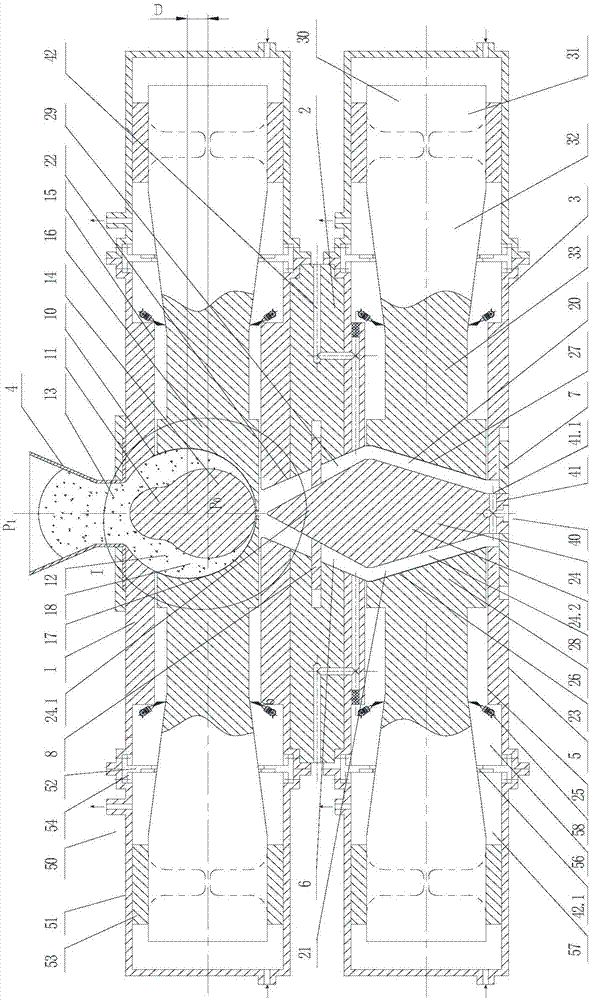
本发明涉及中草药加工的
技术领域:
,具体涉及一种博落回超声微粉碎装置及博落回总生物碱提取工艺。
背景技术:
:博落回茎、叶、果实均含有生物碱。在植物体各个器官中这些生物碱的含量是不同的。实验结果表明,在同一生长时期、同一种植区域内,博落回植株地上部分各器官中生物碱的含量是果实>叶>茎。在浙江地区,7~11月份正是博落回植株结果的时节。在这一阶段,应采收博落回果实提取其生物碱。野生博落回植株各器官中生物碱含量均高于种植博落回植株。提取博落回生物碱的方法较多,典型的有采用溶剂法和大孔树脂法,提取时间较长,提取率低。影响提取转移率的因素很多,固液比、提取时间、提取温度。另外还有微波辅助提取、超声波辅助提取。但是,还有一个比较重要的因素,即被提取物的原料颗粒大小。颗粒越小,越容易提取。四川宝鼎香中药科技开发有限公司的发明专利cn104262448a公开了一种从甘草中提取甘草酸的方法,其中,对甘草粉碎粒径的选择,将风干后的甘草粉碎成不同粒径,采用药典2010版中的水煮法进行提取、冷却后,调节ph为2.0,离心,收集沉淀物,干燥后得到甘草酸粗品,不同粒径的甘草颗粒的收率如下表。粒径(μm)305075100150200250收率1.8%3.6%3.3%3.1%2.7%2.6%1.9%得出结论,50-200μm时,收率相对较高,粒径在50μm时,收率最高。那么,如何能把博落回干燥的果实、茎、叶粉碎成50um这么小的颗粒呢?微粉碎技术。现有技术的微粉碎一般包括机械粉碎机、振动磨和气流粉碎机。机械粉碎机是利用高转速的搅拌臂带动介质球和物料,使之发生摩擦、撞击、剪切,从而使物料细化。一般物料可细化至d90<2μm,d50达0.1-1μm。振动磨石利用高速振动使介质产生振动冲击及介质回转,使粉料得到正向撞击的同时又得到剪切力的作用,其效率比机械粉碎机高10-20倍,振动磨产品的平均粒径可达到2-3μm以下。气流磨粉机,俗称流能磨,是一种利用高压气流使粉碎物料粒子相互激烈碰撞冲击、摩擦以及利用气流对物料的直接剪切作用达到粉碎效果的设备。气流磨粉碎产品的细度可达到2-40μm。尽管上述三类方法均能得到微米级颗粒,但是都具有效率低,粒径分布不易控制的问题。因此,有必要针对微粉碎进行针对性改进,以解决效率低、粒径分布不易控制的问题,突破中草药提取方面的瓶颈。技术实现要素:针对上述现有技术中存在的缺陷,本发明的目的在于提供一种博落回超声微粉碎装置及博落回总生物碱提取工艺。本发明的目的是这样实现的,一种博落回超声微粉碎装置,包括顺序竖直设置在机架上的一级粉碎机构和二级粉碎机构,机架包括顺序叠置的第一模板、第二模板和第三模板,加料斗设置在第一模板上;一级粉碎机构包括圆柱形料腔和圆柱辊,圆柱形料腔的轴线垂直于加料斗水平地设置第一模板中,且圆柱辊轴线与圆柱形料腔轴线平行下移偏心距离水平固定在圆柱形料腔中;圆柱辊轴线与加料斗轴线构成平面л;第一模板于圆柱形料腔两侧分别轴对称地、轴线垂直于平面л地开设超声头安装孔,第一振动头可水平振动地安装在第一超声头安装孔中,所述第一振动头固定在超声振动机构上;二级粉碎机构设置在第三模板中,二级粉碎机构包括第二料腔,第二料腔中固定有芯模,第三模板正对芯模两侧面分别轴对称地、轴线垂直于平面л地开设第二超声头安装孔,第二振动头可水平振动地安装在第二超声头安装孔中。进一步地,所述第二料腔包括首尾相接的倒v形腔和v形微粉碎腔,芯模包括倒v形分流梭和v形芯,倒v形分流梭与倒v形腔构成分流通道,v形芯侧面与第二振动头之间构成微粉碎通道,微粉碎通道设有粉末流化机构。进一步地,所述粉末流化机构包括入射气流结构和溢出气流结构,入射气流结构设置在微粉碎通道底部,溢出气流结构设置在分流流道中,入射气流结构包括设置在v形芯底部两侧面的多个入射气流孔,溢出气流结构包括对应接续流道缝位置设置在第三模板中的多个溢出气流孔。进一步地,所述第一振动头具有第一超声作用面,该第一超声作用面与圆柱辊表面形成横截面连续变窄的超声作用区域,第一超声作用面的下边缘低于圆柱辊圆柱表面最低点且下边缘距离该最低点距离为下边缘距离,该下边缘距离决定了该一级粉碎机构的最小颗粒直径。进一步地,所述第二振动头具有第二超声作用面,第二超声作用面为平行于v形芯侧面的斜面。进一步地,超声振动机构包括一体顺序连接的超声转换器、变幅杆和振动杆,第一振动头或第二振动头同轴地固定在振动杆端部。进一步地,第一模板、第三模板侧面通过法兰对合方式固定有可拆定位结构,可拆定位结构包括超声定位壳,弹簧板和支撑定位夹,超声振动机构通过弹簧板和支撑定位夹可水平振动地藕接在超声定位壳中。进一步地,还包括与圆柱辊一体连接的分流锥,分流锥横截面为轴线平行于圆柱辊轴线且位于圆柱辊轴线正上方的凸圆弧。一种博落回总生物碱超声辅助提取工艺,包括如下步骤:1)一级粉碎,将冷冻干燥的博落回植株经粉碎机构粉碎,过筛得到粒径小于1mm的博落回颗粒;2)超声微粉碎,将所述博落回颗粒通过超声粉碎机构,微粉碎成20-100μm的博落回微颗粒;3)超声辅助提取将博落回微颗粒加入到有机溶剂中,液料比为150-250l/kg,并在如权利要求1-8任一所述博落回超声微粉碎装置中连续循环20-40min,提取温度为55℃-70℃,得博落回提取液;4)分离纯化,将所述博落回提取液分离纯化,得到博落回总生物碱。进一步地,所述博落回超声微粉碎装置得到的博落回颗粒粒径在20-50μm。所述博落回超声微粉碎装置及其超声辅助提取工艺,通过颗粒重力下落的第一超声作用区域,和内置粉末流化结构40的微粉碎通道,微粉碎通道中再次长时间作用超声波振动,使得微粉碎粒径可控,使得博落回总生物碱的转移率大大增加。附图说明图1为本发明一种博落回超声微粉碎装置的主剖视图。图2为本发明一种博落回超声微粉碎装置的图1中局部放大图i。图3为本发明一种博落回总生物碱超声辅助提取工艺的流程图。上述图中的附图标记:1第一模板,2第二模板,3第三模板,4加料斗,5机架,6分流流道,7底阀门,8中阀门10一级粉碎机构,11分流锥,12圆柱形料腔,13颈腔,14圆柱辊,15第一超声头安装孔,16第一振动头,17第一超声作用面,18超声作用区域,19第一料缝隙20二级粉碎机构,21第二料腔,22倒v形腔,23v形微粉碎腔,24芯模,25第二超声头安装孔,26第二振动头,27第二超声作用面,28微粉碎通道,29分流流道30超声振动机构,31超声波转换器,32变幅杆,33振动杆40粉末流化机构,41入射气流结构,42溢出气流结构50可拆定位结构,51超声定位壳,52弹簧板,53支撑定位夹,54肩槽,55紧固螺栓,56缓冲室,57定位室具体实施方式以下结合附图对本发明的实施例作详细说明,但不用来限制本发明的范围。实施例一如图1所示,一种博落回超声微粉碎装置,包括顺序竖直设置在机架5上的一级粉碎机构10和二级粉碎机构20,机架5包括顺序叠置的第一模板1、第二模板2和第三模板3,加料斗4设置在第一模板1上;一级粉碎机构10设置在第一模板1中,一级粉碎机构10包括圆柱形料腔12,圆柱形料腔12的轴线垂直于加料斗4水平地设置第一模板1中,所述圆柱形料腔12通过颈腔13连通加料斗4,分流锥11与圆柱辊14一体连接,且圆柱辊轴线与圆柱形料腔12轴线下移偏心距离d水平固定在第一模板2的圆柱形料腔12中,圆柱辊表面最低点距离圆柱形料腔12为下边缘距离l1,优选下边缘距离l1小于1mm;圆柱辊轴线通过圆心p0并与加料斗轴线p0p1构成平面л。第一模板1于圆柱形料腔12两侧分别轴对称地、轴线垂直于平面л地开设第一超声头安装孔15,第一振动头16安装在第一超声头安装孔15中。所述第一振动头16固定在超声振动机构30上;超声振动机构30包括一体顺序连接的超声转换器31、变幅杆32和振动杆33,第一振动头16同轴地固定在振动杆33端部;所述第一振动头16具有第一超声作用面17,所述第一超声作用面17为圆柱面,第一超声作用面17位于振动原点时,该圆柱面与圆柱形料腔12内表面重合且振动杆33的轴线垂直于平面л,圆柱辊轴线与第一超声作用面17轴线下移偏心距离d,此时第一超声作用面17的上边缘距离圆柱辊14圆柱表面距离为上边缘距离l0,第一超声作用面17的下边缘低于圆柱辊圆柱表面最低点且下边缘距离该最低点距离为下边缘距离l1,该下边缘距离l1决定了粉碎的最小颗粒直径。该第一超声作用面17与圆柱辊14表面形成横截面连续变窄的超声作用区域18。两侧的第一超声作用面17之间形成出第一料缝隙19。第二模板2中设有倒v形分流流道6,分流流道6连通所述第一料缝隙19。二级粉碎机构20设置在第三模板3中,二级粉碎机构20包括第二料腔21,所述第二料腔21包括首尾相接的倒v形腔22和v形微粉碎腔23,第二料腔21中固定有芯模24,所述芯模24横截面为梭子形,包括倒v形分流梭24.1和v形芯24.2,倒v形分流梭24.1与倒v形腔22构成分流通道29。第三模板3正对v形芯24.2两侧面分别轴对称地、轴线垂直于平面л地开设第二超声头安装孔25,第二振动头26安装在第二超声头安装孔25中。所述第二振动头26固定在超声振动机构30上;第二振动头26同轴地固定在振动杆33端部;所述第二振动头26具有第二超声作用面27,第二超声作用面27为平行于v形芯24.2侧面的斜面,第二超声作用面27和v形芯24.2侧面之间形成微粉碎通道28。为了让二级粉碎机构能够更长时间地作用在因重力在微粉碎通道28中自由下落的粉末颗粒上,在微粉碎通道28底部设有粉末流化机构40,所述粉末流化机构40包括入射气流结构41和溢出气流结构42,入射气流结构41设置在微粉碎通道28底部,溢出气流结构42设置在分流流道29中。入射气流结构41包括设置在v形芯24.2底部两侧面的多个入射气流孔41.1,所述入射气流孔41.1由入射气流管道接气源。溢出气流结构42包括对应接续流道缝29位置设置在第三模板中的多个溢出气流孔42.1。微粉碎通道28底部设有底阀门7,分流通道29中设有中阀门8,所述底阀门7、中阀门8关闭时,在微粉碎通道28中,颗粒粉末在粉末流化机构40的作用下浮动在在微粉碎通道28中,第二振动头26持续作用超声波于颗粒粉末,将其均匀振动成更小的颗粒。作用一定时间后,底阀门7开启,关闭粉末流化机构40,符合粒径要求的微粉末从微粉碎通道28中流出。底阀门7关闭,中阀门8打开,在对接流道缝29中积累的颗粒粉末进入微粉碎通道28中,第二振动头26的超声波又作用在新的颗粒粉末上。因为是水平配置超声振动机构30,第一模板1、第三模板3侧面通过法兰对合方式固定有可拆定位结构50,可拆定位结构50包括超声定位壳51,弹簧板52和支撑定位夹53,超声定位壳51固定在第一模板1、第三模板3侧面,第一模板法兰和超声定位壳法兰分别具有台阶部,对合时所述台阶部形成肩槽54。超声换能器31松弛地夹持在支撑定位夹53中,同时变幅杆32上的固定法兰固定在弹簧板52的凹槽内并通过螺栓固连,弹簧板52边缘伸入肩槽54内通过紧固螺栓55紧固。调整在肩槽54内的垫片可将超声作用面调整到最佳位置,两点支撑柱状的超声振动机构,比较稳定。固定法兰设有气体溢出孔56,以减少超声振动的空气阻力。弹簧板52分别和第一超声头安装孔15、第二超声头安装孔25之间形成缓冲室56,超声定位壳51和弹簧板52之间形成定位室57,定位室56设有入口和出口,通干燥空气以防止漏电发生。缓冲室内围绕第一超声头安装孔15圆周分布有多个挡尘毛刷58。一种使用上述博落回超声微粉碎装置的博落回总生物碱超声辅助提取工艺,包括如下步骤:1)一级粉碎,将冷冻干燥的博落回植株经粉碎机构粉碎,过筛得到粒径小于1mm的博落回颗粒;2)超声微粉碎,将所述博落回颗粒通过所述博落回超声微粉碎装置,微粉碎成20-100μm的博落回微颗粒;3)超声辅助提取将博落回微颗粒加入到乙醇水溶液中,其中乙醇水溶液的体积分数为80-90%,ph值为5-6,液料比为150-250l/kg,持续超声作用20-40min,提取温度为55℃-70℃,得博落回提取液。4)分离纯化,将所述博落回提取液分离纯化,得到博落回总生物碱;为了测定转移率,取生物碱含量为0.76%的野生博落回叶10kg,按照粒径不同范围,分别重复三次上述提取工艺,分别计算转移率,得到如下表1:重量相同、微粉碎粒径不同的三批次的博落回颗粒,粒径范围20-110μm时,总生物碱的平均转移率为96.2%。工作原理:为了解决“效率低、粒径不易控制”的技术问题,本申请采用如下技术手段:1)一级粉碎,第一超声作用面和圆柱辊面之间构成横截面积从上至下逐渐减小的超声作用区域,下边缘距离l1使得一级粉碎可控粒径第一超声作用面和圆柱辊面之间构成横截面积从上至下逐渐减小的超声作用区域,圆柱辊轴线与第一超声作用面17轴线下移偏心距离d,第一超声作用面17的下边缘低于圆柱辊圆柱表面最低点且下边缘距离该最低点距离为下边缘距离l1,当原料颗粒从加料斗加入时,粉末进入超声作用区域,通过超声波的作用,再通过上述几何约束,使得只有粒径小于下边缘距离l1的颗粒才能从第一料缝隙19流出,以此来使一级粉碎粒径可控。2)二级粉碎,一级粉碎粒径配合粉末流化机构,便于在微粉碎通道再次作用超声波,进行进一步粉碎下边缘距离l1优选小于1mm,一级粉碎粒径已经非常细,粒径这么细的颗粒如果仅靠重力会堆在底部,通过粉末流化机构则飘浮在微粉碎通道中,这样在第二超声作用面的超声波作用下,粉末进一步粉碎成20-100μm的微粉末,优选到20-50μm,直到作用到规定时间,微粉碎通道中的微粉末才会从底阀门7排出。一级粉碎是二级粉碎的基础,一级粉碎和二级粉碎的效果叠加,使得原料粉末粉碎到微米级别。3)圆柱辊两侧圆柱表面和第一、二超声作用面分别构成对称设置的超声作用区域和微粉碎通道,效率提高对称在圆柱表面两侧的超声作用区域和微粉碎通道,使得粉碎区域增加一倍,效率提高。所述博落回超声微粉碎装置及其超声辅助提取工艺,通过颗粒重力下落的第一超声作用区域,和内置粉末流化结构40的微粉碎通道,微粉碎通道中再次长时间作用超声波振动,使得微粉碎粒径可控,使得博落回总生物碱的转移率大大增加。当前第1页12