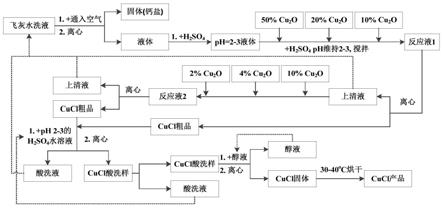
1.本发明涉及一种含氯离子废水高值化利用制氯化亚铜的方法,尤其涉及一种垃圾焚烧飞灰中氯离子高值化利用制氯化亚铜的方法,属于废水处理领域。
背景技术:2.随着城市化进程加快,国内生活垃圾焚烧总规模近100万吨/天,年产生量1000万吨,且以每年5
‑
9%的速度急剧增加。飞灰产生量约3万吨/天,飞灰中含有大量氯盐、重金属、二噁英等有机毒物。我国在飞灰处理的技术研究起步较晚,目前对飞灰处理主要通过稳定化填埋,由于固化/稳定化填埋存在增容量大、长期稳定性差等问题,因而急需开发减容量大、无害化彻底、资源化程度高的飞灰处置关键技术,实现氯盐、重金属、二噁英等有机毒物清洁化处理及资源化利用。
3.焚烧飞灰主要成分为氧化钙、氧化硅等物质,与水泥成分相似,可替代部分水泥,因此现有技术有通过将其掺入水泥以进一步处理飞灰的技术。但焚烧生成的飞灰中包含了大量的氯离子,掺入水泥中会产生如下危害,(1)腐蚀作用:溶液中氯离子能够不同程度的破坏金属以及合金表层钝化膜,使其产生晶间腐蚀、缝隙腐蚀以及点蚀等,影响工业设备的正常运行,产生安全隐患。(2)影响建筑物正常寿命:当混凝土中氯离子含量较大时,将腐蚀其中的钢筋,会使混凝土膨胀、疏松,降低了其抗化学腐蚀、耐磨性和强度,破坏建筑结构。(3)对人体的毒性:高含氯量的飞灰在后续处理时对工人人体代谢、气管、皮肤等方面产生毒性反应,严重时还可致癌。
4.现有针对飞灰中的氯离子的处理还有其他方法,例如利用氯离子有水溶性高的特点,通过水洗可洗出大部分的氯离子,但是仍需进一步处理含氯废水。含氯废水目前常用处理方法有离子交换法、蒸发浓缩法、化学沉淀法、电化学法。离子交换树脂吸附过程中存在管道易堵塞,吸附终点和解吸终点无法及时准确地确定等问题,蒸发浓缩和电化学法耗能高,不适合大量废水处理。化学沉淀法有银沉淀法、氯铝酸钙和铜粉法,银原理价格昂贵,氯铝酸钙投加量难以控制,尚处于研究阶段。现有也有通过氧化亚铜来除去氯离子的工艺,但是氧化亚铜除氯用量较大,一般为理论氧化亚铜用量的2~6倍,在氧化亚铜充分过量的情况下达到96%甚至更高的除氯效果,将得到的氧化亚铜与氯化亚铜混合物用火碱处理得到氢氧化亚铜,高温脱水得到氧化亚铜回用。但亚铜化合物极不稳定,ph过低容易歧化,ph过高易氧化,且由于产物量过大,在回用的火碱处理,高温干燥等过程中造成严重损失。另外氯离子其实生成大量的氯化钠废盐,仍需下一步处理。虽达到循环利用的效果,但经济价值不大。总的来看,目前各种除氯方法主要是富集浓缩待下一步处理,并存在成本过高,效果欠佳的问题。氯离子处理技术还很欠缺,亟待研发出更多绿色有效的除氯方法。
技术实现要素:5.[技术问题]
[0006]
现有除氯方法存在成本高、效果差等问题,尤其是利用氧化亚铜来除去氯离子的
工艺存在除氯用量较大且回收率低,浪费严重的问题。
[0007]
[技术方案]
[0008]
为了解决上述问题,本发明将飞灰酸浸后经固液分离得到酸浸液,再将氧化亚铜作为氯结合剂加入到飞灰酸浸液中,经过分步处理得到高纯度具有一定价值的产物氯化亚铜,本发明方法大大降低了氧化亚铜用量,大幅减少氯离子处理成本,同时提高了氯化亚铜的纯度,使得氯离子实现了资源化利用,提高了经济效益。
[0009]
具体的,本发明提供了一种含氯离子废水高值化利用制氯化亚铜的方法,所述方法包括以下步骤:
[0010]
(1)一次反应:取含有氯离子的废水,并调节其ph为2~3.5,之后按照cl
‑
浓度添加氧化亚铜理论用量的50~80%,期间维持ph在2
‑
3.5,氧化亚铜添加完成后搅拌反应8
‑
15min,反应结束后离心,得到氯化亚铜粗品和上清液,上清液待二次反应;
[0011]
(2)二次反应:在步骤(1)得到的上清液中加入氧化亚铜加入量,且一次反应和二次反应共加入氧化亚铜为理论量的90~100%,期间维持ph在2
‑
3.5,氧化亚铜添加完成后搅拌反应8
‑
12min,反应结束后离心,得到氯化亚铜粗品;
[0012]
(3)将步骤(1)和步骤(2)得到的氯化亚铜粗品进行酸洗、醇洗、干燥即可。
[0013]
在本发明的一种实施方式中,所述含有氯离子的废水包括任意含有氯离子的废水,例如,焚烧垃圾等得到的飞灰水洗液,铜电解液等。
[0014]
在本发明的一种实施方式中,所述含有氯离子的废水中氯离子浓度为10
‑
100g/l。
[0015]
在本发明的一种实施方式中,当所述含有氯离子的废水呈碱性时(例如飞灰水洗液),调节其ph为2~3之前,优选先通过在废水体系中通入空气2
‑
4h使其ph到7
‑
7.5的方式来进行处理,既能够节约后续酸的用量,又能吸收空气中的co2气体,减少温室气体的含量。
[0016]
在本发明的一种实施方式中,调节ph的过程优选添加硫酸进行调节。
[0017]
在本发明的一种实施方式中,所述硫酸的浓度为2
‑
8mol/l。
[0018]
在本发明的一种实施方式中,硫酸保持持续加入,维持体系ph恒定在2
‑
3.5之间。
[0019]
在本发明的一种实施方式中,所述搅拌反应优选在室温下进行,所述室温的温度为10~40℃。
[0020]
在本发明的一种实施方式中,所述氧化亚铜可以市购或者通过以下方法制备得到:阳极氧化电解法和葡萄糖还原法。
[0021]
在本发明的一种实施方式中,步骤(1)中,一次反应过程中,优选的,氧化亚铜分批添加,优选分3~5批添加。
[0022]
在本发明的一种实施方式中,步骤(2)中,二次反应过程中,优选的,氧化亚铜分批添加,优选分3~5批添加。
[0023]
在本发明的一种实施方式中,分3~5次加入,每次间隔0.5~1min,当分3次加入时,依次加入该次反应加入量的10~70%、10~70%、10~70%的氧化亚铜;当分4次加入时,依次加入该次反应加入量的10~60%、10~60%、10~60%、10~60%的氧化亚铜;当分5次加入时,依次加入该次反应加入量的10~50%、10~50%、10~50%、10~50%、10~50%的氧化亚铜。
[0024]
在本发明的一种实施方式中,步骤(1)中,一次反应过程中优选在无氧环境下进行反应。
[0025]
在本发明的一种实施方式中,步骤(2)中,二次反应过程中优选在无氧环境下进行反应。
[0026]
在本发明的一种实施方式中,步骤(3)中,所述酸洗包括:加入一定体积ph=2~3的硫酸溶液洗涤氯化亚铜粗品,再次离心,重复操作1~3次,得到酸洗氯化亚铜。
[0027]
在本发明的一种实施方式中,步骤(3)中,所述醇洗包括:加入一定体积的无水乙醇继续洗涤得到的酸洗氯化亚铜,离心,重复操作1~2次,得到醇洗氯化亚铜。
[0028]
在本发明的一种实施方式中,步骤(3)中,所述干燥包括,将得到的醇洗氯化亚铜放入真空干燥箱中,于30~100℃,干燥30~120min,得到氯化亚铜产品。
[0029]
在本发明的一种实施方式中,步骤(2)中离心得到的上清液可作为水洗废水等工艺用水。
[0030]
本发明还提供了一种飞灰处理方法,所述方法包括水洗飞灰得到飞灰水洗液,再利用上述处理含氯废水的方式进行处理。
[0031]
本发明还提供了一种垃圾处理的方法,所述方法包括焚烧垃圾,将得到的飞灰进行水洗得到飞灰水洗液,再利用上述处理含氯废水的方式进行处理。
[0032]
本发明相对于现有技术,具有以下的优点和效果:
[0033]
(1)本发明利用氧化亚铜作为除氯剂,结合两次反应除氯,最终总除氯效果可达96%,且得到纯度95%以上的氯化亚铜产品,实现了含氯废水的除氯处理,且得到的氯化亚铜可以作为副产物进行售卖,提高了经济效益。
[0034]
(2)本发明通过改进工艺(两步反应、维持ph稳定、分批加入、无氧操作)使得本发明方法大大减少了氯化亚铜的用量,仅使用理论用量90~100%的氧化亚铜即可实现氯离子的脱除,较现有技术极大的减少了氧化亚铜的用量,具有十分重要的意义。
附图说明
[0035]
图1本发明的氧化亚铜除氯流程图。
具体实施方式
[0036]
氯离子的测定以及除氯率的计算公式:雷磁pxsj
‑
216f离子计
[0037][0038]
式(1)中c1、v1代表初始溶液cl
‑
浓度和体积,c2、v2代表除氯后溶液cl
‑
浓度和体积
[0039]
氯化亚铜纯度的测定方法:按照gb/t 27562
‑
2011《工业氯化亚铜》标准中方法测定,同时用icp验证;通过xrd对氯化亚铜进行表征;
[0040]
氯化亚铜产率的计算公式:
[0041]
式(2)中m2代表产物总质量,m1代表投入氧化亚铜总质量。
[0042]
下面结合实施例对本发明作进一步的描述,但本发明的实施方式不限于此。
[0043]
含氯废水为飞灰水洗液,来自于江苏某垃圾焚烧厂公司,氯离子浓度为0.8
‑
1.5mol/l。
[0044]
氧化亚铜的制备方法:葡萄糖还原法:在剧烈搅拌下将溶液10ml浓度50g/l葡萄糖溶液加入到溶液50ml浓度为10g/l乙酸铜溶液中并搅拌10min。然后,在70℃下向该混合物
中加入25ml浓度为20g/l氢氧化钠溶液并保持搅拌1小时。离心得到产物,用去离子水和无水乙醇冲洗3次(离心机转速11000r/min),产物在60℃下真空干燥至恒重。
[0045]
电解法:铜板作阳极,钛网作阴极,食盐溶液作阳极电解液,ctab(十六烷基三甲基溴化铵)为添加剂,阴极用氢氧化钠溶液。反应过程中阳极液要不断搅拌,分别控制反应时的面电流密度为30、40、50a/m2。反应1h后阳极沉淀经分离、漂洗、过滤、于燥后即为成品氧化亚铜。
[0046]
实施例1
[0047]
(1)一次反应:制备氯化亚铜粗品:取100ml飞灰水洗液(cl
‑
浓度30g/l),体系中通入空气4h,检测ph到7左右,滴加硫酸至ph为2.5,后分别按照理论氧化亚铜(6.05g)50%、60%、70%、80%、90%、100%、120%的添加量(分别对应nacl:cu2o=1:0.25、1:0.3、1:0.35、1:0.4、1:0.45、1:0.5、1:0.6)分批加入cu2o(分三批加入,依次加入添加量的62.5%、25%和12.5%,添加间隔为1min),期间不断补加硫酸维持ph在2.5左右,在室温下搅拌10min,反应结束后离心,得到氯化亚铜粗品和上清液,氯化亚铜粗品进行后处理,上清液待二次反应;
[0048]
(2)二次反应:取步骤(1)得到的上清液,添加cu2o使得步骤(1)和步骤(2)总的添加量为理论添加量的96%或100%(分三批添加,同第一次反应),同样步骤重复一次反应,反应后得氯化亚铜粗品与一次反应得的氯化亚铜粗品进行合并处理;
[0049]
(3)产品后处理:酸洗:加入80mlph=2.6的硫酸溶液洗涤上述粗品,再次离心,重复操作2次,得到酸洗氯化亚铜;醇洗:加入80ml的无水乙醇继续洗涤上述氯化亚铜,离心,重复操作2次,得到醇洗氯化亚铜;干燥:将上述氯化亚铜放入真空干燥箱中,于45℃,干燥60min,得到氯化亚铜产品。余氯的上清液可以回用洗飞灰。
[0050]
此实施例的一次反应的结果见表1。综合考虑产物纯度和产率的影响因素,当nacl:cu2o≥1:0.5时,尽管除氯效果有一定的提升,但是产品氯化亚铜的纯度却明显下降,因此,选择以nacl:cu2o=1:0.25~0.45即一次反应按照cu2o理论量的50~90%添加,剩余氯离子进行二次反应。
[0051]
表1一次反应的摩尔量比对除氯效果以及氯化亚铜的影响
[0052]
nacl:cu2o1:0.251:0.31:0.351:0.41:0.451:0.51:0.6除氯率(%)48.3958.1868.1376.2484.7588.8789.66产品纯度(%)98.1598.0498.1898.1495.0385.4678.38产品产率(%)83.1383.6385.987.886.3988.5290.63
[0053]
反应条件:初始cl
‑
(30g/l),ph值=2.5,室温,10min,搅拌速度400r/min。
[0054]
二次反应得到的除氯效果见表2。与表1相比,可见,在与一次加入等量的情况下(甚至更少,一次反应加入100%或120%,两次反应加入总量为96%),氧化亚铜分两次加入得到了更好的除氯效果和更高的产物浓度,以80%+20%为例,最终得到的产物氯化亚铜的纯度可达97%以上,除氯率也可以高达95.8%,明显高于一次100%添加氧化亚铜的效果(氯化亚铜纯度为85.46%,除氯率为88.87%)。因此,选择两次反应添加氧化亚铜的方法处理水洗飞灰水。此外,从表2还可以看出,第一次反应加入量在50%
‑
80%(对应第二次反应加入量为50%
‑
20%)时,可以得到95%以上的除氯效果和纯度97%以上的氯化亚铜产物。以80%+20%为例,当第二次适当少的添加(16%)氧化亚铜时,虽然会降低稍稍降低除氯率
但同时可以小幅提高产物纯度,因此,为了节约成本,优选80%+16%的投加方式。
[0055]
表2二次反应的摩尔量比对除氯效果以及氯化亚铜的影响
[0056]
nacl:cu2o1:0.251:0.21:0.151:0.11:0.081:0.05对应一次反应1:0.251:0.31:0.351:0.41:0.41:0.45除氯率(%)48.6338.9129.3619.5618.869.85产品纯度(%)96.0596.3996.1496.2696.6192.14产品产率(%)91.2591.4290.8990.5289.5389.21
[0057]
反应条件:初始cl
‑
(30g/l),ph值=2.5,室温,10min,搅拌速度400r/min。
[0058]
实施例2
[0059]
以实施例1一次反应添加80%、二次反应添加16%为例,改变搅拌反应的时间分别为2、5、8、10(实施例1)、12、15min,其余操作步骤同实施例1,结果见表3。可见,当反应搅拌时间为10~15min时,既可以保证除氯率,又能保证氯化亚铜纯度不低于96%,反应效果在10min左右达到最佳,之后继续反应导致氯离子的释放和亚铜离子氧化和歧化,使产品纯度略有降低,时间最优选控制在10~12min。
[0060]
表3反应搅拌时间对总除氯效果以及氯化亚铜的影响
[0061]
t/min258101215除氯率(%)62.1982.7490.6495.1095.1092.47产品纯度(%)67.4284.9593.1097.8997.5596.54产品产率(%)94.9292.4389.3488.187.587.7
[0062]
反应条件:初始cl
‑
(30g/l),ph值=2.5,室温,搅拌速度400r/min,添加80%+16%。
[0063]
实施例3
[0064]
以实施例1一次反应添加80%、二次反应添加16%为例,改变实施例1的反应搅拌速度为200r/min和600r/min,其余操作参数和实施例1一致,结果见表4,可见,搅拌速度对产品影响较小。
[0065]
表4搅拌速度对对总分批除氯效果以及氯化亚铜的影响
[0066]
r/min200400600除氯率(%)95.0295.1095.05产品纯度(%)97.7397.8997.84产品产率(%)88.688.188.3
[0067]
反应条件:初始cl
‑
(30g/l),ph值=2.5,室温,搅拌反应10min。
[0068]
实施例4
[0069]
以实施例1一次反应添加80%、二次反应添加16%为例,改变实施例1的氯离子的初始浓度分别为10、40、50、100g/l,其余操作参数和实施例1一致,结果见表5。
[0070]
可见,氯离子的初始浓度不宜过高,为了保证产品纯度,控制初始浓度在100g/l以下,最好不要超过50g/l,更优选选择30g/l以下。
[0071]
表5cl
‑
浓度对对总除氯效果以及氯化亚铜的影响
[0072][0073][0074]
反应条件:ph值=2.5,室温,10min,搅拌速度400r/min。
[0075]
实施例5
[0076]
(1)一次反应:制备氯化亚铜粗品:取100ml飞灰水洗液(cl
‑
浓度30g/l),体系中通入空气4h,检测ph到7左右,滴加硫酸至ph在2.5,后按照理论氧化亚铜(6.05g)80%的添加量加入cu2o(一次性加入),期间不断补加硫酸维持ph在2.5左右,在室温下搅拌10min,反应结束后离心,得到氯化亚铜粗品和上清液,氯化亚铜粗品进行后处理,上清液待二次反应;
[0077]
(2)二次反应:取步骤(1)得到的上清液,添加cu2o使得步骤(1)和步骤(2)总的添加量为理论添加量的96%(一次性加入),同样步骤重复一次反应,反应后得氯化亚铜粗品与一次反应产物合并处理;上清液反应后cl
‑
浓度降至2.97g/l,除氯效果达到90.1%。
[0078]
(3)产品后处理:酸洗:加入80mlph=2.6的硫酸溶液洗涤上述粗品,再次离心,重复操作2次,得到酸洗氯化亚铜;醇洗:加入一定体积的无水乙醇继续洗涤上述氯化亚铜,离心,重复操作2次,得到醇洗氯化亚铜;干燥:将上述氯化亚铜放入真空干燥箱中,于45℃,干燥60min,得到氯化亚铜产品,得到氯化亚铜产品5.15g,产率85.2%,测得产品纯度为95.16%,反应液合并用于水洗飞灰。
[0079]
实施例6
[0080]
以实施例1一次反应添加80%、二次反应添加16%为例,搅拌反应过程在无氧环境下进行(通入氮气进行保护),其他操作步骤和参数同实施例。结果发现,上清液反应后cl
‑
浓度降至1.41g/l,除氯效果达到95.3%。得到氯化亚铜产品5.40g,产率89.4%,测得产品纯度为98.56%。可见,无氧环境会稍微提高处理效果,但是提升不明显。
[0081]
实施例7
[0082]
备氯化亚铜粗品:取100ml飞灰水洗液(cl
‑
浓度30g/l),体系中通入空气4h,检测ph到7左右,滴加硫酸至ph为0.5、1、1.5和2,后分别按照理论nacl:cu2o=1:0.5分批加入cu2o(分三批加入,依次加入添加量的62.5%、25%和12.5%,添加间隔为1min),期间分别不断补加硫酸维持ph或一次添加硫酸(硫酸总量一致),在室温下搅拌10min,反应结束后离心,得到氯化亚铜粗品和上清液,氯化亚铜粗品进行后处理。
[0083]
结果见表6,可以看出同样量的硫酸情况下,当采用将硫酸持续加入以维持体系ph值稳定状态可以得到更好的除氯效果和纯度更高的产品。
[0084]
表6硫酸一次加入和持续加入的对比
[0085][0086]
反应条件:初始cl
‑
(30g/l),摩尔量比(nacl:cu2o=1:0.5),室温,10min,搅拌速度400r/min。注:持续调节是将一次调节为0.5时的硫酸量分批持续加入,使体系ph值保持恒定。
[0087]
实施例8
[0088]
以实施例1一次反应添加80%、二次反应添加16%为例,调节ph分别为1、1.5、2、2.5(实施例1)、3、3.5,其余操作步骤同实施例1,结果见表7。综合考虑除氯效果和产物纯度两方面因素,选择持续控制体系ph为2
‑
3.5,最优选ph为2~3。
[0089]
表7ph值对二次总反应的影响
[0090]
ph值11.522.533.5除氯率(%)96.7996.0295.8495.1094.9893.29产品纯度(%)86.5494.2197.3297.8997.7397.32产品产率(%)87.4286.7586.388.188.2688.28
[0091]
反应条件:初始cl
‑
(30g/l),室温,10min,搅拌速度400r/min,一次反应添加80%、二次反应添加16%。
[0092]
实施例9
[0093]
以实施例1一次反应添加80%、二次反应添加16%为例,改变实施例1的含氯废水为制备氧化亚铜的铜电解液,氯离子含量49.7g/l,无需通入空气,其余操作参数和实施例1一致。按照理论氧化亚铜添加量(10.02g)的80%+16%分批加入,上清液反应后cl
‑
浓度降至2.2g/l,除氯效果达到95.2%。得到氯化亚铜产品8.95g,产率89.3%,测得产品纯度为98.63%。表明此方法不仅适用于飞灰水洗液,也适用于其他含氯废水的处理。
[0094]
实施例10
[0095]
以实施例1一次反应添加80%、二次反应添加16%为例,一次反应和二次反应过程中分批加入氧化亚铜(分3~5次加入,每次间隔0.5~1min,当分3次加入时,依次加入10~70%、10~70%、10~70%的氧化亚铜;当分4次加入时,依次加入10~60%、10~60%、10~60%、10~60%的氧化亚铜;当分5次加入时,依次加入10~50%、10~50%、10~50%、10~50%、10~50%的氧化亚铜),其余操作参数同实施例1。
[0096]
经过检测,除氯率达95%以上;氯化亚铜产率88%以上、纯度97%以上。
[0097]
表8分批添加的次数对二次总反应的影响
[0098]
[0099][0100]
反应条件:初始cl
‑
(30g/l),室温,10min,搅拌速度400r/min,一次反应添加80%、二次反应添加16%。其中,分三次添加时,分别添加所需添加量的62.5%、25%和12.5%,添加间隔为1min;分四次添加时,分别添加所需添加量的50%、25%、12.5%和12.5%,添加间隔为1min;分五次添加时,分别添加所需添加量的30%、30%、20%、10%和10%,添加间隔为0.5min。
[0101]
虽然本发明已以较佳实施例公开如上,但其并非用以限定本发明,任何熟悉此技术的人,在不脱离本发明的精神和范围内,都可做各种的改动与修饰,因此本发明的保护范围应该以权利要求书所界定的为准。