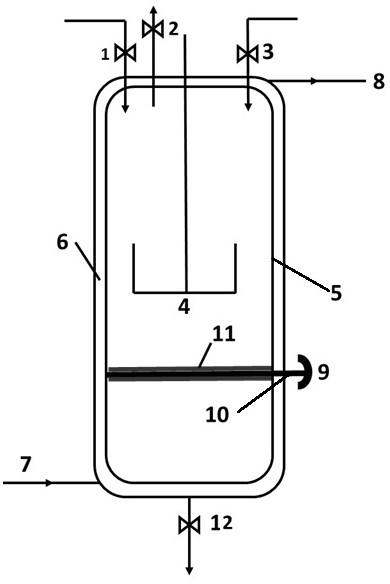
1.本发明属于酸型柴油抗磨剂制备技术领域,具体涉及一种分离饱和脂肪酸制备柴油抗磨剂的装置和方法。
背景技术:2.随着环境污染日趋严重,对柴油中硫含量等指标控制越来越严格。通过对柴油加氢精制可以降低硫含量,但同时,加氢精制工艺在去除柴油中硫的同时,其本身抗磨润滑性能也随之变差,由此引发了人们不希望看到的负面问题,主要体现在低硫柴油使发动机油泵和气缸的磨损严重,发动机的寿命大大降低,油品在短时间内出现安定性较差、油品色相恶化等许多方面的问题。为了提高低硫柴油的润滑性,添加柴油抗磨剂是改进柴油润滑性非常有效的手段。目前低硫柴油最为经济、有效的润滑改进剂为不饱和脂肪酸。
3.不饱和脂肪酸抗磨剂是低硫柴油改进润滑性的主要品种,国外主要采用妥尔油脂肪酸作为柴油抗磨剂,在我国缺少妥尔油脂肪酸的生产及提纯工艺,因此主要以棉籽油脂肪酸和大豆油脂肪酸等植物油酸为生产原料制备酸型柴油抗磨剂,但其中饱和脂肪酸含量较高不能直接作为柴油抗磨剂使用。为了去除饱和脂肪酸,传统方法是将脂肪酸直接冷冻,促使饱和脂肪酸结晶,然后将结晶压榨分离除去,或者精馏分馏的方式使其中的饱和脂肪酸含量降低到2.5%以下,以满足酸型柴油抗磨剂的使用标准q/shcg57-2014。
4.cn108085142a公开了一种不饱和脂肪酸型柴油抗磨剂的制备方法,通过高效精馏分离方法将饱和脂肪酸从脂肪酸中分离出来,但是由于脂肪酸沸点较高,相对分子量差别不大,造成分离条件苛刻,能耗高的同时对分离设备要求也较高。cn106350217a公开了一种低温冷冻的工艺方法来去除饱和脂肪酸,但需要添加0.1%-1%的聚α-烯烃用作结晶改进剂才能满足其分离使用标准。
技术实现要素:5.针对以上不足,本发明提供一种分离饱和脂肪酸制备柴油抗磨剂的装置和方法,利用本发明的装置和方法,将冷冻结晶和分离整合于一体,可以高效及快速方便地实现饱和脂肪酸的分离,并有利于节省能量,得到饱和脂肪酸含量≯2.5%的酸型柴油抗磨剂,具有较高产品收率。
6.为了实现以上技术目的,本发明采用的技术方案如下:本发明第一方面的技术目的是提供一种分离饱和脂肪酸制备柴油抗磨剂的装置,包括一个结晶釜,结晶釜上设置至少4个开口,分别作为进气口、出气口、进料口和出料口,并在相应管道上设置阀门,所述结晶釜内中下部水平安装一个可控制翻转的过滤隔板,将结晶釜分成上下两部分,所述过滤隔板的边缘与釜体壁密封,过滤隔板的板面为镂空,过滤隔板的两面分别固定铺设有滤布;所述进气口、出气口和进料口设置于结晶釜的上半部分,所述出料口设置于结晶釜的底部。
7.在上述装置中,所述过滤隔板的作用是对边缘形成密封,形成釜内上下两层空间,
并在其上铺设滤布,保证在不加压条件下液体物料不渗漏到下层空间。因此,上述过滤隔板除了与釜体边缘形成密封,还要对滤布有足够的支撑。作为具体的实施方式之一,所述过滤隔板具有如下结构:所述过滤隔板具有十字、米字或类似的多根支撑条结构的支撑架,优选为十字或米字支撑架,在支撑架上设置若干同心圆支架,以形成对滤布的支撑,所述过滤隔板的最外缘为硅胶层,以与釜体间密封。
8.进一步的,所述滤布(单层)的材质为涤纶、锦纶、维伦、丙纶或全棉等,织法为斜纹、平纹或缎纹等,耐温>100℃,重量>500g/m2,厚度>1mm,透气度为15-50l/m2·
s。
9.进一步的,所述滤布铺设1-4层,优选2-3层。
10.进一步的,所述结晶釜内上部还设置一个搅拌桨,所述搅拌桨用于搅拌进入结晶釜内被隔离在过滤隔板上部的液体。
11.进一步的,所述结晶釜的釜体外还安装有保温夹层,并设置有加热/冷却介质进口和加热/冷却介质出口。
12.本发明第二方面的技术目的是提供一种利用上述装置进行饱和脂肪酸分离以制备柴油抗磨剂的方法,包括以下步骤:(1)开启进料口和出气口,将原料加入至结晶釜中,关闭进料口,加热至原料融化,消除结晶记忆,恒温保持;(2)关闭出气口,开始降温,当体系出现浑浊时,停止降温,恒温保持;(3)保温结束后,继续降温至0℃~5℃,停止降温,恒温保持;再继续降温至-10℃~-5℃,停止降温,恒温保持;(4)开启进气口,向结晶釜内通入压缩气体,使液体透过过滤隔板上的滤布层,通过出料口收集所述抗磨剂;(5)过滤完成后,开启出气口,泄压,翻转过滤隔板180
°
,重新开启进料口,加入新的原料,加温融化原料的同时,过滤隔板上和掉落在结晶釜下部的滤渣也开始融化,通过出料口收集;如此反复进行抗磨剂的制备。
13.进一步的,步骤(1)中加热至40℃-90℃,优选55℃-75℃。
14.进一步的,步骤(1)中恒温时间为20min-90min,优选30min-60min,以让原料充分融化,消除结晶记忆。
15.进一步的,步骤(2)中降温速率为0.1℃/min-1℃/min,优选0.1℃/min-0.5℃/min;保温时间为30min-240min,优选60min-180min。
16.进一步的,步骤(3),降温到0℃-5℃的降温速率为0.1-0.5℃/min,第一次恒温保持的时间为30min-240min,优选60min-180min。继续降温到-10℃~-5℃的降温速率为0.1-0.5℃/min,第二次恒温保持的时间为60min-300min,优选180min-300min。
17.进一步的,步骤(4)中向结晶釜内通入压缩气体使加压速率为0.02mpa/min-0.1mpa/min,优选0.02mpa/min-0.04mpa/min,终压控制在0.2mpa-1.2mpa(表压),优选0.2mpa-0.8mpa,终压状态下保持2h-10h,优选4h-8h。
18.进一步的,步骤(1)、步骤(2)和步骤(3)的过程中保持搅拌。搅拌速率20-400rpm,优选50-300rpm。
19.与现有技术相比,本发明具有如下优势:本发明提供的装置和方法将冷冻结晶和分离饱和脂肪酸整合于一体,在一个装置
内完成上述步骤,通过精准的程序降温实现了饱和脂肪酸的结晶析出与分离,设备投资小,操作简单,分离效果好,适用于酸型柴油抗磨剂的制备,并且合理利用热量。
20.本发明的其它特征和优点将在随后的具体实施方式部分予以详细说明。
附图说明
21.图1.实施例1的分离饱和脂肪酸制备柴油抗磨剂的装置示意图;图2.过滤隔板的俯视结构示意图。
具体实施方式
22.下述非限制性实施例可以使本领域的普通技术人员更全面地理解本发明,但不以任何方式限制本发明。
23.实施例1本实施例公开一种分离饱和脂肪酸制备柴油抗磨剂的装置:如图1所示,其包括一个结晶釜5,结晶釜5顶部设置三个开口,并连接阀门,分别为原料进口阀1,放空阀2,压缩空气进口阀3,结晶釜5底部设置一个开口,并连接阀门,为出料阀12,所述结晶釜内中下部水平安装一个过滤隔板10,其延伸到釜体外的部分为旋转手柄9,控制其实现180
°
翻转,所述过滤隔板10将结晶釜5分成上下两部分,所述过滤隔板10的俯视结构示意图如图2所示,其具有十字支撑架,在支撑架上设置若干同心圆支架以形成对铺设在其上的滤布11的支撑,其边缘为硅胶层,与釜体壁间实现密封;结晶釜内上部设置一个搅拌桨4,用于搅拌进入结晶釜内被隔离在过滤隔板10上部的液体;结晶釜体壁上设置保温夹层6,其上设置加热/冷却介质进口7和加热/冷却介质出口8。
24.以下实施例提供了利用上述装置分离饱和脂肪酸制备柴油抗磨剂的方法,植物油酸原料及产品的组成及含量按照以下方法进行:参考gb/t 17376-2008动植物油脂、脂肪酸甲酯制备:称取抗磨剂样品100~250mg置于50ml烧瓶中,加入5ml三氟化硼甲醇溶液,然后接冷凝器,迅速向烧瓶中导入几分钟干燥氮气将空气排掉,水浴回流30min,在冷凝器顶部加入适量的异辛烷与沸腾的混合溶液中。取下冷凝器,拿出烧瓶。立即加入20ml饱和氯化钠溶液。塞住烧瓶,猛烈振摇至少15s。继续加入饱和氯化钠溶液至烧瓶颈部,静置分层。吸取1ml~2ml上层异辛烷溶液于5ml玻璃瓶中,加入适量无水硫酸钠去除溶液中痕量的水,待上气相色谱分析。同时,将软脂酸甲酯、硬脂酸甲酯、油酸甲酯、亚油酸甲酯的标样进行气相色谱分析。
25.气相色谱分析条件:agilent gc-2010 型气相色谱仪配 fid 检测器;色谱柱为hp-innowax型毛细管柱,60m
×
0.53 mm
×
1μm。进样口温度290℃;进样量5μl;分流进样,分流比20:1;柱初温180℃,保持2min,以5℃/min升温速率升温至240℃,保持6min;检测器温度300℃。
26.在定性分析确定的基础上,进行植物油酸的定量分析:采用归一法进行定量分析。
27.定量分析结果用下式计算:
在以下实施例和对比例中,使用的工业植物油酸具体成分为:软脂酸甲酯2.845%,硬脂酸甲酯4.955%,油酸甲酯28.995%,亚油酸甲酯55.287%。
28.实施例2选用的滤布为涤纶材质,平纹编制,密度615g/m2,厚度1.05mm,透气率18l/m2,在过滤隔板10的两面分别铺设1层。
29.分离饱和脂肪酸制备柴油抗磨剂的方法步骤如下:(1)开启进口阀1和放空阀2,将200g上述工业植物油酸原料加入至结晶釜5中,关闭进口阀1,开启搅拌,搅拌速率为200rpm,加热至75℃,原料融化,恒温60min;(2)关闭放空阀2,按照0.2℃/min速率降温至21℃,出现浑浊,停止降温,保温1h;(3)保温结束后,继续按照0.2℃/min速率降温至5℃,恒温1h,再继续按照0.5℃/min速率降温至-5℃,恒温4h;(4)关闭搅拌,开启压缩空气进口阀3和出料阀12,向结晶釜内通入压缩气体,按照0.02mpa/min速率加压至0.6mpa(表压),使液体透过过滤隔板10上的滤布层,保持6h,通过出料阀12收集所述抗磨剂产品143.6g;(5)过滤完成后,开启放空阀2,泄压至大气压,180
°
翻转过滤隔板10,重新开启进口阀1,加入新的原料,加温融化原料的同时,过滤隔板10上和掉落在结晶釜下部的滤渣也开始融化,通过出料阀12收集,为饱和脂肪酸;如此反复进行抗磨剂的制备。
30.经计算抗磨剂产品收率71.3%,经气相分析,饱和脂肪酸含量2.17%。
31.实施例3选用的滤布与实施例2相同,在过滤隔板10的两面分别铺设1层。
32.制备柴油抗磨剂的方法中,除了步骤(2)和(3)中降温速率改变为0.5℃/min,其他同实施例2,得到抗磨剂产品140.4g。
33.经计算产品收率70.2%,经气相分析,饱和脂肪酸含量2.23%。
34.实施例4选用的滤布为涤纶材质,平纹编制,密度510g/m2,厚度1.0mm,透气率25l/m2,在过滤隔板10的两面分别铺设1层。
35.制备柴油抗磨剂的方法中,除了步骤(2)和(3)中降温速率改变为0.5℃/min,步骤(4)中按照0.04mpa/min速率加压至1.2mpa,保持6h外,其他步骤同实施例2。得到抗磨剂产品145.4g。
36.经计算产品收率72.7%,经气相分析,饱和脂肪酸含量2.36%。
37.实施例5选用的滤布为涤纶材质,平纹编制,密度615g/m2,厚度1.05mm,透气率25l/m2,在过滤隔板10的两面分别铺设2层。
38.除步骤(3)为:保温结束后,继续按照0.2℃/min速率降温至3℃,恒温1h,再继续按照0.5℃/min速率降温至-8℃,恒温4h;其余制备柴油抗磨剂的方法步骤同实施例4,得到抗磨剂产品144.8g。
39.经计算产品收率72.4%,经气相分析,饱和脂肪酸含量2.19%。
40.对比例1滤布选型:全棉,平纹,密度420g/m2,厚度0.6mm,透气率60l/m2,在过滤隔板10的两面分别铺设1层。
41.制备柴油抗磨剂的方法步骤同实施例2,得到抗磨剂产品155.5g。
42.经计算产品收率77.8%,经气相分析,饱和脂肪酸含量2.78%。
43.对比例2选用的滤布同实施例2,在过滤隔板10的两面分别铺设1层。
44.制备柴油抗磨剂的方法中,除了步骤(2)和(3)中降温速率改变为2℃/min外,其他步骤同实施例2。得到抗磨剂产品137.8g。
45.经计算产品收率68.9%,经气相分析,饱和脂肪酸含量2.62%。
46.对比例3选用的滤布同实施例2,在过滤隔板10的两面分别铺设2层。
47.制备柴油抗磨剂的方法中,除了步骤(3)中降温至-5℃后恒温0.5h外,其他步骤同实施例2。得到抗磨剂产品158.9g。
48.经计算产品收率79.5%,经气相分析,饱和脂肪酸含量2.67%。