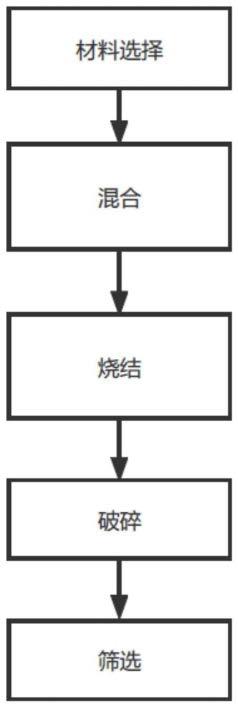
1.本发明涉及脱水技术领域,具体涉及一种用于污泥脱水的物理调理剂制备方法及该物理调理剂。
背景技术:2.在当前污泥处理处置过程中,由于污泥自身成分复杂,含有有机物与无机物,且内部结构复杂,黏性高,污水处理厂剩余污泥的含水率一般高达到96.0%~99.3%,经浓缩后污泥的含水率仍高达90%以上,普通机械方法只能把表面吸附水和毛细水除去,难以将结合水和间隙水除去。经普通机械脱水后污泥的含水率仍在80%左右。为满足于污泥的运输、填埋或资源化利用,在现有技术中,通常会对污泥进行预处理和深度脱水,之后再进行干化处理,将污泥水分脱到可利用的水分要求,但处置成本远高于污泥自身价值,形成“负”资源利用现状。
3.当前污泥调理方法主要有物理调理法、化学调理法、微生物调理法。
4.传统物理调理主要包括加热和冷冻调理,加热调理技术成本较高,冷冻调理技术受气候条件的限制,使得这两种技术难以推广使用;
5.各种方法在实际中均有应用,但以化学调理法为主。化学法调理污泥中,阳离子聚丙烯酰胺(pam)是目前污水处理厂应用最广泛的污泥脱水剂之一,但其存在成本高、难溶解、脱水效果不好等缺点。一些絮凝剂单独使用时投药量大,无机成分比例增加会导致其肥效和热值降低,且易产生二次污染,还存在苛刻的ph值和离子强度要求。此外,组成比例和投加顺序对污泥脱水有很大的影响;
6.微生物絮凝调理技术是使用微生物絮凝剂进行污泥调理的技术。微生物絮凝剂制备成本较高,且针对性不强,所以目前微生物絮凝剂主要还是和传统絮凝剂联用调理污泥。
7.污泥经过调理后机械脱水,不同的调理方法和不同的机械脱水工艺,污泥最终的含水率也不同,活性污泥含水率一般可达60%。脱水污泥的含水率不能满足污泥处置的要求:如作为肥料或土壤改良剂用于土地利用,要求含水率降为20%~40%;直接焚烧要求含水率低于50%。脱水污泥中的水分主要为细胞内部结合水和部分颗粒吸附水及毛细水。要进一步去除这部分水分,常规的机械脱水方法已不再适用。
8.污泥干化是在机械脱水后,利用热能将污泥中的水分变为水蒸气而散失,得到含水率15%~40%的干化污泥,目前应用最广泛、最成熟的是热干化技术。污泥热干化根据热介质与污泥接触方式可分为直接热干化、间接热干化技术。由于热介质与污泥直接接触而受污染,废气须经无害化处理后排放,此外直接干化所需要的能耗较高,热干化尾气处理也需要高昂的费用。间接加热的特点是热源与污泥不直接接触,通过加热容器将热量间接传递给污泥,但是其热传输效率和蒸发率较差,污泥中的有机物不易分解,并且需要配备单独的热源系统,投资和维护成本较大。
9.综上所述,目前所使用的污泥脱水方法中,化学调理法处理污泥普遍存在脱水效率低、工艺复杂、成本高、应用领域窄、对环境造成污染、难以实现资源化利用等问题。而污
泥干化处置方式也有着能耗高、投资和维护成本较大、对环境造成二次污染等缺点。
10.因此,如何在实际应用中,根据污泥的性质、污泥处置方式、经济状况、土地资源状况等选择一种合适、工艺简单、成本低且耗能低的污泥脱水工艺,达到污泥资源化利用的水分要求,对于推动污泥处置事业的持续进步,真正实现污泥的资源化利用具有重要意义。
技术实现要素:11.针对现有技术中存在的技术问题,本发明的目的是:提供一种可通过物理作用提高脱水效果且易于回收的用于污泥脱水的物理调理剂的制备方法及该物理调理剂。
12.为了达到上述目的,本发明采用如下技术方案:一种用于污泥脱水的物理调理剂制备方法,包括如下步骤,
13.s1,选择表面层材料和芯层材料,芯层材料为磁性金属材料;
14.s2,将表面层材料和芯层材料混合搅拌,形成混合料;
15.s3,将混合料送入烧结炉中进行烧结;
16.s4,对烧结后的混合料进行破碎处理,得到混合料颗粒;
17.s5,对混合料颗粒进行筛选。
18.采用上述制备方法制得的物理调理剂,在高压作用下对污泥进行脱水,调理剂与污泥相互填充,从而起到骨架作用,可在外力挤压作用下,对污泥颗粒进行物理破壁,将污泥内部水分挤压出来,由于上述作用为物理作用,表面层材料为不与污泥发生化学反应的材料,将污泥水分脱出后可将此调理剂与污泥分离,调理剂继续使用,既减小了脱水成本,又减小了调理剂对环境的污染。
19.作为一种优选,表面层材料包括骨料和助剂,芯层材料和骨料均呈粉末状,芯层材料的粒度为15~250微米,骨料的粒度小于100微米。
20.作为一种优选,助剂包括助熔剂和粘结剂,骨料的成分包括铝的氧化物和硅的氧化物,助熔剂的成分包括钾、钠、钙和镁的氧化物中的多种,粘结剂为硅酸盐或磷酸盐溶液。
21.作为一种优选,步骤s2中,骨料和芯层材料的体积比为3:1~10:1。
22.作为一种优选,芯层材料为铁和/或钴。
23.作为一种优选,步骤s3中,烧结前对混合料进行烘干处理。
24.作为一种优选,步骤s3中,烧结温度大于800℃。
25.作为一种优选,步骤s4中,采用破碎机或球磨机对烧结后的混合料进行破碎处理。
26.作为一种优选,步骤s5中,先通过筛分法按粒径筛选出包裹有表面层材料的混合料颗粒,再通过磁选法筛选出带磁性的混合料颗粒,然后通过浮选法筛选出芯层材料被表面层材料完全包裹的混合料颗粒。
27.一种用于污泥脱水的物理调理剂,由上述物理调理剂制备方法制成,物理调理剂包括多个调理剂颗粒,调理剂颗粒由表面层材料包裹或半包裹芯层材料形成。
28.物理调理剂可通过与污泥混合填充到污泥内部,通过电荷中和和吸附架桥来改善絮体的形成,在污泥内部起到骨架的作用,增加泥饼内部的刚性和骨架结构,进而提供更多的水通道以达到增强污泥脱水的效果。此外,调理剂与污泥内部形成相互挤压的状态,在足够大的外力作用之下细小颗粒对于污泥细胞表面产生的局部高温能够对污泥细胞壁进行破壁,将细胞水释放为自由水,从而提高脱水率。
29.总的说来,本发明具有如下优点:
30.(1).深度脱水效率高:污泥含水率能下降至15%~40%,能满足后续污泥处置的要求,无需再进行深度脱水和高温干化,更加节省中间成本。
31.(2).产品适用范围广:污泥是由亲水性胶体和大颗粒凝聚体组成的非均相体系,具有胶体性质,普通脱水方式需要针对污泥性质选择合适的脱水工艺,而物理调理剂对于各种污泥均具备良好的适应性,真正实现对污泥的资源化利用。
32.(3).环境污染小:由于上述作用不发生化学反应仅为物理作用,脱出水分后,调理剂颗粒可回收,不会对环境造成二次污染。
33.(4).成本低:调理剂颗粒可回收重复使用且能效低,投资成本较小。
34.(5).工艺操作较简单:本发明仅需将物理调理剂与污泥混合进行压滤脱水,能更大的节省人工成本。
附图说明
35.图1为一种用于污泥脱水的物理调理剂制备方法流程图。
具体实施方式
36.下面将结合附图和具体实施方式来对本发明做进一步详细的说明。
37.实施例一
38.一种用于污泥脱水的物理调理剂制备方法,包括如下步骤,
39.s1,选择表面层材料和芯层材料,芯层材料为磁性金属材料;
40.s2,将表面层材料和芯层材料混合搅拌,形成混合料;
41.s3,将混合料送入烧结炉中进行烧结;
42.s4,对烧结后的混合料进行破碎处理,得到混合料颗粒;
43.s5,对混合料颗粒进行筛选。
44.步骤s1中,首先选择芯层材料,从密度大、硬度大的具有磁性金属材料中选择,其密度需大于污泥的密度的1.5倍。其膨胀系数一般较高,两种材料之间热膨胀系数不匹配会产生热应力,为了能减小两层之间脱落的可能性,要尽量提高表面层的热膨胀系数与芯层接近。
45.步骤s3中,烧结温度大于800℃。
46.步骤s3中,烧结前对混合料进行烘干处理。
47.步骤s4中,采用破碎机或球磨机对烧结后的混合料进行破碎处理。
48.步骤s5中,先通过筛分法按粒径筛选出包裹有表面层材料的混合料颗粒,再通过磁选法筛选出带磁性的混合料颗粒,然后通过浮选法筛选出芯层材料被表面层材料完全包裹的混合料颗粒。
49.筛选时,由于只有具有了芯层材料的颗粒才具有磁性,因此通过磁选法可筛选出带有芯层材料的部分,而由于只要包裹了表面层材料,其粒度、颗粒质量等特性会出现一定的差异,因此可以通过筛分法和浮选法继续进行筛选。
50.表面层材料包括骨料和助剂,芯层材料和骨料均呈粉末状,芯层材料的粒度为15~250微米,骨料的粒度小于100微米。
51.骨料的成分包括al2o3(氧化铝)和sio2(氧化硅),助剂的成分包括k2o(氧化钾)、mgo(氧化镁)、na2o(氧化钠)、cao(氧化钙)、zno(氧化锌)、k2sio3(硅酸钾)、na2o
·
nsio2(硅酸钠)、k3po4(磷酸钾)、al(h2po4)3(磷酸二氢铝)、zrsio4(硅酸锆)等材料中一种或多种。
52.其中铝、硅的氧化物起骨架材料的作用,钾、钠、钙、镁的氧化物起助熔的作用,硅酸盐与磷酸盐溶液主要起粘结剂的作用,需要根据污泥性能需求采取不同的表面层材料及不同的结合方式制备出应用性能不同的调理剂颗粒。例如污泥中酸性过高,就需要提高抗酸碱腐蚀特性的原材料比例,为了有效增强调理剂颗粒硬度和耐磨性,可加入一些氧化铬等。为提高涂层的耐热性可添加二氧化钛等。
53.步骤s2中,骨料和芯层材料的体积比为3:1~10:1。
54.一种用于污泥脱水的物理调理剂,由上述物理调理剂制备方法制成,物理调理剂包括多个调理剂颗粒,调理剂颗粒由表面层材料包裹或半包裹芯层材料形成。
55.由上述制备方法制成的调理剂颗粒的粒度为30~350微米,表面层厚度在250微米以下。
56.筛选后,测试产品是否具备耐磨性、抗热震性和耐腐蚀性。
57.耐磨性:采用失重法测量15h磨损率小于0.6%,测试时,分别把称量好质量的调理剂颗粒和一定量的研磨介质混合,在行星球磨机上进行研磨,在此过程中,既有磨料对试样的磨损,又有对试样的冲击。混磨15h后取出,分离样品并烘干测其质量。以试样磨损后的质量减少百分率即磨损率表征其耐磨性,磨损率越小,表明其耐磨性越好。
58.抗热震性:通过急冷急热法升温至800℃测试表面层材料的抗热震性,循环15次以上不出现裂纹或脱落,测试时,直接将样品放在800℃加热10分钟后取出,于室温中冷却。加热、冷却1次为1个循环。
59.耐腐蚀性:在30%浓度的h2so4溶液中的平均腐蚀速率为2
×
10
-5
mm/h以下,且在10%浓度的naoh溶液中平均腐蚀速率为4
×
10
-7
mm/h以下。
60.实施例二
61.芯层材料为铁,表面层材料为玻璃熔块、氧化铬粉、粘土粉和硅酸锆微粉等材料的混合物,其主要成分为sio2和al2o3。
62.氧化铬粉的加入是为了与基体材料相匹配,且氧化铬具有较好的抗氧化性和耐磨性。玻璃熔块可以降低材料的熔点,使粉料更易于烧结,且由于具有较大的热膨胀系数,因此有利于表面层与芯层金属材料的结合,在高温烧结时有液相生成,使表面层材料的孔隙率下降,金属芯层的表面形成致密的、不透气的液相粘附层,使表面层收缩,有利于解决在冷却时因金属芯层收缩较大而与表面层剥离的问题。黏土粉可以提高表面层的粘结性和烧结性能,及与污泥混合时料浆的悬浮性。硅酸锆微粉的加入可提高调理剂的耐磨性。
63.本实施例未提及部分同实施例一。
64.上述实施例为发明较佳的实施方式,但本发明的实施方式并不受上述实施例的限制,其他的任何未背离本发明的精神实质与原理下所作的改变、修饰、替代、组合、简化,均应为等效的置换方式,都包含在本发明的保护范围之内。