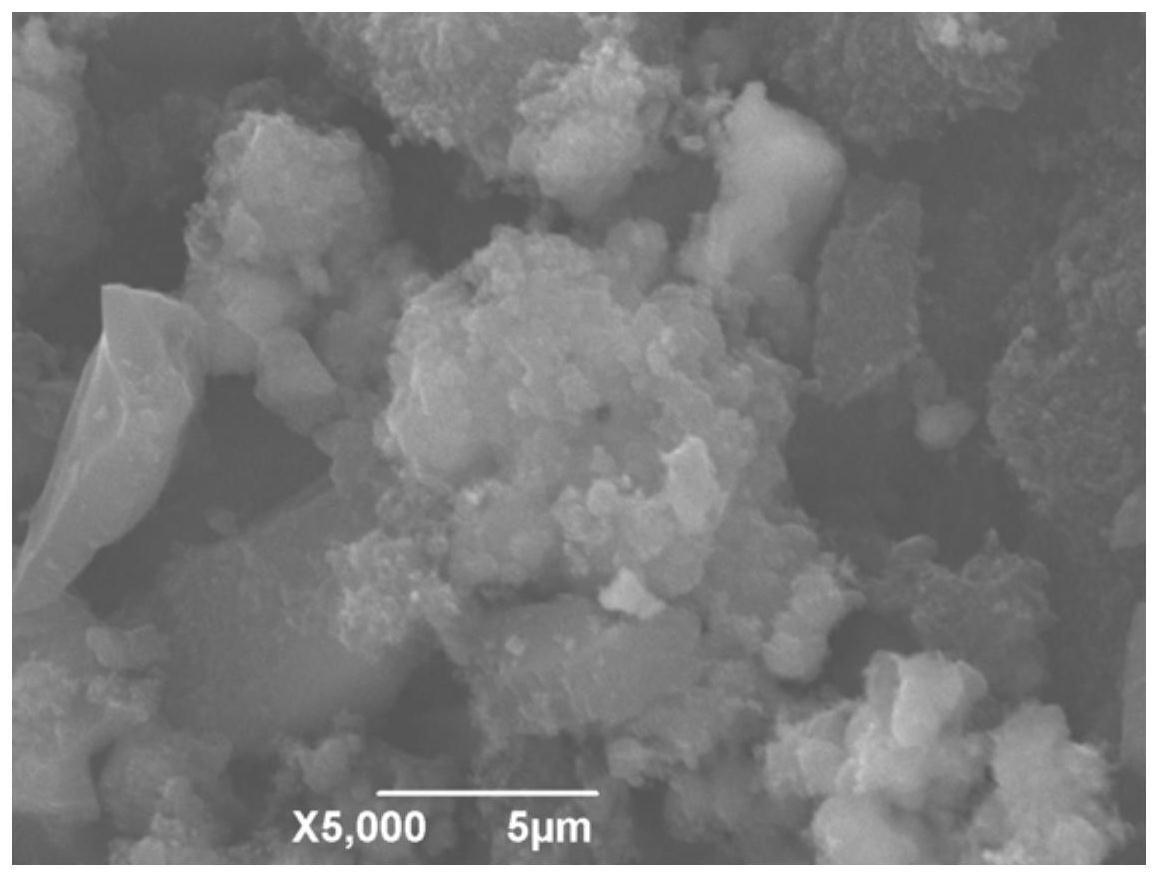
一种低温scr脱硝催化剂及其制备方法
技术领域
1.本发明属于大气污染治理技术、固废资源回收利用和低温scr催化剂制备技术领域,具体涉及一种低温scr脱硝催化剂及其制备方法。
背景技术:2.nox是一种主要的大气污染物,同时也是大气污染物治理的重点与难点,近年来其排放量一直高居不下。大量排放的nox导致雾霾、酸雨和光化学烟雾等自然灾害频发,对人们的日常生活和生命安全造成了严重影响,因此加强对nox的治理已经势在必行。选择性催化还原技术(scr)由于技术成熟、脱硝效率高和经济性好等优点应用最广泛,而该技术的核心在于scr催化剂,催化剂性能优劣是决定整个scr系统脱硝效果和经济性的关键,因此开发高效经济的scr催化剂是当下主要研究方向。目前商用钒钛系催化剂,由于具有脱硝效率高和抗so2效果好等优点而得到广泛应用,但是其并不适用于烟气温度较低的环境,而且制备成本相对较高、钒也易流失造成二次污染。因此,开发出一种性能稳定、活性温度窗口较宽、环境友好、制备成本低的催化剂尤为重要。
3.fcc废催化剂是石油工业使用后产生的固体废弃物,目前我国每年的fcc废催化剂产量已经超过10万吨,而大部分化工企业对fcc废催化剂处置都是采取填埋的方式,这不仅对生态环境造成严重威胁而且还制约了fcc废催化剂的资源化利用。fcc废催化剂的主要成分为al2o3和sio2,还有一定量的无机氧化物和稀土氧化物,如cao、fe2o3、mgo、ceo2、la2o3和v2o5,且其本身具有分子筛结构,作为脱硝催化剂原料具有极好的优势。
4.经检索,中国专利公开号为cn110357464a,公开日为2019年10月22日,名称为一种废fcc催化剂资源化利用的方法,其技术方案是:将20~40wt%的废fcc催化剂、30~50wt%的活性原料和20~40wt%的固体碱激发剂混合,搅拌,得到类地聚合物粉体。按所述类地聚合物粉体:水的质量比为1:0.3~0.5,将水加入所述类地聚合物粉体中,搅拌,得到类地聚合物凝胶。将所述类地聚合物凝胶加入模具中,振动,在养护箱内养护,脱模,室温继续养护3~7天,得到类地聚合物材料。又如公开号为cn108993531a,公开日为2018年12月14日,该发明公开了一种废fcc催化剂资源化利用的方法,其技术方案是:以50~70wt%的废fcc催化剂、25~45wt%的黏土和2~5wt%的tio2为催化剂原料,混合,烘干,研磨;置入圆盘造粒机,边转动边喷洒占催化剂原料10~15wt%的过渡金属盐水溶液,转动圆盘造粒机至形成粒径为3~5mm的球状催化剂颗粒;烘干,于1080~1200℃条件下烧结15~30min,制得臭氧催化剂。按照臭氧催化剂的填充体积为氧化塔或反应池有效容积的45~60%,将臭氧催化剂填充于催化氧化塔或反应池,臭氧投加量为50~75mg/l,反应15~30min,深度处理后的难降解工业废水cod达标排放。以上对fcc的处理方法均为将fcc作为活性组分的载体,其不足之处在于,使用的载体比表面积和孔隙率较小,限制了活性物种的分散性和活性中心的暴露。
5.生物炭是一种成本低廉、制备工艺简便,具有发达多孔结构与丰富比表面积的炭质材料。其原材料来源广泛,比较常见的有树木、农作物和动物粪便等,而且由于生物质是
可再生资源,因此理论上生物炭的原料是用之不尽取之不竭的。富含碳元素的生物炭在一定反应温度下可以直接用来还原nox,而且由于自身孔隙结构发达,可以直接用来吸附nox,或者提供较大的比表面积作为载体负载其他活性物质制备scr催化剂来转化nox,是一种制备scr脱硝催化剂的优良材料。
6.经检索,中国专利公开号为cn107694578a,公开日为2018年2月16日,发明名称为一种同时脱硫和硝汞的生物炭载体催化剂的制备方法,该发明将生物质原料洗净、粉碎,然后置于惰性气体氛围、温度为400~1200℃条件下进行高温焙烧2~6h,研磨,过筛,水洗至上清液无悬浮的浑浊物,干燥得到生物炭;将生物炭与化学活化剂混合均匀并在温度为300~900℃条件下焙烧2~6h得到生物炭载体,将生物炭载体置于浸渍液中浸渍处理0.5~2h,然后在温度为50~100℃条件下干燥,再置于惰性气体氛围、温度为450~950℃条件下进行高温焙烧3~6h即得生物炭载体催化剂,其中浸渍液为活性金属硝酸盐溶液与纳米贵金属溶液的混合浸渍液。该发明方法制备的生物炭载体催化剂在氨法还原一氧化氮的同时脱除冶炼烟气中的二氧化硫和单质汞,催化效率高,操作简便。其不足之处在于,生物炭主要起吸附作用,其用于催化反应在中氧化还原能力较低。赵中昆等在《mnox基催化剂低温nh3‑
scr脱硝研究进展》中公开了将mnox负载在载体上,作为催化剂在nh3‑
scr反应中表现出一定的催化活性。以上mnox负载在单一载体上,其催化活性提高有限。
技术实现要素:7.1.要解决的问题
8.本发明的主要目的在于针对现有scr脱硝催化剂低温脱硝效率差、制备成本高以及固废资源无法充分利用问题,提供一种低温scr脱硝催化剂及其制备方法。该催化剂以fcc废催化剂和生物炭混合物为载体,负载过渡金属氧化物高温焙烧制备所得。该催化剂克服了制备成本高昂的缺点,并将fcc废催化剂重新利用,实现了固废资源能源化。采用本发明的制备方法能够显著提高催化剂的低温脱硝效率,且涉及的制备工艺简单,原料来源广,具有重要的经济和环境效益。
9.2.技术方案
10.为了解决上述问题,本发明所采用的技术方案如下:
11.一种低温scr脱硝催化剂,包括复合载体和过渡金属氧化物,所述复合载体包括fcc废催化剂和生物炭,所述生物炭与fcc废催化剂的质量比为1:3~3:1,所述过渡金属氧化物负载在复合载体上,所述过渡金属氧化物中过渡金属元素的负载量为复合载体重量的5wt%~20wt%。
12.更进一步地,所述fcc废催化剂的比表面积为85.74m2·
g
‑1,平均孔径为9.35mm,所述fcc废催化剂和生物炭为粒径40
‑
60目的粉末。
13.更进一步地,所述过渡金属为mn,所述过渡金属氧化物包括mn2o3、mno2和mn3o4中的一种或多种。此外,过渡金属如cu、fe、ti、v、mo也可形成过渡金属氧化物负载在fcc废催化剂和生物炭的复合载体上,作为催化剂应用于低温scr脱硝中。
14.一种低温scr脱硝催化剂的制备方法,其步骤如下:
15.(1)称取及配置:分别称取fcc废催化剂、生物炭和过渡金属盐,配置过渡金属盐水溶液;
16.(2)浸渍:将称取的fcc废催化剂和生物炭分散到过渡金属盐水溶液中,再添加去离子水,搅拌均匀,充分浸渍;
17.(3)干燥:取出步骤(2)所得混合物置于干燥仪器中蒸干;
18.(4)焙烧:将干燥后的样品置于惰性气氛下焙烧,然后炉冷至常温,即得低温scr脱硝催化剂。
19.其中,步骤(2)中添加去离子水是为了充分浸渍,此处采取的是过量浸渍法,在实际操作过程中,实际配置的硝酸锰溶液浓度较大,按质量比量取硝酸锰溶液,不足以完全浸渍粉状生物炭和fcc废催化剂,因此进一步添加去离子水,将fcc废催化剂和生物炭在过渡金属盐水溶液中充分浸渍。
20.更进一步地,所述过渡金属盐水溶液为硝酸锰水溶液,也可采用氯化锰水溶液或硫酸锰水溶液,用于提供mn源,所述过渡金属盐水溶液质量浓度为50wt%。
21.更进一步地,步骤(2)中将fcc废催化剂和生物炭投加到过渡金属盐水溶液中后进行磁力搅拌20~30min,加入去离子水完全浸没后进行超声浸渍处理1h;
22.步骤(3)中干燥温度为90℃~110℃,此温度范围的干燥温度均可实现混合物的干燥,且对其成分、性质等无影响,在实际实验过程中,可将干燥温度设为105℃,干燥时间设为12h;所述设备包括干燥箱,还可使用管式炉或马弗炉,能实现样品的干燥即可;
23.步骤(4)所述惰性气氛为氮气气氛,还可使用氩气气氛或氦气气氛,其作用与氮气气氛相同;所述焙烧温度为400~600℃,焙烧时间为1~5h。
24.更进一步地,所述fcc废催化剂可采用直接购得的未经过预处理的fcc废催化剂,也可采用经过预处理的fcc废催化剂,所述fcc废催化剂的预处理方法为:
[0025]ⅰ.将fcc废催化剂研磨,过40目筛,得到40
‑
60目的均匀筛目大小的fcc废催化剂颗粒;
[0026]ⅱ.研磨后fcc废催化剂颗粒于110℃下烘干;
[0027]
更进一步地,所述生物炭为改性生物炭,所述改性生物炭的制备方法包括:
[0028]ⅰ.浸渍:将粉碎玉米芯投加到酸溶液中,浸渍处理;
[0029]ⅱ.干燥:捞出玉米芯干燥;
[0030]ⅲ.热解:将干燥后的玉米芯在惰性气氛下热解得热解炭;
[0031]ⅳ.洗涤:冷却后,取出热解炭浸泡在酸溶液中煮沸并搅拌,而后用去离子水反复清洗至洗涤液呈中性;
[0032]
ⅴ
.干燥后即得改性生物炭。
[0033]
更进一步地,步骤ⅰ所述酸溶液包括磷酸、盐酸或硝酸,其中,优选的为磷酸,所述酸的浓度为70wt%,所述浸渍为超声浸渍,浸渍的时间为1h;生物炭的改性是为了提升生物炭的比表面积和孔隙度,从而增强负载过渡金属后的脱硝效率,其中优选的为磷酸,通过磷酸浸渍对生物炭起到了化学活化改性,改性后提高了生物炭的比表面积和平均孔径,改性前比表面积为109.23m2·
g
‑1,平均孔径为1.848nm,改性后比表面积为1352.36m2·
g
‑1,平均孔径为5.498nm。
[0034]
步骤ⅱ所述干燥温度为90℃~110℃,干燥时间为12~24h,此范围的干燥温度和干燥时间均可实现混合物的干燥,且对其成分、性质等无影响,在实际实验过程中,可将干燥温度设为105℃,干燥时间设为24h;
[0035]
步骤ⅲ所述惰性气氛为氮气气氛、氩气气氛或氦气气氛,所述热解温度为600℃,热解时间为1h;
[0036]
步骤ⅳ所述酸溶液为盐酸、磷酸或硫酸,其中优选的为盐酸,所述酸溶液的浓度为0.1mol/l,所述去离子水的温度为80℃。
[0037]
以fcc废催化剂和改性生物炭为原料制备scr催化剂,不但解决了催化剂制备成本高的特点,而且可以提升催化剂的机械强度,降低生物炭的损失,实现废弃资源的合理利用,具有良好的经济效益、社会效益和环境效益。
[0038]
3.有益效果
[0039]
相比于现有技术,本发明的有益效果为:
[0040]
(1)本发明制备的催化剂在100~280℃范围内都具有优异的脱硝性能,活性温度窗口较宽,可适用于不同的烟气条件,生物炭在100℃以下仅起到吸附作用,当温度达到200℃以上,生物炭与nox发生反应;fcc废催化剂的使用温度为150℃以上,随着反应温度的上升其脱硝性能逐渐增加,在250℃时脱硝效率达到最高。将生物炭与fcc废催化剂掺混负载mn得到的低温scr脱硝催化剂的使用温度在120℃时,脱硝效率即可达到90%以上,mn负载能使脱硝活性中心由催化剂表面转移到mn氧化物表面,提升了催化剂的低温活性;
[0041]
(2)本发明结合生物炭具有较大比表面积和丰富的孔隙结构,对no具有较强吸附性能,同时生物炭中的c和co可以作为还原剂,催化no转化成n2(2c+2no
→
n2+2co,2co+2no
→
n2+2co2),fcc废催化剂中含有一定量cao、fe2o3、mgo、ceo2、la2o3和v2o5等,这些金属氧化物对no具有催化还原性能。将两者按照一定比例机械混合后,利用生物炭的高吸附性能与fcc废催化剂的碱性吸收作用和催化还原作用,实现对no的高效协同脱除;
[0042]
(3)本发明以fcc废催化剂为原料制备scr脱硝催化剂,用于工业烟气中nox脱除,不仅实现了工业固废的高价值循环再利用,而且降低了脱硝催化剂的制备成本,达到了“以废止废”的目的;
[0043]
(4)本发明解决了钒钛系催化剂低温脱硝效率低,生物炭催化剂机械强度低、易粉化、着火点低等问题,通过将生物炭与fcc废催化剂掺混,制备了强度高、孔隙发达、比表面积高的催化剂载体,有效提升了催化剂脱硝效率和生物炭损耗;
[0044]
(5)本发明克服了现有低温scr催化剂组分复杂,需要多种组分协同作用才能保证催化效率的不足,本发明仅以mn氧化物作为活性组分,既可获得较高的低温脱硝效率,避免了药品资源的不必要浪费,具有较高的研究和市场推广价值。
附图说明
[0045]
以下将结合附图和实施例来对本发明的技术方案作进一步的详细描述,但是应当知道,这些附图仅是为解释目的而设计的,因此不作为本发明范围的限定。此外,除非特别指出,这些附图仅意在概念性地说明此处描述的结构构造,而不必要依比例进行绘制。
[0046]
图1为本发明实施例中采用固定床反应装置的结构示意图;
[0047]
图2为实施例1制备的scr催化剂的sem图;
[0048]
图3为实施例1制备的scr催化剂的eds图像;
[0049]
图4为实施例1
‑
4所得催化剂的脱硝效率曲线;
[0050]
图5为实施例7
‑
8所得催化剂的脱硝效率曲线;
[0051]
图6为对比例1所得催化剂的脱硝效率曲线;
[0052]
图7为对比例2所得催化剂的脱硝效率曲线;
[0053]
图8为实施例1制备的scr催化剂的ftir图谱;
[0054]
图9为生物炭改性前后的ftir图谱。
具体实施方式
[0055]
下文对本发明的示例性实施例的详细描述参考了附图,该附图形成描述的一部分,在该附图中作为示例示出了本发明可实施的示例性实施例。尽管这些示例性实施例被充分详细地描述以使得本领域技术人员能够实施本发明,但应当理解可实现其他实施例且可在不脱离本发明的精神和范围的情况下对本发明作各种改变。下文对本发明的实施例的更详细的描述并不用于限制所要求的本发明的范围,而仅仅为了进行举例说明且不限制对本发明的特点和特征的描述,以提出执行本发明的最佳方式,并足以使得本领域技术人员能够实施本发明。因此,本发明的范围仅由所附权利要求来限定。
[0056]
其中,表1为各实施例实验参数。
[0057]
表1各实施例实验参数
[0058][0059]
以下实施例中,所有未具体注明的工业设备或装置均采用本领域内的常规设备或装置。所述fcc废催化剂取自安庆石化公司,类型为zsm
‑
5,主要成分为sio2和al2o3,以及一定量的cao、fe2o3、mgo、ceo2、la2o3和v2o5。其比表面积为85.74m2·
g
‑1,平均孔径为9.35mm。所述改性生物炭是由70wt%磷酸超声浸渍玉米芯1h,在105℃下干燥24h,在氮气氛围中于
600℃条件下热解1h后,投入0.1mol/l盐酸溶液中煮沸并搅拌,而后用80℃去离子水反复清洗至洗涤液呈中性,干燥后即得改性生物炭。
[0060]
其中,粉末生物炭的比表面积为1352.36m2·
g
‑1,平均孔径为5.498mm。
[0061]
通过ftir图谱,如图9所示,可以看出,改性前后生物炭的表面官能团数量和种类均发生了一定的变化。经过改性处理后的生物炭在500~1000cm
‑1范围内的吸收峰种类增加(主要为芳香族化合物c
‑
h基团),且改性后生物炭在3417cm
‑1处和1114cm
‑1处的峰强度要高于未改性前,表明改性后生物炭表面的羟基(
‑
oh)官能团和碳氧键(c
‑
o)数量增多。从而进一步增强了生物炭的低温脱硝活性,因此在负载过渡金属后制得的催化剂低温脱硝性能较原始生物炭负载后制得的催化剂更优。
[0062]
实施例1
[0063]
按2:1的比例称取改性生物炭和fcc废催化剂,进行机械掺混之后制备催化剂载体,其中改性生物炭为浓度70wt%的磷酸溶液超声浸渍1h,于105℃条件下干燥24h后600℃热解一小时制得。以硝酸锰为mn源,mn元素负载量为15%,添加去离子水配置硝酸锰溶液,将称取的改性生物炭和fcc废催化剂浸渍于硝酸锰溶液中,用玻璃棒搅拌均匀超声浸渍处理2h,取出置于105℃下干燥12h。将烘干后样品在氮气气氛下500℃焙烧2h,等炉温冷却后取出研磨至40~60目,即得本实施例的mnox/(sfcc+pcb)scr催化剂,sem、eds和ftir图像分别如图2、图3和图8所示,催化剂表面有明显的絮状颗粒物团聚,从eds谱图中可以看出,催化剂中含有大量c、o、mn元素,以及少量的al和p,且mn元素出现区域中含有o元素,由ftir图谱可以观测到存在mn
‑
o键,由此可知在mn改性复合催化剂中活性组分是以金属氧化物的形式存在的。
[0064]
采用图1所示固定床流动反应装置进行烟气脱硝性能检测,反应在以n2为平衡气,nh3为还原剂,no和o2为反应气体的模拟烟气(400ppmno+400ppmnh3+5%o2,总流量为130ml/min)的环境中进行。其中反应空速为5800h
‑1,反应温度测试区间为100℃~280℃(每隔20℃设置一个反应温度点),由可编程温度控制器控制,加热炉以5℃/min的速度升温到指定反应温度,实验中每隔反应温度点都连续监测30min。采用烟气分析仪测定反应装置入口和出口处烟气中no浓度,并在出口处设尾气处理装置,实验结果如图4所示。
[0065]
实施例2
[0066]
与实施例1的制备方法相同,不同点在于,本实施例中mn元素负载量为10wt%,将所得催化剂置于图1所示固定床流动反应装置中进行烟气脱硝性能检测,模拟烟气由no、nh3、o2、n2四种气体组成,其中no为400ppm,nh3为400ppm,o2的体积分数为5%,n2作为平衡气体,空速比为5800h
‑1,实验温度范围为100℃~280℃,实验结果如图4所示。由图可以看出,本实施例所得催化剂在100℃~160℃温度范围内,脱硝效率低于实施例1,在160℃~280℃温度范围内,脱硝效率高于实施例1,这是因为随着mn负载量的减少,催化剂表面的mnox含量也减少了,从而致使催化剂在低温时的脱硝活性下降,但随着反应温度升高,催化剂中其他活性物质开始参与催化反应,过高的mn负载量会引起团聚,堵塞催化剂的孔道,导致其脱硝效率不升反降。
[0067]
实施例3
[0068]
与实施例1的制备方法相同,不同点在于,本实施例中mn元素负载量为5wt%,将所得催化剂置于图1所示固定床流动反应装置中进行烟气脱硝性能检测,模拟烟气由no、nh3、
o2、n2四种气体组成,其中no为400ppm,nh3为400ppm,o2的体积分数为5%,n2作为平衡气体,空速比为5800h
‑1,实验温度范围为100℃~280℃,实验结果如图4所示,由图可以看出,本实施例所得催化剂在100℃~280℃之间的脱硝效率低于实施例2,催化剂表面的mnox含量进一步减少导致活性位点过少,限制脱硝效率。
[0069]
实施例4
[0070]
与实施例1的制备方法相同,不同点在于,本实施例中mn元素负载量为20wt%,将所得催化剂置于图1所示固定床流动反应装置中进行烟气脱硝性能检测,模拟烟气由no、nh3、o2、n2四种气体组成,其中no为400ppm,nh3为400ppm,o2的体积分数为5%,n2作为平衡气体,空速比为5800h
‑1,实验温度范围为100℃~280℃,实验结果如图4所示,由图可以看出,本实施例所得催化剂在100℃~280℃之间的脱硝效率高于实施例3,低于实施例1和实施例2,这是因为mn负载量过高时,其焙烧产生的mnox容易在催化剂表面产生团聚,且过多的mnox还会堵塞催化剂孔道,阻碍气体与活性点之间的反应,从而导致催化剂脱硝效率下降。
[0071]
实施例5
[0072]
与实施例1的制备方法相同,不同点在于,本实施例中催化剂焙烧温度为600℃。将所得催化剂置于图1所示固定床流动反应装置中进行烟气脱硝性能检测,模拟烟气由no、nh3、o2、n2四种气体组成,其中no为400ppm,nh3为400ppm,o2的体积分数为5%,n2作为平衡气体,空速比为5800h
‑1,实验温度范围为100℃~280℃,该催化剂的催化活性低于实施例1,这是因为焙烧温度过高导致催化剂烧结和孔结构坍塌,使催化剂比表面积下降和活性位减小,同时也会导致催化剂的活性组分晶相结构被破坏,从而导致脱硝效率下降。
[0073]
实施例6
[0074]
与实施例1的制备方法相同,不同点在于,本实施例中催化剂焙烧时间为5h。将所得催化剂置于图1所示固定床流动反应装置中进行烟气脱硝性能检测,模拟烟气由no、nh3、o2、n2四种气体组成,其中no为400ppm,nh3为400ppm,o2的体积分数为5%,n2作为平衡气体,空速比为5800h
‑1,实验温度范围为100℃~280℃,该催化剂的催化活性低于实施例1,这是因为焙烧时间过长,导致催化剂表面生成的mn金属氧化物烧结与载体相互反应,使催化剂表面的活性位点减少或催化活性下降,从而大大降低了催化剂的脱硝效率。
[0075]
实施例7
[0076]
按2:1的比例称取改性生物炭和fcc废催化剂,进行机械掺混之后制备催化剂载体。以硝酸锰为mn源,mn元素负载量为15wt%,添加去离子水配置硝酸锰溶液,将称取的改性生物炭和fcc废催化剂浸渍于硝酸锰溶液中,用玻璃棒搅拌均匀超声浸渍处理2h,取出置于105℃下蒸干。将烘干后样品在氮气气氛下500℃焙烧2h,等炉温冷却后取出研磨至40~60目,即得本实施例的mnox/(sfcc+pcb)scr催化剂。
[0077]
采用图1所示固定床流动反应装置进行烟气脱硝性能检测,反应在以n2为平衡气,nh3为还原剂,no和o2为反应气体的模拟烟气(400ppmno+400ppmnh3+5%o2,总流量为130ml/min)的环境中进行。其中反应空速为9200h
‑1,反应温度测试区间为100℃~280℃(每隔20℃设置一个反应温度点),由可编程温度控制器控制,加热炉以5℃/min的速度升温到指定反应温度,实验中每隔反应温度点都连续监测30min。采用烟气分析仪测定反应装置入口和出口处烟气中no浓度,并在出口处设尾气处理装置,实验结果如图5所示,与实施例1相比,随着反应空速的增加,催化剂脱硝效率有所下降,但是变化并不明显,这说明催化剂具有较强
的抗空速性能。
[0078]
实施例8
[0079]
按2:1的比例称取改性生物炭和fcc废催化剂,进行机械掺混之后制备催化剂载体。以硝酸锰为mn源,mn元素负载量为15wt%,添加去离子水配置硝酸锰溶液,将称取的改性生物炭和fcc废催化剂浸渍于硝酸锰溶液中,用玻璃棒搅拌均匀超声浸渍处理2h,取出置于105℃下干燥12h。将烘干后样品在氮气气氛下500℃焙烧2h,等炉温冷却后取出研磨至40~60目,即得本实施例的mnox/(sfcc+pcb)scr催化剂。
[0080]
采用图1所示固定床流动反应装置进行烟气脱硝性能检测,反应在以n2为平衡气,nh3为还原剂,no和o2为反应气体的模拟烟气(400ppmno+400ppmnh3+5%o2,总流量为130ml/min)的环境中进行。其中反应空速为28000h
‑1,反应温度测试区间为100℃~280℃(每隔20℃设置一个反应温度点),由可编程温度控制器控制,加热炉以5℃/min的速度升温到指定反应温度,实验中每隔反应温度点都连续监测30min。采用烟气分析仪测定反应装置入口和出口处烟气中no浓度,并在出口处设尾气处理装置,实验结果如图5所示,催化剂脱硝效率低于实施例1和实施例8,这是因为随着反应空速迅速增加,导致烟气与催化剂的接触时间变短,烟气中的nh3与no来不及吸附于催化剂表面的活性位上,很多活性中心未实现其作用,烟气就被排出,从而脱硝效率下降。
[0081]
实施例9
[0082]
与实施例1的制备方法相同,不同点在于,本实施例中催化剂焙烧温度为400℃。将所得催化剂置于图1所示固定床流动反应装置中进行烟气脱硝性能检测,模拟烟气由no、nh3、o2、n2四种气体组成,其中no为400ppm,nh3为400ppm,o2的体积分数为5%,n2作为平衡气体,空速比为5800h
‑1,实验温度范围为100℃~280℃,该催化剂的催化活性高于实施例5低于实施例1,这是因为温度较低时无法彻底分解硝酸锰,导致催化剂不能完全活化,因此其脱硝活性低于实施例1,但总体上相比于发生烧结和孔道结构被破坏的实施例5,其脱硝活性还是要高不少。
[0083]
实施例10
[0084]
与实施例1的制备方法相同,不同点在于,本实施例中催化剂焙烧时间为1h。将所得催化剂置于图1所示固定床流动反应装置中进行烟气脱硝性能检测,模拟烟气由no、nh3、o2、n2四种气体组成,其中no为400ppm,nh3为400ppm,o2的体积分数为5%,n2作为平衡气体,空速比为5800h
‑1,实验温度范围为100℃~280℃,该催化剂的催化活性低于实施例1高于实施例6,这是因为焙烧时间过短,焙烧不充分导致金属盐分解不完全,催化剂表面的活性物质较少和分布不均,从而其脱硝活性低于实施例1,但是相比于焙烧时间过长导致烧结的实施例6,其脱硝活性还是要高不少。
[0085]
实施例11
[0086]
与实施例1的制备方法相同,不同点在于,本实施例中催化剂焙烧时间为3h。将所得催化剂置于图1所示固定床流动反应装置中进行烟气脱硝性能检测,模拟烟气由no、nh3、o2、n2四种气体组成,其中no为400ppm,nh3为400ppm,o2的体积分数为5%,n2作为平衡气体,空速比为5800h
‑1,实验温度范围为100℃~280℃,该催化剂的催化活性低于实施例1高于实施例10,即最佳焙烧时间介于1~3h之间,当焙烧时间低于2h时,其由于焙烧不充分脱硝活性下降,而超过3h时,则会因为焙烧时间过久导致烧结,降低催化剂的脱硝活性。
[0087]
实施例12
[0088]
与实施例1的制备方法相同,不同点在于,本实施例中按3:1的比例称取改性生物炭和fcc废催化剂,进行机械掺混之后制备催化剂载体。将所得催化剂置于图1所示固定床流动反应装置中进行烟气脱硝性能检测,模拟烟气由no、nh3、o2、n2四种气体组成,其中no为400ppm,nh3为400ppm,o2的体积分数为5%,n2作为平衡气体,空速比为5800h
‑1,实验温度范围为100℃~280℃,该催化剂的催化活性在反应温度低于140℃时高于实施例1,这是因为生物炭的比表面积和孔隙率要比fcc废催化剂大,可以使所负载活性物质过渡金属mn在催化剂表面分散的更均匀,其丰富的孔隙结构还可以增强催化剂的吸附性能,因此生物炭的掺混比例越高催化剂低温脱硝活性越高。而当反应温度高于140℃时催化剂的脱硝活性低于实施例1,这是因为生物炭的导热性与热稳定性较fcc废催化剂相比要差,因此生物炭的掺混比例越高催化剂的散热性能和抗烧结性能越差,其在中高温时脱硝活性也就越低。
[0089]
实施例13
[0090]
与实施例1的制备方法相同,不同点在于,本实施例中按1:3的比例称取改性生物炭和fcc废催化剂,进行机械掺混之后制备催化剂载体。将所得催化剂置于图1所示固定床流动反应装置中进行烟气脱硝性能检测,模拟烟气由no、nh3、o2、n2四种气体组成,其中no为400ppm,nh3为400ppm,o2的体积分数为5%,n2作为平衡气体,空速比为5800h
‑1,实验温度范围为100℃~280℃,该催化剂的催化活性在反应温度低于140℃时低于实施例1,在反应温度高于140℃时催化活性高于实施例12低于实施例1,这是因为当fcc掺混比上升后催化剂载体的比表面积和孔隙率下降了,导致其负载过渡金属mn后低温脱硝效率下降,但是fcc废催化剂掺混量的增加使得催化剂的散热性能和抗烧结性能提升,同时由于fcc废催化剂中含有一定量的活性物质,也提升了催化剂的催化性能,因此在反应温度大于140℃后其脱硝效率要高于实施例12,fcc废催化剂掺混量过大后载体比表面积和孔隙度的下降引起的活性下降要大于fcc废催化剂自身带来的活性提升,致使其在反应温度大于140℃后脱硝活性低于实施例1。
[0091]
对比例1
[0092]
与实施例1的制备方法相同,不同点在于,本对比例不进行mn负载处理,即mn元素负载量为0。将所得催化剂置于图1所示固定床流动反应装置中进行烟气脱硝性能检测,模拟烟气由no、nh3、o2、n2四种气体组成,其中no为400ppm,nh3为400ppm,o2的体积分数为5%,n2作为平衡气体,空速比为5800h
‑1,实验温度范围为100℃~280℃,实验结果如图6所示,催化剂的催化活性低于实施例1,这是因为fcc废催化剂为分子筛结构,其主要成分为al2o3和sio2,在使用后,其表面结构坍塌,部分活性位点被覆盖;生物炭在100℃~280℃温度范围内主要起吸附作用,催化脱硝效率有限,负载mn后,脱硝活性中心由催化剂表面转移到mn氧化物表面,mnox在100℃~280℃温度范围内对脱硝反应具有催化性能,提升了催化剂的低温活性,提高催化剂的脱硝效率。
[0093]
对比例2
[0094]
与实施例1的制备方法相同,不同点在于,本对比例仅以改性生物炭为载体,负载mn氧化物制备催化剂。将所得催化剂置于图1所示固定床流动反应装置中进行烟气脱硝性能检测,模拟烟气由no、nh3、o2、n2四种气体组成,其中no为400ppm,nh3为400ppm,o2的体积分数为5%,n2作为平衡气体,空速比为5800h
‑1,实验温度范围为100℃~280℃,实验结果如图
7所示,催化剂的催化活性高于实施例1,这是因为改性生物炭具有发达的空隙结构与较大的比表面积,其作为载体制备mnox具有较好的分散性,制得的催化剂具有较多的活性位点,在催化脱硝反应中表现出较高的活性,而fcc废催化剂在使用后,其表面的孔结构在使用过程中发生坍塌或填充,孔隙率和比表面积有所下降,随着fcc废催化剂的加入,复合载体的比表面积与孔隙大小降低,使mn在负载时分散度下降,表面活性位点减少,从而导致脱硝效率下降。
[0095]
上述实施例仅为清楚的说明本发明的原理及功效,而并非对实施方式进行限制。本领域技术人员皆可在本发明技术构思范围内做各种改动或修改,这里无需也无法对所有的实施方式予以穷举,这些等价形式同样应当视为本发明所公开内容,仍属于本发明权利所限定的范围。