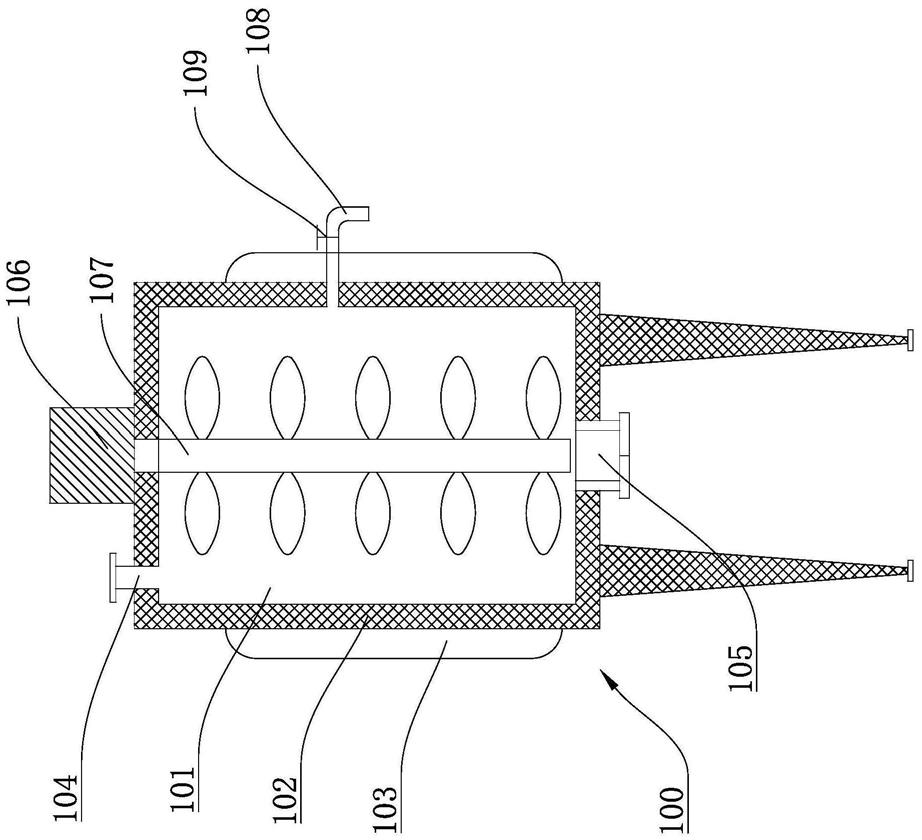
1.本发明属于胶水处理技术领域,尤其涉及一种胶水沉积液渣分离方法。
背景技术:2.板材涂胶好后,橡胶辊上会有大量胶水,即白乳胶,白乳胶/是醋酸乙烯单体在引发剂作用下经聚合反应而制得的一种热塑性粘合剂,其主要成分为聚醋酸乙烯酯。产线需要定期清洗橡胶辊,清洗后,会得到白乳胶和水的混合液,混合液不能直接排放。现有技术中的企业往往需要交给专门的环保处理单位进行处理,处理价格十分高昂,导致生产成本较高。
3.例如,中国发明专利申请公开了一种废弃胶水的综合处理方法[申请号:201910333721.7],该发明专利申请包括以下步骤:1收集来自洗涤池的废弃胶水并输送至化学反应锅内,然后往化学反应锅中加入废弃胶水总量10-12%的氯化物,开启搅拌器搅拌2-3min,然后静置4h以上;2按照絮凝剂与废弃胶水的用量比为150-160g:1m3,在上述化学反应锅中加入絮凝剂,再次搅拌5-8min,静置36h以上,化学反应锅内的物料出现分层,上层为水层,下层为沉淀渣;3将水层通过水泵抽出排入污水管道,将沉淀渣经出渣槽送入沉淀物处理箱内,同时往沉淀渣中加入固化剂并搅拌均匀,然后采用压滤机对沉淀渣进行脱水处理得到渣块,最后将渣块烘干。
[0004]
该发明专利申请具有对废弃胶水中的胶分子产生分解催化作用和分子粉末的絮凝,能够有效的净化分离出无害化水层及易处理的沉淀渣的优势,但其不能适用于主要成分为聚醋酸乙烯酯的白乳胶,故仍未解决上述问题。
技术实现要素:[0005]
本发明的目的是针对上述问题,提供一种可使胶水有效沉积,有效降低了企业生产成本的胶水沉积液渣分离方法。
[0006]
为达到上述目的,本发明采用了下列技术方案:
[0007]
一种胶水沉积液渣分离方法,包括以下步骤:
[0008]
步骤一:将混有胶水的待分离混合液导入搅拌桶内;
[0009]
步骤二:向搅拌桶内加入预处理剂并启动搅拌,混合5-10min;
[0010]
步骤三:再在搅拌条件下向搅拌桶内加入处理剂,加热至50-70℃,搅拌20-40min,得到处理后的混合物;
[0011]
步骤四:将步骤三中得到的处理后的混合物转移至分离设备中进行固液分离,分离得到的固体物质即为胶水沉积后形成的固废,进行危废处理。
[0012]
在上述的胶水沉积液渣分离方法中,所述预处理剂包括质量份数分别为6-10份的硫酸化蓖麻油、2-4份的乙醇和0.1-0.5份的氯化钠。
[0013]
在上述的胶水沉积液渣分离方法中,所述预处理剂包括质量份数分别为8份的硫酸化蓖麻油、3份的乙醇和0.3份的氯化钠。
[0014]
在上述的胶水沉积液渣分离方法中,所述步骤二中在加入预处理剂前还包括预热待分离混合液的步骤,预热温度为40-50℃。
[0015]
在上述的胶水沉积液渣分离方法中,所述处理剂包括聚合氯化铝、破乳剂、聚丙烯酰胺、氢氧化钠和硝酸钡。
[0016]
在上述的胶水沉积液渣分离方法中,所述处理剂包括质量份数分别为10-20份的聚合氯化铝、50-70份的破乳剂、0.5-2份的聚丙烯酰胺、10-20份的氢氧化钠和5-15份的硝酸钡。
[0017]
在上述的胶水沉积液渣分离方法中,所述处理剂包括质量份数分别为15份的聚合氯化铝、60份的破乳剂、1份的聚丙烯酰胺、15份的氢氧化钠和10份的硝酸钡。
[0018]
在上述的胶水沉积液渣分离方法中,所述搅拌桶包括内部具有搅拌空间的桶体,所述桶体外具有加热夹套,桶体上端具有进料口,下端具有出料口,所述进料口和出料口均与搅拌空间相连通,搅拌电机固定设置在桶体的顶端,搅拌杆一端驱动连接在搅拌电机上,另一端延伸至搅拌空间内,所述桶体侧面还设有与搅拌空间相连通的取样口,截止阀设置在取样口上并切换取样口处于开启状态或关闭状态。
[0019]
在上述的胶水沉积液渣分离方法中,所述分离设备包括壳体,所述壳体内设有用于固液分离的旋转分离桶,所述旋转分离桶内设有分离空腔,固定连接在壳体上的驱动电机与旋转分离桶驱动连接,进料管道固定连接在壳体上且一端延伸至旋转分离桶内并与分离空腔相连通,还包括刮壁组件,所述刮壁组件一端固定在壳体上,另一端延伸贴合在旋转分离桶的内侧壁上。
[0020]
在上述的胶水沉积液渣分离方法中,所述刮壁组件包括固定设置在壳体顶部的刮壁电机,所述旋转分离桶与刮壁电机外壁转动密封连接,刮壁电机的输出轴一端延伸至分离空腔内且固定连接有刮板,所述刮板远离输出轴的一端延伸贴合至旋转分离桶的内侧壁上,且启动驱动电机和刮壁电机可使刮板与旋转分离桶的内侧壁之间发生相对位移。
[0021]
与现有的技术相比,本发明的优点在于:
[0022]
1、本发明利用预处理剂进行预处理后,再加入处理剂促使胶水固化沉积,处理方法简单,产生该胶水混合物的企业可利用该方法自行处理,无需交给专门的环保处理单位进行处理,有效降低了企业的生产成本。
[0023]
2、本发明在加入预处理剂前还进行了预热处理,进一步提高了沉积效果。
[0024]
3、本发明的分离设备还包括一刮壁组件,可在分离过程中及时的刮下贴合在旋转分离桶内壁上的固体物质,有效的提高了分离效率。
附图说明
[0025]
图1是本发明的结构框图;
[0026]
图2是搅拌桶的结构示意图;
[0027]
图3是分离设备的结构示意图;
[0028]
图中:搅拌桶100、搅拌空间101、桶体102、加热夹套103、进料口104、出料口105、搅拌电机106、搅拌杆107、取样口108、分离设备200、壳体201、旋转分离桶202、分离空腔203、驱动电机204、进料管道205、括刮壁组件206、刮壁电机207、输出轴208、刮板209。
具体实施方式
[0029]
下面结合附图和具体实施方式对本发明做进一步详细的说明。
[0030]
实施例1
[0031]
本实施例提供一种胶水沉积液渣分离方法,包括以下步骤:
[0032]
步骤一:将混有胶水的待分离混合液导入搅拌桶100内;
[0033]
步骤二:预热至40℃,再向搅拌桶100内加入预处理剂并启动搅拌,混合5min;
[0034]
步骤三:再在搅拌条件下向搅拌桶100内加入处理剂,加热至50℃,搅拌20min,得到处理后的混合物;
[0035]
步骤四:将步骤三中得到的处理后的混合物转移至分离设备200中进行固液分离,分离得到的固体物质即为胶水沉积后形成的固废,进行危废处理。
[0036]
其中,预处理剂包括质量份数分别为6份的硫酸化蓖麻油、4份的乙醇和0.5份的氯化钠,预处理剂的加入量为待分离混合液总质量的0.7%;处理剂包括质量份数分别为10份的聚合氯化铝、70份的破乳剂、2份的聚丙烯酰胺、20份的氢氧化钠和15份的硝酸钡,处理剂的加入量为待分离混合液总质量的1.3%。
[0037]
结合图1和图2所示,所述搅拌桶100包括内部具有搅拌空间101的桶体102,所述桶体102外具有加热夹套103,桶体102上端具有进料口104,下端具有出料口105,所述进料口104和出料口105均与搅拌空间101相连通,搅拌电机106固定设置在桶体102的顶端,搅拌杆107一端驱动连接在搅拌电机106上,另一端延伸至搅拌空间101内,所述桶体102侧面还设有与搅拌空间101相连通的取样口108,截止阀109设置在取样口108上并切换取样口108处于开启状态或关闭状态。
[0038]
使用时,混有胶水的待分离混合液通过进料口104进入桶体102内,加热夹套103可对桶体102内的待分离混合液进行加热,加入预处理剂后启动搅拌电机106带动搅拌杆107转动以实现混合均匀,再在搅拌状态下加入处理剂,在处理过程中可通过取样口108取样观测。处理完成后,处理后的混合物通过截止阀109放出。
[0039]
结合图1和图3所示,所述分离设备200包括壳体201,所述壳体201内设有用于固液分离的旋转分离桶202,所述旋转分离桶202内设有分离空腔203,固定连接在壳体201上的驱动电机204与旋转分离桶202驱动连接,进料管道205固定连接在壳体201上且一端延伸至旋转分离桶202内并与分离空腔203相连通,还包括刮壁组件206,所述刮壁组件206一端固定在壳体201上,另一端延伸贴合在旋转分离桶202的内侧壁上。
[0040]
具体的说,所述刮壁组件206包括固定设置在壳体201顶部的刮壁电机207,所述旋转分离桶202与刮壁电机207外壁转动密封连接,刮壁电机207的输出轴208一端延伸至分离空腔203内且固定连接有刮板209,所述刮板209远离输出轴208的一端延伸贴合至旋转分离桶202的内侧壁上,且启动驱动电机204和刮壁电机207可使刮板209与旋转分离桶202的内侧壁之间发生相对位移。
[0041]
使用时,处理后的混合物通过进料管道205进入至旋转分离桶202的分离空腔203内。启动驱动电机204使得旋转分离桶202发生旋转,旋转分离桶202采用的为现有技术中类似旋分筛或甩滤机结构,即侧壁上设有小孔或贴合有滤布,以使得旋转过程中分离空腔203内的液体排出,而固体被旋转分离桶202的侧壁阻挡,但固体累计过多会导致分离孔被大量堵塞,分离效率慢。故设置一个刮壁组件206,启动驱动电机204和刮壁电机207可使刮板209
与旋转分离桶202的内侧壁之间发生相对位移,即刮壁电机207和驱动电机204在驱动转速上有略微的差异,使得刮板209可持续刮除旋转分离桶202的侧壁上的固体。故本发明的分离设备还包括一刮壁组件,可在分离过程中及时的刮下贴合在旋转分离桶内壁上的固体物质,有效的提高了分离效率。
[0042]
实施例2
[0043]
本实施例提供一种胶水沉积液渣分离方法,包括以下步骤:
[0044]
步骤一:将混有胶水的待分离混合液导入搅拌桶100内;
[0045]
步骤二:预热至50℃,再向搅拌桶100内加入预处理剂并启动搅拌,混合10min;
[0046]
步骤三:再在搅拌条件下向搅拌桶100内加入处理剂,加热至70℃,搅拌40min,得到处理后的混合物;
[0047]
步骤四:将步骤三中得到的处理后的混合物转移至分离设备200中进行固液分离,分离得到的固体物质即为胶水沉积后形成的固废,进行危废处理。
[0048]
其中,预处理剂包括质量份数分别为10份的硫酸化蓖麻油、2份的乙醇和0.1份的氯化钠,预处理剂的加入量为待分离混合液总质量的0.7%;处理剂包括质量份数分别为20份的聚合氯化铝、50份的破乳剂、0.5份的聚丙烯酰胺、10份的氢氧化钠和5份的硝酸钡,处理剂的加入量为待分离混合液总质量的1.3%。
[0049]
搅拌桶100和分离设备200的具体结构与实施例1相同,故在此不在赘述。
[0050]
实施例3
[0051]
本实施例提供一种胶水沉积液渣分离方法,包括以下步骤:
[0052]
步骤一:将混有胶水的待分离混合液导入搅拌桶100内;
[0053]
步骤二:预热至45℃,再向搅拌桶100内加入预处理剂并启动搅拌,混合8min;
[0054]
步骤三:再在搅拌条件下向搅拌桶100内加入处理剂,加热至60℃,搅拌30min,得到处理后的混合物;
[0055]
步骤四:将步骤三中得到的处理后的混合物转移至分离设备200中进行固液分离,分离得到的固体物质即为胶水沉积后形成的固废,进行危废处理。
[0056]
其中,预处理剂包括质量份数分别为8份的硫酸化蓖麻油、3份的乙醇和0.3份的氯化钠,预处理剂的加入量为待分离混合液总质量的0.7%;处理剂包括质量份数分别为15份的聚合氯化铝、60份的破乳剂、1份的聚丙烯酰胺、15份的氢氧化钠和10份的硝酸钡,处理剂的加入量为待分离混合液总质量的1.3%。
[0057]
搅拌桶100和分离设备200的具体结构与实施例1相同,故在此不在赘述。
[0058]
对比例1
[0059]
本对比例提供一种胶水沉积液渣分离方法,包括以下步骤:
[0060]
步骤一:将混有胶水的待分离混合液导入搅拌桶100内;
[0061]
步骤二:向搅拌桶100内加入预处理剂并启动搅拌,混合8min;
[0062]
步骤三:再在搅拌条件下向搅拌桶100内加入处理剂,加热至60℃,搅拌30min,得到处理后的混合物;
[0063]
步骤四:将步骤三中得到的处理后的混合物转移至分离设备200中进行固液分离,分离得到的固体物质即为胶水沉积后形成的固废,进行危废处理。
[0064]
其中,预处理剂包括质量份数分别为8份的硫酸化蓖麻油、3份的乙醇和0.3份的氯
化钠,预处理剂的加入量为待分离混合液总质量的0.7%;处理剂包括质量份数分别为15份的聚合氯化铝、60份的破乳剂、1份的聚丙烯酰胺、15份的氢氧化钠和10份的硝酸钡,处理剂的加入量为待分离混合液总质量的1.3%。
[0065]
搅拌桶100和分离设备200的具体结构与实施例1相同,故在此不在赘述。
[0066]
对比例2
[0067]
本对比例提供一种胶水沉积液渣分离方法,包括以下步骤:
[0068]
步骤一:将混有胶水的待分离混合液导入搅拌桶100内;
[0069]
步骤二:预热至60℃,再向搅拌桶100内加入预处理剂并启动搅拌,混合8min;
[0070]
步骤三:再在搅拌条件下向搅拌桶100内加入处理剂,加热至60℃,搅拌30min,得到处理后的混合物;
[0071]
步骤四:将步骤三中得到的处理后的混合物转移至分离设备200中进行固液分离,分离得到的固体物质即为胶水沉积后形成的固废,进行危废处理。
[0072]
其中,预处理剂包括质量份数分别为8份的硫酸化蓖麻油、3份的乙醇和0.3份的氯化钠,预处理剂的加入量为待分离混合液总质量的0.7%;处理剂包括质量份数分别为15份的聚合氯化铝、60份的破乳剂、1份的聚丙烯酰胺、15份的氢氧化钠和10份的硝酸钡,处理剂的加入量为待分离混合液总质量的1.3%。
[0073]
搅拌桶100和分离设备200的具体结构与实施例1相同,故在此不在赘述。
[0074]
对比例3
[0075]
本对比例提供一种胶水沉积液渣分离方法,包括以下步骤:
[0076]
步骤一:将混有胶水的待分离混合液导入搅拌桶100内;
[0077]
步骤二:预热至45℃,再向搅拌桶100内加入预处理剂并启动搅拌,混合8min;
[0078]
步骤三:再在搅拌条件下向搅拌桶100内加入处理剂,加热至60℃,搅拌30min,得到处理后的混合物;
[0079]
步骤四:将步骤三中得到的处理后的混合物转移至分离设备200中进行固液分离,分离得到的固体物质即为胶水沉积后形成的固废,进行危废处理。
[0080]
其中,预处理剂包括质量份数分别为8份的硫酸化蓖麻油和3份的乙醇,预处理剂的加入量为待分离混合液总质量的0.7%;处理剂包括质量份数分别为15份的聚合氯化铝、60份的破乳剂、1份的聚丙烯酰胺、15份的氢氧化钠和10份的硝酸钡,处理剂的加入量为待分离混合液总质量的1.3%。
[0081]
搅拌桶100和分离设备200的具体结构与实施例1相同,故在此不在赘述。
[0082]
对比例4
[0083]
本对比例提供一种胶水沉积液渣分离方法,包括以下步骤:
[0084]
步骤一:将混有胶水的待分离混合液导入搅拌桶100内;
[0085]
步骤二:预热至45℃,再向搅拌桶100内加入预处理剂并启动搅拌,混合8min;
[0086]
步骤三:再在搅拌条件下向搅拌桶100内加入处理剂,加热至60℃,搅拌30min,得到处理后的混合物;
[0087]
步骤四:将步骤三中得到的处理后的混合物转移至分离设备200中进行固液分离,分离得到的固体物质即为胶水沉积后形成的固废,进行危废处理。
[0088]
其中,预处理剂包括质量份数分别为8份的硫酸化蓖麻油、3份的乙醇和3份的氯化
钠,预处理剂的加入量为待分离混合液总质量的0.7%;处理剂包括质量份数分别为15份的聚合氯化铝、60份的破乳剂、1份的聚丙烯酰胺、15份的氢氧化钠和10份的硝酸钡,处理剂的加入量为待分离混合液总质量的1.3%。
[0089]
搅拌桶100和分离设备200的具体结构与实施例1相同,故在此不在赘述。
[0090]
对比例5
[0091]
本对比例提供一种胶水沉积液渣分离方法,包括以下步骤:
[0092]
步骤一:将混有胶水的待分离混合液导入搅拌桶100内;
[0093]
步骤二:预热至45℃,再向搅拌桶100内加入预处理剂并启动搅拌,混合8min;
[0094]
步骤三:再在搅拌条件下向搅拌桶100内加入处理剂,加热至60℃,搅拌30min,得到处理后的混合物;
[0095]
步骤四:将步骤三中得到的处理后的混合物转移至分离设备200中进行固液分离,分离得到的固体物质即为胶水沉积后形成的固废,进行危废处理。
[0096]
其中,预处理剂包括质量份数分别为0.3份的氯化钠,预处理剂的加入量为待分离混合液总质量的0.7%;处理剂包括质量份数分别为15份的聚合氯化铝、60份的破乳剂、1份的聚丙烯酰胺、15份的氢氧化钠和10份的硝酸钡,处理剂的加入量为待分离混合液总质量的1.3%。
[0097]
搅拌桶100和分离设备200的具体结构与实施例1相同,故在此不在赘述。
[0098]
对比例6
[0099]
本对比例提供一种胶水沉积液渣分离方法,包括以下步骤:
[0100]
步骤一:将混有胶水的待分离混合液导入搅拌桶100内;
[0101]
步骤二:预热至45℃,再向搅拌桶100内加入预处理剂并启动搅拌,混合8min;
[0102]
步骤三:再在搅拌条件下向搅拌桶100内加入处理剂,加热至60℃,搅拌30min,得到处理后的混合物;
[0103]
步骤四:将步骤三中得到的处理后的混合物转移至分离设备200中进行固液分离,分离得到的固体物质即为胶水沉积后形成的固废,进行危废处理。
[0104]
其中,预处理剂包括质量份数分别为8份的硫酸化蓖麻油、3份的乙醇和0.3份的氯化钠,预处理剂的加入量为待分离混合液总质量的0.7%;处理剂包括质量份数分别为15份的聚合氯化铝、60份的破乳剂、1份的聚丙烯酰胺和15份的氢氧化钠,处理剂的加入量为待分离混合液总质量的1.3%。
[0105]
搅拌桶100和分离设备200的具体结构与实施例1相同,故在此不在赘述。
[0106]
对比例6
[0107]
本对比例提供一种胶水沉积液渣分离方法,包括以下步骤:
[0108]
步骤一:将混有胶水的待分离混合液导入搅拌桶100内;
[0109]
步骤二:预热至45℃,再向搅拌桶100内加入预处理剂并启动搅拌,混合8min;
[0110]
步骤三:再在搅拌条件下向搅拌桶100内加入处理剂,加热至60℃,搅拌30min,得到处理后的混合物;
[0111]
步骤四:将步骤三中得到的处理后的混合物转移至分离设备200中进行固液分离,分离得到的固体物质即为胶水沉积后形成的固废,进行危废处理。
[0112]
其中,预处理剂包括质量份数分别为8份的硫酸化蓖麻油、3份的乙醇和0.3份的氯
化钠,预处理剂的加入量为待分离混合液总质量的0.7%;处理剂包括质量份数分别为15份的聚合氯化铝、60份的破乳剂、1份的聚丙烯酰胺和15份的氢氧化钠,处理剂的加入量为待分离混合液总质量的1.3%。
[0113]
搅拌桶100和分离设备200的具体结构与实施例1相同,故在此不在赘述。
[0114]
应用例1
[0115]
取同一批混有胶水的待分离混合液,平均分为7份,编号为实验组1-7。
[0116]
实验组1通过实施例3中记载的方案进行处理,得到胶水固废1;
[0117]
实验组2通过对比例1中记载的方案进行处理,得到胶水固废2;
[0118]
实验组3通过对比例2中记载的方案进行处理,得到胶水固废3;
[0119]
实验组4通过对比例3中记载的方案进行处理,得到胶水固废4;
[0120]
实验组5通过对比例4中记载的方案进行处理,得到胶水固废5;
[0121]
实验组6通过对比例5中记载的方案进行处理,得到胶水固废6;
[0122]
实验组7通过对比例6中记载的方案进行处理,得到胶水固废7;
[0123]
将胶水固废1-7通过相同的条件进行烘干,然后称重,结果如下表所示:
[0124]
实验组固废干重(kg)实验组112.4实验组210.6实验组311.7实验组49.6实验组57.5实验组68.2实验组79.8
[0125]
结果分析:从上述表格可以看出,实验组1中得到的固废干重最终,即利用本发明提供的1方法对胶水沉积的最为彻底,故达到了本发明的预期目的。
[0126]
本文中所描述的具体实施例仅仅是对本发明精神作举例说明。本发明所属技术领域的技术人员可以对所描述的具体实施例做各种各样的修改或补充或采用类似的方式替代,但并不会偏离本发明的精神或者超越所附权利要求书所定义的范围。
[0127]
尽管本文较多地使用了搅拌桶100、搅拌空间101、桶体102、加热夹套103、进料口104、出料口105、搅拌电机106、搅拌杆107、取样口108、分离设备200、壳体201、旋转分离桶202、分离空腔203、驱动电机204、进料管道205、括刮壁组件206、刮壁电机207、输出轴208、刮板209等术语,但并不排除使用其它术语的可能性。使用这些术语仅仅是为了更方便地描述和解释本发明的本质;把它们解释成任何一种附加的限制都是与本发明精神相违背的。