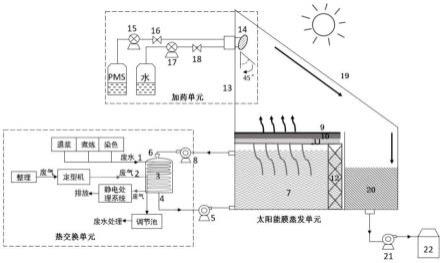
1.本发明涉及一种利用余热及太阳能膜蒸发对印染废水再生的系统及方法,属于废水膜处理的技术领域。
背景技术:2.随着水资源的短缺和更严格的排放标准,开发废水处理技术尤为迫切。而纺织印染行业作为能源密集型产业之一,同时也是用水量和废水排放量大的工业之一。印染废水色度深,有机物污染量高,毒性强、且难以生物降解。其中在染色过程中80%的水作为废水排放。
3.印染行业在生产过程中要消耗和产生了大量的热能。工艺过程中能源消耗均以废气、废水的方式流失到环境中。退浆、煮练和染色工艺的废水温度高达 70~90℃,热定形产生的废气温度在120~180℃。在处理印染废水的同时,充分利用好工艺产生的热能,是实现印染废水低能耗处理的重要手段。
4.太阳能蒸发系统作为一种新型的清洁能源得到了越来越多的关注。通过在膜上沉积适量的光热材料使膜兼具光热转化功能。光热膜在自然光辐射下,将表面吸附的废水蒸发,通过收集器将冷凝的水蒸汽收集,从而实现废水处理及水回收。将光热蒸发系统与印染余热结合,处理印染废水,在光照充足的地区具有很大的应用价值和优势,如新疆地区环境温度为33~38℃,全年日照时数为2600~3400 小时,全年太阳能总辐射量每平方米为5000~6490兆焦耳。然而,光热废水处理存在膜表面盐结晶、光热材料热转化效率低、热损失大和挥发性有机物截留低等问题。如何提高光热废水处理效率是光热印染废水处理的关键。
技术实现要素:5.本发明的目的是提供一种利用余热及太阳能膜蒸发对印染废水再生的系统及方法,利用清洁能源对印染废水进行处理。
6.为了实现上述目的,本发明提供了一种利用余热及太阳能膜蒸发对印染废水再生的系统,其特征在于:包括热交换单元、太阳能膜蒸发单元和加药单元;
7.所述热交换单元包括两相换热器,所述两相换热器设有废水进口和废气进口;
8.所述太阳能膜蒸发单元包括:
9.并排设置的集水池和纯水收集槽;
10.设于集水池上方的光热膜蒸发器;
11.设于光热膜蒸发器上方的冷凝装置,所述冷凝装置与纯水收集槽连接;
12.所述加药系统包括与喷淋头连接的pms输送管道和纯水输送管道,所述 pms输送管道和纯水输送管道并联,所述pms输送管道上设有输送泵三和pms 阀;所述纯水输送管道上设有输送泵四和纯水阀;
13.所述两相换热器的底部设有与集水池下端相连接的出液口,所述出液口与集水池下端通过输送泵一连接;
14.所述两相换热器的顶部设有与集水池上端相连接的进液口,所述进液口与集水池上端通过输送泵二连接;
15.所述太阳能膜蒸发单元与加药系统之间通过喷淋头连接,所述喷淋头设于光热膜蒸发器与冷凝装置之间,用于向光热膜蒸发器上喷洒pms或纯水;
16.所述光热膜蒸发器底部设有自动升降杆,并利用plc与加药系统联动。
17.优选地,所述光热膜蒸发器从上至下依次包括光热膜、吸水纸和用作漂浮体的泡沫层,所述泡沫层中设有导水通道,所述泡沫层底部设有自动升降杆;所述吸水纸的材质为中性棉纤维,厚度为0.5~1.5mm;所述泡沫层的材质为聚乙烯发泡棉,其厚度为2~5mm;所述导水通道为吸水纸条。
18.优选地,所述冷凝装置为斜置于集水池和纯水收集槽上方的石英玻璃、 pmma塑料板、pc塑料板或pp塑料板,其透光率≥90%,厚度为0.1-3mm;所述冷凝装置内表面设有涂覆的疏水材料,其厚度为1-10μm,光热膜蒸发器集热作用下水受热蒸发产生蒸汽,蒸汽与冷凝装置内表面接触凝结成水滴后,在重力作用下流到纯水收集槽。
19.优选地,所述热交换单元的热源来自于印染生产过程中的高温介质,包括:退浆、煮炼和染色产生的超过80℃的废水,以及定型机产生的120~180℃的废气。
20.优选地,所述光热膜为负载有碳基mof材料的光热膜,所述碳基mof材料中的碳基为石墨烯、碳纳米管和碳化木制材料中的一种,所述碳基mof材料的负载量为0.2~1mg/cm2。
21.优选地,所述碳基mof材料的制备方法包括如下步骤:
22.步骤1:采用原位生长法在碳基材料表面长zif层,将碳基材料分散在n-n 二甲基甲酰胺和甲醇的混合液中,超声处理,得到碳基混合液;
23.步骤2:将六水合硝酸锌分散于甲醇中得到溶液a,将二甲基咪唑分散于甲醇中得到溶液b;
24.步骤3:在上述碳基混合液中依次加入溶液a和溶液b,搅拌反应,反应结束后离心,并用甲醇洗涤,取下层液,将下层液进行真空过滤后在真空干燥箱中烘干,得到碳基mof材料。
25.本发明还提供了一种利用余热及太阳能膜蒸发对印染废水再生的方法,采用权利要上述的系统进行再生处理,具体包括:待处理印染废水进入热交换单元进行预热,预热后的印染废水通过出液口输送到太阳能膜蒸发单元的集水池进行处理,光热膜蒸发器受太阳光照射将光能转换为热能,集水池中的水进入光热膜蒸发器受热蒸发,蒸汽从光热膜材料的膜孔中逃逸,与上方的冷凝装置接触凝结成水滴,水在重力作用下流到纯水收集槽进行收集,在此期间加药系统交替喷洒用于降解印染废水中有机物的pms和用于清洗光热膜的纯水,纯水冲洗时自动升降杆自动抬高膜一侧,冲洗结束后回到初始位置。
26.优选地,所述印染废水先是流经两相换热器的水-水热交换区域,然后气-水热交换区域,达到预定温度后流出两相换热器,进入太阳能膜蒸发单元。
27.优选地,所述再生处理过程中,白天利用太阳能界面蒸发原理,热交换时间短,控制两相换热器使待处理印染废水流出温度为40~60℃,通过太阳光加热光热膜表面进行二次加热,界面蒸发-冷凝实现废水再生;夜间利用膜蒸馏原理,热交换时间长,控制两相换热器使待处理印染废水流出温度为60~80℃,膜蒸馏
ꢀ‑
冷凝实现废水再生。
28.优选地,所述加药系统喷洒药剂根据plc编程进行交替喷洒,所述pms的浓度为0.2~2mm,每30min喷洒一次pms,每次10min,喷淋头旋转角度为 0~45
°
;当水蒸发速率降低20~40%时,用纯水冲洗膜表面,冲洗5min,冲洗时升降器自动抬高膜一侧至60
°
,冲洗结束后回到初始位置。
29.本发明的原理:
30.热交换单元利用印染工段中的高温废水和定型废气的余热对低浓度待处理印染废水进行加热;太阳能膜蒸发单元利用的光热材料为碳基mof材料,利用 mof材料多孔及隔热的特点提高光吸收抑制热损失,从而有效提高蒸发通量和光热转化效率;加药单元采用间歇式喷洒pms和水到光热界面,利用热活化原理产生强氧化性的自由基来降解易挥发性有机物,从而提高再生水的水质,水淋洗作用还可以减少表面盐结垢,提高运行效率。本发明的系统和方法处理效率高,产水水质好,运行成本低,适合光照充足和缺水区域推广使用。
31.与现有技术相比,本发明的有益效果在于:
32.(1)本发明巧用热交换系统对印染废水的余温加以利用,作为太阳能膜蒸发系统的补充温度,不仅提高了废热的利用率,减少了热量输入,还提高了蒸发温度和效率;
33.(2)本发明采用碳基金属有机骨架(mof)材料,改善了碳基材料散热快的缺点,将碳基材料用zif-8包裹起来,利用mof多孔及隔热的特点,增加光吸收的同时将光转化的热量限制在碳基材料层,降低热量向周围空气的传递,从而减少热损失,实现高效的光热蒸汽转化;
34.(3)本发明在太阳能膜蒸发系统连接加药系统,投加pms降解有机物,在光热或废水余热条件下会活化过硫酸根产生大量具有强氧化性的硫酸根自由基 (so4
·
);相比于传统高级氧化工艺所生产的羟基自由基(
·
oh),so4
·
具有更高的氧化能力,能够有效地将膜表面污染物及挥发性有机物转化为低毒、易被生物降解的小分子物质。整合高级氧化和光热废水处理极大地提高了系统对有毒挥发性有机物的拦截效率,降低产水毒性。
附图说明
35.图1为本发明太阳能膜蒸发系统装置示意图;
36.附图标记说明:1.废水进口;2.废气出口;3.两相换热器;4.出液口;5.输送泵一5;6.进液口;7.集水池;8.输送泵二;9.光热膜;10.吸水纸;11.泡沫层; 12.自动升降杆;13.隔热层;14.淋喷头;15.输送泵三;16.pms阀;17.输送泵四;18.纯水阀;19.冷凝装置;20.纯水收集槽;21.输出泵;22.储水池。
具体实施方式
37.为使本发明更明显易懂,兹以优选实施例,并配合附图作详细说明如下。
38.实施例1
39.一种利用余热及太阳能膜蒸发对印染废水再生的系统,如图1所示,包括热交换单元、太阳能膜蒸发单元和加药单元;
40.所述热交换单元包括两相换热器3,所述两相换热器3设有废水进口1和废气进口2;
41.所述太阳能膜蒸发单元包括:
42.并排设置的集水池7和纯水收集槽20;
43.设于集水池7上方的光热膜蒸发器;
44.设于光热膜蒸发器上方的冷凝装置19,所述冷凝装置与纯水收集槽20连接;
45.所述加药系统包括与喷淋头14连接的pms输送管道和纯水输送管道,所述 pms输送管道和纯水输送管道并联,所述pms输送管道与pms桶连接,所述纯水输送管道与纯水桶连接;所述pms输送管道上设有输送泵三15和pms阀 16;所述纯水输送管道上设有输送泵四17和纯水阀18。
46.所述两相换热器3的底部设有与集水池7下端相连接的出液口4,所述出液口4与集水池7下端通过输送泵一5连接;
47.所述两相换热器3的顶部设有与集水池7上端相连接的进液口6,所述进液口与集水池7上端通过输送泵二8连接;
48.所述太阳能膜蒸发单元与加药系统之间通过喷淋头14连接,所述喷淋头14 设于光热膜蒸发器与冷凝装置19之间,用于向光热膜蒸发器上喷洒pms或纯水;
49.所述光热膜蒸发器底部设有自动升降杆12,并利用plc与加药系统联动。自动升降杆运行时与喷淋头联动,喷洒pms时,升降杆不运行;喷淋纯水时,升降器运行,并抬高光热膜蒸发器一侧至60
°
;喷淋结束时,升降杆恢复初始位置。
50.所述光热膜蒸发器从上至下依次包括光热膜9、吸水纸10和用作漂浮体的泡沫层11,所述泡沫层中设有导水通道,所述泡沫层11底部设有自动升降杆12;所述吸水纸的材质为中性棉纤维,厚度为0.5~1.5mm;所述泡沫层的材质为聚乙烯发泡棉,其厚度为2~5mm;所述导水通道为吸水纸条。
51.所述冷凝装置19为斜置于集水池和纯水收集槽上方的石英玻璃(也可选用 pmma塑料板、pc塑料板或pp塑料板),其透光率≥90%,厚度为0.1-3mm;所述石英玻璃内表面设有涂覆的疏水材料,疏水材料选用氟硅材料或高分子熔体聚合物,其厚度为1-10μm,光热膜蒸发器集热,水受热蒸发发产生蒸汽,与冷凝装置内表面接触凝结成水后,在重力作用下流到纯水收集槽。石英玻璃一侧架设于竖立的隔热层13上,相对立的一侧架设在纯水收集槽的侧壁上,所述隔热层13采用导热系数低的聚苯乙烯或气凝胶材料制成,厚度为2~5cm,其架设于集水池的侧壁上。
52.所述纯水收集槽20通过输出泵21连接储水池22。
53.所述热交换单元的热源来自于印染生产过程中的高温介质,包括:退浆、煮炼和染色产生的超过80℃的废水,以及定型机产生的120~180℃的废气。
54.所述光热膜为负载有碳基mof材料的光热膜,其吸光率》80%,光热膜的制备方法是:将碳基mof材料溶于1wt%的pvdf溶液中,然后通过滴加-抽滤或喷涂的方法将碳基mof材料负载于光热基膜上,其中,所述碳基mof材料中的碳基为石墨烯(也可以选用碳纳米管和碳化木制材料中的一种),所述碳基 mof材料的负载量为0.2~1mg/cm2,其制备方法如下:
55.①
采用原位生长法在碳基材料表面长zif层,将0.1g碳基材料分散在40 mln-n二甲基甲酰胺(dmf)和10ml甲醇的混合液中,超声1h;
②
将六水合硝酸锌分散于甲醇中得到六水合硝酸锌溶液(0.1m),将二甲基咪唑分散于甲醇中得到二甲基咪唑溶液(0.2m);
③
在超
声后的碳基混合液中先加入六水合硝酸锌溶液随后加入二甲基咪唑溶液,500rpm下搅拌5h。所得的混合液在3000 rpm下进行离心,并用甲醇洗涤三次,取下层液。将下层液进行真空过滤后在真空干燥箱中烘干,得到碳基mof材料。
56.其中,利用两相换热器把印染工艺产生的高温介质中的热量交换出来,排出的高浓度废水经过调节池排到废水处理系统;剩余的废气通过静电处理系统处理后排放。
57.实施例2
58.某印染有限责任公司是国内较大规模的印染企业之一。其染色废水量约为 1000m3/d,cod达2700mg/l-4400mg/l,色度达500-600(目视比色法)。该厂为了实行节能减排,对废水进行资源化处理。后通过预实验,利用余热及太阳能膜蒸发系统,对部分生产线印染废水进行实验室处理。待处理印染废水进入热交换单元,退浆、煮炼和染色产生的废水从废水口进入,定型机产生的废气从废气口进入,共同进入两相换热器,控制两相换热器使料液流出温度为40~60℃,预热后的印染废水输送到集水池,在太阳光作用下蒸发,蒸汽从光热膜材料中的膜孔中逃逸,与冷凝结构接触后凝结成水滴,在重力作用下流到纯水槽中。其中,每30min喷洒一次pms,每次10min,浓度为0.25mm,喷淋头旋转角度为0~45
°
;根据plc编程进行交替喷洒,当水蒸发速率降低20~40%时,用纯水冲洗膜表面,冲洗5min,冲洗时升降器自动抬高膜一侧至60
°
,冲洗结束后回到初始位置;光热膜材料选用石墨烯mof材料,负载量为0.8mg/cm2;处理结果如下:
59.一个太阳光下,无余热利用时,石墨烯膜平均蒸发通量仅0.82kg/m2h,而 mof石墨膜蒸发通量为1.23kg/m2h,五个太阳光下平均蒸发速率为6.93kg/m2h。说明mof光热材料具有优异的光热转换效率。利用印染余热结合光热时,料液进入光热装置前温度提高至63℃,因此界面蒸发的速率加快,平均蒸发速率进一步提高至1.72kg/m2h,比单纯太阳光照射提高了40%。在间歇式清洗下,石墨烯mof材料光热废水处理运行一周,蒸发速率可维持在1.15kg/m2h,说明间歇式清洗可维持光热膜材料的光热性能。
60.太阳能光热蒸发处理印染废水,色度及cod去除率达到99%,toc去除 97%;蒸馏水电导低于100μs/cm,表明太阳能膜蒸发系统具有优异的有机物截留和脱盐性能。
61.对蒸馏产水中挥发性机污染物监测发现,mof改性蒸发材料结合pms活化对苯酚类去除率达到85%,蒸馏苯酚类浓度降低至1.2mg/l,优于pvdf基膜的苯酚拦截效率(25%)。利用优异的光热膜和pms活化处理印染废水,降低了产水中有毒挥发性有机物的含量。