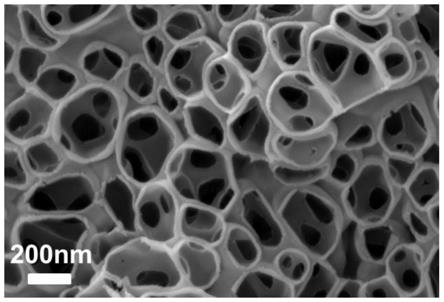
1.本发明属于碳材料合成技术领域,具体涉及一种金属原子负载氮掺杂多孔碳材料及其超组装制备方法。
背景技术:2.多孔材料具有优良的孔道结构、极大的比表面积以及良好的机械性能,使其在识别分离、催化合成、军事工程、生物技术等多领域具有广泛的应用前景。在各类碳质材料中,多孔碳材料具有高度发达的孔隙结构、大的比表面积和优异的导电性,并且制备多孔碳材料的原材料来源广泛、价格低廉,可进行大规模的生产,因此被广泛应用于能源存储与转化、催化和大分子吸附等诸多领域。
3.金属单原子负载基体材料最初出现将催化研究的体系深入到了一个更加微观的尺度。其由于其超小的尺寸而具有许多独特的催化性能,逐渐成为近年来的研究热点,特别是通过将金属单原子负载于碳载体表面的方法,有效阻止了金属单原子的聚集,引起了广大科研工作者的广泛关注。金属单原子负载的多孔碳材料由于其金属组分尺寸远小于普通金属颗粒而具有很多独特的性能:急剧增大的表面自由能、不饱和的配位环境、金属
‑
载体之间的相互作用等,这些特性使金属单原子负载的多孔碳材料展现出了卓越的催化活性及选择性。然而,其性能决定应用远远不止于电催化领域,最近报道其可用于锂金属负极均匀沉积和锂硫电池硫正极催化等方面。制约其制备难点在于金属原子及其易聚集,所以选择可以加强与单原子之间相互作用的碳载体以防止单原子聚集是该领域面临的重大挑战。
技术实现要素:4.本发明是为了解决上述问题而进行的,目的在于提供一种金属原子负载氮掺杂多孔碳材料及其超组装制备方法,不仅制备成本低,步骤简便,而且稳定性好,毒性小,适用于大规模工业化生产。
5.本发明提供了一种金属原子负载氮掺杂多孔碳材料的超组装制备方法,具有这样的特征,包括以下步骤:步骤s1,在饱和盐溶液中加入金属盐、碳源前驱体、氮源前驱体,溶解后形成前驱体溶液;步骤s2,将所述前驱体溶液先使用液氮快速冷冻,再迅速放入冷冻干燥机中完全干燥成固体前驱体;步骤s3,将所述固体前驱体在惰性气体下于500℃~600℃热解0.5h~2h,再850℃~950℃热解2h~3h,冷却获得黑色固体;步骤s4,将所述黑色固体放入硫酸溶液中进行蚀刻,干燥后在850℃~950℃下热解2h~3h,得到金属原子负载氮掺杂多孔碳材料,其中,所述金属盐与所述氮源前驱体的摩尔比为1:50
‑
1:100。
6.在本发明提供的金属原子负载氮掺杂多孔碳材料的超组装制备方法中,还可以具有这样的特征:其中,金属盐为金属氯化盐或金属硝酸盐。
7.在本发明提供的金属原子负载氮掺杂多孔碳材料的超组装制备方法中,还可以具有这样的特征:其中,碳源前驱体为糖类化合物。
8.在本发明提供的金属原子负载氮掺杂多孔碳材料的超组装制备方法中,还可以具
有这样的特征:其中,糖类化合物为葡萄糖、蔗糖或琼脂糖中的任意一种或几种。
9.在本发明提供的金属原子负载氮掺杂多孔碳材料的超组装制备方法中,还可以具有这样的特征:其中,氮源前驱体为氰胺类化合物。
10.在本发明提供的金属原子负载氮掺杂多孔碳材料的超组装制备方法中,还可以具有这样的特征:其中,氰胺类化合物为双氰胺或三聚氰胺。
11.在本发明提供的金属原子负载氮掺杂多孔碳材料的超组装制备方法中,还可以具有这样的特征:其中,金属盐为fecl3·
6h2o、cocl2·
6h2o、cucl2·
2h2o、ni(no3)2·
6h2o或mn(no3)2·
6h2o中的任一种。
12.在本发明提供的金属原子负载氮掺杂多孔碳材料的超组装制备方法中,还可以具有这样的特征:其中,饱和盐溶液为氯化钠、氯化钾或氯化锌中的任意一种的饱和溶液。
13.在本发明提供的金属原子负载氮掺杂多孔碳材料的超组装制备方法中,还可以具有这样的特征:其中,步骤s2中,将前驱体溶液在冷冻干燥机中于≤
‑
50℃干燥12小时~48小时干燥成固体前驱体。
14.本发明还提供了一种金属原子负载氮掺杂多孔碳材料,具有这样的特征,由金属原子负载氮掺杂多孔碳材料的超组装制备方法制备得到。
15.发明的作用与效果
16.根据本发明提供的金属原子负载氮掺杂多孔碳材料及其超组装制备方法,该多孔碳材料以糖类为碳源,氰胺类为氮源,盐为模板,金属氯化盐或硝酸盐水合物为金属原子源来制备。该多孔碳材料利用盐为模板进行使糖类进行组装成为连续的多孔结构,氰胺类热解形成的氮配位与金属原子进行配位,再经过去模板、酸刻蚀和二次热解的方法制备。该材料的优点在于:孔道连续性好,制备原料正本低廉,可负载金属原子种类多样等,可用于电催化和电极材料等领域。
17.现有技术相比,本发明所提供的制备方法具有如下优点及突出性的技术效果:原料有糖类、氰胺类、常见金属盐类水合物均成本较低;制备方法简单,适用性广,适合大规模生产;溶剂采用水,具有毒性小、价格便宜的特点。本发明所能提供的金属单原子负载的氮掺杂多孔碳材料制备方法适用于大规模工业生产,应用范围涉及催化、超级电容器和电池等领域。
附图说明
18.图1是本发明的实施例1制备的钴单原子负载的氮掺杂多孔碳材料的扫描电子显微镜图(sem);
19.图2是本发明的实施例1制备的钴单原子负载的氮掺杂多孔碳材料的透射电子显微镜区域元素扫描图(tem
‑
mapping);
20.图3是本发明的实施例1制备的钴单原子负载的氮掺杂多孔碳材料的x射线衍射图;以及
21.图4是本发明的实施例1制备的钴单原子负载的氮掺杂多孔碳材料的x射线光电子能谱图。
具体实施方式
22.为了使本发明实现的技术手段、创作特征、达成目的与功效易于明白了解,以下结合实施例及附图对本发明一种金属原子负载氮掺杂多孔碳材料及其超组装制备方法作具体阐述。
23.本发明的实施例中的方法如无特别说明均为常规方法,本发明的实施例中的原材料如无特别说明均能从公开商业途径获得。
24.本发明的金属原子负载氮掺杂多孔碳材料的超组装制备方法,包括以下步骤:
25.步骤s0,饱和盐模板水溶液的配制:选用氯化钠、氯化钾或氯化锌中的一种或几种作为盐类模板剂,然后将相应的盐类模板剂按照饱和溶解度计算出一定量的水需要的相应的盐的质量,配制成饱和盐溶液作为饱和盐模板水溶液。例如,44ml去离子水配制氯化钠的饱和溶液,氯化钠用量为16g。由于氯化钠等盐模板为易于使用的模板,既环保又易于用水除去并可以通过重结晶回收。
26.步骤s1,前驱体溶液的配制:在饱和盐溶液中加入金属盐、碳源前驱体、氮源前驱体,溶解后形成前驱体溶液。其中,金属盐与氮源前驱体的摩尔比为1:50
‑
1:100。
27.金属盐为金属氯化盐或金属硝酸盐的水合物。例如,金属盐可以为fecl3·
6h2o、cocl2·
6h2o、cucl2·
2h2o、ni(no3)2·
6h2o、mn(no3)2·
6h2o中的任一种。
28.碳源前驱体选择为成本较低的糖类化合物,包括葡萄糖、蔗糖和琼脂糖等,可以是这些物质中的任意一种或几种。氮源前驱体选择富含氮元素的氰胺类化合物,例如双氰胺或三聚氰胺等。
29.具体操作为:
30.称取一定量的金属氯化或硝酸盐水合物、2g糖类和一定量的氰胺类加入到中配制好的饱和盐模板溶液中,由于氰胺类化合物在室温下溶解度较低,可用加热超声使其溶解。金属氯化盐或金属硝酸盐水合物与氰胺类化合物两者的摩尔比为1:50
‑
1:100。
31.步骤s2,前驱体溶液的迅速冷冻和冷冻干燥:将前驱体溶液先使用液氮快速冷冻,再迅速放入冷冻干燥机中完全干燥成固体前驱体。冷冻干燥温度为
‑
50℃及以下,时间为12小时至48小时,可根据溶剂量调整。
32.步骤s3,固体前驱体第一次热解:将固体前驱体在惰性气体下于500℃~600℃热解0.5h~2h,再850℃~950℃热解2h~3h,冷却获得黑色固体。热解惰性气体可包括氮气或氩气等。
33.具体操作为:将固体前驱体放入瓷舟中,在管式炉中,惰性气体下,先每分钟5℃的升温速度升至500℃~600℃热解0.5h~2h小时,再每分钟4℃的升温速度升至850℃~950℃保温2h~3h,冷却至室温,得到黑色固体。
34.步骤s4,前驱体的酸刻蚀和第二次热解:将黑色固体放入硫酸溶液中进行蚀刻,干燥后在850℃~950℃下热解2h~3h,得到金属原子负载氮掺杂多孔碳材料。
35.具体操作为:将步骤s3中获得的黑色固体放入到0.5m硫酸溶液中进行刻蚀,刻蚀掉团聚形成纳米颗粒的金属,在室温条件下刻蚀6个小时,再60℃烘干。烘干后的碳材料再850℃~950℃保温2h~3h,去除其他杂质,冷却至室温获得最终产物。
36.根据步骤s1中金属盐的种类,得到的碳材料中的金属单原子为铁、钴、铜、镍或锰原子。
37.实施例1:
38.将16g氯化钠溶于44ml去离子水中,配制成饱和氯化钠溶液,然后加入113mgcocl2·
6h2o,2g葡萄糖,2g双氰胺,形成均匀的粉红色溶液,将其放入液氮中迅速冷冻,然后迅速转移到
‑
50℃的冷冻干燥机中冷冻干燥48小时,然后将获得的固体转移到陶瓷坩埚中进行热解,在管式炉中,氮气下,先每分钟5℃的升温速度升温至550℃热解1小时,再每分钟3℃的升温速度至900℃热解2小时,冷却至室温后获得黑色粉末。黑色粉末用0.5m硫酸在室温下刻蚀6小时,用去离子水洗涤,干燥后再900℃热解2小时,得到黑色钴单原子负载的氮掺杂多孔碳材料。
39.对该实施例钴单原子负载的氮掺杂多孔碳材料进行扫描电子显微镜检测、透射电子显微镜区域元素扫描检测、x射线衍射检测及x射线光电子能谱检测,检测结果见图1~4。
40.图1是本发明的实施例1制备的钴单原子负载的氮掺杂多孔碳材料的扫描电子显微镜图(sem)。
41.从图1可知,制备的钴单原子负载的氮掺杂材料具有连续的多孔结构,并且孔分布均匀。
42.图2是本发明的实施例1制备的钴单原子负载的氮掺杂多孔碳材料的透射电子显微镜区域元素扫描图(tem
‑
mapping)。其中,图2中的a是暗场条件下该材料的tem图片;b是碳元素的分布情况图;c是氮元素的分布情况图;d是钴元素的分布情况图。
43.从图2可知,氮元素和钴元素已成功负载和掺杂于多孔碳材料之中,各元素在材料中分布均匀。
44.图3是本发明的实施例1制备的钴单原子负载的氮掺杂多孔碳材料的x射线衍射图。
45.从图3可知,制备的该多孔碳材料只包含碳的衍射峰,未显现出钴纳米颗粒的峰,说明制备的碳材料中的钴是以原子级分布的,并未聚集成大的纳米颗粒。
46.图4是本发明的实施例1制备的钴单原子负载的氮掺杂多孔碳材料的x射线光电子能谱图。其中,图4中的a是x射线光电子能谱全谱图以及各元素含量图;b是氮元素的x射线光电子能谱图;c是钴元素的x射线光电子能谱图。
47.从图4可知,氮元素以四种不同的形式掺杂进入制备的多孔碳材料之中,掺杂形式多样为不同的应用提供了条件。而钴元素的x射线光电子能谱曲线噪声很大,表明钴元素含量少且不聚集,以原子形式存在其中。
48.实施例2:
49.将16g氯化钠溶于44ml去离子水中,配制成饱和氯化钠溶液,然后加入128mgfecl3·
6h2o,2g蔗糖,2g双氰胺,形成均匀的橙色溶液,将其放入液氮中迅速冷冻,然后迅速转移到
‑
50℃的冷冻干燥机中冷冻干燥48小时,然后将获得的固体转移到陶瓷坩埚中进行热解,在管式炉中,氮气下,先每分钟5℃的升温速度升温至550℃热解1小时,再每分钟3℃的升温速度至900℃热解2小时,冷却至室温后获得黑色粉末。黑色粉末用0.5m硫酸在室温下刻蚀6小时,用去离子水洗涤,干燥后再900℃热解2小时,得到黑色铁单原子负载的氮掺杂多孔碳材料。
50.实施例3:
51.将15g氯化钾溶于44ml去离子水中,配制成饱和氯化钾溶液,然后加入
55mgcucl2·
2h2o,2g蔗糖,2g三聚氰胺,形成均匀的蓝绿色溶液,将其放入液氮中迅速冷冻,然后迅速转移到
‑
50℃的冷冻干燥机中冷冻干燥48小时,然后将获得的固体转移到陶瓷坩埚中进行热解,在管式炉中,氮气下,先每分钟5℃的升温速度升温至550℃热解1小时,再每分钟3℃的升温速度至900℃热解2小时,冷却至室温后获得黑色粉末。黑色粉末用0.5m硫酸在室温下刻蚀6小时,用去离子水洗涤,干燥后再900℃热解2小时,得到黑色铜单原子负载的氮掺杂多孔碳材料。
52.实施例4:
53.将15g氯化钾溶于44ml去离子水中,配制成饱和氯化钾溶液,然后加入92mgni(no3)2·
6h2o,2g蔗糖,2g三聚氰胺,形成均匀的绿色溶液,将其放入液氮中迅速冷冻,然后迅速转移到
‑
50℃的冷冻干燥机中冷冻干燥48小时,然后将获得的固体转移到陶瓷坩埚中进行热解,在管式炉中,氮气下,先每分钟5℃的升温速度升温至550℃热解1小时,再每分钟3℃的升温速度至900℃热解2小时,冷却至室温后获得黑色粉末。黑色粉末用0.5m硫酸在室温下刻蚀6小时,用去离子水洗涤,干燥后再900℃热解2小时,得到黑色镍单原子负载的氮掺杂多孔碳材料。
54.实施例5:
55.将19g氯化锌溶于44ml去离子水中,配制成饱和氯化钾溶液,然后加入90mgmn(no3)2·
6h2o,2g蔗糖,2g三聚氰胺,形成均匀的淡黄色溶液,将其放入液氮中迅速冷冻,然后迅速转移到
‑
50℃的冷冻干燥机中冷冻干燥48小时,然后将获得的固体转移到陶瓷坩埚中进行热解,在管式炉中,氮气下,先每分钟5℃的升温速度升温至550℃热解1小时,再每分钟3℃的升温速度至900℃热解2小时,冷却至室温后获得黑色粉末。黑色粉末用0.5m硫酸在室温下刻蚀6小时,用去离子水洗涤,干燥后再900℃热解2小时,得到黑色锰单原子负载的氮掺杂多孔碳材料。
56.实施例的作用与效果
57.根据本发明的实施例提供的金属原子负载氮掺杂多孔碳材料及其超组装制备方法,该多孔碳材料以糖类为碳源,氰胺类为氮源,盐为模板,金属氯化盐或硝酸盐水合物为金属原子源来制备。该多孔碳材料利用盐为模板进行使糖类进行组装成为连续的多孔结构,氰胺类热解形成的氮配位与金属原子进行配位,再经过去模板、酸刻蚀和二次热解的方法制备。该材料的优点在于:孔道连续性好,制备原料正本低廉,可负载金属原子种类多样等,可用于电催化和电极材料等领域。
58.现有技术相比,本发明的实施例所提供的制备方法具有如下优点及突出性的技术效果:原料有糖类、氰胺类、常见金属盐类水合物均成本较低;制备方法简单,适用性广,适合大规模生产;溶剂采用水,具有毒性小、价格便宜的特点。本发明的实施例所能提供的金属单原子负载的氮掺杂多孔碳材料制备方法适用于大规模工业生产,应用范围涉及催化、超级电容器和电池等领域。
59.上述实施方式为本发明的优选案例,并不用来限制本发明的保护范围。对于本领域技术人员来说,本技术可以有各种更改和变化。凡在本技术的精神和原理之内所作的任何修改、等同替换、改进等,均应包含在本技术的权利要求范围之内。