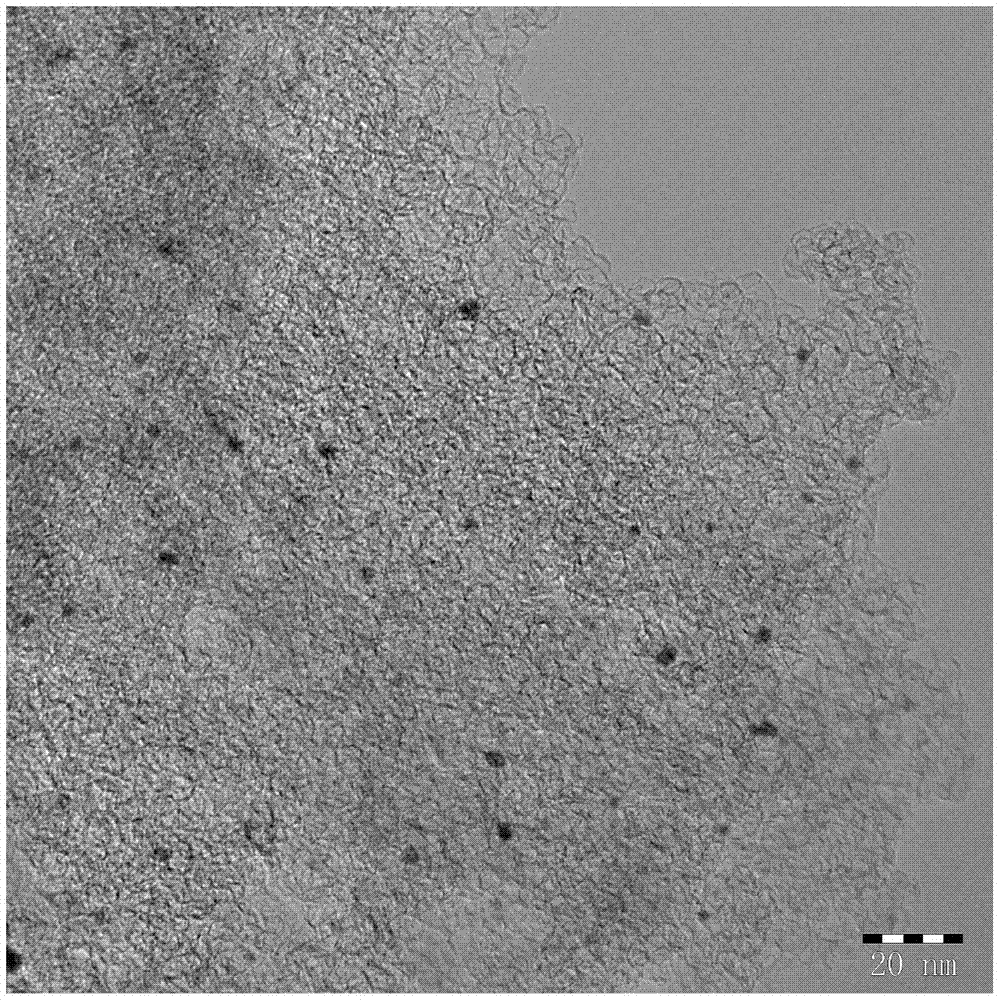
本发明属于贵金属催化剂制备
技术领域:
,具体涉及一种pt-fe/c催化剂及其制备方法和应用。
背景技术:
:氯代苯胺是用于合成染料、医药和农药等的重要中间体,市场需求量很大,主要生产方法是还原氯代硝基苯,其中铁粉还原法和硫化碱还原法环境污染十分严重。催化加氢法污染小、产品质量高,但因脱卤较为严重而造成设备腐蚀和产品纯度下降,因此如何抑制氯代硝基苯催化加氢中的脱氯问题,是现在研究的重点和难点。目前主要有两种方法:一是向反应体系中加入助剂来抑制脱卤,但助剂会污染产品,分离困难;二是改善催化剂的性能,以达到抑制脱卤的目的。例如专利cn103349983a提供一种卤代硝基苯催化加氢制卤代苯胺用催化剂及应用,该催化剂由活性炭载体,和附着于活性炭载体上的活性组分0.1wt%~5wt%铂组成。该催化剂载体经过无机酸回流处理1~3小时,再用碳酸盐溶液浸泡,然后按现有方法制备催化剂,该催化剂能较好的抑制脱卤,但载体预处理工艺复杂,影响生产成本。专利cn1199935提供一种卤代硝基苯催化加氢合成卤代苯胺的生产方法,该方法以炭纳米管为载体,pt、pd为活性组分制备催化剂。该催化剂能有效抑制脱卤,但是碳纳米管生产成本较高,不利于产业化。技术实现要素:针对现有技术的不足,本发明提供了一种用于氯代硝基苯无溶剂催化加氢制备氯代苯胺反应的pt-fe/c催化剂。本发明采用比表面积为1200~2000m2/g活性炭作为载体,通过氧化处理在载体表面引入/增加含氧官能团,有利于活性组分在载体上的均匀负载。调整剂改变了载体的湿润性,使活性组分能顺利均匀地分散于载体表层,还原得到的活性纳米粒子粒径小,分布窄。铂铁双金属之间具有协同作用,既保证了硝基催化加氢应有活性,又有效抑制了脱氯,提高了选择性。本发明提供的pt-fe/c催化剂通过下述技术方案予以实现:pt-fe/c催化剂由活性组分和载体组成,所述活性组分包括pt、fe及铁的氧化物,所述载体为活性炭;其中,pt占pt-fe/c催化剂总质量的0.5~3%(例如1~2%),fe与pt的质量比为0.5~4:1(例如1~2:1)。其中,上述pt-fe/c催化剂中,所述活性组分的粒径为1~5nm。其中,上述pt-fe/c催化剂中,所述活性炭的比表面为1200~2000m2/g,例如1300~1900m2/g、1400~1800m2/g、1500~1700m2/g。本发明还提供上述pt-fe/c催化剂的制备方法,该方法包括以下步骤:(一)对活性炭进行氧化预处理,洗涤干燥后,作为载体备用;(二)将铂化合物及铁化合物溶于溶剂,加入载体调节剂,配制成活性组分浸渍液;(三)将活性组分浸渍液加入到步骤(一)所述的载体中,搅拌吸附,静置,得到载铂、铁的炭载体;(四)将还原剂加入到步骤(二)所述的溶剂中,配制成含还原剂的溶液,将其加入到步骤(三)中所述载铂、铁的炭载体中,搅拌浆化,调ph,保温反应,加入乙醇水溶液稀释,静置陈化,过滤洗涤,干燥,得到pt-fe/c催化剂。其中,上述pt-fe/c催化剂的制备方法,步骤(一)中,所述氧化预处理的操作为:使用双氧水处理活性炭0.5~2h,双氧水与活性炭的固液比(ml/g)为1:8~12,例如1:10。其中,上述pt-fe/c催化剂的制备方法,步骤(一)中,所述活性炭的比表面为1200~2000m2/g,例如1300~1900m2/g、1400~1800m2/g、1500~1700m2/g。其中,上述pt-fe/c催化剂的制备方法,步骤(二)中,所述铂化合物为氯铂酸、四氯化铂、乙酰丙酮铂、氯铂酸钾、氯铂酸钠、二亚硝基二氨铂的一种、两种或更多种。其中,上述pt-fe/c催化剂的制备方法,步骤(二)中,所述铁化合物为三氯化铁、硝酸铁、氯化亚铁、硫酸亚铁的一种、两种或更多种。其中,上述pt-fe/c催化剂的制备方法,步骤(二)中,所述载体调整剂为脂肪酸酰胺、油脂、油酸和羧酸的一种、两种或更多种;所述载体调整剂的用量为载体质量的5~50%,例如10~30%。其中,上述pt-fe/c催化剂的制备方法,步骤(二)中,所述溶剂为乙二醇、三缩四乙二醇、丁二醇、异丙醇中的一种、两种或更多种。其中,上述pt-fe/c催化剂的制备方法,步骤(三)中,所述静置的时间为3~24h,例如10~20h。其中,上述pt-fe/c催化剂的制备方法,步骤(四)中,所述还原剂为甲醛、甲醇、甲酸钠、葡萄糖、水合肼、硼氢化钠中的一种、两种或更多种;所述还原剂用量为铂质量的2~15倍,例如5~10倍。其中,上述pt-fe/c催化剂的制备方法,步骤(四)中,调ph时使用碱液,所述碱液为氢氧化钠溶液、氢氧化钾溶液、碳酸钠溶液、碳酸钾溶液中的一种、两种或更多种。其中,上述pt-fe/c催化剂的制备方法,步骤(四)中,所述ph值为8~14,例如12~13。其中,上述pt-fe/c催化剂的制备方法,步骤(四)中,所述反应的条件为:30~90℃下保温1~3h,例如60~80℃下保温1~2h。另外,本发明还提供上述pt-fe/c催化剂在氯代硝基苯加氢制备氯代苯胺中的应用。优选地,在无溶剂条件下催化氯代硝基苯液相加氢制备氯代苯胺中的应用。具体地,加氢反应在无溶剂、无助剂条件下进行,催化剂用量为反应底物质量的0.5%~3%,反应温度为50~110℃,加氢压力为0.5~1.2mpa,反应时间为20~120min。本发明与现有技术相比,具有以下有益效果:本申请催化剂制备步骤简单,活性组分粒径为1~5nm,分布窄、分散均匀;铂铁双金属之间存在协同催化效应,在保持高活性和选择性的同时,能够有效抑制脱氯副反应的发生,减少了产品分离纯化步骤,提升了产品质量。附图说明图1为实施例6制备的pt-fe/c催化剂的透射电镜图(tem图,标尺=20nm)。具体实施方式下文将结合具体实施例对本发明的技术方案做更进一步的详细说明。下列实施例仅为示例性地说明和解释本发明,而不应被解释为对本发明保护范围的限制。凡基于本发明上述内容所实现的技术均涵盖在本发明旨在保护的范围内。除非另有说明,以下实施例中使用的原料和试剂均为市售商品,或者可以通过已知方法制备。以下实施例中,所用活性炭的比表面积为1473m2/g。实施例1一、10wt%双氧水处理活性炭1h,固液比(g/ml)为1:10,洗涤干燥后作为载体备用;二、将含0.1g铂的氯铂酸及0.96g六水合氯化铁溶于16ml乙二醇溶剂,加入载体调整剂1.0g油酸,搅拌30min,配置成活性组分浸渍液;三、将活性组分浸渍液加入到9.7g双氧水处理过的活性炭中,搅拌吸附,静置16h,得到载铂、铁的炭载体;四、将0.5g甲醛溶液加入到80ml乙二醇溶剂中,搅拌均匀后加入到步骤(三)中载铂、铁的载体中,搅拌分散30min,滴入10wt%naoh溶液调体系ph=12~13,升温至80℃,保温1.5h,加入体积比为1:1的乙醇水溶液80ml稀释,静置陈化12h,过滤洗涤,干燥,得到1%pt-2%fe/c催化剂。实施例2一、10wt%双氧水处理活性炭1h,固液比为1:10,洗涤干燥后备用;二、将含0.2g铂的氯铂酸及1.94g六水合氯化铁溶于32ml乙二醇,加入2.0g油酸,搅拌30min,配置成活性组分浸渍液;三、将活性组分浸渍液加入到19.4g氧化处理过的活性炭中,搅拌吸附,静置16h,得到载铂、铁的炭载体;四、将0.8g甲酸钠溶于150ml乙二醇中,搅拌均匀后加入到步骤(三)中载铂、铁的载体中,搅拌分散30min,滴入10wt%naoh溶液调体系ph=12~13,升温至80℃,保温1.5h,加入体积比为1:1的乙醇水溶液150ml稀释,静置陈化,过滤洗涤,干燥,得到1%pt-2%fe/c催化剂。实施例3同实施例1,不同的是六水合氯化铁的量为0.49g,得到的催化剂为1%pt-1%fe/c催化剂。实施例4同实施例1,不同的是铁化合物为九水合硝酸,得到的催化剂为1%pt-2%fe/c催化剂。实施例5同实施例1,不同的是载体调剂为脂肪酰胺,得到的催化剂为1%pt-2%fe/c催化剂。实施例6同实施例1,不同的是溶剂为三缩四乙二醇,还原剂为0.1g硼氢化钠,得到的催化剂为1%pt-2%fe/c催化剂。图1为本实施例制备得到的催化剂的tem图,可以看出其活性组分的粒径集中分布在1~5nm之间,粒径分布窄且分散均匀。对比例1同实施例1,不同的是省略步骤(一),活性炭载体不经过双氧水处理。对比例2一、10wt%双氧水处理活性炭1h,固液比(g/ml)为1:10,洗涤干燥后作为载体备用;二、将含0.1g铂的氯铂酸溶于16ml乙二醇溶剂,加入载体调整剂1.0g油酸,搅拌30min,配置成活性组分浸渍液;三、将活性组分浸渍液加入到9.9g双氧水处理过的活性炭中,搅拌吸附,静置16h,得到载铂的炭载体;四、将0.5g甲醛溶液加入到80ml乙二醇溶剂中,搅拌均匀后加入到步骤(三)中载铂的载体中,搅拌分散30min,滴入10wt%naoh溶液调体系ph=12~13,升温至80℃,保温1.5h,加入体积比为1:1的乙醇水溶液80ml稀释,静置陈化12h,过滤洗涤,干燥,得到1%pt/c催化剂。对比例3同实施例1,不同的是fe/pt质量比为1:8,得到1%pt-8%fe/c催化剂。测试例1将实施例1~6中的pt/c催化剂用于催化邻氯硝基苯加氢制备邻氯苯胺的反应中。反应在500ml高压釜中进行。向釜中投入100g邻氯硝基苯、0.8g催化剂pt-fe/c、封闭高压釜。氮气置换3次,开搅拌升温,转速800r/min。当釜温达到80℃时,通氢气充压至0.9~1.1mpa,计时反应,保持釜温80℃,每10min测试吸氢速率。当不吸氢时停止反应,将高压釜骤冷至50℃以下,卸压开釜,将反应液离心分离后取样,气相色谱分析各产物含量。结果如下表1所示。表1.催化剂样品反应时间转化率选择性脱氯率实施例1102min100%99.9%0.07%实施例2110min100%99.9%0.08%实施例392min100%99.8%0.09%实施例4109min100%99.9%0.09%实施例5103min100%99.9%0.08%实施例699min100%99.9%0.06%对比例1114min100%99.8%0.14%对比例296min100%94.8%4.23%对比例3120min66.37%99.9%0.09%以上,对本发明的实施方式进行了说明。但是,本发明不限定于上述实施方式。凡在本发明的精神和原则之内,所做的任何修改、等同替换、改进等,均应包含在本发明的保护范围之内。当前第1页12