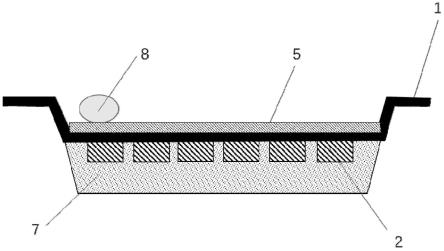
1.本发明涉及微流控芯片制造技术领域,特别涉及一种具有平整介电层表面的微流控芯片的制作模具。
背景技术:2.微流控,是一种精确控制和操控微尺度流体,尤其特指亚微米结构的技术,在dna芯片、芯片实验室、微进样技术和微热力学技术等方向得到了发展。传统的微流控芯片,利用mems微加工技术在芯片上集成微阀、微泵、微小电极和微小传感器等器件,同时在芯片表面刻蚀出微型沟道,通过流体在沟道中的流动完成分离、运输、检测等分析过程。微流控芯片又可分为连续微流控芯片和数字微流控芯片。其中连续微流控芯片的操控对象为连续流体,而数字微流控芯片的操控对象为微液滴。数字微流控芯片(dmf)是近10年来发展迅猛的一种新兴技术,以控制实现单个或多个离散液滴在芯片平面上运动为基础,利用液滴表面的电湿润现象,通过向芯片上的电极上施加电压,从而改变芯片介电层与其上液滴的固液表面张力,实现液滴在平面上的灵活运动。现有的数字微流控芯片产品的介电层难以避免因下方电极突起而造成的介电层表面的凹凸不平。介电层表面凹凸不平会对液滴灵活运动造成一定障碍,影响数字微流控芯片产品的性能和质量。
3.现有的数字微流控芯片加工方式难以对芯片表面进行有效的平整化处理。现有的技术无论是pcb加工技术还是mems加工技术皆属于“正序加工”工艺。“正序加工”的特征为,加工从基板开始堆叠数字微流控技术芯片的各个结构层,例如“电线层”,“绝缘层”,“电极层”,“介电层”。由于“介电层”永远是“正序加工”工艺堆叠的最后一层,所以他的平整度会受下方各个结构层累计影响的。
4.通过mems加工工艺制备的数字微流控芯片虽然可以通过减薄抛光介电层将打磨平整,但是减薄抛光工序有一定的限制性。当部分介电层陷入电极层之间的间隙,且表面低于电极层表面时,减薄抛光工序则无法减薄至完全平整。而且,将制备好的芯片进行抛光处理,不仅增加加工成本,也降低良品率,并且会造成一定程度的加重批间差的问题。通过pcb加工技术生产的数字微流控芯片虽然可以通过填充电极层的电极之间的缝隙来减轻不平整性,但无法彻底解决“正序加工”带来的凹凸不平的问题。近年来,一种新型柔性数字微流空芯片采用了“倒序加工”的新方法。这种“倒序加工“的方法通过先制备介电层,而后在依次堆叠电极层,绝缘层,电线层等电路结构。由于“倒序加工”的第一层是介电层,也就避免了累计堆叠造成的结构性凹凸不平。虽然“倒序加工”的数字微流控芯片表面平整但是柔软。其柔软的特性造成这种数字微流控芯片封装在硬质的基板上时,表面容易凹陷。最终,封装好的这种数字微流控芯片还是会有一定程度凹凸不平并造成液滴移动不畅,影响最终产品的性能和质量。
技术实现要素:5.为解决上述问题,本新型提供一种新的微流控芯片及其制备模具,由高压成型注
塑工艺制备具有平整介电层的微流控芯片,以确保介电层表面光滑平整。
6.一种介电层表面平整的微流控芯片,包括介电层和电路层,液滴在介电层相对电路层的另一面移动,所述介电层的未形成所述电路层的一侧为平整面。
7.进一步的,所述平整面的平整度x
min
/y
max
≧100。其中,x
min
为芯片表面电极与电极之间间距最小的值。y
max
为芯片表面电极突出最高的高度值。
8.进一步的,所述平整面的平整度xmin/ymax≧1000。
9.进一步的,介电层上印刷或者涂布有电路层,即通过先制备介电层,而后在介电层上依次设置电路层。
10.进一步的,在电路层上设置介电层,即采用正序加工工艺,从基板开始堆叠数字微流控技术芯片的各电路层,在最后一层电路层结构上设置介电层。
11.进一步的,用带有介电层成型面的制作模具对芯片介电层未形成所述电路层的一侧压平处理可以得到表面平整的介电层。
12.进一步的,所述介电层作为制备电路层的的基底材料,在所述介电层上利用印刷、打印或者蚀刻的方式形成包含电极层的电路层,所述电路层用于产生驱动位于所述介电层上与所述电路层相对一面的微液滴的电场。本发明采用的技术方案直接在介电层上形成所需电路层,所以电路层与介电层能够充分接触,使得电路层、介电层、位于介电层上与电路层相对一面的微液滴三者构成一个等效的平板电容。当对电路层施加电压时,介电层可以有效地避免电路层和微液滴之间的电荷交换而导致微液滴发生电解现象。在传统芯片中先形成电路层而后形成介电层的方案中,因电路层本身高低不平,附在电路层上方的介电层亦会高低不平并在电极间留有间隙,影响微液滴的移动。本发明所采用的技术方案先形成介电层,再在介电层上形成电路层,因此介电层上、与电路层相对的一面不会产生高低不平和间隙,利用介电层这一侧平整的表面承载微液滴,使微液滴在受到驱动时不被阻挡,顺畅移动。
13.进一步的,所述电路层包括电极层以及电线层,电极层与电线层以共层的形式处于同一层。电极层由按需设计的多个单电极组成。当微液滴位于某些单电极(以下称为“上位电极”)上时,微液滴的周缘部会接触到另外的、数个不同方向的单电极(以下称为“下位电极”)。当微液滴周围的下位电极未被加上电压时,微液滴会在上位电极上保持当前位置。当某一方向的下位电极被施加电压且上位电极和其他方向的下位电极未被施加电压时,微液滴部分接触加压的下位电极的接触角θ将减小,而液滴其他部位的接触角维持不变,因而使得液滴产生向一侧铺展的趋势,施加的电压越大,则接触角变化的越大,当电压大到一定程度时,液滴两侧会产生非常大的接触角差异,则液滴向一侧铺展的趋势更强烈,此时液滴内部会出现一个非常大的压力差,当这个压力差达到一定阈值时,液滴就会向加压的下位电极移动,实现微液滴位移的操作,微液滴现在所处的电极为新上位电极。电线层由按需设计的多条电线组成,将单电极之间、电极与外部电压连接,使电压能够施加在各个单电极上。采用共层的设计使电极层与电线层能够充分接触,确保每个单电极可以具有驱动微液滴的电压,且电极层与电线层可以同时形成,降低了工艺难度,减少了生产成本。
14.进一步的,在介电层上依次形成电极层、绝缘层以及电线层,电极层、绝缘层以及电线层共同构成电路层且以堆叠的形式形成为多层结构。对于较复杂的电路层设计,电极层与电线层共层容易发生短路,影响芯片的使用,且工艺上难以实现,因此将电极层与电路
层堆叠形成,并在两层之间加入绝缘层使两层隔离。电极层形成在介电层上,通过绝缘层将电极层与电线层隔离,使得位于介电层上与电路层相对一面的微液滴受到电极层的驱动时不会被电线层影响,能够准确向施加电压的方向移动。
15.进一步的,电极层的厚度为0.1-100um,电线层的厚度为0.1-100um。电极层的厚度为0.1-100um,使其能够产生足够的电压驱动微液滴,电线层的厚度为 0.1-100um,使其能够承受足够的外部电压同时传输给电极层。
16.进一步的,薄膜为双层结构的薄膜,其中一层为用作介电层的功能膜,另一层为离型膜。电路层形成在用作介电层的功能膜上与离型膜相反的一面,离型膜可以保护功能膜,在形成电路层的过程中不会受损。且足够薄的介电层可以有效地降低产生介电润湿的起始电压,增大微液滴两侧的电压差,使微液滴受到电压驱动更灵敏,提高芯片的实际应用意义,但同时介电层越薄强度越弱,在生产过程中易造成破损,双层结构的薄膜增加了薄膜的整体厚度,使电路层能够形成在介电层上而不对其造成损害,克服因介电层过薄而产生的工艺缺陷。
17.进一步的,薄膜为单层结构的薄膜。当薄膜使用高介电常数的材料时,可以有效降低驱动微液滴使之移动所需的电压,有利于微液滴的驱动。但过薄的介电层在电路层形成过程中易受损,因此选用厚度适宜的单层高介电薄膜能够使芯片具有灵敏性同时降低工艺难度,降低了生产成本。
18.进一步的,所述介电层未形成所述电路层的一侧涂布有疏水层。在作为介电层的薄膜未形成有所述电路层的一面上涂布疏水层,使微液滴与疏水层接触,增大微液滴在芯片表面的接触角,当对芯片施加电压时,微液滴两侧的接触角差异更大,有利于微液滴内部不平衡力的产生,从而促进微液滴的驱动。且微液滴与芯片表面的接触面变小,使芯片表面更光滑,减小了驱动微液滴所需克服的摩擦阻力。
19.进一步的,为了让本发明中微流控芯片形成平整的介电层外表面,本发明采用的技术方案提供一种新型工艺模具。所述工艺模具包括:第一模具、第二模具,所述第一模具连接有第一喷嘴。所述第二模具上设置有平整的的介电层成型面。第一模具、第二模具贴合后中部形成铸造腔,所述芯片介电层的未形成所述电路层的一侧朝向第二模具的介电层成型面,注塑液自第一喷嘴进入铸造腔,挤压微流控芯片,注塑液冷却后与芯片结合成型。芯片介电层未形成所述电路层的一侧与介电层成型面匹配形成平整的芯片介电层表面。
20.进一步的,所述注塑液应当选用低熔点注塑材料,其熔点不应高于200℃,进一步优选的是,所述注塑液为树脂材料。
21.进一步的,为了保护本发明中微流控芯片的介电层表面,成型流程如下:将所述微流控芯片置于第一、第二模具间,所述芯片介电层未形成所述电路层的一侧上设有可分离的离型膜,所述芯片的电路层朝向第一模具,离型膜朝向第二模具。将第一、第二模具贴合,自第一喷嘴注塑注塑液。待冷却后将第一、第二模具分开,将所述离型膜自所述芯片介电层分离,即可得到本发明具有平整介电层的微流控芯片。
22.本实用新型的介电层表面平整的微流控芯片,其在制备过程中,将所述印刷电路层的介电层置于第一、第二模具间,所述电路层朝向第一模具,介电层朝向第二模具。将第一、第二模具贴合,自第一喷嘴注塑注塑液。利用自第一喷嘴注塑进的高压液态树脂,使得介电层与介电层成型面贴合均匀受力,最终得到具有平整表面的介电层。在此过程中,通过
对第一模具、第二模具的铸造腔的合理设置,可以得到注塑成型的底座或者外壳。
23.本实用新型提供的技术方案具有以下有益效果:
24.1.对于“正序加工”带来的介电层表面凹凸不平,利用介电层成型面将芯片介电层表面压平,可以尽可能的提高芯片介电层表面的平整度。
25.2.对于“倒序加工”后由于进行封装所带来的介电层表面凹凸不平,本发明采用的技术方案采用高压注塑成型工艺,在封装的同时,利用介电层成型面与芯片介电层表面相配合挤压,使得封装完成后芯片介电层具有完全平整的表面。
26.3.本介电层表面平整的微流控芯片制作模具适用于任何柔性的数字微流控芯片,在确保介电层表面平整度的同时能够完成封装工艺,有效的提高了产品的性能和质量,大大的降低芯片的生产制造成本。
附图说明
27.图1为现有技术中微流控芯片的结构示意图。
28.图2为本发明的一种具体实施例微流控芯片的结构示意图。
29.图3为本发明的另一种具体实施例微流控芯片的结构示意图。
30.图4为本发明的一种具体实施例工艺流程图一。
31.附图说明:1-介电层,2-电路层,8-液滴,7-底座,5-疏水层,3-离型膜,41-第一模具,411-底座空间腔,42-第二模具,43-第一喷嘴,6-注塑液。
具体实施方式
32.下面结合附图,对本发明的技术方案做进一步解释说明。
33.实施例1:
34.一种介电层表面平整的微流控芯片,包括介电层1及印刷在所述介电层1 上的电路层2,液滴8在介电层1相对电路层2的另一面移动,所述介电层1的未形成所述电路层的一侧为平整面。所述平整面的成型方法为用带有介电层成型面的制作模具对芯片介电层未形成所述电路层的一侧压平处理可以得到表面平整的介电层。
35.所述介电层1作为制备电路层2的基底材料,在所述介电层1上利用蚀刻的方式形成包含电极层的电路层2,所述电路层2用于驱动位于所述介电层1上与所述电路层相对一面的液滴8。此外,我们还在介电层未形成所述电路层的一侧涂布疏水层5。
36.实施例2:
37.一种介电层表面平整的微流控芯片,包括电路层2和设置在所述电路层2 上的介电层1,所述介电层1的未形成所述电路层的一侧为平整面。所述平整面的成型方法为用带有介电层成型面的制作模具对芯片介电层未形成所述电路层的一侧压平处理可以得到表面平整的介电层。
38.实施例3:
39.一种微流控芯片,包括介电层1和设置在所述介电层1上的电路层2,所述介电层1的未形成所述电路层的一侧为平整面。所述介电层1外侧涂布疏水层5。所述电路层2包括依次形成在介电层1上的电极层、绝缘层以及电线层,电极层、绝缘层以及电线层共同构成电路层2且以堆叠的形式形成为多层结构。将上述微流控芯片放入制作模具的铸造腔中,芯片
介电层1未形成所述电路层的一侧与介电层成型面44贴合,液态树脂自与电路层2同侧的第一喷嘴43进入铸造腔并充满铸造腔,对微流控芯片进行挤压使其贴紧介电层成型面44。注塑完成后电路层一侧形成树脂底座完成封装,介电层具有平整表面。
40.实施例4:
41.一种介电层表面平整的微流控芯片制作模具,包括:第一模具41、第二模具42,所述第一模具41连接有第一喷嘴43。所述第二模具42上设置有介电层成型面44。第一模具41、第二模具42贴合后中部形成铸造腔,所述介电层1 的未形成所述电路层的一侧朝向第二模具42的介电层成型面44,注塑液6自第一喷嘴43进入铸造腔,挤压微流控芯片,介电层成型面44与介电层1未形成所述电路层的一侧相配合成型。
42.实施例5:
43.一种介电层表面平整的微流控芯片制作模具,包括:第一模具41、第二模具42,所述第一模具41连接有第一喷嘴43,所述第一模具41上设置有底座空间腔411,所述第二模具42上设置有介电层成型面44。第一模具41、第二模具 42贴合后中部形成铸造腔,微流控芯片设置于其中,所述介电层1的未形成所述电路层的一侧朝向第二模具42的介电层成型面44,注塑液6自第一喷嘴43 进入铸造腔,挤压微流控芯片,介电层成型面44与介电层1未形成所述电路层的一侧相配合成型得到平整面。待冷却后将第一模具41、第二模具42分开,电路层2外侧形成注塑底座7。即可得到本发明具有平整介电层的微流控芯片。
44.为了保护介电层表面在高温高压注塑过程中不被破坏,我们在注塑前在介电层1未形成所述电路层的一侧设置一层离型膜3。
45.本发明所采用的技术方案通过注塑液对位于工艺模具内的微流控芯片进行挤压,使得微流控芯片的介电层未形成所述电路层的一侧均匀的受力,在介电层成型面的配合下形成平整表面。
46.以上详细描述了本发明的设计思路,本发明的技术方案不限于上述实施方式中的具体细节,在本发明的技术构思范围内,可以对本发明的技术方案进行多种变换,这些简单变型均属于本发明的保护范围。