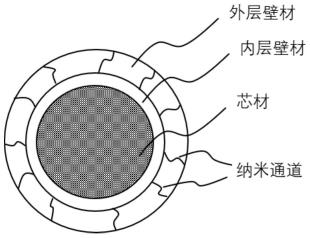
1.本技术涉及微胶囊技术领域,具体涉及微胶囊化过渡金属离子捕捉剂及制备方法、二次电池用隔膜、二次电池、电池模块、电池包和装置。
背景技术:2.近年来,随着锂离子电池的应用范围越来越广泛,锂二次电池也已广泛被用作电动车辆(ev)和混合动力电动车辆(hev)的能量存储系统和电源。由于锂离子电池取得了极大的发展,因此对其能量密度、循环性能、安全性能以及使用寿命等也提出了更高的要求。
3.在二次电池的正极活性材料中,由于制造工艺等原因,不可避免的会掺入一定量的过渡金属离子(例如fe
3+
、fe
2+
、以及cu
2+
等),电池经过长期循环后这些过渡金属离子会慢慢从正极游离出来,并迁移至负极,被还原成金属单质,从而导致电池自放电,造成电池性能快速衰减。因此,如何防止或者消除这些缓慢累计产生的过渡金属离子,一直是锂电行业的一个难点。
4.而现有的硫化物类金属离子捕捉剂的捕捉去除能力比较强,在环保和水处理行业得到广泛应用,能够将水溶液中的过渡金属离子降至ppm级以下。但是目前业内还没有将硫化物类金属离子捕捉剂用于二次电池领域的相关产品以及文献报道。
技术实现要素:5.本技术是鉴于上述课题而进行的,其目的在于,提供一种微胶囊化过渡金属离子捕捉剂及制备方法,使用该微胶囊化过渡金属离子捕捉剂的二次电池用隔膜,能够捕捉二次电池的使用过程中产生的过渡金属离子杂质,且实现微胶囊化过渡金属离子捕捉剂的缓释,减少过渡金属离子在负极析出而出现的电池自放电问题,延长二次电池的循环寿命。
6.为了达到上述目的,本技术提供了一种微胶囊化过渡金属离子捕捉剂及制备方法、二次电池用隔膜、二次电池、电池模块、电池包和装置。
7.本技术的第一方面提供了一种微胶囊化过渡金属离子捕捉剂,其特征在于,
8.所述微胶囊化过渡金属离子捕捉剂包括芯材、内层壁材以及外层壁材,其中,所述芯材为碱金属硫化物;所述内层壁材为熔点大于50℃的疏水性聚合物;所述外层壁材为聚脲类树脂。
9.由此,本技术的微胶囊化过渡金属离子捕捉剂通过内外层壁材将芯材进行二次包覆,从而实现微胶囊化过渡金属离子捕捉剂芯材与外部体系的非直接接触,另外,在将微胶囊化过渡金属离子捕捉剂制成隔膜的过程中,由于加入大量的石蜡油和戊烷,经过外层的纳米通道而将内层壁材去除,从而起到释放微胶囊化过渡金属离子捕捉剂芯材的作用。并且,随着时间的推移而析出的微胶囊化过渡金属离子捕捉剂芯材能够缓慢的通过外层壁材的纳米通道扩散到外部体系,实现金属离子捕捉剂的缓释,并且延长缓释时间,甚至达2年以上。
10.在任意实施方式中,所述碱金属硫化物包含选自硫化锂、硫化钠、以及硫化钾中的
至少一种,可选为硫化锂。
11.由此,选择含锂的硫化物作为芯材,不仅能够捕捉体系内过渡金属离子,而且能够向体系内补充锂。
12.在任意实施方式中,所述熔点大于50℃的疏水性聚合物包含选自石蜡、及聚乙烯中的至少一种,可选地,所述聚乙烯为低分子量聚乙烯蜡,所述低分子量聚乙烯蜡的重均分子量为1000~3000。
13.由此,通过选择熔点大于50℃的疏水性聚合物作为内层壁材,能够通过物理包覆等方法将作为芯材的碱金属硫化物保护起来。并且有利于通过化学包覆等方法,在对所述芯材包覆内层壁材的基础上,进一步包覆一层坚固稳定的外层壁材。
14.在任意实施方式中,所述聚脲类树脂包含选自聚脲树脂、脲-甲醛-三聚氰胺树脂、脲醛树脂以及聚脲-聚氨酯树脂中的至少一种。
15.由此,选择所述聚脲类树脂作为外层壁材,有利于外层壁材的性质稳定化,且使外层壁材具有良好的耐溶剂能力,可实现芯材的稳定缓释的效果。
16.在任意实施方式中,所述外层壁材与所述芯材和所述内层壁材之和的重量比为2.5:1~5:1。
17.由此,所述外层壁材与所述芯材和所述内层壁材之和的重量比在2.5:1~5:1的范围内,则包覆厚度适度,不会导致芯材的释放速率变得过慢或过快,因此,能够实现良好的芯材的释放,良好地应用于锂离子二次电池等环境中。
18.在任意实施方式中,所述内层壁材与所述芯材的重量比为2:1~3:1。
19.由此,所述内层壁材与所述芯材的重量比在2:1~3:1的范围内,则包覆厚度适度,不会导致芯材的释放速率变得过慢或过快,因此,能够实现良好的芯材的释放,良好地应用于锂离子二次电池等环境中。
20.在任意实施方式中,所述微胶囊化过渡金属离子捕捉剂的粒径为10μm以下,可选为5μm以下。
21.由此,通过选择微胶囊化过渡金属离子捕捉剂粒径为10μm以下,可选为5μm以下,将其制成二次电池用隔膜,能够有效避免在隔膜上可能出现的由微胶囊化过渡金属离子捕捉剂导致的毛刺和突起。
22.本技术的第二方面还提供一种微胶囊化过渡金属离子捕捉剂的制备方法,其特征在于,
23.包括以下工序:
24.工序1:在惰性气氛保护的手套箱内,将作为内层壁材的熔点大于50℃的疏水性聚合物加热熔化成液体,保持温度不变,加入碱金属硫化物作为芯材并搅拌得到混合物料,在维持内层壁材液态的条件下,将该混合物料利用高剪切乳化机进行分散破碎,形成悬浮液,然后将该悬浮液利用喷雾冷凝法制成以碱金属硫化物为芯材且以熔点大于50℃的疏水性聚合物为内层壁材的内层包覆微胶囊,将该内层包覆微胶囊清洗后,对其进行干燥、过筛;以及
25.工序2:将工序1中得到的所述内层包覆微胶囊加入作为外层壁材的聚脲类树脂中,利用原位聚合法进行二次包覆,然后,对其进行干燥、过筛,得到微胶囊化过渡金属离子捕捉剂。
26.由此,在惰性气氛保护的手套箱内操作进行工序1,能够避免空气中的湿气对芯材的影响。另外,由于内层壁材熔化成液体,即使通过高剪切乳化机进行分散破碎,也能够实现对芯材的保护并使其均匀化,从而获得粒径均一的芯材。进一步通过喷雾冷凝的方法进行造粒,能够将芯材保护在不溶于水的内层壁材(相当于内壳)内。然后通过工序2的原位聚合的方式,在外层再包覆一层坚固的聚脲类树脂作为外层壁材(相当于外壳),从而获得缓释性良好的微胶囊化过渡金属离子捕捉剂。
27.在任意实施方式中,在所述工序1中,所述内层壁材与所述芯材的投料重量比为2:1~3:1。
28.由此,若所述内层壁材与所述芯材的投料重量比不高于3:1,则能够实现芯材以适度的速率进行释放,并且后期内层壁材的去除也变得容易(在后期制膜的过程中,由于加入大量的石蜡油和戊烷,在高温条件下,内层壁材能够容易地被这两种溶剂洗出而除去),并且,若上述投料重量比不低于2:1,则能够实现完全包覆,且包覆厚度适度,有利于下一步的二次包覆(即外层壁材的包覆)。
29.在任意实施方式中,在所述工序2中,所述外层壁材与所述内层包覆微胶囊的投料重量比为5:1~10:1。
30.由此,若所述外层壁材与所述内层包覆微胶囊的投料重量比不低于5:1,则包覆厚度适度,不会导致芯材的释放速率变得过快。若上述投料重量比不高于10:1,则包覆厚度适度,不会导致芯材的释放速率变得过慢,因此,上述投料重量比在5:1~10:1的范围内,能够实现良好的芯材的释放,良好地应用于锂离子二次电池等环境中。
31.在任意实施方式中,在所述工序1中,所述惰性气氛为干燥氮气,分散破碎的时间为0.5-2h,可选为1h-1.5h,所述混合物料中的碱金属硫化物被破碎至粒径2μm以下,过筛选择粒径5μm以下的筛分;或者,
32.在所述工序2中,过筛选择粒径10μm以下的筛分,可选为粒径5μm以下的筛分。
33.本技术的第三方面提供一种二次电池用隔膜,其特征在于,
34.包含以下组成:
35.以100重量份高分子基膜树脂为基准,0.1~10重量份所述本技术第一方面的微胶囊化过渡金属离子捕捉剂、以及0.01~0.1重量份抗氧剂。
36.由此,在二次电池的使用过程中产生的过渡金属离子杂质在经过隔膜时被微胶囊化过渡金属离子捕捉剂捕捉并转化为惰性的化学物质,从而解决了由于大量过渡金属离子迁移至负极、还原沉积而电池进行自放电所导致的锂电池循环寿命快速衰减的问题。
37.在任意实施方式中,所述高分子基膜树脂包含聚烯烃或氟化聚烯烃中的至少一种。
38.由此,选择聚烯烃或氟化聚烯烃作为高分子基膜树脂,能够容易地使用湿法工艺进行加工,从而减少对微胶囊的损伤,同时能够有利于广泛适用在现有的二次电池中。
39.在任意实施方式中,所述抗氧剂包含亚磷酸酯类抗氧剂、受阻胺类抗氧剂、酚类抗氧剂、醌类抗氧剂中的至少一种。
40.由此,选择亚磷酸酯类抗氧剂、受阻胺类抗氧剂、酚类抗氧剂、醌类抗氧剂作为抗氧剂,能够有效避免由高温工艺引起的高分子基膜树脂的氧化分解和黄变,其中,可选为同时使用亚磷酸酯类抗氧剂与受阻胺类抗氧剂,即使添加量小,也能够在避免高分子基膜树
脂的氧化分解和黄变方面,获得良好的改善效果。
41.在任意实施方式中,所述微胶囊化过渡金属离子捕捉剂粒径为10μm以下,可选为5μm以下。
42.由此,选择微胶囊化过渡金属离子捕捉剂粒径为10μm以下,可选为5μm以下,能够有效避免在隔膜上可能出现的由微胶囊化过渡金属离子捕捉剂导致的毛刺和突起。
43.本技术的第四方面提供一种二次电池,包括本技术第三方面的二次电池用隔膜。
44.本技术的第五方面提供一种电池模块,包括本技术的第四方面的二次电池。
45.本技术的第六方面提供一种电池包,包括本技术的第四方面的二次电池或者本技术第四方面的电池模块。
46.本技术的第七方面提供一种用电装置,包括选自本技术的第三方面的二次电池、本技术的第四方面的电池模块或本技术的第五方面的电池包中的一种以上。
47.本技术的第八方面提供一种用途,即,所述微胶囊化过渡金属离子捕捉剂用于捕捉过渡金属离子的水处理的用途。
附图说明
48.图1为本技术一实施方式的微胶囊化过渡金属离子捕捉剂的示意图。
49.图2为分别由实施例1和对比例1中得到的二次电池用隔膜制作成二次电池的70℃胀气性能测试结果的比较曲线。
50.图3为分别由实施例1和对比例1中得到的二次电池用隔膜制作成二次电池的25℃循环性能测试结果的比较曲线。
51.图4为分别由实施例1和对比例1中得到的二次电池用隔膜制作成二次电池的45℃循环性能测试结果的比较曲线。
52.图5为本技术一实施方式的二次电池的示意图。
53.图6为图5所示的本技术一实施方式的二次电池的分解图。
54.图7为本技术一实施方式的电池模块的示意图。
55.图8为本技术一实施方式的电池包的示意图。
56.图9为图8所示的本技术一实施方式的电池包的分解图。
57.图10为本技术一实施方式的二次电池用作电源的装置的示意图。
58.附图标记说明:
59.1 电池包
60.2 上箱体
61.3 下箱体
62.4 电池模块
63.5 二次电池
64.51 壳体
65.52 电极组件
66.53 顶盖组件
具体实施方式
67.以下,适当地参照附图详细说明具体公开了本技术的微胶囊化过渡金属离子捕捉剂及制备方法、二次电池用隔膜、二次电池、电池模块、电池包和装置的实施方式。但是会有省略不必要的详细说明的情况。例如,有省略对已众所周知的事项的详细说明、实际相同结构的重复说明的情况。这是为了避免以下的说明不必要地变得冗长,便于本领域技术人员的理解。此外,附图及以下说明是为了本领域技术人员充分理解本技术而提供的,并不旨在限定权利要求书所记载的主题。
68.为了简明,本技术具体地公开了一些数值范围。然而,任意下限可以与任意上限组合形成未明确记载的范围;以及任意下限可以与其它下限组合形成未明确记载的范围,同样任意上限可以与任意其它上限组合形成未明确记载的范围。此外,每个单独公开的点或单个数值自身可以作为下限或上限与任意其它点或单个数值组合或与其它下限或上限组合形成未明确记载的范围。
69.本技术中微胶囊化是指用天然或合成的高分子材料包埋微小的固体颗粒,形成粒径为几微米至几毫米、具有半透性或密封性囊膜粒子的过程。其中,包裹在微胶囊内部的物质称为芯材,外部的囊膜称为壁材。以往的微胶囊制备方法有凝聚法、乳化法和喷雾干燥等。而本技术中作为微胶囊制备方法采用喷雾冷凝法+原位聚合法双层微胶囊化技术。
70.微胶囊化过渡金属离子捕捉剂
71.本技术的一个实施方式中,本技术提出了一种微胶囊化过渡金属离子捕捉剂,其特征在于,
72.所述微胶囊化过渡金属离子捕捉剂包括芯材、内层壁材以及外层壁材,其中,所述芯材为碱金属硫化物;所述内层壁材为熔点大于50℃的疏水性聚合物;所述外层壁材为聚脲类树脂。
73.本技术通过使用喷雾冷凝法+原位聚合法双层微胶囊化技术,对芯材进行熔点大于50℃的疏水性聚合物和聚脲类树脂的双层包覆,从而不仅能够实现过渡金属离子捕捉剂的作用,而且还能够避免芯材与外部体系(电解液)的直接接触。另外,在将微胶囊化过渡金属离子捕捉剂制成隔膜的过程中,由于加入大量的石蜡油和戊烷,经过外层的纳米通道而将内层壁材去除,从而起到释放微胶囊化过渡金属离子捕捉剂芯材的作用。并且即使随着时间的推移,微胶囊过渡金属离子捕捉剂的芯材也能够缓慢地通过外层壁材的纳米通道,扩散到外部体系,实现微胶囊过渡金属离子捕捉剂的缓释作用,从而延长缓释时间,甚至达2年以上。
74.在一些实施方式中,例如,所述碱金属硫化物包含选自硫化锂、硫化钠、以及硫化钾中的至少一种。其中,从既能够捕捉体系内过渡金属离子,又能够体系补充锂的观点出发,可以选择含锂的硫化物作为芯材。
75.在一些实施方式中,例如,所述熔点大于50℃的疏水性聚合物包含选自石蜡、及聚乙烯中的至少一种,可选地,所述聚乙烯为低分子量聚乙烯蜡,所述低分子量聚乙烯蜡的重均分子量为1000~3000。通过选择熔点大于50℃的疏水性聚合物作为内层壁材,能够通过物理方法包覆硫化锂等碱金属硫化物,将作为芯材的碱金属硫化物微粒保护起来,而且有利于通过化学包覆等方法进一步包覆一层坚固稳定的外层壁材。如不采用熔点大于50℃的疏水性聚合物的内层壁材先保护碱金属硫化物,而包覆其他化合物,则可能使作为芯材的
碱金属硫化物从内层壁材中露出,从而不可避免地与外部体系接触,若碱金属硫化物接触到水,则遇水发生反应,导致芯材丧失功能性且释放出剧毒的硫化氢气体,因此,无法得到目标的微胶囊化过渡金属离子捕捉剂。
76.在一些实施方式中,例如,所述聚脲类树脂包含选自聚脲树脂、脲-甲醛-三聚氰胺树脂、脲醛树脂以及聚脲-聚氨酯树脂中的至少一种。由于选择上述聚脲类树脂作为外层壁材,有利于外层壁材的性质稳定化,且有良好的耐溶剂能力,可实现芯材的稳定缓释的效果。
77.在一些实施方式中,所述外层壁材与所述芯材和所述内层壁材之和的重量比为2.5:1~5:1。
78.由此,所述外层壁材与所述芯材和所述内层壁材之和的重量比在2.5:1~5:1的范围内,则包覆厚度适度,不会导致芯材的释放速率变得过慢或过快,因此,能够实现良好的芯材的释放,良好地应用于锂离子二次电池等环境中。具体来说,由于外层壁材与所述芯材和所述内层壁材之和的重量比控制在上述范围内,实现外层壁材对内层壁材的完全包覆且包覆适量,微量的芯材的释放速度与正极侧微量的杂质过渡金属离子的产生速度接近,这样释放出来的碱金属硫化物迅速与杂质过渡金属离子反应掉,大大减少了二次电池中过渡金属离子(例如fe
3+
、fe
2+
、以及cu
2+
等)穿过隔膜到达负极还原成金属而产生的自放电问题。因而,使用所述微胶囊化过渡金属离子捕捉剂的二次电池具有更高的荷电保持能力及容量恢复能力、以及优异的安全性能和循环性能。
79.在一些实施方式中,所述内层壁材与所述芯材的重量比为2:1~3:1。
80.由此,所述内层壁材与所述芯材的重量比在2:1~3:1的范围内,则包覆厚度适度,有利于下一步的二次包覆(即外层壁材的包覆),且不会导致芯材的释放速率变得过慢或过快,因此,能够实现良好的芯材的释放,良好地应用于锂离子二次电池等环境中。具体来说,由于所述内层壁材与所述芯材的重量比控制在上述范围内,实现内层壁材对芯材的完全包覆且包覆适量,能够有效避免作为芯材的碱金属硫化物从内层壁材中露出,从而不可避免地与外部体系接触。这是因为若碱金属硫化物接触到水,则遇水发生反应,导致芯材丧失功能性且释放出剧毒的硫化氢气体。
81.在一些实施方式中,所述微胶囊化过渡金属离子捕捉剂的粒径为10μm以下,可选为5μm以下。
82.由此,通过选择微胶囊化过渡金属离子捕捉剂粒径为10μm以下,可选为5μm以下,将其制成二次电池用隔膜,能够有效避免在隔膜上可能出现的由微胶囊化过渡金属离子捕捉剂导致的毛刺和突起。
83.在一些实施方式中,所述微胶囊化过渡金属离子捕捉剂用于捕捉过渡金属离子的水处理的用途。
84.由此,本技术的微胶囊化过渡金属离子捕捉剂由于通过使用喷雾冷凝法+原位聚合法双层微胶囊化技术,对芯材进行熔点大于50℃的疏水性聚合物和聚脲类树脂的双层包覆,从而不仅能够实现过渡金属离子捕捉剂的作用,而且还能够避免芯材与外部体系(电解液)的直接接触。另外,在将微胶囊化过渡金属离子捕捉剂投入含有过渡金属离子的废水之前,可以采用石蜡的良溶剂(如庚烷、石油醚、二甲苯等)浸泡本技术的微胶囊化过渡金属离子捕捉剂,将石蜡内层壁材清洗除去,从而起到释放微胶囊化过渡金属离子捕捉剂芯材的
作用。并且即使随着时间的推移,微胶囊过渡金属离子捕捉剂的芯材也能够缓慢地通过外层壁材的纳米通道,扩散到外部体系,实现微胶囊过渡金属离子捕捉剂的缓释作用,从而延长缓释时间,甚至达2年以上。
85.微胶囊化过渡金属离子捕捉剂的制备方法
86.本技术的一个实施方式中,本技术还提供一种微胶囊化过渡金属离子捕捉剂的制备方法,其特征在于,
87.包括以下工序:
88.工序1:在惰性气氛保护的手套箱内,将作为内层壁材的熔点大于50℃的疏水性聚合物加热熔化成液体,保持温度不变,并加入碱金属硫化物作为芯材搅拌得到混合物料,在维持内层壁材液态的条件下,将该混合物料利用高剪切乳化机进行分散破碎,形成悬浮液,然后将该悬浮液利用喷雾冷凝法制成以碱金属硫化物为芯材且以熔点大于50℃的疏水性聚合物为内层壁材的内层包覆微胶囊,将该内层包覆微胶囊清洗后,对其进行干燥、过筛;以及
89.工序2:将工序1中得到的所述内层包覆微胶囊加入作为外层壁材的聚脲类树脂中,利用原位聚合法进行二次包覆,然后,对其进行干燥、过筛,得到微胶囊化过渡金属离子捕捉剂。
90.本技术通过使用喷雾冷凝法+原位聚合法双层微胶囊化技术将硫化物类过渡金属离子捕捉剂作为芯材包覆起来,实现过渡金属离子捕捉剂的胶囊化。
91.在惰性气氛保护的手套箱内操作进行工序1,能够避免空气中的湿气对芯材的影响。另外,由于内层壁材熔化成液体,即使通过高剪切乳化机进行分散破碎,也能够实现对芯材的保护并使其均匀化,从而获得粒径均一的芯材。进一步通过喷雾冷凝的方法进行造粒,能够将芯材保护在不溶于水的内层壁材(相当于内壳)内。然后通过工序2的原位聚合的方式,在外层再包覆一层坚固的聚脲类树脂作为外层壁材(相当于外壳),从而获得缓释性良好的微胶囊化过渡金属离子捕捉剂。
92.在一些实施方式中,例如,在所述工序1中,所述内层壁材与所述芯材的投料重量比为2:1~3:1。若所述内层壁材与所述芯材的投料重量比不高于3:1,则能够实现芯材以适度的速率进行释放,另外,若上述投料重量比不低于2:1,则能够实现包覆完全,且包覆厚度适度,有利于下一步的二次包覆(即外层壁材的包覆)。
93.在一些实施方式中,例如,在所述工序2中,所述外层壁材与所述内层包覆微胶囊的投料重量比为5:1~10:1。若所述外层壁材与所述内层包覆微胶囊的投料重量比不低于5:1,则包覆厚度适度,不会导致芯材的释放速率变得过快。若上述投料重量比不高于10:1,则包覆厚度适度,不会导致芯材的释放速率变得过慢,因此,上述投料重量比在5:1~10:1的范围内,能够实现良好的芯材的释放,良好地应用于锂离子二次电池等环境中。
94.在一些实施方式中,在所述工序1中,所述惰性气氛为干燥氮气,分散破碎的时间为0.5-2h,可选为1h-1.5h,所述混合物料中的碱金属硫化物被破碎至粒径2μm以下,过筛选择粒径5μm以下的筛分;或者,
95.在所述工序2中,过筛选择粒径10μm以下的筛分,可选为粒径5μm以下的筛分。
96.二次电池用隔膜
97.本技术的一个实施方式中,本技术还提供一种二次电池用隔膜,其特征在于,
98.包含以下组成:
99.以100重量份高分子基膜树脂为基准,0.1~10重量份所述本技术第一方面的微胶囊化过渡金属离子捕捉剂、以及0.01~0.1重量份抗氧剂。
100.由此,在二次电池隔膜中添加了本技术的微胶囊化过渡金属离子捕捉剂。由于双层微胶囊化技术将碱金属硫化物类芯材包覆起来,实现过渡金属离子捕捉剂的微胶囊化,将本技术的微胶囊化过渡金属离子捕捉剂添加到隔膜材料中加工形成二次电池用隔膜。这样实现了碱金属硫化物类芯材与外部二次电池电解液的非直接接触,而且在将微胶囊化过渡金属离子捕捉剂制成隔膜的过程中,由于加入大量的石蜡油和戊烷,经过外层的纳米通道而将内层壁材去除,从而起到释放微胶囊化过渡金属离子捕捉剂芯材的作用。随着时间的推移,碱金属硫化物类芯材能够缓慢的通过外层壁材纳米通道渗透扩散到外部电解质中,实现微胶囊过渡金属离子捕捉剂的缓释,释放出的芯材能够捕捉外部二次电池电解液中的过渡金属离子,同时含过渡金属离子的电解液也可以渗透到微胶囊内部被芯材捕捉。这种微胶囊过渡金属离子捕捉剂的有效缓释时间很长,在电池充放电经过500次循环后依然具有缓释效果,有利于例如锂离子二次电池这种过渡金属离子缓慢生成而又需要除去过渡金属离子的体系。当锂离子二次电池使用本技术的二次电池用隔膜时,即使电解液体系所含的过渡金属离子偏高,则无论本技术的微胶囊过渡金属离子捕捉剂缓慢渗透到外部电解质液体中,还是外部的电解液缓慢渗透和扩散到微胶囊过渡金属离子捕捉剂的内部,都能够实现对过渡金属离子的清除或降低。因此,本技术的二次电池用隔膜的重要用途之一就是除去或降低二次电池使用一段时间后产生的过渡金属离子,减少过渡金属离子在负极析出出现电池自放电,从而延长二次电池的循环寿命。
101.在一些实施方式中,例如,所述高分子基膜树脂包含聚烯烃或氟化聚烯烃中的至少一种。由此,选择聚烯烃或氟化聚烯烃作为高分子基膜树脂,能够容易地使用湿法工艺进行加工,从而减少对微胶囊的损伤,同时能够有利于广泛适用在现有的二次电池中。
102.在一些实施方式中,例如,所述的抗氧剂包含亚磷酸酯类抗氧剂、受阻胺类抗氧剂、酚类抗氧剂、醌类抗氧剂中的至少一种。由此,选择亚磷酸酯类抗氧剂、受阻胺类抗氧剂、酚类抗氧剂、醌类抗氧剂作为抗氧剂,能够有效避免由高温工艺引起的高分子基膜树脂的氧化分解和黄变,其中,可选为同时使用亚磷酸酯类抗氧剂与受阻胺类抗氧剂,即使添加量小,也能够在避免高分子基膜树脂的氧化分解和黄变方面,获得良好的效果。
103.在一些实施方式中,例如,所述微胶囊化过渡金属离子捕捉剂粒径为10μm以下,可选为5μm以下。由此,能够有效避免使用所述微胶囊化过渡金属离子捕捉剂的二次电池隔膜上出现由微胶囊导致的毛刺和突起。
104.另外,以下适当参照附图对本技术的二次电池、电池模块、电池包和装置进行说明。
105.本技术的一个实施方式中,提供一种二次电池。
106.通常情况下,二次电池包括正极极片、负极极片、电解液和隔膜。在电池充放电过程中,活性离子在正极极片和负极极片之间往返嵌入和脱出。电解质在正极极片和负极极片之间起到传导离子的作用。隔膜设置在正极极片和负极极片之间,主要起到防止正负极短路的作用,同时可以使离子通过。
107.[正极极片]
[0108]
正极极片包括正极集流体以及设置在正极集流体至少一个表面的正极膜层,所述正极膜层包括本技术第一方面的正极活性材料。
[0109]
作为示例,正极集流体具有在其自身厚度方向相对的两个表面,正极膜层设置在正极集流体相对的两个表面的其中任意一者或两者上。
[0110]
本技术的二次电池中,所述正极集流体可采用金属箔片或复合集流体。例如,作为金属箔片,可采用铝箔。复合集流体可包括高分子材料基层和形成于高分子材料基层至少一个表面上的金属层。复合集流体可通过将金属材料(铝、铝合金、镍、镍合金、钛、钛合金、银及银合金等)形成在高分子材料基材(如聚丙烯(pp)、聚对苯二甲酸乙二醇酯(pet)、聚对苯二甲酸丁二醇酯(pbt)、聚苯乙烯(ps)、聚乙烯(pe)等的基材)上而形成。
[0111]
正极膜层还可选地包括导电剂。但对导电剂的种类不做具体限制,本领域技术人员可以根据实际需求进行选择。作为示例,用于正极膜层的导电剂可以选自超导碳、乙炔黑、炭黑、科琴黑、碳点、碳纳米管、石墨烯及碳纳米纤维中的一种以上。
[0112]
本技术中可按照本领域已知的方法制备正极极片。作为示例,可以将本技术的正极活性材料、导电剂和粘结剂分散于溶剂(例如n-甲基吡咯烷酮(nmp))中,形成均匀的正极浆料;将正极浆料涂覆在正极集流体上,经烘干、冷压等工序后,得到正极极片。
[0113]
[负极极片]
[0114]
负极极片包括负极集流体以及设置在负极集流体至少一个表面上的负极膜层,所述负极膜层包括负极活性材料。
[0115]
作为示例,负极集流体具有在其自身厚度方向相对的两个表面,负极膜层设置在负极集流体相对的两个表面中的任意一者或两者上。
[0116]
本技术的二次电池中,所述负极集流体可采用金属箔片或复合集流体。例如,作为金属箔片,可以采用铜箔。复合集流体可包括高分子材料基层和形成于高分子材料基材至少一个表面上的金属层。复合集流体可通过将金属材料(铜、铜合金、镍、镍合金、钛、钛合金、银及银合金等)形成在高分子材料基材(如聚丙烯(pp)、聚对苯二甲酸乙二醇酯(pet)、聚对苯二甲酸丁二醇酯(pbt)、聚苯乙烯(ps)、聚乙烯(pe)等的基材)上而形成。
[0117]
本技术的二次电池中,所述负极膜层通常包含负极活性材料以及可选的粘结剂、可选的导电剂和其他可选助剂,通常是由负极浆料涂布干燥而成的。负极浆料涂通常是将负极活性材料以及可选的导电剂和粘结剂等分散于溶剂中并搅拌均匀而形成的。溶剂可以是n-甲基吡咯烷酮(nmp)或去离子水。
[0118]
作为示例,导电剂可选自超导碳、乙炔黑、炭黑、科琴黑、碳点、碳纳米管、石墨烯及碳纳米纤维中的一种以上。
[0119]
作为示例,粘结剂可选自丁苯橡胶(sbr)、聚丙烯酸(paa)、聚丙烯酸钠(paas)、聚丙烯酰胺(pam)、聚乙烯醇(pva)、海藻酸钠(sa)、聚甲基丙烯酸(pmaa)及羧甲基壳聚糖(cmcs)中的一种以上。
[0120]
其他可选助剂例如是增稠剂(如羧甲基纤维素钠(cmc-na))等。
[0121]
本技术的二次电池中,所述负极膜层除了包括负极活性材料外,还可选地包括其它常用负极活性材料,例如,作为其它常用负极活性材料,可列举出人造石墨、天然石墨、软炭、硬炭、硅基材料、锡基材料和钛酸锂等。所述硅基材料可选自单质硅、硅氧化合物、硅碳复合物、硅氮复合物以及硅合金中的一种以上。所述锡基材料可选自单质锡、锡氧化合物以
及锡合金中的一种以上。
[0122]
[电解液]
[0123]
电解液在正极极片和负极极片之间起到传导离子的作用。本技术对电解液的种类没有具体的限制,可根据需求进行选择。例如,所述电解液包括电解质盐和溶剂。
[0124]
在一些实施方式中,电解质盐可选自lipf6、libf4、liclo4、liasf6、lifsi、litfsi、litfs、lidfob、libob、lipo2f2、lidfop及litfop中的一种以上。
[0125]
在一些实施方式中,溶剂可选自碳酸亚乙酯(ec)、碳酸亚丙酯(pc)、碳酸甲乙酯(emc)、碳酸二乙酯(dec)、碳酸二甲酯(dmc)、碳酸二丙酯(dpc)、碳酸甲丙酯(mpc)、碳酸乙丙酯(epc)、碳酸亚丁酯(bc)、氟代碳酸亚乙酯(fec)、甲酸甲酯(mf)、乙酸甲酯(ma)、乙酸乙酯(ea)、乙酸丙酯(pa)、丙酸甲酯(mp)、丙酸乙酯(ep)、丙酸丙酯(pp)、丁酸甲酯(mb)、丁酸乙酯(eb)、1,4-丁内酯(gbl)、环丁砜(sf)、二甲砜(msm)、甲乙砜(ems)及二乙砜(ese)中的一种以上。
[0126]
在一些实施方式中,所述电解液中还可选地包括添加剂。例如添加剂可以包括负极成膜添加剂,也可以包括正极成膜添加剂,还可以包括能够改善电池某些性能的添加剂,例如改善电池过充性能的添加剂、改善电池高温性能的添加剂、以及改善电池低温性能的添加剂等。
[0127]
[隔膜]
[0128]
采用电解液的二次电池中,还包括隔膜。隔膜设置在正极极片和负极极片之间,起到隔离的作用。所述隔膜包括本技术第三方面提供的二次电池用隔膜。
[0129]
在一些实施方式中,隔膜的材质可选自玻璃纤维、无纺布、聚乙烯、聚丙烯及聚偏二氟乙烯中的一种以上。隔膜可以是单层薄膜,也可以是多层复合薄膜,没有特别限制。在隔膜为多层复合薄膜时,各层的材料可以相同或不同,没有特别限制。
[0130]
在一些实施方式中,正极极片、负极极片和隔膜可通过卷绕工艺或叠片工艺制成电极组件。
[0131]
在一些实施方式中,二次电池可包括外包装。该外包装可用于封装上述电极组件及电解液。
[0132]
在一些实施方式中,二次电池的外包装可以是硬壳,例如硬塑料壳、铝壳、钢壳等。二次电池的外包装也可以是软包,例如袋式软包。软包的材质可以是塑料,作为塑料,可列举出聚丙烯(pp)、聚对苯二甲酸丁二醇酯(pbt)以及聚丁二酸丁二醇酯(pbs)等。
[0133]
本技术对二次电池的形状没有特别的限制,其可以是圆柱形、方形或其他任意的形状。例如,图5是作为一个示例的方形结构的二次电池5。
[0134]
在一些实施方式中,参照图6,外包装可包括壳体51和盖板53。其中,壳体51可包括底板和连接于底板上的侧板,底板和侧板围合形成容纳腔。壳体51具有与容纳腔连通的开口,盖板53能够盖设于所述开口,以封闭所述容纳腔。正极极片、负极极片和隔膜可经卷绕工艺或叠片工艺形成电极组件52。电极组件52封装于所述容纳腔内。电解液浸润于电极组件52中。二次电池5所含电极组件52的数量可以为一个或多个,本领域技术人员可根据具体实际需求进行选择。
[0135]
在一些实施方式中,二次电池可以组装成电池模块,电池模块所含二次电池的数量可以为一个或多个,具体数量本领域技术人员可根据电池模块的应用和容量进行选择。
[0136]
图7是作为一个示例的电池模块4。参照图7,在电池模块4中,多个二次电池5可以是沿电池模块4的长度方向依次排列设置。当然,也可以按照其他任意的方式进行排布。进一步可以通过紧固件将该多个二次电池5进行固定。
[0137]
可选地,电池模块4还可以包括具有容纳空间的外壳,多个二次电池5容纳于该容纳空间。
[0138]
在一些实施方式中,上述电池模块还可以组装成电池包,电池包所含电池模块的数量本领域技术人员可以根据电池包的应用和容量进行选择。
[0139]
图8和图9是作为一个示例的电池包1。参照图8和图9,在电池包1中可以包括电池箱和设置于电池箱中的多个电池模块4。电池箱包括上箱体2和下箱体3,上箱体2能够盖设于下箱体3,并形成用于容纳电池模块4的封闭空间。多个电池模块4可以按照任意的方式排布于电池箱中。
[0140]
另外,本技术还提供一种用电装置,所述用电装置包括本技术提供的二次电池、电池模块、或电池包中的一种以上。所述二次电池、电池模块、或电池包可以用作所述装置的电源,也可以用作所述装置的能量存储单元。所述装置可以但不限于是移动设备(例如手机、笔记本电脑等)、电动车辆(例如纯电动车、混合动力电动车、插电式混合动力电动车、电动自行车、电动踏板车、电动高尔夫球车、电动卡车等)、电气列车、船舶及卫星、储能系统等。
[0141]
作为所述用电装置,可以根据其使用需求来选择二次电池、电池模块或电池包。
[0142]
图10是作为一个示例的用电装置。该装置为纯电动车、混合动力电动车、或插电式混合动力电动车等。为了满足该装置对二次电池的高功率和高能量密度的需求,可以采用电池包或电池模块。
[0143]
作为另一个示例的用电装置可以是手机、平板电脑、笔记本电脑等。该装置通常要求轻薄化,可以采用二次电池作为电源。
[0144]
实施例
[0145]
以下,说明本技术的实施例。下面描述的实施例是示例性的,仅用于解释本技术,而不能理解为对本技术的限制。实施例中未注明具体技术或条件的,按照本领域内的文献所描述的技术或条件或者按照产品说明书进行。所用试剂或仪器未注明生产厂商者,均为可以通过市购获得的常规产品。本技术实施例中各成分的含量,如果没有特别说明,均以质量计。
[0146]
实施例1:
[0147]
微胶囊化过渡金属离子捕捉剂a1的制备
[0148]
1)内层微胶囊制备:
[0149]
在干燥氮气保护的手套箱内,将40.0g石蜡加热熔化成液体,并保温维持液体状态,加入20.0g硫化锂,按照石蜡与硫化锂的重量比为2:1的方式混合,将混合物料放入高剪切乳化机分散破碎1h,将硫化锂破碎至粒径2μm以下,形成悬浮液。然后将此悬浮液采用喷雾冷凝法制成约60g以硫化锂为芯材、以石蜡为内层壁材的内层包覆微胶囊,用乙醇清洗后,干燥、过筛后待用;
[0150]
2)外层二次包覆微胶囊制备:
[0151]
取37%~40%甲醛溶液69.1g、脲24.4g置于250ml三口烧瓶,并安装冷凝回流装
置,搅拌溶解,利用氢氧化锂调节ph值至8~9,升温至70℃搅拌反应90min,形成约93.5g脲醛树脂预聚物;将全部脲醛树脂预聚物转移至2000ml三口烧瓶,加蒸馏水1350.0g、低分子量聚羧酸锂分散剂(上海鼎和化工制)4.0g搅拌均匀,加入上述制备的内层包覆微胶囊5.0g,提升搅拌转速至1500r/min,搅拌分散20min,然后升温至35℃~37℃,滴加盐酸调节ph值至1.5~2.0,维持转速和温度不变继续反应8h,之后以氢氧化锂溶液中和反应至中性,停止搅拌。倒出反应物,离心过滤-1000ml蒸馏水清洗,反复过滤-清洗6次,干燥除去水分,过筛即得到约30g双层包覆的硫化锂微胶囊作为微胶囊过渡金属离子捕捉剂a1。
[0152]
二次电池用隔膜b1的制备
[0153]
将上述双层包覆的硫化锂微胶囊(即微胶囊过渡金属离子捕捉剂)过筛,选取粒径10μm以下的筛分20g和1000g超高分子量聚乙烯gx5028(美国lyondellbasell制)在双行星动力混合机低速干混均匀;然后在所得到的混合物料中添加1000g石蜡油、1g抗氧剂cyanox2777(美国cyanamid制)并转移至实验用非啮合式双螺杆挤出机,200℃塑化挤出流延成膜,降温固液分离后,在110℃进行双向拉伸,然后使用戊烷萃取石蜡油,在115℃进行热定型扩孔,得到20μm厚度的二次电池用隔膜b1。
[0154]
实施例2:
[0155]
微胶囊化过渡金属离子捕捉剂a2的制备
[0156]
1)内层微胶囊制备:
[0157]
在干燥氮气保护的手套箱内,将40.0g石蜡加热熔化成液体,并保温维持液体状态,加入20.0g硫化钠,按照石蜡与硫化钠的重量比为2:1的方式混合,将混合物料放入高剪切乳化机分散破碎1h,将硫化钠破碎至粒径2μm以下,形成悬浮液。然后将此悬浮液采用喷雾冷凝法制成约60g以硫化钠为芯材、以石蜡为内层壁材的内层包覆微胶囊,用乙醇清洗后,干燥、过筛后待用;
[0158]
2)外层二次包覆微胶囊制备:
[0159]
取37%~40%甲醛溶液69.1g、脲24.4g置于250ml三口烧瓶,并安装冷凝回流装置,搅拌溶解,以氢氧化钠调节ph值至8~9,升温至70℃搅拌反应90min,形成脲醛树脂预聚物;将全部脲醛树脂预聚物转移至2000ml三口烧瓶,加蒸馏水1350.0g、低分子量聚羧酸钠分散剂4.0g搅拌均匀,加入上述制备的内层包覆微胶囊10.0g,提升搅拌转速至1500r/min搅拌分散20min,然后升温至35℃~37℃,滴加盐酸调节ph值至1.5~2.0,维持转速和温度不变继续反应8h,到达反应时间后以氢氧化钠溶液中和反应至中性,停止搅拌。倒出反应物,离心过滤-1000ml蒸馏水清洗,反复过滤-清洗6次,干燥除去水分,过筛即得到约35g双层包覆的硫化钠微胶囊作为微胶囊过渡金属离子捕捉剂a2。
[0160]
二次电池用隔膜b2的制备
[0161]
将上述双层包覆的硫化钠微胶囊(即微胶囊过渡金属离子捕捉剂)过筛,选取粒径10μm以下的筛分20g和400g超高分子量聚乙烯ticona gur4012(德国塞拉尼斯制)在双行星动力混合机低速干混均匀,然后在所得的混合物料中添加500g石蜡油、0.04g抗氧剂cyanox2777(美国cyanamid制)并转移至实验用非啮合式双螺杆挤出机,在200℃塑化挤出流延成膜,降温固液分离后,在110℃进行双向拉伸,然后使用戊烷萃取石蜡油,在115℃进行热定型扩孔,得到12μm厚度的二次电池用隔膜b2。
[0162]
实施例3:
[0163]
微胶囊化过渡金属离子捕捉剂a3的制备
[0164]
1)内层微胶囊制备:
[0165]
在干燥氮气保护的手套箱内,将40.0g石蜡加热熔化成液体,并保温维持液体状态,加入20.0g硫化锂,按照石蜡与硫化锂的重量比为2:1的方式混合,将混合物料放入高剪切乳化机分散破碎1h,将硫化锂破碎至2μm以下,形成悬浮液。然后将此悬浮液采用喷雾冷凝法制成以硫化锂为芯材、以石蜡为内层壁材的内层包覆微胶囊,用乙醇清洗后,干燥、过筛后待用;
[0166]
2)外层二次包覆微胶囊制备:
[0167]
取37%~40%甲醛溶液46.7g、脲16.35g、三聚氰胺16.35g置于250ml三口烧瓶,安装冷凝回流装置,搅拌溶解,以氢氧化锂调节ph值至8~9,升温至70℃搅拌反应90min,形成脲-三聚氰胺-甲醛树脂预聚物;将全部脲醛树脂预聚物转移至2000ml三口烧瓶,加蒸馏水1350.0g、低分子量聚羧酸锂分散剂4.0g搅拌均匀,加入上述制备的内层包覆微胶囊7.0g,提升搅拌转速至1500r/min搅拌分散20min,然后升温至35℃~37℃,滴加盐酸调节ph值至1.5~2.0,维持转速和温度不变继续反应8h,到达反应时间后以氢氧化锂溶液中和反应至中性,停止搅拌。倒出反应物,离心过滤-1000ml蒸馏水清洗,反复过滤-清洗6次,干燥除去水分,过筛即得约33g到双层包覆的硫化锂微胶囊作为微胶囊过渡金属离子捕捉剂a3。
[0168]
二次电池用隔膜b3的制备
[0169]
将上述双层包覆的硫化锂微胶囊(即微胶囊过渡金属离子捕捉剂)过筛,选取粒径10μm以下的筛分20g和400g超高分子量聚乙烯ticona gur4012(德国塞拉尼斯制)在双行星动力混合机低速干混均匀;然后将混合料添加200g石蜡油,0.2g抗氧剂cyanox2777(美国cyanamid制)并转移至实验用非啮合式双螺杆挤出机,200℃塑化挤出流延成膜,降温固液分离后,在110℃进行双向拉伸,然后使用戊烷萃取石蜡油,在115℃进行热定型扩孔,得到12μm厚度的二次电池用隔膜b3。
[0170]
实施例4:
[0171]
微胶囊化过渡金属离子捕捉剂a4的制备
[0172]
1)内层微胶囊制备:
[0173]
在干燥氮气保护的手套箱内,将40.0g低分子量聚乙烯蜡nv-506p(科米诺集团制)加热熔化成液体,并保温维持液体状态,加入10.0g硫化锂,按照低分子量聚乙烯蜡与硫化锂的重量比为4:1的方式混合,将混合物料放入高剪切乳化机分散破碎1h,将硫化锂破碎至2μm以下,形成悬浮液。然后将此悬浮液采用喷雾冷凝法制成约50g以硫化锂为芯材、以低分子量聚乙烯蜡为内层壁材的内层包覆微胶囊,用乙醇清洗后,干燥、过筛后待用;
[0174]
2)外层二次包覆微胶囊制备:
[0175]
取37%~40%甲醛溶液69.1g、脲24.4g置于250ml三口烧瓶,并安装冷凝回流装置,搅拌溶解,利用氢氧化锂调节ph值至8~9,升温至70℃搅拌反应90min,形成约93.5g脲醛树脂预聚物;将全部脲醛树脂预聚物转移至2000ml三口烧瓶,加蒸馏水1350.0g、低分子量聚羧酸锂分散剂4.0g搅拌均匀,加入上述制备的内层包覆微胶囊5.0g,提升搅拌转速至1500r/min,搅拌分散20min,然后升温至35℃~37℃,滴加盐酸调节ph值至1.5~2.0,维持转速和温度不变继续反应8h,之后以氢氧化锂溶液中和反应至中性,停止搅拌。倒出反应物,离心过滤-1000ml蒸馏水清洗,反复过滤-清洗6次,干燥除去水分,过筛即得到约30g双
层包覆的硫化锂微胶囊作为微胶囊过渡金属离子捕捉剂a4。
[0176]
二次电池用隔膜b4的制备
[0177]
将上述双层包覆的硫化锂微胶囊(即微胶囊过渡金属离子捕捉剂)过筛,选取粒径10μm以下的筛分20g和1000g超高分子量聚乙烯gx5028(美国lyondellbasell制)在双行星动力混合机低速干混均匀;然后在所得到的混合物料中添加1000g石蜡油、1g抗氧剂cyanox2777(美国cyanamid制)并转移至实验用非啮合式双螺杆挤出机,200℃塑化挤出流延成膜,降温固液分离后,在110℃进行双向拉伸,然后使用戊烷萃取石蜡油,在115℃进行热定型扩孔,得到20μm厚度的二次电池用隔膜b1。
[0178]
实施例5:
[0179]
微胶囊化过渡金属离子捕捉剂a5的制备
[0180]
1)内层微胶囊制备:
[0181]
在干燥氮气保护的手套箱内,将60.0g石蜡加热熔化成液体,并保温维持液体状态,加入20.0g硫化锂,按照石蜡与硫化锂的重量比为3:1的方式混合,将混合物料放入高剪切乳化机分散破碎1h,将硫化锂破碎至2μm以下,形成悬浮液。然后将此悬浮液采用喷雾冷凝法制成约80g以硫化锂为芯材、以石蜡为内层壁材的内层包覆微胶囊,用乙醇清洗后,干燥、过筛后待用;
[0182]
2)外层二次包覆微胶囊制备:
[0183]
取37%~40%甲醛溶液69.1g、脲24.4g置于250ml三口烧瓶,并安装冷凝回流装置,搅拌溶解,利用氢氧化锂调节ph值至8~9,升温至70℃搅拌反应90min,形成约93.5g脲醛树脂预聚物;将全部脲醛树脂预聚物转移至2000ml三口烧瓶,加蒸馏水1350.0g、低分子量聚羧酸锂分散剂4.0g搅拌均匀,加入上述制备的内层包覆微胶囊3.0g,提升搅拌转速至1500r/min,搅拌分散20min,然后升温至35℃~37℃,滴加盐酸调节ph值至1.5~2.0,维持转速和温度不变继续反应8h,之后以氢氧化锂溶液中和反应至中性,停止搅拌。倒出反应物,离心过滤-1000ml蒸馏水清洗,反复过滤-清洗6次,干燥除去水分,过筛即得到约28g双层包覆的硫化锂微胶囊作为微胶囊过渡金属离子捕捉剂a5。
[0184]
二次电池用隔膜b5的制备
[0185]
将上述双层包覆的硫化锂微胶囊(即微胶囊过渡金属离子捕捉剂)过筛,选取粒径10μm以下的筛分20g和1000g超高分子量聚乙烯gx5028(美国lyondellbasell制)在双行星动力混合机低速干混均匀;然后在所得到的混合物料中添加1000g石蜡油、1g抗氧剂cyanox2777(美国cyanamid制)并转移至实验用非啮合式双螺杆挤出机,200℃塑化挤出流延成膜,降温固液分离后,在110℃进行双向拉伸,然后使用戊烷萃取石蜡油,在115℃进行热定型扩孔,得到20μm厚度的二次电池用隔膜b5。
[0186]
实施例6:
[0187]
微胶囊化过渡金属离子捕捉剂a6的制备
[0188]
1)内层微胶囊制备:
[0189]
在干燥氮气保护的手套箱内,将40.0g石蜡加热熔化成液体,并保温维持液体状态,加入20.0g硫化锂,按照石蜡与硫化锂的重量比为2:1的方式混合,将混合物料放入高剪切乳化机分散破碎1h,将硫化锂破碎至2μm以下,形成悬浮液。然后将此悬浮液采用喷雾冷凝法制成约40g以硫化锂为芯材、以石蜡为内层壁材的内层包覆微胶囊,用乙醇清洗后,干
燥、过筛后待用;
[0190]
2)外层二次包覆微胶囊制备:
[0191]
取37%~40%甲醛溶液69.1g、脲24.4g置于250ml三口烧瓶,并安装冷凝回流装置,搅拌溶解,利用氢氧化锂调节ph值至8~9,升温至70℃搅拌反应90min,形成约93.5g脲醛树脂预聚物;将全部脲醛树脂预聚物转移至2000ml三口烧瓶,加蒸馏水1350.0g、低分子量聚羧酸锂分散剂4.0g搅拌均匀,加入上述制备的内层包覆微胶囊20.0g,提升搅拌转速至1500r/min,搅拌分散20min,然后升温至35℃~37℃,滴加盐酸调节ph值至1.5~2.0,维持转速和温度不变继续反应8h,之后以氢氧化锂溶液中和反应至中性,停止搅拌。倒出反应物,离心过滤-1000ml蒸馏水清洗,反复过滤-清洗6次,干燥除去水分,过筛即得到约45g双层包覆的硫化锂微胶囊作为微胶囊过渡金属离子捕捉剂a6。
[0192]
二次电池用隔膜b6的制备
[0193]
将上述双层包覆的硫化锂微胶囊(即微胶囊过渡金属离子捕捉剂)过筛,选取粒径10μm以下的筛分20g和1000g超高分子量聚乙烯gx5028(美国lyondellbasell制)在双行星动力混合机低速干混均匀;然后在所得到的混合物料中添加1000g石蜡油、1g抗氧剂cyanox2777(美国cyanamid制)并转移至实验用非啮合式双螺杆挤出机,200℃塑化挤出流延成膜,降温固液分离后,在110℃进行双向拉伸,然后使用戊烷萃取石蜡油,在115℃进行热定型扩孔,得到20μm厚度的二次电池隔膜b6。
[0194]
对比例1:
[0195]
二次电池用隔膜b7的制备:
[0196]
取1000g超高分子量聚乙烯gx5028(美国lyondellbasell制)、1000g石蜡油,1g抗氧剂cyanox2777(美国cyanamid制)并转移至实验用非啮合式双螺杆挤出机,在200℃塑化挤出流延成膜,降温固液分离后,在110℃进行双向拉伸,在使用戊烷萃取石蜡油,在115℃进行热定型扩孔,得到20μm厚度的二次电池用隔膜b7。
[0197]
对比例2:
[0198]
二次电池用隔膜b8的制备:
[0199]
将实施例1中包覆石蜡的硫化锂微胶囊(硫化锂包单层石蜡,未包覆外层壁材)a7过筛,选取粒径10μm以下的筛分20g和1000g超高分子量聚乙烯gx5028(美国lyondellbasell制)在双行星动力混合机低速干混均匀;然后在所得到的混合物料中添加1000g石蜡油,1g抗氧剂cyanox2777(美国cyanamid制)并转移至实验用非啮合式双螺杆挤出机,在200℃塑化挤出流延成膜,降温固液分离后,在110℃进行双向拉伸,在使用戊烷萃取石蜡油,在115℃进行热定型扩孔,得到20μm厚度的二次电池用隔膜b8。
[0200]
ncm811三元锂离子二次软包电池的制备
[0201]
将以上的本技术的实施例1~3和对比例1~3制备的隔膜(b1~b6)作为ncm811三元锂离子二次软包电池隔膜;
[0202]
将正极活性材料lini
0.8
co
0.1
mn
0.1
o2、导电剂乙炔黑、粘结剂聚偏二氟乙烯(pvdf)按重量比94:3:3在n-甲基吡咯烷酮溶剂体系中充分搅拌混合均匀后,涂覆于铝箔上烘干、冷压,得到正极极片;
[0203]
将负极活性材料人造石墨、导电剂乙炔黑、粘结剂丁苯橡胶(sbr)以及增稠剂碳甲基纤维素钠(cmc)按照重量比95:2:2:1在去离子水水性体系中充分搅拌混合均匀后,涂覆
于铜箔上烘干、冷压,得到负极极片;
[0204]
将1mol/l的lipf6有机溶剂溶液作为电解质,有机溶剂为碳酸乙烯酯(ec)、碳酸二乙酯(dec)、碳酸二甲酯(dmc)体积比为1:1:1的混合物、另外再添加2.0%成膜助剂碳酸亚乙烯酯(vc);
[0205]
将上述正极片、隔膜、负极片在环境湿度小于2%的环境下组装,经注入电解液、化成、分容,分别得到容量为5ah,2.8v-4.25v的ncm811三元锂离子二次软包电池。
[0206]
性能测试
[0207]
1、二次电池初始克容量测试
[0208]
将上述制备的各二次电池,分别在25℃恒温环境下,静置5min,按照1/3c放电至2.8v,静置5min后,按照1/3c充电至4.25v,然后在4.25v下恒压充电至电流≤0.05ma,静置5min,此时的充电容量记为c0,然后按照1/3c放电至2.8v,此时的放电容量为初始放电容量,记为d0。
[0209]
将测试的放电容量值(即初始放电容量d0)除以二次电池中正极活性材料的质量,即为正极活性材料的全电初始克容量。
[0210]
2、二次电池在25/45℃循环性能测试
[0211]
将上述制备的各二次电池,分别在25℃或45℃的恒温环境下,在2.8~4.25v下,按照1c充电至4.25v,然后在4.25v下恒压充电至电流≤0.05ma,静置5min,然后按照1c放电至2.8v,容量记为dn(n=0,1,2
……
),重复上述操作,进行500次循环,测定容量保持率。
[0212]
3、二次电池70℃胀气性能测试
[0213]
对于上述制备的100%soc的各二次电池(保护电压范围:2.7-4.3v,标称容量2.25ah),利用排水法测量存储前的初始电芯(裸电芯)体积,然后将上述各二次电池分别在70℃存储于存储炉中,每隔48h将电芯拿出存储炉,冷却至室温后再次利用排水法测量电芯体积,存储30天结束测试,或者体积膨胀超过50%停止存储。
[0214]
二次电池70℃存储30天后的胀气量=[二次电池70℃存储30天后的电芯体积-二次电池的初始电芯体积]
÷
初始放电容量d0。
[0215]
4、荷电保持能力与容量恢复能力
[0216]
常温下将上述制备的各二次电池,以1/3c充至4.25v,在60℃温度下存储60天,恢复至常温下并保持5小时,以1/3c放电至2.8v,记录放电容量作为放电容量c1,计算荷电保持能力d1,d1=放电容量c1÷
额定容量
×
100%;继续以1/3c充至4.25v,再以1/3c放电至截止2.8v,记录放电容量作为放电容量c2,计算容量恢复能力d2,d2=放电容量c2÷
额定容量
×
100%。
[0217]
5、45℃、500次循环测试后拆包测试负极过渡金属离子含量
[0218]
将上述进行45℃、500次循环测试后的二次电池进行拆包,取出负极,对其消解后,采用icp-aes法测试过渡金属(包括ni、co、mn、cu、fe)离子含量。
[0219]
表1实施例1-6和对比例1-2的微胶囊化过渡金属离子捕捉剂的参数
[0220][0221]
表2实施例1-6和对比例1-2的二次电池用隔膜的参数
[0222][0223]
注:抗氧剂cyanox2777为亚磷酸酯类抗氧剂与受阻胺类抗氧剂的混合物。
[0224]
表3实施例1-6和对比例1-2的隔膜制成的全电池对比测试数据
[0225][0226]
从表3可以看出,实施例1~6的隔膜b1~b6使用了本技术的微胶囊化过渡金属离子捕捉剂。由隔膜b1~b6制成的二次电池,在循环性能方面具有明显的提升,这是因为在循环过程中,二次电池正极产生的过渡金属离子在通过隔膜b1~b6的过程中被有效的“拦截”,有效的提升了二次电池的性能。另外,还具有较高的初始克容量,良好的荷电保持能力、容量恢复能力,并且在高温贮存胀气性能方面也具有明显的提升。因此,实施例1~6的隔膜b1~b6由于使用了本技术的微胶囊化过渡金属离子捕捉剂,因此在能量密度、循环性能、安全性能等方面具有优异的技术效果。
[0227]
相对于此,对比例1的隔膜b7未添加任何过渡金属离子捕捉剂,因此,无法有效地除去锂离子二次电池中的过渡金属离子,从而导致在循环性能上明显较差。另外,在荷电保持能力、容量恢复能力、高温贮存胀气量方面也显示出下降的倾向。对比例2的b8隔膜由于使用了没有包覆外层壁材的微胶囊化过渡金属离子捕捉剂,因此,作为芯材的碱金属硫化物被过快地释放到电解液中,虽然降低了过渡金属离子的含量,但也由于快速释放导致了大量副反应的产生,在能量密度、循环性能、安全性能等方面不仅没有提升,反而出现了大幅下降。
[0228]
另外,实施例4~6与实施例1~3相比,虽然这些实施例均在能量密度、循环性能和安全性能的改善方面,均取得了良好的效果。但由于实施例4的隔膜4使用了内层壁材与芯材的重量比为4:1的微胶囊化过渡金属离子捕捉剂a4,内层壁材包覆偏厚,因此,芯材释放的速度变慢,导致二次电池中过渡金属离子的含量稍高,影响了二次电池的循环性能,在能量密度、安全性能等方面也有下降的倾向。实施例5的隔膜b5使用了外层壁材与内层包覆芯材的重量比为8.3:1的微胶囊化过渡金属离子捕捉剂a5,由于外层壁材包覆较厚,芯材释放的速度变慢,导致二次电池中过渡金属离子的含量稍高,影响了二次电池的循环性能,在能量密度、安全性能等方面也有下降的倾向。实施例6的隔膜b6使用了外层壁材与内层包覆芯
材的重量比为1.2:1的微胶囊化过渡金属离子捕捉剂a6,由于外层壁材包覆较薄,因此,芯材释放变快,虽然降低了二次电池中过渡金属离子的含量,但也带来了一些副反应,在能量密度、循环性能和安全性能的改善方面,也稍弱于实施例1~3。
[0229]
需要说明的是,本技术不限定于上述实施方式。上述实施方式仅为例示,在本技术的技术方案范围内具有与技术思想实质相同的构成、发挥相同作用效果的实施方式均包含在本技术的技术范围内。此外,在不脱离本技术主旨的范围内,对实施方式施加本领域技术人员能够想到的各种变形、将实施方式中的一部分构成要素加以组合而构筑的其它方式也包含在本技术的范围内。