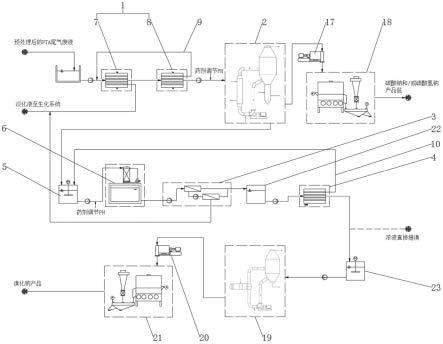
从pta尾气处理废液中回收溴元素及钠元素的装置
技术领域
1.本实用新型涉及对苯二甲酸的氧化废液处理技术领域,尤其是涉及一种从pta尾气处理废液中回收溴元素及钠元素的装置。
背景技术:2.pta(对苯二甲酸)是一种重要的化工原料,其生产过程包括氧化和精制两个过程。在氧化过程中,对原料px(对二甲苯)进行氧化,以醋酸作为溶剂,醋酸钴、醋酸锰作为催化剂,溴化物作为助催化剂,pta氧化尾气经适当处理后,得到含有大量碳酸氢钠及碳酸钠、溴化钠、醋酸钠、有机物及其他杂质的尾气处理废液。
3.目前,这种pta废液由于含有大量污染物,不能直接排放,而是需要在投加大量的硫酸将废液中和后,送至生化系统进行处理,达标排放。对于pta尾气废液的处理主要停留在前处理+调质+生化处理的达标阶段,这种处理方式除溴外,可以达到国家规定的排放标准,仅进行适当处理达标排放,会损失废液中大量可回收利用的高价值物料。pta废液中含有大量的碳酸氢钠及碳酸钠、溴化钠等极具经济价值的物质,通过适当的工艺技术,对废水中的这些物质进行提取,不仅可以获得可观的经济价值,还可降低能耗以及减少二氧化碳排放等环境效益。以某年产250万吨/年pta生产装置为例,产生的尾气处理废液约为210m3/h,其中含有约4.5吨碳酸钠/碳酸氢钠、约0.35吨溴化钠,仅这两项的经济价值每年超过亿元,同时每年可减少33000吨硫酸的消耗,减少15000吨二氧化碳的排放。
4.因此,如何解决现有技术中pta废液仅通过硫酸中和及生化处理排放,易造成碳酸氢钠、碳酸钠及溴化钠等高价值物料损失的技术问题,已成为本领域人员需要解决的重要技术问题。
技术实现要素:5.本实用新型的目的在于提供一种从pta尾气处理废液中回收溴元素及钠元素的装置,解决了现有技术中pta废液仅通过硫酸中和及生化处理排放,易造成碳酸氢钠、碳酸钠及溴化钠等高价值物料损失的技术问题。本实用新型提供的诸多技术方案中的优选技术方案所能产生的诸多技术效果详见下文阐述。
6.为实现上述目的,本实用新型提供了以下技术方案:
7.本实用新型提供的从pta尾气处理废液中回收溴元素及钠元素的装置,包括:第一浓缩组件,用于对废液进行浓缩处理;第一蒸发结晶器,用于对碳酸钠和/或碳酸氢钠进行蒸发结晶;特种纳滤组件,用于对所述第一蒸发结晶器产出的母液进行溴化钠分离处理;第二浓缩组件,用于对溴化钠淡水溶液进行浓缩处理;其中,所述第一浓缩组件、所述第一蒸发结晶器、所述特种纳滤组件和所述第二浓缩组件均相依次连通。
8.进一步地,还包括用于对所述第一蒸发结晶器产出的母液进行稀释和调节ph值处理的母液罐和脱碳塔,所述母液罐的入口与所述第一蒸发结晶器的母液出口相连通,所述母液罐的出口与所述脱碳塔相连通,所述母液罐上或所述母液罐的出口管路上设置有脱料
口,所述脱碳塔的液体出口与所述特种纳滤组件相相连通。
9.进一步地,所述第一浓缩组件包括相连通设置的一级电渗析器和二级电渗析器,所述二级电渗析器的淡化液出口设置有与所述一级电渗析器的入口相连通的第二回流管。
10.进一步地,所述第二浓缩组件包括反渗透组件和/或电渗析组件,所述反渗透组件和/或所述电渗析组件的产水出口设置有与所述母液罐相连通的第一回流管。
11.进一步地,所述第一蒸发结晶器为强制循环结晶结构,所述第一蒸发结晶器包括进料口、闪蒸罐、设置于所述闪蒸罐外部的循环泵以及强制循环换热器,所述闪蒸罐、所述循环泵和所述强制循环换热器依次呈环状连接,所述进料口设置于所述循环泵和所述强制循环换热器之间。
12.进一步地,所述闪蒸罐的下部设置有盐腿,所述盐腿内设置用于对碳酸钠和/或碳酸氢钠的结晶体进行去杂质的淘洗组件,所述盐腿上设置有淘洗进水口和结晶出料口,所述结晶出料口依次连接设置有用于提升结晶体浓度的第一增稠器、用于进行固液分离的第一离心机以及用于对结晶体进行干燥处理的第一干燥设备。
13.进一步地,所述第一离心机为双推料离心脱水机。
14.进一步地,还包括用于对高浓度溴化钠溶液进行蒸发结晶处理的第二蒸发结晶器,其与所述第二浓缩组件相连通。
15.进一步地,所述第二蒸发结晶器的物料出口依次连接设置有用于提升结晶体浓度的第二增稠器、用于进行固液分离的第二离心机以及用于对结晶体进行干燥处理的第二干燥设备。
16.进一步地,所述第一蒸发器为mvr蒸发器,所述第二蒸发结晶器为tvr蒸发器。
17.本实用新型相较于现有技术具有以下有益效果:
18.本实用新型提供的从pta尾气处理废液中回收溴元素及钠元素的装置,通过第一浓缩组件对废液进行初步浓缩,能够提高其内溶质的浓度,然后通过第一蒸发结晶器对浓缩液进行蒸发结晶,将废液中大量的碳酸钠和/或碳酸氢钠结晶出来,达到回收利用的目的,经过结晶后的母液含有大量的高价值溴化钠,通过特种纳滤组件能够将溴化钠从母液中进行分离出来,获得溴化钠淡水溶液,然后通过第二浓缩组件将溴化钠淡水溶液进行进一步浓缩处理,得到高浓度溴化钠溶液,进而通过对高浓度溴化钠溶液进行直接提溴或蒸发结晶处理即可得到高价值的溴化钠产品。通过本实用新型提供的装置对pta氧化尾气处理废液进行处理,能够使废液中大部分溶质被回收,转化为具有高经济价值的碳酸钠和/或碳酸氢钠产品盐以及溴化钠产品盐,对90%以上的盐分进行了回收,剩余的废液也转化为易处理的低含盐废水,处理后的淡化液由于减少了盐分,更有利于后续生化系统进行处理,废水中剩余溴浓度也可达标,使得整体的废水经适当处理后可完全达标排放或回用。
附图说明
19.为了更清楚地说明本实用新型实施例或现有技术中的技术方案,下面将对实施例或现有技术描述中所需要使用的附图作简单地介绍,显而易见地,下面描述中的附图仅仅是本实用新型的一些实施例,对于本领域普通技术人员来讲,在不付出创造性劳动的前提下,还可以根据这些附图获得其他的附图。
20.图1是本实用新型实施例提供的从pta尾气处理废液中回收溴元素及钠元素的装
置的整体结构示意图;
21.图2是本实用新型实施例提供的第一蒸发结晶器的结构示意图;
22.图3是本实用新型实施例提供的第二蒸发结晶器的结构示意图。
23.图中1-第一浓缩组件;2-第一蒸发结晶器;3-特种纳滤组件;4-第二浓缩组件;5-母液罐;6-脱碳塔;7-一级电渗析器;8-二级电渗析器;9-第二回流管;10-第一回流管;11-闪蒸罐;12-循环泵;13-强制循环换热器;14-盐腿;15-淘洗进水口;16-结晶出料口;17-第一离心机;18-第一干燥设备;19-第二蒸发结晶器;20-第二离心机;21-第二干燥设备;22-纳滤产水罐;23-溴化钠储液罐;24-进料口。
具体实施方式
24.为使本实用新型的目的、技术方案和优点更加清楚,下面将对本实用新型的技术方案进行详细的描述。显然,所描述的实施例仅仅是本实用新型一部分实施例,而不是全部的实施例。基于本实用新型中的实施例,本领域普通技术人员在没有做出创造性劳动的前提下所得到的所有其它实施方式,都属于本实用新型所保护的范围。
25.本实用新型的目的在于提供一种从pta尾气处理废液中回收溴元素及钠元素的装置,解决了现有技术中pta废液仅通过硫酸中和及生化处理排放,易造成碳酸氢钠、碳酸钠及溴化钠等高价值物料损失的技术问题。
26.以下,参照附图对实施例进行说明。此外,下面所示的实施例不对权利要求所记载的实用新型内容起任何限定作用。另外,下面实施例所表示的构成的全部内容不限于作为权利要求所记载的实用新型的解决方案所必需的。
27.下面结合具体的实施例对本实用新型的技术方案进行详细的说明。
28.实施例1:
29.参照图1,本实施例提供的从pta尾气处理废液中回收溴元素及钠元素的装置包括第一浓缩组件1、第一蒸发结晶器2、特种纳滤组件3以及第二浓缩组件4,第一浓缩组件1用于对废液进行浓缩处理,第一蒸发结晶器2用于对碳酸钠和/或碳酸氢钠进行蒸发结晶,特种纳滤组件3用于对第一蒸发结晶器2产出的母液进行溴化钠分离处理,第二浓缩组件4用于对溴化钠淡水溶液进行浓缩处理,其中,第一浓缩组件1、第一蒸发结晶器2、特种纳滤组件3和第二浓缩组件4均相依次连通,如此设置,本实用新型从废液的特性出发,通过第一浓缩组件1对废液进行初步浓缩,能够提高其内溶质的浓度,然后通过第一蒸发结晶器2对浓缩液进行蒸发结晶,将废液中大量的碳酸钠和/或碳酸氢钠结晶出来,达到回收利用的目的,经过结晶后的母液含有大量的高价值溴化钠,通过特种纳滤组件3能够将溴化钠从母液中进行分离出来,获得溴化钠淡水溶液,然后通过第二浓缩组件4将溴化钠淡水溶液进行进一步浓缩处理,得到高浓度溴化钠溶液,进而通过对高浓度溴化钠溶液进行直接提溴或蒸发结晶处理即可得到高价值的溴化钠产品。通过本实用新型提供的装置对pta氧化尾气处理废液进行处理,能够使废液中大部分溶质被回收,转化为具有高经济价值的碳酸钠和/或碳酸氢钠产品盐以及溴化钠产品盐,对90%以上的盐分进行了回收,剩余的废液也转化为易处理的低含盐废水,处理后的淡化液由于减少了盐分,更有利于后续生化系统进行处理,废水中剩余溴浓度也可达标,使得整体的废水经适当处理后可完全达标排放或回用。本实用新型在回收pta氧化尾气处理废液中具有经济价值组分、实现较高经济价值的同时,也可
降低传统pta氧化尾气处理废液的处理工艺中硫酸的消耗以及二氧化碳的排放,具有变废为宝、节能减排的环保意义,解决了现有技术中pta废液仅通过硫酸中和及生化处理排放,易造成碳酸氢钠、碳酸钠及溴化钠等高价值物料损失的技术问题。
30.需要说明的是,纳滤是一种介于反渗透和超滤之间的压力驱动膜分离过程,纳滤膜孔径在几个纳米左右,可以截留分子量大的离子,且纳滤膜的特殊结构允许某些单价离子通过但截留二价以上的多价离子,而通过特种纳滤组件3的加强过滤,克服了普通纳滤膜对醋酸根截留率低的特点,可在有效地截流溶液中的硫酸根、醋酸根等离子的同时,保持对溴离子有较好通透性,溶液中的溴化钠基本可透过此特种纳滤组件3,使用此特种纳滤组件3可以达到将溴化钠与其他杂质分离的效果。脱碳后的母液经特种纳滤分离后,得到含有高纯度溴化钠的纳滤产水,纳滤浓水端则为含醋酸钠、硫酸钠及少部分溴化钠的浓缩液,纳滤浓缩液水量较小,没有重新提取溶质的价值,因此,能够将其与一级电渗析器7的淡化液混合后排至生化系统进行生化处理,含高纯度溴化钠的纳滤产水进入纳滤产水罐22中进行储存,以便进行后续处理。
31.实施例2:
32.参照图1,本实施例在实施例1的基础上,对从pta尾气处理废液中回收溴元素及钠元素的装置进行了进一步地限定。本实用新型还包括用于对第一蒸发结晶器2产出的母液进行稀释和调节ph值处理的母液罐5和脱碳塔6,母液罐5的入口与第一蒸发结晶器2的母液出口相连通,以便于从第一蒸发结晶器2中分离出的母液能够储存至母液罐5中进行进一步地处理。母液罐5的出口与脱碳塔6相连通,母液罐5上或母液罐5的出口管路上设置有用于投放酸性物质的投料口,以便于投放酸性物质调节稀释母液的ph值,脱碳塔6的液体出口与特种纳滤组件3相连通,如此设置,从第一蒸发结晶器2中分离出的母液能够储存至母液罐5中,对母液能够在母液罐5中进行稀释,并通过投料口投放酸性物质调节母液的ph值至酸性状态,能够使母液中的碳酸根和/或碳酸氢根转化为碳酸,碳酸在水中不稳定,易分解为水和二氧化碳。然后将酸性母液输送至脱碳塔6进行脱碳处理,具体地,脱碳塔6采用填料式,稀释酸化后的母液从脱碳塔6顶部进入,经过布水装置后进入填料层,脱碳塔6底部设置了机械风机将空气从脱碳塔6底部引入,并与水流形成逆向的空气流,酸化后的母液中,碳酸分解为二氧化碳和水,且二氧化碳随着高速流动的空气脱离溶液散入大气中,使水中碳酸根的离子平衡向着生成二氧化碳的方向移动,从而使水中的碳酸根和/或碳酸氢根以二氧化碳的形式被脱除。脱碳后的母液稀释液进入脱碳塔6底部的脱碳水池中,后续转入特种纳滤组件3中进行进一步处理。
33.作为本实用新型实施例可选地实施方式,第一浓缩组件1包括相连通设置的一级电渗析器7和二级电渗析器8,二级电渗析器8的淡化液出口设置有与一级电渗析器7的入口相连通的第二回流管9,如此设置,二级电渗析器8的淡化液能够通过第二回流管9回流至一级电渗析器7的入口处,重新进行电渗析循环,能够极大地提高对废液中溶质的回收率,避免浪费。
34.作为本实用新型实施例可选地实施方式,第二浓缩组件4包括反渗透组件和/或电渗析组件,反渗透组件和/或电渗析组件的产水出口设置有与母液罐5相连通的第一回流管10,如此设置,反渗透组件和/或电渗析组件均能够对特种纳滤组件3的流出的溴化钠淡水溶液进行高效浓缩处理,能够提高溴化钠淡水溶液的浓度形成高浓度溴化钠溶液,并能减
少后续工艺的处理负荷,高浓度溴化钠溶液可排出至溴化钠储液罐23中进行储存。而且第二浓缩组件4的产水出口流出的清净淡水能够通过第一回流管10回流至母液罐5内,对母液进行稀释,即直接使用本系统产水对母液进行稀释,减少了外水的输入。
35.参照图1-2,作为本实用新型实施例可选地实施方式,第一蒸发结晶器2为强制循环结晶结构,第一蒸发结晶器2包括进料口24、闪蒸罐11、设置于闪蒸罐11外部的循环泵12以及强制循环换热器13,闪蒸罐11、循环泵12和强制循环换热器13依次呈环状连接,进料口24设置于循环泵12和强制循环换热器13之间,如此设置,二级电渗析器8中流出的浓缩液进入到第一蒸发结晶器2的壳体内与结晶浓缩液混合,循环泵12能够提供驱动力,使第一蒸发结晶器2内的浆液流过强制循环换热器13,换热器壳体侧蒸汽经冷凝放出的热量为换热管内侧的循环结晶浓缩液提供热量,能够将浓缩液的温度加热至70~90℃,换热器的水位静水压头使管道内的液体不至于沸腾。第一蒸发结晶器2还可配置真空和冷凝装置对系统进行减压,换热后的浓缩液返回结晶器的壳体后由于压力降低将发生闪蒸,产生水蒸气并释放出热量。产生的水蒸气从闪蒸罐11顶部逸出进入冷凝器冷凝,其中,若第一蒸发结晶器2采用mvr蒸发,则进入蒸汽压缩机,蒸汽压缩机消耗电能将水蒸气加压后转入强制循环换热器13的加热室作为结晶器的热源,蒸汽换热后得到的冷凝水可作为洁净的工厂用水进行回用。随着蒸发的进行,浓缩液的浓度逐渐增加,当浓缩液达到结晶饱和点时,一水碳酸钠和/或碳酸氢钠从结晶器中的浓缩液中析出。
36.进一步地,闪蒸罐11的下部设置有盐腿14,盐腿14内设置用于对碳酸钠和/或碳酸氢钠的结晶体进行去杂质的淘洗组件,盐腿14上设置有淘洗进水口15和结晶出料口16,如此设置,随着析出的盐结晶体不断聚集,盐结晶体将会沉降到盐腿14处,盐腿14处通过设置逆流向上的淘洗组件,能够利用淘洗进水口15的进水淘洗落下的结晶盐,颗粒较小的结晶盐被淘洗水溶解并随水流向上移动,颗粒较大的盐颗粒落到盐腿14底部的结晶出料口16。结晶出料口16依次连接设置有用于提升结晶体浓度的第一增稠器、用于进行固液分离的第一离心机17以及用于对结晶体进行干燥处理的第一干燥设备18,如此设置,结晶出料口16处颗粒较大的盐随浆液经泵转入第一增稠器中进行增稠,能够使其浆液内结晶体的浓度达到20%-50%(表观固液比)后,进入第一离心机17中进行离心分离,优选地,第一离心机17可采用双推料离心脱水机,进料为含固量为20%-50%(表观固液比)的盐浆液,经离心分离后,可以得到自由水含量≤5%的一水碳酸钠和/或碳酸氢钠结晶体,第一离心机17内分离出的离心母液可通过管路返回到第一蒸发结晶器2中继续浓缩,而离心分离出的结晶体被送入第一干燥设备18内进行干燥。
37.其中,第一干燥设备18主要包含带振动功能的流化床干燥器、空气换热器、旋风分离器、布袋除尘机、送风机以及引风机。含一定自由水和结晶水的一水碳水钠和/或碳酸氢钠经进入布料器的分散作用均匀地进入振动流化床,与经过蒸汽换热后的热空气充分接触,在流化床干燥器内产生流态化,在此状态下脱除结晶水和自由水,脱除的水分随热空气进入旋风分离器和布袋除尘机后排至外界大气,高温的干燥盐颗粒则经过低温空气换热降温后,从流化床干燥器的出口流出,通过流化床干燥器干燥后可得到纯度>99%的碳酸钠和/或碳酸氢钠产品盐。
38.参照图1和图3,作为本实用新型实施例可选地实施方式,本实用新型还包括用于对高浓度溴化钠溶液进行蒸发结晶处理的第二蒸发结晶器19,其与第二浓缩组件4相连通,
即通过第二蒸发结晶器19为溴化钠蒸发结晶器,其能够对高浓度溴化钠溶液进行蒸发结晶处理。第二蒸发结晶器19的结构与第一蒸发结晶器2的结构相近,第二蒸发结晶器19也主要包括闪蒸罐11、循环泵12、强制循环换热器13、蒸汽热泵、蒸汽冷凝器及真空泵,高浓度溴化钠溶液进入到结晶器的壳体内与结晶浓缩液混合,循环泵12使结晶器内的浆液流过强制循环换热器13,在此获得来自加热器壳体侧蒸汽的热量。强制循环换热器13的排出管道内的水位静水压头可抑制管道内的沸腾,当换热后的浆液返回结晶器壳体时将发生闪蒸,产生水蒸气并释放出热量,产生的水蒸气从闪蒸罐11顶部逸出并进入蒸汽热泵,在蒸汽热泵中通过动力蒸汽射流增压后,进入强制循环换热器13的加热室作为结晶器的热源,蒸汽换热后得到的冷凝水可作为洁净的工厂用水进行回用。
39.进一步地,第二蒸发结晶器19的物料出口依次连接设置有用于提升结晶体浓度的第二增稠器、用于进行固液分离的第二离心机20以及用于对结晶体进行干燥处理的第二干燥设备21,如此设置,随着蒸发的进行,浓缩液的浓度逐渐增加,当浓缩液浓度达到溴化钠结晶饱和点时,溴化钠晶体从结晶器中的浓缩卤液中析出。当卤液中的晶体比例达到10%-25%(表观固液比)后,能够由浆料泵将卤液转入第二增稠器中增稠,使其晶体浓度达到20%-50%(表观固液比)后,进入第二离心机20中对其进行离心分离,可以得到自由水含水率≤5%的溴化钠结晶体,第二离心机20中的离心母液可返回至第二蒸发结晶器19中继续浓缩,而离心分离出的溴化钠结晶体可被送入到第二干燥设备21内进行干燥,能够进一步去除溴化钠结晶体中的水分,得到纯度>98.5%的溴化钠产品盐。
40.优选地,第二蒸发结晶器19为tvr蒸发器,以适应高浓度溴化钠溶液纯度高及流量小的特点。
41.在本实用新型的描述中,需要说明的是,除非另有说明,“多个”的含义是两个或两个以上;术语“上”、“下”、“左”、“右”、“内”、“外”、“前端”、“后端”、“头部”、“尾部”等指示的方位或位置关系为基于附图所示的方位或位置关系,仅是为了便于描述本实用新型和简化描述,而不是指示或暗示所指的装置或元件必须具有特定的方位、以特定的方位构造和操作,因此不能理解为对本实用新型的限制。此外,术语“第一”、“第二”、“第三”等仅用于描述目的,而不能理解为指示或暗示相对重要性。
42.在本实用新型的描述中,还需要说明的是,除非另有明确的规定和限定,术语“安装”、“相连”、“连接”应做广义理解,例如,可以是固定连接,也可以是可拆卸连接,或一体地连接;可以是机械连接,也可以是电连接;可以是直接相连,也可以通过中间媒介间接相连。对于本领域的普通技术人员而言,可视具体情况理解上述术语在本实用新型中的具体含义。
43.以上所述,仅为本实用新型的具体实施方式,但本实用新型的保护范围并不局限于此,任何熟悉本技术领域的技术人员在本实用新型揭露的技术范围内,可轻易想到变化或替换,都应涵盖在本实用新型的保护范围之内。因此,本实用新型的保护范围应以所述权利要求的保护范围为准。