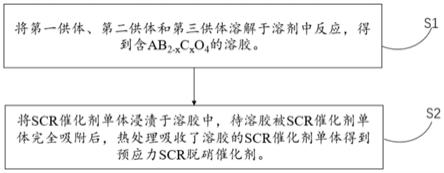
一种预应力scr脱硝催化剂及其制备方法
技术领域
1.本发明涉及大气污染物减排技术领域,尤其涉及一种scr脱硝催化剂及其制备方法。
背景技术:2.目前,scr脱硝催化剂产品的应用环境多是含有高含量粉尘、微量重金属、so2等复杂工业烟气,当烟气通过催化剂的气流通道时,在高空速的条件下会引起催化剂磨损,催化剂一经磨损则不可逆转,催化剂磨损是降低scr催化剂脱硝效率和寿命的重要因素。
3.为降低scr催化剂的磨损,现有技术常采用具有硬化组分的盐溶液对催化剂端头进行硬化处理;或将耐磨原料,如sic加入到催化剂基体中。但第一种方法因硬化组分负载量较少且部分硬化液没有活性导致磨损率高、磨损寿命短和脱硝效率减小,而且仅仅端面的硬化还不能完全解决催化剂磨损的问题;第二种方法在使用过程中催化剂普通组分与耐磨组分因相变产生的体积变化不同会局部产生应力集中从而导致催化剂的碎裂。
4.因此,如何增强scr催化剂,提高scr催化剂成品率,减缓scr催化剂磨损问题,是亟待解决的问题。
技术实现要素:5.为了解决上述技术问题,本发明提供了一种预应力scr脱硝催化剂及其制备方法。
6.根据本申请的一个方面,提供了一种预应力scr脱硝催化剂,包括:scr催化剂单体以及表面强化层材料,表面强化层材料负载在scr催化剂单体表面;表面强化层材料的结构式为ab2‑
x
c
x
o4,x为0.5~1.6;其中,a、b、c为互不相同的金属组分。
7.可选择地,a和b选自mn、co、cu、fe、mo、ni和ba中任意不同的两种;
8.c选自cu、ce、la、ga、sn和lu中任意一种;
9.且a、b、c为互不相同的金属组分。
10.可选择地,表面强化层材料由第一供体、第二供体和第三供体反应得到;
11.第一供体为含a的可溶性盐;
12.第二供体为含b的可溶性盐;
13.第三供体为含c的可溶性盐。
14.可选择地,表面强化层材料由第一供体、第二供体和第三供体反应得到;
15.第一供体为含a的可溶性盐;第二供体为含b的可溶性盐;第三供体为含c的可溶性盐;
16.第一供体选自硝酸锰、硝酸钴、硝酸铜、硝酸铁、柠檬酸铁、正钼酸铵、仲钼酸铵、硝酸镍、醋酸镍、硝酸钡中的一种或多种;
17.第二供体选自硝酸锰、硝酸钴、醋酸铜、硝酸铜、硝酸铁、柠檬酸铁、正钼酸铵、仲钼酸铵、硝酸镍、醋酸镍、硝酸钡中的一种或多种;
18.第三供体选自醋酸铜、硝酸铜、硝酸铈、醋酸铈、硝酸镧、乙酸镧、醋酸镓、乙酸锡、
硝酸镥中的一种或多种。
19.可选择地,以质量分数计,金属组分a的含量为scr催化剂单体的0.5~3wt%;金属组分b的含量为scr催化剂单体的0.5~3wt%;金属组分c的含量为scr催化剂单体的2~5wt%。
20.可选择地,表面强化层材料的厚度h为:
21.其中,h为表面强化层材料的厚度;h为scr催化剂单体的厚度;a
m
为scr催化剂单体的横截面积;a
s
为表面强化层材料的横截面积。
22.根据本申请的另一个方面,提供了一种预应力scr脱硝催化剂的制备方法,包括以下步骤:
23.s1将第一供体、第二供体和第三供体溶解于溶剂中反应,得到ab2‑
x
c
x
o4前驱体溶液;
24.s2将scr催化剂单体浸渍于前驱体溶液中,待前驱体溶液被scr催化剂单体吸附后,热处理吸收了前驱体溶液的scr催化剂单体得到预应力scr脱硝催化剂。
25.可选择地,步骤s1的具体操作为:
26.将第一供体、第二供体、第三供体按照预定比例溶解到去离子水或无水乙醇中配制成混合溶液;将混合溶液置于30~50℃温度条件下,恒温油浴搅拌2~48小时,得到前驱体溶液;
27.第一供体为含a的可溶性盐;第二供体为含b的可溶性盐;第三供体为含c的可溶性盐;
28.a和b选自mn、co、cu、fe、mo、ni和ba中任意不同的两种;
29.c选自cu、ce、la、ga、sn和lu中任意一种;
30.且a、b、c为互不相同的金属组分。
31.可选择地,步骤s1中的具体操作为:
32.将第一供体、第二供体、第三供体溶解到去离子水或无水乙醇中配制成复合溶液;复合溶液中第一供体的浓度为0.5~5mol/l,第二供体的浓度为0.5~5mol/l,第三供体的浓度为2~5mol/l;
33.将混合溶液置于30~50℃温度条件下,恒温油浴搅拌2~48小时,得到前驱体溶液;
34.第一供体为含a的可溶性盐;第二供体为含b的可溶性盐;第三供体为含c的可溶性盐;且a、b、c为互不相同的金属组分;
35.其中,第一供体选自硝酸锰、硝酸钴、硝酸铜、硝酸铁、柠檬酸铁、正钼酸铵、仲钼酸铵、硝酸镍、醋酸镍、硝酸钡中的一种或多种;
36.第二供体选自硝酸锰、硝酸钴、醋酸铜、硝酸铜、硝酸铁、柠檬酸铁、正钼酸铵、仲钼酸铵、硝酸镍、醋酸镍、硝酸钡中的一种或多种;
37.第三供体选自醋酸铜、硝酸铜、硝酸铈、醋酸铈、硝酸镧、乙酸镧、醋酸镓、乙酸锡、硝酸镥中的一种或多种。
38.可选择地,步骤s2的具体操作为:
39.将scr催化剂单体浸渍于前驱体溶液中,待前驱体溶液被scr催化剂单体吸附后,
热处理吸附了前驱体溶液的scr催化剂单体,使表面强化层材料负载在scr催化剂单体表面,表面强化层材料的厚度h=a
m
/a
s
,得到预应力scr脱硝催化剂
40.本申请的预应力scr脱硝催化剂在scr催化剂单体形成表面强化层材料,大幅提高scr脱硝催化剂的耐磨性能和弯曲强度,进而提高其工程应用寿命。
附图说明
41.构成本发明的一部分的附图用来提供对本发明的进一步理解,本发明的示意性实施例及其说明用于解释本发明,并不构成对本发明的不当限定。在附图中:
42.图1是一示例中预应力scr脱硝催化剂的制备方法的流程图。
具体实施方式
43.为使本发明实施例的目的、技术方案和优点更加清楚,下面将结合本发明实施例中的附图,对本发明实施例中的技术方案进行清楚、完整地描述,显然,所描述的实施例是本发明一部分实施例,而不是全部的实施例。基于本发明中的实施例,本领域普通技术人员在没有做出创造性劳动前提下所获得的所有其他实施例,都属于本发明保护的范围。需要说明的是,在不冲突的情况下,本申请中的实施例及实施例中的特征向量可以相互任意组合。
44.目前,scr脱硝催化剂产品的应用环境多是含有高含量粉尘、微量重金属、so2等复杂工业烟气,当烟气通过催化剂的气流通道时,在高空速的条件下会引起催化剂磨损,催化剂一经磨损则不可逆转,催化剂磨损是降低scr催化剂脱硝效率和寿命的重要因素。
45.为降低scr催化剂的磨损,现有技术常采用具有硬化组分的盐溶液对催化剂端头进行硬化处理;或将耐磨原料,如sic加入到催化剂基体中。但第一种方法因硬化组分负载量较少且部分硬化液没有活性导致磨损率高、磨损寿命短和脱硝效率减小,而且仅仅端面的硬化还不能完全解决催化剂磨损的问题;第二种方法在使用过程中催化剂普通组分与耐磨组分因相变产生的体积变化不同会局部产生应力集中从而导致催化剂的碎裂。
46.本申请提供了一种预应力scr脱硝催化剂,包括:scr催化剂单体以及表面强化层材料,表面强化层材料负载在scr催化剂单体表面;表面强化层材料的结构式为ab2‑
x
c
x
o4,x为0.5~1.6。其中,a、b、c为互不相同的金属组分,例如,表面强化层材料femn
1.5
ce
0.5
o4,feco
1.2
la
0.8
o4,nico
0.4
sn
1.6
o4等。
47.本申请的预应力scr脱硝催化剂在scr脱硝催化剂表面形成表面强化层材料,大幅提高scr脱硝催化剂的耐磨性能和弯曲强度,进而提高其工程应用寿命。
48.作为本申请的一个优选实施方式,表面强化层材料是尖晶石型氧化物。
49.尖晶石型氧化物的热稳定性好,熔点及硬度极高,同时耐腐蚀性强,是一类重要功能材料,尖晶石型氧化物的粒径大、比表面积小、电化学活性低。本申请的scr催化剂单体表面负载尖晶石型氧化物,幅提高scr脱硝催化剂的耐磨性能和弯曲强度,进而提高其工程应用寿命。
50.本申请通过多种氧化物在scr催化剂单体上高温原位反应生成尖晶石型氧化物,scr催化剂单体本身的活性氧化物与多种氧化物相互作用,影响尖晶石型氧化物在scr催化剂单体上的纳米颗粒的生长形态、电子效应和几何效应,使得在scr催化剂单体形成的表面
强化层材料为尖晶石结构,表面强化层材料的耐磨性能和弯曲强度更好。
51.作为本申请的一个实施方式,a和b选自mn、co、cu、fe、mo、ni和ba中任意不同的两种。c选自cu、ce、la、ga、sn和lu中任意一种。且a、b、c为互不相同的金属组分。
52.其中,负载在scr催化剂单体表面的表面强化层材料可以包括一种或一种以上的结构式为ab2‑
x
c
x
o4,x为0.5~1.6的尖晶石型氧化物。
53.作为本申请的一个实施方式,表面强化层材料由第一供体、第二供体和第三供体反应得到;第一供体为含a的可溶性盐;第二供体为含b的可溶性盐;第三供体为含c的可溶性盐。
54.作为本申请的一个实施方式,表面强化层材料由第一供体、第二供体和第三供体反应得到。
55.第一供体为含a的可溶性盐;第二供体为含b的可溶性盐;第三供体为含c的可溶性盐。
56.第一供体选自硝酸锰、硝酸钴、硝酸铜、硝酸铁、柠檬酸铁、正钼酸铵、仲钼酸铵、硝酸镍、醋酸镍、硝酸钡中的一种或多种。
57.第二供体选自硝酸锰、硝酸钴、醋酸铜、硝酸铜、硝酸铁、柠檬酸铁、正钼酸铵、仲钼酸铵、硝酸镍、醋酸镍、硝酸钡中的一种或多种。
58.第三供体选自醋酸铜、硝酸铜、硝酸铈、醋酸铈、硝酸镧、乙酸镧、醋酸镓、乙酸锡、硝酸镥中的一种或多种。
59.作为本申请的一个实施方式,以质量分数计,金属组分a的含量为预应力scr脱硝催化剂的0.5~3wt%;金属组分b的含量为预应力scr脱硝催化剂的0.5~3wt%;金属组分c的含量为预应力scr脱硝催化剂的2~5wt%。
60.作为本申请的一个实施方式,表面强化层材料的厚度h为:
61.其中,h为表面强化层材料的厚度;h为scr催化剂单体的厚度;a
m
为scr催化剂单体的横截面积;a
s
为表面强化层材料的横截面积。
[0062][0063]
σ
pre
为预应力scr脱硝催化剂的预应力。
[0064]
α
m
与α
s
分别为scr催化剂单体和表面强化层材料的热膨胀系数。
[0065]
e
s
与e
m
分别为scr催化剂单体和表面强化层材料的弹性模量。
[0066]
δt
s
为预应力scr脱硝催化剂从烧结温度降到20℃的等效温差。
[0067]
本申请在scr催化剂单体表面形成的表面强化层材料的厚度与预应力scr脱硝催化剂的预应力σ
pre
成正比。
[0068]
其中,预应力scr脱硝催化剂的预应力σ
pre
应为正值,预应力scr脱硝催化剂的预应力σ
pre
应低于表面强化层自身的耐压值,预应力scr脱硝催化剂的预应力σ
pre
对应形成的拉应力,应低于scr催化剂单体的强度。优选地,预应力σ
pre
为1000~1200mpa。
[0069]
作为本申请的一个实施方式,scr催化剂单体为预定形状或预定规格的scr催化剂单体。该预定形状可以为板式、蜂窝式和波纹式等;预定规格为截面2m2、1m2等。
[0070]
例如,scr催化剂单体为蜂窝式scr催化剂单体,scr催化剂单体的孔数为9孔、16孔、18孔、20孔、25孔或30孔等。scr催化剂单体的比表面积为110m2/g以上、孔容积为0.36cm3/g以上、孔径为10.5nm以上;优选的,scr催化剂单体为16孔蜂窝式scr催化剂单体,scr催化剂单体的比表面积为120~150m2/g、孔容积为0.42~0.56cm3/g、孔径为11.5~20.5nm。
[0071]
如图1所示,本申请的预应力scr脱硝催化剂的制备方法,包括以下步骤:
[0072]
s1将第一供体、第二供体和第三供体溶解于溶剂中反应,得到含ab2‑
x
c
x
o4的前驱体溶液。
[0073]
s2将scr催化剂单体浸渍于前驱体溶液中,待前驱体溶液被scr催化剂单体吸附后,热处理吸收了前驱体溶液的scr催化剂单体得到预应力scr脱硝催化剂。
[0074]
本申请通过热处理在scr催化剂单体表面形成表面强化层材料,第一供体、第二供体和第三供体在较高的加热温度下反应,形成尖晶石型氧化物。
[0075]
作为本申请的一个实施方式,步骤s1的具体操作为:将第一供体、第二供体、第三供体按照预定比例溶解到去离子水或无水乙醇中配制成混合溶液;将混合溶液置于30~50℃温度条件下,恒温油浴搅拌2~48小时,得到前驱体溶液。
[0076]
在此实施方式中,30~50℃温度条件是第一供体、第二供体及第三供体的较快溶解与去离子水及无水乙醇较少蒸发的平衡适宜温度;恒温油浴搅拌2~48小时是第一供体、第二供体及第三供体的溶解完全及均化充分的平衡时间。
[0077]
第一供体为含a的可溶性盐;第二供体为含b的可溶性盐;第三供体为含c的可溶性盐。
[0078]
a和b选自mn、co、cu、fe、mo、ni和ba中任意不同的两种。
[0079]
c选自cu、ce、la、ga、sn和lu中任意一种。
[0080]
且a、b、c为互不相同的金属组分。
[0081]
作为本申请的一个实施方式,步骤s1中的具体操作为:
[0082]
将第一供体、第二供体、第三供体溶解到去离子水或无水乙醇中配制成复合溶液;复合溶液中第一供体的浓度为0.5~5mol/l,第二供体的浓度为0.5~5mol/l,第三供体的浓度为2~5mol/l。
[0083]
将混合溶液置于30~50℃温度条件下,恒温油浴搅拌2~48小时,得到前驱体溶液。
[0084]
第一供体为含a的可溶性盐;第二供体为含b的可溶性盐;第三供体为含c的可溶性盐;且a、b、c为互不相同的金属组分。
[0085]
其中,第一供体选自硝酸锰、硝酸钴、硝酸铜、硝酸铁、柠檬酸铁、正钼酸铵、仲钼酸铵、硝酸镍、醋酸镍、硝酸钡中的一种或多种。
[0086]
第二供体选自硝酸锰、硝酸钴、醋酸铜、硝酸铜、硝酸铁、柠檬酸铁、正钼酸铵、仲钼酸铵、硝酸镍、醋酸镍、硝酸钡中的一种或多种。
[0087]
第三供体选自醋酸铜、硝酸铜、硝酸铈、醋酸铈、硝酸镧、乙酸镧、醋酸镓、乙酸锡、硝酸镥中的一种或多种。
[0088]
作为本申请的一个实施方式,步骤s2的具体操作为:将scr催化剂单体浸渍于前驱体溶液中,待前驱体溶液被scr催化剂单体吸附后,热处理吸附了前驱体溶液的scr催化剂
单体,使表面强化层材料负载在scr催化剂单体表面,表面强化层材料的厚度h为:
[0089]
其中,h为表面强化层材料的厚度;h为scr催化剂单体的厚度;a
m
为scr催化剂单体的横截面积;a
s
为表面强化层材料的横截面积。为表面强化层材料的横截面积。
[0090]
σ
pre
为预应力scr脱硝催化剂的预应力。
[0091]
α
m
与α
s
分别为scr催化剂单体和表面强化层材料的热膨胀系数。
[0092]
e
s
与e
m
分别为scr催化剂单体和表面强化层材料的弹性模量。
[0093]
δt
s
为预应力scr脱硝催化剂从烧结温度降到20℃的等效温差。
[0094]
本申请在scr催化剂单体表面形成的表面强化层材料的厚度与预应力scr脱硝催化剂的预应力σ
pre
成正比。
[0095]
其中,预应力scr脱硝催化剂的预应力σ
pre
可预先设定,预应力scr脱硝催化剂的预应力σ
pre
的设定值应为正值,预应力scr脱硝催化剂的预应力σ
pre
应低于表面强化层自身的耐压值,预应力scr脱硝催化剂的预应力σ
pre
对应形成的拉应力,应低于scr催化剂单体的强度。优选地,预应力σ
pre
为1000~1200mpa。
[0096]
作为本申请的一个实施方式,步骤s2的具体操作为:将scr催化剂单体浸渍于前驱体溶液中,待前驱体溶液被scr催化剂单体吸收后,将吸收了前驱体溶液的scr催化剂单体在80~120℃温度中、干燥6
‑
12小时,再以600
‑
1000℃的温度煅烧干燥后的scr催化剂单体0.5
‑
6小时,得到预应力scr脱硝催化剂。
[0097]
在此实施方式中,低温干燥(80~120℃温度、干燥6
‑
12小时)是为了脱除负载前驱体的scr催化剂的多余自由水,且不影响后续高温煅烧产物的形貌和含量。高温煅烧(600
‑
1000℃的温度、煅烧0.5
‑
6小时)是为了形成表面强化层材料的结构ab2‑
x
c
x
o4,这种高温氧化处理后能够产生尖晶石结构。
[0098]
下面列出本申请预应力scr脱硝催化剂的具体实施例:
[0099]
实施例
[0100]
表1示出了本发明预应力scr脱硝催化剂的部分实施例。需要指出的是,本发明的预应力scr脱硝催化剂具体结构并不局限于表1中数据。
[0101]
表1预应力scr脱硝催化剂组分含量实施例
[0102]
[0103][0104]
其中,本申请实施例1~4中scr催化剂单体选用博霖环保科技股份有限公司,货号为bl
‑
mw
‑
1476的scr催化剂材料。
[0105]
本申请实施例1~4中scr催化剂单体选用威达蓝海环保科技有限公司,货号为wl
‑
gw
‑
5042e的scr催化剂材料。
[0106]
对比测试例
[0107]
对实施例1
‑
8的预应力scr脱硝催化剂和对比例1、对比例2的scr催化剂材料的性能进行了磨损性能测试、寿命测试、寿命测试和脱硝活性性能测试,具体测试结果如表2所示。
[0108]
磨损性能测试:将待测试催化剂置于120
±
5℃的恒温烘箱中连续干燥化,然后取出称重,分别记为mi,并自然冷却至室温后放置到催化剂磨损测试平台中测试。在测试样品仓中放置i个(依次排列为w1、w2……
w
i
)试样,调整好风速和给料量(石英粉等),经过2小时的磨损、取出并用压缩空气吹担去除试样表面的粉尘后,再将样品置于120
±
5℃的恒温烘箱中干燥化,取出并测量实验试样的重量,分别记为m1、m2……
m
i
,w此来计算试样的磨损速率和磨失量。
[0109]
寿命测试:由数据筛选模块通过调取scr脱硝活性评价装置近1年以内的scr脱硝装置运行数据,筛选运行时间最长的烟气温度和烟气流速对应区间内的数据点,并去除参数异常的数据点。再用活性计算模块计算了最常用运行工况下催化剂的活性系数均值,寿命评估模块通过脱硝装置nox进口浓度、烟气流量等运行参数和污染物排放标准计算催化剂达到寿命时的临界活性,进而根据催化剂活性衰减规律得到催化剂的剩余使用寿命。
[0110]
强度性能测试:将成型后的催化剂置于试验机平台上,进行连续加压,在压力突然下降时读取最大压力值。该仪器可以测试催化剂的轴向和径向机械强度。
[0111]
脱硝活性性能测试:将待测试催化剂置于催化剂评价装置反应器中,在模拟烟气组成为(体积比)800ppm nox,nh3流量为1ml/min,100ppm so2,6%o2,12%co2,hcl流量为40ml/min,n2为载气,空速为60000h
‑1进行测试。
[0112]
表2 scr脱硝催化剂性能测试及对比结果
[0113][0114]
其中,对比例1的scr催化剂材料产自博霖环保科技股份有限公司,货号为bl
‑
mw
‑
1476的scr催化剂材料;
[0115]
对比例2的scr催化剂材料产自威达蓝海环保科技有限公司,货号为wl
‑
gw
‑
5042e的scr催化剂材料。
[0116]
由表2性能测试数据可以看到,本发明的预应力scr脱硝催化剂较scr催化剂单体的磨损失重率降低16.7~25.0%;催化剂寿命提高15~25%;催化剂活性提高5.3~10%;强度性能也优于对比scr催化剂。
[0117]
综上,发明所涉及的预应力scr催化剂单体在scr催化剂单体形成表面强化层材料,大幅提高scr脱硝催化剂的耐磨性能和弯曲强度,进而提高其工程应用寿命。
[0118]
需要说明的是,在本文中,术语“包括”、“包含”或者其任何其他变体意在涵盖非排他性的包含,从而使得包括一系列要素的物品或者设备不仅包括那些要素,而且还包括没有明确列出的其他要素,或者是还包括为这种物品或者设备所固有的要素。在没有更多限制的情况下,由语句“包括
……”
限定的要素,并不排除在包括所述要素的物品或者设备中还存在另外的相同要素。
[0119]
以上实施例仅用以说明本发明的技术方案而非限制,仅仅参照较佳实施例对本发明进行了详细说明。本领域的普通技术人员应当理解,可以对本发明的技术方案进行修改或者等同替换,而不脱离本发明技术方案的精神和范围,均应涵盖在本发明的权利要求范围当中。