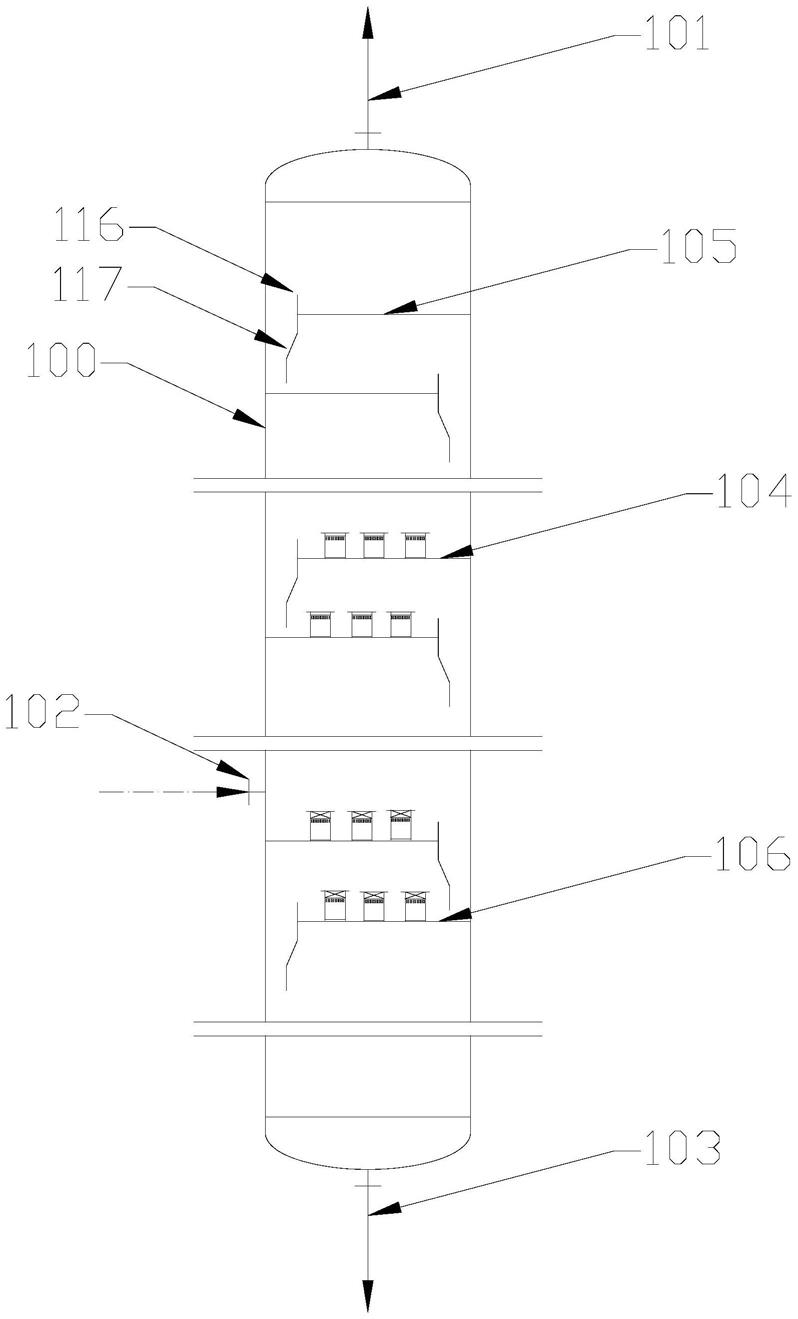
1.本实用新型涉及化工设备领域,尤其涉及一种分离丙烯醛的精馏装置。
背景技术:2.丙烯醛水合反应制3
‑
羟基丙醛是丙烯醛制备1,3
‑
丙二醇工艺的第一步反应,该反应是在酸性树脂催化剂的作用下生成3
‑
羟基丙醛。为了提高产物的选择性,丙烯醛的转化率维持在40~70%,生成的水合液中丙烯醛含量高,不仅造成原料丙烯醛的浪费,而且对后续的加氢反应的催化剂产生影响,造成产物中的副产物增加,使得产品的精制的难度增加。并且由于丙烯醛是不饱和醛类,化学性质活泼,在60℃以上就会发生自聚反应,并且3
‑
羟基丙醛和丙烯醛可以发生羟醛缩合反应,降低了产品收率,也影响了产品的纯度。故需要在进行加氢反应前应对水合液中的丙烯醛进行分离。
3.传统工艺采用精馏的方式对水合液进行分离回收丙烯醛,精馏装置多采用散装填料或大孔径筛孔塔板,但该类内件易堵且传质效率不高,堵塞后更换填料,会造成装置的停车,影响了装置的产能,而塔板堵塞后会使全塔压降升高,造成全塔温度升高,加速了丙烯醛和3
‑
羟基丙醛的聚合反应。专利us3518310、us5093537、us6140543提出采用薄膜蒸发器以降低水合液与热源的接触时间,减少了丙烯醛和3
‑
羟基丙醛的聚合反应,但降膜蒸发器的设备投资大,操作困难;专利cn1398843a提出在精馏塔底引入惰性气体,降低塔釜温度,但会造成塔顶冷凝效率降低,尾气处理负荷增大;专利cn101033180a提出采用分段设置不同种类塔内件的方式,即精馏段上部采用新型垂直筛板,精馏段上段采用并流喷射填料塔板,提馏段采用规整填料。这种采用组合内件的形式发挥了各自优势,但所采用的新型垂直筛板,并流喷射填料塔板板上存在弓形区及较多的液相死区,会促使液相在板上发生聚合,而提馏段设置的填料会加剧3
‑
羟基丙醛的聚合。
技术实现要素:4.为了解决上述技术问题,本实用新型提供了一种分离丙烯醛的精馏装置。本实用新型装置以进料口为界限上下分为精馏段和提馏段,精馏段上部采用高效导向塔板,精馏段下部采用导向立体喷射塔板,提馏段采用导向复合立体喷射塔板。通过对精馏装置内不同内件的选用,解决了在分离过程中丙烯醛和3
‑
羟基丙醛的聚合问题,增加了精馏装置的运行周期。
5.本实用新型的具体技术方案为:一种分离丙烯醛的精馏装置,包括塔体,所述塔体的顶部、侧部和底部分别设有塔顶气相出口、进料口和塔底液相出口。所述塔体以进料口为界限,分为位于上段的精馏段和位于下段的提馏段;所述精馏段内由下至上设有若干导向立体喷射塔板和若干高效导向塔板;所述提馏段内设有若干导向复合立体喷射塔板;所述高效导向塔板、导向立体喷射塔板和导向复合立体喷射塔板各自交错设置以形成折流通道。
6.本实用新型装置以进料口为界限上下分为精馏段和提馏段,精馏段上部采用高效
导向塔板,精馏段下部采用导向立体喷射塔板,提馏段采用导向复合立体喷射塔板。
7.上述装置的工作原理为:被分离物料液(含丙烯醛和3
‑
羟基丙醛的水合液溶液)由进料口进入塔内,混合液在提馏段塔板上与塔底上升的气相进行传质,部分未冷凝气相进入精馏段塔板上的回流液继续进行气液传质。通过精馏段和提馏段塔板上的气液传质过程,在塔顶获得轻组分丙烯醛,塔底得到重组分3
‑
羟基丙醛的水溶液。
8.本发明通过对精馏装置内不同内件的选用,可解决在分离过程中丙烯醛和3
‑
羟基丙醛的聚合问题,进而增加精馏装置的运行周期。
9.作为优选,所述高效导向塔板上布设有导向孔,所述导向孔的边缘处设有向上凸起的导向板,所述导向孔与导向板形成的孔缝开口与其所在高效导向塔板上液相的流动方向一致。
10.在上述结构中,导向孔与导向板组合所形成的孔缝,其开口与液相的流动方向一致。在运行过程中,从下层塔板上升的气相通过导向孔和孔缝进入塔板上的液相中,在该过程中,由孔缝喷出的气相方向与液流方向存在一定的角度,利用速度的分解方法可以将气相分为水平方向和垂直方向(见图4)。其中垂直方向的气相垂直上升穿过塔板上的液层形成鼓泡来进行传质,水平方向与塔板上液相的流动方向相同可以促进液相在塔板上的流动,促进了液相梯度的降低并减少了返混的产生,防止塔板上死区的形成。
11.作为优选,所述高效导向塔板上靠近塔体侧壁处位置的导向孔的分布密度大于高效导向塔板中心位置。
12.进行上述设计的原因是:靠近塔壁处为塔板上液相流动缓慢区,此处易形成传质死区。增加导向孔布置数量有利于推动板上液相流动,防止传质死区产生。
13.作为优选,所述导向立体喷射塔板包括塔板和帽罩;所述塔板的中心区域和靠近塔体侧壁处位置分别设有大孔和导向孔;每一个所述大孔上罩设有所述帽罩,所述帽罩的侧壁上布设有筛孔,帽罩的侧壁顶部和底部周向上分别设有上端狭缝和下端狭缝;所述导向孔的边缘处设有向上凸起的导向板,所述导向孔与导向板形成的孔缝开口与其所在塔板上液相的流动方向一致。
14.在上述结构中,塔板上开设大孔(例如圆形或矩形),孔上设置对应形状的帽罩,帽罩上端侧面开设筛孔,帽罩顶部和底部留有狭缝,帽罩底部与塔板间留有狭缝。在靠近塔体侧壁处布置一定数量的导向孔。在运行过程中,下层塔板的气相分别通过导向孔和板上的大孔进入塔板。进入导向孔和孔缝的气相促进了液相梯度的降低并减少了返混的产生,防止塔板上死区的形成。进入板上大孔的气相将塔板上的液相从帽罩底部的下端狭缝中提升,液相在提升过程中开始破碎形成小液滴并与气相充分接触混合,上升的气液混合相一部分通过帽罩上的筛孔喷出罩外,另一部分从帽罩顶部的上端狭缝中喷出。
15.作为优选,所述导向复合立体喷射塔板包括塔板、帽罩和填料;所述塔板的中心区域和靠近塔体侧壁处位置分别设有大孔和导向孔;每一个所述大孔上罩设有所述帽罩,所述帽罩的顶部装填有所述填料,帽罩的侧壁上布设有筛孔,帽罩的侧壁顶部和底部周向上分别设有上端狭缝和下端狭缝;所述导向孔的边缘处设有向上凸起的导向板,所述导向孔与导向板形成的孔缝开口与其所在塔板上液相的流动方向一致。
16.导向复合立体喷射塔板与导向立体喷射塔板的区别是在帽罩上端加装填料层,从帽罩底部的下端狭缝进入帽罩中的液相在破碎成小液滴后一部分从筛孔喷出罩外,另一部
分进入帽罩上端的填料层中完成气液两相的传质。
17.作为优选,所述导向板的截面为内弧面朝向导向孔的弧形。
18.弧形的设置可以有效将上升的气相方向转变为近45度斜向上方向。
19.作为优选,所述填料为金属开孔板波纹填料或金属开孔丝网填料。
20.作为优选,所述高效导向塔板的数量占总塔板数量的10~40%,优选15~30%;所述导向立体喷射塔板的数量占总塔板数量的5~35%,优选15~30%;所述导向复合立体喷射塔板的数量占总塔板数量的15~70%,优选30~60%。
21.进行上述分配的原因是:高效导向筛板的抗堵性能较好,但传质效率差且压降高,使用在精馏段上部丙烯醛浓度较高的区域;导向立体喷射塔的抗堵性能弱于上者但传质效率较高且压降低,用于精馏段的下部;导向复合立体喷射塔板传质效率高,压降大,但抗堵性较差,用于提馏段区域。
22.作为优选,所述高效导向塔板的开孔率为5~15%;所述导向立体喷射塔板的开孔率为5~20%,帽罩上筛孔孔径为3~15mm;所述导向复合立体喷射塔板的开孔率为5~20%,帽罩上筛孔孔径为3~15mm,所述填料的厚度占帽罩高度的20~40%。
23.在上述开孔率较为合理,若开孔率较小会增加塔板的压降,不利于塔釜温度的降低,开孔率较大塔板易产生漏液等不正常操作,降低塔板的传质效率,全塔理论板数降低。同样,孔径太小会增加塔板的压降,孔径过大会不利于气液两相的接触,降低塔板的传质效率。
24.作为优选,所述高效导向塔板、导向立体喷射塔板和导向复合立体喷射塔板的缺口边缘上下侧分别设有溢流堰和降液导向板;其中:高效导向塔板上的溢流堰高度为5~45mm,导向立体喷射塔板上的溢流堰高度为10~50mm,导向复合立体喷射塔板上的溢流堰高度为10~50mm;所述降液导向板的径向截面为与塔体侧壁平行的弧形,降液导向板呈阶梯式向下延伸靠近塔体侧壁且弧长变短。
25.与现有技术对比,本实用新型的有益效果是:
26.本实用新型通过选用不同类型的塔板,精馏段上部采用高效导向塔板,精馏段下部采用导向立体喷射塔板,提馏段采用导向复合立体喷射塔板,该精馏装置利用了高效导向塔板抗堵性能好,压降低的特点和导向立体塔板传质性能好,处理负荷大的特点。与原工艺采用大孔筛板的精馏装置相比,该实用新型塔板效率提高100%,操作弹性提高50%以上,处理负荷提高100%。与专利cn101033180a塔板组合方式相比,装置的抗堵性能更好,塔板上的导向孔促进板上液层的均匀分布,减少液相死区的形成,而且精馏塔顶部采用高效导向筛孔塔板更易清洗。
27.该精馏装置由于上部的丙烯醛浓度较高,发生聚合的可能性更大,故在精馏段上部选用高效导向筛孔塔板,精馏段下部选用导向立体喷射塔板,具有较大通量和较高传质效率的同时,塔板的抗堵性能较强且易清洗。提馏段中丙烯醛的浓度有所降低,但水合产物3
‑
羟基丙醛的浓度增加且操作温度较高,发生聚合的可能性较大,故选用导向复合立体喷射塔板,提高了塔板的传质效率,同时其还具有较高的抗堵性能。采用该种组合的精馏装置全塔压降低至4~15 kpa,塔底温度降低至50~65℃,有效防止了塔内丙烯醛与3
‑
羟基丙醛的聚合反应。
附图说明
28.图1为本实用新型的一种精馏装置塔内结构示意图;
29.图2为本实用新型中的一种导向立体喷射塔板的结构示意图;
30.图3为本实用新型中的一种导向复合立体喷射塔板的结构示意图;
31.图4为本实用新型中的一种导向孔和导向板的结构示意图;
32.图5为本实用新型中的一种导向立体喷射塔板和导向复合立体喷射塔板的开孔区域示意图。
33.附图标记为:塔体100,塔顶气相出口101、进料口102,塔底液相出口103,导向立体喷射塔板104,高效导向塔板105,导向复合立体喷射塔板106,导向孔107,导向板108,塔板109,帽罩110,大孔111,筛孔112,上端狭缝113,下端狭缝114,填料115,溢流堰116,降液导向板117。
具体实施方式
34.下面结合实施例对本实用新型作进一步的描述。在本实用新型中所涉及的装置、连接结构和方法,若无特指,均为本领域公知的装置、连接结构和方法。
35.总实施例
36.如图1所示,一种分离丙烯醛的精馏装置,包括塔体100,所述塔体的顶部、侧部和底部分别设有塔顶气相出口101、进料口102和塔底液相出口103。所述塔体以进料口为界限,分为位于上段的精馏段和位于下段的提馏段;所述精馏段内由下至上设有若干导向立体喷射塔板104和若干高效导向塔板105;所述提馏段内设有若干导向复合立体喷射塔板106;所述高效导向塔板、导向立体喷射塔板和导向复合立体喷射塔板各自交错设置以形成折流通道。
37.其中:
38.所述高效导向塔板上布设有导向孔107(开孔率为5~15%),如图4所示,所述导向孔的边缘处设有向上凸起的导向板108,所述导向孔与导向板形成的孔缝开口与其所在高效导向塔板上液相的流动方向一致。高效导向塔板上靠近塔体侧壁处位置的导向孔的分布密度大于高效导向塔板中心位置。
39.如图2所示,所述导向立体喷射塔板包括塔板109和帽罩110;如图5所示,所述塔板的中心区域和靠近塔体侧壁处位置分别设有大孔111和导向孔,开孔率为5~20%;每一个所述大孔上罩设有所述帽罩,所述帽罩的侧壁上布设有筛孔112(孔径为3~15mm),帽罩的侧壁顶部和底部周向上分别设有上端狭缝113和下端狭缝114;所述导向孔的边缘处设有向上凸起的导向板,所述导向孔与导向板形成的孔缝开口与其所在塔板上液相的流动方向一致。
40.如图3所示,所述导向复合立体喷射塔板包括塔板、帽罩和填料115(金属开孔板波纹填料或金属开孔丝网填料);所述塔板的中心区域和靠近塔体侧壁处位置分别设有大孔和导向孔,开孔率为5~20%;每一个所述大孔上罩设有所述帽罩,所述帽罩的顶部装填有所述填料(厚度占帽罩高度的20~40%),帽罩的侧壁上布设有筛孔(孔径为3~15mm),帽罩的侧壁顶部和底部周向上分别设有上端狭缝和下端狭缝;所述导向孔的边缘处设有向上凸起的导向板,所述导向孔与导向板形成的孔缝开口与其所在塔板上液相的流动方向一致。
41.在上述结构中,所述导向板的截面为内弧面朝向导向孔的弧形。高效导向塔板的
数量占总塔板数量的10~40%,优选15~30%;导向立体喷射塔板的数量占总塔板数量的5~35%,优选15~30%;导向复合立体喷射塔板的数量占总塔板数量的15~70%,优选30~60%。
42.所述高效导向塔板、导向立体喷射塔板和导向复合立体喷射塔板的缺口边缘上下侧分别设有溢流堰116和降液导向板117;其中:高效导向塔板上的溢流堰高度为5~45mm,导向立体喷射塔板上的溢流堰高度为10~50mm,导向复合立体喷射塔板上的溢流堰高度为10~50mm;所述降液导向板的径向截面为与塔体侧壁平行的弧形,降液导向板呈阶梯式向下延伸靠近塔体侧壁且弧长变短。
43.实施例1
44.如图1所示,一种分离丙烯醛的精馏装置,包括塔体100(塔高8000 mm,塔径500 mm),所述塔体的顶部、侧部和底部分别设有塔顶气相出口101、进料口102和塔底液相出口103。所述塔体以进料口为界限,分为位于上段的精馏段和位于下段的提馏段;所述精馏段内由下至上设有8块导向立体喷射塔板104和2块高效导向塔板105;所述提馏段内设有4块导向复合立体喷射塔板106;所述高效导向塔板、导向立体喷射塔板和导向复合立体喷射塔板各自交错设置以形成折流通道。
45.其中:
46.所述高效导向塔板上布设有导向孔107(孔径大小为10*20mm 矩形开孔,导向孔开孔率为2%),如图4所示,所述导向孔的边缘处设有向上凸起的导向板108,凸起高度为3mm,所述导向孔与导向板形成的孔缝开口与其所在高效导向塔板上液相的流动方向一致。高效导向塔板上靠近塔体侧壁处位置的导向孔的分布密度大于高效导向塔板中心位置。
47.如图2所示,所述导向立体喷射塔板包括塔板109和帽罩110;如图5所示,所述塔板的中心区域和靠近塔体侧壁处位置分别设有大孔111(孔径大小为60*180mm矩形)和导向孔1(孔径大小为10*20mm 矩形开孔),总开孔率为15%;每一个所述大孔上罩设有所述帽罩,所述帽罩的侧壁上布设有筛孔112(孔径为6 mm),帽罩的侧壁顶部和底部周向上分别设有上端狭缝113和下端狭缝114;所述导向孔的边缘处设有向上凸起的导向板,所述导向孔与导向板形成的孔缝开口与其所在塔板上液相的流动方向一致。
48.如图3所示,所述导向复合立体喷射塔板包括塔板、帽罩和填料115(金属开孔板波纹填料);所述塔板的中心区域和靠近塔体侧壁处位置分别设有大孔和导向孔,开孔率为15%;每一个所述大孔上罩设有所述帽罩,所述帽罩的顶部装填有所述填料(厚度占帽罩总高度的30%),帽罩的侧壁上布设有筛孔(孔径为6mm),帽罩的侧壁顶部和底部周向上分别设有上端狭缝和下端狭缝;所述导向孔的边缘处设有向上凸起的导向板,所述导向孔与导向板形成的孔缝开口与其所在塔板上液相的流动方向一致。
49.所述高效导向塔板、导向立体喷射塔板和导向复合立体喷射塔板的缺口边缘上下侧分别设有溢流堰116和降液导向板117;其中:高效导向塔板上的溢流堰高度为15mm,导向立体喷射塔板上的溢流堰高度为15mm,导向复合立体喷射塔板上的溢流堰高度为15mm;所述降液导向板的径向截面为与塔体侧壁平行的弧形,降液导向板呈阶梯式向下延伸且弧形直径递增。
50.将含有4%(质量)丙烯醛的水合液从进料口连续进入精馏装置,该装置塔高8000 mm,塔径500 mm,提馏段安装8块导向复合立体喷射塔板,精馏段上部安装2块高效导向塔板,精馏段下部安装4块导向立体喷射塔板,溢流堰高度均为15 mm,全塔压降为11 kpa,塔
底操作温度为62 ℃,控制塔底丙烯醛含量<0.5%(质量),满足后续加氢反应的要求。该精馏装置连续运行300 小时后塔底操作温度升高至64 ℃,精馏段理论板数为4块,提馏段理论板数为5块,整塔理论板数为9块。精馏装置塔板上聚合物质与对比例1相比明显减少。
51.对比例1
52.与实施例1的区别在于:将含有4%(质量)丙烯醛的水合液从进料口连续进入丙烯醛精馏装置,该装置塔高8000 mm,塔径500 mm,提馏段安装8块导向复合立体喷射塔板,精馏段安装6块导向立体喷射塔板,溢流堰高度均为15 mm,全塔压降为10 kpa,塔底操作温度为60 ℃,控制塔底丙烯醛含量<0.5%(质量),满足后续加氢反应的要求。该精馏装置连续运行300 小时后塔底操作温度升高至65 ℃,精馏段理论板数为4块,提馏段理论板数为5块,整塔理论板数为9块。装置精馏段上部导向立体喷射塔板的帽罩筛孔部产生少量聚合物质。
53.对比例2
54.与实施例1的区别在于:将含有4%(质量)丙烯醛的水合液从进料口连续进入丙烯醛精馏装置,该装置塔高8000 mm,塔径500 mm,提馏段安装8块导向复合立体喷射塔板,精馏段安装6块高效导向塔板,溢流堰高度均为15 mm,全塔压降为13 kpa,塔底操作温度为65 ℃,控制塔底丙烯醛含量<0.5%(质量),满足后续加氢反应的要求。该精馏装置连续运行300 小时后塔底操作温度升高至68 ℃,精馏段理论板数为3块,提馏段理论板数为5块,整塔理论板数为8块。精馏塔全塔压降升高,理论板数减少。
55.对比例3
56.与实施例1的区别在于:将含有4%(质量)丙烯醛的水合液从进料口连续进入精馏装置,该装置塔高8000 mm,塔径500 mm,提馏段安装8块复合立体喷射塔板,精馏段上段安装2块普通筛孔塔板(区别在于无导向板),精馏段下段安装4块立体喷射塔板,溢流堰高度均为15 mm,全塔压降为10 kpa,塔底操作温度为60 ℃,控制塔底丙烯醛含量<0.5%(质量),满足后续加氢反应的要求。该精馏装置连续运行300 小时后塔底操作温度升高至68 ℃,精馏段理论板数为4块,提馏段理论板数为5块,整塔理论板数为9块。精馏装置塔板未布置导向孔的弓形区及其他死区存在大量的聚合物质,导致塔板效率下降,全塔压降升高。
57.对比例4
58.与实施例1的区别在于:将含有4%(质量)丙烯醛的水合液从6物料进口连续进入丙烯醛精馏装置,该装置塔高8000 mm,塔径500 mm,提馏段安装2 m金属规整填料,精馏段上部安装2块高效导向塔板,精馏段下部安装4块导向立体喷射塔板,溢流堰高度均为15 mm,全塔压降为6 kpa,塔底操作温度为55 ℃,控制塔底丙烯醛含量<0.5%(质量),满足后续加氢反应的要求。该精馏装置连续运行300 小时后塔底操作温度升高至65 ℃,精馏段理论板数为4块,提馏段理论板数为5块,整塔理论板数为9块。精馏装置提馏段填料内含有大量的聚合产物,全塔压降增加,塔板效率下降。
59.对比例5
60.与实施例1的区别在于:将含有4%(质量)丙烯醛的水合液从6物料进口连续进入丙烯醛精馏装置,该装置塔高8000 mm,塔径500 mm,提馏段安装8块大孔筛板,精馏段安装6块大孔筛板,孔径大小为12mm,开孔率为13%,溢流堰高度均为15 mm,全塔压降为12 kpa,塔底操作温度为60 ℃,控制塔底丙烯醛含量<0.5%(质量),满足后续加氢反应的要求。该精馏
装置连续运行300 小时后塔底操作温度升高至68 ℃,精馏段理论板数为3块,提馏段理论板数为4块,整塔理论板数为7块。塔板效率较低,塔板上液相死区产生较多的聚合物质。
61.以上所述,仅是本实用新型的较佳实施例,并非对本实用新型作任何限制,凡是根据本实用新型技术实质对以上实施例所作的任何简单修改、变更以及等效结构变换,均仍属于本实用新型技术方案的保护范围。