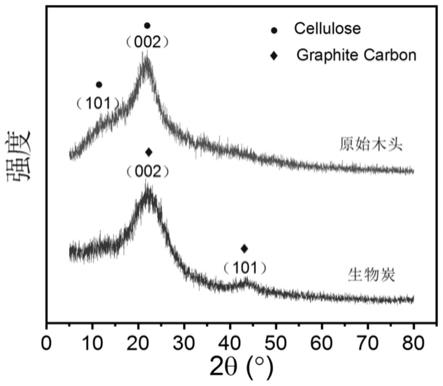
1.本发明涉及催化分解技术领域,特别是涉及一种生物炭材料的制备方法及其应用。
背景技术:2.臭氧(o3)作为一种有害的大气污染物,一直受到人们的广泛关注。臭氧是氧气的一种同素异形体,它存在于大气中,靠近地球表面的浓度为0.001~0.03ppm,是由大气中氧气吸收了波长小于185nm紫外线后生成的,此臭氧层可吸收太阳光中对人体有害的短波(30nm以下)光线,防止这种短波光线射到地面,使生物免受紫外线的伤害。而对流层中的臭氧主要是由挥发性有机化合物(vocs)和氮氧化物(no
x
)两种主要空气污染物之间的光化学反应形成的。这些反应依赖于热和阳光,因此夏季o3浓度更高。长期接触高浓度的臭氧会对身体造成损害,比如出现疲乏、咳嗽、胸闷胸痛、皮肤起皱、恶心头痛、脉搏加速、记忆力衰退、视力下降等症状。不仅如此,臭氧也会对植物造成损害,使植物叶子变黄甚至枯萎,造成农林植物减产、经济效益下降等。因此,臭氧污染防治刻不容缓。
3.目前,对臭氧的净化方法包括吸附法、热分解法和催化分解法。其中,吸附法往往受吸附剂容量的限制,且吸附剂对臭氧只吸附不消除,容易造成二次污染;此外,o3可在250℃高温下立刻分解,但热分解法技术能耗高,不适宜广泛使用;光催化是消除o3的另一种方法,然而,这种技术需要较长的停留时间(秒级),考虑到室内通风效率,催化剂需要在很短的停留时间(几百分之一秒)内作用于通风系统中。且多数方法更适用于室内臭氧的去除,对于室外的臭氧污染问题,目前并没有有效的解决方法。
4.因此,提供一种无需额外供能、活性高、成本低、便于实际应用的催化材料,对于有效去除室外空气中的臭氧污染具有重要的实用价值。
技术实现要素:5.本发明的目的是提供一种以木头为基材的生物炭材料的制备方法及其应用,制备的生物炭材料可作为臭氧净化材料,应用到任一需要净化臭氧的净化装置中,或者直接将净化材料放置于需要净化臭氧的空间内,有效解决室外空气中的臭氧污染问题。
6.为实现上述目的,本发明提供了如下方案:
7.本发明提供一种生物炭材料的制备方法,以木材为原料,直接通过缺氧高温热解方法制备得到,所述高温热解温度为500~900℃。
8.进一步地,高温热解气氛为ar、he或n2,气体流量为5~50ml/min。
9.进一步地,所述木材为松木、香樟、黄杉、楝木、榆木、泡桐或榉木。
10.本发明由木材直接缺氧高温热解所制得的生物炭材料具有较大的比表面积,升高反应温度对臭氧的降解效果较好。因此若将该材料用于室外(如建筑楼顶),利用太阳自身的光热效应,即使不额外供能也可以达到较好的去除效果。此制备方法简单,且使用的是自然环境中常见的木材,价廉易得。既合理利用了自然资源,又高效降解了空气中的臭氧。
11.进一步地,制备方法还包括以下步骤:以木材为原料,将木材粉碎后,加入到铁溶液和镁溶液的混合溶液中,搅拌均匀,烘干,粉碎过筛,在惰性气体或氮气气氛下进行缺氧高温热解,冷却至室温后,研磨,过筛即可。
12.进一步地,所述混合溶液中镁和铁的摩尔比为1:1。
13.进一步地,所述铁溶液为fe(no3)3·
9h2o,所述镁溶液为mg(no3)2·
6h2o。
14.进一步地,所述高温热解温度为400~550℃。
15.进一步地,所述木材与所述混合溶液的质量比为1:(2~3)。
16.本发明改进的生物炭材料的制备方法以木材为原料,将其与铁、镁混合,然后再通过缺氧高温热解制备,不仅能降低高温热解温度,还能够显著增大生物炭材料的比表面积和孔隙率。制备的生物炭材料除了比表面积和孔隙率大幅度增加外,还具有多种物相结构,主要有钙钛矿型(mgfeo3)、尖晶石结构(mgfe2o4)、铁的氧化物(feo、fe2o3、fe3o4)和镁的氧化物(mgo),生物炭材料的多孔结构及较大的比表面积与上述多种物相之间的协同作用,可有效提高最终制备的生物炭材料的比表面积和孔隙率,阻止金属氧化物等颗粒的团聚或浸出,制备的生物炭材料表面还有形状大小不规则的粒状结构,活性位点众多,提高对臭氧的分解速率。
17.本发明还提供一种所述制备方法制备得到的生物炭材料。
18.本发明还提供所述生物炭材料在催化臭氧氧化或净化臭氧污染中的应用。
19.进一步地,所述生物炭材料可应用到任一需要净化臭氧的净化装置中;或直接将其放置于需要净化臭氧的空间内,解决室外臭氧污染问题。
20.本发明公开了以下技术效果:
21.(1)本发明由木材经过高温热解制得生物炭材料,制备工艺简单、成本低,易于大规模生产。
22.(2)本发明利用生物炭材料的良好吸附性,使所述材料可以高效净化空气中的臭氧,利于活性组分进行催化氧化反应。
23.(3)本发明的生物炭材料可以作为净化材料直接放在室外,不额外供能的情况下有较好的去除效果,净化成本低,且可长期连续作用。
附图说明
24.为了更清楚地说明本发明实施例或现有技术中的技术方案,下面将对实施例中所需要使用的附图作简单地介绍,显而易见地,下面描述中的附图仅仅是本发明的一些实施例,对于本领域普通技术人员来讲,在不付出创造性劳动性的前提下,还可以根据这些附图获得其他的附图。
25.图1为实施例1所用榉木木材和榉木木材所制得的生物炭材料的x射线衍射图;
26.图2为实施例1所用榉木原木的场发射扫描电子显微镜切面(左)和表面照片(右);
27.图3为实施例1榉木生物炭材料的场发射扫描电子显微镜切面(左)和表面照片(右);
28.图4为实施例1榉木生物炭材料的透射电子显微镜照片;
29.图5为实施例1~5制得的榉木生物炭材料在不同温度下对空气中臭氧的去除效果;
30.图6为用于测试生物炭材料性能的实验装置实物图;
31.图7为用于测试生物炭材料性能的实验装置流程图;
32.图8为实施例1中由不同木材制得的生物炭材料分解臭氧的实验结果;
33.图9为实施例1~5榉木制备的生物炭材料分解臭氧的实验结果。
具体实施方式
34.现详细说明本发明的多种示例性实施方式,该详细说明不应认为是对本发明的限制,而应理解为是对本发明的某些方面、特性和实施方案的更详细的描述。
35.应理解本发明中所述的术语仅仅是为描述特别的实施方式,并非用于限制本发明。另外,对于本发明中的数值范围,应理解为还具体公开了该范围的上限和下限之间的每个中间值。在任何陈述值或陈述范围内的中间值以及任何其他陈述值或在所述范围内的中间值之间的每个较小的范围也包括在本发明内。这些较小范围的上限和下限可独立地包括或排除在范围内。
36.除非另有说明,否则本文使用的所有技术和科学术语具有本发明所述领域的常规技术人员通常理解的相同含义。虽然本发明仅描述了优选的方法和材料,但是在本发明的实施或测试中也可以使用与本文所述相似或等同的任何方法和材料。本说明书中提到的所有文献通过引用并入,用以公开和描述与所述文献相关的方法和/或材料。在与任何并入的文献冲突时,以本说明书的内容为准。
37.在不背离本发明的范围或精神的情况下,可对本发明说明书的具体实施方式做多种改进和变化,这对本领域技术人员而言是显而易见的。由本发明的说明书得到的其他实施方式对技术人员而言是显而易见得的。本发明说明书和实施例仅是示例性的。
38.关于本文中所使用的“包含”、“包括”、“具有”、“含有”等等,均为开放性的用语,即意指包含但不限于。
39.实施例1
40.在使用管式炉之前,先向管内通氮气30min,流量为50ml/min,将尺寸为2
×
2cm的圆柱形榉木、松木、香樟、黄杉、楝木、榆木、泡桐分别放入管式炉中并以5℃/min的升温速率从室温升至800℃,恒温6h,等待管式炉冷却降温后即可将生物炭材料取出。
41.本实施例所用榉木木材和榉木木材所制得的生物炭材料的x射线衍射图见图1,在原木(r-wood)样品的图线中,观察到位于15
°
和24
°
的2个特征衍射峰,与纤维素相匹配;在由原木所制得生物炭样品(c-wood)的图线中,观察到位于24
°
和44
°
的2个特征衍射峰,与石墨碳相对应,表明原木经炭化这一过程转化成了生物炭。
42.本实施例所用榉木原木的场发射扫描电子显微镜切面和表面照片见图2,可看出原始木材表面微孔少且切开后内部杂乱无序,不利于臭氧吸附。
43.本实施例榉木所得生物炭材料比表面积为751m2/g,孔隙率为17%,孔容积为0.05cm3/g,孔径分布介于3~5nm,场发射扫描电子显微镜切面和表面照片见图3,可以看出生物炭材料表面微孔多且大小不一,有利于暴露更多的催化活性位点和促进臭氧吸附。切开后内部纹路清晰,有利于阳光在内部进行多次反射,使样品能均匀地吸收热量,进一步促进臭氧分解。
44.本实施例榉木所得生物炭材料的透射电子显微镜照片见图4,图4中所圈的平行条
纹表明材料由少数堆叠层构成,内部会进行循环的电子跃迁。
45.实施例2
46.在使用管式炉之前,先向管内通氮气30min,流量为50ml/min,再将尺寸为2
×
2cm的圆柱形榉木放入管式炉中并以5℃/min的升温速率从室温升至500℃,恒温6h,等待管式炉降温后便可将生物炭材料取出,比表面积为736m2/g,孔隙率为7%,孔容积为0.02cm3/g,孔径分布为3~6nm。
47.实施例3
48.在使用管式炉之前,先向管内通氮气30min,流量为50ml/min,再将尺寸为2
×
2cm圆柱形榉木放入管式炉中并以5℃/min的升温速率从室温升至600℃,恒温6h,等待管式炉降温后便可将生物炭材料取出,比表面积为741m2/g,孔隙率为10%,孔容积为0.03cm3/g,孔径分布为4~5nm。
49.实施例4
50.在使用管式炉之前,先向管内通he气30min,流量为50ml/min,再将尺寸为2
×
2cm圆柱形榉木放入管式炉中并以5℃/min的升温速率从室温升至700℃,恒温6h,等待管式炉降温后便可将生物炭材料取出,比表面积为746m2/g,孔隙率为13%,孔容积为0.04cm3/g,孔径分布为4~5nm。
51.实施例5
52.在使用管式炉之前,先向管内通ar气30min,流量为50ml/min,再将尺寸为2
×
2cm圆柱形榉木放入管式炉中并以5℃/min的升温速率从室温升至900℃,恒温6h,等待管式炉降温后便可将生物炭材料取出,比表面积为756m2/g,孔隙率为23%,孔容积为0.07cm3/g,孔径分布为3~5nm。
53.在不同温度下测定实施例1~5制得的榉木生物炭材料对空气中臭氧的去除效果,结果见图5。所得生物炭材料的臭氧降解实验在反应炉中进行,通过臭氧分析仪(ozt-350型)在线检测臭氧的实时浓度。从图5可知,在干空气条件下(rh=3.1%),臭氧转化率随温度的升高而增加,当温度升至90℃时,在一定时间内(6h)去除率可达100%,这表明反应温度越高去除效果越好。
54.图6为用于测试生物炭材料性能的实验装置实物图,图7为用于测试生物炭材料性能的实验装置使用流程图,图8为实施例1中由不同木材制得的生物炭材料分解臭氧的实验结果,图9为实施例1~5榉木制备的生物炭材料分解臭氧的实验结果。从图8可以看出,由不同种类木材所制得的生物炭材料对臭氧的去除效果相差较大,其中黄杉的效果最好,在相同反应条件下对臭氧的去除率可达100%。
55.为了确定最佳的木材热解温度,选取500~900℃的温度范围来作比较,从图9可以看出当温度达到800℃及以上时,在一定时间内(6h)臭氧可被完全去除。这表明热解温度越高,木材炭化越充分,表面的多孔结构有利于臭氧的去除。
56.实施例6
57.以黄杉为原料,将黄杉粉碎过100目筛后,加入到fe(no3)3·
9h2o溶液和mg(no3)2·
6h2o溶液的混合溶液中,黄杉与混合溶液的质量比为1:2,混合溶液中镁和铁的摩尔比为1:1,搅拌均匀,200r/min的摇床振荡浸渍24h,60℃烘干,粉碎过100目筛,将其倒入瓷舟中,放入管式炉中,在使用管式炉之前,先向管内通氮气30min,流量为40ml/min,并以5℃/min的
升温速率从室温升至400℃,恒温6h,等待管式炉冷却降温后,将瓷舟取出,经研钵碾碎,过100目筛后得到生物炭材料,比表面积为924m2/g,孔隙率为53%,孔容积为0.15cm3/g,孔径分布介于5~7nm。由xrd衍射图可以看出本实施例制备的生物炭材料物相主要有钙钛矿型(mgfeo3)、尖晶石(mgfe2o4)、铁的氧化物(feo、fe2o3、fe3o4)和镁的氧化物(mgo)结构,由场发射扫描电子显微镜表面照片看出表面有形状大小不规则的粒状结构,活性位点众多。
58.实施例7
59.以黄杉为原料,将黄杉粉碎过100目筛后,加入到fe(no3)3·
9h2o溶液和mg(no3)2·
6h2o溶液的混合溶液中,黄杉与混合溶液的质量比为1:2,混合溶液中镁和铁的摩尔比为1:1,搅拌均匀,200r/min的摇床振荡浸渍24h,60℃烘干,粉碎过100目筛,将其倒入瓷舟中,放入管式炉中,在使用管式炉之前,先向管内通ar气30min,流量为30ml/min,并以5℃/min的升温速率从室温升至450℃,恒温6h,等待管式炉冷却降温后,将瓷舟取出,经研钵碾碎,过100目筛后得到生物炭材料,比表面积为931m2/g,孔隙率为55%,孔容积为0.18cm3/g,孔径分布介于5~7nm。
60.实施例8
61.以黄杉为原料,将黄杉粉碎过100目筛后,加入到fe(no3)3·
9h2o溶液和mg(no3)2·
6h2o溶液的混合溶液中,黄杉与混合溶液的质量比为1:2,混合溶液中镁和铁的摩尔比为1:1,搅拌均匀,200r/min的摇床振荡浸渍24h,60℃烘干,粉碎过100目筛,将其倒入瓷舟中,放入管式炉中,在使用管式炉之前,先向管内通氮气30min,流量为20ml/min,并以5℃/min的升温速率从室温升至500℃,恒温6h,等待管式炉冷却降温后,将瓷舟取出,经研钵碾碎,过100目筛后得到生物炭材料,比表面积为934m2/g,孔隙率为56%,孔容积为0.17cm3/g,孔径分布介于6~7nm。
62.实施例9
63.以黄杉为原料,将黄杉粉碎过100目筛后,加入到fe(no3)3·
9h2o溶液和mg(no3)2·
6h2o溶液的混合溶液中,黄杉与混合溶液的质量比为1:2,混合溶液中镁和铁的摩尔比为1:1,搅拌均匀,200r/min的摇床振荡浸渍24h,60℃烘干,粉碎过100目筛,将其倒入瓷舟中,放入管式炉中,在使用管式炉之前,先向管内通he气30min,流量为5ml/min,并以5℃/min的升温速率从室温升至550℃,恒温6h,等待管式炉冷却降温后,将瓷舟取出,经研钵碾碎,过100目筛后得到生物炭材料,比表面积为937m2/g,孔隙率为55%,孔容积为0.16cm3/g,孔径分布介于5~8nm。
64.对比例1
65.同实施例7,不同之处仅在于混合溶液中镁和铁的摩尔比为1:3。
66.本对比例制备的生物炭材料的比表面积为390m2/g,孔隙率为15%,孔容积为0.05cm3/g,孔径分布介于5~8nm。
67.镁和铁的摩尔比改变之后,未生成尖晶石、钙钛矿物相,表面未观察到明显的粒状结构,显著减小了生物炭材料的比表面积。
68.测试实施例6~9和对比例1制备的生物炭材料对臭氧的降解能力(rh=3.1%,t=90℃),臭氧降解实验在反应炉中进行,通过臭氧分析仪(ozt-350型)在线检测臭氧的实时浓度,不同时间臭氧去除率(%)结果见表1。
69.表1
[0070] 30min50min80min100min200min实施例695%100%100%100%100%实施例798%100%100%100%100%实施例8100%100%100%100%100%实施例998%100%100%100%100%对比例185%86%95%100%100%
[0071]
由表1可知实施例6~9制备的生物炭材料可以明显缩短降解臭氧的时间。
[0072]
以上所述的实施例仅是对本发明的优选方式进行描述,并非对本发明的范围进行限定,在不脱离本发明设计精神的前提下,本领域普通技术人员对本发明的技术方案做出的各种变形和改进,均应落入本发明权利要求书确定的保护范围内。