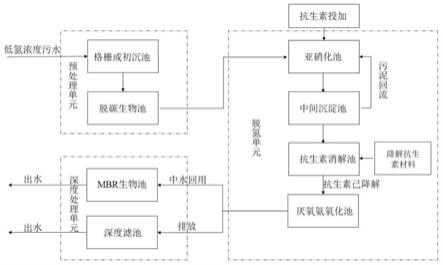
1.本发明属于水处理技术领域,具体涉及一种抗生素限制硝化细菌的低氨氮浓度污水主流厌氧氨氧化工艺。
背景技术:2.厌氧氨氧化工艺在厌氧条件下,以无机氨为电子供体,以硝酸盐或亚硝酸盐为电子受体,将氨氧化成氮气,这比全程硝化(氨氧化为硝酸盐)节省60%以上的供氧量。以氨为电子供体还可节省传统生物脱氮工艺中所需的碳源。部分亚硝化
‑
厌氧氨氧化工艺(pn
‑
a工艺)为厌氧氨氧化技术应用的常用工艺,部分亚硝化段(pn)将反应器中一半以上的氨氮氧化为亚硝氮,为厌氧氨氧化段提供了所需的亚硝酸盐,适用于高氨氮废水的去除。在污泥厌氧消化沼液应用中具有诸多优点,需氧量少;不需要有机碳源,减少了剩余污泥产量;降低了运营成本。
3.pn
‑
a工艺处理高含氮废水中,高浓度的氨氮产生了较高的游离氨浓度抑制了部分亚硝化生物段内的nob菌的生长及繁殖。通过运行条件的调控,成功实现了氨氮的亚硝化过程,抑制了亚硝态氮向硝态氮的转化。在主流低氨氮浓度污水处理系统中,常面临着外加碳源多,氧需求量大等问题,因此pn
‑
a工艺如何在主流低氨浓度污水处理中应用,受到广泛关注。然而,在实际应用中在低氨氮浓度污水氨氮浓度低,亚硝化生物段内游离氨浓度难以长期抑制nob菌。如何在低氨氮浓度污水处理的pn段抑制硝化细菌,实现亚硝化的稳定运行,是pn
‑
a工艺在低氨氮浓度污水主流厌氧氨氧化应用面临的主要问题。
4.抗生素是指由微生物(包括细菌、真菌、放线菌属)或高等动植物在生活过程中所产生的具有抗病原体或其他活性的一类次级代谢产物,能干扰其他生活细胞发育功能的化学物质。抗生素等抗菌剂的抑菌或杀菌作用,主要是针对“细菌有而人(或其他动植物)没有”的机制进行杀伤,包含四大作用机理,即:抑制细菌细胞壁合成,增强细菌细胞膜通透性,干扰细菌蛋白质合成以及抑制细菌核酸复制转录。抗生素的作用具有选择性,不同抗生素对不同病原菌的作用不一样。对某种抗生素敏感的病原菌种类称为该抗生素的抗生谱(抗菌谱)。仅对单一菌种或属有抗菌作用。在农业领域,为了抑制土壤中硝化细菌的硝化作用,常使用抗生素抑制硝化细菌,实现植物对土壤中氮素的高利用率。使用的抗生素种类包括但不限于土霉素、甲硝唑、呋喃唑酮、庆大霉素等。
5.选用抗生素(包括但不限于土霉素、甲硝唑、呋喃唑酮、庆大霉素等)对硝化细菌进行抑制,保留氨氧化古菌活性,成功实现低浓度下废水的亚硝化过程,是低氨氮浓度污水主流厌氧氨氧化工艺应用的重要过程。
技术实现要素:6.本发明提供了一种抗生素限制硝化细菌的低氨氮浓度污水主流厌氧氨氧化系统及其工艺,解决了pn
‑
a工艺处理低氨氮浓度污水时,亚硝化段难以控制的问题,有助于厌氧
氨氧化工艺在主流污水处理领域的应用。
7.本发明的技术方案之一,一种抗生素限制硝化细菌的低氨氮浓度污水主流厌氧氨氧化工艺系统,包括预处理单元,脱氮单元以及深度处理单元,预处理单元输出连接脱氮单元,脱氮单元的输出连接深度处理单元;所述的预处理单元包括依次连接的大颗粒悬浮物去除装置和脱碳处理生物池;所述的脱氮单元包括依次连接的亚硝化生物池,中间沉淀池和抗生素消解池以及厌氧氨氧化生物池;所述的深度处理单元为mbr生物池或深度滤池;其中:所述的脱碳处理生物池出水口与亚硝化生物池进水口相连通;所述的厌氧氨氧化生物池出水口与深度处理单元进水口相连通。本发明的技术方案之二,采用上述系统进行低氨氮浓度污水主流厌氧氨氧化工艺的运行方法,包括:第1阶段低氨氮浓度污水经过预处理装置,由格栅或初沉池去除水中大颗粒悬浮物,进入脱碳生物池降解进水中有机碳;第2阶段随后投加抗生素进入亚硝化段中,所述抗生素包括但不限于土霉素、甲硝唑、呋喃唑酮、庆大霉素,抑制亚硝化段的硝化细菌(aob和nob),使氨氧化古菌(aoa)为优势菌种,在亚硝化将部分氨氮氧化为亚硝氮,完成亚硝化过程;进入中间沉淀池将出水中污泥沉淀后回流进亚硝化,出水进入抗生素消解池去除抗生素;去除抗生素后进入厌氧氨氧化段进行厌氧氨氧化反应;第3阶段厌氧氨氧化出水经过mbr生物池或深度滤池深度处理,满足排放标准后排放。第1阶段中,所述的低氨氮浓度污水进入脱碳生物池,温度控制在30
‑
35度,水力停留时间5
‑
12h,溶氧控制在0.8
‑
2.0mg/l之间;第2阶段中,所述的低氨氮浓度污水脱碳后进入亚硝化生物池,温度控制在32
‑
34度,每日投加1
‑
10mg/l土霉素或0.1
‑
5mg/l甲硝唑,或20
‑
50mg/l呋喃唑酮,或2
‑
15mg/l庆大霉素,抑制aob和nob的活性,氨氧化古菌(aoa)为优势菌种;所述的亚硝化池出水进入中间沉淀池,水力停留时间10
‑
20h,污泥回流至亚硝化池,中间沉淀池出水进入抗生素消解池;所述的中间沉淀池出水进入抗生素消解池,抗生素消解池投加的抗生素降解材料包括但不限于四环素降解菌或高锰酸钾或tio2光催材料或乙酸钙不动杆菌等,水力停留时间10
‑
20h,投加量为0.1
‑
1mg/l去除水中抗生素;所述的抗生素消解池出水进入厌氧氨氧化池,温度32
‑
34度,水力停留时间10
‑
20h,通过自控装置投加酸碱控制ph 7.5
‑
8.0,厌氧状态;第3阶段中,所述的厌氧氨氧化出水以中水回用为目的,进入mbr生物池,水力停留时间10
‑
20h,温度30
‑
35度,ph 7.0
‑
8.0;所述厌氧氨氧化出水以排放为目的,进入深度滤池,水力停留时间10
‑
20h。
35.与现有技术相比,本发明具有以下有益效果:
36.对低氨氮浓度污水进行脱碳预处理,有益于减轻脱氮单元的有机碳负荷。pn段投加抗生素后,异养菌也被灭活,pn段难以去除废水中的有机碳,减少有机物进入厌氧氨氧化段引起的负面影响。脱碳预处理可采用传统活性污泥法,但不投加额外碱度和碳源,保持低水力停留时间和低溶氧浓度,利用废水中的碱度及碳源进行反应。降低预处理能耗及药剂投加费用运行。
37.亚硝化段优势菌种:氨氧化古菌(aoa)。亚硝化段中一般选用氨氧化细菌(aob菌)为优势菌种。然而在低氨氮主流废水处理工艺中,较低的氨氮浓度难以实现稳定的亚硝化反应。本发明中,选择培育驯化氨氧化古菌(aoa)为亚硝化段的优势菌种,减少了常规亚硝化段aob、nob细菌同时存在运行过程中产生的各种生存竞争,免去为了维持aob为优势细菌而进行的各种繁杂操作。
38.投加抗生素抑制aob、nob两种细菌,保持aoa菌种优势。抗生素常用于抑制土壤中硝化细菌,提高植物的氮利用率。本发明中,抗生素的投加抑制了aob、nob及部分的未查明属性的细菌,有利于促进aoa古菌的生长繁殖,提升丰度,提高pn段的氨氮转化效率和反应器运行的稳定性。
附图说明
43.图1为本发明处理方法的工艺流程图
具体实施方式
44.下面将结合本发明实施例,对本发明实施例中的技术方案进行清除、完整的描述,显然,所描述的实施例仅仅是本发明一部分实施例,而不是全部实施例。基于本发明中的实施例,本领域普通技术人员在没有做出创造性劳动前提下所获得的所有其他实施例,都属于本发明保护的范围。
45.另外,为了更好的说明本发明的内容,在下文的具体实施例中给出了众多的具体细节。本领域技术人员应当理解,没有某些具体细节,本发明同样可以实施。在另外一些实施例中,对于本领域技术人员熟知的方法、手段未作详细描述,以便于凸显本发明的主旨。本发明中,表述原料含量的单位均基于重量份及,除非另外说明。另外,关于本发明的技术指标的测定方法均为本领域内使用标准方法,具体可参见最新的国家标准,除非另外说明。
46.应当理解,本文所使用的诸如“具有”、“包含”以及“包括”术语并不排除一个或多个其他元件或其组合的存在或添加。
47.本发明的技术方案之一,一种抗生素(包括但不限于土霉素、甲硝唑、呋喃唑酮、庆大霉素等)限制硝化细菌的低氨氮浓度污水主流厌氧氨氧化工艺系统,图1所示,包括预处理单元,脱氮单元以及深度处理单元,预处理单元输出连接脱氮单元,脱氮单元的输出连接深度处理单元;
48.所述的预处理单元包括依次连接的大颗粒悬浮物去除装置和脱碳处理生物池;
49.所述的脱氮单元包括依次连接的亚硝化生物池,中间沉淀池和抗生素消解池以及厌氧氨氧化生物池;
50.所述的深度处理单元包括但不仅限于mbr生物池或深度滤池;
51.所述的脱碳处理生物池出水口与亚硝化生物池进水口相连通;
52.所述的厌氧氨氧化生物池出水口与深度处理单元(mbr生物池或深度滤池)进水口相连通;
53.作为本发明的进一步改进,所述的大颗粒悬浮去处装置包括但不仅限于格栅,初沉池;
54.作为本发明的进一步改进,所述的脱碳处理生物池包括但不仅限于进出水管道,
进出水泵,搅拌桨、曝气装置、气体流量计、溶氧监控设备、ph在线监控设备,药剂储存投加设备及温度监控设备;
55.作为本发明的进一步改进,所述的脱碳处理生物池后方设置有泥水分离区域(大小及分离方式不限);
56.作为本发明的进一步改进,所述的亚硝化生物池包括但不仅限于进出水管道,进出水泵,搅拌桨、曝气装置、气体流量计、溶氧监控设备、ph在线监控设备,药剂储存投加设备及温度监控设备;
57.作为本发明的进一步改进,所述的中间沉淀池大小及沉降方式不限,设置回流管道与亚硝化池相连;
58.作为本发明的进一步改进,所述的抗生素消解池内包括但不仅限于固定填料装置;
59.作为本发明的进一步改进,所述的厌氧氨氧化生物池包括但不限于进出水管道,进出水泵,搅拌桨、气体流量计、ph在线监控设备,酸碱投加设备及温度监控设备;
60.作为本发明的进一步改进,所述的mbr生物池膜类型包括但不仅限于平板型、管型、螺旋型及中空纤维型等,分离方式包括但不限于反应膜、离子交换膜、渗透膜等;
61.作为本发明的进一步改进,所述的深度滤池包括但不仅限于滤布滤池或生物滤池等。
62.本发明的技术方案之二,采用上述装置进行低氨氮浓度污水主流厌氧氨氧化工艺运行的方法,图1所包括以下三个阶段:
63.第1阶段低氨氮浓度污水经过预处理装置,由格栅或初沉池去除水中大颗粒悬浮物,进入脱碳生物池降解进水中有机碳。第2阶段随后投加抗生素(包括但不限于土霉素、甲硝唑、呋喃唑酮、庆大霉素等)进入亚硝化段中,抑制亚硝化段的硝化细菌(aob和nob),使氨氧化古菌(aoa)为优势菌种,在亚硝化将部分氨氮氧化为亚硝氮,完成亚硝化过程。进入中间沉淀池将出水中污泥沉淀后回流进亚硝化,出水进入抗生素消解池去除抗生素(包括但不限于土霉素、甲硝唑、呋喃唑酮、庆大霉素等)。去除抗生素后进入厌氧氨氧化段进行厌氧氨氧化反应。第3阶段厌氧氨氧化出水经过mbr生物池或深度滤池深度处理,满足排放标准后排放。
64.作为本发明的进一步改进,低氨氮浓度污水主流厌氧氨氧化工艺中废水依次进入大颗粒悬浮物去除装置,脱碳生物池,亚硝化生物池,中间沉淀池,抗生素消解池,厌氧氨氧化池,mbr生物池或深度滤池均以混合均匀的连续流模式运行。
65.作为本发明的进一步改进,低氨氮浓度污水为生活源,工业园,农业源等的一种或多种混合物。
66.作为本发明的进一步改进,所述的低氨氮浓度污水通过物理过滤(格栅)或重力沉降(沉淀池)去除水中的大颗粒;
67.作为本发明的进一步改进,所述的低氨氮浓度污水进入脱碳生物池,采用的生物脱碳技术包括但不限于传统活性污泥法,温度控制在30
‑
35度,无需外加碳源及碱度,水力停留时间5
‑
12h,溶氧控制在0.8
‑
2.0mg/l之间;
68.作为本发明的进一步改进,所述的低氨氮浓度污水脱碳后进入亚硝化生物池,温度控制在32
‑
34度,每日投加1
‑
10mg/l土霉素(或0.1
‑
5mg/l甲硝唑,或20
‑
50mg/l呋喃唑酮,或2
‑
15mg/l庆大霉素等),抑制aob和nob的活性,氨氧化古菌(aoa)为优势菌种。每日投加适当碱度,水力停留时间10
‑
20h,ph 7.0
‑
8.0;
69.作为本发明的进一步改进,所述的亚硝化池中的抗生素种类不做限制,包括但不限于包括但不限于土霉素、甲硝唑、呋喃唑酮、庆大霉素等;
70.作为本发明的进一步改进,所述的亚硝化池出水进入中间沉淀池,水力停留时间10
‑
20h,污泥回流至亚硝化池,中间沉淀池出水进入抗生素消解池;
71.作为本发明的进一步改进,所述的中间沉淀池出水进入抗生素消解池,抗生素消解池投加的抗生素降解材料包括但不限于四环素降解菌或高锰酸钾或tio2光催材料或乙酸钙不动杆菌等,水力停留时间10
‑
20h,投加量为0.1
‑
1mg/l去除水中抗生素;
72.作为本发明的进一步改进,所述的抗生素消解池出水进入厌氧氨氧化池,温度32
‑
34度,无需外加碱度,水力停留时间10
‑
20h,通过自控装置投加酸碱控制ph 7.5
‑
8.0,厌氧状态;
73.作为本发明的进一步改进,所述的厌氧氨氧化出水以中水回用为目的,进入mbr生物池,水力停留时间10
‑
20h,温度30
‑
35度,ph 7.0
‑
8.0;
74.作为本发明的进一步改进,所述厌氧氨氧化出水以排放为目的,进入深度滤池,水力停留时间10
‑
20h。
75.实施例1
76.污水氨氮浓度500
‑
1000mg/l,cod浓度300
‑
500mg/l,ss 150
‑
500mg/l
77.低氨氮浓度污水进入主流厌氧氨氧化工艺,具体工艺流程如下:污水进入预处理系统,格栅将大颗粒悬浮物截留。随后进入活性污泥脱碳生物池停留20小时,cod去除80%,预处理单元出水cod浓度60
‑
100mg/l。由于预处理单元无碳源和碱度投加,氨氮去除10%。预处理单元出水氨氮浓度450
‑
900mg/l。进入亚硝化池,并投入1mg/l抗生素(包括但不限于土霉素、甲硝唑、呋喃唑酮、庆大霉素等),水力停留时间20小时。氨氮50%转化为亚硝氮,亚硝化生物池出水氨氮浓度225
‑
450mg/l,出水亚硝氮浓度225
‑
450mg/l。进入中间沉淀池,水力停留时间5小时,污泥回流至亚硝化池,出水进入抗生素消解池,抗生素(包括但不限于土霉素、甲硝唑、呋喃唑酮、庆大霉素等)浓度去除90%。随后出水进入厌氧氨氧化池,水力停留时间12小时,氨氮亚硝氮去除率均可达到95%以上。出水氨氮及亚硝氮浓度低于10mg/l。
78.实施例2
79.污水氨氮浓度300
‑
500mg/l,cod浓度300
‑
500mg/l,ss 150
‑
500mg/l。
80.同实例1,区别在于亚硝化池水力停留时间10小时,厌氧氨氧化池水力停留时间5小时。
81.实施例3
82.污水氨氮浓度300
‑
1000mg/l,cod浓度100
‑
300mg/l,ss 150
‑
500mg/l。
84.同实例1或实例2。区别在于活性污泥脱碳生物池水力停留时间缩短至5小时以下。