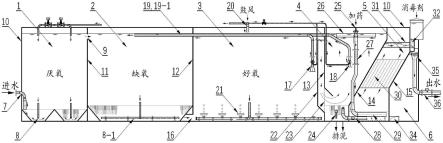
乡村污水集装箱式a2o一体化处理装置
技术领域
1.本实用新型涉及污水处理装备技术领域,具体涉及乡村污水集装箱式a2o 一体化技术,特别是将活性污泥法、空气提升和混凝沉淀技术创新结合于集装箱式箱体内,通过结构紧凑化、装置标准化、操作简便化,最终实现低成本污水处理和高效率脱氮除磷二者的有效兼顾。
背景技术:2.污水生化处理技术是当今世界各国应用最广泛的污水处理技术,其中,最简便、最高效的aao(厌氧anaerobic—缺氧anoxic—好氧oxic的缩写简称,亦为a2o)脱氮除磷技术,已经成为城市或城镇污水处理技术的主流。然而,在集装箱式污水处理装备领域,由于体积尺寸的制约,过去多采用生物接触氧化法技术,近来大多采用膜-生物反应器(membrane bio-reactor,简称 mbr)技术;前者属于生物膜法技术,其出水一般只能达到《城镇污水处理厂污染物排放标准》的一级b标准;后者属于膜分离与a2o活性污泥法复合技术,以膜组件取代系统末端的二沉池,出水虽能满足当今更高的一级a标准要求,但复杂的系统、相对过高的能耗、依赖外部团队的清洗(在线物理清洗、必须专业化的离线多品类药剂的化学清洗、不同时间段清洗等),以及膜组件老化和结垢堵塞需要更换且费用高昂,因而局限了该技术产品在广大乡村、分散居民点的低成本使用。
3.我们熟知,任何污水处理设施,除了需要一次性建设投资外,在设计寿命期内每天的污水处理,还需要耗电耗药、出渣排泥、人员值班和维修维护等费用来维持正常运转,因此,污水处理永远无法一蹴而就、一劳永逸,况且,污水处理是一门技术性很强的专业,出水要持续稳定达到规定的排放标准绝非易事。事实上,由于乡村较低的薪酬对污水处理专业人才缺乏吸引力,而且污水处理日常运维费用又无长期可靠的来源,加上小型污水处理没有规模效应可言,致使许多造价昂贵、操作复杂、运行成本高企的处理设施难以正常发挥作用,使得水污染治理和水环境保护效果大打折扣。
4.因此,迫切需要发明一种脱氮除磷效率高、出水水质好且稳定、长期运行成本低、采购制作造价低、结构紧凑化、装置标准化、操作简便化、运输安装便利化、日常检修维护工作量小的集装箱式一体化装备,以符合当今广大乡村污水处理的实际需要,以应对乡村环保专业人才难觅、环保资金短缺的现实。
技术实现要素:5.本实用新型的目的,在于提供一种创新的乡村污水集装箱式a2o一体化处理装置,以解决上述背景技术中提出的问题,切实做到低成本污水处理和高效率脱氮除磷二者兼顾,为水环境保护减轻各方的财政经济压力,真正做到可持续发展。
6.为实现上述目的,本实用新型的技术方案如下:
7.总体的,乡村污水集装箱式a2o一体化处理装置,包括集装箱式矩形箱体 10,以及箱内带孔洞的第一直隔板11、第二直隔板12、第三直隔板13和第四斜隔板14、第五斜隔板15
共五块隔板将空间按顺序分隔成的厌氧反应区1、缺氧脱氮区2、好氧硝化区3、泥水重力分离区4、混凝反应-斜管沉淀区5、接触消毒区6共六大功能区组成。箱内各区由孔洞、管道及组件、集水槽等连通。箱外经预处理后的污水,从进水管7进入箱内首端厌氧反应区1,依序进行生化物化强化处理、气提循环及加药过程,所产剩余污泥经大口排泥管24 排出,最后,清水经与箱体末端相连的流量计36计量后排出。
8.进一步的,所述厌氧反应区1为矩形箱体10与第一直隔板11合围的矩形空间,该区的起端下部有污水进水管7、底部有厌氧空气搅拌管8;
9.所述进水管7在厌氧反应区1内的入流口位置及布水流向,是位于该区的平面中部和距离底板高度≤800mm的位置,且布水的流向是向两侧对称布水和 /或向下布水;
10.所述厌氧反应区1的底部,设有2根平行的水平空气搅拌管8,该搅拌管中心距底板的高度≤300mm,该2根搅拌管轮流间歇使用,即轮流间歇启闭该搅拌管连接的压缩空气管路所一一对应的电磁阀/电动阀进行短促空气搅拌;
11.所述缺氧脱氮区2为第一直隔板11与第二直隔板12两者之间的矩形空间,该区底部有空气搅拌管8-1,该搅拌管为2根平行的水平空气搅拌管8-1,该2根搅拌管轮流间歇使用,即轮流间歇启闭该搅拌管连接的压缩空气管路所一一对应的电磁阀/电动阀进行短促空气搅拌;该区水面下紧贴水面处还有硝化液回流管19和悬浮污泥回流管19-1;
12.所述缺氧脱氮区2上部水面处的硝化液回流管19,其管道口中心与第一直隔板11上所对应的第一小孔9中心的距离≤1200mm;
13.所述缺氧脱氮区2上部水面处的悬浮污泥回流管19-1,其管道口中心与第一直隔板11上所对应的第一小孔9中心的距离≤1200mm;
14.所述好氧硝化区3为第二直隔板12与第三直隔板13两者之间的矩形空间,该区的底部有微孔曝气装置21,末端有点式气提装置17用于回流硝化液至缺氧区,该气提装置的出口连接硝化液回流管19,该回流管的另一端延伸至缺氧脱氮区2;该区末端还有竖直导流方管22用于出水到下一区域;
15.所述竖直导流方管22,其上口淹没于好氧硝化区3的设计水面下,下口通过所述直隔板13的第三中孔23与泥水重力分离区4相通;
16.所述竖直导流方管22的底部为封闭的斜面,该斜面的水平倾角为35
°
~ 65
°
,该倾角便于该斜面上的积泥能随水流滑落,并改善泥水重力分离区4的进水流态。
17.所述泥水重力分离区4为第三直隔板13与第四斜隔板14两者之间的半y 形空间,该区的底部有大口排泥管24;水深中部偏上位置有线式气提装置18 用于回流悬浮污泥至缺氧区,该气提装置的出口连接悬浮污泥回流管19-1,该回流管的另一端延伸至缺氧脱氮区2的上层起端贴近水面处;该区的水面中间上方位置,设有药剂投加口25,该投加口下方水面处设有集水管/槽26,且与更下方的管式混合器27呈t形相连,并继续向下穿越斜隔板14进入混凝反应-斜管沉淀区5,然后经l形管道与布水穿孔管29相连;
18.所述混凝反应-斜管沉淀区5为第四斜隔板14与第五斜隔板15两者之间的 s形折板空间,该区的底部两侧有穿孔排泥管28、底部中间有布水穿孔管29,中部有污水专用型斜管/斜板填料30,水面处有均匀集水的清水集水槽31;该布水穿孔管29为水平布置,且布水的孔口均朝下,其管道中心线距离底板高度150mm~350mm,且该穿孔管29的口径大于管式混合器27的口径;
19.所述接触消毒区6为第五斜隔板15与矩形箱体10合围的梯形空间,该区有3块竖向隔板33,用于将接触消毒区6的容积分为4等份,该区起端顶部还有消毒剂装置/投加点32,末端水面处有清水出水堰35,该出水堰的出口通过管道管件连接至箱体外,最后在箱体外与出水流量计36相连;所述竖向隔板33的第1块第3块的底部中心左侧,开有过水孔洞34。
20.所述第一直隔板11的上方贴近水面处,开有第一小孔9,用于水流从厌氧反应区1流向缺氧脱氮区2;
21.所述第二直隔板12的底部,开有第二小孔16,用于水流从缺氧脱氮区2 流向好氧硝化区3;
22.所述第三直隔板13的靠近底部位置,开有第三中孔23,用于水流从好氧硝化区3流向泥水重力分离区4;
23.所述第四斜隔板14的下部,开有孔洞用于穿越l形管道,将水流从泥水重力分离区4导入到混凝反应-斜管沉淀区5;
24.所述第五斜隔板15的上部,开有清水集水槽31的穿壁孔洞,用于水流从混凝反应-斜管沉淀区5进入到接触消毒区6;
25.所述厌氧空气搅拌管8、缺氧空气搅拌管8-1、点式气提装置17、线式气提装置18所需的压力空气源,均与好氧硝化区3顶外的空气管道20相接;所述微孔曝气装置21亦接自该空气管道20;所述空气管道20与箱外的曝气鼓风机通过管道相连;
26.所述厌氧反应区1、缺氧脱氮区2、好氧硝化区3、泥水重力分离区4形成第一水面,混凝反应-斜管沉淀区5为第二水面,接触消毒区6为第三水面,此三个水面的高度依次下降,成为水流从进水管7流向出水堰35的持久动力;
27.所述第一水面高于第二水面250mm~400mm,第二水面高于第三水面 200mm~350mm。
28.上述各组件部件,以焊接和/或法兰连接为主要连接方式,按照设定的平面位置和高度位置进行有效连接,最终制造成乡村污水集装箱式a2o一体化处理装置。
29.本实用新型乡村污水集装箱式a2o一体化处理装置的工作过程是这样的。
30.首先需要说明的是,鉴于集装箱式污水处理装置的容积十分有限,考虑日常操作的便利性和防止内部淤积堵塞,一般来讲,污水在进入集装箱式箱体之前,必须经过箱体之外的预处理,通常包括格栅拦渣、调节池调节、沉泥沉砂和污水泵提升等工序过程,而本实用新型亦不例外,故,经预处理过后的污水,才能进入本实用新型进行脱氮除磷生化物化处理,其工作过程如下:
31.总体的,污水从进水管7进入厌氧反应区1,之前,该污水来自箱体外的污水调节提升泵(带搅拌功能)池,而该调节池不仅接收待处理污水,也接收来自本实用新型a2o一体化装置的排泥,故,进入本实用新型的污水实际是污水和活性污泥的混合液。混合液在厌氧反应区1的厌氧条件下进行生化反应,其中的聚磷菌通过释放体内的磷酸盐而获取能量,用于吸收污水中可快速降解有机物并转化为phb(聚β羟丁酸)储存于细胞体内。当这些聚磷菌进入后续的好氧条件时,就降解体内储存的phb开始细胞的合成增殖并大量吸收磷,形成含磷量高的污泥,该污泥将随剩余污泥一起排出系统,从而达到生化除磷的目的。之后,污水随流程从第一小孔9进入缺氧脱氮区2,与后续环节回流来的硝化液及回流来的悬浮污泥混合,在该区进行反硝化脱氮生化反应,脱氮之后,再从第二小孔16进入好氧硝化区3进行曝
气处理。经过充分的好氧生化反应后所得硝化混合液,一部分经点式气提装置17回流至缺氧区2进入下一轮循环,另一部分进入泥水重力分离区4。进入泥水分离区4的混合液经泥水重力分离,分离出来的悬浮污泥经线式气提装置18回流至缺氧区2进入下一轮循环,而上清液则汇集并加药后经管式混合器27水力混合,由l形管道导入斜管沉淀区5底部做均匀布水,在斜管区进行混凝反应-斜管沉淀物化处理,此时各项残余污染物被进一步去除,最后,上层清水从集水槽31汇集后进入接触消毒区6,在投加消毒剂进行半小时接触消毒后,箱体末端的达标清水经与箱体相连的流量计36计量后排放。
32.进一步的,本实用新型详细而具体的工作过程如下:
33.厌氧反应区1:污水从进水管7进入箱内厌氧反应区1的起端下部,实则是污水和活性污泥的混合液,在该区厌氧环境下(溶解氧do≤0.2mg/l),活性污泥聚磷菌释放体内的磷酸盐而获取能量,吸收污水中可快速降解有机物并转化为phb(聚β羟丁酸)储存于细胞体内。为了确保均质传质,也为了防止活性污泥在该区沉淀淤积,该区底部设有厌氧空气搅拌管8取代常规的机械搅拌装置,采用轮流、间歇、短促释放的空气泡来翻腾搅动水体。经过厌氧生化反应完成厌氧释磷任务的泥水混合液,从该区末端第一直隔板11上第一小孔9 (共2个)穿越,进入下一区域继续新的生化反应。
34.缺氧脱氮区2:从第一小孔9进入到缺氧脱氮区2的泥水混合液,与回流而来的硝化液和回流而来的悬浮污泥一起,在该区水面的起端进行混合,随即开始进行缺氧反硝化脱氮生化反应(形成氮气溢出),而反应底物为硝化液所携带的硝酸盐及中间产物亚硝酸盐,所需营养物则为进水中可生化降解的有机污染物。回流的硝化液和回流的悬浮污泥两者,均含有活性污泥。所述硝化液来自后续好氧硝化区3的末端,是通过点式气提装置17气提回流而来;所述悬浮污泥则来自更后部的泥水重力分离区4,是通过线式气提装置18气提回流而来。缺氧区混合液在缓慢行进和生化反应的过程中,被底部2根平行的水平空气搅拌管8-1轮流间歇释放的空气泡翻腾搅动,有助于反应产物中的微小氮气气泡顺利溢出,同时防止了活性污泥在该区沉淀淤积。
35.此后,在缺氧脱氮区2内完成反硝化脱氮任务的混合液,从该区末端第二直隔板12上第二小孔16(共2个)穿越,进入下一区域继续新的生化反应。
36.好氧硝化区3:混合液在该区充裕的溶解氧(do)环境下,好氧微生物将该区污水中剩余的含碳有机污染物(因在前两个区域中作为碳源消耗了一部分)吸附氧化分解和部分合成为新生菌体,硝化菌将污水中的氨氮硝化成亚硝态氮及硝态氮,聚磷菌将污水中的磷超量吸收。经过充分的好氧生化反应,当混合液慢速行进至该区末端时,污水中各项污染物已经得到大幅度去除,但已经改变形态尚未得到消除的硝化产物,需要回流到缺氧脱氮区2进行缺氧反硝化脱氮,才能实现总氮(tn)的削减。此时,大部分混合液需要由本区末端的点式气提装置17,通过气提方式回流到前面的缺氧区2进行反硝化脱氮而进入下一轮循环,少部分混合液经竖直导流方管22从上往下,再穿越第三直隔板 13上第三中孔23,进入下一区域进行泥水重力分离。
37.泥水重力分离区4:曝气处理后的混合液进入到泥水重力分离区4的下部,随后在上升行进的过程中,因水平面的截面积越来越大而流速越来越缓,当某高度位置固体颗粒的沉降速度(v
下
)与该处水流上升的速度(v
上
)相等时,污泥颗粒将处于悬浮态的静止状态,其污泥上部将形成泥水分界面,该分界面之上的澄清液即上清液,此时已满足一级b水质指
标要求,该上清液将从泥水分离区水面处的集水管/槽26汇集,经加药混合后下穿第四斜隔板14,进入下一区域即斜管区5开始深度处理,而泥水分离区4被截留下来的悬浮污泥,则通过线式气提装置18源源不断回流至缺氧区2进入下一轮循环。另外,该区底部沉淀浓缩的污泥,一部分作为剩余污泥从底部大口排泥管24排出系统,该剩余污泥包含老化污泥、生化除磷污泥以及后续的化学除磷污泥三者,另一部分作为厌氧反应污泥,以箱外排泥阀控制的重力流形式,自流进入箱体之外预处理工序的进水调节池,并经污水泵的提升返回到本实用新型的厌氧反应区1,以便聚磷菌重回系统进行生化除磷。以剩余污泥形式排出系统的污泥,其处理处置由其他相关设备或方法进行无害化处理。
38.混凝反应-斜管沉淀区5:前述经过加药混合后的上清液,通过l形管道穿越第四斜隔板14,进入到斜管区5进行混凝反应-斜管沉淀的深度处理。所述加药为碱式氯化铝(pac)、三氯化铁(fecl3)等常规水处理药剂药液的计量投加,所述混合为药剂与水在管式混合器27中的快速水力混合。在斜管区5进行的混凝反应,其动力来自于泥水分离区4和斜管区5两者之间的水面高差,即所述的第一水面与第二水面之间的250mm~400mm高差。该区以辅助化学除磷的方式进一步去除残余的磷,同时以絮凝沉淀的方式进一步去除残余的化学需氧量(cod)、悬浮固体(ss)、色度等,使得出水的cod、ss、总磷 (tp)、色度等指标,能够持续稳定地达到更高的一级a标准。在该区域中,残余污染物通过化学反应生成的絮凝体,在著名的浅层沉淀原理作用下,在向上流经污水专用型斜管/斜板填料30的过程中,被拦截沉淀在填料内斜壁上继而下滑坠落到箱体底板成为化学污泥,该化学污泥既含有老化死亡的活性污泥菌体碎片和去除的cod及ss,也含有化学除磷的tp沉淀物。在箱内外的水压差作用下,该化学污泥通过底部两侧的穿孔排泥管28排入箱体外的调节池(水面高程低于斜管区水面),又经过调节池污水泵提升回到本区前面的泥水重力分离区4,最后以剩余污泥的形式排出系统。
39.斜管区5的表层清水,经清水集水槽31收集后穿越第五斜隔板15上部,进入到接触消毒区6进行最后的消毒。
40.接触消毒区6:设置在该区起端顶部的消毒剂装置/投加点32,对汇入起端的清水投加消毒剂,含消毒剂的清水在该区须接触停留30min或以上,待充分杀灭细菌后,再从该区末端的出水堰35溢出,此时,细菌学指标合格的清水,经与箱体末端相连的流量计36计量后排出。
41.为了保证消毒效果,避免接触消毒的水流出现短流,本实用新型在接触消毒区6内设有3块竖向隔板33,其中的第1块第3块隔板的底部中心左侧开有过水孔洞34,这样就使得水流能在该区间上下左右曲折前行,确保了水流在该区接触停留30min或以上,达到充分杀灭细菌的目的。
42.本实用新型采用了以下五项独创性的创新技术,特别适用于非mbr类型集装箱式污水处理装置,其技术创造性、先进性和显著的实用性阐述如下:
43.一、空气双旋轮流间歇短促搅拌技术
44.该技术概括为:在偏置的空气搅拌作用下,在不同时间上,以最少的充氧方式,使厌氧区、缺氧区内的流体做竖向左旋和竖向右旋的偏心运动、交替运动和间歇运动。
45.具体为:本实用新型乡村污水集装箱式a2o一体化处理装置,分别在厌氧反应区1、缺氧脱氮区2的底部两侧,各对称布置2根可分别控制运行的空气搅拌管8和8-1,2根相互平
行且水平安装,管中心距底板的安装高度约为 100mm。与搅拌管t形相接的空气进气立管,是从矩形箱体10顶部的压缩空气管路引入的,且每根搅拌管各自连接一台电磁阀/电动阀,该阀门为常闭型阀门。运行时,该2根搅拌管轮流间歇使用,即由plc控制器或时间控制器轮流间隔控制所对应电磁阀/电动阀的启闭:当一根开启时,另一根处于关停状态,且开启的时长较短,关停的时长较长,而且轮流开启和关停。
46.应用上述独创的空气双旋轮流间歇短促搅拌技术,主要目的有3个:
47.1是为了取消常规厌氧区、缺氧区配置的潜水搅拌机或桨式搅拌器等水力机械,使得电动马达尽可能减少,减少了易损件,使得装置发生故障的几率尽可能降低,使得本实用新型变得精简而非繁琐,因而减少了本实用新型的检修维护工作量,同时降低了人工成本;
48.2是为了克服以往空气搅拌的缺陷,例如,某些集装箱式污水处理装置虽然也采用了空气搅拌,通常是单根直线形或l形、u形或o形搅拌管,但其运行时,在离搅拌管稍远之处极易出现水力死角,因死角处活性污泥沉降淤积继而发生团块污泥死亡上浮,会严重影响出水水质;或者,为避免淤积死亡而加大空气量或搅拌时长,却又导致厌氧区、缺氧区的do值升高,厌氧环境、反硝化的缺氧环境受到不利影响甚至破坏,使得厌氧释磷、反硝化脱氮效果变差,最终出水tp、tn值升高甚至不达标;而采用本实用新型独创的空气双旋轮流间歇短促搅拌技术,却不会发生此类问题;
49.3是为了满足厌氧反应区1、缺氧脱氮区2的正常生产需要和节能需要,具体表现在:应用独创的双旋空气搅拌,强化混合液中反应底物及营养物与活性污泥微生物之间的传质交换,强化污水与回流硝化液、回流悬浮污泥的混合,强化反硝化产物微小氮气泡的扰动脱除。另外,由于是短促而间歇性的空气搅拌,因此,本独创技术的运用,既保证了对厌氧区、缺氧区do的最少输入,又使得搅拌能耗处于相对最低水平,对整体降低污水处理能耗起到了正面作用。
50.二、集装箱式污水处理气提双回流免维护节能技术
51.该技术概括为:在集装箱式装置的狭小空间内,利用点式气提装置将好氧区末端的硝化液回流到缺氧区,同时,利用线式气提装置将泥水重力分离区的悬浮污泥回流到缺氧区,而气提所需的动力,均源于污水处理用的曝气鼓风机,无需增设额外的动力机械。
52.具体就是:本实用新型在好氧硝化区3的末端设置点式气提装置17,用于硝化液回流至前端的缺氧脱氮区2,以满足反硝化脱氮处理的工艺需要,取代安装复杂的硝化液回流泵及阀门管路和排气设施;同时,在泥水重力分离区4 的中部带状位置,设置线式气提装置18,用于泥水分离后被截留的悬浮污泥回流至前端的缺氧脱氮区2,以满足生化处理系统活性污泥的动态平衡,保障整个污水处理系统的正常运转,取代安装复杂的污泥回流泵及阀门管路和排气设施。由于箱内的气提装置并无水下活动部件和水下电机,且全部管路及阀门设置极为简单,控制气提空气量的阀门均位于箱体外顶,又因所需空气能耗相比水泵机械甚微,故,上述两种气提回流在箱内的部分实属免维护和节能型。
53.应用上述气提双回流免维护节能技术,既满足了工艺流程的需要,又省去了两种回流泵及复杂的安装及占用的空间,不仅简化了运行管理,而且节能,实现了不设置箱内箱外电动设备的愿望,免去了复杂的维修维护,大大降低了日常运行成本和维修维护及人力成本。
54.三、小型污水装备的两级沉淀低水头节能技术
55.该技术概括为:在小型污水装备狭小空间内,利用升流式悬浮澄清和斜管沉淀两者的共用斜壁,巧妙实现紧邻且紧密的两级沉淀,且两级沉淀的水头差小,初级沉淀为不加药自然重力式,二级沉淀为加药混凝-斜管式,两相耦合,最终实现了加药量少、混凝沉淀效果好,而占用的箱体空间少和能耗及管理代价小的技术优势。
56.该技术的发明应用,主要解决了集装箱式狭小空间的三个技术问题,一是以往单级沉淀的实际污泥面积负荷过高(国家设计规范要求污泥固体负荷应≤ 150kg/m2·
d~200kg/m2·
d周进周出二沉池),且单级二沉池仅能保证出水达到一级b标准;二是以往单级沉淀无法很好地在箱内进行加药混凝沉淀,也就无法通过低药耗来实现高效率的辅助化学除磷和混凝沉淀来进一步削减cod、 ss、色度、tp等污染物,也就无法满足当今更高要求的一级a标准;三是以往若要实现两级沉淀就只能在两个箱体内分别完成,且两者之间的水头差往往会达到500~600mm,极不利于高程系统的布置和节能使用,也不利于装置的整装一体化。
57.本实用新型采用低阻力的快速管式混合器27进行水力混合,在斜管区5 底部的大空间进行混凝反应,其动力来自于泥水分离区4和斜管区5两者之间的水面高差,即所述的第一水面与第二水面之间的250mm~400mm高差,无需额外的水力机械提供动力,仅依靠设计时确定的水面高差提供持久动力。
58.因此,本实用新型利用小型污水装备的两级沉淀低水头节能技术,直接获得了高标准出水水质,还节省了宝贵的箱体空间,降低了系统装备投资,简化了运行管理,节约了总体能耗,降低了日常运行成本和维修维护成本。
59.四、斜管沉淀浅池布水与接触混凝技术
60.通常,用于污水处理的升流式异向流斜管(板)沉淀池的水深,一般在 3.40~4.40m,而集装箱式污水处理装置因受公路运输限高的制约,就只能将本实用新型集装箱式装置的斜管沉淀水深控制在不大于2.50m(考虑了与前一区域泥水重力分离区4的水力高差),因此,在高度数据上可谓“寸土寸金”。
61.本实用新型采用面向集装箱式污水处理装置特定的斜管沉淀浅池布水与接触混凝技术,将本实用新型集装箱式装置的斜管沉淀水深,成功控制在2.40m 左右,获得了令人满意的效果。
62.具体就是:斜管区上部水深0.50m,标准斜管斜长1.00m(60
°
角)的高度是0.866m,斜管区底部含缓冲层的高度1.014m,合计深度2.38m。为此,需要在底部含缓冲层的1.014m高度中,既要考虑均匀布水,又要考虑足够的絮凝时间和接触混凝效果,还要考虑沉淀的化学污泥高效排泥(尽量多排浓泥少排水),故,本实用新型采用的浅池布水与接触混凝技术,是集装箱式污水处理的核心技术之一,属于集装箱式污水领域的首创。
63.进一步的技术表现:经过加药和管式混合器27水力混合后的上清液,通过l形管道与斜管区5底部的布水穿孔管29相连,该布水穿孔管29为水平布置,且全部布水孔口均朝下而非朝上,其管道中心线距离底板高度150mm~ 350mm,且该布水管29的口径大于管式混合器27的口径;故,布水水流是朝向底板的喷射流,且布水穿孔管29的起端孔和末端孔的流速流量相差极小 (大阻力孔口布水原理——大管道小孔口布水),然后通过底板向两侧和孔口投影四周反射,反射作用将线性布水变成整个平面的缓慢均匀上升流,这样,既延长了有效的絮凝反应时间,强化了絮凝效果,又避免了出现短流和局部斜管冒浑水。
64.水流在整个平面缓慢均匀上升穿越悬浮泥层的过程中,与早先絮体和沉泥颗粒充分接触,又进一步提高了絮凝反应效果,使得絮体颗粒发育越来越大,局部位置的颗粒越来越密实而沉淀到两侧的u形穿孔排泥管28附近,部分轻质细小的颗粒随上升水流进入到斜管/斜板填料30中,在著名的浅层沉淀原理作用下,轻质细小颗粒被拦截沉淀在填料内斜壁上,继而下滑坠落到箱体底板成为污泥。在箱内底板两侧的污泥,通过两侧的穿孔排泥管28排出并经调节池污水泵提升,回到泥水重力分离区4后以剩余污泥的形式排出系统。
65.本实用新型应用上述浅池布水与接触混凝技术,满足了混凝反应-斜管沉淀在狭小空间的布局,实现了强化物化处理过程,用两级沉淀耦合的较低空间占用、少量的常规药剂和极低的能耗付出,进一步去除残余的cod、ss、 tp、色度等污染物,确保了出水稳定达到一级a标准,不仅简化了运行管理,免去了mbr复杂的清洗维修维护,节省了更换膜组件的昂贵成本,而且节约了70%的电费,大大降低了日常运行成本和人力成本。总之,获得了显著的有益效果。
66.五、小型污水集装箱式耦合接触消毒功能的一体化技术
67.该技术概括为:在集装箱式装置的末端,即斜管填料的斜壁外部空间,在该梯形空间内,充分利用该空间耦合成接触消毒空间,设置3块竖向隔板将该空间分成4等份,形成水流“迷宫”从而防止出现短流。
68.该技术必要性:鉴于一级b标准的细菌学指标(粪大肠菌群数104个/ l)与一级a(103个/l)相差10倍,而以往的集装箱式污水处理装置并不十分重视消毒问题,往往没有考虑,或者只简单化考虑使用紫外线消毒装置(紫外照度随灯管老化衰减,细菌学指标几乎不达标),故,本实用新型攻坚克难,采用集装箱式污水处理耦合接触消毒功能的一体化技术,有效解决了一级 a全指标(含细菌学指标)达标的难题,因而,本耦合技术十分必要。
69.具体的,设置在接触消毒区6起端顶部的消毒剂装置/投加点32,对汇入起端的清水投加消毒剂,含消毒剂的清水在该区须接触停留30min或以上,待充分杀灭细菌后,再从该区末端的出水堰35溢出,此时,细菌学指标合格的清水,经与箱体末端相连的流量计36计量后排出。
70.更进一步的,为了保证消毒效果,避免接触消毒的水流出现短流,本实用新型设置的3块竖向隔板33,其中的第1块第3块隔板的底部中心左侧开有过水孔洞34,这样就使得水流能在该区间上下左右曲折前行,确保了水流在该区接触停留30min或以上,达到充分杀灭细菌的目的。
71.本实用新型在技术经济两大层面,具有以下五点最明显的有益效果:
72.1、可满足集装箱式非mbr小型污水高标准处理要求:本实用新型装置技术独创且领先,其脱氮除磷效率高,出水水质好,各项指标均能达到一级a标准,无漏项无弱项,性能均衡,运行中的气路水路泥路药路等指标可控可调,水质达标易于掌控;
73.2、技术可靠性高:本实用新型装置不仅运行稳定可靠,还表现在技术原理、技术参数和构造细节各方面均十分可靠。本实用新型使用的专业术语规范,无隐秘难解的环节,无晦涩难懂的概念,更无故弄玄虚,内部构造一目了然,清晰明确,在技术路线规划设计时,就已经充分考虑了如何避免淤积堵塞和便于检修,且从理论深层次考虑如何预先消除潜在故障因素,因此,相比其他集装箱式污水处理装置,本实用新型使用者只要正常使用即可做到无后顾之忧;
74.3、整体造价低,制作不复杂,性价比高:采用集装箱式设计制造,内部构造紧凑化,反应容积最大化,装置标准化,无特殊材料(全部为常规水处理器材),无水下活动部件,通过构造和工艺设计已将淤积堵塞的可能性降至最低;箱内采用的空气双旋搅拌、微孔曝气、气提双回流、大口排泥、管式混合、反射布水、穿孔排泥、均匀集水、“迷宫”接触消毒等,以及箱外的污水提升泵、曝气鼓风机等部件装置,均为常规型,无昂贵材质要求,无特种部件 /组件,无昂贵价格制约,因此,相比集装箱式mbr装置而言,性价比优势十分明显;
75.4、日常运行成本低,使用单位或政府付费的财政经济压力低:
76.本实用新型在小型污水一体化处理领域,处于最低电耗、最低药耗水平。原因是污水处理,除了必须的进水污水泵提升和鼓风机曝气两项最基本的用电外,集装箱式装置本体并不直接用电,内部仅依靠重力(预置的水位差保障水往低处流、自然沉淀)和空气动力(气提动力源),与其他污水处理装置相比,本实用新型将搅拌能耗、回流能耗(多重回流、降低扬程)、药剂投加能耗、鼓风曝气能耗(较低气水比)、药耗(包含漂白精粉消毒剂等)已经降至最低,或者说效率已提升至最高。因此,本实用新型已将活性污泥法污水处理装置的能耗药耗降至行业最低,也就是说,同为集装箱式装置,相同污水处理量的情况下,同为一级a标准,则本实用新型的用电量最少,用药量最少,直接运行成本最低,水环境保护的经济代价最低;
77.5、运行操作简单,维修维护工作量小,维修(小修、大修)成本摊销低:
78.对运行管理人员的专业技能要求低,稍加培训即可上岗,不会因为过往装备操作复杂、对技能要求高而薪资又低导致人才难觅人才难留,或者干脆无人管理致使系统处于瘫痪状态的情况出现。本实用新型极少出现故障,且故障易于观察,容易修复,无需特别专业的团队千里迢迢诊断维修,亦无昂贵的部件 /组件需要频繁更换,且有可能需要更换的斜管/斜板填料、阀门等,均为水处理常规通用产品,不受专利价格因素制约。总之,本实用新型在运行过程中的人力资源成本、日常维修和/或专业维修的修理成本等单项成本和综合成本,都是目前行业同类最低,因而最易于环境保护的可持续发展。
79.综上所述,本实用新型乡村污水集装箱式a2o一体化处理装置,一次性建造成本(造价)最低,日常性各项运行成本包括人力和维修成本最低,也就是说,乡村污水的低成本处理和高标准处理,两者得到了有效兼顾。因此,本实用新型的应用前景十分广阔。
附图说明
80.图1为本实用新型的主剖面示意图。
81.图2为本实用新型的平面示意图。
82.图3为本实用新型的厌氧反应区1-1剖面示意图。
83.图4为本实用新型的缺氧脱氮区2-2剖面示意图。
84.图5为本实用新型的好氧硝化区3-3剖面示意图。
85.图6为本实用新型的好氧硝化区末端4-4剖面示意图。
86.图7为本实用新型的泥水重力分离区5-5剖面示意图。
87.图8为本实用新型的6-6剖面示意图。
88.图9为本实用新型的7-7剖面示意图。
89.图10为本实用新型的混凝反应-斜管沉淀区8-8剖面示意图。
90.图11为本实用新型的接触消毒区9-9剖面示意图。
91.图12为本实用新型的接触消毒区10-10剖面示意图。
92.其中:1—厌氧反应区,2—缺氧脱氮区,3—好氧硝化区,4—泥水重力分离区,5—混凝反应-斜管沉淀区,6—接触消毒区,7—进水管,8—厌氧空气搅拌管,8-1—缺氧空气搅拌管,9—第一小孔,10—矩形箱体,11—第一直隔板,12—第二直隔板,13—第三直隔板,14—第四斜隔板,15—第五斜隔板,16—第二小孔,17—点式气提装置,18—线式气提装置,19—硝化液回流管, 19-1—悬浮污泥回流管,20—空气管道,21—微孔曝气装置,22—竖直导流方管,23—第三中孔,24—大口排泥管,25—药剂投加口,26—集水管/槽, 27—管式混合器,28—穿孔排泥管,29—布水穿孔管,30—斜管/斜板填料, 31—清水集水槽,32—消毒剂装置/投加点,33—竖向隔板,34—过水孔洞, 35—出水堰,36—流量计。
具体实施方式
93.为了更好地理解本实用新型的技术方案,下面结合具体实施例进行阐述。显然,所描述的实施例仅仅是本实用新型的一部分实施例,不是全部实施例,在不脱离本实用新型精髓和原则的情况下,凡对本实施例进行变化、改进、修改、替换、整合和变型等,都属于本实用新型保护的范围。
94.实施例一
95.本实施例的乡村污水集装箱式a2o一体化处理装置,处理能力75m3/d,参照外贸集装箱的外部尺寸设计,具体参照40尺超高集装箱40hq型号的外形长12.192m
×
宽2.438m
×
高2.896m,本实施例的矩形箱体10外部实际尺寸为:长7.50m
×
宽2.43m
×
高2.88m,该外部尺寸不会受国内运输车辆和国内公路限宽限高的制约,因此便利于本实用新型在工厂批量化生产制造,也就是装置标准化和运输无障碍化,请参见图1、图2、图3。
96.本实施例具体由矩形箱体10和第一直隔板11,第二直隔板12,第三直隔板13,第四斜隔板14,第五斜隔板15,共五块隔板将箱内空间依序分隔成的厌氧反应区1、缺氧脱氮区2、好氧硝化区3、泥水重力分离区4、混凝反应-斜管沉淀区5、接触消毒区6共五大功能区组成。
97.所述厌氧反应区1、缺氧脱氮区2、好氧硝化区3、泥水重力分离区4形成第一水面,混凝反应-斜管沉淀区5为第二水面,接触消毒区6为第三水面,此三个水面的高度依次下降,成为水流从进水管7流向出水堰35的持久动力。
98.所述第一水面高于第二水面300mm,第二水面高于第三水面280mm。
99.所述第一水面的上部净超高为170mm,第二水面的上部净超高为 470mm,第三水面的上部净超高为750mm。
100.所述六大功能区的宽度,与矩形箱体10的有效宽度均相同。
101.所述厌氧反应区1长1.00m,水深2.68m,有效容积6.244m3,水力停留时间hrt=2.00h,混合液悬浮固体平均浓度x=4gmlss/l,污泥回流比 r=50%。
102.所述缺氧脱氮区2长1.70m,水深2.68m,有效容积10.615m3,水力停留时间hrt=3.40h,混合液悬浮固体平均浓度x=6gmlss/l,bod污泥负荷 ls=0.0482kgbod5/(kgmlss
·
d),脱氮速率k
de
=0.044kgno
3-n/ (kgmlss
·
d),污泥龄θc=21d,污泥回流比r=50%,硝化液回流比 ri=250%。
103.所述好氧硝化区3长2.21m,水深2.68m,有效容积13.800m3,水力停留时间hrt=4.41h,总氮负荷率0.043(≤0.05)kgtn/(kgmlss
·
d),混合液悬浮固体平均浓度x=6gmlss/l,污泥龄θc=21d,污泥回流比r=50%,硝化液回流比ri=250%。
104.所述泥水重力分离区4上部长1.67m,底部长0.50m,水深2.68m,有效容积6.375m3,沉淀时间2.04h,表面负荷为0.803m3/(m2·
h)。
105.所述混凝反应-斜管沉淀区5水面长0.66m,但斜管区域的实际长0.81m,水深2.38m,有效容积5.026m3,沉淀时间1.608h,斜管表面负荷为1.656m
3 /(m2·
h),其中,斜管下部的混凝区容积2.471m3,混凝反应时间0.79h=47.4 min。
106.所述接触消毒区6上部长0.25m,底部长0.89m,水深2.10m,有效容积 3.51m3,接触消毒时间即水力停留时间hrt=1.12h=67min。
107.如图1、图2、图3所示,所述厌氧反应区1内,在离底板高度450mm处的首端平面中心位置,设有污水进水管7,口径为dn65;在底部高度100mm 处设有2根平行的空气搅拌管8-1,口径为dn25,每根管上开有6个@150mm 布置且朝下45
°
的φ4mm喷气小孔。每根空气搅拌管8-1接一根dn20的空气立管,且在箱外顶部各对应设置一台电磁阀/电动阀,并与plc控制器或时间控制器衔接。所述厌氧反应区1的末端,在第一直隔板11的上部开有2个第一小孔9(尺寸200
×
100mm),对称布置,与缺氧脱氮区2相通。为了防止底部边角出现泥沙淤积,还设置了底部锥坡,同时也起到了空气搅拌导流的增强效果。
108.如图1、图2、图4所示,所述缺氧脱氮区2内,在水面下贴近水面处靠近第一小孔的位置,设有硝化液回流管19和悬浮污泥回流管19-1的出流管道口,规格均为dn65,管口分别距离第一小孔9中心300mm;另外,在底部高度100mm处设有2根平行的空气搅拌管8-1,口径为dn32,每根管上开有10 个@150mm布置且朝下45
°
的φ4mm喷气小孔。每根空气搅拌管8-1接一根 dn25的空气立管,且在箱外顶部各对应设置一台电磁阀/电动阀,并与plc 控制器或时间控制器衔接。所述缺氧脱氮区2的末端,在第二直隔板12的底部开有2个第二小孔16(尺寸200
×
150mm),对称布置,与好氧硝化区3相通。为了防止底部边角出现泥沙淤积,还设置了底部锥坡,同时也起到了空气搅拌导流的增强效果。
109.如图1、图2、图5和图6所示,所述好氧硝化区3内,底部设有15个通用型微孔曝气盘,即微孔曝气装置21的规格为φ215mm,通过该区中部的曝气立管与箱外的曝气鼓风机用阀门管道等相连。该区的末端设有1套点式气提装置17,气提动力源自箱外顶部的曝气鼓风机压力空气管,与生化反应鼓风曝气共用同一动力。所述点式气提装置17的进口设在水深中部附近,出口通过管道管件与贴近水面处的硝化液回流管19相接,最终送往缺氧脱氮区2贴水面处靠近第一小孔9中心的距离300mm位置,以便与厌氧处理后的污水充分混合。好氧硝化区3的末端平面中部位置紧贴第三直隔板13处,还设有竖直导流方管22,方管规格300
×
180mm,顶部敞口离水面200mm,底部用斜板封闭,斜板水平角45
°
,通过第三直隔板13下部的第三中孔23与泥水重力分离区4 相通,第三中孔23的大小尺寸为540
×
300mm。
110.如图1、图2、图7、图8和图9所示,所述泥水重力分离区4内,其底部设有大口排泥管24,排泥管口径dn65,含2个对称布置的朝下排泥口,设置成大口的原因是防止底层污泥中的纤维毛发糖果纸等垃圾杂质堵塞排泥口,为了防止底部角落出现泥沙淤积,还设置了底部锥坡,同时也起到了污泥重力浓缩的效果;水深中部偏上位置设有线式气提装置18,气提动力源自箱外顶部的曝气鼓风机压力空气管,与生化反应鼓风曝气共用同一动力。所述线
式气提装置18的进口为纵向水平的穿孔吸泥管上的吸泥孔口,出口通过管道管件与贴近水面处的悬浮污泥回流管19-1相接,最终送往缺氧脱氮区2贴水面处靠近第一小孔9中心的距离300mm位置,以便与厌氧处理后的污水充分混合;该区的水面中间上方位置,设有药剂投加口25,其下方水面处设有集水管/槽 26,用于收集该区的上清液至下一区域,集水管/槽26与更下方的管式混合器27呈t形相连,管式混合器27为低阻力固定螺旋叶片快速混合型,规格为 dn65;管式混合器27下方再接管道向下穿越斜隔板14进入混凝反应-斜管沉淀区5,经l形管道与布水穿孔管29相连。
111.如图1、图2、图9和图10所示,所述混凝反应-斜管沉淀区5内,底部两侧各设一根穿孔排泥管28并连成u形,规格dn80,管道底部开有间隔均匀的φ24mm进泥小孔,采用内外静压差排泥,由电动阀门控制间隔周期排泥,由于该区的污泥所含杂质较少,主要是絮凝沉淀的化学污泥,因而不采用大口排泥而采用成熟的大阻力穿孔管排泥方式,另外,两侧边角还设置了底部锥坡,起到污泥重力浓缩的效果,该排泥经箱外调节池污水泵提升,回到所述泥水重力分离区4后以剩余污泥的形式排出系统;所述斜管区5的底部中间设有布水穿孔管29规格dn80,水平布置且布水孔口朝下,管道中心线距离底板高度 180mm,均布6个φ24mm布水孔,采用比管式混合器dn65大一个规格的 dn80布水穿孔管29,其目的是保障管道上首孔和末孔的布水流量差尽可能小;另外,该区水深中部设有污水专用型标准蜂窝斜管/斜板填料30,口径为φ80mm,斜长为1000mm,60
°
倾角,沉淀在该填料内斜壁上继而下滑坠落到箱体底板的化学污泥,通过穿孔排泥管28排出;同时,在水面处还设有3根平行的清水集水槽31,此时,该表层清水除细菌学指标外,其余各项均符合一级 a排放标准,与其他技术相比,减少了需要频繁反冲洗的过滤设备设施,因而从造价、运行能耗、管理上都有很大节省;总之,该区的水力混合和絮凝反应动力,来自于泥水分离区4和斜管区5两者之间的水面高差,即所述的第一水面与第二水面之间的300mm高差,无需额外的水力机械提供动力,仅依靠设计时确定的水面高差提供持久动力。最后,清水经集水槽31收集后穿越第五斜隔板15,进入到接触消毒区6进行消毒处理。
112.如图1、图2、图11和图12所示,所述接触消毒区6内,设有3块竖向隔板33将该区空间均分为4等份,其中的第1块第3块板底部左侧设有过水孔洞 34,该过水孔尺寸200
×
100mm,第2块板顶部低于设计水面80mm;在该区的起端上方设有消毒剂装置/投加点32,对汇入的清水投加固体消毒剂溶液,固体消毒剂可以是缓释氯片/漂白粉/漂白精粉等,可根据市场供应情况采购选定;在该区的末端贴近水面处,设有dn150规格的出水堰35,堰顶标高低于设计水面40mm,出水堰的出口通过dn65管道管件连接至箱体外,经过消毒后的清水从出水堰35溢出并通过与箱体末端相连的流量计36计量后排出,该流量计的规格为dn65。
113.本实施例的乡村污水集装箱式a2o一体化处理装置,其进水水质和出水水质,见下表。
[0114][0115]
结果表明:对一般的生活污水而言,本实施例的乡村污水集装箱式a2o一体化处理装置,在两级沉淀而没有过滤的情况下,出水水质可以稳定达到国家一级a标准。本实施例处理每m3污水的电耗(含污水提升、鼓风曝气等)、药耗、人工及大修摊销等直接成本合计为0.58元,其建设投资、占地、运行成本等与现有其他集装箱式污水处理一级a技术同等规模相比,大致可节约50%左右,因而,本实用新型的技术经济效益非常显著,获得了良好的污水脱氮除磷深度处理效果和技术经济效果。
[0116]
实施例二
[0117]
本实施例的乡村污水集装箱式a2o一体化处理装置,处理能力150m3/ d,参照外贸集装箱的外部尺寸设计,具体参照40尺超高集装箱40hq型号的外形长12.192m
×
宽2.438m
×
高2.896m,本实施例的矩形箱体10外部实际尺寸为:长12.150m
×
宽2.43m
×
高2.88m,该外部尺寸不会受国内运输车辆和国内公路限宽限高的制约,因此便利于本实用新型在工厂批量化生产制造,也就是装置标准化和运输无障碍化,请参见图1、图2、图3。
[0118]
本实施例的构造形式与实施例一相同。为避免重复,将相同的内容略去,不同的内容如下:
[0119]
所述六大功能区的宽度,与矩形箱体10的有效宽度均相同。
[0120]
所述厌氧反应区1长2.00m,水深2.68m,有效容积12.488m3,水力停留时间hrt=2.00h,混合液悬浮固体平均浓度x=4gmlss/l,污泥回流比 r=50%。
[0121]
所述缺氧脱氮区2长3.22m,水深2.68m,有效容积20.107m3,水力停留时间hrt=3.22h,混合液悬浮固体平均浓度x=6gmlss/l,bod污泥负荷 ls=0.0467kgbod5/(kgmlss
·
d),脱氮速率k
de
=0.0436kgno
3-n/ (kgmlss
·
d),污泥龄θc=21d,污泥回流比r=50%,硝化液回流比 ri=250%。
[0122]
所述好氧硝化区3长4.02m,水深2.68m,有效容积25.102m3,水力停留时间hrt=4.01h,总氮负荷率0.0429(≤0.05)kgtn/(kgmlss
·
d),混合液悬浮固体平均浓度x=6gmlss/l,污泥龄θc=21d,污泥回流比r=50%,硝化液回流比ri=250%。
[0123]
所述泥水重力分离区4上部长1.90m,底部长0.73m,水深2.68m,有效容积7.811m3,沉淀时间1.25h,表面负荷为1.412m3/(m2·
h)。
[0124]
所述混凝反应-斜管沉淀区5水面长0.75m,但斜管区域的实际长0.90m,水深2.38m,有效容积5.525m3,沉淀时间0.884h,斜管表面负荷为2.98m3/ (m2·
h),其中,斜管下部的混凝区容积2.6837m3,混凝反应时间0.4293 h=25.7min。
[0125]
所述接触消毒区6上部长0.25m,底部长0.89m,水深2.10m,有效容积 3.51m3,接触消毒时间即水力停留时间hrt=0.561h=33.6min。
[0126]
如图1、图2、图3所示,所述厌氧反应区1内,在离底板高度500mm处的首端平面中心
位置,设有污水进水管7,口径为dn80;在底部高度100mm 处设有2根平行的空气搅拌管8-1,口径为dn32,每根管上开有每根管上开有 10个@170mm布置且朝下45
°
的φ4mm喷气小孔。每根空气搅拌管8-1接一根dn32的空气立管,且在箱外顶部各对应设置一台电磁阀/电动阀,并与 plc控制器或时间控制器衔接。所述厌氧反应区1的末端,在第一直隔板11的上部开有2个第一小孔9(尺寸200
×
200mm),对称布置,与缺氧脱氮区2相通。为了防止底部边角出现泥沙淤积,还设置了底部锥坡,同时也起到了空气搅拌导流的增强效果。
[0127]
如图1、图2、图4所示,所述缺氧脱氮区2内,在水面下贴近水面处靠近第一小孔的位置,设有硝化液回流管19和悬浮污泥回流管19-1的出流管道口,规格均为dn80,管口分别距离第一小孔9中心300mm;另外,在底部高度100mm处设有2根平行的空气搅拌管8-1,口径为dn40,每根管上开有每根管上开有16个@140mm布置且朝下45
°
的φ4mm喷气小孔。每根空气搅拌管8-1接一根dn40的空气立管,且在箱外顶部各对应设置一台电磁阀/电动阀,并与plc控制器或时间控制器衔接。所述缺氧脱氮区2的末端,在第二直隔板12的底部开有2个第二小孔16(尺寸200
×
200mm),对称布置,与好氧硝化区3相通。为了防止底部边角出现泥沙淤积,还设置了底部锥坡,同时也起到了空气搅拌导流的增强效果。
[0128]
如图1、图2、图5和图6所示,所述好氧硝化区3内,底部设有27个通用型微孔曝气盘,即微孔曝气装置21的规格为φ215mm,通过该区中部的曝气立管与箱外的曝气鼓风机用阀门管道等相连。该区的末端设有1套点式气提装置17,气提动力源自箱外顶部的曝气鼓风机压力空气管,与生化反应鼓风曝气共用同一动力。所述点式气提装置17的进口设在水深中部附近,出口通过管道管件与贴近水面处的硝化液回流管19相接,最终送往缺氧脱氮区2贴水面处靠近第一小孔9的距离300mm位置,以便与厌氧处理后的污水充分混合。好氧硝化区3的末端平面中部位置紧贴第三直隔板13处,还设有竖直导流方管 22,方管规格400
×
240mm,顶部敞口离水面200mm,底部用斜板封闭,斜板水平角45
°
,通过第三直隔板13下部的第三中孔23与泥水重力分离区4相通,第三中孔23的大小尺寸为740
×
400mm。
[0129]
如图1、图2、图7、图8和图9所示,所述泥水重力分离区4内,其底部设有大口排泥管24,排泥管口径dn65,含2个对称布置的朝下排泥口,设置成大口的原因是防止底层污泥中的纤维毛发糖果纸等垃圾杂质堵塞排泥口,为了防止底部角落出现泥沙淤积,还设置了底部锥坡,同时也起到了污泥重力浓缩的效果;水深中部偏上位置设有线式气提装置18,气提动力源自箱外顶部的曝气鼓风机压力空气管,与生化反应鼓风曝气共用同一动力。所述线式气提装置18的进口为纵向水平的穿孔吸泥管上的吸泥孔口,出口通过管道管件与贴近水面处的悬浮污泥回流管19-1相接,最终送往缺氧脱氮区2贴水面处靠近第一小孔9中心的距离300mm位置,以便与厌氧处理后的污水充分混合;该区的水面中间上方位置,设有药剂投加口25,其下方水面处设有集水管/槽 26,用于收集该区的上清液至下一区域,集水管/槽26与更下方的管式混合器27呈t形相连,管式混合器27为低阻力固定螺旋叶片快速混合型,规格为 dn80;管式混合器27下方再接管道向下穿越斜隔板14进入混凝反应-斜管沉淀区5,经l形管道与布水穿孔管29相连。
[0130]
如图1、图2、图9和图10所示,所述混凝反应-斜管沉淀区5内,底部两侧各设一根穿孔排泥管28并连成u形,规格dn80,管道底部开有间隔均匀的φ24mm进泥小孔,采用内外静压差排泥,由电动阀门控制间隔周期排泥,由于该区的污泥所含杂质较少,主要是絮凝沉淀的化学污泥,因而不采用大口排泥而采用成熟的大阻力穿孔管排泥方式,另外,两侧边角还
设置了底部锥坡,起到污泥重力浓缩的效果,该排泥经箱外调节池污水泵提升,回到所述泥水重力分离区4后以剩余污泥的形式排出系统;所述斜管区5的底部中间设有布水穿孔管29规格dn100,水平布置且布水孔口朝下,管道中心线距离底板高度 200mm,均布8个φ24mm布水孔,采用比管式混合器dn80大一个规格的 dn100布水穿孔管29,其目的是保障管道上首孔和末孔的布水流量差尽可能小;另外,该区水深中部设有污水专用型标准蜂窝斜管/斜板填料30,口径为φ80mm,斜长为1000mm,60
°
倾角,沉淀在该填料内斜壁上继而下滑坠落到箱体底板的化学污泥,通过穿孔排泥管28排出;同时,在水面处还设有3根平行的清水集水槽31,此时,该表层清水除细菌学指标外,其余各项均符合一级 a排放标准,与其他技术相比,减少了需要频繁反冲洗的过滤设备设施,因而从造价、运行能耗、管理上都有很大节省;总之,该区的水力混合和絮凝反应动力,来自于泥水分离区4和斜管区5两者之间的水面高差,即所述的第一水面与第二水面之间的300mm高差,无需额外的水力机械提供动力,仅依靠设计时确定的水面高差提供持久动力。最后,清水经集水槽31收集后穿越第五斜隔板15,进入到接触消毒区6进行消毒处理。
[0131]
如图1、图2、图11和图12所示,所述接触消毒区6内,设有3块竖向隔板33将该区空间均分为4等份,其中的第1块第3块板底部左侧设有过水孔洞 34,该过水孔尺寸250
×
120mm,第2块板顶部低于设计水面80mm;在该区的起端上方设有消毒剂装置/投加点32,对汇入的清水投加固体消毒剂溶液,固体消毒剂可以是缓释氯片/漂白粉/漂白精粉等,可根据市场供应情况采购选定;在该区的末端贴近水面处,设有dn200规格的出水堰35,堰顶标高低于设计水面40mm,出水堰的出口通过dn80管道管件连接至箱体外,经过消毒后的清水从出水堰35溢出并通过与箱体末端相连的流量计36计量后排出,该流量计的规格为dn80。
[0132]
本实施例的乡村污水集装箱式a2o一体化处理装置,其进水水质和出水水质,见下表。
[0133][0134]
结果表明:本实施例的乡村污水集装箱式a2o一体化处理装置,在两级沉淀而没有过滤的情况下,出水水质可以稳定达到国家一级a标准。本实施例处理每m3污水的电耗(含污水提升、鼓风曝气等)、药耗、人工及大修摊销等直接成本合计为0.55元,其建设投资、占地、运行成本等与现有其他集装箱式污水处理一级a技术同等规模相比,大致可节约50%左右,因而,本实用新型的技术经济效益非常显著,获得了良好的深度处理效果和技术经济效果。
[0135]
本实用新型乡村污水集装箱式a2o一体化处理装置,仅需要定期观察排泥量筒sv30(污泥沉降比——活性污泥在1升量筒中沉降30min后的体积,ml /l)和svi(污泥体积指数——活性污泥静沉30min后1g干污泥所占的体积,ml/g)指数情况,根据操作规程结合上述实际观察,适当调整确定间隔多久时间开启一次排泥。除此之外,本实用新型乡村污水
集装箱式a2o一体化处理装置的运行极为简捷,通常可处于无人值守状态,只需值班人员定期观察是否存在堵塞、溢流和冒浑水等异常即可,因此,本实用新型乡村污水集装箱式a2o一体化处理装置的高效率、高可靠性、节能和最低运行成本显露无疑。
[0136]
从以上两个实施例可以看出,本实用新型不仅可以处理不同规模的农村生活污水,而且可以低成本进行深度处理直接达到一级a标准,无需另外增设复杂的滤池或mbr膜组件。因此,本实用新型与其他集装箱式污水处理装备相比,获得了工艺简捷、建造低成本、运行低成本的有益效果。
[0137]
最后应说明的是:以上仅为本实用新型的优选实施例而已,并不用于限制本实用新型,对于本领域的技术人员来说,其依然可以对本实用新型所述各实施例的技术方案进行修改,或者对其中部分技术特征进行等同替换,所作的任何修改、等同替换、改进等,均应包含在本实用新型的保护范围之内。