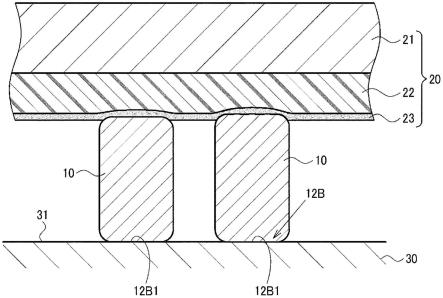
1.本发明涉及电子部件的制造方法,该电子部件的制造方法包含如下工序:涂覆工序,在多个电子部件主体涂覆导电性膏;以及印前工序,该印前工序在涂覆工序之前实施。
背景技术:2.本技术的申请人提出了例如在层叠陶瓷电容器、电感器、热敏电阻等电子部件主体的端面浸渍涂覆导电性膏层,从而在电子部件主体形成外部电极来制造电子部件的装置和方法(专利文献1)。作为在电子部件主体的端面浸渍涂覆导电膏层的涂覆工序之前的工序,专利文献1的图1的(b)公开了印前方法。如图19所示,在印前工序中,针对主面1未铺设导电膏的平台2,使电子部件主体3下降,并使电子部件主体3的端面4与平台2的主面1接触。然后,电子部件主体3上升。同时保持印前的多个电子部件主体3的夹具(支承板)5具有供电子部件主体3嵌入例如橡胶制的夹具主体6的贯通孔7。多个电子部件主体3的全长为l1、l2而不同,从而具有全长差δl的偏差。通过实施印前工序,多个电子部件主体3分别从贯通孔7突出的长度l,即从夹具主体6到多个电子部件主体3的各个端面4的高度l变得均匀。由此,无论是否存在全长差δl,都能够使多个电子部件主体3的各个端面4的位置对齐。
3.现有技术文献
4.专利文献
5.专利文献1:日本特许第6633829号公报
技术实现要素:6.发明所要解决的课题
7.同时被分批处理的电子部件主体3的数量变多时,难以使电子部件主体3嵌入图19所示的夹具主体6的孔7。因此,作为保持多个电子部件主体3的其他夹具,考虑在形成于作为刚体的基材的粘接层粘接并保持电子部件主体3。但是,即使使粘接保持于夹具的电子部件主体3的端面4与平台2接触并进行印前,也不具有图19所示的夹具5的孔7的功能,因此无法使多个电子部件主体3的各个端面4的位置对齐。
8.本发明的几个方式的目的在于提供能够一边粘接并保持多个电子部件主体,一边使多个电子部件主体的各个端面的位置对齐的电子部件的制造方法。
9.用于解决课题的手段
10.(1)本发明的一个方式涉及电子部件的制造方法,该电子部件的制造方法包含如下工序:涂覆工序,分别在多个电子部件主体上涂覆膏;以及印前工序,该印前工序在所述涂覆工序之前实施,其中,所述印前工序包含如下工序:第1工序,使所述多个电子部件主体的各个第1端部粘接于粘接面,该粘接面位于平板材料的露出表面,该平板材料设置于夹具;第2工序,使所述夹具相对于平台相对移动;第3工序,使所述平板材料成为软化状态,使所述多个电子部件主体的与所述各个第1端部相反的一侧的各个第2端部与所述平台接触,由此使所述平板材料变形而使所述各个第2端部的端面的位置对齐;第4工序,在所述各个
第2端部的端面的位置对齐的状态下,使所述平板材料成为固化状态;以及然后使所述夹具相对于所述平台相对移动,具有所述端。
11.根据本发明的一个方式,在设置于夹具的平板材料处于软化状态时,能够使与平台接触的多个电子部件主体的各个第2端部的端面的位置对齐,然后平板材料固化。由此,通过粘接而被夹具保持的多个电子部件主体以各个第2端部的端面的位置对齐的方式被夹具保持。这样,能够一边粘接并保持多个电子部件主体,一边使多个电子部件主体的各个端面的位置对齐。如果在该印前工序之后实施涂覆工序,则能够使涂覆于多个电子部件主体的各个端面的膏的膜厚均匀化。作为相变化为软化和固化的平板材料,能够使用热可塑性树脂(热可塑性粘接剂)、热固化性树脂、热可塑性弹性体、热固化性弹性体等。而且,在这些树脂或弹性体中,尤其能够使用形状记忆树脂、能够软化和固化的刺激响应性材料(凝胶、树脂、弹性体等)等。
12.(2)在本发明的一个方式(1)中,可以是,还包含如下膏去除工序:在所述涂覆工序之后,从在所述夹具所保持的所述多个电子部件主体的所述各个第2端部上涂覆的所述膏去除多余的膏来形成膏层。通过追加该工序,能够提高涂覆形成于多个电子部件主体的膏的膜厚的均匀性。
13.(3)在本发明的一个方式(1)或(2)中,可以是,还包含如下拆卸工序:在所述涂覆工序或所述膏去除工序之后,从所述夹具拆卸所述多个电子部件主体,在所述拆卸工序中,通过使在所述第3工序中变形并且在所述第4工序中固化的所述平板材料再次软化,而成为能够从所述夹具拆卸所述多个电子部件主体的状态。由此,能够降低从夹具拆卸多个电子部件主体时的负荷。另外,为了再利用通过拆卸工序软化的平板材料,例如,能够整形为在上次第1工序中使用的原来的形状(例如平板)并使其固化。另外,在不具有如热固化性树脂那样软化和固化的可逆相的情况下,也可以进行材料再循环而不再利用电子部件主体的拆卸后的平板材料。如果像这样平板材料为一次性,也可以使平板材料强制变形而破坏形状。由此,在拆卸工序中不需要使平板材料再次软化。
14.(4)在本发明的一个方式(1)或(2)中,可以是,还包含如下拆卸工序:在所述涂覆工序或所述膏去除工序之后,从所述夹具拆卸所述多个电子部件主体,在所述拆卸工序中,使在所述第3工序中变形并且在所述第4工序中固化的所述平板材料变形为作为能够从所述夹具拆卸所述多个电子部件主体的状态的、所述软化状态和所述固化状态以外的保形状态。这样,能够直接再利用拆卸工序之后的平板材料。
15.(5)在本发明的一个方式(4)中,可以是,所述平板材料为形状记忆树脂,可以是,在所述第1工序、所述第2工序以及所述拆卸工序中,所述形状记忆树脂被设定为作为被形状记忆的一次赋形的平板形状,在所述第3工序、所述第4工序以及所述第5工序中,所述形状记忆树脂分别被设定为作为使所述各个第2端部的所述端面的位置对齐的所述软化状态或所述固化状态的任意的二次赋形。能够有效地利用形状记忆树脂的形状记忆状态(一次赋形)作为软化状态和固化状态(二次赋形)以外的保形状态。
16.(6)在本发明的一个方式(5)中,可以是,在所述第2工序中,开始进行所述形状记忆树脂向所述软化状态的转移。这样,在电子部件主体与平台接触的同时,形状记忆树脂变形,因此能够缩短印前工序。当然,也可以在第2工序之前的第1工序开始形状记忆树脂向软化状态的转移。
17.(7)在本发明的一个方式(3)中,可以是,所述平板材料为热可塑性树脂,可以是,在所述第1工序和所述第2工序中,所述热可塑性树脂为固化状态,在所述第3工序和所述拆卸工序中,设定为大于等于玻璃化转变点的温度而使所述热可塑性树脂为软化状态,在所述第4工序和所述第5工序中,所述热可塑性树脂成为固化状态。能够有效地利用在市场中提供的、容易得到的热可塑性树脂作为夹具中的能够变形的部件。
18.(8)在本发明的一个方式(5)~(7)中,可以是,所述夹具包含基材和形成所述粘接面的粘接层,所述平板材料夹入配置于所述基材与所述粘接层之间,在所述第3工序中,仿照所述平板材料的变形而使所述粘接层变形。这样,通过粘接层变形,能够使粘接并被保持的多个电子部件主体的各个端面的位置对齐。
19.(9)在本发明的一个方式(7)中,可以是,所述热可塑性树脂为热可塑性粘接剂。如果使用热可塑性粘接剂作为平板材料,不需要成为平板材料和粘接层的双层结构。
20.(10)在本发明的一个方式(7)或(9)中,可以是,在所述拆卸工序中,使所述热可塑性树脂在成型部件内软化。这样,能够使热可塑性树脂可靠地恢复为能够再利用的形状。
21.(11)在本发明的一个方式(1)~(10)中,可以是,通过设置于所述夹具或保持所述夹具的基座的调温部将所述平板材料设定为所述软化状态和所述固化状态。调温部也可以具有加热部和冷却部双方,也可以是例如如珀耳帖元件这样兼用作为加热部和冷却部。通过将调温部设置于夹具或基座,能够高效地对平板材料进行调温。
22.(12)在本发明的一个方式(5)或(6)中,可以是,通过设置于所述夹具或保持所述夹具的基座的调温部将所述形状记忆树脂设定为所述一次赋形和所述二次赋形的各状态。通过将调温部设置于夹具或基座,能够以将形状记忆树脂切换为一次赋形和二次赋形双方并设定的方式进行调温。
23.(13)在本发明的一个方式(1)~(10)中,可以是,通过设置于所述夹具或保持所述夹具的基座的加热部将所述平板材料设定为所述软化状态,通过设置于所述平台的冷却部将所述平板材料设定为所述固化状态。通过将加热部设置于夹具或基座,能够高效地对平板材料进行加热,通过将冷却部设置于平台,能够经由多个电子部件主体对平板材料进行冷却。而且,通过分开地配置加热部和冷却部,能够降低一方对另一方产生的不良影响。
24.(14)在本发明的一个方式(5)或(6)中,可以是,通过设置于所述夹具或保持所述夹具的基座的加热部将所述形状记忆树脂设定为所述软化状态和所述一次赋形,通过设置于所述平台的冷却部将所述形状记忆树脂设定为所述固化状态。通过将加热部设置于夹具或基座,能够高效地对形状记忆树脂进行加热,并将其设定为软化状态或一次赋形,通过将冷却部设置于平台,能够经由多个电子部件主体对形状记忆树脂进行冷却并使其固化。
附图说明
25.图1的(a)和图1的(b)是示出印前工序的图。
26.图2的(a)~图2的(c)是示出涂覆工序的图。
27.图3的(a)~图3的(c)是示出去除多余的膏的工序的图。
28.图4是示出第1和第3实施方式的第1工序的图。
29.图5是示出第1和第3实施方式的第2工序的图。
30.图6是示出第1和第3实施方式的第3和第4工序的图。
31.图7是示出第1和第3实施方式的第5工序的图。
32.图8是示出第1实施方式的拆卸工序的图。
33.图9的(a)、图9的(b)是示出由第1实施方式制造的膏层的膜厚的图。
34.图10是示出第1和第3实施方式的第1工序的图。
35.图11是示出第2实施方式的第2工序的图。
36.图12是示出第2实施方式的第3和第4工序的图。
37.图13是示出第2实施方式的第5工序的图。
38.图14是示出第2实施方式的拆卸工序的图。
39.图15是示出在夹具的基材设置调温部而得到的制造装置的图。
40.图16是示出在固定夹具的基座设置调温部而得到的制造装置的图。
41.图17是示出在夹具的基材设置加热部、在平台设置冷却部而得到的制造装置的图。
42.图18是示出在固定夹具的基座设置加热部、在平台设置冷却部而得到的制造装置的图。
43.图19是示出以往的印前方法的图。
具体实施方式
44.在下述的说明中,提供了用于实施所提出的主题的不同特征的多个不同的实施方式和实施例。当然,这些方式仅仅是例子,并不意味着进行限定。此外,在本公开中,在各种例子中,存在参照标号和/或文字重复的情况。像这样重复是为了简洁清楚,其本身并不需要与各种实施方式和/或所说明的结构之间存在关系。此外,当记述为第1要素与第2要素“连接”或“连结”时,像这样的记述包含第1要素与第2要素相互直接连接或连结的实施方式,并且也包含在第1要素与第2要素之间夹着大于等于一个的其它要素,而使该第1要素与该第2要素相互间接连接或连结的实施方式。另外,当记述为第1要素相对于第2要素“移动”时,像这样的记述包含第1要素和第2要素中的至少一方相对于另一方进行移动的相对移动的实施方式。
45.1.电子部件的制造方法
46.本实施方式的电子部件的制造方法包含在夹具保持电子部件主体来实施的印前工序和涂覆工序,根据需要,也可以包含在涂覆工序之后实施的膏去除工序。在涂覆工序或膏去除工序之后,电子部件主体从夹具被拆卸。以下,对各工序进行概述。
47.作为电子部件的制造方法,图1~图3示意性地示出了电容器的外部电极成型方法的主要工序。能够在电子部件主体10的印前工序、涂覆工序以及膏去除工序中兼用的平台30例如由陶瓷、花岗岩、金属等形成。平台30上设置有刮板单元40。刮板单元40能够沿平台30的表面31移动。刮板单元40将以均匀高度铺设导电膏的浸渍层50的例如金属制的刀具42和从平台30的表面31刮除导电膏的例如橡胶制的刀具44分别支承为能够独立升降。
48.平台30的上方配置有能够相对于固定板34升降的可动板32。夹具20被可动板32支承为装卸自如,因此可动板32也称为基座。固定板34支承有升降马达36,可动板32利用被升降马达36旋转驱动的丝杠轴38而升降。
49.1.1.印前工序
50.如图1的(a)所示,预先将保持有多个电子部件主体10的夹具20搬入外部电极形成装置。电子部件主体10的第1端部12a成为被夹具20保持的固定端部,第2端部12b成为自由端。被搬入的夹具20固定于可动板32。图1的(b)示出了电子部件主体10的端面高度的调整工序(印前工序)。在图1的(b)中,针对未铺设有导电膏的平台30,通过可动板32使电子部件主体10相对下降,从而使电子部件主体10的第2端部12b的端面12b1与平台30接触。然后,电子部件主体10利用可动板32而相对上升。由此,电子部件主体10的端面12b1的高度变得均匀。
51.1.2.涂覆工序
52.图2的(a)~图2的(c)示出了导电膏的涂覆工序。在图2的(a)中,通过刮板单元40使被设定为规定高度的刀具42水平移动,从而在平台30上形成由导电膏构成的一定高度的浸渍层50。在图2的(b)中,通过可动板32使电子部件主体10下降,从而使电子部件主体10的第2端部12b浸渍于平台30上的浸渍层50。这时,可以使电子部件主体10的端面12b1与平台30的表面31接触,或者也可以不接触。然后,电子部件主体10利用可动板32而上升。由此,电子部件主体10的第2端部12b形成有导电膏层14。
53.1.3.膏去除工序
54.图3的(a)~图3的(c)示出了膏去除工序(吸印工序)。图3的(a)示出了通过刮板单元40使以与平台30的表面31接触的方式下降的刀具44水平移动,从而刮除平台30上的导电膏的工序。在图3的(b)中,通过可动板32使电子部件主体10下降,从而使形成于电子部件主体10的第2端部12b的导电膏层14与平台30接触。然后,电子部件主体10利用可动板32而上升。由此,电子部件主体10的第2端部12b的多余的膏转印于平台30,从而形成平坦化的导电膏层14a。另外,如果使用由本技术的申请人提出的日本特许第6633829号(注:滑动吸印)、日本特愿2019-125369(注:螺旋吸印)或pct/jp2020/010448等记载的膏去除工序来代替图3的(a)~图3的(c)所示的以往的膏去除工序,则导电膏层14a得到进一步改善。
55.2.第1实施方式
56.接着,参照图4~图8对第1实施方式的印前工序和拆卸工序的详细情况进行说明。在图4中,夹具20包含基材21和平板材料22。基材21是具有保形性的刚体,并被图1的(a)等所示的可动板32支承为装卸自如。基材21也发挥支承平板材料22的支承部的作用。基材21和平板材料22与平台30的表面31平行地配置。平板材料22例如能够是形状记忆树脂。在形状记忆树脂22不具有粘接功能的情况下,形状记忆树脂22的露出表面形成有粘接层23。粘接层23形成粘接电子部件主体10的第1端部12a的粘接面。
57.形状记忆树脂22由对在模具内对形状记忆树脂进行成型时的成型品的形状进行固定的“固定相”和伴随着温度变化而可逆地产生软化与固化的“可逆相”的双相构造构成。以下,在本说明书中,将固定相称为形状记忆状态,将可逆相中的一个称为软化状态,将可逆相中的另一个称为固化状态。而且,将在固定相的形状称为一次赋形,将在软化后固化时的形状称为二次赋形。形状记忆树脂22是在对以粉末状或颗粒状供给的树脂进行加热/熔融并向模具等中注入而进行赋形之后,经过冷却工序而成型为一次赋形的形状。将一次赋形后的形状记忆树脂22在适当的二次赋形温度下变形为任意的形状,并在保持施加应力的状态下,冷却至室温时,固定为二次赋形的形状。将二次赋形后的形状记忆树脂22再次加热至适当的温度时,恢复成一次赋形时的形状。关于形状记忆树脂,例如记载于着色剂,636.353-359.1990。
58.2.1.第1工序
59.图4示出了印前工序中的第1工序。在第1工序中,电子部件主体10的第1端部12a粘接于夹具20的粘接层23。另外,为了将多个电子部件主体10一并粘接于夹具20的粘接层23,使用将多个电子部件主体10排列并保持的排列夹具。在这里,在本实施方式中使用的形状记忆树脂22为市售的jmade形状记忆塑料(面状保持型、平板的厚度为0.4mm、形状恢复温度为60℃)。在使形状记忆树脂22为常温来实施的第1工序中,形状记忆树脂22的形状为一次赋形后的0.4mm厚的平板(形状记忆状态)。被夹具20保持的多个电子部件主体10有时会由于从粘接层23到端面12b1的长度为l1、l2而不同从而具有偏差δl=l2-l1。在这种情况下,两个电子部件主体10的端面12b1的位置未对齐。
60.2.2.第2工序
61.图5示出了印前工序中的第2工序。在第2工序中,使夹具20相对于平台30相对移动。在图5中,使夹具20相对于固定的平台30下降。在该第2工序中,形状记忆树脂22的形状也是一次赋形后的0.4mm厚的平板(形状记忆状态)。
62.2.3.第3工序和第4工序
63.图6示出了印前工序中的第3工序和第4工序。在第3工序中,将形状记忆树脂22加热为比玻璃化转变点高的例如70~120℃从而成为软化状态,使电子部件主体10的第2端部12b与平台30接触规定时间。软化温度能够大于等于玻璃化转变点且不足熔点。由此,使形状记忆树脂22和粘接层23加压变形。形状记忆树脂22的形状成为二次赋形。另外,也可以在第2工序中开始形状记忆树脂22的强制加热。在第4工序中,保持使电子部件主体10的第2端部12b与平台30接触的状态,将形状记忆树脂22从不足玻璃化转变点例如强制冷却为常温的范围从而成为固化状态。形状记忆树脂22保持二次赋形的状态被固化。通过实施第3工序和第4工序,电子部件主体10的第2端部12b的端面12b1的位置能够与平台30的表面对齐到同一平面上。
64.2.4.第5工序
65.图7示出了印前工序中的第5工序。在第5工序中,使夹具20相对于平台30相对移动,从而使端面12b1的位置对齐的电子部件主体10离开平台30。由此,印前工序完成。另外,在图7中,使夹具20相对于固定的平台30上升。而且,该第5工序能够使二次赋形后的形状记忆树脂22为常温来实施。
66.2.5.拆卸工序
67.在印前工序完成之后,实施上述的涂覆工序,进一步根据需要实施膏去除工序。无论怎样,在针对被夹具20保持的电子部件主体10的处理完成后,电子部件主体10从夹具20被拆卸。因此,在拆卸工序中,使形状记忆树脂22变形为作为能够从夹具20拆卸电子部件主体10的状态的软化状态和固化状态的形状(二次赋形)以外的保形状态。在形状记忆树脂22的情况下,能够作为二次赋形以外的保形状态恢复为一次赋形。通过再加热为形状恢复温度例如大于等于60℃,从二次赋形恢复为一次赋形,由此形状记忆树脂22如图8所示成为平板。由此,粘接层23也被平坦化,因此能够从粘接层23容易地拆卸电子部件主体10。
68.2.6.评价
69.对形成于通过第1实施方式的制造方法制造的电子部件主体10的第2端部12b的膏
层14a的膜厚进行评价。另外,关于在涂覆工序之后实施的膏去除工序,使用由本技术的申请人提出的日本特许第6633829号公开的吸印工序。
70.在评价时,以一对的方式分别准备两种与图4的(a)所示的长度l1、l2对应的规格长度为603mm的电子部件主体10,并对每一对膏层14a的膜厚的偏差进行评价。针对每个两种长度的电子部件主体10,对使用第1实施方式的制造方法形成的膏层14a的膜厚(实施例)与不使用第1实施方式的制造方法形成的膏层14a的膜厚(比较例)进行比较。在比较例中,在第1实施方式的印前工序中,在第3和第4工序停止形状记忆树脂22的加热/冷却。将图4的(a)所示的长度l1的电子部件主体10作为比较例1或实施例1。将图4的(a)所示的长度l2的电子部件主体10作为比较例2或实施例2。在作为一对比较对象的比较例1、2中,图4的(a)所示的电子部件主体10的长度l1、l2的偏差δl也反映于膏层14a。另外,为了将电子部件主体10的长度l1、l2的偏差δl较大的电子部件主体10作为一对评价对象,将不同制造商的产品作为一对评价对象。
71.关于膏层14a的膜厚的偏差,在比较例1、2之间为39~88μm,但在实施例1、2之间为2~18μm。也就是说,可以看出,即使图4的(a)所示的电子部件主体10的长度l1、l2的偏差δl为39~88μm,通过第1实施方式的方法,膏层14a的膜厚的偏差也被抑制为2~18μm。
72.作为一例,相当于图4的(a)的长度l1的比较例1的膏层14a的最大膜厚为79μm,但在实施例1中,如图9的(a)所示,膏层14a的最大膜厚为37μm。相当于图4的(a)的长度l2的比较例2的膏层14a的最大膜厚为24μm,但在实施例2中,如图9的(b)所示,膏层14a的最大膜厚为38μm。在一对比较例1、2之间的膏层14a的偏差为55μm(79-24),但在一对实施例1、2之间的膏层14a的偏差被抑制到仅有1μm(38-37)。
73.上述评价是针对形成于图4的(a)所示的电子部件主体10的第2端部12b的膏层14a的评价。在第2端部12b形成有膏层14a的电子部件主体10通过上述拆卸工序从夹具20被拆卸。然后,形成有膏层14a的第2端部12b保持于夹具20,与电子部件主体10的第1端部12a同样地形成有膏层14a。
74.因此,对形成于图4的(a)所示的电子部件主体10的第1端部12a的膏层14a也进行了评价。这时,通过第1实施方式的方法制造的评价对象中的相当于图4的(a)的长度l1的实施例1的形成于电子部件主体10的第2端部12b的膏层14a的膜厚选择32~40μm的范围的膜厚。在该实施例1的电子部件主体10的第1端部12a通过第1实施方式的方法形成的膏层14a的膜厚为32~45μm。也就是说,形成于第2端部12b的膏层14a的膜厚的偏差为8μm(40-32),形成于第1端部12a的膏层14a的膜厚的偏差为13μm(45-32),形成于两端部12a、12b的膏层14a的膜厚的偏差为相同程度。
75.接着,相当于图4的(a)的长度l2的实施例2的形成于电子部件主体10的第2端部12b的膏层14a的膜厚选择31~38μm的范围的膜厚。在该实施例2的电子部件主体10的第1端部12a通过第1实施方式的方法形成的膏层14a的膜厚为35~40μm。也就是说,形成于第2端部12b的膏层14a的膜厚的偏差为7μm(38-31),形成于第1端部12a的膏层14a的膜厚的偏差为5μm(40-35),形成于两端部12a、12b的膏层14a的膜厚的偏差为相同程度。
76.通过以上的评价结果,根据第1实施方式可知,能够降低图4的(a)所示的多个电子部件主体10的长度l1、l2的偏差δl反映在形成于多个电子部件主体10的第1、第2端部12a、12b的膏层14a的膜厚差的程度。由此,能够大幅降低多个电子部件主体10的各膏层14a的膜
厚差。
77.3.第2实施方式
78.接着,参照图10~图14对第2实施方式的印前工序和拆卸工序的详细情况进行说明。在图10中,夹具20包含基材21和平板材料24。平板材料24例如可以是热可塑性树脂。热可塑性树脂24可以是热可塑性粘接剂。这样,粘接层23在图4示出但在这里不需要,热可塑性粘接剂24的露出表面形成粘接电子部件主体10的第1端部12a的粘接面。
79.热可塑性粘接剂24具有伴随着温度变化而可逆地引起软化与固化的“可逆相”。热可塑性粘接剂24在大于等于玻璃化转变点的温度变形为任意的形状,并在保持施加应力的状态下,冷却时则固化。热可塑性粘接剂24能够适当地使用熔融涂覆主成分为热可塑性树脂的固态粘接剂,通过冷却而固化从而表达粘接强度的、例如热可塑性聚酯系热熔粘接剂等热熔形。
80.3.1.第1工序
81.图10示出了印前工序中的第1工序。在第1工序中,电子部件主体10的第1端部12a粘接于夹具20的热可塑性粘接剂24。在第1工序中使用的热可塑性粘接剂24为常温,以平板被固化。被夹具20保持的多个电子部件主体10有时会由于从粘接层23到端面12b1的长度为l1、l2而不同从而具有偏差δl=l2-l1。在这种情况下,两个电子部件主体10的端面12b1的位置未对齐。
82.3.2.第2工序
83.图11示出了印前工序中的第2工序。在第2工序中,使夹具20相对于平台30相对移动。在图5中,使夹具20相对于固定的平台30下降。在该第2工序中,热可塑性粘接剂24也为常温,以平板被固化。
84.3.3.第3工序和第4工序
85.图12示出了印前工序中的第3工序和第4工序。在第3工序中,将热可塑性粘接剂24加热为大于等于玻璃化转变点的温度从而成为软化状态,并使电子部件主体10的第2端部12b与平台30接触。由此,通过压力使热可塑性粘接剂24变形。在第4工序中,保持使电子部件主体10的第2端部12b与平台30接触的状态,将热可塑性粘接剂24例如强制冷却为小于玻璃化转变点的常温从而成为固化状态。热可塑性粘接剂24保持着在第3工序中被赋予的形状而被固化。通过第3工序和第4工序的实施,电子部件主体10的第2端部12b的端面12b1的位置能够与平台30的表面对齐在同一平面上。
86.3.4.第5工序
87.图13示出了印前工序中的第5工序。在第5工序中,使夹具20相对于平台30相对移动,从而使端面12b1的位置对齐的电子部件主体10离开平台30。由此,印前工序完成。另外,在图7中,使夹具20相对于固定的平台30上升。而且,该第5工序能够将在第3工序和第4工序中变形的热可塑性粘接剂24的形状在常温下维持来实施。
88.3.5.拆卸工序
89.在拆卸工序中,为了能够从夹具20拆卸电子部件主体10,使热可塑性粘接剂24软化。为此,将热可塑性粘接剂24加热为大于等于玻璃化转变点的温度。这时,为了防止热可塑性粘接剂24的非预期的变形,如图14所示,能够使用成型部件60。成型部件60能够覆盖热可塑性树脂24的露出面,尤其是图14所示的热可塑性粘接剂24的下表面。成型部件60具有
防止与电子部件主体10干涉的孔61。在成型部件60内软化的热可塑性粘接剂24从在第3工序和第4工序中被赋予的形状恢复为原来的平板。由此,能够容易从平坦化的热可塑性粘接剂24拆卸电子部件主体10。
90.4.第3实施方式
91.在第3实施方式中,作为夹具20中的平板材料,使用不是热可塑性粘接剂24的热可塑性树脂25。在图4~图9中,图示出了在基材21与粘接层23之间配置热可塑性树脂25来代替第1实施方式的形状记忆树脂22而得到的方式。由此,只要将第1实施方式中的形状记忆树脂22变更为热可塑性树脂25,就能够在第1工序~第5工序中使热可塑性树脂25与第2实施方式同样地进行相变化来实施印前工序。
92.拆卸工序能够以覆盖图9的粘接层23的方式配置图14所示的成型部件60来实施。或者,也可以不配置成型部件60,粘接层23发挥成型部件60的功能。
93.5.第4实施方式
94.接着,对夹具20中的平板材料22、24或25的温度调整部进行说明。另外,图15~图18是关于第1实施方式对温度调整部进行说明的,但在第2实施方式和第3实施方式中也同样能够应用。
95.在图15中,在夹具20的基材21设置调温部100。调温部100可以具有加热部和冷却部双方,也可以是例如如珀耳帖元件这样兼用作为加热部和冷却部。这样,调温部100经由例如能够由金属等导电性较高的材料形成的基材21,能够高效地对形状记忆树脂22进行加热或冷却。在图16中,在固定夹具20的基座32设置调温部100。这样,调温部100能够经由例如能够由金属等导电性较高的材料形成的基座32和基材21对形状记忆树脂22高效地进行加热或冷却。这样,通过将调温部100设置于夹具20或基座32,能够以将形状记忆树脂22切换并设定为一次赋形和二次赋形双方的方式进行调温。
96.在第2和第3实施方式中,通过设置于夹具20或基座32的调温部100,能够将热可塑性树脂(热可塑性粘接剂)24、25设定为软化状态和固化状态。
97.在图17中,在夹具20的基材21设置加热部110、在平台30设置冷却部120。在图18中,在固定夹具20的基座32设置加热部110、在平台30设置冷却部120。通过设置于夹具20或基座32的加热部110将形状记忆树脂22设定为软化状态和形状记忆状态。通过设置于平台30的冷却部120,形状记忆树脂22经由多个电子部件主体10被冷却从而被设定为固化状态。而且,通过将加热部110与冷却部120分开配置,能够降低一方对另一方产生的不良影响。
98.在第2和第3实施方式中,通过设置于夹具20或基座32的加热部110,能够将热可塑性树脂(热可塑性粘接剂)24、25设定为软化状态。通过设置于平台30的冷却部120,形状记忆树脂22经由多个电子部件主体10被冷却从而被设定为固化状态。
99.另外,如上述那样对本实施方式进行了详细说明,但是本领域技术人员能够容易地理解到,可进行实体上未脱离本发明的新颖内容和效果的多种变形。因此,这样的变形例全部包含在本发明的范围内。
100.例如,作为相变化为软化和固化的平板材料,除了形状记忆树脂或热可塑性树脂(热可塑性粘接剂)之外,能够使用热固化性树脂、能够软化和固化的刺激响应性材料等。关于刺激响应性树脂,例如记载于日本机械学会刊2004.11vol.107no.1032。刺激响应性材料是通过物理性刺激(温度、光、磁场、电流)而性质发生变化的凝胶、树脂或弹性体等,但近年
来,由产业技术综合研究所、北海道大学、筑波大学、山形大学、庆应大学等报告了通过物理性刺激而可逆地发生软化/固化的材料。由此,也可以使用可逆地发生软化/固化的刺激响应性树脂作为平板材料。在这种情况下,将图15~图18所示的调温部100、加热部110以及冷却部120分别变更为物理性刺激部。
101.标号说明
102.10:电子部件主体;12a:第1端部;12b:第2端部;12b1:端面;14、14a:膏层;20:夹具;21:基材;22:平板材料(形状记忆树脂);23:粘接层;24:平板材料(热可塑性粘接剂);25:平板材料(热可塑性树脂);30:平台;32:基座(可动板);50:成型部件;100:调温部;110:加热部;120:冷却部。