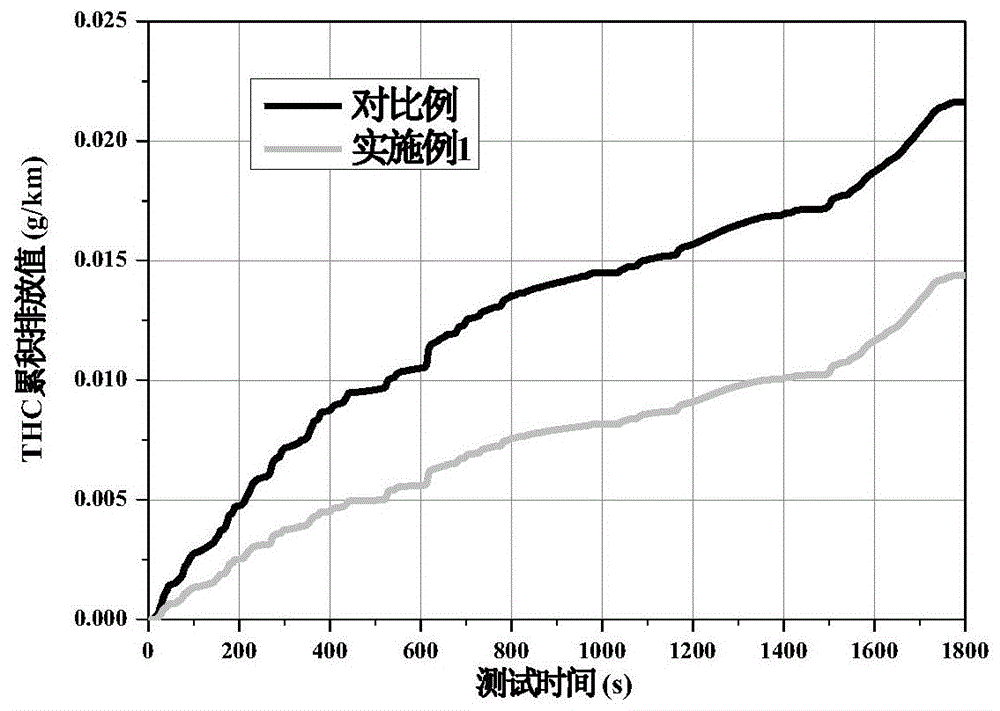
本发明涉及一种具有低温吸附能力的柴油车氧化型催化剂及其制备方法,本发明属于催化剂制备
技术领域:
。
背景技术:
:柴油发动机被广泛应用于重型汽车、非道路机械、船舶、国防装备等领域,但其对大气环境的污染不能被忽视。柴油车排放的污染物中主要有一氧化碳(co)、碳氢(hc)、氮氧化物(nox)以及颗粒物(pm),颗粒物主要有干碳、可溶性有机物(sof)和少量的硫酸及硫酸盐组成。柴油车尾气中的hc(包括各种链状烃和芳香烃)和co是由于燃油不完全燃烧产生的,且在不同工况下尾气中各污染物组分含量有所变化。柴油机通常传统燃烧方式下尾气中hc和co浓度较低,但是在新型的燃烧方式,如预混合压缩点火,可同时减少nox和pm的产生下,会产生相当数量的hc和co,其中冷启动阶段的hc和co排放量占比最大。柴油机氧化催化剂(doc)是最早得到应用的柴油机尾气后处理技术,其主要用于消除尾气中的hc、co和pm中的sof,通常在250℃以上的环境下催化消除效果较好。一方面,柴油车(特别是轻型柴油车)绝大部分行驶工况的排气温度低于250℃,这就直接导致了doc对hc/co的转化率不足。另一方面,通过提高doc中贵金属用量能够一定程度上提升涂层的低温起燃活性,但是冷启动阶段排放的大量hc/co无法得到有效处理。近年来,分子筛被普遍用作doc的涂层材料,其主要作用就是用于吸附冷启动阶段(低温段)排放的大量hc/co。然而,如何高效利用分子筛的低温吸附能力、优化催化剂涂层配方中的分子筛的添加工艺一直是doc催化剂涂层开发及应用的研究难点。技术实现要素:本发明的目的之一是克服现有技术中存在的不足,提供一种起燃温度低、热稳定性好的柴油车氧化型催化剂。本发明的另一目的是提供一种具有低温吸附能力的柴油车氧化型催化剂的制备方法。按照本发明提供的技术方案,所述具有低温吸附能力的柴油车氧化型催化剂,在载体上涂覆有活性层涂层,在活性层涂层上涂覆有吸附层涂层;活性层涂层包括氧化铈和镧-铝复合氧化物,活性层的涂覆量为70~160克/升;活性层中负载有贵金属pt和pd,贵金属的涂覆量为1.0~4.5克/升;吸附层涂层为分子筛,吸附层涂层的涂覆量为10~50克/升。作为优选,所述贵金属pt与贵金属pd的质量比为1:(0.1~10)。作为优选,所述活性层中氧化铈与镧-铝复合氧化物的质量比为1:(3~9)。作为优选,所述镧-铝复合氧化物中氧化镧与氧化铝的质量比为1:(19~99)。作为优选,所述分子筛为β型分子筛、cha型分子筛或者mfi型分子筛。作为优选,所述载体为堇青石陶瓷蜂窝或铁铬铝金属蜂窝,所述载体的孔密度为200~600目/平方英尺。一种具有低温吸附能力的柴油车氧化型催化剂的制备方法包括如下步骤:(1)等体积浸渍法制备镧-铝复合氧化物:按氧化镧与氧化铝的质量比为1:19~99分别称取硝酸镧和氧化铝,按氧化铝的饱和吸附量配制硝酸镧水溶液,将所配制的硝酸镧水溶液滴加至氧化铝中并持续搅拌2~8小时,然后静置、陈化6~15小时后在100~170℃条件下烘干,并于700~850℃焙烧后得到镧-铝复合氧化物;(2)活性层涂层浆液的制备:按氧化铈与镧-铝复合氧化物的质量比为1:3~9将氧化铈与镧-铝复合氧化物分别加入至去离子水中搅拌形成浆液,氧化铈与镧-铝复合氧化物的总质量与去离子水的质量比为2:3~8,然后采用球磨工艺处理浆液,控制颗粒d90为5~35μm;持续搅拌过程中,根据载体上贵金属的涂覆量为1.0~4.5克/升计算贵金属的需要量,将贵金属pt和pd前驱体溶液加入到上述浆液中,搅拌均匀,形成活性层最终浆液;(3)吸附层涂层浆液的制备:将分子筛加入至去离子水中搅拌形成浆液,其中分子筛与去离子水的质量比为1:3~6,然后采用球磨工艺处理浆液,控制颗粒d90为6~25μm,制得吸附层涂层浆液;(4)活性层浆液涂覆:将载体堇青石陶瓷蜂窝或铁铬铝金属蜂窝浸泡在活性层最终浆液中,浸泡0.5~5min后取出,采用压缩空气将载体内部的通道吹通,吹扫时间为0.5~3min,然后将载体在100~150℃条件下干燥3~8小时,最后将载体在350~550℃条件下焙烧1~3小时后冷却至室温,即得到半成品催化剂;(5)吸附层浆液涂覆:将步骤(4)制备得到的半成品催化剂浸泡在吸附层浆液中,浸泡0.5~5min后取出,采用压缩空气将载体内部的通道吹通,吹扫时间为0.5~3min,然后将载体在100~150℃条件下干燥3~8小时,最后将载体在350~550℃条件下焙烧1~3小时,即得到柴油车氧化型催化剂。本发明将活性层、吸附层在载体上进行分层涂覆,有效避免了分子筛与贵金属浆液的直接接触,确保了分子筛的结构稳定性,进而提升了分子筛的低温吸附能力。另外,本发明通过等体积浸渍法制备得到了镧-铝复合氧化物,将其作为活性层涂层基底,能够有效提升氧化铝的热稳定性、增强涂层对贵金属pt/pd的锚定作用。同时在活性层涂层配方中添加一定比例的氧化铈,显著提高了涂层的低温co起燃活性。本发明制备方法简单、适用于工业化生产,且制备得到的柴油车氧化型催化剂起燃温度低、热稳定性好。附图说明图1是本发明实施例1与对比例的thc累积排放曲线图。图2是本发明实施例1与对比例的co累积排放曲线图。具体实施方式下面结合具体实施例对本发明作进一步说明。下面将结合具体实施例对本发明作进一步的说明。实施例1一种具有低温吸附能力的柴油车氧化型催化剂,催化剂载体为堇青石蜂窝陶瓷,体积为1.678升,孔密度为400目/平方英尺;活性涂层中含有氧化铈和镧-铝复合氧化物,涂层涂覆量为100克/升,吸附层为h型β分子筛,涂覆量为20克/升;活性层中负载的贵金属的涂覆量为2.5克/升,其中贵金属pt与贵金属pd的质量比为3:2。制备方法包括如下步骤:(1)等体积浸渍法制备镧-铝复合氧化物:镧-铝复合氧化物采用等体积浸渍法制备。称取质量为990克的活性氧化铝粉体,称取质量为26.6克六水合硝酸镧溶解,配制成所用活性氧化铝饱和吸附量的水溶液,再将硝酸镧水溶液滴加至氧化铝粉体中并持续搅拌3小时;然后静置、陈化8小时,之后在110℃烘干14小时,在500℃焙烧3小时后得到镧-铝复合氧化物,制备得到的镧-铝复合氧化物中,氧化镧与氧化铝的质量比为1:49。(2)活性层浆液的制备:称取去离子水1400克,加入镧-铝复合氧化物800克,氧化铈200克,搅拌均匀形成涂层浆液,然后采用球磨工艺处理浆液,控制浆液颗粒度d90为20微米;持续搅拌过程中,将含15克纯pt的硝酸铂溶液、10克纯pd的硝酸钯溶液混合后滴加至涂层浆液中,搅拌均匀4h,形成活性层最终浆液。(3)吸附层涂层浆液的制备:称取300克的β分子筛加入至1200克的去离子水中搅拌形成浆液,然后采用球磨工艺处理浆液,控制颗粒d90为15微米,制得吸附层涂层浆液。(4)活性层浆液涂覆:将载体堇青石陶瓷蜂窝或铁铬铝金属蜂窝浸泡在活性层最终浆液中,浸泡0.5~5分钟后取出,采用压缩空气将载体内部的通道吹通,吹扫时间为0.5~3分钟,然后将载体在100~150℃条件下干燥3~8小时,最后将载体在350~550℃条件下焙烧1~3小时后冷却至室温,即得到半成品催化剂。(5)吸附层浆液涂覆:将步骤(4)制备得到的半成品催化剂浸泡在吸附层浆液中,浸泡0.5~5分钟后取出,采用压缩空气将载体内部的通道吹通,吹扫时间为0.5~3分钟,然后将载体在100~150℃条件下干燥3~8小时,最后将载体在350~550℃条件下焙烧1~3小时,即得到成品催化剂。实施例2:具体制备方法与实例1基本相同,不同之处在于,所用镧-铝复合氧化物中,氧化镧与氧化铝的质量比为1:99。实施例3:具体制备方法与实例1基本相同,不同之处在于,所用镧-铝复合氧化物中,氧化镧与氧化铝的质量比为1:19。实施例4:具体制备方法与实例1基本相同,不同之处在于,所述活性层中氧化铈与镧-铝复合氧化物的质量比为1:9。实施例5:具体制备方法与实例1基本相同,不同之处在于,所述活性层中氧化铈与镧-铝复合氧化物的质量比为1:3。实施例6:具体制备方法与实例1基本相同,不同之处在于,所述吸附层中h型β分子筛的涂覆量为50克/升。实施例7具体制备方法与实例1基本相同,不同之处在于,所述吸附层中h型β分子筛的涂覆量为10克/升。实施例8具体制备方法与实例1基本相同,不同之处在于,所述活性层的涂覆量为70克/升、贵金属的涂覆量为1.0克/升、吸附层涂层的涂覆量为10克/升。实施例9具体制备方法与实例1基本相同,不同之处在于,所述活性层的涂覆量为160克/升、贵金属的涂覆量为4.5克/升、吸附层涂层的涂覆量为50克/升。对比例对比例与实施例1相比,对比例的制备方法中不区分活性层及吸附层,β分子筛加入至活性层浆液中,共同球磨得到涂层浆液后进行贵金属的添加以及催化剂的涂覆。一种具有低温吸附能力的柴油车氧化型催化剂,催化剂载体为堇青石蜂窝陶瓷,体积为1.678升,孔密度为400目/平方英尺;涂层中含有氧化铈、镧-铝复合氧化物和h型β分子筛,涂层涂覆量为120克/升;贵金属的涂覆量为2.5克/升,其中贵金属pt与贵金属pd的质量比为3:2。制备方法包括如下步骤:(1)等体积浸渍法制备镧-铝复合氧化物:镧-铝复合氧化物采用等体积浸渍法制备。称取质量为990克的活性氧化铝粉体,称取质量为26.6克六水合硝酸镧溶解,配制成所用活性氧化铝饱和吸附量的水溶液,再将硝酸镧水溶液滴加至氧化铝粉体中并持续搅拌3小时;然后静置、陈化8小时,之后在110℃烘干14小时,在500℃焙烧3小时后得到镧-铝复合氧化物,制备得到的镧-铝复合氧化物中,氧化镧与氧化铝的质量比为1:49。(2)涂层浆液的制备:称取去离子水1600克,加入镧-铝复合氧化物800克、氧化铈200克和β分子筛200克,搅拌均匀形成涂层浆液,然后采用球磨工艺处理浆液,控制浆液颗粒度d90为20微米;持续搅拌过程中,将含15克纯pt的硝酸铂溶液、10克纯pd的硝酸钯溶液混合后滴加至涂层浆液中,搅拌均匀4h,形成活性层最终浆液。(3)涂层浆液涂覆:将载体堇青石陶瓷蜂窝或铁铬铝金属蜂窝浸泡在活性层最终浆液中,浸泡0.5~5分钟后取出,采用压缩空气将载体内部的通道吹通,吹扫时间为0.5~3分钟,然后将载体在100~150℃条件下干燥3~8小时,最后将载体在350~550℃条件下焙烧1~3小时后冷却至室温,即得到成品催化剂。催化剂进行性能评价将制备得到的催化剂样品进行实验室模拟配气评价,配气成分表如表1所示。在样品评价过程中,由温控仪控制电炉程序升温,由hc分析仪、co分析仪和so2分析仪测量反应前后气体各组分的浓度,得到不同温度下样品的转化率,并由此得到样品的t50(转化率为50%时催化剂入口的温度)。hc和co的t50温度越低,表明催化剂的起燃性能越好,对实施例1-7制备的催化剂以及对比例制备的催化剂性能评价结果见表2。表1气体含量气体含量hc(c3h6)800ppmo210%no300ppmso250ppmco1000ppmh2o10%co26%n2余氮表2样品hct50(℃)cot50(℃)1140101214210831451054139110514898613710671431078168121912992对比例142104由表2可知,采用本发明中的制备方法得到的柴油车氧化型催化剂的hc和co的t50温度较低,低温起燃性能优异。其中,实施例1制备得到的催化剂的hc和co的t50略低于对比例制备得到的催化剂,但性能差距不大。因此,为了进一步考察本发明催化剂的低温吸附性能,进一步对实施例1和对比例制备得到的催化剂封装后进行了整车wltc排放测试(gb18352.6-2016,ⅰ型试验)。因为wltc测试循环前598s为低速段,即车辆冷启动、低排气温度阶段,所以低速段的气体污染物排放值能够直接反映出催化剂低温吸附/起燃性能。图1和图2分别为所制备催化剂wltc测试循环的thc和co累积排放曲线图,如图所示,实施例1前598s的thc及co累计排放明显低于对比例(特别是前200s的冷启动阶段),而上述两样品的hc/co起燃t50无显著差别,这就表明本发明制备的催化剂具备更加突出的低温吸附性能。当前第1页12