抽吸泵、反洗泵和废水输送泵,所述膜过滤抽吸泵和反洗泵与所述膜催化臭氧反应单元相连;所述废水输送泵连接所述沉淀单元和所述膜催化臭氧反应单元。
22.根据本发明另一实施方式,所述平板陶瓷膜孔径为50~200nm,平均孔径为100nm,膜通量为20~120l/m2·
h,更优选40~80l/m2·
h;以所述平板陶瓷膜质量为基准,所述催化剂负载量为1%~10%,更优选4%~8%,所述催化剂中mn和ce的摩尔比为1:1。
23.与现有技术相比,本发明充分利用废水中自身碱度,并通过预反应利用臭氧破坏废水的阻垢体系,实现废水中钙镁硬度的高效去除;在反应区,利用陶瓷膜膜表面和“膜孔反应器”效应催化臭氧氧化废水中的有机物,实现去除有机物和提高可生化性的目的。更进一步,在预反应过程中利用反应区内回收的尾气中的残余臭氧,减少臭氧的排放并降低处
理成本。本发明的方法,不加入生石灰、碳酸钠、絮凝剂等,节约成本。并且,本发明的装置和方法很好解决现有技术药剂加量大,产泥量大、投资高等问题。
附图说明
24.通过参照附图详细描述其示例实施方式,本发明的上述和其它特征及优点将变得更加明显。
25.图1是本发明的预处理方法的流程示意图。
26.图2是本发明的预处理装置的结构示意图。
27.其中,附图标记说明如下:
28.1-预反应单元;2-沉淀单元;3-膜催化臭氧反应单元;4-负硬度水进口管线;5-酸碱加药装置及ph监测系统;6-臭氧尾气管线及曝气装置;7-臭氧输入管线及曝气装置;8-膜组件;9-反洗泵;10-清水池;11-膜过滤抽吸泵;12-连接膜过滤抽吸泵出水和预反应单元进水管线;13-废水输送泵;14-预反应单元和沉淀单元的底部管线;15-连接预反应单元溢流口和沉淀单元进水口管线
具体实施方式
29.为更好地说明本发明,便于理解本发明的技术方案,下面对本发明进一步详细说明。但下述的实施例仅仅是本发明的简易例子,并不代表或限制本发明的权利保护范围,本发明保护范围以权利要求书为准。
30.如图1所示,本发明含阻垢剂负硬度水的预处理方法,包括:s1,调节待处理含阻垢剂负硬度水的ph值,并向待处理含阻垢剂负硬度水中通入臭氧(o3);s2,使经过s1步骤处理的水中的沉淀物沉降;s3,使经过s2步骤沉降后的上层清液进入膜催化臭氧反应区并通入臭氧,通过内置的膜组件过滤清液并通过臭氧氧化处理清液。
31.本发明的预处理方法,在s1步骤中,通入的o3破坏废水中的阻垢剂形成的阻垢体系,使体系中的钙、镁离子释放出来,利用废水中自身的碱度和添加的oh根碱度,协同作用使得阻垢体系释放的钙镁离子与碱度结合形成钙镁沉淀,实现废水中钙镁硬度的高效去除。
32.优选,在s1步骤中,通过采用硫酸、氢氧化钠、氢氧化钾调节待处理含阻垢剂负硬度水的ph值为9~11。ph值超出11也可以实现钙镁的沉淀,但在预处理后的处理工序中还需要将废水中的ph降低,增加工序流程且需要加更多的药剂,增加了工艺的成本,优选ph的上限值为11。ph值小于9,则钙镁沉淀的效果不佳。当ph值超出11时,优选采用硫酸调节ph值。从挥发性来说,硫酸相比盐酸、硝酸挥发性更低,相对安全;另外,还存在氯离子会腐蚀金属、硝酸根引起氮含量高等不好影响。当ph值小于9时,优选采用氢氧化钠和/或氢氧化钾调节ph值。相比于碳酸盐、碳酸氢盐来说,氢氧化钠和氢氧化钾调节效率高,可以减少药剂加量,降低成本。在s1步骤中通入的臭氧相对于待处理含阻垢剂负硬度水中阻垢剂,质量比是0.1~0.5。臭氧量不足(质量比小于0.1)时,不能有效地破坏阻垢剂的结构,从而不利于钙镁离子的沉淀。臭氧量超量(质量比大于0.5)时,则会有效氧化破坏阻垢剂结构,但尾气会残留未反应的臭氧造成氧化剂浪费,后续需要加臭氧破坏器来减少臭氧对环境的危害。
33.更进一步,在s1步骤中通入的臭氧来自于s3步骤中收集的尾气,将尾气的臭氧用
于氧化破坏阻垢剂的阻垢体系,因此不用额外设置尾气臭氧破坏器。从而减少预处理过程向环境中释放臭氧的量,同时也减少臭氧的使用量,减少对环境的污染、降低成本。
34.s1步骤中待处理含阻垢剂负硬度水的硬度(碳酸钙计)为80~480mg/l,碱度(碳酸钙计)为390~1200mg/l,浊度为2~40ntu,cod为20~150mg/l,调节待处理含阻垢剂负硬度水的ph值为9~11,通入的臭氧浓度为0.1~5mg/l,气液比5,处理1小时。在s3步骤中,通入的臭氧浓度为5~10mg/l,气液比为5,臭氧投加量25~50mg/l,处理1小时。
35.在s2步骤中,采用斜板或斜管沉淀方式沉降沉淀物,液面负荷为3~10m3/m2·
h。
36.在s3步骤中,膜组件为平板陶瓷膜,平板陶瓷膜负载有mn氧化物和ce氧化物催化剂。平板陶瓷膜孔径为50~200nm,平均孔径为100nm,膜通量为20~120l/m2·
h,优选40~80l/m2·
h;以平板陶瓷膜质量为基准,催化剂负载量为1%~10%,优选4%~8%,催化剂中mn和ce的摩尔比为1:1。利用陶瓷膜膜表面和“膜孔反应器”效应催化臭氧氧化废水中的有机物。同时,臭氧氧化废水中的有机物还可以起到净化陶瓷膜作用,延长陶瓷膜的化学清洗周期。
37.本发明的方法还可以包括s4步骤,清水反洗和/或化学清洗膜组件。可以采用清水反洗、化学清洗相结合的方式。其中,膜抽吸时间:清水反洗时间为5~60min:0.1~2min,优选10~30min:0.5~1min。跨膜压差>0.04mpa时,进行化学清洗,酸洗常用2%的柠檬酸、盐酸或硝酸溶液,碱洗常用0.2%氢氧化钠溶液。
38.本发明还提供一种含阻垢剂负硬度水的预处理装置。如图2所示,本发明的预处理装置包括依次相连的预反应单元1、沉淀单元2和膜催化臭氧反应单元3。
39.待处理的废水通过负硬度水进口管线4进入预反应单元1。在预处理单元调节待处理含阻垢剂负硬度水的ph值,并通过臭氧预处理待处理废水。装置中还可以包括酸碱加药装置及ph监测系统5和臭氧尾气管线及曝气装置6。通过酸碱加药装置及ph监测系统5向预反应单元1中加药,从而控制待处理非水的ph值在预定的范围内。通过臭氧尾气管线及曝气装置6向预反应单元1通入o3。臭氧尾气管线及曝气装置6可以采用聚四氟乙烯材质管线和钛曝气盘或钛曝气棒,通过曝气扰动实现预反应单元1的废水均匀反应。可以采用从膜催化臭氧反应单元3回收的臭氧来预处理待处理的废水。臭氧尾气管线及曝气装置6的臭氧尾气管线可以通过与膜催化臭氧反应单元3相连,来收集膜催化臭氧反应单元3排出的尾气。优选的方案,还可以包括控制模块(图中未示出),酸碱加药装置及ph监测系统5通过控制模块在线监测预反应单元1,实现酸碱药剂加量控制和ph调节控制。
40.在预反应单元1中是利用o3,更优选利用膜催化臭氧反应单元3排出尾气中残余臭氧,破坏废水中阻垢剂的阻垢体系,使得与阻垢剂络合钙镁离子以释放出来,利用废水中自身的碱度和添加的oh根碱度,协同作用使得阻垢体系释放的钙镁离子与碱度结合形成钙镁沉淀,实现废水中钙镁硬度的高效去除。
41.经过预反应单元1预处理后的废水通过连接预反应单元溢流口和沉淀单元进水口管线15进入沉淀单元2中,使得废水中的钙镁沉淀物沉降。沉淀单元2可以采用斜管式沉淀或斜板式沉淀。斜管式沉淀或斜板式沉淀装置的材质可以为聚乙烯、乙丙共聚、聚氯乙烯、玻璃钢或其组合,更优选聚乙烯、聚氯乙烯。作为优选的技术方案,沉淀单元2采用斜板或斜管倾角为60
°
,液面负荷选择3~10m3/m2·
h。在装置中还可以设置管道定期排泥,例如通过预反应单元和沉淀单元的底部管线14定期排出预反应单元1和沉淀单元2底部沉积物,达到
除硬除浊的目的。
42.沉淀单元2的上层清液通过管线进入膜催化臭氧反应单元3,废水输送泵管线上还可以包括废水输送泵13以提供动力。膜催化臭氧反应单元3包括内置的膜组件8和臭氧输入管线及曝气装置7。膜组件8进一步过滤水中的沉淀物,同时膜组件8上负载催化剂催化臭氧氧化有机物的反应。膜组件8可以是平板陶瓷膜,基材可以是al2o3。在平板陶瓷膜的支撑层和膜层都可以负载有催化剂。催化剂可以为mn氧化物和ce氧化物。平板陶瓷膜孔径范围50~200nm,平均孔径为100nm,膜通量为20~120l/m2·
h,更优选40~80l/m2·
h。负载的催化剂中,mn氧化物和ce氧化物催化剂,mn和ce摩尔比为1:1,以al2o3陶瓷膜质量为基准,催化剂负载量为1%~10%,更优选4~8%。通过臭氧输入管线及曝气装置7向膜催化臭氧反应单元3通过臭氧,氧化水中的有机物。作为优选的方案,臭氧输入管线及曝气装置5采用聚四氟乙烯材质管线和钛曝气盘或钛曝气棒,通过曝气扰动实现膜催化臭氧反应单元3内臭氧与有机物的均匀反应。如果经过处理后的水达到标准,通过膜过滤抽吸泵11进入清水池10。如果经过处理后的水未达到标准,通过连接膜过滤抽吸泵出水和预反应单元进水管线12重新回到预反应单元1再次进入处理流程。
43.装置还可以包括清洗膜组件8的部件。例如在装置中增加反洗泵9。当停止处理废水时,利用反洗泵9将清水池10中的清水、碱液或酸液清洗膜催化臭氧反应单元3中的膜组件8。清洗后的膜组件8再次用于废水处理。
44.以下通过实施例和对比例来详细解释说明本发明的发明构思。
45.实施例1-8和对比例1-3处理的表1所述的某煤化工含阻垢剂负硬度水水质情况,待处理废水的情况如下:
46.表1某煤化工含阻垢剂负硬度水水质情况
[0047][0048][0049]
实施例1
[0050]
以批次1水样为处理对象,调节预反应单元的待处理废水的ph为10.5,尾气臭氧平均浓度1mg/l,控制气液比为5,臭氧与阻垢剂质量比为0.25,停留时间为1h。预反应后进入沉淀单元,设定液面负荷为4m3/m2·
h进行沉淀,出水进入膜催化臭氧反应区,选用负载5%的mn氧化物和ce氧化物催化剂,平均孔径为100nm,膜通量为60l/m2·
h,臭氧o3浓度为6mg/l,气液比为5,停留时间1h,经过该工艺处理后,出水总硬度为80mg/l,浊度为1.5ntu,cod为
60mg/l,bod为25mg/l,可生化性b/c为0.42。陶瓷膜平均化学清洗周期为35天,运行1年,化学清洗后的跨膜压差未见明显增大。
[0051]
实施例2
[0052]
以批次1水样为处理对象,调节预反应单元的待处理废水的ph为11,尾气臭氧平均浓度1mg/l,控制气液比为5,臭氧与阻垢剂质量比为0.25,停留时间为1h。预反应后进入沉淀单元,设定液面负荷为4m3/m2·
h进行沉淀,出水进入膜催化臭氧反应区,选用负载5%的mn氧化物和ce氧化物催化剂,平均孔径为100nm,膜通量为60l/m2·
h,臭氧o3浓度为6mg/l,气液比为5,停留时间1h,经过该工艺处理后,出水总硬度为70mg/l,浊度为1ntu,cod为55mg/l,bod为25mg/l,可生化性b/c为0.45。陶瓷膜平均化学清洗周期为40天,运行1年,化学清洗后的跨膜压差未见明显增大。
[0053]
实施例3
[0054]
以批次1水样为处理对象,调节预反应单元的待处理废水的ph为10.5,尾气臭氧平均浓度1.5mg/l,控制气液比为5,臭氧与阻垢剂质量比为0.38,停留时间为1h。预反应后进入沉淀单元,设定液面负荷为4m3/m2·
h进行沉淀,出水进入膜催化臭氧反应区,选用负载5%的mn氧化物和ce氧化物催化剂,平均孔径为100nm,膜通量为60l/m2·
h,臭氧o3浓度为8mg/l,气液比为5,停留时间1h,经过该工艺处理后,出水总硬度为65mg/l,浊度为1ntu,cod为50mg/l,bod为20mg/l,可生化性b/c为0.40。陶瓷膜平均化学清洗周期为45天,运行1.5年,化学清洗后的跨膜压差未见明显增大。
[0055]
实施例4
[0056]
以批次1水样为处理对象,调节预反应单元的待处理废水的ph为10.5,尾气臭氧平均浓度0.8mg/l,控制气液比为5,臭氧与阻垢剂质量比为0.2,停留时间为1h。预反应后进入沉淀单元,设定液面负荷为4m3/m2·
h进行沉淀,出水进入膜催化臭氧反应区,选用负载7%的mn氧化物和ce氧化物催化剂,平均孔径为100nm,膜通量为60l/m2·
h,臭氧o3浓度为6mg/l,气液比为5,停留时间1h,经过该工艺处理后,出水总硬度为85mg/l,浊度为1.5ntu,cod为50mg/l,bod为20mg/l,可生化性b/c为0.40。陶瓷膜平均化学清洗周期为30天,运行1年,化学清洗后的跨膜压差未见明显增大。
[0057]
实施例5
[0058]
以批次2水样为处理对象,调节预反应单元的待处理废水的ph为10.5,尾气臭氧平均浓度1mg/l,控制气液比为5,臭氧与阻垢剂质量比为0.2,停留时间为1h。预反应后进入沉淀单元,设定液面负荷为4m3/m2·
h进行沉淀,出水进入膜催化臭氧反应区,选用负载5%的mn氧化物和ce氧化物催化剂,平均孔径为100nm,膜通量为60l/m2·
h,臭氧o3浓度为6mg/l,气液比为5,停留时间1h,经过该工艺处理后,出水总硬度为90mg/l,浊度为1.5ntu,cod为75mg/l,bod为30mg/l,可生化性b/c为0.40。陶瓷膜平均化学清洗周期为25天,运行1年,化学清洗后的跨膜压差未见明显增大。
[0059]
实施例6
[0060]
以批次2水样为处理对象,调节预反应单元的待处理废水的ph为10.5,尾气臭氧平均浓度1.5mg/l,控制气液比为5,臭氧与阻垢剂质量比为0.3,停留时间为1h。预反应后进入沉淀单元,设定液面负荷为4m3/m2·
h进行沉淀,出水进入膜催化臭氧反应区,选用负载5%的mn氧化物和ce氧化物催化剂,平均孔径为100nm,膜通量为60l/m2·
h,臭氧o3浓度为8mg/
l,气液比为5,停留时间1h,经过该工艺处理后,出水总硬度为75mg/l,浊度为1ntu,cod为65mg/l,bod为25mg/l,可生化性b/c为0.38。陶瓷膜平均化学清洗周期为35天,运行1年,化学清洗后的跨膜压差未见明显增大。
[0061]
实施例7
[0062]
以批次2水样为处理对象,调节预反应单元的待处理废水的ph为10.5,尾气臭氧平均浓度0.8mg/l,控制气液比为5,臭氧与阻垢剂质量比为0.16,停留时间为1h。预反应后进入沉淀单元,设定液面负荷为4m3/m2·
h进行沉淀,出水进入膜催化臭氧反应区,选用负载7%的mn氧化物和ce氧化物催化剂,平均孔径为100nm,膜通量为60l/m2·
h,臭氧o3浓度为6mg/l,气液比为5,停留时间1h,经过该工艺处理后,出水总硬度为80mg/l,浊度为1.5ntu,cod为70mg/l,bod为25mg/l,可生化性b/c为0.36。陶瓷膜平均化学清洗周期为30天,运行1年,化学清洗后的跨膜压差未见明显增大。
[0063]
实施例8
[0064]
以批次2水样为处理对象,调节预反应单元的待处理废水的ph为11,尾气臭氧平均浓度1mg/l,控制气液比为5,臭氧与阻垢剂质量比为0.2,停留时间为1h。预反应后进入沉淀单元,设定液面负荷为4m3/m2·
h进行沉淀,出水进入膜催化臭氧反应区,选用负载7%的mn氧化物和ce氧化物催化剂,平均孔径为100nm,膜通量为60l/m2·
h,臭氧o3浓度为8mg/l,气液比为5,停留时间1h,经过该工艺处理后,出水总硬度为70mg/l,浊度为0.8ntu,cod为60mg/l,bod为20mg/l,可生化性b/c为0.33。陶瓷膜平均化学清洗周期为40天,运行1年,化学清洗后的跨膜压差未见明显增大。
[0065]
对比例1
[0066]
以批次1水样为处理对象,调节预反应单元的待处理废水的ph为10.5,尾气臭氧平均浓度0mg/l,控制气液比为5,臭氧与阻垢剂质量比为0,停留时间为1h。预反应后进入沉淀单元,设定液面负荷为4m3/m2·
h进行沉淀,出水进入膜催化臭氧反应区,选用负载5%的mn氧化物和ce氧化物催化剂,平均孔径为100nm,膜通量为60l/m2·
h,臭氧o3浓度为6mg/l,气液比为5,停留时间1h,经过该工艺处理后,出水总硬度为130mg/l,浊度为2ntu,cod为70mg/l,bod为25mg/l,可生化性b/c为0.36。陶瓷膜平均化学清洗周期为10天,运行6个月,化学清洗后的跨膜压差明显增大。
[0067]
对比例2
[0068]
以批次1水样为处理对象,调节预反应单元的待处理废水的ph为10.5,尾气臭氧平均浓度0mg/l,控制气液比为5,臭氧与阻垢剂质量比为0,停留时间为1h。预反应后进入沉淀单元,设定液面负荷为4m3/m2·
h进行沉淀,出水进入膜催化臭氧反应区,选用负载5%的mn氧化物和ce氧化物催化剂,平均孔径为100nm,膜通量为60l/m2·
h,臭氧o3浓度为0mg/l,气液比为5,停留时间1h,经过该工艺处理后,出水总硬度为240mg/l,浊度为2ntu,cod为78mg/l,bod为8mg/l,可生化性b/c为0.10。陶瓷膜平均化学清洗周期为7天,运行5个月,化学清洗后的跨膜压差明显增大。
[0069]
对比例3
[0070]
以批次1水样为处理对象,预反应单元不调ph值,尾气臭氧平均浓度1mg/l,控制气液比为5,臭氧与阻垢剂质量比为0.25,停留时间为1h。预反应后进入沉淀单元,设定液面负荷为4m3/m2·
h进行沉淀,出水进入膜催化臭氧反应区,选用负载5%的mn氧化物和ce氧化物
催化剂,平均孔径为100nm,膜通量为60l/m2·
h,臭氧o3浓度为6mg/l,气液比为5,停留时间1h,经过该工艺处理后,出水总硬度为260mg/l,浊度为2ntu,cod为65mg/l,bod为25mg/l,可生化性b/c为0.38。陶瓷膜平均化学清洗周期为13天,运行7个月,化学清洗后的跨膜压差明显增大。
[0071]
对比实施例1-8和对比例1-3相比,显著降低了出水的总硬度和浊度。并且经过本发明的方法处理的废水,提供了出水的可生化性。因此,经过本发明预处理的废水可以降低后续处理的成本。
[0072]
本发明有效实现含阻垢剂负硬度水除硬除浊除有机物的预处理的目的,并能保持长周期的运行,与常规工艺相比具有节省药剂,膜清洗周期长,膜运行周期长,减少固废产生,保证煤化工水处理系统的长周期稳定运行,具有重要意义。
[0073]
显然,本发明的上述实施例仅仅是为了清楚说明本发明所作的举例,而并非是对本发明的实施方式的限定。对于所属领域的普通技术人员来说,在上述说明的基础上还可以做出其它不同形式的变化或变动。这里无需也无法对所有的实施方式予以穷举。凡在本发明的精神和原则之内所作的任何修改、等同替换和改进等,均应包含在本发明权利要求的保护范围之内。