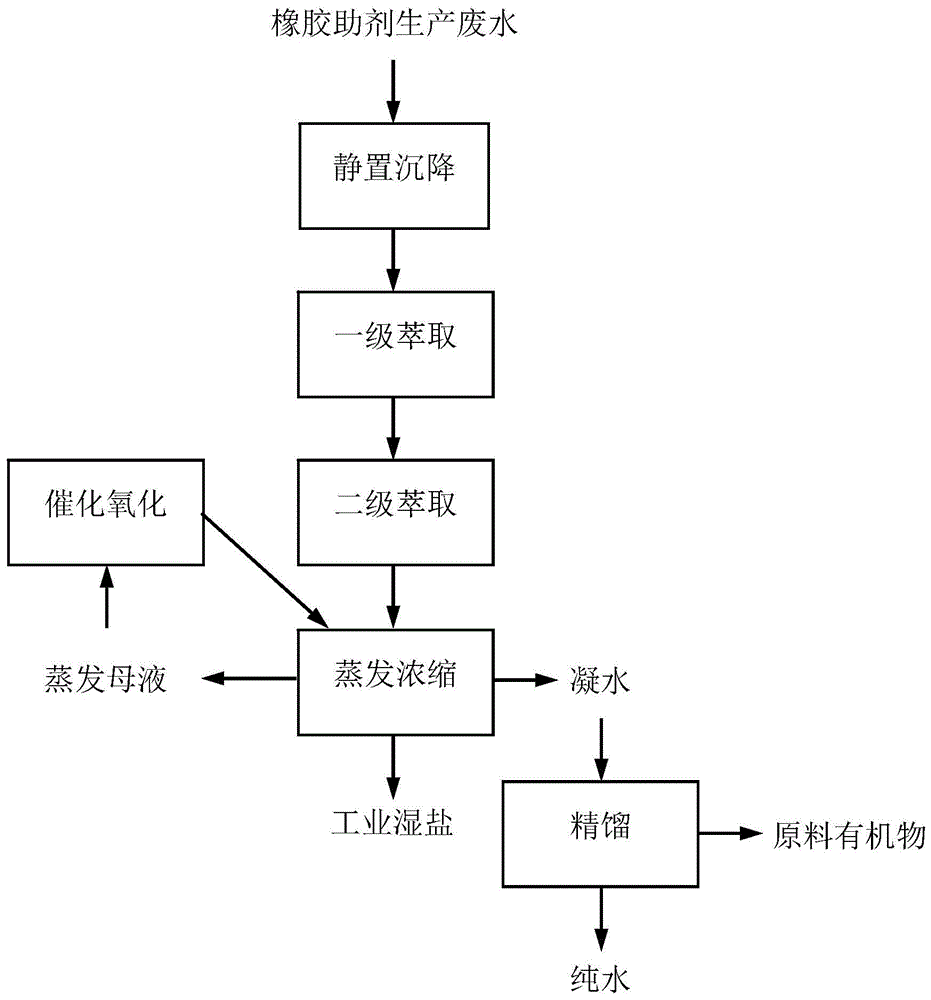
本发明涉及废水处理领域,具体地说,涉及一种橡胶助剂生产废水的处理方法。
背景技术:
:高盐高有机物工业废水是一类常见的难处理废水,一般指总含盐质量分数大于1%、有机物含量高而且成分复杂的废水。高盐高有机物工业废水由于其高盐度会对微生物的生长造成危害,很难直接用生物法来处理;再加上其有机物含量高而且成分复杂,有些有机物的沸点比水低,而有些有机物的沸点比水高,使之更加难以有效处理。高盐高有机物工业废水一旦进入环境,会对周边的生态系统造成极大的破坏,是目前国内外废水处理领域公认的难题。相较于含有其他无机盐的高盐高有机物工业废水,高氯化钠高有机物工业废水是最难处理的品类之一,主要原因在于:1)高氯化钠废水具有很强的腐蚀性,导致设备的耐温防腐投资加大,运行寿命缩短;2)氯化钠的溶解度随温度变化小,采用蒸发浓缩工艺处理会导致蒸水量大,运行能耗高;3)相较于其他无机盐,氯化钠的市场需求有限,且国内副产氯化钠废盐量大,销路极其有限,废盐资源化效果偏差;4)处理高氯化钠高有机物工业废水的现有工艺很难将氯化钠水溶液或氯化钠湿盐中的有机物有效去除,导致下游可应用的领域极其有限。因此,相较于含有其他无机盐的高盐高有机物工业废水,高氯化钠高有机物工业废水不仅进一步提高了处理要求,还大幅提高了处理工艺的开发难度。橡胶助剂生产废水作为一种常见的高氯化钠高有机物工业废水,主要含有苯并噻唑类物质、少量原料有机物、氯化钠等多种污染物。由于该废水含有胺类物质,生化处理需要考虑脱氮,目前常用的脱氮工艺为a/o工艺,即缺氧~好氧的生物处理工艺。由于该废水是工业废水,其中的营养物质不完全,需要额外添加营养物质,例如磷、钾等无机盐。同时还需要曝气,这就需要消耗大量的电能,据不完全统计,污水生化处理的花费中,曝气的费用约占60~80%。同时,生物处理工艺也会产生大量的污泥,如果处理不及时,还会产生二次污染。研究者基于橡胶助剂生产废水进行了大量研究,公开了各种处理方法。例如cn104291506a公开了一种微波强化微电解组合氧化处理橡胶助剂废水的方法,所述处理方法包括酸化反应处理、氧化处理、微电解反应处理、微波反应处理、中和反应处理、分离处理和贮水池处理。虽然所述处理方法可以实现橡胶助剂废水的有效处理,但是没有实现无机盐和原料有机物的回收利用,还会产生大量污泥,造成二次污染,同时具有工艺流程长、运行成本高等缺陷。cn108218146a公开了一种橡胶助剂类高浓度有机废水的处理工艺及处理系统,所述处理工艺包括沉淀处理、催化氧化处理、混凝和絮凝处理、蒸发处理、冷凝水净化处理、净化水深度氧化处理。虽然所述处理工艺可以实现橡胶助剂废水的有效处理,且利于规模化实施,但是没有实现无机盐和原料有机物的回收利用,还具有工艺流程长、运行成本高等缺陷。cn106277519a公开了一种橡胶助剂废水资源化处理系统及方法,所述处理方法包括沉淀气浮、mvr蒸发、树脂吸附、精馏和fenton氧化。虽然所述处理方法能量和药品消耗少,可有效回收橡胶助剂残留原料,但是仍会得到需要排放的废水,没有实现无害化处理和零排放。以上现有技术中虽然公开了针对橡胶助剂生产废水的处理方法,但仍然存在设备投入成本或者工艺运行成本高,有机物去除不充分,无机盐资源没有有效利用等问题。因此,如何开发一种行之有效的橡胶助剂生产废水处理方法,既能去除成分复杂且难处理的有机物,又能实现无机盐资源和原料有机物资源的有效回收利用,是目前亟待解决的问题。技术实现要素:鉴于现有技术中存在的问题,本发明提出一种橡胶助剂生产废水的处理方法,所述处理方法包括除杂、萃取、蒸发浓缩和催化氧化,结合了多操作处理的技术特点,并通过各步骤间相互协同作用,可以进行无机盐和有机物的分步骤分离,实现无机盐资源和原料有机物资源的有效回收利用,最终实现了橡胶助剂生产废水的无害化处理和零排放。为达此目的,本发明采用以下技术方案:本发明的目的之一在于提供一种橡胶助剂生产废水的处理方法,所述处理方法包括如下步骤:(1)将橡胶助剂生产废水进行除杂;(2)将步骤(1)除杂后的废水进行萃取;(3)将步骤(2)萃取后的废水进行蒸发浓缩,过滤得到工业湿盐和蒸发母液;(4)将步骤(3)得到的蒸发母液进行催化氧化处理,得到的处理液回用于步骤(3)所述蒸发浓缩。本发明中所提及的橡胶助剂生产废水是指cod含量在1000~100000mg/l、无机盐含量在15~300g/l的废水,尤其是指cod含量在5000~100000mg/l、无机盐含量在50~250g/l的废水。其中,所述cod含量具体可以是1000mg/l、3000mg/l、5000mg/l、7000mg/l、10000mg/l、25000mg/l、30000mg/l、50000mg/l、70000mg/l或100000mg/l等,所述无机盐含量具体可以是15g/l、25g/l、50g/l、70g/l、100g/l、130g/l、150g/l、180g/l、200g/l、250g/l或300g/l等,但并不仅限于所列举的数值,以上数值范围内其他未列举的数值同样适用。本发明中所提供的处理方法将除杂、萃取、蒸发浓缩和催化氧化相结合,各步骤间通过相互协同作用,可以实现无机盐和有机物的有效分离,不仅可以得到满足工业标准的无机盐,将其用于配制离子膜烧碱行业要求的原料盐水,还可将凝水精馏得到的原料有机物进行回收利用,真正实现无机盐资源和原料有机物资源的有效回收利用,保证了橡胶助剂生产废水的无害化处理和零排放。作为本发明优选的技术方案,步骤(1)所述除杂包括沉降、离心、过滤或膜过滤中的任意一种或至少两种的组合,所述组合典型但非限制性的实例是:沉降和过滤的组合,沉降和膜过滤的组合或离心和过滤的组合等。优选地,步骤(1)所述除杂为静置沉降并过滤。优选地,所述静置沉降的时间为0.5~100h,例如0.5h、1h、5h、10h、24h、30h、36h、48h、60h、70h或100h等,但并不仅限于所列举的数值,该数值范围内其他未列举的数值同样适用,优选为24~48h。优选地,所述过滤的过滤孔径为10~15000目,例如10目、30目、50目、100目、300目、500目、2000目、5000目、10000目或15000目等,但并不仅限于所列举的数值,该数值范围内其他未列举的数值同样适用,优选为50~500目。本发明中所提供的处理方法通过静置沉降和过滤操作,可以有效去除橡胶助剂生产废水中的悬浮物,从而为后续的萃取创造良好的条件。作为本发明优选的技术方案,步骤(2)所述萃取为至少一级萃取。优选地,步骤(2)所述萃取为两级萃取,包括一级萃取和二级萃取。优选地,所述一级萃取的ph环境为1~5,例如1、2、3、4或5等,但并不仅限于所列举的数值,该数值范围内其他未列举的数值同样适用,优选为1~3。优选地,所述一级萃取剂和步骤(1)过滤后废水的体积比为0.01~0.3:1,例如0.01:1、0.05:1、0.1:1、0.13:1、0.15:1、0.2:1、0.25:1或0.3:1等,但并不仅限于所列举的数值,该数值范围内其他未列举的数值同样适用,优选为0.1~0.2:1。优选地,所述二级萃取的ph环境为7~11,例如7、8、9、10或11等,但并不仅限于所列举的数值,该数值范围内其他未列举的数值同样适用,优选为9~11。优选地,所述二级萃取剂和一次萃取后废水的体积比为0.01~0.3:1,例如0.01:1、0.05:1、0.1:1、0.13:1、0.15:1、0.2:1、0.25:1或0.3:1等,但并不仅限于所列举的数值,该数值范围内其他未列举的数值同样适用,优选为0.1~0.2:1。本发明中所提供的处理方法采用了至少一级的萃取处理,可以根据橡胶助剂生产废水的具体组成进行萃取级数的调整。本发明所述两级萃取,包括一级萃取和二级萃取的操作,先通过一级萃取除去废水中的大分子有机物,再通过二级萃取除去废水中的有机胺类化合物,从而实现协同萃取作用下有机物的高效去除,并为后续蒸发浓缩大幅度提高无机盐的提取率提供有利条件。作为本发明优选的技术方案,步骤(3)所述蒸发浓缩的浓缩比例为40~90%,例如40%、50%、65%、70%、80%、85%或90%等,但并不仅限于所列举的数值,该数值范围内其他未列举的数值同样适用,优选为80~85%。优选地,步骤(3)所述蒸发浓缩的蒸发方式为简单蒸发、多效蒸发或mvr蒸发中的任意一种或至少两种的组合,所述组合典型但非限制性的实例是:简单蒸发和多效蒸发的组合,简单蒸发和mvr蒸发的组合或多效蒸发和mvr蒸发的组合等,优选为mvr蒸发。优选地,步骤(3)所述蒸发浓缩得到的凝水进行精馏处理。本发明中所述精馏处理通过对不同温度下馏分的回收,可以实现不同原料有机物的分离,并将这些原料有机物回用到生产过程中。同时,精馏过后的母液可以作为纯水回用到生产过程中。作为本发明优选的技术方案,步骤(4)所述催化氧化的ph环境为1~6,例如1、2、3、4、5或6等,但并不仅限于所列举的数值,该数值范围内其他未列举的数值同样适用,优选为3~4。优选地,所述ph环境的调节剂为盐酸。优选地,所述盐酸的质量浓度为1~35.5%,例如1%、5%、10%、18%、28%、31%、33%或35.5%等,但并不仅限于所列举的数值,该数值范围内其他未列举的数值同样适用,优选为28~31%。作为本发明优选的技术方案,步骤(4)所述催化氧化采用的催化剂为可溶性过渡金属氯化物。优选地,所述催化剂为氯化铁、氯化钴、氯化铜、氯化锌或氯化锰中的任意一种或至少两种的混合物,所述混合物典型但非限制性的实例是:氯化铁和氯化钴的混合物,氯化铁和氯化铜的混合物,氯化锌和氯化锰的混合物或氯化钴和氯化锰的混合物等。优选地,所述催化剂与步骤(3)得到的蒸发母液的质量比为1:100~100000,例如1:100、1:500、1:1000、1:3000、1:5000、1:7000、1:10000、1:20000、1:50000、1:80000或1:100000等,但并不仅限于所列举的数值,该数值范围内其他未列举的数值同样适用,优选为1:5000~20000。作为本发明优选的技术方案,步骤(4)所述催化氧化采用的氧化剂为空气、氧气、双氧水、次氯酸钠或臭氧中的任意一种或至少两种的混合物,所述混合物典型但非限制性的实例是:空气和氧气的混合物,空气和双氧水的混合物,空气和次氯酸钠的混合物、双氧水和次氯酸钠的混合物、空气和臭氧的混合物或氧气和臭氧的混合物等,优选为空气和氧气的混合物。优选地,所述氧化剂中有效氧与步骤(3)得到的蒸发母液中cod含量的质量比为1~20:1,例如1:1、5:1、7:1、10:1、15:1、18:1或20:1等,但并不仅限于所列举的数值,该数值范围内其他未列举的数值同样适用,优选为1~10:1。作为本发明优选的技术方案,步骤(4)所述催化氧化的反应温度为50~500℃,例如50℃、100℃、150℃、200℃、300℃、400℃或500℃等,但并不仅限于所列举的数值,该数值范围内其他未列举的数值同样适用,优选为200~300℃。优选地,步骤(4)所述催化氧化的反应压力为表压0~100mpa,例如0mpa、2mpa、4mpa、6mpa、10mpa、20mpa、30mpa、50mpa或100mpa等,但并不仅限于所列举的数值,该数值范围内其他未列举的数值同样适用,优选为表压2~6mpa。优选地,步骤(4)所述催化氧化的反应停留时间为0.001~10h,例如0.001h、0.005h、0.01h、0.05h、0.1h、0.5h、1h、5h或10h等,但并不仅限于所列举的数值,该数值范围内其他未列举的数值同样适用,优选为0.01~1h。优选地,步骤(4)所述催化氧化的反应器为釜式反应器、管式反应器、塔式反应器或微通道反应器中的任意一种或至少两种的组合,所述组合典型但非限制性的实例是:釜式反应器和管式反应器的组合,管式反应器和塔式反应器的组合,塔式反应器和微通道反应器的组合或微通道反应器和釜式反应器的组合等,优选为微通道反应器。本发明中所提供的处理方法采用催化氧化来处理蒸发母液,可以在催化剂作用下加速氧化和分解有机物,从而实现了蒸发母液中有机物的高效去除。同时,将去除有机物后的蒸发母液回用至蒸发浓缩步骤,保证了蒸发母液中的高浓度无机盐的回收利用,真正实现了无机盐资源的充分回收。作为本发明优选的技术方案,所述处理方法包括如下步骤:(1)将橡胶助剂生产废水静置沉降0.5~100h,然后以过滤孔径为10~15000目进行过滤;(2)将步骤(1)过滤后的废水进行一级萃取和二级萃取,其中一级萃取的ph环境为1~5,且所述一级萃取剂和步骤(1)过滤后废水的体积比为0.01~0.3:1;二级萃取的ph环境为7~11,且所述二级萃取剂和一次萃取后废水的体积比为0.01~0.3:1;(3)将步骤(2)萃取后的废水进行蒸发浓缩,浓缩比例为40~90%,蒸发方式为mvr蒸发,过滤得到工业湿盐和蒸发母液;其中,步骤(3)所述蒸发浓缩得到的凝水进行精馏处理;(4)将步骤(3)得到的蒸发母液进行催化氧化处理,采用质量浓度为1~35.5%的盐酸调节至ph环境为1~6,加入催化剂和氧化剂在50~500℃和表压0~100mpa下进行催化氧化,反应停留时间为0.001~10h,将得到的处理液回用于步骤(3)所述蒸发浓缩。本发明的目的之二在于提供一种采用目的之一所述处理方法得到的工业湿盐,将其用于配制满足离子膜烧碱行业要求的原料盐水。与现有技术相比,本发明至少具有以下有益效果:(1)本发明所述橡胶助剂生产废水处理方法的适用范围广,可以用于处理cod含量在1000~100000mg/l、无机盐含量在15~300g/l的橡胶助剂生产废水;(2)本发明所述处理方法得到的工业湿盐满足国家标准gb/t5462-2015中的有关规定,可以用于配制满足离子膜烧碱行业要求的原料盐水;(3)本发明所述处理方法可以将废水中的原料有机物进行回收利用;(4)本发明所述处理方法具有操作简单、反应周期短、能耗较低的优点,并且不会产生二次污染,基本上实现了100%回用和无害化处理。附图说明图1是本发明提供的橡胶助剂生产废水处理方法的流程图。具体实施方式下面结合附图并通过具体实施方式来进一步说明本发明的技术方案。本领域技术人员应该明了,所述实施例仅仅是帮助理解本发明,不应视为对本发明的具体限制。本发明提供的橡胶助剂生产废水的处理方法,其流程如图1所示,具体包括如下步骤:(1)将橡胶助剂生产废水静置沉降并过滤;(2)将步骤(1)过滤后的废水进行一级萃取和二级萃取;(3)将步骤(2)萃取后的废水进行蒸发浓缩,过滤得到工业湿盐和蒸发母液;其中,步骤(3)所述蒸发浓缩得到的凝水进行精馏处理,得到原料有机物和纯水;(4)将步骤(3)得到的蒸发母液进行催化氧化处理,得到的处理液回用于步骤(3)所述蒸发浓缩。为便于理解本发明,本发明列举实施例如下。实施例1一种cod含量为35000mg/l、氯化钠含量为230g/l的橡胶防老剂tmq生产废水,其处理方法包括如下步骤:(1)将橡胶防老剂tmq生产废水静置沉降24h,然后以过滤孔径为500目进行过滤;(2)将步骤(1)过滤后的废水进行一级萃取,其中一级萃取的ph环境为1,一级萃取剂为萃取剂甲苯,且所述一级萃取剂和步骤(1)过滤后废水的体积比为0.3:1;(3)将步骤(2)萃取后的废水进行蒸发浓缩,浓缩比例为85%,蒸发方式为mvr蒸发,过滤得到工业湿盐和蒸发母液;其中,步骤(3)所述蒸发浓缩得到的凝水进行精馏处理,50~70℃馏分得到丙酮,70~90℃馏分得到苯胺,将精馏母液收集作为纯水;(4)将步骤(3)得到的蒸发母液进行催化氧化处理,采用质量浓度为28%的盐酸调节至ph环境为3,加入氯化铜作为催化剂,且催化剂与步骤(3)得到的蒸发母液的质量比为1:20000,搅拌均匀后泵入微通道反应器中,在200℃和表压6mpa下,用空气作为氧化剂进行催化氧化反应,空气中有效氧与步骤(3)得到的蒸发母液中cod含量的质量比为10:1,反应停留时间为1h,将得到的处理液回用于步骤(3)所述蒸发浓缩。实施例2一种cod含量为33000mg/l、氯化钠含量为105g/l的橡胶硫化促进剂dcbs生产废水,其处理方法包括如下步骤:(1)将橡胶硫化促进剂dcbs生产废水在30℃下静置沉降10h,然后以过滤孔径为1500目进行过滤;(2)将步骤(1)过滤后的废水进行一级萃取和二级萃取,其中一级萃取的ph环境为3,一级萃取剂为萃取剂异丙醇,且所述一级萃取剂和步骤(1)过滤后废水的体积比为0.15:1;二级萃取的ph环境为8,二级萃取剂为二环己胺,且所述二级萃取剂和一次萃取后废水的体积比为0.2:1;(3)将步骤(2)萃取后的废水进行蒸发浓缩,浓缩比例为90%,蒸发方式为mvr蒸发,过滤得到工业湿盐和蒸发母液;其中,步骤(3)所述蒸发浓缩得到的凝水进行精馏处理,50~60℃馏分得到异丙醇,60~95℃馏分得到二环己胺,将精馏母液收集作为纯水;(4)将步骤(3)得到的蒸发母液进行催化氧化处理,采用质量浓度为30%的盐酸调节至ph环境为5,加入质量比为5:1的氯化铜和氯化钴作为催化剂,且催化剂与步骤(3)得到的蒸发母液的质量比为1:10000,搅拌均匀后泵入微通道反应器中,在500℃和表压10mpa下,用氧气作为氧化剂进行催化氧化反应,空气中有效氧与步骤(3)得到的蒸发母液中cod含量的质量比为15:1,反应停留时间为0.01h,将得到的处理液回用于步骤(3)所述蒸发浓缩。实施例3一种cod含量为30000mg/l、氯化钠含量为153g/l的橡胶促进剂cbs生产废水,其处理方法包括如下步骤:(1)将橡胶促进剂cbs生产废水在10℃下静置沉降60h,然后以过滤孔径为5000目进行过滤;(2)将步骤(1)过滤后的废水进行一级萃取和二级萃取,其中一级萃取的ph环境为5,一级萃取剂为萃取剂环己胺,且所述一级萃取剂和步骤(1)过滤后废水的体积比为0.25:1;二级萃取的ph环境为9,二级萃取剂为sflj-336,且所述二级萃取剂和一次萃取后废水的体积比为0.1:1;(3)将步骤(2)萃取后的废水进行蒸发浓缩,浓缩比例为75%,蒸发方式为mvr蒸发,过滤得到工业湿盐和蒸发母液;其中,步骤(3)所述蒸发浓缩得到的凝水进行精馏处理,6075℃馏分得到环己胺,75~90℃馏分得到甲苯,将精馏母液收集作为纯水;(4)将步骤(3)得到的蒸发母液进行催化氧化处理,采用质量浓度为31%的盐酸调节至ph环境为2,加入质量比为1:1的氯化铜和氯化钴作为催化剂,且催化剂与步骤(3)得到的蒸发母液的质量比为1:100000,搅拌均匀后泵入微通道反应器中,在300℃和表压4mpa下,用氧气作为氧化剂进行催化氧化反应,空气中有效氧与步骤(3)得到的蒸发母液中cod含量的质量比为2:1,反应停留时间为1h,将得到的处理液回用于步骤(3)所述蒸发浓缩。实施例4一种cod含量为25000mg/l、氯化钠含量为250g/l的橡胶促进剂tbbs生产废水,其处理方法包括如下步骤:(1)将橡胶促进剂tbbs生产废水静置沉降48h,然后以过滤孔径为500目进行过滤;(2)将步骤(1)过滤后的废水进行一级萃取和二级萃取,其中一级萃取的ph环境为2,一级萃取剂为萃取剂flj-332,且所述一级萃取剂和步骤(1)过滤后废水的体积比为0.2:1;二级萃取的ph环境为11,二级萃取剂为sflj-336,且所述二级萃取剂和一次萃取后废水的体积比为0.15:1;(3)将步骤(2)萃取后的废水进行蒸发浓缩,浓缩比例为80%,蒸发方式为mvr蒸发,过滤得到工业湿盐和蒸发母液;其中,步骤(3)所述蒸发浓缩得到的凝水进行精馏处理,50~70℃馏分得到叔丁胺,70~85℃馏分得到甲苯,将精馏母液收集作为纯水;(4)将步骤(3)得到的蒸发母液进行催化氧化处理,采用质量浓度为10%的盐酸调节至ph环境为4,加入质量比为20:1:1的氯化铜、氯化铁和氯化钴作为催化剂,且催化剂与步骤(3)得到的蒸发母液的质量比为1:15000,搅拌均匀后泵入微通道反应器中,在260℃和表压5.5mpa下,用空气作为氧化剂进行催化氧化反应,空气中有效氧与步骤(3)得到的蒸发母液中cod含量的质量比为5:1,反应停留时间为0.2h,将得到的处理液回用于步骤(3)所述蒸发浓缩。实施例5本实施例提供一种cod含量为25000mg/l、氯化钠含量为250g/l的橡胶促进剂tbbs生产废水的处理方法,所述处理方法参照实施例4,区别在于:(2)将步骤(1)过滤后的废水只进行一级萃取,其中一级萃取的ph环境为2,一级萃取剂为萃取剂flj-332,且所述一级萃取剂和步骤(1)过滤后废水的体积比为0.2:1。本发明所述国家标准gb/t5462-2015中,对精制工业盐中的工业湿盐进行了相关描述,具体见表1。表1项目优级一级二级氯化钠/(g/100g)≥96.095.093.3水分/(g/100g)≤3.003.504.00水不溶物/(g/100g)≤0.050.100.20钙镁离子总量/(g/100g)≤0.300.500.70硫酸根离子/(g/100g)≤0.500.701.00将上述实施例得到的工业湿盐进行含量测定,并参照国家标准gb/t5462-2015进行等级判断,具体结果见表2。表2项目实施例1实施例2实施例3实施例4实施例5氯化钠/(g/100g)95.596.397.396.593.5水分/(g/100g)3.242.862.982.533.12水不溶物/(g/100g)0.080.050.050.040.19钙镁离子总量/(g/100g)0.450.280.250.210.57硫酸根离子/(g/100g)0.080.060.120.080.41等级一级优级优级优级二级将上述实施例测定的cod检测结果汇总在表3中。表3项目实施例1实施例2实施例3实施例4实施例5橡胶助剂生产废水35000mg/l33000mg/l30000mg/l25000mg/l25000mg/l精馏母液350mg/l130mg/l210mg/l150mg/l490mg/l催化氧化处理液4000mg/l2700mg/l3500mg/l3000mg/l5600mg/l将实施例4和5进行对比可以看出,针对相同的橡胶助剂生产废水,采用两级萃取的实施例4可以得到优级工业湿盐,但是只采用一级萃取的实施例5却得到了二级工业湿盐。此外,采用两级萃取的实施例4可以得到cod含量更低的精馏母液和催化氧化处理液。然而,同样只采用一级萃取的实施例1却可以得到一级工业湿盐,以及cod含量较低的精馏母液和催化氧化处理液。因此,虽然本发明所述处理方法中优选两级萃取,但是针对一些特定组成废水,一级萃取同样可以达到有效的处理效果。由表2和表3的结果可以看出,实施例1至5采用本发明所述处理方法,可以对多种橡胶助剂生产废水进行有效处理,既能得到满足国家标准gb/t5462-2015规定的工业湿盐,又能通过凝水的精馏处理,得到cod含量<500mg/l的精馏母液来作为纯水,还能通过蒸发母液的催化氧化处理,得到cod含量<6000mg/l的高盐度处理液,进一步通过高盐度处理液的回用实现了无机盐资源的充分回收。申请人声明,本发明通过上述实施例来说明本发明的详细结构特征,但本发明并不局限于上述详细结构特征,即不意味着本发明必须依赖上述详细结构特征才能实施。所属
技术领域:
的技术人员应该明了,对本发明的任何改进,对本发明所选用部件的等效替换以及辅助部件的增加、具体方式的选择等,均落在本发明的保护范围和公开范围之内。以上详细描述了本发明的优选实施方式,但是,本发明并不限于上述实施方式中的具体细节,在本发明的技术构思范围内,可以对本发明的技术方案进行多种简单变型,这些简单变型均属于本发明的保护范围。另外需要说明的是,在上述具体实施方式中所描述的各个具体技术特征,在不矛盾的情况下,可以通过任何合适的方式进行组合,为了避免不必要的重复,本发明对各种可能的组合方式不再另行说明。此外,本发明的各种不同的实施方式之间也可以进行任意组合,只要其不违背本发明的思想,其同样应当视为本发明所公开的内容。当前第1页1 2 3