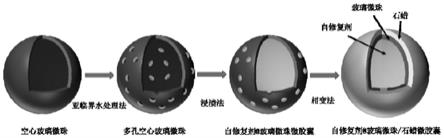
1.本发明涉及新材料技术领域,具体涉及一种新型的自修复自润滑双功能微胶囊及其制备方法和应用。
背景技术:2.微胶囊是一种具有核壳结构的微米粒子,可根据不同的应用需求设计它们的核(芯材)和壳(壁材)。近几年来,微胶囊在自修复及自润滑材料领域有广泛的应用。其中,微胶囊在自修复领域的应用主要是制备自修复聚合物基复合材料、自修复防腐涂层和自修复混凝土等。
3.在微胶囊的制备过程中,将修复剂作为芯材,再以有机或无机材料或有机/无机杂化材料作为壁材,壁材的主要作用是对芯材加以保护或使得微胶囊具有缓释功能。将微胶囊埋植于基体材料中,当基体材料受到损伤或产生微裂纹时,微胶囊破裂,释放的修复剂填补微裂纹,并在微裂纹处形成自修复膜,将裂纹修补,从而实现对基体材料的自修复。
4.微胶囊在自润滑领域的应用主要是制备自润滑聚合物基复合材料,其中将润滑剂作为芯材,再以有机或无机材料或有机/无机杂化材料作为壁材制备微胶囊。将微胶囊添加于复合材料基体中,材料在摩擦磨损作用下导致微胶囊破裂,释放出的润滑剂会在摩擦表面形成自润滑转移膜,从而有效改善材料的耐摩擦磨损性能。
5.目前文献中报道的微胶囊通常使用的壁材主要有有机壁材,如脲醛树脂、密胺树脂、聚氨酯、聚脲、聚砜、聚苯乙烯等。采用这些有机物做微胶囊的壁材时,一般采用原位聚合、界面聚合、溶剂挥发等化学方法或物理化学法来合成微胶囊。在微胶囊化的过程中,会涉及到多种化学试剂的使用。对于微胶囊常用的无机壁材如二氧化硅或者有机无机杂化壁材如聚砜/二氧化硅、聚苯乙烯/二氧化硅等,也要通过溶胶凝胶法或组合其它化学方法等制得。因此在微胶囊化过程中涉及多种化学试剂的使用,从而导致微胶囊以及基于微胶囊的复合材料的生产对环境造成负担,因此非常迫切需要环境友好的微胶囊以及基于微胶囊的复合材料及其制备方法。
6.本发明开发了一种环境友好型微胶囊化方法,在微胶囊的制备过程中不使用或使用微量化学试剂。同时,将自修复剂和自润滑剂分别引入到微胶囊的芯材与壁材结构中,使得制备的微胶囊同时具有自修复和自润滑功能,可将其应用于聚合物基复合材料基体中,制备具有自修复及自润滑双功能的聚合物基复合材料或涂层。
技术实现要素:7.本发明提供了一种新型自修复自润滑双功能微胶囊及其制备方法和在聚合物基复合材料中的应用。该微胶囊以空心多孔玻璃微珠为载体,通过物理浸渍法在其空腔内部浸渍自修复剂(干性油类、异氰酸酯类、环氧树脂类等),制备得到自修复剂@玻璃微珠微胶囊;再采用相变法将相变材料(例如石蜡)包覆在浸渍了自修复剂的玻璃微珠外表面,最终制备得到自修复剂@玻璃微珠/自润滑剂双壁微胶囊(见附图1),相变材料壁层不仅对玻璃
微珠表面多孔结构进行包封从而阻止芯材修复剂的泄露,同时相变材料作为一种润滑剂,也使得微胶囊同时具有自润滑功能。
8.具体地说,本发明在第一方面提供了一种制备自修复自润滑双功能微胶囊的方法,所述方法包括如下步骤:
9.(1)使用自修复剂浸渍空心多孔微珠,得到自修复剂浸渍微珠胶囊;
10.(2)将处于熔融状态的自润滑剂与所述自修复剂浸渍微珠胶囊混合均匀,得到双功能混合料;
11.(3)将所述双功能混合料喷涂在收集板上,然后从所述收集板上收集冷却后的双功能混合料,获得双功能微胶囊。
12.本发明在第二方面提供了根据本发明第一方面所述的方法制得的自修复自润滑双功能微胶囊。
13.本发明在第三方面提供了一种制备自修复自润滑双功能复合材料的方法,所述方法包括:
14.(1)制备包含树脂基体、固化剂和溶剂的树脂基体混合物;
15.(2)在搅拌所述树脂基体混合物的同时,将权利要求7所述的双功能微胶囊喷入到所述树脂基体混合物中并分散均匀,制得树脂混合物;
16.(3)将所述树脂混合物固化,得到自修复自润滑双功能复合材料。
17.本发明在第四方面提供了根据本发明第三方面所述的方法制得的自修复自润滑双功能复合材料。
18.相对于现有技术,本发明具有以下有益的技术效果:
19.(1)本发明在微胶囊化过程中,多孔玻璃微珠的制备采用亚临界水处理方法,整个过程只在水中进行或加入少量氢氧化钠即可;本发明在自修复剂@微珠微胶囊制备过程中采用物理浸渍法,不涉及化学试剂的使用,因此,与目前文献报道的自修复或自润滑微胶囊比较,本发明的微胶囊制备方法绿色环保。
20.(2)本发明在自修复剂@玻璃微珠/相变材料双壁微胶囊制备过程中,采用相变法,在相变材料熔融状态下进行微胶囊包覆,冷却后相变材料由液相转为固相,最终可以形成玻璃微珠/相变材料双壁层结构。与目前文献报道的自修复或自润滑微胶囊比较,本发明的微胶囊制备方法所制备得到的微胶囊芯材具有自修复作用,壁材具有自润滑作用,能满足双功能复合材料或涂层的应用。
21.(3)本发明所制备的含该微胶囊的聚合物基复合材料或涂层显示出了优异的自修复和自润滑性能。
附图说明
22.图1是本发明新型自修复自润滑双功能微胶囊的制备过程示意图
23.图2显示玻璃微珠及微胶囊的sem图,其中,图(a)显示的是玻璃微珠的sem图;图(b)显示了多孔玻璃微珠的sem图;图(c)显示亚麻油@玻璃微珠/石蜡微胶囊的sem图。
24.图3显示了不同微胶囊含量的环氧树脂涂层(a-d:0,5,10,15wt.%)在3.5wt.%nacl盐水中浸泡(1-4:1,5,10,15天)后划痕处的腐蚀情况。
具体实施方式
25.为使本发明实施例的目的、技术方案和优点更加清楚,下面将结合本发明实施例中的附图,对本发明实施例中的技术方案进行清楚、完整地描述,显然,所描述的实施例是本发明的一部分实施例,而不是全部的实施例。基于本发明中的实施例,本领域普通技术人员在没有做出创造性劳动的前提下所获得的所有其他实施例,都属于本发明保护的范围。
26.本发明在第一方面提供了一种制备自修复自润滑双功能微胶囊的方法,所述方法包括如下步骤:
27.(1)使用自修复剂浸渍空心多孔微珠,得到自修复剂浸渍微珠胶囊;
28.(2)将处于熔融状态的自润滑剂与所述自修复剂浸渍微珠胶囊混合均匀,得到双功能混合料;
29.(3)将所述双功能混合料喷涂在收集板上,然后从所述收集板上收集冷却后的双功能混合料,获得双功能微胶囊。
30.在一些优选的实施方式中,所述自修复试剂为选自干性油、异氰酸酯和环氧树脂中的一种或多种自修复剂。
31.在另一些优选的实施方式中,所述自润滑剂为相变材料,优选的是,所述相变材料是室温下为固体状态的石蜡,更优选的是,所述石蜡的熔点为45至70℃(例如为50或60℃)。
32.在另一些优选的实施方式中,所述空心多孔微珠为外径为5至200微米,内径为2至180微米的球形微珠。优选的是,所述空心多孔微珠为空心多孔玻璃微珠。更优选的是,所述空心多孔微珠通过如下方法制备:将空心玻璃微珠放入碱液中,得到空心微珠混合物,将所述空心玻璃微珠混合物放入反应釜中,将温度升至150至300℃(例如200或250℃)的温度并使所述反应釜内压力升至0.5至9mpa(例如1、2或5mpa)的压力并保温保压1至3小时(例如2小时),然后冷却至室温,得到空心多孔玻璃微珠。进一步优选的是,所述碱液是浓度为0.1至1m(例如0.5m)的氢氧化钠水溶液或氢氧化钾水溶液。当然,如果采用水代替所述碱液,也能获得多孔结构。但是从生产效率等角度来看,优选采用碱液而不是纯水。
33.在另一些优选的实施方式中,步骤(1)通过如下方式进行:将空心多孔微珠加入到自修复剂中并分散均匀,再放入真空烘箱中以移除空心多孔微珠内的气泡,使得自修复剂浸渍到所述空心多孔微珠中,再在常温下放置3至24小时(例如6、9、12、15、18或21小时),将所得产物过滤,清洗,得到所述自修复剂浸渍微珠胶囊。优选的是,所述空心多孔微珠和自修复剂的质量比为1:(2~10),例如为1:(3、4、5、6、7、8或9)。更优选的是,所述分散通过超声分散的方式进行,超声分散的功率为50w至360w;超声分散的时间为10至30分钟(例如20分钟)。进一步优选的是,所述真空烘箱的温度为室温至80℃,真空度为0.01-0.09mpa,浸渍时间为0.5至2小时(例如1或1.5小时)。
34.在另一些优选的实施方式中,在步骤(2)中,所述相变材料在80至120℃(例如90、100或110℃)保温5至20分钟(例如10或15分钟)以使所述相变材料处在充分的熔融状态。优选的是,在步骤(2)中,所述自修复剂浸渍微珠胶囊和所述相变材料的质量比为1:(0.4~0.8),例如1:(0.4、0.5、0.6或0.7)。如果相变材料用量过低,可能无法充分包覆自修复剂浸渍微珠胶囊;如果相变材料用量过大,则可能导致所包覆的相变材料层厚度过大,使得其中的自修复剂在微胶囊受到破坏时无法顺畅地释放自修复剂以执行自修复功能。
35.在另一些优选的实施方式中,在步骤(3)中,所述喷涂通过将所述双功能混合料倒
入在80至120℃(例如90、100或110℃)预热的喷枪中进行喷涂来实现。优选的是,在步骤(3)中,所述收集板为玻璃板。
36.现在参见图1。图1显示了本发明第一方面所述的方法的一些更具体的实施方式。如图1所示,所述方法包括如下步骤:
37.(1)采用亚临界水处理方法制备多孔玻璃微珠
38.将空心玻璃微珠放入0至1mol/l氢氧化钠水溶液中(玻璃微珠与氢氧化钠水溶液质量比1:(20-100),得到空心微珠混合物;将空心微珠混合物放入带有磁力搅拌的高温高压反应釜中,将反应釜的温度升至150-300℃,反应釜内的压力也随着温度增加而增加至0.5至9mpa,在此状态下保持1至3小时后,反应釜自然冷却到室温,用去离子水对产品进行清洗,在真空烘箱内在室温至80℃的温度,0.01-0.09mpa真空度条件下浸渍,得到空心多孔玻璃微珠;
39.(2)采用浸渍法制备自修复剂@玻璃微珠微胶囊
40.将干燥后的空心多孔玻璃微珠放入自修复剂中(质量比1:(2-10)),超声分散10-30min(超声功率为50w至360w),再放入真空烘箱在室温至80的温度,0.01-0.09mpa的真空度下浸渍0.5至2小时,充分移除空心玻璃微珠内的气泡,自修复剂通过多孔表面逐渐浸渍到玻璃微珠空腔内,再在常温下放置3至24小时以提高自修复剂浸渍率。浸渍后的产品经过过滤、溶剂清洗去除玻璃微珠外表面残留的自修复剂后,得到自修复剂@玻璃微珠微胶囊;
41.(3)自修复剂@玻璃微珠/自润滑剂双壁微胶囊的制备
42.将固体石蜡加热到80-120℃后保温5-20min,使固体石蜡充分熔融。将所述自修复剂@玻璃微珠微胶囊添加到熔融石蜡中(微胶囊与石蜡质量比1:0.4-0.8),搅拌均匀后,将混合物倒入在80-120℃下预热的喷枪中,将喷枪中混合物喷至玻璃板上,自然冷却后收集产品,得到自修复剂@玻璃微珠/石蜡双壁微胶囊(即双功能微胶囊)。
43.本发明在第二方面提供了根据本发明第一方面所述的方法制得的自修复自润滑双功能微胶囊。
44.本发明在第三方面提供了一种制备自修复自润滑双功能复合材料的方法,所述方法包括:
45.(1)制备包含树脂基体、固化剂和溶剂的树脂基体混合物;
46.(2)在搅拌所述树脂基体混合物的同时,将权利要求7所述的双功能微胶囊喷入到所述树脂基体混合物中并分散均匀,制得树脂混合物;
47.(3)将所述树脂混合物固化,得到自修复自润滑双功能复合材料。
48.在一些优选的实施方式中,所述树脂基体选自环氧树脂、聚氨酯树脂、醇酸树脂中的一种或多种。
49.固化剂的选择决定于树脂基体的选择。一般在销售树脂基体时,都会配有相应的固化剂。因此,在本发明中,固化剂无需针对各种树脂基体列出相应的固化剂,本领域技术人员完全有能力根据树脂基体的选择来选用相应的固化剂。
50.在另一些优选的实施方式中,所述树脂基体混合物包含质量比为3:1:1的树脂基体、固化剂和溶剂。
51.在另一些优选的实施方式中,所述溶剂选自乙醇、异丙醇中的一种或多种。
52.在另一些优选的实施方式中,所述微胶囊的添加量为1至20质量%。
53.在另一些优选的实施方式中,固化为室温固化,固化时间为24至72小时。
54.在一些更具体的实施方式中,所述方法制得的是模具成型材料形式的自修复/自润滑双功能复合材料,所述方法包括如下步骤:
55.(1)制备包含树脂基体、固化剂和溶剂的树脂基体混合物;
56.(2)在搅拌所述树脂基体混合物的同时,将本发明第二方面所述的双功能微胶囊通过喷枪喷至所述树脂基体混合物中,所述微胶囊的添加量1-20wt.%(以树脂基体和固化剂的总重量计),得到树脂混合物,其中所述树脂基体可以是环氧树脂、聚氨酯树脂、醇酸树脂等;
57.(3)将所述树脂混合物注入到成型模具中,室温固化24至72小时,制得聚合物基自修复自润滑双功能复合材料。
58.在另一些更具体的实施方式中,所述方法制得的是涂层形式的自修复自润滑双功能复合材料,并且包括如下步骤:
59.(1)将涂层基板(通常可以为金属板)用砂纸打磨,再用去离子水和乙醇清洗,烘箱干燥备用;
60.(2)制备包含树脂基体、固化剂和溶剂的树脂基体混合物;
61.(3)将本发明第二方面所述的双功能微胶囊通过喷枪喷至所述树脂基体混合物(以树脂基体和固化剂的总重量计,所述双功能微胶囊的添加量为1-20wt.%)并搅拌均匀(喷射过程中树脂基体混合物容器中可以伴有磁力搅拌),得到含有微胶囊的树脂混合物,其中所述树脂基体可以是环氧树脂、聚氨酯树脂或醇酸树脂等;
62.(4)将含有微胶囊的树脂混合物均匀涂于基板表面(涂层干膜厚度可根据需要调解在50-500μm之间),室温下固化24-72h,制备得到自修复自润滑双功能复合材料涂层。
63.在另一些更具体的实施方式中,所述方法制得的是交替涂层形式的自修复自润滑双功能复合材料涂层,并且所述方法包括如下步骤:
64.(1)将涂层基板(通常为金属板)用砂纸打磨,再用去离子水和乙醇清洗,烘箱干燥备用;
65.(2)配制包含树脂基体、固化剂和溶剂的树脂基体混合物。
66.(3)准备两个喷枪,喷枪1中加入所述树脂基体混合物,喷枪2加入本发明第二方面所述的双功能微胶囊(喷枪内温度保持在80-120℃的温度范围内)。将涂层基板放在加热台上,加热台的温度控制在室温-50℃的温度范围内,将喷枪1中树脂混合物喷涂于基板表面,形成一层树脂涂层,放置5-30min待溶剂挥发后,再将喷枪2中微胶囊喷于上述涂层表面(微胶囊添加量1-20wt.%),重复上述操作,可根据需要喷涂多次树脂层和微胶囊,最后一层再喷上树脂涂层,喷涂后将涂层在室温下固化24-72h,最终制备得到自修复自润滑双功能复合材料涂层。
67.在一些实施方式中,可以将本发明第一方面所述方法的步骤(2)制得的双功能混合料代替所述双功能微胶囊。
68.本发明在第四方面提供了根据本发明第三方面所述的方法制得的自修复自润滑双功能复合材料。
69.在一些优选的实施方式中,所述材料为模具固化成型材料。
70.在另一些优选的实施方式中,所述材料为涂层材料,更优选的是,所述涂层材料的
厚度为50至500微米(例如为100、200、300或400微米)。
71.实施例
72.制备例1
73.将1g外径为20μm、内径为18μm的空心玻璃微珠(参见图2的图(a))和40ml(0.1mol/l)氢氧化钠水溶液加入到反应釜中,密闭状态下升温至250℃,在此温度下维持2h后,反应釜自然冷却至室温,过滤、去离子水洗涤、干燥后得到多孔空心玻璃微珠。
74.将1g多孔空心玻璃微珠分散到10g作为自修复剂的亚麻油中,以180w的超声功率超声分散20min,放入真空烘箱中在50℃温度,0.06mpa真空度下浸渍30min,再在空气中放置12h,过滤并用乙酸乙酯溶剂洗掉玻璃微珠外表面的亚麻油,得到自修复剂@玻璃微珠微胶囊(参见图2的图(b))。
75.将1.2g固体石蜡(熔点为70℃)在120℃下熔融10min,将喷枪放入120℃烘箱中充分预热(预热至120℃),将2g自修复剂@玻璃微珠微胶囊加入到熔融的石蜡中,搅拌均匀后,倒入预热的喷枪中,以光滑的玻璃板为收集板,将喷枪中的混合物喷至玻璃板上,石蜡从熔融液态转为室温下的固态,并包裹在自修复剂@玻璃微珠微胶囊的外表面上,收集产品后得到自修复剂@玻璃微珠/石蜡微胶囊(参见图2的图(c))。
76.制备例2
77.采用与制备例1基本相同的方法进行,不同之处在于,采用异氰酸酯代替亚麻油作为自修复剂。
78.制备例3
79.采用与制备例1基本相同的方法进行,不同之处在于,采用环氧树脂代替亚麻油作为自修复剂。
80.制备例4
81.采用与制备例1基本相同的方法进行,不同之处在于,采用多孔空心玻璃微珠的用量为5g。
82.制备例5
83.采用与制备例1基本相同的方法进行,不同之处在于,固体石蜡的用量为1.6g。
84.制备例6
85.采用与制备例1基本相同的方法进行,不同之处在于,固体石蜡的用量为0.8g。
86.结果发现,制备例1至6都制得的结构完整的双功能微胶囊。
87.应用例1
88.将环氧树脂,固化剂(环氧树脂和固化剂购自黑龙江省科学院石油化学研究院)和乙醇溶剂按照3:1:1质量比混合均匀,制得树脂基体混合物。在搅拌所述树脂基体混合物的同时,从喷枪中将制备例1制得的微胶囊喷入所述树脂基体混合物中,使微胶囊在树脂混合物中均匀分散,得到环氧树脂混合物,其中微胶囊占所述树脂基体混合物的质量百分比5wt.%。将环氧树脂混合物倒入成型模具中,室温下固化24h,制备得到自修复自润滑双功能复合材料。
89.应用例2
90.将不锈钢板用砂纸打磨,再用去离子水和乙醇清洗,烘箱干燥备用。
91.将环氧树脂,固化剂(环氧树脂和固化剂黑龙江省科学院石油化学研究院)和乙醇
溶剂按照3:1:1质量比混合均匀,得到树脂基体混合物。在搅拌所述树脂基体混合物的同时,从喷枪中将制备例1制得的微胶囊喷入所述树脂基体混合物中,使微胶囊在树脂混合物中均匀分散,得到环氧树脂混合物,其中微胶囊与树脂混合物质量比10wt.%。将环氧树脂混合物均匀涂于处理后的钢板上,干膜厚度约为300μm,室温下固化48h,制备得到自修复自润滑双功能复合材料涂层。
92.应用例3
93.将不锈钢板用砂纸打磨,再用去离子水和乙醇清洗,烘箱干燥备用。
94.将环氧树脂,固化剂(环氧树脂和固化剂黑龙江省科学院石油化学研究院)和乙醇溶剂按照3:1:1质量比混合均匀,制得树脂基体混合物。
95.然后,将所述树脂基体混合物放入喷枪1中。将制备例1制得的微胶囊放入喷枪2中(喷枪内温度保持在80-120℃的温度范围内)。将不锈钢板放在加热台上,加热台升温至40℃。将喷枪1中树脂基体混合物喷涂于不锈钢板表面,形成一层树脂涂层,放置10min待溶剂挥发后再将喷枪2中微胶囊喷于上述涂层表面(以树脂基体和固化剂的总重量计,微胶囊添加量10wt.%,全文涉及微胶囊添加量支出,均以树脂基体和固化剂的总重量计),形成微胶囊层。按照上述方法依次再喷涂树脂涂层、微胶囊层、树脂涂层。喷涂后将涂层在室温下固化72h,制备得到自修复自润滑双功能复合材料涂层。
96.测试例1:环氧树脂涂层的自润滑性能
97.采用摩擦磨损实验,通过摩擦系数和磨损量的变化评价环氧树脂复合材料涂层的自润滑性能。将制备例1中制得的亚麻油@玻璃微珠/石蜡微胶囊添加到环氧树脂涂层(制备方法同应用例2)中,添加量分别为0、5、10、15wt.%,复合材料涂层的摩擦系数和磨损量随着微胶囊添加量的增加逐渐降低,添加了10wt.%亚麻油@玻璃微珠/石蜡微胶囊的环氧树脂复合材料涂层摩擦系数从0.5156降低到0.0662,摩擦损失从0.2854g/0.5h下降到0.098g/0.5h。但继续增加微胶囊含量到15wt.%时,复合材料涂层的摩擦系数和磨损量又会升高,这主要是由于微胶囊添加量过高会影响树脂基体的力学性能,力学性能也是影响材料摩擦磨损性能的一个主要原因。这组实验结果表明,添加粒径约为20μm的亚麻油@玻璃微珠/石蜡微胶囊时,环氧树脂复合材料涂层具有最佳的减摩耐磨效果即自润滑性能。
98.测试例2:环氧树脂涂层的自修复性能
99.采用盐雾试验,通过在3.5wt.%的nacl盐水溶液中浸泡涂层15天,观察涂层划痕处腐蚀情况评价环氧树脂复合材料涂层的自修复性能(参见下表1)。将亚麻油@玻璃微珠/石蜡微胶囊添加到环氧树脂涂层中,添加量分别为0、5、10、15wt.%,按照应用例2的方法制备涂层,然后在涂层表面划十字划痕,划痕深度直达金属基底。然后将涂层在常温下放置72h,允许划痕处实现自修复。此过程中划痕处微胶囊破裂,释放出的亚麻油遇到空气中氧气后发生交联反应形成自修复膜,将划痕处修复。观察和记录涂层浸泡第1、5、10和15天后的腐蚀情况。图(a1至a4)为纯环氧涂层腐蚀情况,可以考到,没有添加微胶囊的涂层划痕处在浸泡第1天便开始发生腐蚀,划痕处有明显的锈迹,浸泡时间越长,腐蚀现象越严重。图(b1至b4)为添加了5wt.%微胶囊的环氧涂层腐蚀情况,与纯环氧树脂涂层相比,腐蚀情况略有好转,但浸泡15天后划痕处腐蚀现象仍较严重,这表明5wt.%微胶囊所释放出来的亚麻油修复剂不足以充分的修复划痕处。图(c1至c4)为添加了10wt.%微胶囊的环氧涂层腐蚀情况,可以观察到,涂层在整个浸泡期间内几乎无腐蚀现象发生,说明划痕处形成了的新
的自修复膜,阻止了腐蚀介质的渗入,从而抑制了金属基底的腐蚀。图(d1至d4)为添加了15wt.%微胶囊的环氧涂层腐蚀情况,可以观察到涂层在浸泡第10天发现腐蚀现象,其抗腐蚀效果虽然优于纯环氧树脂涂层,但不如添加了10wt.%微胶囊的环氧涂层的抗腐蚀效果好,这主要是因为微胶囊含量过高会影响树脂基体的机械性能及与基底的界面粘结性能,进而影响涂层的整体抗腐蚀性能。这组实验结果表明,添加粒径约为20μm的亚麻油@玻璃微珠/石蜡微胶囊时,环氧树脂复合材料涂层具有最佳的抗腐蚀效果即自修复性能。
100.表1.测试例2的试验设计方案
[0101][0102][0103]
最后应说明的是:以上实施例仅用以说明本发明的技术方案,而非对其限制;尽管参照前述实施例对本发明进行了详细的说明,本领域的普通技术人员应当理解:其依然可以对前述各实施例所记载的技术方案进行修改,或者对其中部分技术特征进行等同替换;而这些修改或者替换,并不使相应技术方案的本质脱离本发明各实施例技术方案的精神和范围。