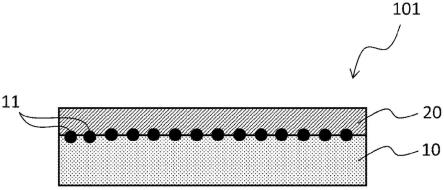
1.本发明涉及排气净化催化剂装置。
背景技术:2.作为将从柴油发动机排出的排气中的nox在向大气中放出之前进行还原净化的技术,已知有选择性接触还原(scr:selective catalytic reduction)系统。scr系统是使用还原剂、例如氨来将排气中的no
x
还原为n2的技术。
3.在该scr系统中,为了提高no
x
的还原净化率,有时还原剂被过量地使用,在该情况下,在no
x
的还原中未被使用的未反应的还原剂从scr催化剂排出。在作为还原剂使用了氨的情况下,来自scr催化剂的氨的排出有时被称为“氨逃逸”。
4.希望逃逸了的氨在利用asc(ammonia slip catalyst:氨逃逸催化剂)进行氧化净化后向大气中放出。于是,在scr系统中,asc例如与scr层层叠或者以配置于scr层的后段的状态来并用的情况较多。
5.在这方面,在专利文献1中公开了一种选择性氨氧化用的二官能性催化剂,其包含铂(pt)、第二金属、耐火性金属氧化物及沸石。在该专利文献1中记载了asc的一般的构成。
6.另外,在专利文献2中记载了一种用于选择性氨氧化的二元金属催化剂,其包含二氧化硅/氧化铝比(sar)小于30的分子筛,并且,该分子筛包含离子交换铜(cu)及离子交换铂(pt)。
7.再者,在专利文献3中公开了一种利用co脉冲法来测定担载于载体上的贵金属催化剂粒子的平均粒径的方法。在专利文献3的技术中,即使是载体包含显示osc(oxygen strage capacity:氧吸藏释放能力)的材料的情况,co脉冲也不被载体消耗,实质上全部的co被贵金属催化剂粒子吸附。因而,根据专利文献3所公开的方法说明了能够准确地评价贵金属催化剂粒子的状态。
8.在先技术文献
9.专利文献
10.专利文献1:日本特表2010-519039号公报
11.专利文献2:日本特表2012-507400号公报
12.专利文献3:日本特开2005-283129号公报
技术实现要素:13.作为在asc中的nh3氧化净化的副反应生成物,生成n2o。n2o是影响到地球温暖化的温室效应气体,因此其排出量应该被抑制。
14.在具备asc的scr系统中,将生成的n2o利用scr来进行净化是困难的。因而,希望asc中的n2o的生成量尽可能少。
15.本发明是鉴于上述的情况而完成的,其目的是提供nh3氧化净化效率充分高、且n2o的生成量少的排气净化催化剂装置。
16.解决上述课题的本发明如下。
17.[方案1]一种排气净化催化剂装置,是包含基材和所述基材上的scr催化剂层的排气净化催化剂装置,
[0018]
所述基材包含直接担载于所述基材上的催化剂贵金属粒子,
[0019]
所述催化剂贵金属粒子包含pt,
[0020]
所述催化剂贵金属粒子的平均粒径为30nm以上且120nm以下。
[0021]
[方案2]根据方案1所述的排气净化催化剂装置,
[0022]
相对于所述催化剂贵金属粒子的总质量,所述催化剂贵金属粒子中的pt以外的贵金属的含有比例为10质量%以下。
[0023]
[方案3]根据方案1或2所述的排气净化催化剂装置,
[0024]
所述催化剂贵金属粒子的平均粒径超过50nm且为100nm以下。
[0025]
[方案4]根据方案1~3的任一项所述的排气净化催化剂装置,
[0026]
所述scr催化剂层包含掺杂有cu或fe的沸石。
[0027]
[方案5]根据方案1~4的任一项所述的排气净化催化剂装置,
[0028]
所述scr催化剂层包含选自cu-cha型沸石、cu-bea型沸石、fe-mfi型沸石和fe-bea型沸石中的至少1种。
[0029]
[方案6]根据方案1~5的任一项所述的排气净化催化剂装置,
[0030]
所述催化剂贵金属粒子还包含pd。
[0031]
[方案7]根据方案1~6的任一项所述的排气净化催化剂装置,
[0032]
所述排气净化催化剂装置实质上不包含直接担载于所述基材上的催化剂贵金属粒子以外的贵金属。
[0033]
[方案8]根据方案1~7的任一项所述的排气净化催化剂装置,
[0034]
还具有包含氧化铈(ceria)的osc层。
[0035]
[方案9]根据方案8所述的排气净化催化剂装置,
[0036]
所述氧化铈以氧化铈-氧化锆(zirconia)复合氧化物的形态包含于所述osc层。
[0037]
[方案10]根据方案8或9所述的排气净化催化剂装置,
[0038]
在所述基材与所述scr催化剂层之间具有所述osc层。
[0039]
根据本发明,能提供nh3氧化净化效率充分高、且n2o的生成量少的排气净化催化剂装置。
附图说明
[0040]
图1是示出本发明的排气净化催化剂装置的构成的一例的概略截面图。
[0041]
图2是示出本发明的排气净化催化剂装置的构成的另一例的概略截面图。
具体实施方式
[0042]
[排气净化催化剂装置]
[0043]
本发明的排气净化装置,是包含基材和基材上的scr催化剂层的排气净化装置,
[0044]
基材包含直接担载于该基材上的催化剂贵金属粒子,
[0045]
催化剂贵金属粒子包含pt,
[0046]
催化剂贵金属粒子的平均粒径为30nm以上且120nm以下。
[0047]
在本发明的排气净化装置中,利用基材上的scr催化剂层,进行以氨为还原剂的、基于nox的选择接触还原的净化。此时,过量地供给且在nox的选择接触还原中未被使用的剩余的氨由直接担载于基材上的催化剂贵金属粒子氧化净化。
[0048]
本发明的排气净化装置,也可以除了上述的基材及scr催化剂层以外还具有包含氧化铈的osc层(氧贮藏)。
[0049]
osc层显示氧吸藏释放能力,具有在稀气氛下吸藏氧但在浓气氛下放出氧的功能。因而,直接担载于基材上的催化剂贵金属粒子的nh3氧化净化活性提高,尤其是在低温区域中的nh3氧化净化能力进一步提高。因此,该osc层优选配置于离催化剂贵金属粒子近的场所,例如,可以存在于基材与scr催化剂层之间。
[0050]
再者,在以往已知的asc中,作为nh3的氧化催化剂发挥功能的pt以担载于大面积的无机氧化物载体粒子上的状态存在于基材上的催化剂涂层中。在该情况下,pt作为比较小的粒径的微小粒子担载于载体粒子上。
[0051]
然而,本发明人发现:根据具有包含担载于大面积的载体上的比较小的粒径的pt粒子的催化剂涂层的构成的asc,在n2o的生成量的抑制上存在界限。
[0052]
于是,在本发明中,通过将pt直接担载于基材上且设为比较大的粒径的粒子,得到了nh3氧化净化效率优异、并且n2o的生成量少的排气净化催化剂装置。
[0053]
以下,一边参照附图,一边对本发明的排气净化催化剂装置的典型的构成进行说明。
[0054]
在图1及图2中示出了本发明的排气净化催化剂装置的构成的例子。
[0055]
图1的排气净化催化剂装置(101),包含基材(10)和基材(10)上的scr催化剂层(20)。该排气净化催化剂装置(101)中的基材(10)包含直接担载于基材(10)上的催化剂贵金属粒子(11)。
[0056]
在图2的排气净化催化剂装置(102)中,包含基材(10)和基材(10)上的scr催化剂层(20),并且,基材(10)包含直接担载于基材(10)上的催化剂贵金属粒子(11),这与图1的排气净化催化剂装置(101)是同样的。然而,该排气净化催化剂装置(102)在基材(10)与scr催化剂层(20)之间具有osc层(30)。
[0057]
在图1的排气净化催化剂装置(101)及图2的排气净化催化剂装置(102)中,催化剂贵金属粒子(11)包含pt。该催化剂贵金属粒子(11)的平均粒径为30nm以上且120nm以下。
[0058]
图2的排气净化催化剂装置(102)中的osc层(30)包含氧化铈。osc层(30)中的氧化铈例如可以以氧化铈-氧化锆复合氧化物的形态包含于osc层(30)中。
[0059]
以下,对本发明的排气净化装置的各构成要素依次进行说明。
[0060]
《基材》
[0061]
作为本发明的排气净化催化剂装置中的基材,能够使用作为排气净化催化剂装置的基材而一般所使用的基材。例如可以是由堇青石、sic、不锈钢、无机氧化物粒子等材料构成的例如直流型的整体式蜂窝基材。
[0062]
本发明的排气净化催化剂装置中的基材,包含直接担载于基材上的催化剂贵金属粒子。所谓“直接担载于基材上”意味着催化剂贵金属粒子不藉由构成基材的无机氧化物以外的无机氧化物载体而附着于基材。
[0063]
(催化剂贵金属粒子)
[0064]
催化剂贵金属粒子包含pt。
[0065]
催化剂贵金属粒子也可以包含pt以外的贵金属。催化剂贵金属粒子中包含的pt以外的贵金属例如可以是pt以外的铂族元素,例如可以是选自ru、rh、pd、os和ir中的1种以上,可以是选自rh和pd中的1种以上,尤其可以是pd。
[0066]
包含pt并且包含pt以外的贵金属的催化剂贵金属粒子,粒径的控制容易,另一方面,pt以外的贵金属的含量过度大的催化剂贵金属粒子有时产生n2o的生成量多这一问题。从这些观点出发,相对于所述催化剂贵金属粒子的总质量,催化剂贵金属粒子中的、pt以外的贵金属的含有比例可以为20质量%以下、18质量%以下、15质量%以下、12质量%以下、10质量%以下、8质量%以下、5质量%以下、3质量%以下、或0质量%,可以为超过0质量%、1质量%以上、3质量%以上、5质量%以上、8质量%以上、或10质量%以上。
[0067]
催化剂贵金属粒子的平均粒径为30nm以上且120nm以下。若催化剂贵金属粒子的平均粒径小于30nm,则有时n2o的生成量变多。另一方面,若催化剂贵金属粒子的平均粒径超过120nm,则有时nh3氧化净化能力受损。催化剂贵金属粒子的平均粒径,从抑制n2o的生成的观点出发,可以为例如35nm以上、40nm以上、45nm以上、50nm以上、超过50nm、55nm以上、60nm以上、或65nm以上,从使nh3氧化净化能力提高的观点出发,可以为110nm以下、100nm以下、90nm以下、80nm以下、75nm以下、70nm以下、或65nm以下。催化剂贵金属粒子的平均粒径,作为典型例如可以超过50nm且为100nm以下。
[0068]
在本说明书中,催化剂贵金属粒子的平均粒径是利用一氧化碳(co)脉冲法测定出的值。催化剂贵金属粒子的平均粒径的测定,依照专利文献3(日本特开2005-283129号公报)中所记载的方法进行。
[0069]
具体而言,将排气净化催化剂装置粉碎成例如0.5mm以下的细片而得到粉碎物作为测定试样,进行氧化处理及还原处理后,进行利用二氧化碳(co2)来进行的处理,然后供于基于co脉冲法的测定。氧化处理及还原处理可以在适当的高温、例如400℃下进行。利用co2来进行的处理可以在比较低的温度、例如50℃下进行。基于co脉冲法的测定可以在比较低的温度、例如50℃下进行。
[0070]
在该方法中,在基于co脉冲法的测定之前进行测定试样的co2处理是重要的。在排气净化催化剂装置包含osc材料的情况下,通过该co2处理,该osc材料的吸附位点被co2堵塞。因而可以认为,若在co2处理后施行co脉冲法,则向试样供给的co不会被osc材吸附、消耗,实质上全部量吸附于贵金属催化剂粒子。
[0071]
因此,能够估算为:通过co脉冲法向试样供给的co量与排出气体中包含的co量的差量是吸附于催化剂贵金属粒子的co的量。
[0072]
而且,假定为每1个在催化剂贵金属粒子的表面露出的催化剂贵金属原子吸附1个co,能够算出催化剂贵金属粒子的平均粒径。
[0073]
根据吸附co量进行的催化剂贵金属粒子的平均粒径的计算例如可以如以下那样进行。
[0074]
若将co吸附量设为v
chem
(cm3),将每1原子的催化剂贵金属的金属截面积设为ρm(nm2),将每1g测定试样的催化剂贵金属粒子的质量设为c(g),则每1g催化剂贵金属粒子的表面积am(metal)(m2/g)由下述数学式(1)表示。数学式(1)中的sf被称为“化学计量因数”,
是表示每1个催化剂贵金属原子吸附几个co的数。在本说明书中,如上述那样假定为sf=1。
[0075][0076]
通过数学式(1)得到的每1g催化剂贵金属粒子的表面积am(metal)(m2/g),能够使用催化剂贵金属粒子的平均半径r(cm)、每1g催化剂贵金属粒子的催化剂贵金属粒子数α(个)、及催化剂贵金属粒子的质量c(g)来如下述数学式(2)那样改写。
[0077][0078]
另一方面,每1g催化剂贵金属粒子的体积(cm3),使用催化剂贵金属粒子的平均半径r(cm)、每1g催化剂贵金属粒子的催化剂贵金属粒子数α(个)、催化剂贵金属粒子的质量c(g)、及催化剂贵金属的密度ρ(g/cm3)来由下述数学式(3)表示。
[0079][0080]
根据数学式(2)及(3),催化剂贵金属粒子的平均半径r(cm)能够采用下述数学式(4)计算。
[0081]
r=3/(am(metal)
×
ρ
×
106)
ꢀꢀꢀ
(4)
[0082]
因此,能够采用下述数学式(5)来得到催化剂贵金属粒子的平均粒径d(nm)。
[0083]
d=2r
×
109ꢀꢀꢀ
(5)
[0084]
在本发明的排气净化催化剂装置中,直接担载于基材上的催化剂贵金属粒子的担载量是任意的。然而,作为每1l基材的催化剂贵金属粒子的质量,从确保充分高的nh3氧化净化能力的观点出发,可以为例如0.01g/l以上、0.03g/l以上、0.05g/l以上、0.08g/l以上、或0.10g/l以上,从使nh3氧化净化能力与催化剂装置的制造成本的平衡适当的观点出发,可以为例如2.00g/l以下、1.50g/l以下、1.00g/l以下、0.80g/l以下、0.50g/l以下、0.30g/l以下、或0.10g/l以下。
[0085]
本发明的排气净化催化剂装置,优选实质上不包含直接担载于基材上的催化剂贵金属粒子以外的贵金属。所谓“排气净化催化剂装置实质上不包含直接担载于基材上的催化剂贵金属粒子以外的贵金属”意味着:排气净化催化剂装置中包含的总贵金属质量之中的、直接担载于基材上的催化剂贵金属粒子以外的贵金属的质量所占的比例为5质量%以下、3质量%以下、1质量%以下、0.5质量%以下、0.3质量%以下、或0.1质量%以下,或者,排气净化催化剂装置完全不包含直接担载于基材上的催化剂贵金属粒子以外的贵金属。
[0086]
《scr催化剂层》
[0087]
本发明的排气净化催化剂装置,在包含被直接担载的催化剂贵金属粒子的基材上具有scr催化剂层。该scr催化剂层包含掺杂有cu或fe的沸石。scr催化剂层例如也可以还包含掺杂有cu或fe的沸石以外的无机氧化物、粘合剂等的任意成分。
[0088]
(掺杂有cu或fe的沸石)
[0089]
在scr催化剂层中,掺杂有cu或fe的沸石作为nox的基于nh3的选择还原催化剂发挥功能。
[0090]
scr催化剂层中的沸石的晶体结构是任意的。若将能够应用于本发明的质子沸石的晶体结构与各自的结构码(记载于括号内)一起示出,则例如可以是a型(lta)、铁氧体(fer)、mcm-22(mww)、zsm-5(mfi)、丝光沸石(mor)、l型(ltl)、x型或y型(fau)、β型(bea)、菱沸石(cha)等,可以是cdo型、gon型等。
[0091]
在本说明书中,关于掺杂有cu或fe的沸石,在母体沸石的结构码之前附带“cu
‑”
或“fe
‑”
来参照。例如,将在菱沸石型的母体沸石中掺杂有cu的沸石记载为“cu-cha型沸石”。
[0092]
本发明中的scr催化剂层可以包含选自cu-cha型沸石、cu-bea型沸石、fe-mfi型沸石和fe-bea型沸石中的至少1种。
[0093]
针对沸石的、cu或fe的掺杂量,以掺杂了cu或fe的沸石的总质量为基准,从确保充分高的nox还原净化活性的观点出发,可以cu和fe各自独立地为例如0.5质量%以上、1.0质量%以上、1.5质量%以上、2.0质量%以上、2.5质量%以上、或3.0质量%以上。
[0094]
关于针对沸石的、cu或fe的掺杂量的上限值,从提高nox还原净化活性的观点来看,没有限制,但即使过度地增加该掺杂量,nox还原净化活性也并不会无限制地上升。因此,从维持排气净化催化剂装置的适当的制造成本的观点出发,针对沸石的、cu或fe的掺杂量,以掺杂了cu或fe的沸石的总质量为基准,可以cu和fe各自独立地为例如20质量%以下、15质量%以下、12质量%以下、10质量%以下、8质量%以下、或6质量%以下。
[0095]
掺杂有cu或fe的沸石的量,作为每1l基材的该沸石的质量,从确保充分高的nox选择还原净化能力的观点出发,可以为例如30g/l以上、40g/l以上、50g/l以上、60g/l以上、70g/l以上、或80g/l以上,例如从降低催化剂装置的压力损失的观点出发,可以为例如200g/l以下、150g/l以下、120g/l以下、110g/l以下、100g/l以下、或90g/l以下。
[0096]
(掺杂有cu或fe的沸石以外的无机氧化物)
[0097]
scr催化剂层也可以还包含掺杂有cu或fe的沸石以外的无机氧化物。scr催化剂层中包含的无机氧化物粒子例如可以是选自铝、硅、钛、锆、稀土元素等中的1种或2种以上的元素的氧化物的粒子。作为无机氧化物粒子,具体地可列举例如氧化铝粒子、氧化铈粒子、氧化铈-氧化锆复合氧化物粒子等。
[0098]
(粘合剂)
[0099]
scr催化剂层也可以还包含粘合剂。作为粘合剂,可列举例如氧化铝溶胶、氧化锆溶胶、二氧化硅溶胶、二氧化钛溶胶等。
[0100]
《osc层》
[0101]
本发明的排气净化催化剂装置也可以还具有包含氧化铈的osc层。
[0102]
(氧化铈)
[0103]
osc层包含氧化铈。
[0104]
osc层的氧化铈量,从确保充分高的osc能力的观点出发,作为每1l基材的氧化铈量,可以为例如1g/l以上、3g/l以上、5g/l以上、或7g/l以上。另一方面,从降低催化剂装置的压力损失的观点出发,每1l基材的氧化铈量可以为例如50g/l以下、40g/l以下、30g/l以下、20g/l以下、15g/l以下、或10g/l以下。
[0105]
osc层的氧化铈,可以是氧化铈单独的形态,也可以以氧化铈-氧化锆复合氧化物的形态包含于osc层,也可以是它们的混合物。osc层中包含的氧化铈-氧化锆复合氧化物中的氧化铈含量,可以为例如5质量%以上、10质量%以上、20质量%以上、30质量%以上、40
质量%以上、50质量%以上、60质量%以上、70质量%以上、80质量%以上、或90质量%以上。
[0106]
如上所述,osc层显示氧吸藏释放能力,具有使直接担载于基材上的催化剂贵金属粒子的nh3氧化净化活性提高的功能。因此,该osc层优选配置于离催化剂贵金属粒子近的场所,例如可以存在于基材与scr催化剂层之间。
[0107]
(任意成分)
[0108]
osc层也可以包含氧化铈和氧化铈-氧化锆复合氧化物以外的任意成分。osc层的任意成分,可以是例如氧化铈和氧化铈-氧化锆复合氧化物以外的无机氧化物、粘合剂等。
[0109]
osc层中包含的、氧化铈和氧化铈-氧化锆复合氧化物以外的无机氧化物粒子例如可以是选自铝、硅、钛、锆、稀土元素(但是,将铈除外)等中的1种或2种以上的元素的氧化物的粒子。作为无机氧化物粒子,具体地可列举例如氧化铝粒子、氧化锆粒子等。
[0110]
作为osc层中包含的粘合剂,可列举例如氧化铝溶胶、氧化锆溶胶、二氧化硅溶胶、二氧化钛溶胶等。
[0111]
[排气净化催化剂装置的制造方法]
[0112]
本发明的排气净化催化剂装置只要具有上述的构成即可,可以采用任意的方法来制造。
[0113]
然而,本发明的排气净化催化剂装置例如可以采用下述的本发明的排气净化催化剂装置的制造方法来制造,该制造方法包含以下工序:
[0114]
在基材上直接担载催化剂贵金属粒子(催化剂贵金属粒子担载工序);以及
[0115]
在直接担载有催化剂贵金属粒子的基材上形成scr催化剂层(scr催化剂层形成工序)。
[0116]
本发明的排气净化催化剂装置的制造方法,例如也可以在催化剂贵金属粒子担载工序之后且scr催化剂层形成工序之前还包含形成osc层的工序(osc层形成工序)。
[0117]
(催化剂贵金属粒子担载工序)
[0118]
在本工序中,在基材上直接担载催化剂贵金属粒子。
[0119]
基材可以根据期望的排气净化催化剂装置中的基材来适当选择。例如可以是堇青石制的直流型整体式蜂窝基材。
[0120]
通过在该基材上涂覆包含催化剂贵金属前驱体的涂布液,并进行烧成,从而在基材上直接担载催化剂贵金属粒子。在涂覆后且烧成前,可以根据需要进行涂层的干燥。
[0121]
作为涂布液中的催化剂贵金属前驱体,可以是期望的催化剂贵金属的例如硝酸盐、硫酸盐、卤化物、配位化合物等。配位化合物例如可以是包含四氨络离子的配位化合物等。
[0122]
涂布液的溶剂可以是水或水性有机溶剂、或者它们的混合物,作为典型是水。
[0123]
涂布液的涂覆以及涂覆后的干燥及烧成分别可以依照公知的方法进行。
[0124]
(scr催化剂层形成工序)
[0125]
在本工序中,在直接担载有催化剂贵金属粒子的基材上形成scr催化剂层。
[0126]
本工序例如可以通过在直接担载有催化剂贵金属粒子的基材上涂覆包含掺杂有cu或fe的沸石及根据需要的除此以外的任意成分的浆料、并进行烧成来进行。在涂覆后、烧成前,也可以根据需要来进行涂层的干燥。
[0127]
浆料的分散介质可以是水或水性有机溶剂、或者它们的混合物,作为典型是水。
[0128]
浆料的涂覆、以及涂覆后的干燥及烧成分别可以依照公知的方法来进行。
[0129]
(osc层形成工序)
[0130]
本工序是形成osc层的工序。该osc层形成工序例如可以在催化剂贵金属粒子担载工序之后、scr催化剂层形成工序之前进行。
[0131]
本工序,除了将含有的成分根据期望的osc层来适当地进行变更以外,可以与scr催化剂层形成工序同样地进行。
[0132]
实施例
[0133]
[催化剂涂层形成用浆料的制备]
[0134]
(1)含pt溶液的制备
[0135]
(1-1)含pt溶液a1
[0136]
向二氯四氨合铂(ii)水溶液(金属pt换算0.2g)中添加纯水400g及有机多糖类,搅拌混合3小时,得到了含pt溶液a1。
[0137]
(1-2)含pt-pd溶液a2
[0138]
向含pt溶液a1中进一步添加二氯四氨合钯(ii)水溶液(金属pd换算0.02g)并使其溶解,得到了含pt-pd溶液a2。
[0139]
(1-3)含pt-pd溶液a3
[0140]
向含pt溶液a1中进一步添加二氯四氨合钯(ii)水溶液(金属pd换算0.01g)并使其溶解,得到了含pt-pd溶液a3。
[0141]
(2)含沸石浆料的制备
[0142]
(2-1)含沸石浆料b1
[0143]
使cu-cha型沸石(cu掺杂量5质量%,sar8)85g及二氧化硅溶胶粘合剂15g分散于纯水200g中,得到了含沸石浆料b1。
[0144]
(2-2)含沸石浆料b2
[0145]
除了取代cu-cha型沸石而使用了cu-bea型沸石(cu掺杂量5.9质量%,sar25)85g以外,与含沸石浆料b1的制备同样地操作,得到了含沸石浆料b2。
[0146]
(2-3)含沸石浆料b3
[0147]
除了取代cu-cha型沸石而使用了fe-mfi型沸石(fe掺杂量2.0质量%,sar30)85g以外,与含沸石浆料b1的制备同样地操作,得到了含沸石浆料b3。
[0148]
(2-4)含沸石浆料b4
[0149]
除了取代cu-cha型沸石而使用了fe-bea型沸石(fe掺杂量5.0质量%,sar25)85g以外,与含沸石浆料b1的制备同样地操作,得到了含沸石浆料b4。
[0150]
(3)含cz浆料
[0151]
使氧化铈-氧化锆复合氧化物(氧化铈含量56.5质量%)(cz)15g分散于水,得到了含cz浆料。
[0152]
(4)含pt/al2o3浆料
[0153]
将二氯四氨合铂(ii)水溶液(金属pt换算0.1g)溶解于纯水45g中,得到了水溶液。向该水溶液中添加氧化铝15g,搅拌了1小时。接着,在120
°
加热5小时,使水蒸发后,在500℃烧成1小时,得到了pt/al2o3粉末。通过使得到的pt/al2o3粉末分散于纯水中,来制备了含
pt/al2o3浆料。
[0154]
[实施例1]
[0155]
(1)排气净化催化剂装置的制造
[0156]
在直流型的堇青石制蜂窝基材(容量约1l)上,遍及蜂窝基材的全长而涂覆含pt溶液a1,在500℃烧成1小时,从而在蜂窝基材上直接担载了由pt构成的催化剂贵金属粒子。
[0157]
接着,在直接担载了催化剂贵金属粒子的蜂窝基材上,遍及该蜂窝基材的全长而涂覆含沸石浆料b1,在500℃烧成1小时,形成scr催化剂层,由此,制造了实施例1的排气净化催化剂装置。
[0158]
(2)排气净化催化剂装置的评价
[0159]
(2-1)催化剂贵金属粒子的平均粒径的测定
[0160]
催化剂贵金属粒子(pt粒子或pt-pd粒子)的平均粒径采用一氧化碳(co)脉冲吸附法来测定。
[0161]
对于将上述得到的排气净化催化剂装置粉碎成0.5mm以下的细片而得到的测定试样,进行基于以下的条件的前处理后,利用co脉冲吸附法进行气体化学吸附测定来调查co的吸附量,根据假定为1分子pt吸附1个co而算出的pt的吸附表面积和排气净化催化剂装置中的pt的担载量,来算出了pt的平均粒径。
[0162]
试样的前处理条件如下。
[0163]
第1步骤:一边以40℃/分的升温速度从室温升温至400℃,一边流通包含10体积%的氧(o2)的he气;
[0164]
第2步骤:在到达400℃后,维持该温度,流通包含10体积%的氧(o2)的he气15分钟;
[0165]
第3步骤:维持400℃,流通氦(he)15分钟;
[0166]
第4步骤:维持400℃,流通包含10体积%的氢(h2)的he气15分钟;
[0167]
第5步骤:维持400℃,流通he 15分钟;
[0168]
第6步骤:一边以35℃/分的降温速度从400℃降温至50℃,一边流通he;
[0169]
第7步骤:维持50℃,流通包含10体积%的二氧化碳(co2)的he气10分钟;
[0170]
第8步骤:维持50℃,流通he 10分钟。
[0171]
co脉冲吸附法中的探测气体设为包含1体积%的co的he气。另外,co吸附量根据利用tcd检测器进行的热导率测定来算出。
[0172]
(2-2)排气净化能力的评价
[0173]
一边使水分浓度10体积%的空气在得到的排气净化催化剂装置中流通,一边在630℃加热50小时,来进行了水热耐久处理。
[0174]
将包含浓度已知的nh3及no
x
的模型气体向水热耐久处理后的排气净化催化剂装置中导入而使其流通,测定排出气体中的nh3及no
x
浓度,分别求出了采用以下的数学式算出的nh3氧化率及n2o选择率。
[0175]
nh3氧化率(%)={(导入气体中的nh3浓度-排出气体中的nh3浓度)/导入气体中的nh3浓度}
×
100
[0176]
n2o选择率(%)={排出气体中的n2o浓度
×
2/(导入气体中的nh3浓度-排出气体中的nh3浓度)}
×
100
[0177]
模型气体的导入条件按以下那样设定:
[0178]
模型气体导入温度:250℃
[0179]
模型气体的组成:no:0ppm、nh3:500ppm、o2:10%、h2o:5%及n2平衡
[0180]
模型气体导入时的空间速度:60000h-1
[0181]
关于实施例1的排气净化催化剂装置,将在上述的条件下测定出的nh3氧化率及n2o选择率在表1中示出。
[0182]
[实施例2]
[0183]
取代含pt溶液a1而使用含pt-pd溶液a2,将直接担载于蜂窝基材上的催化剂贵金属粒子设为pt-pd合金粒子(pd 9.1质量%),除此以外,与实施例1同样地操作,制造出实施例2的排气净化催化剂装置并进行了评价。评价结果在表1中示出。
[0184]
[实施例3]
[0185]
通过将与实施例2同样地制造出的排气净化催化剂装置在630℃进一步烧成50小时,来制造了实施例3的排气净化催化剂装置。
[0186]
关于得到的排气净化催化剂装置,与实施例1同样地进行了评价。评价结果在表1中示出。
[0187]
[实施例4]
[0188]
取代含pt溶液a1而使用含pt-pd溶液a3,将直接担载于蜂窝基材上的催化剂贵金属粒子设为pt-pd合金粒子(pd 16.7质量%),除此以外,与实施例1同样地操作,制造出实施例4的排气净化催化剂装置并进行了评价。评价结果在表1中示出。
[0189]
[实施例5~7]
[0190]
取代含沸石浆料b1而分别使用了含沸石浆料b2(实施例5)、b3(实施例6)及b4(实施例7),除此以外,与实施例1同样地操作,制造出实施例5~7的排气净化催化剂装置并进行了评价。评价结果在表1中示出。
[0191]
[实施例8]
[0192]
(1)排气净化催化剂装置的制造
[0193]
在与在实施例1中使用的基材相同的类型的堇青石制蜂窝基材(容量约1l)上,遍及蜂窝基材的全长而涂覆含pt溶液a1,在500℃烧成1小时,从而在蜂窝基材上直接担载了由pt构成的催化剂贵金属粒子。接着,在直接担载了催化剂贵金属粒子的蜂窝基材上,遍及该蜂窝基材的全长而涂覆含cz浆料,使其干燥,形成了osc层。进而,在该osc层上,遍及蜂窝基材的全长而涂覆含沸石浆料b1,在500℃烧成1小时,形成scr催化剂层,由此,制造了实施例8的排气净化催化剂装置。
[0194]
(2)排气净化催化剂装置的评价
[0195]
关于得到的排气净化催化剂装置,与实施例1同样地进行了评价。评价结果在表1中示出。
[0196]
[实施例9]
[0197]
取代含pt溶液a1而使用含pt-pd溶液a2,将直接担载于蜂窝基材上的催化剂贵金属粒子设为pt-pd合金粒子(pd 9.1质量%),除此以外,与实施例8同样地操作,制造出实施例9的排气净化催化剂装置并进行了评价。评价结果在表1中示出。
[0198]
[比较例1]
[0199]
(1)排气净化催化剂装置的制造
[0200]
在与在实施例1中使用的基材相同的类型的堇青石制蜂窝基材(容量约1l)上,从排气流的下游端起在基材长度的80%的范围涂覆含pt/al2o3浆料,在500℃烧成1小时,从而在蜂窝基材上形成了包含pt/al2o3的nh3氧化催化剂层。
[0201]
接着,在形成有nh3氧化催化剂层的蜂窝基材上,从排气流的上游端起遍及基材全长地涂覆含沸石浆料b1,在500℃烧成1小时,形成scr催化剂层,由此,制造了比较例1的排气净化催化剂装置。
[0202]
(2)排气净化催化剂装置的评价
[0203]
关于得到的排气净化催化剂装置,与实施例1同样地进行了评价。评价结果在表1中示出。
[0204]
[比较例2]
[0205]
通过将与比较例1同样地制造出的排气净化催化剂装置在630℃进一步烧成50小时,来制造了比较例2的排气净化催化剂装置。
[0206]
关于得到的排气净化催化剂装置,与实施例1同样地进行了评价。评价结果在表1中示出。
[0207]
[比较例3]
[0208]
通过将与实施例1同样地制造出的排气净化催化剂装置在630℃进一步烧成50小时,来制造了比较例3的排气净化催化剂装置。
[0209]
关于得到的排气净化催化剂装置,与实施例1同样地进行了评价。评价结果在表1中示出。
[0210][0211]
参照表1,可理解到以下的内容。
[0212]
在催化剂贵金属粒子的平均粒径大的、比较例3的排气净化催化剂装置中,nh3氧
化率低为15%。另一方面,在催化剂贵金属粒子的平均粒径小的、比较例1及比较例2的排气净化催化剂装置中,n2o选择率高为86%(比较例1)或60%(比较例2)。
[0213]
与此相对,在催化剂贵金属粒子的平均粒径为30nm以上且120nm以下的、本发明的实施例1~9的排气净化催化剂装置中,nh3氧化率高为83%以上,并且,n2o选择率显示低为58%以下的值,nh3氧化净化能力及n2o逃逸特性这两者都优异。在这些实施例之中的、催化剂贵金属粒子中包含的pd量为0.15g/l以下的实施例1~3及5~9中,n2o选择率显示出44%以下的极低的值。
[0214]
另外,确认到:在本发明的排气净化催化剂装置中,即使是将scr催化剂层中包含的沸石的种类变更为cu-cha型(实施例1~4、8及9)、cu-bea型(实施例5)、fe-mfi型(实施例6)、及fe-bea(实施例7)的情况,nh3氧化净化能力和n2o逃逸特性这两者也都优异。
[0215]
而且,如在实施例8及9的排气净化催化剂装置的评价结果中所看到的那样,确认到:在基材与scr催化剂层之间配置了osc层的情况下,nh3氧化净化能力及n2o逃逸特性不会受损,尤其是nh3氧化净化能力显示出极高的性能。
[0216]
附图标记说明
[0217]
10 基材
[0218]
11 催化剂贵金属粒子
[0219]
20 scr催化剂层
[0220]
30 osc层
[0221]
101、102 排气净化催化剂装置