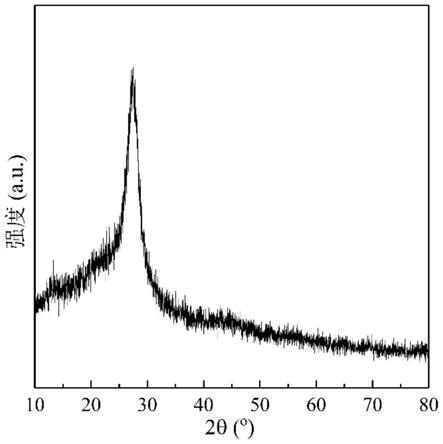
1.本发明属于材料制备技术领域,具体涉及一种石墨型氮化碳负载单原子钴催化剂及其制备方法和应用。
背景技术:2.环己烷分子氧氧化生成的环己醇、环己酮和己二酸是重要的药物中间体和有机溶剂,同时也是工业上生产己内酰胺、尼龙的关键原材料。由于环己醇、环己酮相比于环己烷活性更高、更易被氧化,致使有大量副产物的生成。同时,生成的副产物有机酸和水,易吸附于催化剂表面,导致催化剂迅速失活。其中,构建高效催化剂调控环己烷氧化路径,提高目标产物的选择性,抑制副产物的生成,是提高生产效率和降低物/能耗水平的根本途径,同时也是研究的难点石墨型氮化碳(g-c3n4)作为一种无金属n型半导体,具有独特的物化性质。由于g-c3n4结构稳定、比表面积高、孔隙发达,因此常被作为催化剂的载体,用于多相催化反应。例如,tian等将g-c3n4负载的ag催化剂用于苯乙烯氧化,显示出优越的催化性能(acs catalysis 2021, 11, 4946)。此外,鉴于g-c3n4表面疏水的特性,能够有效避免环己烷氧化反应过程中生成的有机酸和水在表面的吸附,从而预期可以显著减缓催化剂失活进程。
3.目前,已由大量金属催化剂被开发用于环己烷分子氧氧化反应,其中钴基催化剂因其低廉的价格以及优越的性能而广受关注(molecular catalysis 2019, 466, 130)。li和jing等分别提出co
2+
很可能是催化环己烷氧化的活性物种(catalysis letters 2010, 136, 20和journal of fuel chemistry and technology 2016, 44, 1249)。近期,yuan等基于有机金属骨架材料开发了多种钴基催化剂用于环己烷氧化,获得了较高的催化性能(catalysis letters 2021, doi.org/10.1007/s10562-021-03638-0和korean journal of chemical engineering 2020, 37, 1137)。hao等采用氮掺杂的石墨烯负载钴,并将其用于催化环己烷氧化,环己烷转化率达到8.9%,环己醇和环己酮的总选择性为85.7%。郝芳等制备了含钴的类沸石咪唑骨架材料并应用于环己烷氧化反应中(cn106632055),该催化剂上环己烷转化率达到了13.8%,环己醇和环己酮的总选择性为79.9%。尽管这些钴基催化剂对环己烷氧化显示出较高得性能,但其反应条件较严苛,且催化剂稳定性差、易失活(aiche journal 2016, 62, 4384)。因此,开发高性能钴基氧化催化剂显得尤为重要。
技术实现要素:4.目的:为解决现有技术的不足,本发明提供一种石墨型氮化碳(g-c3n4)负载单原子钴催化剂及其制备方法和应用。
5.技术方案:为解决上述技术问题,本发明采用的技术方案为:第一方面,提供一种石墨型氮化碳负载单原子钴催化剂的制备方法,包括:步骤(1),称取一定量的三聚氰胺溶于50-80
ꢀ°
c热水中,在搅拌条件下加入一定质量的硅凝胶,得反应液;将反应液50-80
ꢀ°
c下搅拌反应至水分完全蒸干,所得固体样品在氮
气氛围中500-550
ꢀ°
c焙烧3-6 h后,用氟氢化铵溶液刻蚀除去二氧化硅,经离心、洗涤、干燥后得石墨型氮化碳g-c3n4;其中,反应液中加入的三聚氰胺、硅凝胶、水的质量比为(1-4):3:10;步骤(2),称取一定质量步骤(1)中制得的石墨型氮化碳分散于水中,在搅拌条件下向上述分散液中滴加硝酸钴水溶液,得反应液;将反应液在20~30
ꢀ°
c下搅拌反应12-24 h,经离心、洗涤、干燥后、氮气氛围350-500
ꢀ°
c下焙烧2-4 h后,制得石墨型氮化碳负载单原子分散钴催化剂;其中,反应液中硝酸钴的浓度为0.068~0.407 mol
∙
l-1
,反应液中加入的石墨型氮化碳、硝酸钴、水的质量比为1:(0.16-0.93):138。
6.在一些实施例中,步骤(1)中,反应液中加入的三聚氰胺、硅凝胶、水的质量比为1:3:10。
7.在一些实施例中,步骤(1)制得的g-c3n4载体为介孔结构,比表面积不低于100 m2∙
g-1
,优选为123-340 m2∙
g-1
;更优选地,所述g-c3n4的比表面积为340 m2∙
g-1
。
8.在一些实施例中,步骤(2)中,反应液中加入的石墨型氮化碳、硝酸钴、水的质量比为1:0.93:138。
9.在一些实施例中,步骤(1)中,在氮气氛围中550
ꢀ°
c焙烧4 h;步骤(2)中,氮气氛围400
ꢀ°
c下焙烧2 h。
10.在一些实施例中,制备方法具体包括:称取一定量的三聚氰胺溶于70
ꢀ°
c热水中,在剧烈搅拌下加入一定质量的硅凝胶,其中三聚氰胺、硅凝胶、水的质量比为(1-4):3:10,然后搅拌至水分完全蒸干,所得固体样品在氮气氛围中550
ꢀ°
c焙烧4 h后,用氟氢化铵溶液刻蚀除去二氧化硅,最后经离心、洗涤、干燥后得到g-c3n4(记为g-c3n
4-x,x表示反应液中三聚氰胺的比例);称取一定量上述制得的g-c3n4悬浮于水中,在剧烈搅拌下向上述溶液中滴加硝酸钴水溶液,硝酸钴溶度在0.068至0.407 mol
∙
l-1
之间,上述最终反应液中g-c3n4、硝酸钴、水质量比为1:(0.16-0.93):138,随后室温搅拌12 h,经离心、洗涤、干燥、氮气氛围400
ꢀ°
c下焙烧2 h后,即制得所述g-c3n4负载单原子钴催化剂(记为wco/g-c3n
4-x,w表示钴负载量,wt%)。
11.第二方面,提供一种石墨型氮化碳负载单原子钴催化剂,由上述的方法制备得到。
12.所述催化剂为石墨型氮化碳负载钴单原子,为钴为单原子分散于g-c3n4载体表面。
13.在一些实施例中,催化剂中钴的负载量为0.01-0.09 wt%。
14.所述的g-c3n4载体为介孔结构,比表面积可在123-340 m2∙
g-1
之间调控;负载在上述g-c3n4载体表面上的钴为单原子分散,与载体形成了-n-co-n-的稳定结构,上述催化剂中钴的负载量可在0.01-0.09 wt%之间调控。
15.优选地,所述g-c3n4的比表面积为340 m2∙
g-1
,催化剂中钴负载量为0.09 wt%。
16.第三方面,提供所述石墨型氮化碳负载单原子钴催化剂用于对环己烷进行分子氧氧化反应的催化剂。能够提高氧化速率、提高环己醇、环己酮、己二酸选择性以及用于延长催化剂寿命。
17.有益效果:本发明提供的一种石墨型氮化碳负载单原子钴催化剂及其制备方法和应用,具有以下优点:1. 采用二氧化硅凝胶作为模板,合成了高比表面积的氮化碳(不加模板合成的氮
化碳比表面积很低),从而有利于钴物种在氮化碳载体表面的分散; 通过改变三聚氰胺的浓度,调控g-c3n4片的厚度,能够有效增加g-c3n4的比表面积和孔容;其次,在通过吸附法负载钴时,g-c3n4表面带负电荷的吡啶n能够与硝酸钴溶液中的钴离子发生静电作用,从而有利于钴在g-c3n4表面实现单原子分散。
18.2. 本发明的g-c3n4负载单原子钴催化剂在环己烷氧化反应中,大幅提高了氧化速率,提高了环己醇、环己酮、己二酸的选择性,抑制了其他副产物的生成。
19.3. g-c3n4负载单原子钴催化剂因其表面疏水的特性,避免了反应中生成的有机酸以及水的吸附,减缓了催化剂失活,显著提高了催化剂的稳定性。
20.4. 本发明的g-c3n4负载单原子钴催化剂制备工艺简单、绿色,成本低,具有良好的工业化应用前景。
附图说明
21.图1为g-c3n4和co(no3)2结构示意图和电荷分布图;图2为本发明实施例1制备的g-c3n4负载单原子钴催化剂的x射线衍射图;图3为本发明实施例1制备的g-c3n4负载单原子钴催化剂的透射电镜图;图4为本发明实施例1制备的g-c3n4负载单原子钴催化剂的氮气吸附脱附等温线和孔径分布图;图5为本发明实施例2制备的g-c3n4负载单原子钴催化剂的x射线衍射图;图6为本发明实施例2制备的g-c3n4负载单原子钴催化剂的透射电镜图;图7为本发明实施例2制备的g-c3n4负载单原子钴催化剂的氮气吸附脱附等温线和孔径分布图;图8为本发明实施例3制备的g-c3n4负载单原子钴催化剂的x射线衍射图;图9为本发明实施例3制备的g-c3n4负载单原子钴催化剂的透射电镜图;图10为本发明实施例3制备的g-c3n4负载单原子钴催化剂的氮气吸附脱附等温线和孔径分布图;图11为本发明实施例3制备的g-c3n4负载单原子钴催化剂的x射线光电子能谱图和结构示意图;图12为对比例1制备的g-c3n4负载钴催化剂的x射线衍射图;图13为对比例1制备的g-c3n4负载钴催化剂的透射电镜图;图14为对比例2制备的g-c3n4负载钴催化剂的x射线衍射图;图15为对比例2制备的g-c3n4负载钴催化剂的透射电镜图;图16为本发明实施例1制备的g-c3n4负载单原子钴催化剂上环己烷氧化转化率和产物分布图;图17为本发明实施例2制备的g-c3n4负载单原子钴催化剂上环己烷氧化转化率和产物分布图;图18为本发明实施例3制备的g-c3n4负载单原子钴催化剂上环己烷氧化转化率和产物分布图;图19为本发明实施例3制备的g-c3n4负载单原子钴催化剂上环己烷氧化循环性能图;
图20为对比例1制备的g-c3n4负载钴催化剂上环己烷氧化转化率和产物分布图;图21为对比例2制备的g-c3n4负载钴催化剂上环己烷氧化转化率和产物分布图。
具体实施方式
22.下面结合附图和实施例对本发明所述技术方案进行详细阐述。以下实施例仅用于更加清楚地说明本发明的技术方案,而不能以此来限制本发明的保护范围。
23.实施例1称取一定量的三聚氰胺溶于60
ꢀ°
c热水中,在剧烈搅拌下加入一定质量的硅凝胶,其中三聚氰胺、硅凝胶、水的质量比为4:3:10,然后搅拌至水完全蒸干,所得固体样品在氮气氛围中550
ꢀ°
c焙烧4 h后,用氟氢化铵溶液刻蚀除去二氧化硅,最后经离心、洗涤、干燥后得到g-c3n4载体,记为g-c3n
4-4;称取一定量上述制得的g-c3n
4-4悬浮于水中,在剧烈搅拌下向上述溶液中滴加浓度为0.0678 mol
∙
l-1
的硝酸钴水溶液,上述反应液中g-c3n
4-4、硝酸钴、水质量比为1:0.16:138,随后室温搅拌12 h;经离心、洗涤、干燥、氮气氛围400
ꢀ°
c下焙烧2 h后,即制得所述催化剂,记为0.01co/g-c3n
4-4。
24.图1a为g-c3n4和co(no3)2结构示意图和电荷分布图,可以看出g-c3n4中n和c原子分别带负电荷和正电荷,co(no3)2中co离子带正电荷;图1b为co(no3)2在g-c3n4表面的吸附构型图,可以看出当co(no3)2以co离子与g-c3n4中吡啶n作用时,吸附能最大,意味着吸附结构最稳定。这表明制备得到的wco/g-c3n
4-x催化剂中co以单原子形式与吡啶n作用。
25.图2为制备得到的0.01co/g-c3n
4-4催化剂的x射线衍射(xrd)图谱,经xrd物相鉴定,可以确定合成了石墨型氮化碳材料,且无钴物种衍射峰表明钴物种高度分散。
26.经元素组成分析,确定0.01co/g-c3n
4-4催化剂中钴的负载量约为0.01 wt%。
27.图3为制备得到的0.01co/g-c3n
4-4催化剂的透射电镜图,可以看出g-c3n
4-4为介孔片状结构,且无金属钴纳米颗粒存在,这也间接证明钴以原子形式分散于g-c3n
4-4载体表面。
28.图4为制备得到的0.01co/g-c3n
4-4催化剂的氮气吸附脱附等温线和孔径分布图,可以确定0.01co/g-c3n
4-4催化剂的比表面积为123 m2∙
g-1
,平均孔径约为6.6 nm。
29.实施例2称取一定量的三聚氰胺溶于70
ꢀ°
c热水中,在剧烈搅拌下加入一定质量的硅凝胶,其中三聚氰胺、硅凝胶、水的质量比为1:3:10,然后搅拌至水完全蒸干,所得固体样品在氮气氛围中550
ꢀ°
c焙烧4 h后,用氟氢化铵溶液刻蚀除去二氧化硅,最后经离心、洗涤、干燥后得到载体,记为g-c3n
4-1;称取一定量上述制得的g-c3n
4-1悬浮于水中,在剧烈搅拌下向上述溶液中滴加浓度为0.068 mol
∙
l-1
的硝酸钴水溶液,上述最终反应液中g-c3n
4-1、硝酸钴、水的质量比为1:0.16:138,随后室温搅拌12 h,经离心、洗涤、干燥、氮气氛围400
ꢀ°
c下焙烧2 h后,即制得所述催化剂,记为0.03co/g-c3n
4-1。
30.图5为制备得到的0.03co/g-c3n
4-1催化剂的x射线衍射(xrd)图谱,经xrd物相鉴定,可以确定合成了石墨型氮化碳材料,且无钴物种衍射峰表明钴物种高度分散。
31.经元素组成分析,确定0.03co/g-c3n
4-1催化剂中钴的负载量约为0.03 wt%。
32.图6为制备得到的0.03co/g-c3n
4-1催化剂的透射电镜图,可以看出g-c3n
4-1为介孔薄片状结构,且无金属钴纳米颗粒存在,这也间接证明钴以原子形式分散于g-c3n
4-1载体
表面。
33.图7为制备得到的0.03co/g-c3n
4-1催化剂的氮气吸附脱附等温线和孔径分布图,可以确定0.03co/g-c3n
4-1催化剂的比表面积为303 m2∙
g-1
,平均孔径约为5.1 nm。
34.实施例3称取一定量的三聚氰胺溶于80
ꢀ°
c热水中,在剧烈搅拌下加入一定质量的硅凝胶,其中三聚氰胺、硅凝胶、水的质量比为1:3:10,然后搅拌至水完全蒸干,所得固体样品在氮气氛围中550
ꢀ°
c焙烧4 h后,用氟氢化铵溶液刻蚀除去二氧化硅,最后经离心、洗涤、干燥后得到载体,记为g-c3n
4-1;称取一定量上述制得的g-c3n
4-1悬浮于水中,在剧烈搅拌下向上述溶液中滴加浓度为0.407 mol
∙
l-1
的硝酸钴水溶液,上述最终反应液中g-c3n
4-1、硝酸钴、水的质量比为1:0.93:138,随后室温搅拌12 h,经离心、洗涤、干燥、氮气氛围400
ꢀ°
c下焙烧2 h后,即制得所述催化剂,记为0.09co/g-c3n
4-1。
35.图8为制备得到的0.09co/g-c3n
4-1催化剂的x射线衍射(xrd)图谱,经xrd物相鉴定,可以确定合成了石墨型氮化碳材料,且无钴物种衍射峰表明钴物种高度分散。
36.经元素组成分析,确定0.09co/g-c3n
4-1催化剂中钴的负载量约为0.09 wt%。
37.图9为制备得到的0.09co/g-c3n
4-1催化剂的透射电镜图,可以看出g-c3n
4-1为介孔薄片状结构,且无金属钴纳米颗粒存在;mapping图表明钴元素均匀的分散在g-c3n
4-1表面,这些均证明钴以原子形式存在。
38.图10为制备得到的0.09co/g-c3n
4-1催化剂的氮气吸附脱附等温线和孔径分布图,可以确定0.09co/g-c3n
4-1催化剂的比表面积为293 m2∙
g-1
,平均孔径约为5.4 nm。
39.图11a为制备得到的0.09co/g-c3n
4-1催化剂的x射线光电子能谱图,位于结合能781.1 ev的峰归属于co
2+ 2p
3/2
。图11b为制备得到的wco/g-c3n
4-x催化相应的结构示意图。
40.对比例1采用上述制备得到的g-c3n
4-1作为载体,通过浸渍法负载钴。具体步骤为:称取0.01 g硝酸钴溶于4.0 ml水中,随后将硝酸钴水溶液滴加至1.00 g的g-c3n
4-1中,搅拌均匀后室温静置12 h,经氮气氛围400
ꢀ°
c下焙烧2 h后制得对比例,记为co/g-c3n
4-1-im。
41.图12为制备得到的co/g-c3n
4-1-im催化剂的x射线衍射(xrd)图谱,无钴物种衍射峰表明钴物种高度分散。
42.经元素组成分析,确定co/g-c3n
4-1-im催化剂中钴的负载量约为0.31 wt%。
43.图13为制备得到的co/g-c3n
4-1-im催化剂的透射电镜图,可以看出co/g-c3n
4-1-im仍为介孔结构。
44.对比例2该对比例中所用的原材料与实施例3相同,只是制备过程中,硝酸钴与三聚氰胺一起溶于水中。具体步骤为:称取一定量的三聚氰胺和硝酸钴溶于70
ꢀ°
c热水中,在剧烈搅拌下加入一定质量的硅凝胶,其中三聚氰胺、硝酸钴、硅凝胶、水的质量比为1:0.01:3:10,然后搅拌至水完全蒸干,所得固体样品在氮气氛围中550
ꢀ°
c焙烧4 h后,用氟氢化铵溶液刻蚀除去二氧化硅,最后经离心、洗涤、干燥后制得对比例,记为co-g-c3n
4-1。
45.图14为制备得到的co-g-c3n
4-1催化剂的x射线衍射(xrd)图谱,无钴物种衍射峰表明钴物种高度分散。
46.经元素组成分析,确定co-g-c3n
4-1催化剂中钴的负载量约为0.25 wt%。
47.图15为制备得到的co-g-c3n
4-1催化剂的透射电镜图,可以看出co-g-c3n
4-1为介孔结构。
48.催化效果实验将上述实施例制备的石墨型氮化碳负载单原子钴催化剂用于环己烷无溶剂氧化反应。以氧气为氧化剂,氧气压力0.8 mpa,在130
ꢀ°
c条件下反应,实验结果见图16-19。
49.图16-18分别为实施例1、2、3制备得到0.01co/g-c3n
4-4、0.03co/g-c3n
4-1、0.09co/g-c3n
4-1催化剂性能。相比对比例1制备得到的co/g-c3n
4-1-im催化剂上(图20),随反应时间环己烷转化增加逐渐减缓,说明co/g-c3n
4-1-im催化剂完全失活。0.01co/g-c3n
4-4、0.03co/g-c3n
4-1、0.09co/g-c3n
4-1催化剂上环己烷转化率随着反应时间延长均线型增加,说明催化剂无明显失活。反应时间12 h时,三种催化剂上环己烷转化率分别达到14.6%、15.8%、18.2%,0.09co/g-c3n
4-1催化剂上环己醇(a)、环己酮(k)、己二酸(aa)的总选择性达到97.3%。如图19所示,0.09co/g-c3n
4-1经过5次循环实验后,环己烷转化率和目标产物选择性均无明显降低,表明催化结构稳定。对比例2制备得到的co-g-c3n
4-1催化剂上(图21),反应时间12 h时,环己烷转化率仅为9.2%,这是因为钴物种被包覆在载体g-c3n4中。0.09co/g-c3n
4-1优越的催化性能归因于高比表面积的g-c3n
4-1载体,有利于钴物种以原子形式分散;同时疏水表面抑制了有机酸和水的吸附,提高了催化剂稳定性。
50.综上所述可见:本发明提供的石墨型氮化碳负载单原子钴催化剂相对于现有技术,具有显著进步和更优催化效果,而且本发明所述的催化剂制备方法简单,结构可控,适合工业化生产,具有良好的价值和应用前景。
51.以上显示和描述了本发明的基本原理、主要特征以及本发明的优点。本行业的技术人员应该了解,本发明不受上述实施例的限制,上述实施例和说明书中描述的只是说明本发明的原理,在不脱离本发明精神和范围的前提下,本发明还会有各种变化和改进,这些变化和改进都落入要求保护的本发明范围内。本发明要求保护范围由所附的权利要求书及其等效物界定。