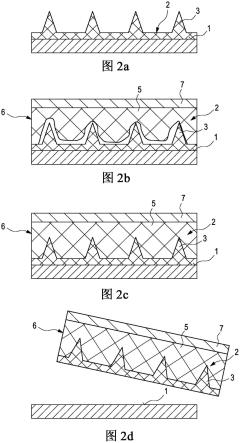
1.本发明涉及一种用于从表面去除覆盖层的方法,特别是从表面上去除由于环境影响而变脆的覆盖层。
背景技术:2.在现有技术中已知为了各种目的而将覆盖层(例如以自粘膜形式)施加到诸如飞机外表层的表面上。除了使用适当设计的膜来施加标志、字样或其他图形元素外,空气动力学功能膜的使用也越来越多。
3.空气动力学功能膜在现有技术中以各种形式和应用领域为人所知,并且经常用于降低环流的物体的表面上的壁剪切应力。为此,空气动力学功能膜通常具有微结构化表面。在此,普遍的微结构是所谓的肋条结构,其具有非常小的、基本上沿着主流动方向延伸的肋片。如果将相应的肋条结构应用到飞机的外表层上,则由此能够减少飞机的流动阻力,从而减少燃料消耗。
4.由于重量的原因,用于安放到飞机外表层的膜通常很薄。同时,它们也受到重大的环境影响。除了空气的过流,在空气中夹带沙子或冰等颗粒和可能对膜或其空气动力学功能表面造成机械损坏外,膜还经常暴露在强烈的太阳辐射下,尤其在处于巡航高度的商用飞机中。
5.由于实际发生的损坏,特别地,空气动力学功能膜需定期更换。然而,已经表明,由于厚度小并且由于在飞机运行期间阳光的强烈辐射,施加在飞机外表层上的膜变得易碎且通常很难去除。在此,目前只能通过非常耗时的手动实施的化学或机械方法才能在不损坏外表层的情况下进行完全且无残留的去除。对健康或环境有害的灰尘和/或化学残留物也可能在相应的方法中产生。
6.类似地,这同样适用于油漆被施加到其表面上并且其中例如形成了所需的微结构的覆盖层。而这些覆盖层也可能会变脆,且必须先费力地去除,然后才能更新。
7.然而,除了在飞机外表层上描述的应用外,相应的覆盖层也用于其他表面,例如在风能设施的转子叶片或高速列车上,它们暴露于类似的环境影响下并且也同样必须去除损坏后才能将它们更新。
技术实现要素:8.因此,本发明的目的是提供一种相对于现有技术改进的方法,该方法用于从表面去除覆盖层,特别是由于环境影响而变得易碎的覆盖层。
9.该目的通过根据独立权利要求的方法实现。有利的改进方案是从属权利要求的主题。
10.因此,本发明涉及一种用于从表面去除覆盖层的方法,包括以下步骤:
[0011]-在待分离的覆盖层上大面积地施加合适地选择的剥离剂,以形成材料配合的连接,使得在剥离剂与待分离的覆盖层之间的连接强于待分离的覆盖层与表面之间的连接;
以及
[0012]-将剥离剂连同附着在其上的待分离的覆盖层一起剥离。
[0013]
首先,解释在本发明范围内使用的一些术语。
[0014]
如果第一连接承受了负载(第二连接在承受该负载时失效),则第一连接比第二连接“更强”。例如,在粘合连接的情况下,为了释放第一连接而必须克服的第一连接的粘合力f
h1
大于第二连接的粘合力f
h2
(f
h1
》f
h2
)。
[0015]
相反,如果第一连接在相同负载下弯曲而第二连接仍然保持,则认为第一连接比第二连接“更弱”。在粘合连接的情况下,第一连接的粘合力f
h1
小于第二连接的粘合力f
h2
(f
h1
《f
h2
)。
[0016]
本发明已经认识到,在首先施加剥离剂时,该剥离剂与待去除的覆盖层牢固连接,使得接下来在剥离该剥离剂时覆盖层粘附在剥离剂上并进而与剥离剂一同剥离,由此能够去除在表面上施加的不能被直接剥离的覆盖层,特别是该覆盖层因为环境影响而变得易碎或已经“变碎”。在此,剥离所需的拉伸强度能够仅由剥离剂产生,因此待剥离的覆盖层的拉伸强度和/或其脆性程度不再重要。
[0017]
因此,在剥离剂被剥离时,待分离的覆盖层实际上粘附到剥离剂上并因此被从表面去除,需要使剥离剂与待分离的覆盖层之间的连接强于待分离的覆盖层与表面之间的连接。如果有足够的关于待分离的覆盖层与表面的连接信息(例如所使用的粘合剂),则能够毫无问题地选择合适的剥离剂,但也能够通过直接在待分离的覆盖层上进行简单测试来确定。
[0018]
剥离剂能够是至少在一侧自粘的、平坦的剥离体并且该剥离体为了施加而利用自粘侧压到待分离的覆盖层上。通过按压,在剥离体与待分离的覆盖层之间产生期望的、对于进一步的工艺所需的材料配合的连接。
[0019]
原则上,剥离体能够是自粘剥离膜。然而,为了在即使待分离的覆盖层的表面被损坏和/或微结构化的情况下也能够在剥离体与待分离的覆盖层之间产生平面连接,优选剥离体在按压方向上是能变形的。如果随后将剥离体压在待分离的覆盖层上,它能够紧贴在其上并在整个表面上与之连接,而不管待分离的覆盖层表面是否存在损坏和/或微结构化。在此,剥离体能够是塑性和/或弹性变形的。
[0020]
特别是在能变形的剥离体的情况下,剥离体的拉伸强度可能不足以能够将剥离体连同粘附在其上的覆盖层一起从表面上毫无问题地剥离。在这种情况下特别优选的是,剥离体在远离待分离的覆盖层的一侧上具有抗拉的剥离层,优选剥离膜。利用相应的剥离层,能够增加剥离体的抗拉强度,从而实现剥离剂连同在其上附着的待分离的覆盖层的根据本发明所提供的剥离。
[0021]
作为使用剥离体作为剥离剂的替代方案,也能够设置能硬化物质作为剥离剂,其在硬化时与待分离的覆盖层材料配合地连接。硬化后,该物质与粘附在其上的待分离的覆盖层一起形成适于剥离的剥离剂。
[0022]
在此,能硬化物质在初始状态下能够是液体或凝胶状的。因此能够容易地将物质大面积地施加到待分离的覆盖层上。硬化后,该物质为固体。
[0023]
网或织物也能够大面积地引入尚未硬化的物质中,其完全被尚未硬化的物质所包围。物质硬化后,网或织物能够增加剥离剂的抗拉强度。
[0024]
不管剥离剂是如何形成的,优选以这样的方式选择:即剥离剂与表面之间的任何连接都弱于剥离剂与待分离的覆盖层之间的连接。还优选的是,剥离剂与表面之间的任何连接也弱于待分离的覆盖层与表面之间的连接。由此确保即使在待分离的覆盖层中故意遗漏或对待分离的覆盖层造成重大损坏的情况下,在按压时剥离剂与表面直接接触的区域中,剥离剂的剥离没有任何问题,并且特别是不会损坏表面。
[0025]
已证明根据本发明的方法特别良好地适用于剥离具有微结构化表面的覆盖层。这尤其适用于覆盖层具有肋条结构——即肋条状表面结构的情况。由于本发明的用于剥离覆盖层的方法不依赖于覆盖层本身的抗拉强度,待分离的覆盖层能够被设计得特别薄进而很轻,并且特别地没有在现有技术中通常额外设置的抗拉附加层。
[0026]
待分离的覆盖层能够是粘接到表面的薄膜或施加到表面的漆层,如有必要分别具有冲压在其上的微结构化的表面。该表面尤其能够是飞机、高速列车或风能设备转子叶片的外表层。
附图说明
[0027]
现在将参照附图根据优选实施例以示例的方式描述本发明。图中示出:
[0028]
图1a-图1d:根据本发明的方法的第一实施例的示意图;
[0029]
图2a-图2d:根据本发明的方法的第二实施例的示意图;和
[0030]
图3a-图3c:根据本发明的方法的第三实施例的示意图。
具体实施方式
[0031]
在图1a中,为了说明根据本发明的方法的第一实施例,商用飞机的外表层的一部分被显示为表面1,在该表面上借助于转移膜(未示出),单个肋条3,它们虽然不直接相互连接,但在本发明的含义内共同形成待分离的膜状覆盖层2。
[0032]
为了分离覆盖层2,首先将剥离体5作为剥离剂6施加到覆盖层2上(图1b),并且随后按压在覆盖层2或表面1上。由于剥离体5是能变形的并且在面向表面1的一侧上是自粘的,所以在剥离体5与覆盖层2之间实现了大面积或全面积的材料配合的连接(图1c)。在此,剥离体5的自粘性被选择为,使得剥离体5与覆盖层2之间的材料配合的连接强于覆盖层2与表面1之间的连接。同时,剥离体5与表面1之间的材料配合的连接应在各个肋条3之间的覆盖层2的区域中足够小,以便后续不会损坏有规律地形成表面1的最外层的油漆。
[0033]
如果完全施加并挤压剥离体5,剥离体5能够作为剥离剂6从表面1上剥离,其中,根据前边所述的在表面1、覆盖层2与剥离体5之间的单个连接关系,覆盖层2粘附在剥离剂6上并因此从表面1上去除(图1d)。
[0034]
图2示出了根据本发明的方法的第二实施例。在表面1(例如飞机的外表层)上,包括肋条3的具有微结构化表面的基本贯穿的膜被布置作为覆盖层2,该覆盖层应被去除(图2a)。
[0035]
为了分离覆盖层2(与根据图1的实施例相比),首先将作为剥离剂6的剥离体5利用其自粘侧施加到覆盖层2上(图2b),并且随后将其按压在覆盖层2或表面1上,从而在剥离剂6与覆盖层2之间生成材料配合的连接(图2c)。在此,与覆盖层2与表面1之间的连接有关的连接特性对应于前面的实施例,因此参考对应的设计方案。
[0036]
在背离表面1的一侧,剥离剂6具有与剥离体5不可分离地连接或与其一体设计的剥离膜7,该剥离膜提高了剥离剂6的抗拉强度,从而简化了在图2d中描绘的剥离剂6连同在其上粘附的覆盖层2的剥离。
[0037]
图3示出了根据本发明的方法的第三实施例。
[0038]
在该实例中,具有肋片3的覆盖层2借助载体膜4紧固到表面1(飞机的外表层),其中,覆盖层2与载体膜4之间的连接强于载体膜4与表面1之间的连接。
[0039]
在该实施例中,将硬化凝胶状物质8作为剥离剂6施加到覆盖层2上,并且在硬化时与待分离的薄膜2形成材料配合的连接(图3b)。由此产生的剥离剂6与覆盖层2之间的材料配合的连接强于覆盖层2与表面1之间的连接,使得当物质8完全硬化后,在剥离剂6被剥离时覆盖层2粘附在其上并且因此连同载体膜4一起从表面1被去除(图3c)。