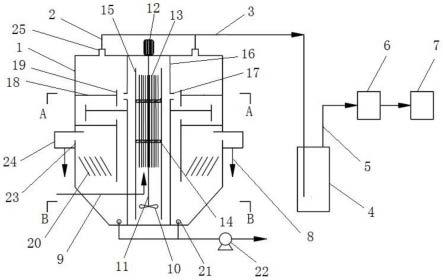
1.本发明涉及废水处理技术领域,特别涉及一种用于处理高含盐废水的一体化内循环电催化反应器。
背景技术:2.随着国家经济的不断提升,工业生产高速发展的同时,大量的高盐废水随之产生。高盐废水中含有大量cl-、so
42-、na
+
、ca
2+
等溶解性无机盐离子,还含有难处理的有机污染物,直接排放不仅污染环境,还给人民生活及身体健康带来严重的危害,随着国家排放标准越来越严格,含盐废水的处理成为环保领域需要重点关注的问题。
3.电催化氧化技术属于典型的高级氧化技术,由于具有操作条件温和、可控性强、绿色清洁的特点而在工业废水、尤其是高盐废水领域受到广泛关注。然而,电催化氧化在应用过程中存在电极结垢问题,这是因为在反应过程中,阴极区ph升高,当溶液中含有ca
2+
、mg
2+
时,阴极表面形成caco3和mg(oh)2。阴极结垢可采用连续旋转刷或旋转叶片、酸洗、倒极、限流等方法去除。然而,上述方法在解决问题的同时,给系统的运行带来额外负担。另外,电催化反应过程中产生的气体通常由专用气液分离器进行气液分离后由风机稀释排放,带来经济上的浪费;电催化反应过程中产生的泥垢通常由专门沉淀池进行固液分离,增加了工艺的复杂性。
技术实现要素:4.本发明为了解决传统电催化反应过程中结垢、气液分离、固液分离导致的工艺复杂、设备繁多以及气体资源浪费的问题,提供了一种一体化内循环电催化反应器。
5.本发明是通过以下技术方案得以实现的。
6.一种一体化内循环电催化反应器,包括反应器本体,反应器本体的顶部设有气体排出口,所述反应器本体的中部竖直设有导流筒;在所述导流筒内,上部设有电极,下部设有搅拌桨,电极和搅拌桨之间设有进水管;所述导流筒外套设有环形的隔板,隔板的上部形成流通口;所述隔板与反应器本体的内壁之间设有多层筛板,筛板位于反应器本体的中上部;所述筛板的下方设有斜管,斜管与筛板之间的反应器本体侧壁上形成出水口。
7.进一步的,所述电极为不少于一组的同心圆管电极,电极通过支撑板固定在导流筒上。
8.进一步的,所述流通口低于导流筒上沿,流通口到隔板顶部的距离为隔板高度的1/3-1/4。
9.进一步的,多层所述筛板上下错位交错排列,且筛板的边沿形成溢流堰。
10.进一步的,所述筛板上设有均匀排列的等径圆孔。
11.进一步的,所述出水口处向上形成薄壁堰,薄壁堰与收集槽连接,收集槽与排水管连接。
12.进一步的,所述反应器本体底部设有环形的穿孔管,穿孔管与抽吸泵连接。
13.进一步的,所述气体排出口与气体排放支管连接,多个气体排放支管均与气体排放管连接,气体排放管连接吸收罐,吸收罐顶部通过气体出口管依次连接干燥器和储存罐。
14.进一步的,所述斜管的倾斜角度为45-60
°
。
15.进一步的,所述斜管下方的反应器本体呈倒圆台型,反应器本体侧壁与水平面夹角为30-45
°
。
16.本技术具有以下有益效果。
17.1.本发明反应器集气液分离、泥垢分离于一体,简化了电催化技术应用的工艺流程;
18.2.本发明反应器内部气体聚集区呈正压状态,且不直接与大气联通,避免了电催化过程中所产气体与空气混合而引起的爆炸危险;
19.3.本发明反应器提高了电极表面冲刷速度,加大水体紊流程度,减缓电极表面浓差极化,提高电极的反应效率。
附图说明
20.图1是本发明的结构示意图;
21.图2是本发明的俯视图;
22.图3是图1中沿a-a线的剖面图;
23.图4是图1中沿b-b线的剖面图。
24.其中,1.反应器本体;2.气体排放支管;3.气体排放管;4.吸收罐;5.气体出口管;6.干燥器;7.储存罐;8.排水管;9.进水管;10.搅拌桨;11.搅拌轴;12.电机;13.电极;14.支撑板;15.导流筒;16.隔板;17.流通口;18.筛板;19.溢流堰;20.斜管;21.穿孔管;22抽吸泵;23.薄壁堰;24.收集槽;25.气体排出口。
具体实施方式
25.下面结合附图和实施例对本发明进行进一步的说明。
26.如图1-4所示,一体化内循环电催化反应器,包括反应器本体1,反应器本体1的器壁由碳钢焊接而成,内衬为耐酸碱的pvc塑料,使设备具备一定的绝缘性、耐腐蚀性和抗压能力。
27.所述反应器本体1的中部竖直设有导流筒15,导流筒15外套设有环形的隔板16,隔板16与反应器本体1的内壁之间设有多层筛板18。导流筒15、隔板16以及筛板18将反应器本体1内分成推进区、电极区、循环区、气液分离区、气体聚集区、沉淀出水区和泥垢区。
28.推进区位于导流筒15内的下部,包括进水管9和搅拌桨10;进水管9出口端位于搅拌桨10的上方,方向向上,搅拌桨10位于推进区的中心,搅拌桨10与搅拌轴11连接,搅拌轴11通过减速器与电机12连接。本技术搅拌器选用推进式搅拌器,兼具推流及搅拌作用。推进区上部与电极区联通,推进区下部与循环区联通。
29.电极区位于导流筒15内的上部,电极区内设有环形排布的不少于一组的电极13,优选为5组,电极13为单极式或复极式连接,阳极和阴极为板式或网式,阳极和阴极是以钛为基材、涂覆贵金属涂层的dsa电极,间距为0.5-5cm。电极组13通过支撑板14固定在导流筒15上。
30.循环区位于导流筒15与隔板16之间,循环区与电极区通过导流筒15分隔,循环区与气液分离区和沉淀出水区之间通过隔板16分隔,循环区上部与电极区联通,循环区下部与推进区联通。所述隔板16上设置流通口17,流通口17低于导流筒15上沿15-50cm,位于隔板16上部1/4位置处,流通口17连接循环区和气液分离区。电极区的气水混合物在水流推进作用以及电催化所产气体的上升气流携带作用下翻滚进入循环区,一部分水流进入流通口17,一部分继续向下运动,与进水共同进入电极区,在搅拌桨10推进作用下,形成电极区和循环区内水流的内循环。
31.气液分离区由多层上下交错排列的筛板18和溢流堰19组成,筛板18的数量不少于2层,优选为3层。所述筛板18上设有均匀排列的等径圆孔,圆孔直径为1-5mm,优选为2mm。气液分离区上一层溢流堰19的下沿低于下一层溢流堰19的上沿。水流沿筛板18横向流动并在溢流堰19的导流作用下,向下进入下一级筛板18,水流进一步向下流动进入沉淀出水区,气体则在流动过程中与水流分离,从下往上进入气体聚集区。
32.沉淀出水区位于气液分离区的下方,沉淀出水区内设有斜管20,斜管20的倾斜角度为45-60
°
。斜管20与最下层筛板18之间形成出水口,出水口处向上形成薄壁堰23,薄壁堰23与收集槽24连接,收集槽24与排水管8连接。所述斜管20下方的反应器本体1呈倒圆台型,侧壁与水平面夹角为30-45
°
。污水在斜管20的作用下,进行泥水分离,泥垢落入泥垢区,处理后的水经过薄壁堰23进入收集槽24,由排水管8排放。由于所产泥垢多为无机垢,斜管20可提高水中泥垢的分离效率。
33.泥垢区位于反应器本体1的底部,泥垢区设有穿孔管21,穿孔管21为环形,穿孔管21的两侧斜向下交错布置孔眼,孔眼直径10-30mm,孔眼环向间距为20-60cm,穿孔管21与抽吸泵22连接。
34.气体聚集区位于气液分离区的上方,气体聚集区顶部即反应器本体1的顶部,为平顶、坡顶或圆弧顶,优选为平顶,并设有高于反应器顶部的气体排出口25,气体排出口25与两根及以上的气体排放支管2连接,优选的,气体排放支管2为六根。多根气体排放支管2均与气体排放管3连接,气体排放管3连接吸收罐4,气体排放管3深入吸收罐4溶液液面以下,吸收罐内装有naoh溶液、na2c03溶液、ca(0h)2溶液中的一种或几种,优选为浓度10%的氢氧化钠溶液。吸收罐4顶部连接气体出口管5,气体出口管5连接干燥器6,干燥器6内装填生石灰、无水氯化钙、活性氧化铝中的一种或几种,优选为生石灰。经干燥后气体进一步进入储存罐7,储存罐7内储存电催化反应过程中产生的氢气。
35.本技术的污水处理流程如下:污水通过管道进入推进区,在推进区内搅拌桨10的作用下,进水与循环区回流的污水混合并被推流送入电极区,混合污水在电极区电催化反应作用下,降解污染物,电催化过程中产生的气体推动混合污水向上流动,进一步翻滚越过电极区进入循环区,污水在流通口17处进行分流,一部分进入气液分离区,另一部分向下进入推进区与进水混合。来自流通口17的污水进入气液分离区后,水流沿筛板18横向流动并在溢流堰19的导流作用下,向下进入下一级筛板18,在筛板18作用下,气体向上进入气体聚集区,污水向下流动进入沉淀出水区,在此进行泥垢和水的分离,其中泥垢落入泥垢区,分离后的净水由收集槽24进入排水管8排放。泥垢在穿孔管21和抽吸泵22的作用下排放,气体聚集区内的混合气体依次通过气体排出口25、气体排放支管2、气体排放管3进入吸收罐4,混合气体中的含氯气体被吸收罐4内碱性溶液吸收,剩余的氢气经干燥器6干燥后进入储存
罐7,可进一步利用。本技术在推进区搅拌桨10的推进作用下,通过内循环可形成1-3倍的循环流量,提高电极表面冲刷速度,加大水体紊流程度,减缓电极表面浓差极化,从而提高电极的反应效率。另外,气液分离区的筛板18使得水流断面增大,流速降低,利于电催化过程中所产气体从水体中溢出,反复折流保障了气体溢出的效率。
36.应用例1
37.天津某石化公司生化出水深度处理采用反渗透工艺,其中反渗透浓水由于具有电导率高、盐含量高、硬度高、cod高的特点,且含有大量难降解物质,采用常规处理工艺难以稳定达到排放标准,采用本发明的一体化内循环电催化反应器进行中试试验。其中,反应器的电极区设置网式同心圆管dsa电极5组,间距1cm,复极式连接;气液分离区设置3层筛板上下错位交错排列,筛板上等径圆孔直径为2mm;顶部设有2个气体排放支管;污泥区底部为环形穿孔管,孔眼直径15mm,孔眼环向间距20cm;吸收罐内装有naoh和na2c03的混合溶液;干燥器内装填生石灰。试验结果显示,当水力停留时间为1h,吨水电耗为6kwh/m3,进水cod在130~150mg/l时,出水cod可稳定低于50mg/l,电极在运行58d时未出现结垢现象,回收的次氯酸钠溶液用于厂区内消毒,氢气经收集后送至下游厂家作为原料使用;与传统电催化反应器相比,该反应器集气液分离、泥垢分离于一体,设备更加紧凑,节省了占地面积,降低了吨水电耗。。
38.应用例2
39.浙江某石化公司污水处理采用a/o+mbr工艺,处理出水不稳定达标,后增设本发明的一体化内循环电催化反应器,反应器的电极区设置板式同心圆管dsa电极6组,间距0.8cm,复极式连接;气液分离区设置4层筛板上下错位交错排列,筛板上等径圆孔直径为2mm;顶部设有3个气体排放支管;污泥区底部为环形穿孔管,孔眼直径18mm,孔眼环向间距30cm;吸收罐内装有naoh溶液;干燥器内装填无水氯化钙;当水力停留时间为1.2h时,吨水电耗为3kwh/m3时,当进水cod≤80mg/l、氨氮≤10mg/l、总氮≤20mg/l时,出水水质实现cod≤50mg/l、氨氮≤5mg/l、总氮≤10mg/l,回收的次氯酸钠溶液用于厂区内循环冷却水杀菌灭藻,氢气经收集后送至下游厂家作为原料使用。。
40.本具体实施方式的实施例均为本发明的较佳实施例,并非依此限制本发明的保护范围,故:凡依本发明的结构、形状、原理所做的等效变化,均应涵盖于本发明的保护范围之内。