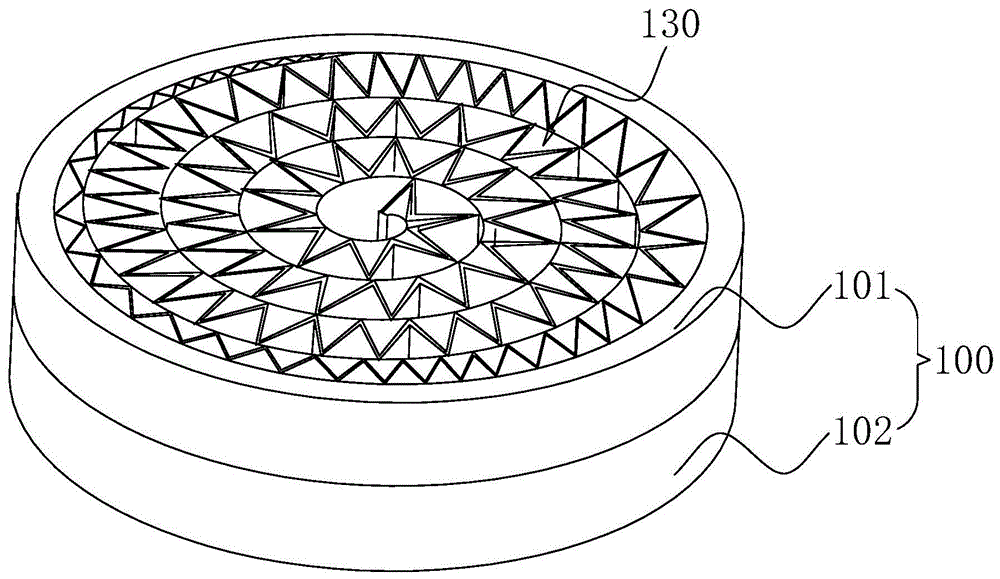
本申请涉及催化燃烧器的
技术领域:
,更具体地说,它涉及一种催化涂层及应用该催化涂层的双层多微孔催化燃烧器。
背景技术:
:燃烧器,是使燃料和空气以一定方式喷出混合燃烧的装置,被广泛应用于集成灶等领域。公开号为cn107401742a的中国专利中公开了一种双层多微孔催化燃烧器,包括主体多微孔催化燃烧板基质,所述主体多微孔催化燃烧板基质上安装有辅助燃烧板基质,所述主体多微孔催化燃烧板基质的目数比辅助燃烧板基质的目数高,所述主体多微孔催化燃烧板基质的厚度大于辅助燃烧板基质的厚度,所述辅助燃烧板基质上涂覆有稀土富氧催化燃烧涂层。上述燃烧器在进行燃烧反应时,空气和燃气混合后进入辅助燃烧板基质和主体多微孔催化燃烧板基质中,并在主体多微孔催化燃烧板基质中进行燃烧反应。针对上述中的相关技术,发明人认为上述稀土富氧催化燃烧涂层的催化效果还有待提高,因此需要一种具有催化效果更好的催化涂层。技术实现要素:为了改善相关技术中催化剂催化效果有待优化的问题,本申请提供一种催化涂层及应用该催化涂层的双层多微孔催化燃烧器。第一方面,本申请提供的一种催化涂层采用如下的技术方案:所述催化涂层包括过渡层、载体层和活性层,所述过渡层由胶粘剂固化得到,其中所述胶粘剂由包含以下质量份的原料制成:通过采用上述技术方案,通常情况下铁铬铝基体的表面比较平滑,催化剂的活性组分很难固定在铁铬铝基体上,进而使得铁铬铝表面催化剂的负载量很难控制。由于催化涂层中采用了过渡层、载体层和活性层,过渡层的设置,提供了载体层与铁铬铝表面固着的介质,使得载体层能够较好地固着到铁铬铝表面;载体层的设置,使得活性层与过渡层间结合更加紧密;活性层的设置,提供了催化燃气燃烧的活性组分附着的区域,从而一定程度上缓解了铁铬铝表面催化剂负载量难以控制的问题,从而提高催化涂层的催化效果。由于采用了lano3·h2o、ce(no3)3·6h2o和hno3,使得在胶粘剂中引入稀土金属元素la和ce,起到对胶粘剂的改性作用,从而提高催化涂层的催化效果。异丁酸的添加起到调节胶体ph值的作用。优选的,所述胶粘剂由以下工艺步骤制备得到:按照质量份数将去离子水、lano3·h2o和ce(no3)3·6h2o加入到sb粉中,按照质量份数加入hno3和异丁酸,得到混合物a,然后对混合物a进行搅拌并恒温加热,控制搅拌速度为300-500r/min,控制体系温度为75-80℃,控制搅拌和加热时间为3-5h,获得所述胶粘剂。通过采用上述技术方案,由于采用了lano3·h2o、ce(no3)3·6h2o和hno3,使得可在胶粘剂中引入稀土元素la和ce,起到对胶粘剂的改性作用,同时通过恒温反应以获得稳定的胶粘剂胶体。优选的,所述载体层由所述胶粘剂和载体剂制备得到,其中所述载体剂由包含以下质量份的原料组成:al2o350-70份;2,2,4-三甲基-1,3-戊二醇15-25份;所述载体层由以下工艺制备得到:将质量比为1:1的所述胶粘剂和所述载体剂进行混合,得到混合物b,然后对混合物b进行搅拌和恒温加热,控制搅拌速度为200-300r/min,控制体系温度为55-60℃,控制反应时间为1-2h,得到混合物e,待混合物e冷却后进行球磨,控制球磨时间为6-8h,得到载体层胶体,将所述载体层胶体固化后得到所述载体层。通过采用上述技术方案,由于采用了al2o3,因此,制备得到的载体剂胶体具有多孔性和良好的粘合性,进而使得活性组分能够更好地固着到载体剂胶体上;2,2,4-三甲基-1,3-戊二醇的添加,起到降低载体剂胶体的表面张力的作用。由于采用胶粘剂和载体剂混合加热的方式,因此,使得载体层胶体中生成具有良好成膜性能的2,2,4-三甲基-1,3-戊二醇单异丁酸酯,进一步提高载体层与过渡层间的粘结强度,同时促进载体层更好地与活性层结合。优选的,所述活性层由所述胶粘剂、所述载体剂和活性组分制备得到,其中所述活性组分由co(no3)2·6h2o、mg(no3)2和(nh2)2co按照摩尔比(2-8):(2-8):50制备而成;所述活性层由以下工艺制备得到:将质量比为1:1:1的所述胶粘剂、所述载体剂和所述活性组分进行混合,得到混合物f,向混合物f中加入hno3,控制搅拌速度为200-300r/min,得到混合物g,将混合物g进行球磨,控制球磨时间为8-10h,得到活性胶体,将所述活性胶体固化后得到所述活性层。通过采用上述技术方案,由于采用了co(no3)2·6h2o、mg(no3)2和(nh2)2co,因此,可通过尿素燃烧法制备得到具有催化活性的co3o4和co、mg氧化物。由于采用了胶粘剂、载体剂和活性组分混合球磨的方式,使得活性组分具有更小的粒径的同时,促进活性组分更好地固着到载体剂上,同时胶粘剂的添加,起到促进各组分相互粘结的作用,进而获得具有良好催化活性和附着性能的活性层胶体。优选的,所述(co(no3)2·6h2o加mg(no3)2)之和:所述(nh2)2co的摩尔比为1:5。通过采用上述技术方案,从而获得百分比含量较高的活性组分,一定程度上增强了活性组分的催化活性,进而提高了催化涂层对燃气的催化燃烧效果。优选的,所述活性组分由以下工艺步骤制备得到:按照摩尔比将co(no3)2·6h2o、mg(no3)2和(nh2)2co混合并搅拌,得到混合物c,将混合物c于室温下进行研磨工作,在体系温度为800-850℃的条件下对研磨后的混合物c进行燃烧反应,控制反应时间为20-30min,得到产物d,将产物d自然冷却,即可得到所述活性组分。通过采用上述技术方案,由于采用了co(no3)2·6h2o、mg(no3)2和(nh2)2co,因此,通过尿素燃烧法制备得到具有催化活性的co3o4和co、mg氧化物;同时采用先对混合物进行研磨再进行燃烧反应的方式,使得制备得到的co3o4和co、mg氧化物具有较小的粒径,进而方便活性组分负载到载体剂胶体上的孔隙中。优选的,所述胶粘剂:所述载体剂:所述活性组分的质量比为(30-40):(20-25):(10-14)。通过采用上述技术方案,从而获取催化活性较高的催化涂层,进一步提高催化涂层对燃气催化燃烧的催化效果。优选的,所述双层多微孔催化燃烧器的催化涂层加工工艺由以下步骤组成:s1)依次用乙醇、稀盐酸、氢氧化钠溶液和去离子水对铁铬铝片进行清洗,对清洗后的铁铬铝片进行干燥;s2)将干燥后的铁铬铝片进行加热预氧化,控制预氧化温度为950℃,控制预氧化时间为12-16h,将预氧化后的铁铬铝片进行自然冷却;s3)将所述步骤s2中自然冷却后的铁铬铝片放入所述胶粘剂中浸渍1h,然后在120℃下干燥2h,在500℃下对铁铬铝片进行焙烧,控制焙烧时间为5h,自然冷却后在铁铬铝片表面形成所述过渡层;s4)将所述步骤s3中形成所述过渡层后的铁铬铝片放入所述载体层胶体中浸渍1h,然后在120℃下干燥2h,在500℃下对铁铬铝片进行焙烧,控制焙烧时间为5h,自然冷却后在铁铬铝片表面形成所述载体层;s5)将所述步骤s4中形成所述载体层后的铁铬铝片放入活性胶体中浸渍1h,然后在120℃下干燥2h,在500℃下对铁铬铝片进行焙烧,控制焙烧时间为5h,自然冷却后在铁铬铝片表面形成所述活性层,得到所述催化涂层。通过采用上述技术方案,由于采用了步骤s1,大大减小了铁铬铝片表面上的油剂、预氧化物和其他的表面杂质的存在量,方便进行后续催化涂层的加工;由于采用了步骤s3、步骤s4和步骤s5,使得铁铬铝表面上依次形成过渡层、载体层和活性层,从而获得具有良好催化燃烧性能的催化涂层,进一步提高燃气燃烧的利用率。第二方面,本申请提供一种应用该催化涂层的双层多微孔催化燃烧器,采用如下的技术方案:一种双层多微孔催化燃烧器,包括主体燃烧层和安装在所述主体燃烧层上的辅助止火层,所述辅助止火层位于靠近气源的一端,所述主体燃烧层上设置有多个供气流通过的第一通道,所述辅助止火层上设置有多个供气流通过的第二通道,所述第二通道的截面面积小于所述第一通道的截面面积,所述主体燃烧层内涂覆有如权利要求1-8任一所述的催化涂层。通过采用上述技术方案,当燃烧器本体进行燃烧反应时,燃气从辅助止火层中的第二通道向主体燃烧层中的第一通道处运动,由于第二通道本身的横截面积较小,从而使得第二通道具有防回火的功能,进而无需添加金属丝网即可实现燃烧器本体防回火的功能;同时主体燃烧层和第一通道的设置,提供了燃气燃烧的空间,使得燃气在主体燃烧层中的第一通道内进行燃烧,增加了燃气在第一通道内的停留时间,一定程度上提高燃气进行燃烧反应的时间,提高了燃气燃烧的利用率;同时催化涂层的设置,促进了燃气再主体燃烧层内充分燃烧,一定程度上增大了对燃气燃烧的利用率,使得燃烧更加充分。优选的,各所述第一通道内开设有多个第一缺口,各所述第二通道内开设有多个第二缺口。通过采用上述技术方案,第一缺口和第二缺口的设置,使得燃气流经第一缺口和第二缺口时产生紊流,从而使得燃气与空气充分接触,一定程度上提高了燃气的燃烧利用率。综上所述,本申请具有以下有益效果:1、由于本申请采用了主体燃烧层、辅助止火层和催化涂层,使得燃气能够在主体燃烧层中进行充分燃烧,增加了燃气进行燃烧反应的时间,一定程度上提高了燃气的燃烧利用率,同时辅助止火层起到防回火的作用,增强了燃烧反应时的安全性;同时通过胶粘剂、载体剂和活性组分的添加,使得活性组分附着到载体剂上后可通过胶粘剂固着到铁铬铝表面上,一定程度上缓解了铁铬铝表面催化剂负载量难以控制的问题,从而提高催化涂层的催化效果。2、本申请中优选采用胶粘剂、载体剂和活性组分,由于胶粘剂中的异丁酸和载体剂中的2,2,4-三甲基-1,3-戊二醇会发生反应,生成具有良好成膜性能的2,2,4-三甲基-1,3-戊二醇单异丁酸酯,进而获得良好固着性能的催化涂层;由于胶粘剂中采用了ce(no3)3·6h2o和lano3·h2o,进而使得催化涂层中引入la2o3和ceo2等氧化物,la2o3和ceo2能够提高al2o3载体涂层的热稳定性和抗烧结性能,进一步促进金属的分散性能;同时ceo2具有一定的贮氧能力,一定程度上提高了催化剂的催化活性。附图说明图1是本申请实施例中燃烧器本体的立体结构示意图;图2是图1所示的辅助止火层的立体结构示意图;图3是图1所示的主体燃烧层的立体结构示意图;图4是本申请实施例中燃烧器本体和安装机构的爆炸结构示意图。附图标记说明:100、燃烧器本体;101、主体燃烧层;1011、主体基板;1012、第一波纹板;102、辅助止火层;1021、辅助基板;1022、第二波纹板;110、第二通道;120、第二缺口;130、第一通道;140、第一缺口;150、安装块;160、安装台;161、第一阶梯;162、第二阶梯;170、锁紧螺栓;180、燕尾槽;190、安装槽;200、控制杆;210、防滑条纹;220、卡接杆;230、限位块;240、限位槽;250、引导斜面。具体实施方式以下结合附图和实施例对本申请作进一步详细说明。以下实施例及对比例中各原料组分的来源信息详见表1表1原料组分来源表原料来源sb粉德国condeachemic公司al2o3天津市百世化工有限公司hno3(ar级)北京北化精细化学品有限公司co(no3)2·6h2o天津市科密欧化学试剂有限公司mg(no3)2济南骏腾化工有限公司(nh2)2co天津市百世化工有限公司ce(no3)3·6h2o天津市科密欧化学试剂有限公司lano3·h2o天津市百世化工有限公司异丁酸天津市百世化工有限公司2,2,4-三甲基-1,3-戊二醇江苏德纳化学股份有限公司乙醇扬州德诺化工有限公司盐酸中山市怡雅生物科技有限公司氢氧化钠天津市百世化工有限公司制备例制备例1一种胶粘剂,由以下质量数的原料制成:sb粉40g;ce(no3)3·6h2o8g;lano3·h2o8g;hno320g;异丁酸6g;去离子水60g。一种胶粘剂的制备工艺具体包括以下工艺步骤:按照质量数依次将去离子水、lano3·h2o和ce(no3)3·6h2o加入到sb粉中,得到混合物a,然后对混合物a进行搅拌,控制转速为300r/min,按照质量比向混合物a中加入hno3和异丁酸,然后对混合物a进行恒温加热,控制体系温度为75℃,控制反应时间为3h,得到胶粘剂。制备例2-5制备例2-5胶粘剂中原料的质量数和工艺参数与制备例1的区别计为表2,其余均与制备例1相同。表2制备例2-5胶粘剂中原料的质量数和工艺参数制备例6一种活性组分,由以下摩尔数的原料制成:co(no3)2·6h2o0.2mol;mg(no3)20.8mol;(nh2)2co5mol。一种活性组分的制备工艺具体包括以下工艺步骤:按照摩尔比将co(no3)2·6h2o、mg(no3)2和(nh2)2co进行混合并搅拌,得到混合物c,然后将混合物c于室温下进行研磨工作,在体系温度为800℃的条件下对研磨后的混合物c进行燃烧反应,控制反应时间为30min,得到产物d,将产物d进行自然冷却,即可得到活性组分。制备例7-10制备例7-10活性组分中原料的摩尔百分比和工艺参数与制备例6的区别计为表3,其余均与制备例6相同。表3制备例7-10活性组分中原料的摩尔百分比和工艺参数实施例实施例1一种催化涂层包括过渡层、载体层和活性层。过渡层由胶粘剂300g制备得到,其中胶粘剂采用深圳市金丝邦胶粘剂有限公司生产的ergo丙烯酸结构胶1307142g。载体层由载体剂200g制备得到,其中载体剂采用天津市百世化工有限公司生产的al2o350g。活性层由活性组分100g制备得到,其中活性组分采用上海久岭化工有限公司生产的5%钯碳催化剂6mol。催化涂层的加工工艺由以下步骤组成:s1)依次用乙醇、稀盐酸、氢氧化钠溶液和去离子水对铁铬铝片进行清洗,铁铬铝片在空气中自然干燥后,将自然干燥后的铁铬铝片放入电热恒温干燥箱内进行干燥,控制干燥温度为120℃,控制干燥时间为3h;s2)将干燥后的铁铬铝片放入管式电阻炉中进行加热预氧化,控制预氧化温度为950℃,控制预氧化时间为12h,将预氧化后的铁铬铝片进行自然冷却;s3)将所述步骤s2中自然冷却后的铁铬铝片放入胶粘剂中浸渍1h,然后在120℃下干燥2h,在500℃下对铁铬铝片进行焙烧,控制焙烧时间为5h,自然冷却后在铁铬铝片表面形成过渡层;s4)将所述步骤s3中形成过渡层后的铁铬铝片放入al2o3粉末中浸渍1h,然后在500℃下对铁铬铝片进行焙烧,控制焙烧时间为5h,自然冷却后在铁铬铝片表面形成所述载体层;s5)将所述步骤s4中形成载体层后的铁铬铝片放入钯碳催化剂粉末中浸渍1h,在500℃下对铁铬铝片进行焙烧,控制焙烧时间为5h,自然冷却后在铁铬铝片表面形成活性层,得到催化涂层。实施例2一种催化涂层,与实施例1的区别在于胶粘剂选用制备例1制备的胶粘剂;步骤s4中将质量比为1:1的胶粘剂和载体剂进行混合,得到混合物b,然后对混合物b进行搅拌和恒温加热,控制搅拌速度为200r/min,控制体系温度为55℃,控制反应时间为1h,得到混合物e,待混合物e冷却后进行球磨,控制球磨时间为6h,得到载体层胶体;将步骤s3中形成过渡层后的铁铬铝片放入所述载体层胶体中浸渍1h,然后在120℃下干燥2h,在500℃下对铁铬铝片进行焙烧,控制焙烧时间为5h,自然冷却后在铁铬铝片表面形成载体层;步骤s5中将质量比为1:1:1的胶粘剂、载体剂和活性组分进行混合,得到混合物f,向混合物f中加入hno3,控制搅拌速度为200r/min,得到混合物g,将混合物g进行球磨,控制球磨时间为8h,得到活性胶体;将所述步骤s4中形成载体层后的铁铬铝片放入活性胶体中浸渍1h,然后在120℃下干燥2h,在500℃下对铁铬铝片进行焙烧,控制焙烧时间为5h,自然冷却后在铁铬铝片表面形成活性层,得到催化涂层。实施例3一种催化涂层,与实施例1的区别在于载体剂中添加了2,2,4-三甲基-1,3-戊二醇15g;步骤s4中将质量比为1:1的胶粘剂和载体剂进行混合,得到混合物b,然后对混合物b进行搅拌和恒温加热,控制搅拌速度为200r/min,控制体系温度为55℃,控制反应时间为1h,得到混合物e,待混合物e冷却后进行球磨,控制球磨时间为6h,得到载体层胶体;将步骤s3中形成过渡层后的铁铬铝片放入所述载体层胶体中浸渍1h,然后在120℃下干燥2h,在500℃下对铁铬铝片进行焙烧,控制焙烧时间为5h,自然冷却后在铁铬铝片表面形成载体层;步骤s5中将质量比为1:1:1的胶粘剂、载体剂和活性组分进行混合,得到混合物f,向混合物f中加入hno3,控制搅拌速度为200r/min,得到混合物g,将混合物g进行球磨,控制球磨时间为8h,得到活性胶体;将所述步骤s4中形成载体层后的铁铬铝片放入活性胶体中浸渍1h,然后在120℃下干燥2h,在500℃下对铁铬铝片进行焙烧,控制焙烧时间为5h,自然冷却后在铁铬铝片表面形成活性层,得到催化涂层。实施例4一种催化涂层,与实施例1的区别在于活性组分采用制备例6制备的活性组分;步骤s4中将质量比为1:1的胶粘剂和载体剂进行混合,得到混合物b,然后对混合物b进行搅拌和恒温加热,控制搅拌速度为200r/min,控制体系温度为55℃,控制反应时间为1h,得到混合物e,待混合物e冷却后进行球磨,控制球磨时间为6h,得到载体层胶体;将步骤s3中形成过渡层后的铁铬铝片放入所述载体层胶体中浸渍1h,然后在120℃下干燥2h,在500℃下对铁铬铝片进行焙烧,控制焙烧时间为5h,自然冷却后在铁铬铝片表面形成载体层;步骤s5中将质量比为1:1:1的胶粘剂、载体剂和活性组分进行混合,得到混合物f,向混合物f中加入hno3,控制搅拌速度为200r/min,得到混合物g,将混合物g进行球磨,控制球磨时间为8h,得到活性胶体;将所述步骤s4中形成载体层后的铁铬铝片放入活性胶体中浸渍1h,然后在120℃下干燥2h,在500℃下对铁铬铝片进行焙烧,控制焙烧时间为5h,自然冷却后在铁铬铝片表面形成活性层,得到催化涂层。实施例5一种催化涂层,与实施例2的区别在于载体剂中添加了2,2,4-三甲基-1,3-戊二醇15g。实施例6一种催化涂层,与实施例2的区别在于活性组分采用制备例6制备的活性组分。实施例7一种催化涂层,与实施例3的区别在于活性组分采用制备例6制备的活性组分。实施例8一种催化涂层,与实施例2的区别在于载体剂中添加了2,2,4-三甲基-1,3-戊二醇15g,活性组分采用制备例6制备的活性组分。实施例9-12中催化涂层的原料配比与实施例8的区别计为表4,其余均与实施例8相同。表4催化涂层的原料配比实施例13-16中催化涂层的原料配比、工艺参数和实施例8的区别计为表5,其余均与实施例8相同。对比例对比例1一种催化涂层,与实施例2的区别在于,未添加胶粘剂。对比例2一种催化涂层,与实施例2的区别在于,未添加载体剂。对比例3一种催化涂层,与实施例2的区别在于,未添加活性组分。对比例4一种催化涂层,与实施例2的区别在于,胶粘剂中未添加ce(no3)3·6h2o和lano3·h2o。对比例5一种催化涂层,与实施例5的区别在于,胶粘剂中未添加异丁酸。应用例参照图1,一种双层多微孔催化燃烧器,燃烧器本体100包括主体燃烧层101和焊接在主体燃烧层101一端的辅助止火层102,辅助止火层102位于主体燃烧层101靠近气源的一端,此处主体燃烧层101的高度和辅助止火层102的高度相同,也可以是主体燃烧层101的高度小于辅助止火层102的高度。参照图2,辅助止火层102包括辅助基板1021和多个焊接在辅助基板1021上的第二波纹板1022,各第二波纹板1022沿辅助基板1021的长度方向依次排布,各第二波纹板1022与辅助基板1021间形成供燃气通过的第二通道110,辅助止火层102由辅助基板1021和各第二波纹板1022沿辅助基板1021长度方向卷绕焊接而成。参照图2,各第二波纹板1022沿辅助基板1021的宽度方向间隔开设有三个第二缺口120,此处第二缺口120的数量也可以是四个,也可以是两个,但凡能够实现燃气在第二通道110内产生紊流的作用即可。参照图3,主体燃烧层101包括主体基板1011和多个焊接在主体基板1011上的第一波纹板1012,各第一波纹板1012沿主体基板1011的长度方向依次排布,各第一波纹板1012与主体基板1011间形成供燃气通过的第一通道130,主体燃烧层101由主体基板1011和各第一波纹板1012沿主体基板1011长度方向卷绕焊接而成。各第一波纹板1012上涂覆有催化涂层,且各第一通道130的截面面积远大于各第二通道110的截面面积。参照图3,各第一波纹板1012沿主体基板1011的宽度方向间隔开设有三个第一缺口140,此处第一缺口140的数量也可以是四个,也可以是两个,但凡能够实现燃气在第一通道130内产生紊流的作用即可。参照图4,辅助止火层102远离主体燃烧层101的一端外侧壁上安装有安装机构,安装机构包括两固定安装在辅助止火层102外侧壁上的安装块150和两用于与炉灶连接的安装台160。安装台160包括第一阶梯161和与第一阶梯161一体成型的第二阶梯162,第一阶梯161的高度小于第二阶梯162的高度,第一阶梯161上螺纹连接有用于将安装台160固定安装到炉灶上的锁紧螺栓170,第二阶梯162的顶面沿竖直方向开设有燕尾槽180,安装块150的底面与辅助止火层102的底面间设置有间距,安装块150的底面上设置有倒角,以方便安装块150滑移进入燕尾槽180内。参照图4,第二阶梯162上开设有与燕尾槽180连通的安装槽190,第二阶梯162顶面转动连接有控制杆200,控制杆200一端伸出第二阶梯162顶面并设置有防滑条纹210,控制杆200的另一端伸入安装槽190内并固定连接有卡接杆220。安装块150的顶面固定连接有限位块230,限位块230的侧壁上开设有限位槽240,限位槽240槽口相对的两侧壁上设置有用于引导卡接杆220滑移进入限位槽240内的引导斜面250。参照图4,燃烧器本体100(参照图1)安装到炉灶上时,辅助止火层102远离主体燃烧层101的一端端面与炉灶顶面抵紧,安装块150的底面与燕尾槽180槽底抵紧,卡接杆220滑移进入限位槽240内,且卡接杆220的顶面和底面分别抵紧限位槽240相对的两侧壁。当需要进行燃烧器本体100的安装工作时,首先两安装台160通过锁紧螺栓170固定安装到炉灶上,然后将辅助止火层102上的两安装块150滑移进入燕尾槽180内,直至安装块150的底面抵紧燕尾槽180底面,此时辅助止火层102的底面与炉灶顶面抵紧,转动控制杆200,控制杆200带动卡接杆220发生转动并滑移进入限位槽240内,卡接杆220的顶面和底面与限位槽240相对的两侧壁抵紧,实现燃烧器本体100在炉灶上的安装工作。然后连通气源,燃气和空气从辅助止火层102中的第二通道110向主体燃烧层101中的第一通道130内运输,燃气和空气经过第二缺口120和第一缺口140处时产生紊流,促进燃气和空气充分接触,最终燃气和空气在第一通道130内催化涂层的作用下充分燃烧。性能检测试验针对实施例1-16和对比例1-5提供的催化涂层,应用于应用例中的双层多微孔催化燃烧器后,依照gbz/t300.37-2017《工作场所空气有毒物质测定第37部分:一氧化碳和二氧化碳》中的一氧化碳和二氧化碳的不分光红外线气体分析仪法,对双层多微孔催化燃烧器燃烧尾气中的co含量进行测量;依照db50/t833-2017《环境空气氮氧化物的测定(一氧化氮和二氧化氮)化学发光法》,对双层多微孔催化燃烧器燃烧尾气中的no含量进行测量,并通过将no的测量结果换算为质量浓度,得到检测数据见表6。表6性能检测数据表结合实施例1-4和对比例1-5并结合表6可以看出,在双层多微孔催化燃烧器中添加催化涂层,能够提高双层多微孔催化燃烧器对燃气的催化燃烧效果,进而降低燃烧尾气中co和no的含量,实现对燃烧尾气的减排;同时深圳市金丝邦胶粘剂有限公司生产的ergo丙烯酸结构胶1307、天津市百世化工有限公司生产的al2o3、上海久岭化工有限公司生产的5%钯碳催化剂能够进一步提升双层多微孔催化燃烧器对燃气的催化燃烧效果,进一步降低燃烧尾气中co和no的含量;由于制备例1的胶粘剂中包含了稀土元素la和ce,进一步使得在催化涂层中引入了la2o3和ceo2,能够提高al2o3载体涂层的热稳定性和抗烧结性能;同时ceo2具有一定的贮氧能力,进而显著提升双层多微孔燃烧器对燃气的催化燃烧效果,从而显著降低燃烧尾气中co和no的含量。由于制备例6中的活性组分中包含了co(no3)2·6h2o、mg(no3)2和(nh2)2co,进而通过尿素燃烧法制备得到具有催化活性的co3o4和co、mg氧化物,同时co、mg氧化物具有一定的贮氧能力,进而显著提升双层多微孔燃烧器对燃气的催化燃烧效果,从而显著降低燃烧尾气中co和no的含量。结合实施例1-8和对比例1-5并结合表6可以看出,胶粘剂中的异丁酸和载体剂中的2,2,4-三甲基-1,3-戊二醇能够在制备催化涂层的过程中反应生成2,2,4-三甲基-1,3-戊二醇单异丁酸酯,从而使得催化涂层在成型过程中具有较好的成膜性,进而提高活性组分在催化涂层上的附着程度,从而提高催化涂层对燃气的催化燃烧效果,显著降低燃烧尾气中co和no的含量。结合实施例8-16并结合表6可以看出,通过提高催化涂层中胶粘剂、载体剂和活性组分的含量,可以提高催化涂层对燃气的催化燃烧效果,进而降低燃烧尾气中的co和no含量。本具体实施例仅仅是对本申请的解释,其并不是对本申请的限制,本领域技术人员在阅读完本说明书后可以根据需要对本实施例做出没有创造性贡献的修改,但只要在本申请的权利要求范围内都受到专利法的保护。当前第1页12