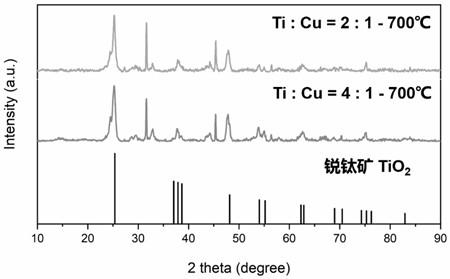
1.本发明属于环保技术领域,具体涉及工业废水的处理工艺,尤其涉及络合态重金属废水的处理工艺。
背景技术:2.有色金属冶炼、电镀等行业的迅猛发展,必然导致含重金属的工业废水产生。工业废水若未经处理直接排放,将会造成严重的水环境污染。工业废水中成分繁多且复杂,含大量具有活性的配体有机物,与重金属离子形成具有较高稳定性和水溶解性的络合态重金属,而由于工业废水中络合态重金属难以被降解,以不同价态在水体、底质和生物中迁移、转化和富集,危害水生动植物,通过食物链浓缩进入人体内,危害人体健康,从工业废水中去除络合态重金属迫在眉睫。
3.伴随工业废水中重金属离子的去除,必然带来含重金属污泥产生。现有重金属污泥处理方法,一般是填埋、焚烧,易带来二次污染。然而重金属污泥中一些重金属元素如铜、镍、锌等化学性质活泼具有导电性、磁性被广泛应用,可以作为其他领域的原材料,特别是作为一些光催化剂(或助催化剂)的重要构成元素;因此,亟需开发一种络合态重金属资源化处置回收的方法实现重金属废水达标排放同时实现资源循环再生利用。
4.授权公告号为cn112978983b的专利文献公开了一种基于铁基生物炭的重金属络合废水处理及其资源化工艺,通过将铁基生物炭加入重金属络合废水中发生吸附反应,后添加氧化剂发生催化破络合反应,含重金属残渣通过淋洗液淋洗得重金属废液再次添加氧化剂蒸干得高纯度重金属盐。该工艺需要经过复杂的化学反应制备铁基生物炭,能耗高,此外,含重金属残渣需要淋洗后二次添加氧化剂蒸干才能实现回收,药剂成本高,工艺复杂。
技术实现要素:5.针对现有技术存在的问题,本发明的目的是解决工业废水中络合态重金属去除工艺复杂以及含重金属污泥处置耗能大、易造成二次污染的缺陷和不足,提供一种简单高效的络合态重金属废水处理及资源化回收的方法。
6.为实现上述目的,本发明提供以下具体的技术方案。
7.一种络合态重金属废水的处理工艺,包括以下步骤:步骤s1,向络合态重金属废水中加入钛盐,控制反应体系的ph值为7~9,反应一段时间后,固液分离,得到混凝污泥,同时废水达标排放;;步骤s2,将混凝污泥脱水、干燥,煅烧,得到金属掺杂钛系光催化剂。。
8.进一步地,在本发明的部分优选实施方式中,所述钛盐为四氯化钛、硫酸钛、三氯化钛中的至少一种。
9.进一步地,在本发明的部分优选实施方式中,所述络合态重金属离子与钛盐中的钛的摩尔比为1:2~6。
10.进一步地,在本发明的部分优选实施方式中,步骤s1所述反应的过程中,搅拌。优
选搅拌速度为300~450rpm。
11.进一步地,在本发明的部分优选实施方式中,步骤s1所述反应的时间为20~50min。
12.进一步地,在本发明的部分优选实施方式中,步骤s2所述煅烧的温度为400~700℃,时间为1~2h。
13.本发明直接将钛盐加入络合态重金属废水中,控制ph值,即可实现重金属废水达标排放;同时得到具有回收价值的钛聚混凝污泥。钛盐投入络合态重金属废水中,水解形成氢氧化物可通过电荷中和、吸附桥联和卷扫网捕作用去除络合态重金属进而实现废水达标排放;此外,得到的钛聚混凝污泥可以转化为二氧化钛光催化剂,而资源化回收的重金属作为掺杂剂存在于二氧化钛光催化剂中,可以提高光催化剂电子-空穴转移/迁移/分离效率,提高降解有机污染物能力。
14.与现有技术相比,本发明具有以下明显的有益技术效果:本发明直接将钛盐加入络合态重金属废水中,一步反应即可在常温下实现络合态重金属的高效去除,而且,钛聚混凝污泥经煅烧后可以转化为具有高附加值的钛系光催化剂。在钛系光催化剂中,重金属离子可以作为掺杂剂提高光催化剂性能,可有效降解有机污染物,实现资源循环再生利用。
附图说明
15.图1为实施例3和实施例4得到的煅烧产物的xrd图。
16.图2为实施例3、实施例4以及对比例1得到的煅烧产物用于甲基橙和磺胺甲恶唑的降解试验结果。
17.图3为实施例5-7的重金属离子去除效果图。
具体实施方式
18.为了便于理解本发明,下文将结合说明书附图和较佳的实施例对本发明做更全面、细致地描述,但本发明的保护范围并不限于以下具体实施例。
19.除非另有定义,下文中所使用的所有专业术语与本领域技术人员通常理解的含义相同。本文中所使用的专业术语只是为了描述具体实施例的目的,并不是旨在限制本发明的保护范围。
20.除非另有特别说明,本发明中用到的各种原材料、试剂、仪器和设备等均可通过市场购买得到或者可通过现有方法制备得到。
21.本发明提供了一种简单高效的络合态重金属废水的处理工艺,将钛盐直接投入含络合态重金属的工业废水中,控制ph值,即可实现络合态重金属的去除,简化了工业废水中重金属的去除工艺。同时,混凝污泥煅烧后得到的钛系光催化剂可有效处理有机污染物。本发明既实现了工业废水中重金属的高效去除,又实现了重金属的资源化利用。
22.具体来说,本发明提供的技术方案如下:一种络合态重金属废水的处理工艺,包括以下步骤:步骤s1,向络合态重金属废水中加入钛盐,控制反应体系的ph值为7~9,反应一段时间后,固液分离,得到混凝污泥,同时废水达标排放;步骤s2,将混凝污泥脱水、干燥,煅烧,得到金属掺杂钛系光催化剂。
23.在具体实施方式中,所述钛盐为四氯化钛、硫酸钛、三氯化钛中的至少一种,进一步优选为四氯化钛。
24.在具体实施方式中,所述络合态重金属离子与钛盐中的钛的摩尔比为1:2~6,进一步优选为1:2~4。
25.在具体实施方式中,步骤s1所述反应的过程中,搅拌。搅拌速度为300~450rpm,优选为350~450rpm。
26.在具体实施方式中,步骤s1所述反应的时间为20~50min,优选为30~50min。
27.在具体实施方式,步骤s2所述煅烧的温度为400~700℃,时间为1~2h。进一步优选煅烧的温度为600~700℃,时间为1h。
28.以下通过具体的实施例做进一步说明。
29.在具体实施例中,含络合态重金属的工业废水来自电镀废水、电子线路板废水等。废水中含有重金属离子cu
2+
、ni
2+
、cr
6+
、zn
2+
,络合剂为乙二胺四乙酸(edta)、柠檬酸(citrate)、酒石酸(tartrate)等。
30.在以下具体实施例1-4中,采用的络合态重金属废水为:目标络合态重金属为cu
2+-citrate,初始重金属离子cu
2+
的浓度为60mg/l。
31.实施例1取500ml预先配制的络合态重金属废水,加入1.88mmol的四氯化钛(ti:cu的摩尔比为2:1),调节ph值为7.5,搅拌,搅拌速度为350rpm,反应30min。反应过程中严格控制体系ph值为7.5。
32.反应结束后,固液分离,得到上清液和污泥。
33.测定上清夜中重金属cu
2+
含量。
34.洗涤污泥,然后污泥经干燥后,在马弗炉中于600℃煅烧1h,得到煅烧产物。
35.实施例2本实施例与实施例1的区别仅在于:在络合态重金属废水中加入3.75mmol的四氯化钛(ti、cu的摩尔比为4:1)。
36.实施例3本实施例与实施例1的区别仅在于:污泥在马弗炉中于700℃煅烧1h。
37.实施例4本实施例与实施例2的区别仅在于:污泥在马弗炉中于700℃煅烧1h。
38.分别测定实施例1和2所得上清液中的cu的含量,结果如表1所示。
39.表1测定实施例3和实施例4所得煅烧产物的物相,结果如图1所示。从图中可以看出,煅烧产物晶体结构为锐钛矿tio2。
40.对比例1将四氯化钛投加到纯水中,四氯化钛的水解产物于700℃煅烧1h,煅烧产物即为钛
系光催化剂。
41.将实施例3、实施例4和对比例1所得煅烧产物用于甲基橙和磺胺甲恶唑的降解试验,结果如图2所示。结果表明,资源回收得到的重金属掺杂钛系光催化剂与对比例1所述的钛系光催化剂相比,具有良好的降解甲基橙和磺胺甲恶唑的效果。
42.实施例5络合态重金属废水为:目标络合态重金属为ni
2+-citrate,初始重金属离子ni
2+
的浓度为60mg/l。
43.取500ml预先配制的络合态重金属废水,加入2.03mmol的四氯化钛(ti:ni的摩尔比为2:1),调节ph值为7.5,搅拌,搅拌速度为350rpm,反应30min。反应过程中严格控制体系ph值为7.5。
44.反应结束后,测定上清液中重金属ni
2+
含量。
45.实施例6络合态重金属废水为:目标络合态重金属为cr
6+-citrate,初始重金属离子cr
6+
的浓度为60mg/l。
46.取500ml预先配制的络合态重金属废水,加入2.3mmol的四氯化钛(ti:cr的摩尔比为2:1),调节ph值为7.5,搅拌,搅拌速度为350rpm,反应30min。反应过程中严格控制体系ph值为7.5。
47.反应结束后,测定上清液中重金属cr
6+
含量。
48.实施例7络合态重金属废水为:目标络合态重金属为zn
2+-citrate,初始重金属离子zn
2+
的浓度为60mg/l。
49.取500ml预先配制的络合态重金属废水,加入1.85mmol的四氯化钛(ti:zn的摩尔比为2:1),调节ph值为7.5,搅拌,搅拌速度为350rpm,反应30min。反应过程中严格控制体系ph值为7.5。
50.反应结束后,测定上清液中重金属zn
2+
含量。
51.实施例5-7所述的废水中相应重金属离子的去除率如图3所示,重金属ni、cr、zn的去除率均非常高。
52.以上所述仅是本发明的优选实施方式,应当指出,对于本技术领域的普通技术人员来说,在不脱离本发明原理的前提下,还可以做出若干改进和润饰,这些改进和润饰也应视为本发明的保护范围。