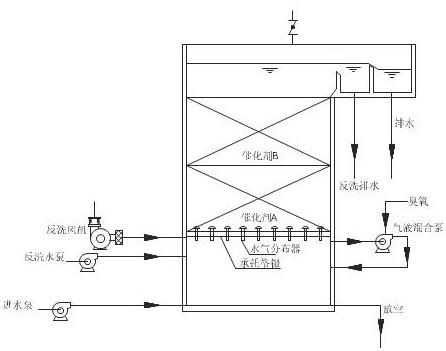
1.本发明属于环境保护技术领域,具体涉及一种污水处理催化臭氧氧化反应器。
背景技术:2.近年来为控制水环境恶化,各地方新排放标准不断出台,如北京市《水污染综合排放标准》(db11-307-2013)规定cod(化学需氧量)a级和b级排放限值分别为20 mg/l和30 mg/l;天津市《城镇污水处理厂污染物排放标准》(db12/599-2015)规定cod的a级和b级排放限值分别为30 mg/l和40 mg/l。污水排放标准的提高,催生了高级氧化污水深度处理技术的发展。
3.臭氧催化氧化法是高级氧化技术的一种,它是在臭氧和催化剂的共同作用下,生成强氧化性的羟基自由基氧化有机物,实现污水处理的目的。与芬顿、光催化、电氧化等高级氧化技术相比,臭氧催化氧化法具有适应面广、成本低、二次污染少等优点,是污水深度处理的优选方法。目前,对于臭氧催化氧化催化剂的主要制备方法有两种,一种是将活性金属负载在氧化铝或瓷球上,再经高温焙烧强化金属固载;另一种是以活性炭为载体,利用浸渍的方法使活性金属以物理或化学吸附的方式负载于孔道表面及内部,形成负载型催化剂。前者机械强度高、耐磨性好,但催化活性低、吸附性能差、床层密度大,反洗不彻底;后者催化活性高、吸附性能好,但机械强度低、耐磨性能差、活性金属易流失、床层密度过小,反洗易跑料。
4.目前,臭氧催化氧化反应器均参照曝气生物滤池设计开发,反应器中催化剂占绝大部分空间,存在着体积大、曝气及反洗系统复杂、检维修难度大、催化反应深度低、反应后气相残留臭氧浓度高、出水存在重金属残留等问题。因此,对反应器如何适应臭氧直接氧化及催化氧化过程,如何与新型高效催化剂匹配的问题需进行深入研究。
5.专利cn1576244a公开了一种催化臭氧去除水中有机污染物的反应器,其特征在于反应器底部的石英砂多孔布气系统或钛多孔布气板使臭氧曝气更加均匀,但在实际工程中经常出现曝气头堵塞的问题。
6.专利2014107775121.3公开了一种外循环污水处理臭氧催化氧化反应器及污水处理方法,将出水部分回流并引入臭氧尾气以提高臭氧的利用率,这种方式增加了回流设备,提高了反应器的造价;同时,回流水的引入提高了进水负荷,减少了停留时间,不利于污染物的降解。
技术实现要素:7.本发明所要解决的技术问题是现有臭氧催化反应器结构设计不合理、催化剂填装量多、曝气及反洗系统复杂、反应深度低、反应后气相残留臭氧浓度高、出水存在重金属残留等问题,提供一种高效的污水处理催化臭氧氧化反应器。
8.本发明基于原理如下:臭氧对有机物的氧化反应分为直接氧化和羟基自由基引发的间接反应,从氧化能力上看羟基自由基的氧化电位为2.8 v,臭氧的氧化电位为2.07 v,
羟基自由基的氧化电位为臭氧的1.35倍,,能够实现有机物的无差别氧化。从自由基生成机理看,3个臭氧分子可生成2个自由基,即生成自由基的过程中氧化剂的总量减少,而污水中一部分有机物的氧化分解电位较低,在臭氧存在条件下即可实现降解。另外,不同类型催化剂所含活性金属组分不同,其对污水中有机物的催化效能也有显著差别,出水中残留金属组分和浓度也不尽相同。因此,如何充分结合并利用臭氧直接氧化和自由基间接氧化过程,利用不同催化剂的特性进行有序匹配,提高臭氧利用的效率,减少出水中重金属含量,并简化反应器结构使之实用化,是设计高效反应器的关键。
9.本发明的实现方式如下:一种污水处理臭氧催化氧化反应器,主要由反应器主体、催化剂、承托格栅、气液混合泵、反洗水泵、反洗水、气分布器构成,其主要特征在于:承托格栅设计在反应器的中部或中部偏下,将反应器分成两部分,即下部的臭氧直接氧化区和上部的臭氧催化氧化区,格栅板上部安装反洗水分布器和反洗气分布器。同时,待处理污水进入反应器与臭氧进行反应,承托格栅上依次装填有催化剂a和催化剂b。其中,所述催化剂a为铁系负载型催化剂,催化剂b为铜系负载型催化剂。
10.上述技术方案中,进水管设置在反应器底部并与外部气液混合泵相连,污水向上流动依次经过臭氧直接氧化区和上部的臭氧催化氧化区,分别发生直接氧化反应和自由基氧化反应,直接氧化区的有效容积占总有效容积的1/3~1/2。
11.上述技术方案中,外部气液混合泵与臭氧发生器出气管路相连,连接管路上设有止回阀和调节阀,污水与臭氧在气液混合泵混合后直接通入反应器底部的臭氧直接氧化区。
12.上述技术方案中,反应器可以为矩形或圆形,总有效高度为4~8 m。根据水量大小和气液混合泵布水能力,将分单格或多格布置,每格占地面积为9~25 m2。
13.上述技术方案中,臭氧投加量与cod之比为1:1至3:1,空速为0.5~3.0 h-1
,反洗过程中气洗强度为5~15 l/m2·
s,水洗强度为4~10 l/m2·
s,反洗过程为:先气洗1~5 min,后水洗5~10 min,反洗周期为5~15 d。
14.上述技术方案中,承托格栅为钢砼或不锈钢材质,承托格栅上依次为不锈钢滤网、承托层、催化剂a和催化剂。
15.上述技术方案中,所述催化剂a包括载体和负载在载体上的活性金属组分,其中以活性炭、分子筛、氧化物中的一种或几种为载体;所述分子筛为a型、y型、beta、zsm-5、mcm-41分子筛中的一种或几种,所述氧化物为氧化铝、二氧化铈、二氧化钛、二氧化硅中的一种或几种;以铁为活性金属组分,活性金属组分以氧化物的含量计,fe2o3为1~10wt%。所述催化剂a中还可以包括助剂组分,所述助剂组分为镍、锌、镁、镧、铈、镨、钕中的一种或多种,所述助剂含量为0.1~5wt%。
16.上述技术方案中,所述催化剂b为铜系负载型催化剂,包括载体和负载在载体上的活性金属组分,其中以活性炭、分子筛、氧化物中的一种或几种为载体;所述分子筛为a型、y型、beta、zsm-5、mcm-41分子筛中的一种或几种,所述氧化物为氧化铝、二氧化铈、二氧化钛、二氧化硅中的一种或几种;以铜为活性金属组分,稀土金属为助剂,以催化剂的重量为基准,活性金属组分以氧化物的含量来计算:cuo为1~10wt%;稀土金属氧化物为0.1~5wt%。所述铜系负载型催化剂活性金属组分中还可以包括铁、镍或钒中的一种或几种。所述的助剂为镧、铈、镨、钕中的一种或多种。
17.上述技术方案中,所述催化剂a和催化剂b的体积比为80%~30%:20%~70%,优选为60%~40%:40%~60%本发明具有如下优点:1、将臭氧催化氧化反应器划分为直接氧化区和上部的臭氧催化氧化区,污水中的有机物污染物首先在直接氧化作用下降解,未能降解的部分进入催化氧化区。较高浓度的臭氧在铁系催化剂的作用下使一部分有机污染物转化,当臭氧浓度进一步降低时再与催化能力较强的铜系催化剂接触,充分发挥铜系催化剂的催化作用;通过铁系催化剂与铜系催化剂的协同作用,不仅有机废水处理效果好,而且还能有效降低金属铜的流失,解决了现有技术中使用铜系催化剂存在的铜金属流失的问题。与传统的全填充型催化反应器相比,该反应器既能减少臭氧用量,又能减少自由基复合的几率,充分发挥直接氧化、间接氧化过程的协同作用,以及间接氧化过程中不同级配催化剂的耦合作用,有机物氧化反应彻底,臭氧利用率高。
18.2、反应器结构简单,污水与臭氧通过气液混合泵预混后进入反应器,直接氧化区不设内构件,不存在曝气头堵塞、难以检修的问题;可以方便的将反应器建造为半地上形式,使催化氧化区位于地上部分,方便更换催化剂,并可降低工程造价。
19.3、由于催化剂具有机械强度高、耐磨性能耗好、比重适中等突出特点,反洗方式设置为先气洗、再反洗,无需设置气、水联合反洗过程,操作简便,水气消耗量低,符合节能减排的理念。
附图说明
20.图1为本发明所述装置的示意图。
21.具体实施方式
22.下面通过实施例对本发明作进一步的阐述,但不仅限于本实施例。
23.催化剂a1的制备(fe-ce/al2o3)将大孔氧化铝粉末与胶溶剂经捏合、碾压、挤条制成直径2.5mm的三叶草形载体,在空气中550℃焙烧后制得al2o3载体,比表面积220 m2/g,孔容0.7 cm3/g,平均孔径10.4nm。称取500g氧化铝载体,根据其吸水率用fe(no3)3·
9h2o和ce(no3)3·
6h2o按fe2o3和ceo2分别占催化剂总重量5%和1.5%的比例配成溶液。用fe-ce溶液等体积浸渍氧化铝载体2小时,80℃烘干,然后在马弗炉中550℃焙烧4小时,温度降到室温后取出,得到催化剂a1。
24.催化剂a2的制备(fe
ꢀ-
ce/zsm-5)将直径2.0mm,比表面积320m2/g,孔容0.3 cm3/g,平均孔径2.4nm的商用zsm-5分子筛条形载体在120℃烘干备用。称取zsm-5分子筛载体500g,用50%的fe (no3)3溶液和ce(no3)3·
6h2o按fe2o3和ceo2分别占催化剂总重量6%和1.5%的比例配成1000 ml溶液。用fe
ꢀ-
ce溶液浸渍zsm-5载体,在恒温水浴中60℃搅拌3小时,在空气中静置24小时后用旋转蒸发器80℃真空蒸干,得到的样品100℃干燥箱中烘干。然后在马弗炉中550℃焙烧4小时,温度降到室温后取出,得到催化剂a2。
25.催化剂b1的制备(cu-ce/ac)
将直径2.0mm,比表面积704m2/g,孔容0.7cm3/g,平均孔径2.0 nm的商用柱状活性炭条在120℃烘干备用。称取500g烘干的活性炭条,根据其吸水率用cu(no3)2·
3h2o和ce(no3)3·
6h2o按cuo和ceo2分别占催化剂总重量5%和1.5%的比例配成溶液。用cu-ce溶液等体积浸渍活性炭条2小时,80℃烘干,550℃氮气气氛下焙烧4小时,温度降到室温后取出,得到催化剂b1。
26.催化剂b2的制备(cu-ce/zsm-5)将直径2.0mm,比表面积320m2/g,孔容0.3 cm3/g,平均孔径2.4nm的商用zsm-5分子筛条形载体在120℃烘干备用。称取zsm-5分子筛载体500g,用cu(no3)2·
3h2o和ce(no3)3·
6h2o按cuo和ceo2分别占催化剂总重量5%和1.5%的比例配成1000 ml溶液。用cu-ce溶液浸渍zsm-5载体,在恒温水浴中60℃搅拌3小时,在空气中静置24小时后用旋转蒸发器80℃真空蒸干,得到的样品100℃干燥箱中烘干。然后在马弗炉中550℃焙烧4小时,温度降到室温后取出,得到催化剂b2。
[0027] 【实施例1】某炼油污水处理场三级生化出水,cod=56 mg/l,bod=1 mg/l,ss=8 mg/l,通过小试结果得到其中可臭氧直接氧化的cod为15 mg/l,可进一步催化氧化的cod为18 mg/l。
[0028]
一种污水处理臭氧催化氧化反应器,如图1所示。污水通过进水管(1)进入气液混合泵(3),与来自臭氧发生器(2)的臭氧充分混合溶解后进入臭氧直接氧化区(4),直接氧化区容积占总容积的1/2。反应过程中,臭氧投加量为90 mg/l,催化氧化区(5)依次填装催化剂a1和催化剂b1,其中两种催化剂体积比为40%和60%。反应器的空速为1.0 h-1
,反洗过程中气洗强度为5 l/m2·
s,水洗强度为4 l/m2·
s,反洗过程中首先气洗1 min,后水洗10 min,反洗周期为5 d。经本反应器处理后,出水cod≤15 mg/l,bod≤0.5 mg/l,ss≤5 mg/l。
[0029]
在与实施例1相同的操作条件下,利用传统反应器填充市售臭氧催化剂,经处理后,出水cod≤28 mg/l,bod≤1.5 mg/l,ss≤5 mg/l,效果低于本反应器。
[0030]
【实施例2】某化工污水处理场二级生化出水,cod=65 mg/l,bod=0.5 mg/l,ss=15 mg/l,通过小试结果得到其中可臭氧直接氧化的cod为12 mg/l,可进一步催化氧化的cod为23 mg/l。
[0031]
一种污水处理臭氧催化氧化反应器,如图1所示。污水通过进水管(1)进入气液混合泵(3),与来自臭氧发生器(2)的臭氧充分混合溶解后进入臭氧直接氧化区(4),直接氧化区容积占总容积的1/3。反应过程中,臭氧投加量为35 mg/l,催化氧化区(5)依次填装催化剂a1和催化剂b2,其中两种催化剂体积比为50%和50%。反应器的空速为3.0 h-1
,反洗过程中气洗强度为15 l/m2·
s,水洗强度为10 l/m2·
s,反洗过程中首先气洗5 min,后水洗5 min,反洗周期为15 d。经本反应器处理后,出水cod≤30 mg/l,bod≤1.0 mg/l,ss≤10 mg/l。
[0032]
在与实施例2相同的操作条件下,利用传统反应器填充市售臭氧催化剂,经处理后,出水cod≤45 mg/l,bod≤3.5 mg/l,ss≤5 mg/l,氧化效果低于本反应器。
[0033] 【实施例3】某印染污水处理场二级生化后的气浮出水,cod=80 mg/l,bod=8 mg/l,ss=5 mg/l,色度=20,通过小试结果得到其中可臭氧直接氧化的cod为18 mg/l,可进一步催化氧化的cod为27 mg/l。
[0034]
一种污水处理臭氧催化氧化反应器,如图1所示。污水通过进水管(1)进入气液混
合泵(3),与来自臭氧发生器(2)的臭氧充分混合溶解后进入臭氧直接氧化区(4),直接氧化区容积占总容积的1/3。反应过程中,臭氧投加量为70 mg/l,催化氧化区(5)依次填装催化剂a2和催化剂b1,其中两种催化剂体积比为70%和30%。反应器的空速为2.0 h-1
,反洗过程中气洗强度为10 l/m2·
s,水洗强度为8 l/m2·
s,反洗过程中首先气洗2 min,后水洗8 min,反洗周期为10 d。经本反应器处理后,出水cod≤25 mg/l,bod≤3.0 mg/l,ss≤10 mg/l。
[0035]
在与实施例3相同的操作条件下,利用传统反应器填充市售臭氧催化剂,经处理后,出水cod≤40 mg/l,bod≤5 mg/l,ss≤15 mg/l,氧化效果低于本反应器。